
книги / Технологии технического обслуживания и ремонта автомобилей
..pdf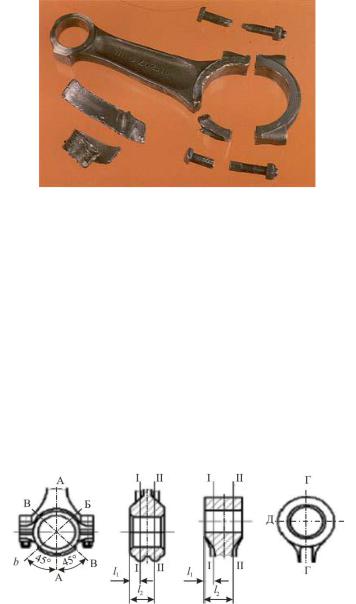
Рис. 4.7. Разрушение шатуна из-за излома болта
Порядок проведения дефектации шатуна и вывод о его состоянии:
1.Провести внешний осмотр детали, визуально исследовав каждый элемент – оценив состояние поверхностей, наличие трещин или изломов, состояние всех отверстий, резьбы, резьбовых соединений. Результаты осмотра занести в отчет.
2.Изучив визуально состояние элементов шатуна, необходимо провести замеры отверстий в головках. Измерение каждой головки провести в поясах I–I, II–II и двух взаимно перпендикулярных плоскостях А–А и Б–Б (рис. 4.8). Провести измерения отверстий шатуна. Результаты измерений занести в отчет
ввиде табл. 4.1.
Рис. 4.8. Порядок измерения шатуна
31
Допустимое значение овальности окружности отверстия шатуна 0,01–0,02 мм. Если разность диаметров отверстия в сечении А–А и в сечении Б–Б больше 0,02 мм, то можно говорить о наличии овальности. Если разность диаметров находится в пределах от 0 до 0,02 мм, то овальность отсутствует.
Допустимое значение конусности окружности отверстия шатуна 0,01–0,02 мм. Если разность диаметров отверстия в поясе I–I и в поясе II–II больше 0,02 мм, то можно говорить о наличии конусности. Если разность диаметров находится в пределах от 0 до 0,02 мм, то конусность отсутствует.
Значения диаметров определяются строго по приведенной схеме на рис. 4.8 с помощью поверенного микрометра [5].
Т а б л и ц а 4 . 1
Результаты измерений шатуна
№ |
Конструк- |
|
|
Размер, мм |
|
Конусность, |
||
тивный эле- |
|
|
|
|
|
|
||
п/п |
DI |
Оваль- |
DII |
Оваль- |
мм |
|||
|
мент |
|
|
ность, мм |
|
|
ность, мм |
|
|
DА |
DБ |
DА |
DБ |
|
|||
|
|
|
||||||
1 |
Отверстие |
|
|
|
|
|
|
|
|
под порш- |
|
|
|
|
|
|
|
|
невой палец |
|
|
|
|
|
|
|
|
|
|
|
|
|
|
|
|
2 |
Отверстие |
|
|
|
|
|
|
|
|
под шейку |
|
|
|
|
|
|
|
|
вала |
|
|
|
|
|
|
|
|
|
|
|
|
|
|
|
|
3. Провести проверку шатуна на изгиб. Для этого шатун укладывают на плиту (рис. 4.9), нажимают на нижнюю часть шатуна и проверяют с помощью щупа зазор между верхней головкой и плитой, затем нажимают на верхнюю часть шатуна и проверяют зазор между нижней головкой и плитой. Зазор не должен превышать: для верхней головки 0,10 мм, для нижней –
0,15 мм.
32
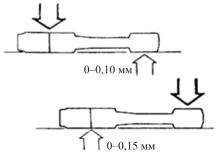
Рис. 4.9. Проверка шатуна на изгиб
4.По результатам органолептической диагностики и проведенных измерений определить отклонение параметров от рабочей нормы.
5.По каждому элементу шатуна распределить в одну из трех групп: норма, допустимое отклонение, брак.
6.По совокупности сгруппированных параметров определить в целом состояние исследуемого шатуна: норма, допустимое отклонение, подлежит ремонту, брак.
7. Результаты проведенных замеров и выводы занести в рабочую тетрадь.
Контрольные вопросы:
1.Из каких материалов изготавливают шатуны?
2.Назовите основные дефекты шатуна.
