
книги / Теория и технология нанесения газотермических покрытий
..pdfляемую поверхность в расплавленном состоянии. Температуру частиц повышают путем увеличения мощности дуги при постоянной производительности. С повышением среднемассовой температуры частиц увеличивается прочность сцепления покрытия с основой и плотность покрытия.
Скорость струи максимальна на срезе сопла (Vр.г = 300…350 м/с) и в пределах начального участка газового потока. Здесь же распыленные частицы получают максимальное ускорение. Скорость газового потока близка к звуковой и даже превышает ее.
В начальный участок входит фронт плавления подаваемого металла, здесь происходит его диспергирование.
Вблизи напыляемой поверхности скорость потока рабочей газовой смеси имеет значения порядка 50–150 м/с.
Энтальпия напыляемых частиц Нч = 2000…10000 кДж/кг. ГПН. При ГПН процесс напыления зависит от величины отно-
шения расхода кислорода к расходу горючего газа β (на практике β = 1…4), состава газового пламени на начальном участке струи, температуры пламени вблизи среза сопла. Скорость газопламенных струй определяется значением β, а также профилированием сопла и составляет 150–200 м/с. Длина высокотемпературной части газопламенной струи (150–250 мм) зависит от рода горючей смеси.
Температура распыляемого материала 2200 °С для порошков и 2700 °С для проволок.
Скорость частиц вблизи поверхности изделия 15–50 м/с. Газовое пламя на начальном этапе формирования имеет форму
полого конуса, расходящегося от сопла. Затем образуется сплошной поток разогретого газа. Струи разогретого газа подобны плазменным, но имеют значительно более низкие температуру, энтальпию
искорость.
Вдвухфазной струе происходит сложное химическое взаимодействие между компонентами: частицами напыляемого материала, горючими, окислительными и нейтральными газами, а также продуктами их взаимодействия. Кроме этого, так как напыление проводят в открытой атмосфере, в факел попадает воздух.
51
Содержанием кислорода регулируются теплофизические свойства струи.
Реакция горения в среде кислорода на один моль горючего газа: C2H2 + O2 = CO2 + H2O +1,265 МДж/моль.
Если в факел пламени попадает воздух, то согласно реакции содержание кислорода уменьшают. Свойства двухфазного потока регулируют также обжатием пламени воздухом.
ПН. Параметры плазменной струи и потока напыляемых частиц взаимосвязаны.
Сначала рассмотрим параметры плазменной струи. К основ-
ным из них, ответственным за параметры напыляемых частиц и состояние поверхности напыления, относятся температура Tп.с, скорость Vп.с, энтальпия Hп.с. Рассматривают среднемассовые значения этих параметров на срезе сопла и их распределение по оси струи и по ее сечению.
Плазменная струя является неизотермическим потоком. Это связано с тем, что при напылении в открытой атмосфере наблюдается выхолаживание струи вследствие инжекции холодного окружающего газа. Поэтому температура плазмы неоднородна как по оси, так и по радиальному сечению. Соответственно температуре изменяются и два других параметра струи – скорость и энтальпия.
Охарактеризуем параметры плазменной струи на срезе сопла:
1.Температура – один из главных параметров струи, она легко регулируется путем изменения мощности, подведенной к распылителю, расхода плазмообразующего газа, доли газа, участвующего
втеплообразовании. Температура плазменной струи на срезе сопла
Tп.с = (6…25)·103 К.
2.Энтальпия зависит от теплофизических свойств плазмообразующего газа. Среднемассовая энтальпия плазменной струи на срезе сопла Hп.с = 2…20 Дж/г.
3. Скорость струи изменяется в широких пределах (Vп.с = = 1000…1500 м/с). Она определяет скорость напыляемых частиц и, соответственно, время их нахождения в двухфазном потоке.
52
Распределение различных параметров тоже имеет примерно одинаковую зависимость. Вблизи среза сопла параметры изменяются мало. Чем больше расстояние от среза сопла, тем более размытым становится профиль распределения параметра.
К параметрам плазменной струи относятся также угол расхождения и длины начального и высокотемпературного участков струи. Стремятся первый параметр уменьшить, а второй увеличить. Этого добиваются, используя ламинарные струи.
