
книги / Теория и технология нанесения газотермических покрытий
..pdfзначение напряжения за период горения дуги меняется вследствие цикличности процесса.
Эффективный КПД нагрева проволоки ηн.п характеризует энергетические затраты на нагрев, плавление и перегрев распыляемого металла электродов.
Вкачестве распыляющего газа используется сжатый воздух. Давление и расход стремятся увеличить, поскольку при этом:
а) возрастает скорость струи; б) возрастает распыляющая способность;
в) увеличивается производительность.
Желательным является обеспечение сверхзвукового истечения струи.
Для эффективной работы необходимо подбирать такие энергетические параметры работы распылителя, при которых максимально удаляется расплавленный материал с электрода. Наличие жидкого слоя расплавленного материала на электроде снижает тепломассоперенос от электрода к электрической дуге. С увеличением расхода
идавления рабочего газа диспергирование распыляемого материала усиливается.
ГПН. Для метода ГПН наиболее важными параметрами, характеризующими энергетический режим работы распылителя, являются вид горючего газа, расход и давление рабочей смеси газов (горючего
иокислительного).
Врабочей смеси газов используют ацетилен, пропан, бутан
идругие виды горючих газов (табл. 3.1).
|
|
|
Таблица 3.1 |
Тепловые характеристики рабочих газов при ГПН |
|||
|
|
|
|
Характеристики |
Ацетилен |
Пропан |
Бутан |
Теплотворная способность |
56,5 |
93,5 |
125,1 |
при 25 °С и 0,1 МПа, МДж/м3 |
|||
Максимальная температура |
3100–3200 |
2400–2700 |
2400–2700 |
газового пламени, К |
|
|
|
Самые высокие температуры достигаются при горении ацетиленокислородной смеси. Но у смесей на основе пропана и бутана
41
более высокие показатели теплотворности. Поэтому наиболее часто на практике используют в качестве рабочей смеси газов пропанобутановую смесь и ацетилен.
Расход газа определяется его давлением. С увеличением расхода возрастает тепловая мощность газового пламени (Wг.п), скорость газового пламени, длина высокотемпературной части потока (Lo). Соответственно росту этих характеристик требуется и увеличение скорости подачи распыляемого материала (проволоки). Производительность при этом также растет.
ПН. При использовании метода ПН энергетические параметры в наибольшей степени ответственны за формирование двухфазного потока и его теплофизических свойств (температуры, энтальпии, скорости).
Рассмотрим влияние на эффективность процесса напыления мощности дуги (рис. 3.5), рода и расхода плазмообразующего газа.
Увеличение мощности дуги Wд влияет на эффективность напыления абсолютно положительно. Улучшаются практически все характеристики как двухфазного потока, так и покрытия. Например, возрастают температура и скорость частиц, производительность процесса напыления, КИМ, плотность покрытия.
Для обеспечения требуемой мощности работы плазмотрона необходимо учитывать два параметра: силу тока и напряжение. Напряжение определяется длиной электрической дуги, которая зависит от конструктивных параметров сопла и вида рабочей смеси газов. Поэтому его величину изменять нельзя. Величину мощности регулируют за счет изменения силы тока.
Величина расхода рабочего газа имеет важное значение для обеспечения максимальной эффективности процесса напыления, ее необходимо подбирать исходя из следующих соображений. При увеличении расхода рабочего газа до оптимального значения происходит улучшение характеристик процесса напыления из-за увеличения скорости распыляемых частиц. Также при увеличении расхода рабочего газа поток частиц, получаемый в результате распыления проволоки, является более дисперсным. При достижении оптималь-
42
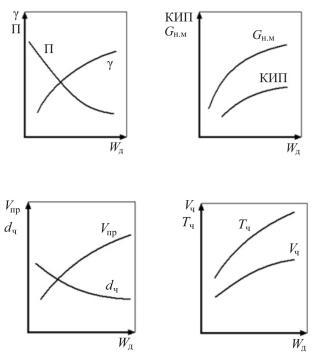
ной величины расхода рабочего газа начинается постепенное уменьшение температуры разогрева частиц, однако их скорости еще хватает для оптимального течения процесса напыления.