3.Назовите виды дефектов и способы их обнаружения.
4.При наличии каких дефектов шатун бракуется?
5.Опишите порядок дефектации шатуна.
6.Какие отклонения формы определяются при измерении отверстий шатуна?
7.Какой измерительный инструмент используется при дефектации шатуна и почему?
33
Лабораторная работа № 5 «ДЕФЕКТАЦИЯ ГОЛОВКИ БЛОКА ЦИЛИНДРОВ»
Цели: изучение техники дефектации головки блока цилиндров, приобретение практических навыков определения дефектов и их сочетаний, использования средств контроля и руководства по капитальному ремонту автомобилей, изучение характера работ, выполняемых дефектовщиком.
Задачи:
1.Изучить теоретический материал.
2.Изучить порядок проведения дефектации головки блока цилиндров.
3.Провести дефектацию и сделать вывод о техническом состоянии головки блока цилиндров.
Содержание работы:
Головка блока цилиндров (ГБЦ) – это верхняя часть блока цилиндров двигателя внутреннего сгорания. Она крепится на нем при помощи болтов или специальных шпилек. Основное назначение головки – контроль поступления топлива в рабочие цилиндры, обеспечение его сгорания, контроль и распределение потоков газов. Именно от точности регулировки отдельных узлов ГБЦ зависит мощность и устойчивость работы всего двигателя в целом [6].
Для различных силовых агрегатов выпускают головки блока цилиндров из чугуна или сплавов на основе алюминия. Именно алюминиевые ГБЦ устанавливаются на большинстве современных автомобилей, что позволяет несколько снизить общий вес силового агрегата.
Для двигателей с рядным расположением цилиндров применяется единая ГБЦ, а для V-образных силовых установок применяют отдельные головки на каждый ряд.
34
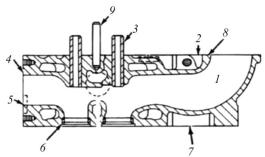
Корпус ГБЦ (картер) получают методом литья и последующей металлообработки (фрезерование, сверление). В теле изделия размещены каналы для циркуляции охлаждающей жидкости, маслопроводы для смазки основных узлов, отдельные камеры сгорания для каждого из цилиндров. Кроме того, в картере имеются отверстия для установки свечей зажигания или форсунок (для дизельных двигателей). По своей конструкции головка считается сложным агрегатом, включающим в себя несколько различных механизмов:
–газораспределительный механизм, обеспечивающий отвод отработанных газов. Клапаны системы газораспределения открываются в четкой последовательности в зависимости от этапов работы каждого отдельного цилиндра;
–привод газораспределительного механизма, обеспечивающий открывание клапанов в необходимый момент;
–площадки для крепления впускного и выпускного коллекторов, обеспечивающих подачу топлива и отвод отработанных газов.
Основные элементы ГБЦ представлены на рис. 5.1.
Рис. 5.1. Основные элементы головки блока цилиндров: 1 – впускной клапан; 2 – верхняя плоскость головки цилиндров (для установки прокладки крышки клапанов); 3 – направляющая втулка клапана;
4 – торцевая поверхность выхлопного канала; 5 – выпускной канал; 6 – седло клапана; 7 – нижняя (рабочая) плоскость головки цилиндров;
8 – торцевая поверхность впускного канала; 9 – шток траверсы
35
Кнесъемным элементам ГБЦ относят направляющие втулки и седла клапанов. Данные элементы обеспечивают герметизацию механизма газораспределения. Монтаж этих деталей осуществляется методом горячей опрессовки, выполнить его самостоятельно, тем более без специального оснащения, практически невозможно, особенно в условиях частного гаража.
Косновным дефектам ГБЦ относятся следующие:
–трещины на поверхности сгорания и на других участках головки;
–износ, повреждения поверхности сгорания;
–отклонения плоскостности поверхности сгорания;
–изменение толщины головки блока цилиндров;
–повреждение клапанов, седел, пружин, направляющих и вращателей клапанов.
Головка цилиндров имеет кольцевые уплотнения или уплотнительную прокладку вокруг отверстий каналов для системы охлаждения. Эрозия металла допустима в следующих местах:
–между кромкой отверстия канала системы охлаждения и внутренним диаметром кольцевого уплотнения (зона 24 на рис. 5.2);
–между уплотнительной прокладкой и наружным диаметром кольцевого уплотнения (зона 25 на рис. 5.2);
–между уплотнительной прокладкой и прокладкой головки цилиндров.
