
книги / Технологии технического обслуживания и ремонта автомобилей
..pdfПример 2. Требуется из цилиндрической заготовки нарезать зубчатое колесо с 83 зубьями. Необходимо определить количество оборотов рукоятки универсальной делительной головки.
Вариант решения 1. Принимаем x = 80.
n = 40/x = 40/80 = 1/2 = 8/16.
Таким образом, обороты рукоятки фиксируются по окружности на лимбе с 16 отверстиями, а вспомогательный раздвижной сектор отмеряем на восемь отверстий.
i |
40(x z) |
|
40(80 83) |
|
40 3 |
|
3 |
|
60 |
|
a |
. |
|
|
|
|
|
|
|||||||
см |
x |
80 |
80 |
2 |
40 |
|
d |
|||||
|
|
Задача решена с помощью двух зубчатых колес a = 60 и d = 40, но так как знак передаточного отношения «минус», то нужно установить последовательно два промежуточных колеса. В данном случае делительный лимб будет вращаться навстречу рукоятке.
Вариант решения 2. Принимаем x = 84.
n = 40/x = 40/84 = 10/21.
Таким образом, обороты рукоятки фиксируются по окружности на лимбе с 21 отверстием, а вспомогательный раздвижной сектор отмеряем на десять отверстий.
i |
40(x z) |
|
40(84 83) |
|
40 1 |
|
10 |
|
2 |
5 |
|
|
40 |
25 |
|
a с |
. |
||
см |
|
x |
84 |
84 |
|
21 |
7 |
3 |
35 |
60 |
b d |
||||||||
|
|
|
|||||||||||||||||
|
Задача |
решена при |
помощи |
четырех |
зубчатых |
колес |
a = 40, b = 35, c = 25, d = 60. Число зубьев подобранных шестерен должно удовлетворять условию сцепляемости
(a + b) > c + (15 – 20); (c + d) > b + (15 – 20).
Пример 3. Требуется из цилиндрической заготовки нарезать зубчатое колесо со 107 зубьями. Необходимо определить
71
количество оборотов рукоятки универсальной делительной головки. Принимаем х = 105.
n = 40/x = 40/105 = 8/21.
Таким образом, обороты рукоятки фиксируются по окружности на лимбе с 21 отверстием, а вспомогательный раздвижной сектор отмеряем на восемь отверстий.
i |
40(x z) |
|
40(105 107) |
|
40 2 |
|
16 |
|
4 |
4 |
|
||||
см |
x |
105 |
|
105 |
21 |
3 |
7 |
||||||||
|
|
||||||||||||||
|
|
|
|
80 40 |
|
|
a с |
. |
|
|
|
|
|
|
|
|
|
|
60 70 |
|
|
|
|
|
|
|
|||||
|
|
|
|
|
b d |
|
|
|
|
|
|
Задача решена с помощью четырех зубчатых колес. Поскольку знак передаточного отношения «минус», вводим одно промежуточное колесо.
Задача на дифференциальное деление имеет несколько решений. Если не удалось подобрать сменные шестерни из комплекта головки, нужно задаться другим x и заново подсчитать
iсм.
Знак «плюс» передаточного отношения iсм показывает, что рукоятка и делительный лимб вращаются в одну сторону, а знак «минус» говорит о том, что рукоятка и делительный диск вращаются в разные стороны.
Дифференциальное деление возможно только при горизонтальном положении шпинделя.
Содержание работы:
Цели работы: изучение устройства универсальной лимбовой делительной головки, знакомство с методами настройки делительной головки для нарезки зубчатых колес, получение практических навыков по настройке делительной головки.
Задачи:
1.Изучить теоретический материал.
2.Изучить методы деления с помощью универсальной лимбовой делительной головки.
3.Провести расчеты.
72
Порядок выполнения работы:
1.Изобразить кинематическую схему делительной головки.
2.Выбрать вариант для расчета по указанию преподавателя (табл. 9.1).
3.Выполнить расчет делительной головки для непосредственного деления.
4.Выполнить расчет делительной головки для простого способа деления.
5.Выполнить расчет и зарисовать схему настройки гитары на дифференциальное деление.
6.По заданию преподавателя произвести настройку и обработку заготовки на вертикальном фрезерном станке 6Н82.
|
|
|
|
|
Т а б л и ц а 9 . 1 |
|
|
|
Варианты задания |
|
|
||
|
|
|
|
|
|
|
|
|
|
Способ деления |
|
||
|
|
|
|
|
|
|
Номер |
Непосредственное |
Простое |
|
Дифференци- |
||
варианта |
|
альное |
||||
|
|
|
|
|
||
|
|
|
|
|
|
|
|
Z |
Z |
Z |
|
α |
Z |
|
|
|
|
|
|
|
1 |
2 |
36 |
29 |
|
10°20´ |
43 |
|
|
|
|
|
|
|
2 |
4 |
18 |
28 |
|
14°30´ |
86 |
|
|
|
|
|
|
|
3 |
3 |
60 |
31 |
|
15°10´ |
94 |
|
|
|
|
|
|
|
4 |
8 |
30 |
32 |
|
16°30´ |
109 |
5 |
6 |
20 |
33 |
|
17°20´ |
111 |
6 |
12 |
120 |
34 |
|
19°30´ |
139 |
|
|
|
|
|
|
|
7 |
3 |
40 |
35 |
|
20°20´ |
141 |
|
|
|
|
|
|
|
8 |
24 |
90 |
36 |
|
30°30´ |
159 |
|
|
|
|
|
|
|
9 |
6 |
18 |
37 |
|
12°30´ |
161 |
|
|
|
|
|
|
|
10 |
8 |
36 |
38 |
|
14°40´ |
172 |
|
|
|
|
|
|
|
11 |
4 |
30 |
39 |
|
11°50´ |
173 |
|
|
|
|
|
|
|
12 |
2 |
20 |
40 |
|
21°20´ |
175 |
|
|
|
|
|
|
|
13 |
12 |
60 |
41 |
|
23°30´ |
179 |
|
|
|
|
|
|
|
14 |
6 |
90 |
42 |
|
22°30´ |
181 |
|
|
|
|
|
|
|
15 |
3 |
40 |
27 |
|
24°30´ |
187 |
|
|
|
|
|
|
|
73
Вариант выполнения работы выбирается из представленной таблицы согласно порядковому номеру студента в списке группы. При этом если студент 16-й по списку, то выбирается 1-й вариант и т.д.