аб
вг
Рис. 3.5. Зависимости параметров ПН от мощности электрической дуги Wд плазмотрона: а – плотности (γ) и пористости (П) покрытия; б – коэффициента использования порошка (КИП) и производительности процесса напыления (Gн.м); в – скорости плавления проволоки (Vпр) и диаметра распыленных частиц (dч); г – температуры (Tч) и скорости (Vч) распыляемых частиц
При дальнейшем увеличении величины расхода рабочего газа параметрыкачества напыляемогопокрытия существенно снижаются.
Рекомендуемая величина расхода рабочего газа обычно имеет значения порядка 2,0–4,0 м3/ч.
43
Вид газов рабочей смеси также оказывает существенное влияние на энергетические параметры процесса напыления и, соответственно, качество напыляемого покрытия. Наиболее перспективны смеси активных и инертных газов. Они улучшают теплообмен между порошковыми частицами и плазмой и увеличивают длину участка нагрева плазменных струй, особенно при использовании водородсодержащих смесей. С низкочастотными пульсациями успешно борются аргон-азотные смеси (70 % Ar и 30 % N2).
ДГН. Для метода ДГН основными энергетическими параметрами являются род и расход газов, отношение расхода кислорода к расходу горючего газа β.
Наибольшая эффективность достигается при использовании ацетиленовой, реже пропан-бутановой смеси (с кислородом) при больших расходах (0,2–6,0 м3/ч).
Большое влияние на эффективность процесса оказывают технологические добавки, в частности наиболее часто употребляемый азот. С одной стороны, избыток азота снижает температуру и скорость напыляемых частиц. С другой стороны, снижение содержания азота или его полное исключение приводит к усилению процесса сажеобразования. Сажеобразование происходит из-за того, что в составе рабочей смеси газов содержится большое количество углерода, который после реакции распада частично соединяется в графит. Углерод забивает канал.
Сажеобразование регулируют соотношением С2Н2 и О2 (параметром β). Если С2Н2 больше 50 %, то образуется свободный углерод, который помимо забивания канала ствола снижает адгезию напыляемых частиц. При содержании О2 выше 56 % пламя будет окислительным. Оптимальным считается соотношение О2:С2Н2 = 1,2. При использовании окисных материалов допускается содержание О2
до 70 %.
В общем, состав смеси влияет на количество тепла, выделившегося при детонации, степень термической диссоциации продуктов детонации, температуру и скорость детонационной волны и продуктов ее распада.
44
3.4. Внешние условия напыления
ЭДМ. Дистанция напыления L (в случае ЭДМ ее называют дистанцией металлизации) обычно составляет 120–150 мм.
ГПН. Для ГПН дистанция напыления L составляет 100–200 мм. ПН. Дистанция напыления L при плазменном напылении может составлять 50–300 мм в зависимости от условий работы. В случае малых дистанций напыления, когда ее величина соразмерна с величиной плазменной дуги, частицы напыляемого материала не всегда успевают прогреться и приобрести необходимую скорость. Кроме того, возможен перегрев детали. Если длина дистанции напыления свыше оптимальной, то резко падают температура и скорость основного участка струи, а также напыляемых частиц. Длина L максимальна при больших мощностях дуги, при ведении процесса в низ-
ком вакууме, при использовании ламинарной плазмы.
Скорость перемещения распылителя составляет 0,05–1,0 м/с. Если скорость низкая, то возможен перегрев детали, но при этом контактная температура частиц увеличивается, что улучшает качество покрытия. Увеличение скорости делает покрытие более равномерным по толщине.
Если процесс ведется в среде защитного газа, то к параметрам рассматриваемой группы относятся расход защитного газа, а также его давление и температура в вакуумной камере.
При снижении давления в камере эффективность процесса значительно увеличивается благодаря тому, что возрастает осевая скорость плазменной струи, а соответственно, и скорость напыляемых частиц. Помимо этого уменьшается угол расхождения струи.
ДГН. При таком напылении дистанция напыления L – это расстояние от открытого конца ствола до подложки. Ее выбирают с учетом глубины загрузки материала в ствол. Она влияет на скорость частиц и адгезионную прочность. Для ДГН дистанция напыления составляет 50–200 мм (определяется материалом, размерами и формой материала, требуемой толщиной покрытия).
45
3.5.Параметры распыляемого материала
иусловия его ввода
ЭДМ. Для этого метода используется проволока диаметром dпр = 1,0…3,5 мм. С его увеличением:
–увеличивается производительность процесса;
–увеличивается неоднородность потока распыляемых частиц. При уменьшении диаметра проволоки dпр требуются более вы-
сокие скорости ее подачи, чтобы обеспечить необходимый расход проволоки.