Эрозия недопустима в зонах 26 и 27, где кольцевое уплотнение или уплотнительная прокладка прилегает к плоскости головки цилиндров, как показано на рис. 5.2 и 5.3. Если в этих местах обнаружена эрозия, следует прошлифовать рабочую плоскость головки цилиндров.
36
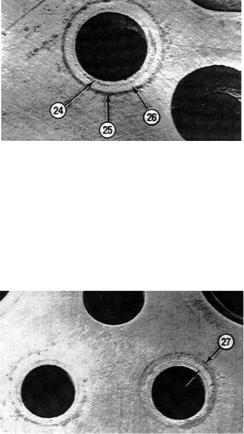
Рис. 5.2. Эрозия, допустимая в зонах 24 и 25 и недопустимая в зоне 26
Данная иллюстрация показывает пример допустимой эрозии – головку можно использовать повторно после шлифовки поверхности для удаления следов эрозии в зоне 27 контакта кольцевого уплотнения и поверхности головки цилиндров.
Рис. 5.3. Эрозия, недопустимая в зоне 27
Не допускаются повреждения седла распылителя (рис. 5.4). При восстановлении возможно шлифование седла, толщина удаленного слоя металла не должна превышать 0,3–0,4 мм. Минимальное расстояние от седла до нижней плоскости головки составляет 16–17 мм.
37
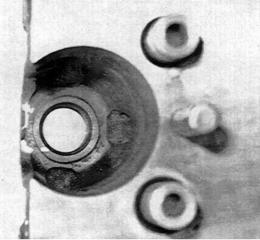
Рис. 5.4. Седло распылителя (для демонстрационных целей головка цилиндров была разрезана)
Осмотрите седло распылителя и убедитесь в отсутствии повреждений. Для проверки высоты головки цилиндров необходимо провести измерения. Для измерения высоты следует применять точное измерительное оборудование – калибр, микрометр или кронциркуль с микрометром.
Для восстановления исходных размеров контактных поверхностей можно применить метод напыления металла. Положите головку цилиндров на плоскость, куда выходит выпускной коллектор. Используя эталон толщины FT-1674 и поверочную планку, замерьте толщину головки в отверстии под болт, как показано на рис. 5.5.
Если эталон выступает над поверхностью головки цилиндров, головку нельзя использовать повторно. Эталон изготовлен исходя из минимальной толщины головки 111,51 мм
(4,390 дюйма).
38
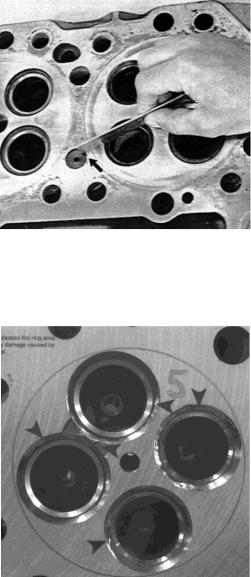
Рис. 5.5. Измерение высоты головки цилиндров
Не допускается выкрашивание металла и механические повреждения, как показано на рис. 5.6, 5.7.
Рис. 5.6. Значительные повреждения поверхностей между впускными клапанами
39
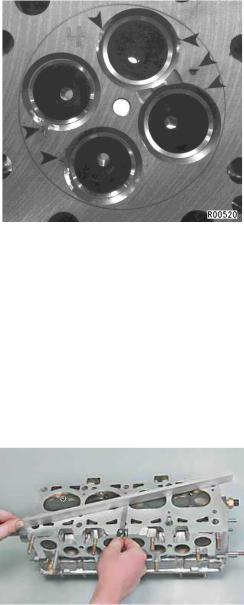
Рис. 5.7. Глубокие выбоины в поверхности и трещины
Для проверки плоскостности головки необходим специальный шаблон, но если его нет, то проверить нижнюю привалочную плоскость головки с достаточной степенью точности можно и при помощи широкой слесарной линейки. Прикладываем линейку по диагонали, ребром к плоскости головки (рис. 5.8). Убеждаемся в отсутствии зазора между ребром линейки и плоскостью головки. Зазор может наблюдаться как в средней части плоскости, так и по ее краям. Замер зазора проводим по обеим диагоналям набором плоских щупов.
Рис 5.8. Определение плоскостности ГБЦ
40