Теперь рассмотрим параметры потока частиц:
1.Температура зависит от степени теплообмена между плазмой
ипорошком. Процесс теплообмена между напыляемыми частицами
иструей плазмы происходит за счет явлений теплопроводности, конвекции и излучения. Теплопроводность – это процесс переноса теплоты в твердом теле, неподвижных жидкости и газе. Конвекция – передача теплоты благодаря движению жидкости или газа. Лучистый теплообмен связан с распространением электромагнитных волн. Совокупность различных видов переноса называют сложным теплообменом.
Температура частиц в плазменном потоке, как правило, равна температуре плавления материала или значительно превышает ее. Но это не означает, что все частицы полностью расплавляются, некоторые не успевают расплавиться. Повышение температуры частиц приводит к увеличению адгезионной и когезионной прочности, хотя при очень высоких температурах создаются благоприятные условия для явлений испарения, сублимации и диссоциации, что отрицательно сказывается на протекании процесса.
2.Струя плазмы служит как для нагрева частиц напыляемого материала, так и для их разгона до требуемых скоростей.
Значение скорости частиц (Vч = 100…500 м/с) определяется действием различных факторов, основными из которых являются аэродинамическое сопротивление частиц, размер частиц, скорость плазменной струи, плотность частиц и плазмы.
Значения скоростей и температур отдельно взятых частиц меняются в зависимости от их положения в пятне напыления. Чем
53
мельче частицы, тем большее различие имеют параметры на периферии и на оси струи. То же самое относится и к плотности потока частиц.
При ПН рекомендуется осуществлять процесс напыления с отсечкой периферийных частиц.
ДГН. На состояние напыляемых частиц при методе ДГН оказывают влияние температура Тг.п, энтальпия Hг.п и скорость Vг.п газового потока внутри ствола, так как дульное пламя, образующееся на выходе из ствола, роли в нагреве частиц не играет.
Внутри ствола различают детонационную волну и следующую за ней горючую смесь – продукты распада волны. Они имеют следующие характеристики:
–волна: Тг.п = 4000…5700 К, Vг.п = 2000…3000 м/с;
–горючая смесь: Тг.п = 3000…4000 К; Vг.п = 850–1100 м/с.
О параметрах потока частиц следует сказать следующее. Вопервых, они имеют очень высокие скорости (800–1000 м/с). Это определяет высокое качество покрытия. Во-вторых, до момента соприкосновения с поверхностью напыления частицы имеют температуру ниже температуры плавления. В момент удара они дополнительно разогреваются выше температуры плавления за счет перехода кинетической энергии в тепловую. Коэффициент использования материала составляет 0,3–0,6.
Контрольные вопросы
1.Для чего необходимо подбирать параметры конструкции распылителя?
2.На что влияют геометрические параметры сопла?
3.Что влияет на энергетическую эффективность работы распылителя?
4.Каковы оптимальные конструктивные параметры распылителя при электродуговой металлизации?
5.Какие параметры влияют на процесс напыления при использовании метода газопламенного напыления?
6.Каковы особенности конструкции соплового устройства газопламенной горелки?
54
7.От каких параметров зависит эффективность процесса дето- национно-газового напыления?
8.Какиепараметрывлияют напроцессплазменногонапыления?
9.Какие конструкции электродов применяют при плазменном напылении?
10.Из каких материалов изготавливают электроды?
11.Как на формирование плазмы влияют параметры электрической дуги?
12.Какие энергетические параметры характеризуют режим работы распылителя при различных методах ГТН?
13.Как вид газов рабочей смеси влияет на процесс напыления?
14.Из каких условий выбирают дистанцию напыления?
15.Как влияют на процесс напыления параметры напыляемого материала и скорость его ввода?
16.Как меняется температура напыляемых частиц в ходе технологического процесса напыления?
55
ГЛАВА 4. МАТЕРИАЛЫ ДЛЯ НАПЫЛЕНИЯ ПОКРЫТИЙ
4.1. Классификация материалов для ГТН
Для напыления применяются следующие материалы [9, 11, 19]:
1)литая проволока (компактный металл);
2)порошки;
3)экструдированные прутки, стержни;
4)порошковая проволока;
5)эластичная проволока (представляет собой порошковую шихту, находящуюся внутри эластичной оболочки, которая сгорает без загазованности покрытий).