Скорость подачи проволоки Vпр выбирают максимальной. При этом должны выдерживаться предельные значения угла фронта плавления проволоки, чтобы увеличить скорость плавления прово-
локи. Допускаемая величина смещения торцов проволоки |
= dпр/4. |
В момент диспергирования частицы материала |
находятся |
в жидком состоянии. Их размер зависит от производительности распыления, обратно пропорционален плотности распыляемого материала и зависит от режима горения дуги. При непрерывном горении диспергирование максимально. Размер металлических частиц обычно составляет 10–100 мкм (для сталей размер частиц 30–50 мкм).
Одной из особенностей процесса является то, что частицы распыляемого материала, покинув электрод, дополнительно диспергируются под влиянием турбулентности газового потока.
Процесс ЭДМ характеризуется большой плотностью потока напыляемых частиц вблизи поверхности изделия, которая составляет 103–105 частиц/(см2·с). Этот показатель определяет высокую производительность распыления.
ГПН. Материал для напыления при ГПН подается в виде порошка или проволоки. Частицы порошкового напыляемого материала должны иметь размеры не более 10–100 мкм. Более крупные частицы не прогреваются. Расход порошка составляет 0,5–3,0 кг/ч.
Существует два метода подачи порошкового напыляемого материала в активную зону:
а) под действием веса порошка; б) с помощью транспортирующего газа (воздуха) под давлени-
ем 0,1–0,2 МПа.
46
При использовании проволоки ее диаметр dпр составляет 1–5 мм, скорость подачи Vпр = 180…500 м/ч. Чем больше диаметр проволоки, тем выше производительность процесса.
ПН. Возможны порошковые и проволочные способы плазменного напыления. Поскольку порошки могут быть изготовлены из любых материалов и более универсальны, чем проволока, методы ПН на основе порошков имеют более широкое применение.
Методом ПН напыляют обычные порошки с размером частиц 40–100 мкм и композиционные порошковые материалы. Гранулометрический состав последних обычно выдержан в узких пределах. Они часто имеют частицы сферической формы, состоят из большого числа химических элементов, покрытия на их основе обладают высокими эксплуатационными характеристиками.
Основной проблемой при напылении порошковых материалов, имеющих частицы большого размера, является неоднородность получаемого покрытия, которая вызвана следующими явлениями:
1)частицы неметаллических материалов плохо прогреваются плазмой, поскольку обладают низкой теплопроводностью;
2)частицы неметаллических материалов плохо прогреваются плазмой, поскольку находятся под воздействием плазмы незначительный промежуток времени (около 1 мкс);
3)используемые рабочие газовые смеси недостаточно хорошо передают теплоту порошковым частицам.
В связи с перечисленными причинами требуется решать проблему эффективности передачи теплоты частицам напыляемого материала за счет увеличения мощности плазменной струи.
Плазменное напыление с распылением проволоки производится двумя способами: с использованием нейтральной проволоки (рис. 3.6, а) и проволоки-анода (рис. 3.6, б).
Процесс подачи проволоки в рабочую зону осуществляется перпендикулярно потоку плазмы. Под воздействием температуры потока плазмы проволока диспергируется на мелкие частицы и увлекается направлением течения в зону напыления. Процесс распыления анодной проволоки характеризуется высокой производительностью, но при этом покрытия имеют более грубую (крупную) структуру.
47
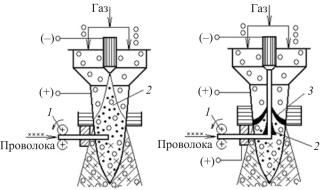
а |
б |
Рис. 3.6. Схема ПН с нейтральной проволокой (а) и проволокой-анодом (б): 1 – подающие ролики; 2 – струя плазмы; 3 – зона зажигания
При проволочных способах напыления стремятся подобрать параметры процесса так, чтобы можно было реализовать мелкокапельное распыление проволоки, способствующее формированию плотной структуры покрытия.
К наиболее ответственным параметрам относятся диаметр проволоки, заглубление при использовании нейтральной проволоки и скорость подачи. Диаметр проволоки dпр обычно составляет 0,8–2,5 мм. Увеличение диаметра приводит к возрастанию среднего размера распыляемых частиц.
