
книги / Теория и технология нанесения газотермических покрытий
..pdfГЛАВА 3. ПАРАМЕТРЫ ТЕХНОЛОГИЧЕСКОГО ПРОЦЕССА ГТН
3.1.Обзор параметров и их влияния на технологический процесс
На технологический процесс газотермического напыления влияют различные параметры, конструкционные и энергетические, связанные с внутренними и внешними процессами [4, 15].
3.1.1. Параметры конструкции распылителя
Параметры конструкции распылителя необходимо подбирать для следующих целей:
1)наиболее оптимального расхода энергии;
2)регулирования скорости потока и энтальпии частиц;
3)возможности регулирования плотности потока частиц. Наиболее ответственной деталью в распылителе является со-
пло. Его основные параметры – диаметр, длина, геометрический профиль. Указанные параметры сопла формируют скорость и плотность потока частиц. Кроме этого, конструктивные параметры определяют тепловой КПД распылителя:
η |
= Wт |
, |
(3.1) |
т.р |
W |
|
|
|
р |
|
|
где Wт – мощность источника теплоты (дуги, плазмы и т.д.), Вт; Wр – мощность, подводимая к устройству для распыления, Вт.
В зависимости от конструктивных параметров ηт.р = 0,3…0,9.
3.1.2.Энергетические параметры работы распылителя
На энергетическую эффективность работы распылителя влияют подводимая к распылителю мощность (Wр), состав газовой смеси и ее расход (Gр.г).
31
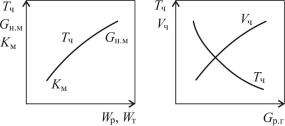
На нагрев распыляемых частиц, характеризующий производительность процесса, расходуется только часть тепловой мощности источника нагрева. КПД нагрева частиц
η |
= |
Нч |
= |
Нч |
, |
(3.2) |
|
|
|||||
н.ч |
|
Wт |
Wр ηт.р |
|
||
|
|
|
где Нч – энтальпия потока напыляемых частиц, Вт.
С увеличением Wт, Wр, ηт.р, ηн.ч возрастают производительность процесса (масса напыленного материала Gн.м), температура частиц
(Тч) и КИМ (Kм) (рис. 3.1, а).
аб
Рис. 3.1. Энергетические параметры работы распылителя
Расход распыляющего газа Gр.г определяет скорость газового потока. С его увеличением также увеличивается и скорость потока распыляемых частиц Vч. Однако необходимо учитывать, что при значительном расходе газа температура частиц Тч в потоке понижа-
ется (рис. 3.1, б).
3.1.3.Параметры распыляемого материала
иего подачи в рабочую зону
Кнаиболее значимым параметрам этой группы относятся физи- ко-механические свойства напыляемого материала, размеры и форма
расходных материалов (диаметр прутка или проволоки dпр), скорость подачи напыляемого материала Vподачи. Величина скорости подачи напыляемого материала определяет производительность процесса
напыления Gн.м.
32
По характеру ввода материала различают осевую и радиальную подачу. Осевая подача имеет преимущества, так как в этом случае увеличиваются температура и скорость частиц, компактность потока.
При ГТН параметры этой группы имеют следующие значения:
диаметр прутка dпр = 0,5…5 мм, скорость подачи Vподачи = 2…10 м/c (выбирают максимальную для заданных режимов); диаметр порош-
ковых частиц dпор = 10…200 мкм. Увеличение размера порошковых частиц требует увеличения мощности распылителя Wр. Мелкие порошки трудно вводить в распылитель, кроме того в процессе нагрева они окисляются на всю глубину. Скорость подачи Vподачи определяют
всоответствии с коэффициентом использования порошка (КИП) (0,3–3 г/с).
3.1.4.Параметры внешних условий напыления
Кпараметрам данной группы можно отнести дистанцию напы-
ления L, температуру изделия Ти, скорость перемещения распылителя V и другие.