Проволоки применяются для ЭДМ, ГПН, ПН. Для ЭДМ проволока должна быть электропроводной, обезжиренной, очищенной от ржавчины, омедненной. Диаметр проволоки не более 2 мм.
Используются следующие виды проволок:
1. Стальная проволока Нп-45 для износостойких наплавок. После напыления твердость слоя составляет 40–42 HRC.
2. Нержавеющие проволоки марок Х13, 2Х13. Марку Х20Н80 используют для получения износостойких покрытий и при напылении подслоя для повышения адгезии.
3. Проволоки из бронзы или латуни для получения антифрик-
ционных покрытий. Особенно эффективно их использование при ЭДМ.
4.Алюминиевая проволока для нанесения покрытий на большие площади с целью защиты от атмосферной коррозии.
5.Молибденовая проволока. Очень часто она используется для формирования промежуточных подслоев покрытий и для получения износостойких покрытий.
Для напыления применяют следующие виды порошковых ма-
териалов:
1)порошки чистых металлов;
2)порошки различных химических соединений (карбидов, оксидов, нитридов);
56
3)механические смеси порошков (как чистых металлов, так
ихимических соединений);
4)экзотермические порошки;
5)порошковые композиционные сплавы:
а) сплавы металлидов, б) самофлюсующиеся порошковые сплавы,
в) порошки высоколегированных сталей, г) порошки легированных чугунов, д) порошки из сплавов цветных металлов;
6)плакированные композиционные порошки;
7)конгломерированные композиционные порошки. Далее рассмотрим некоторые порошковые материалы.
4.2. Порошки чистых металлов
Чистые металлы как материалы для напыления используют редко, так как они не обеспечивают заданный комплекс свойств покрытий.
Порошок железа Fe (размер частиц 40–60 мкм) применяют для восстановления неподвижных посадок корпусных деталей, чтобы восстановить номинальный размер. Твердость формируемого покрытия 150–180 НВ.
Порошок молибдена при использовании придает поверхности хорошие антифрикционные свойства (твердость 200–250 НВ).
Алюминиевые порошки используют для нанесения на крупногабаритные детали химического оборудования для защиты от атмосферной коррозии.
Применение хромовых покрытий ограниченно. Они используются в качестве коррозионностойких.
Покрытия из меди улучшают электропроводность и антифрикционные свойства основного металла.
Покрытия из вольфрама улучшают износостойкость и коррозионную стойкость металлов. Они имеют хорошую адгезию к керамическим материалам.
57

4.3.Композиционные порошки
Внастоящее время производится большое количество порошков из чистых металлов и химических соединений [21].
Перспективным направлением дальнейшего повышения качественных технических характеристик покрытий является применение смесей металлических и керамических порошков. Однако, поскольку компоненты такой порошковой смеси имеют различные фи- зико-механические свойства, например температуру плавления, могут возникать проблемы обеспечения высокого качества покрытий. Решением данной проблемы является использование композиционных порошков, которые представляют собой совокупность исходных компонентов, соединенных в каждой порошковой частице. Таким образом, каждая порошковая частица имеет одинаковые характеристики. Внутри композитной частицы компоненты четко разделены между собой границей раздела.
Композиционные порошки (КП) различаются по следующим критериям:
– структуре композитной порошковой частицы;
– методу получения порошка;
– особенностям взаимодействия компонентов композитной частицы при увеличении температуры;
– техническим характеристикам и назначению покрытия. Различные конструкции композитных порошковых частиц
представлены на рис. 4.1.
а |
б |
в |
г |
д |
е |
Рис. 4.1. Виды композитных порошковых частиц: а – плакированная; б, в – конгломерированная; г, д, е – смешанного типа
Плакированная композитная частица состоит из ядра основного материала, окруженного одним или несколькими слоями других ма-
58
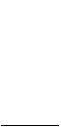
териалов. Конгломерированные композитные частицы делятся на гетеродисперсные (ядро из основного материала окружено более мелкими частицами других материалов) и гомодисперсные (они состоят из практически одинаковых по размеру частиц). В порошках смешанного типа используются комбинации плакированных
иконгломерированных частиц.
