
книги / Теория и технология нанесения газотермических покрытий
..pdfПодготовку стержней проводят теми же способами, что и подготовку проволоки.
1.5. Подготовка напыляемой поверхности
Прочность и качество адгезионного схватывания материалов покрытия и изделия во многом зависят от чистоты контактирующих поверхностей. Перед проведением операции напыления поверхность необходимо очистить от различных загрязнений [8]:
–механических (пыль, абразив, коррозия);
–химически связанных и растворимых в воде (соли, кислоты, оксиды, нитриды и др.);
–газообразных загрязнителей, адсорбированных поверхностью. Особенно неблагоприятное воздействие на качество напыляе-
мого слоя оказывают органические и химически связанные загрязнения поверхности.
Кроме непосредственной очистки напыляемой поверхности изделия от загрязнений необходимо провести энергетическую активацию ее поверхностного слоя. После активации атомы материала изделия в поверхностном слое более интенсивно взаимодействуют с частицами напыляемого материала, в результате повышается качество и адгезионная прочность покрытия.
Поверхность изделия должна обеспечивать улучшение механического закрепления на ней напыляемых частиц, что осуществляется созданием определенного микрорельефа (рекомендуемое значение шероховатости Rz = 20…80 мкм). Наличие микрорельефа на напыляемой поверхности увеличивает площадь контактного взаимодействия материалов изделия и покрытия.
Практически предварительная подготовка поверхности для методов ГТН проводится обезжириванием, механическими способами очистки и абразивно-струйной очисткой.
Обезжиривание проводят в ваннах, погружая в них деталь целиком, или применяют местное обезжиривание путем протирки. Используют щелочные растворы или органические растворители – керосин, бензол, толуол, хлорированные углеводороды и т.п. В особо
11
ответственных случаях используют электрохимическое обезжиривание в щелочных растворах и ультразвуковую очистку. Для капиллярного удаления адсорбированной жидкой смазки используют выжигание с нагревом в печи до 150–200 °С.
Напыляемая поверхность подвергается различным методам механической обработки для придания ей сложного микрорельефа. Микрорельеф можно получать нарезкой (точением, фрезерованием) и накаткой канавок различного профиля. Поскольку микрорельеф имеет существенную толщину, его создают при напылении покрытий достаточно большой толщины, предназначенных для работы в условиях значительных механических нагрузок.
Абразивно-струйная очистка является наиболее часто применяемым способом предварительной подготовки напыляемой поверхности. Могут применяться также методы дробеструйной обработки и аналогичные им. В результате абразивно-струйной очистки происходит не только механическая очистка поверхности, но и удаление с нее химических пленок.
При абразивно-струйной обработке обрабатываемая поверхность обдувается струей сжатого воздуха с частицами абразива. Обработка ведется в полностью изолированных от окружающей среды камерах и является полностью автоматизированной. В качестве абразива обычно применяют электрокорунды, в качестве дроби применяют стальные шарики диаметром 0,5–2 мм. Давление струи сжатого воздуха составляет 0,4–0,7 МПа. Воздух необходимо предварительно очищать от влаги и масла. Дистанция обработки составляет 100–150 мм, время очистки 25–30 с до образования равномерного оттенка поверхности. Интервал времени между обработкой и напылением должен быть минимальным и не превышать 0,5–1 ч.
Для придания микрорельефа напыляемой поверхности также возможно предварительное нанесение промежуточного слоя покрытия, которое обладает повышенными адгезионными свойствами (алюминид никеля).
Все перечисленные ранее способы предварительной подготовки напыляемой поверхности изделия либо используют по отдельности, либо комбинируют друг с другом.
12
Химические способы подготовки поверхности (химическое травление, полировка) в методах ГТН используются редко. Сложность вызывает подбор химических травителей.
В технологию подготовки напыляемой поверхности входит операция по защите участков детали, не подлежащих напылению. Эти участки защищаются экранами из жести или керамическими обмазками на основе жидкого стекла. Отверстия масляных каналов проще всего заглушить деревянной пробкой.