При увеличении дистанции напыления происходит следующее:
– уменьшение температуры напыляемого материала в зоне соприкосновения с напыляемой поверхностью;
– уменьшение скорости потока частиц напыляемого материала
вмомент соприкосновения с напыляемой поверхностью;
–увеличение размеров пятна контакта напыляемого материала
снапыляемой поверхностью;
–увеличение качества напыляемого слоя из-за снижения риска перегрева материала в зоне напыления.
При увеличении температуры изделия Ти повышаются температуры в местах контакта частиц с напыляемой поверхностью. Рекомендуется прогревать изделие до температур порядка 250–300 °С.
Рекомендуемая скорость перемещения распылителя (V = = 0,1…0,5 м/с) позволяет осуществлять процесс напыления с наилучшими термодинамическими показателями, что позволяет формировать качественные покрытия с минимальными рисками неравномерности толщины и перегрева материала покрытия.
33
3.1.5. Параметры, характеризующие термодинамическое состояние струи
Параметры данной группы характеризуют термодинамическое взаимодействие между двухфазной струей напыления (смешанный поток газа и напыляемых частиц) и напыляемойповерхностью изделия.
Двухфазную струю напыления характеризуют следующие показатели:
1)Н, Т, V – энтальпия, температура и скорость струи рабочей газовой смеси, газопламенной или плазменной струи, газового потока внутри ствола;
2)Нч, Тч, Vч – энтальпия потока напыляемых частиц, его температура и скорость;
3)φс – угол расхождения струи;
4)φч – угол расхождения потока частиц;
5)плотность потока частиц.
Методы ГТН позволяют получить:
1) максимальную температуру газового потока Тmax =
=(2…20)·103 К;
2)максимальную скоростьгазового потокаVmax = 100…2000 м/с;
3)φс = 10…20°.
Далее рассмотрим указанные группы параметров для каждого из методов ГТН.
3.2. Конструктивные параметры
ЭДМ. Наиболее важными для данного метода ГТН являются форма и размеры сопла.
По форме сопла могут быть цилиндрические и комбинированные.
Для цилиндрических сопел оптимальный диаметр 4–6 мм. Для комбинированных сопел, состоящих из цилиндрической и расширяющейся конической частей, максимальный диаметр на выходе конической части сопла рекомендуется выбирать величиной 6–8 мм.
Цилиндрические сопла имеют недостатки по сравнению с другими конструкционными формами:
34
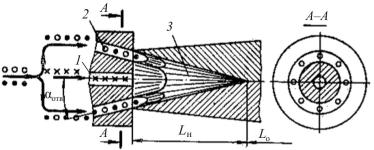
–снижается эффективная длина струи, падает распыляющая способность;
–формируется недостаточно широкое пятно контакта;
–газораспыляющая струя дорасширяется за пределами сопла (нерасчетный режим работы). При высоких скоростях при таком режиме возникают скачки уплотнения, сопровождаемые ударными волнами;
–проволока оказывает влияние на течение струи напыления, что приводит к более высокой турбулентности потока.
Длину сопла рекомендуется выбирать в интервале 30–50 мм. Рекомендуется выбирать угол скрещивания электродов ω = 30°.
При уменьшении значения этого угла происходит разделение потока частиц на две струи, а при увеличении возникают конструктивные сложности для осуществления распыления.
ГПН. На параметры процесса напыления при использовании метода ГПН оказывают влияние: диаметр основного сопла; диаметр вспомогательных отверстий на периферии сопла, угол наклона вспомогательных отверстий к оси основного сопла αотв (рис. 3.2).
Рис. 3.2. Схема соплового устройства газопламенной горелки: 1 – основное сопло; 2 – вспомогательные отверстия; 3 – пламя
Конструктивные параметры соплового устройства оказывают значительное влияние на термодинамические параметры струи.
ПН. На процесс напыления при использовании метода плазменного напыления оказывают влияние следующие параметры
(рис. 3.3):
35

–диаметр сопла dс;
–длина канала сопла lс;
–профилирование канала сопла;
–заглубление электрода в сопле lз;
–способ ввода напыляемого материала;
–характеристики электрода (диаметр dэ, угол заточки αэ, диаметр притупления dп);
–длина привязки самоустанавливающегося или фиксированного анодного пятна lп.