Взависимости от характера взаимодействия порошков при нагреве различают:
– термонейтральные порошки (при нагреве не меняют свои фи- зико-химические свойства);
– экзотермически реагирующие порошки (в них при нагреве протекают химические реакции за счет взаимодействия компонентов; при этом образуются покрытия, состав которых резко отличается от исходного состава).
Наиболее известные композитные порошки для ГТН приведены в табл. 4.1. Среди плакированных порошков преобладают порошки, плакированные никелем (кобальтом). Среди конгломерированных порошков преобладают порошки с нанесенным на поверхность частиц алюминием.
Таблица 4.1
Составы композитных порошков
Экзотермически реагирующие |
|
Термонейтральные |
|
||||
|
|
Ме- |
|
|
Ме- |
|
|
|
Алюмино- |
|
|
туго- |
Ме- |
|
|
Интерме- |
термиче- |
тугоплав- |
Керамика и |
|
плавкое |
твердая |
Прочие |
таллиды |
ские |
кое соеди- |
керметы |
|
соедине- |
смазка |
|
|
|
нение |
|
|
ние |
|
|
|
|
|
|
|
|
|
|
Al-Ni |
Al-NiO |
Ti-Si3N4 |
SiO2-Cr2O3 |
|
WC-Co |
Графит-Ni |
Алмаз- |
Ti-Ni |
Al-MoO3 |
Ti-SiC |
TiO2-Al2O3 |
|
WC-Ni |
CaF2-Ni |
Ni |
Al-Co |
Al-CuO |
Ti-B4C |
ZrO2-Ni |
Cr3C2-Ni |
MoS2-CuSn |
Алмаз- |
|
Si-Co |
|
Zr-Si3N4 |
Al2O3-Ni |
TiB2-Ni |
|
Cu |
|
NiCr-Al |
|
Al-NC |
ZrO2-Cu |
SiC-Cu |
|
|
|
Mo-Ni |
|
|
MgO-Ni |
Cr3C2-Mo |
|
|
|
FeCl-Ni |
|
|
Al2O3-Mo |
|
|
|
|
FeNi-Al |
|
|
|
|
|
|
|
|
|
|
|
|
|
|
59 |
К достоинствам КП относятся:
–формирование защитной пленки на основном материале час-
тицы (Ti-Ni, WC-Ni);
–возможность получения в покрытии мелкодисперсных струк-
тур (WC-BN-Ni, Al2O3-Ni);
–возможность экзотермического взаимодействия компонентов
(Ti-Si3N4, Ni-Al);
–возможность получения покрытий из компонентов, которые не могут самостоятельно использоваться в процессах напыления, например, из-за их низкой термостойкости (медь-SiC, графит-Ni, алмаз-Ni);
–улучшение физико-механических характеристик порошков, увеличение КИМ.
Недостатками КП можно считать следующее:
1) покрытия из КП имеют высокую гетерогенность по сравнению с покрытиями из сплавов;
2) в покрытии из КП процессы взаимодействия могут завершаться достаточно долго, поэтому при эксплуатации покрытия могут происходить объемные изменения и нарушения сплошности, отколы покрытий.
Композитные порошки имеют более высокую себестоимость по сравнению с аналогичными по составу механическими смесями. Но они находят все более широкое применение для нанесения покрытий на ответственные детали и узлы машин, которые работают в экстремальных условиях эксплуатации.
В зависимости от назначения в порошок вводятся различные металлические добавки (табл. 4.2).
|
|
Таблица 4.2 |
|
Добавки в композитных материалах |
|
|
|
|
№ п/п |
Назначение |
Добавка |
1 |
Защита ядра |
Al, Co, Ni |
2 |
Экзотермичность взаимодействия |
Al, B, Cr, Mo, Ni, Si, Ti |
3 |
Синтез износостойких фаз |
B, Cr, Ni, Ti, Fe |
4 |
Антифрикционные свойства |
Cu, Mo, Fe |
5 |
Пластификация покрытия |
Al, Co, Cu, Mo, Ni, Fe |
60