1.6. Контроль качества напыления
Контроль качества напыленных покрытий проводится неразрушающими или разрушающими методами. Неразрушающими методами определяется толщина покрытия и неравномерность этой толщины вдоль оси детали, наличие наружных дефектов (трещины, сколы, вспучивания и т.п.), замеряется твердость, если габариты изделия позволяют транспортировать его к твердомеру.
Разрушающий контроль заключается в изготовлении образцов для анализа непосредственно из напыленного изделия (выборочный контроль). По образцам проводится макро- и микроструктурный анализ покрытий, замер твердости и микротвердости, выявляются пористость и другие скрытые дефекты, косвенно определяется степень адгезии.
1.7. Последующая обработка напыленных изделий
Последующая обработка изделий с газотермическим покрытием обычно представляет собой механическую обработку. Для повышения качества покрытий при необходимости используют термическую обработку, пропитку, обработку лазером.
Механическая обработка проводится для получения требуемой чистоты поверхности и необходимых размеров. Обработка со снятием стружки (кроме оплавленных покрытий) не проводится. Применяют шлифование абразивными кругами марки К3 или алмазными инструментами (алмазный круг, лента).
13
Термическая обработка может проводиться для выравнивания макро- и микроструктуры, для снятия внутренних напряжений. Однако это слишком усложняет технологию получения покрытий в целом и используется крайне редко. В основном для термической обработки покрытий используют метод оплавления, который заключается в нагреве покрытия до температуры плавления напыленного материала. Этот метод, в частности, применяют для покрытий, полученных из самофлюсующихся материалов.
Самофлюсование происходит в том случае, если оксиды обладают определенными свойствами: жидкотекучестью, малой плотностью и низкой температурой плавления. Такими свойствами обладают, например, оксиды B2O3, Cr2O2, SiO2. Оплавление используют для покрытий, полученных из сплавов на никелевой основе Ni-Cr-B-Si (марки ПГ-12Н, ПГ-ХН80СР, СНГН). В этом случае оплавление осуществляют при температуре 1050–1080 °С с выдержкой 1–2 мин. Оксиды при оплавлении всплывают на поверхность и формируют налет. Кроме флюсования при оплавлении происходит формирование карбидных фаз высокой твердости, которые дополнительно улучшают износостойкость поверхности покрытия.
Пропитку применяют после механической обработки для снижения открытой пористости. Для этого на напыленную поверхность наносят пропиточный материал, который при расплавлении проникает за счет капиллярных сил в несплошности покрытия. Так, например, используют медь, различные припои и полимеры при пропитке карбидных и оксидных покрытий.
Лазерная обработка заключается в перемещении луча лазера по напыленной поверхности. Эффект упрочнения проявляется в измельчении структуры, устранении пористости и повышении твердости.
Контрольные вопросы
1.Из каких этапов состоит технологический процесс нанесения покрытий методом ГТН?
2.Из каких этапов состоит конструкторско-технологическая подготовка производства для нанесения покрытий методом ГТН?
14
3.Из какихэтапов состоит техническая подготовкапроизводства?
4.Какие технологические критерии используют при выборе технологии нанесения покрытия?
5.Какие экономические критерии используют при выборе технологии нанесения покрытия?
6.Какие покрытия существуют? Каковы их назначение и свой-
ства?
7.Какие покрытия можно получать методом ГТН?
8.Каким образом предварительно готовят напыляемый материал в виде порошков?
9.Каким образом предварительно готовят напыляемый материал в виде проволоки?
10.Как свойства напыляемой поверхности влияют на качество покрытия?
11.Каким образом подготавливают напыляемую поверхность?
12.Как проводят контроль качества напыленных покрытий?
13.Какими методами можно обрабатывать напыленные по-
крытия?
14.Для чего проводят термическую обработку нанесенных по-
крытий?