Рис. 3.3. Конструктивные параметры распылителя при ПН
В качестве материала электрода при плазменном напылении используют вольфрам (лантанированный или торированный). Стойкость вольфрамового электрода в значительной мере зависит от его формы. Диаметр рабочего электрода составляет от 4 до 60 мм.
Самой важной конструктивной составляющей плазмотрона является сопло.
От конструктивных параметров сопла зависят многие важные параметры процесса плазменного напыления, такие, как скорость потока плазмы, стабильность электрической дуги, тепловой КПД распылителя.
36
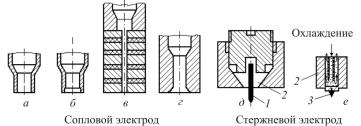
Рассмотрим наиболее распространенные конструкции электродных узлов (рис. 3.4):
а) сопло цилиндрической формы с относительно короткой длиной (порядка 10–30 мм). Такие электроды применяют в плазмотроне, имеющем самоустанавливающуюся электрическую дугу;
б) сопло цилиндрической формы, но на выходе имеется уступ, который служит для изменения характера течения струи;
в) сопло с межэлектродными вставками. Между электродом и пусковой секцией на низких напряжениях возбуждается электрическая дуга. Затем с помощью осциллятора дуга растягивается и горит между электродом и сопловой секцией. При этом мощность дуги повышается за счет увеличения напряжения в 2–3 раза, а увеличение напряжения дает возможность использовать газы с более высоким потенциалом ионизации. Кроме того, температура распределяется равномерно по длине канала сопла, т.е. происходит равномерный прогрев напыляемого материала. Благодаря такой разбивке сопла на секции происходит удлинение электрической дуги и формирование стабильного рабочего пятна;
г) сопло со сложным профилем, что позволяет получать ламинарные потоки, а также разгонять потоки плазмы до сверхзвуковых скоростей;
д) стержневой вольфрамовый электрод; е) стержневой циркониевый электрод.
Рис. 3.4. Конструкции электродов при ПН: 1 – вольфрамовая вставка; 2 – держатель электрода; 3 – циркониевая вставка
Поскольку стойкость сопла составляет от 10 до 50 ч, конструкция держателя должна обеспечивать его быструю смену.
37
Рассматривая конструкцию распылителя, следует отметить также необходимость высокой соосности электрода и сопла.
Диаметр сопла в основном оказывает влияние на скорость истечения плазменной струи и, соответственно, на скорость и температуру напыляемых частиц. Диаметр сопла 3–8 мм.
Одним из важнейших конструкционных параметров плазменного распылителя является длина канала сопла. Она выбирается из следующих соображений. С одной стороны, увеличение длины канала сопла снижает ηт.р. С другой стороны, увеличение длины дуги (опять же прямо зависящей от длины сопла) повышает ηт.р. Поэтому в основном все же стремятся максимально растянуть дугу, что приводит к использованию удлиненных сопел.
Для самоустанавливающихся дуг lс = (2…3)dс. В плазменных распылителях с фиксированной растянутой дугой lс = (5…10)dс.
Длину электрической дуги необходимо фиксировать для уменьшения пульсаций потока плазмы низкочастотного диапазона, что является частым явлением в случае самоустанавливающихся электрических дуг. Горение плазменной струи в канале сопла нестабильно, в дуговых плазмотронах возникают ее колебания, которые имеют периодический и непериодический характер. Нежелательными колебаниями являются низкочастотные пульсации потока плазмы, возникающие в результате износа электрода и наведенные электромагнитными силами со стороны источника питания. В моменты пульсаций, когда длина дуги минимальна, происходит снижение энергии потока плазмы. Это приводит к недостаточному разогреву частиц рабочего порошка, поскольку время нагрева соизмеримо со временем низкочастотной пульсации. Таким образом, фиксирование длины дуги позволяет устранять низкочастотные пульсации и улучшать качество покрытий.