Скорость подачи должна быть оптимальной. Оптимальными считаются условия, при которых скорость подачи напыляемого материала соответствует скорости его плавления, что сопровождается мелкокапельным распылением проволоки. При небольших скоростях образуются крупные капли. Слишком высокие скорости приводят к появлению нерасплавленного стержня. Оптимальная скорость подачи Vпр нейтральной проволоки составляет 10–25 м/с; проволоки-
анода – 30–70 м/с.
При использовании нейтральной проволоки при перпендикулярном способе ее подачи относительно направления потока плазмы на однородность распыления влияет величина заглубления проволо-
48
ки lз в плазменной струе. При малых заглублениях (lз < dс/2) образуются крупные капли. При больших заглублениях (lз > dс/2) формируется поток более дисперсных частиц. Заглубление напрямую связано со скоростью подачи проволоки.
Рассматривая сравнительную эффективность воздействия плазмы при напылении порошком и проволокой, можно отметить следующее. В первом случае (использование порошковых материалов) эффективность во многом определяется конструкцией плазмотрона. При распылении проволоки теплофизика процесса в гораздо меньшей степени определяется конструктивными особенностями плазменного распылителя. В целом использование проволоки в качестве расходного материала имеет преимущества по эффективности энергетических показателей процесса напыления. Также процесс напыления протекает более стабильно, поскольку в нем участвует только расплавленная проволока.
Сопоставляя эффективный КПД нагрева нейтральной проволоки и проволоки-анода (т.е. долю тепла дуги, полученную проволокой), можно сказать, что во втором случае процесс более эффективен. КПД различаются почти в 5 раз. Причиной является различие источников нагрева проволоки: если проволока нейтральная, это теплота плазмы; если проволока – анод, это электроны тока.
ДГН. Для этого метода наибольшее значение имеет диаметр порошковых частиц и их плотность. В зависимости от вида материала используют следующие размеры порошковых частиц:
1)Ni, Co, Cu – 70 мкм;
2)Cr – 50 мкм;
3)Mo, Nb – 10–300 мкм;
4)Al2O3 и другие оксиды – 20 мкм;
5)карбиды – 5 мкм.
Завышенные размеры частиц не позволяют достичь достаточно высоких скоростей, поэтому адгезионная прочность покрытия получается низкой.
При использовании этого метода возникают трудности, связанные с дозированием и подачей порошка в ствол установки.
49
Смесь представляет собой аэрозоль, частицы распределяются в стволе неравномерно из-за сил гравитации, крупные и тяжелые фракции стремятся осесть в нижнюю часть канала ствола. Поэтому иногда применяют вертикальное расположение ствола установки.
Различают осевую и радиальную подачу; импульсную и непрерывную. Абсолютного преимущества не имеет ни один из способов.
Например, радиальная импульсная подача позволяет ввести порошок в заданное время в заданную точку, однако направление подачи не совпадает с направлением фронта волны, отсюда возникает неравномерность концентрации частиц по каналу ствола. Осевая подача дает равномерное распределение частиц, однако порошковое облако растянуто по длине канала.
В ДГН, как и в других методах, используется транспортирующий газ. Его расход также оказывает влияние на эффективность процесса. Здесь нужно отметить, что повышенный расход транспортирующего газа, стабилизируя подачу порошка, в то же время обедняет горючую смесь. При этом снижается энергообмен между теплоносителями и напыляемыми частицами.
Расход порошка может варьироваться в широких пределах от 1 до 12 кг/ч и определяется энергетическими параметрами установки.
Доза порошка не должна быть завышена, так как это приводит к неравномерному нагреву и ускорению частиц.
3.6. Параметры компонентов двухфазного напыляемого потока
ЭДМ. При подаче алюминиевой проволоки температура рабочей газовой смеси Тр.г = 1000…2000 К (при удельной мощности электрической дуги Wд = 3000…8500 кВт/кг).
При ЭДМ максимальное значение температуры рабочей газовой смеси возникает на границе электрической дуги. При дальнейшем движении газовой смеси ее температура значительно снижается.
То же самое можно сказать о температуре напыляемых частиц: их температура имеет максимум вблизи электрической дуги и затем уменьшается. Однако из-за высокой скорости потока рабочей газовой смеси частицы не успевают сильно остыть и попадают на напы-
50