15
ГЛАВА 2. МЕТОДИКА ГТН
2.1. Основные методы ГТН
Методы ГТН классифицируют по следующим признакам:
–по типу используемой энергии – газопламенные и газоэлектрические;
–по способу формирования тепловой энергии – использующие энергию дуги, плазмы, токов высокой частоты, газового пламени;
–по виду распыляемого материала – использующие порошки, проволоку, порошковую проволоку;
–по степени защиты – без использования защитных конструкций, с использованием частичной защиты, герметичных камер;
–по степени механизации и автоматизации процесса – с применением ручных, механизированных (перемещение либо распылителя, либо изделия) конструкций; с полной или частичной автоматизацией работы оборудования;
–по цикличности процесса напыления – с непрерывным процессом (постоянный поток напыляемого материала), с циклическим процессом (периодический поток напыляемого материала).
В настоящее время технология газотермического напыления представлена в основном четырьмя методами [2, 4]:
1) электродуговой металлизацией;
2) газопламенным напылением;
3) плазменным напылением;
4) детонационно-газовым напылением. Рассмотрим эти методы подробнее.
2.1.1. Электродуговая металлизация
Метод электродуговой металлизации (ЭДМ) заключается в распылении струей воздуха или другого газа капель жидкого металла, образующихся в результате плавления расходуемых проволочных электродов за счет создания между ними дугового разряда
(рис. 2.1).
16
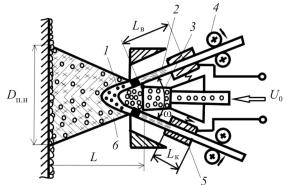
Рис. 2.1. Схема процесса электродуговой металлизации: 1 – зона горения дуги; 2 – проволочные материалы; 3 – сопло; 4 – механизм подачи проволоки; 5 – контактные устройства; 6 – двухфазная струя (Lв – длина вылета электродов; Lк – длина контакта токосъема; L – дистанция напыления; Dп.н – диаметр пятна напыления; ω – угол схождения
электродов; U0 – напряжение между электродами)
Ваппаратах ЭДМ применяются постоянная независимая скорость подачи электродов; дуговой разряд как постоянного, так и переменного тока.
Взависимости от назначения покрытия для напыления используются алюминий, цинк, медь и ее сплавы, углеродистые и нержавеющие стали в виде проволоки диаметром 1–3 мм. Интересной особенностью метода ЭДМ является возможность нанесения композиционных покрытий (типа псевдосплавов) путем распыления проволок из разных металлов.
Метод отличает достаточно высокая производительность, сравнительная простота аппаратурного оформления, широкие возможности механизации и автоматизации процесса. Одновременно с этим принцип ЭДМ резко ограничивает применение метода по напыляемым материалам (используется только металлическая проволока). Особенности этого метода позволяют применять ЭДМ в цехах для восстановления изношенных покрытий и на открытых строительных площадках для нанесения антикоррозионных покрытий на крупногабаритные металлические конструкции.
17
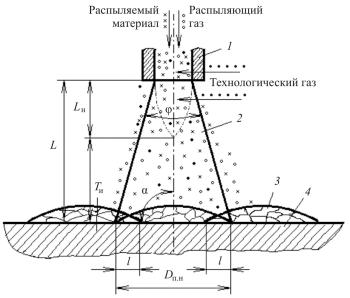
2.1.2. Газопламенное напыление
Принцип метода газопламенного напыления (ГПН) заключается в нагреве напыляемого материала теплом газового пламени и распылении струей сжатого воздуха [13]. Напыляемый материал подается в виде проволоки, порошка, стержней (прутков) и реже в виде гибких жилок в высокотемпературную зону пламени (рис. 2.2).