Большое влияние на процесс плазмообразования оказывает заглубление электрода в сопло. При малых значениях lз резко сокращается ηт.р, таккак электрод является источником энергии дуги.
От вида подачи и места ввода материала зависят нагрев и формирование потока напыляемых частиц. В основном применяется ра-
38
диальная подача. Для достижения наибольших показателей КИМ и КПД необходимо осуществлять ввод рабочего порошка до анодной части сопла.
Различают следующие схемы ввода напыляемого материала
вплазмотрон:
1.Подача материала в зону горения дуги. Применяется для
наиболее тугоплавких материалов (Al2O3 и др.). Недостаток – возможность забивания канала сопла. Чтобы этого не происходило, система должна быть проточной, т.е. требуется равномерная подача порошка без пульсаций.
2.Подача материала внутрь канала сопла на небольшом удалении от среза сопла (3–5 мм). Используется для материалов неодинаковой степени плавления (порошок, проволока). Недостаток – заваривание канала и образование настылов на противоположной сторо-
не входного отверстия. Чтобы уменьшить наростообразование,
вканале сопла делают раструб на диаметр 8–10 мм.
3.Подача материала за срез канала сопла (перпендикулярно электроду или под небольшим встречным углом). Это наиболее рациональная схема, так как она исключает нарушение стабильности процесса из-за забивания канала сопла (зарубежные плазмотроны).
ДГН. К основным параметрам при использовании метода ДГН
относят диаметр ствола dст, длину ствола lст, форму ствола. Ствол изготавливается из цельнотянутых бесшовных труб из нержавеющей стали.
Диаметр ствола dст составляет 8–40 мм (наиболее часто 16–20 мм, с уменьшением этого параметра затрудняется детонационный взрыв). Длину ствола определяют из условия получения максималь-
ных скоростей частиц (lст = 1,2…2 м).
С уменьшением dст и lст уменьшается вводимая порция детонирующей газовой смеси.
Эффективность процесса связана с формой канала, его чисто-
той, отношением lст/dст, наличием форкамеры.
Скорострельность (14 выстрелов в секунду при dст = 25 мм) увеличивает эффективность процесса, производительность, снижает
39
проявления гравитационных сил. Конструкция дозирующих устройств оказывает влияние на стабильность процесса (необходима точность дозирования). Стремятся к системам непрерывного смесеобразования.
3.3. Энергетические параметры
ЭДМ. Применительно к методу ЭДМ наиболее важными параметрами, характеризующими энергетический режим работы распылителя, являются мощность электрической дуги Wд, расход и давление рабочего газа.
С увеличением мощности электрической дуги:
–увеличивается производительность;
–снижается КИМ вследствие увеличения потерь распыляемого материала из-за разбрызгивания и испарения;
–увеличивается адгезионная прочность, так как возрастает температура частиц.
Выбранная Wд определяет производительность и энтальпию по-
тока частиц.
Мощность Wд определяется напряжением и силой тока. Поскольку при плавлении электрода возможно возникновение электрических замыканий из-за коротких электрических дуг, необходимо выбирать такие напряжения, которые обеспечат стабильную работу.
Мощность дуги устанавливают путем регулирования силы тока. Если увеличивать напряжение, то это приведет к увеличению длины электрической дуги, что снизит интенсивность нагрева. При малых длинах электрической дуги электроды нагреваются за счет активных пятен дуги и эффективность распыления повышается.
Эффективный КПД нагрева проволоки
η |
= |
Wэ |
, |
(3.3) |
|
||||
н.п |
|
I U |
|
|
|
|
|
где Wэ – мощность, получаемая электродами, Вт; I – сила тока, А; U – напряжение, В; ток постоянный.
Эффективный КПД нагрева проволоки ηн.п зависит от напряжения дуги и колеблется в широких пределах от 0,35 до 0,9. Среднее
40