Lo
Рис. 2.2. Схема формирования покрытия при газопламенном напылении: 1 – сопло; 2 – газовый поток; 3 – напыляемое покрытие; 4 – напыляемая поверхность (ϕ – угол распыления; α – угол между направлением потока и напыляемой поверхностью; Dп.н – диаметр пятна напыления;
Tи – температура |
на поверхности изделия; l – перекрытие пятен напыления; |
L – дистанция |
напыления; Lн – начальная зона газового потока; |
|
Lo – основная зона газового потока) |
Повышенное давление на выходе из воздушного сопла обеспечивает высокую температуру и скорость газового потока, интенсифицирует процессы нагрева и распыления материала. Для формирования воздушного потока с требуемыми динамическими характери-
18
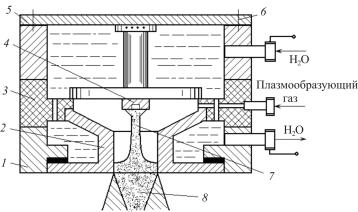
стиками распылительное устройство снабжают дополнительным обжимным соплом. Благодаря такой схеме напыляемый материал нагревается более интенсивно.
С помощью метода ГПН наносятся антикоррозионные и антифрикционные покрытия из алюминия, медных сплавов, нержавеющей стали. Кроме того, он позволяет наносить износостойкие покрытия из самофлюсующихся сплавов. Этим методом наносят полимерные покрытия для восстановительных и декоративных целей. Полимер подается в виде порошка.
Метод широко распространен благодаря своей простоте и технологической гибкости. Очень широко он используется для ручного нестационарного нанесения покрытий на крупногабаритные детали.
2.1.3. Плазменное напыление
Сущность метода плазменного напыления (ПН) заключается в нагреве напыляемого материала и переносе частиц в высокотемпературном потоке газа, образованном при его прохождении через область столба дуги [17] (рис. 2.3). Устройства для генерации высокотемпературных газовых потоков называют дуговыми плазмотронами.
Рис. 2.3. Схема плазменного напыления: 1 – корпус; 2 – подающее сопло; 3 – электрическая изоляция; 4 – рабочий электрод; 5 – прокладки; 6 – элементы крепления; 7 – электрическая дуга; 8 – поток плазмы
19
Плазмой называется газ, который находится в ионизированном состоянии. Ионизация газа происходит в результате потери электронов из-за соударений атомов, вызванных высокими температурой и давлением. При начальном формировании плазмы внутри сопла ее температура достигает 18 000–20 000 °С, однако при дальнейшем движении плазма существенно охлаждается, и уже на рабочем расстоянии порядка 20 мм от сопла температура может составлять
5000–8000 °С.
Плазмотрон состоит из трех основных частей: водоохлаждаемого медного анода, вольфрамового катода и изолятора. Нагрев газа осуществляется передачей энергии от электрической дуги. Электрическая дуга формируется между соплом (анодом) и электродомкатодом. Частицы напыляемого материала вбрасываются в поток плазмы, который разогревает их до расплавленного состояния. Расплавленные частицы разгоняются потоком плазмы до скоростей порядка 300 м/с, после чего сталкиваются с напыляемой поверхностью, формируя покрытие. Для формирования плазмы используют самые различные по свойствам газы от аргона до водяного пара.
Поскольку плазма способна мгновенно расплавить любой материал, метод плазменного напыления является универсальным. Если учесть еще и высокую производительность метода, то он становится самым распространенным.
2.1.4. Детонационно-газовое напыление
Сущность метода детонационно-газового напыления (ДГН)
заключается в детонации смеси горючих газов, в результате которой происходит ее мгновенное ускорение до скоростей порядка 2000 м/с [14]. Смесь горючих газов предварительно помещают в камеру сгорания вместе с порошком напыляемого материала, затем поджигают электрической искрой, в результате чего происходит детонация.
Теплота, выделившаяся при взрыве, и ударная волна обеспечивают разогрев и ускорение частиц порошка, определенные порции которого заранее вводят в ствол установки. При этом частицам порошка сообщается большая кинетическая энергия. Скорость движения частиц составляет 600–1000 м/с, что в 4–7 раз превышает ско-
20