Контрольные вопросы:
1.Назначение универсальной лимбовой делительной го-
ловки.
2.Основные узлы делительной головки.
3.Какой способ деления применяется наиболее часто?
4.Что такое характеристика делительной головки?
5.Для чего необходимы сменные зубчатые колеса гитары
УДГ?
6.Определение и назначение лимба.
7.Зачем нужен раздвижной сектор?
8.Что делать, если на лимбе нет числа отверстий, кратного количеству частей, на которые необходимо разделить заготовку?
9.На каких станках применяется УДГ при производстве зубчатых колес?
74
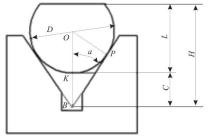
Лабораторная работа № 10 «ОПРЕДЕЛЕНИЕ ПОГРЕШНОСТИ БАЗИРОВАНИЯ»
Цели работы: привить студенту практические навыки по настройке фрезерного станка и закрепить теоретический материал по разделу курса «Точность обработки деталей».
Задачи:
1.Изучить теоретический материал.
2.Произвести настройку фрезерного станка на обработку партии деталей.
3.Обработать партию деталей и определить погрешность базирования.
Содержание работы:
При выполнении работы следует произвести фрезерова-
ние плоскости у цилиндрических валиков, установленных в призме. Как видно из рис. 10.1, при такой схеме обработки и базирования задан размер L, т.е. расстояние фрезеруемой плоскости до измерительной базы на образующей вала (точка K). Надо иметь в виду, что при изменении размера вала положение точки K в пространстве будет меняться.
Инструмент при обработке будет располагаться на таком расстоянии от призмы, что будет выдерживаться размер Н от плоскости до вершины призмы.
Рис. 10.1. Схема к расчету погрешности базирования
75
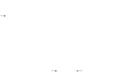
Размером С связаны измерительная и технологическая базы (точки K и В), его можно подсчитать из DОВР:
|
D |
1 |
|
|
|
C |
|
|
|
|
1 . |
2 |
|
|
|||
|
sin |
|
В размерной цепи, указанной на рис. 10.1, замыкающим звеном является размер L, так как он непосредственно не выдерживается, а получается в результате выполнения составляющих звеньев H и C .
Номинальные размеры связаны следующей зависимостью:
|
D |
1 |
|
|
|
|
L H C H |
|
|
|
|
1 |
; |
2 |
|
|
||||
|
sin |
|
|
при 2α = 90°
L H 0,297D;
при 2α = 60°
L H 0,500D.
Допуски этих размеров связаны уравнениями:
при 2α = 90°
L H 0, 207 D ;
при 2α = 60°
L H 0,500 D .
Действительные отклонения от номинала связаны уравнениями:
при 2α = 90°
L H 0, 207 D ;
при 2α = 60°
L H 0,500 D .
76
Из этих выражений видно, что погрешность выполнения размера L зависит от погрешности размера Н и погрешности базирования, которая определяется частью допуска на диаметр вала D.
Порядок выполнения работы:
Работа выполняется при установке валика на призме с углом 2α = 90°. Станок необходимо настроить так, чтобы погрешность базирования располагалась симметрично относительно среднего размера Lср (номинальный размер L задается препода-
вателем).
1.Измерить диаметры всех валиков, входящих в партию,
изаписать в табл. 10.1 их значение в соответствии с номером детали.
Т а б л и ц а 1 0 . 1
Результаты измерений
Размеры и отклоне- |
|
Номер детали |
|
|
ния размеров деталей |
|
|
|
|
1 |
2 |
3 |
и т.д. |
|
|
|
|
|
|
D |
|
|
|
|
|
|
|
|
|
L |
|
|
|
|
|
|
|
|
|
D |
|
|
|
|
|
|
|
|
|
L |
|
|
|
|
|
|
|
|
|
Определить средний диаметр в партии Dср и величину рассеивания Dб Dм , где Dб и Dм – соответственно наибольший и наименьший диаметры заготовок в партии.
2.Подсчитать погрешность базирования и выяснить, какая величина из допуска остается на остальные погрешности.
3.Взять любую деталь из партии, измерить ее диаметр Dx , определить отклонение Dx от Dcp ( x Dx Dср ) и подсчитать
соответствующую погрешность базирования L 0, 207 x . Определить поправку L (поправка – это погрешность, взятая с
77
обратным знаком). Подсчитать необходимый размер настройки станка LH Lср *L .
4.Закрепить выбранную деталь в призме с углом 2α = 90°
иметодом пробных стружек получить размер Lн, т.е. настроить станок так, чтобы погрешность настройки была минимальной.
5.При выполненной настройке произвести фрезерование плоскости у всех валиков в партии.
6.Измерить размер L у всех деталей и записать в табл. 10.1 в соответствии с номером детали.
7. Подсчитать отклонения D и L от их среднего размера
изаписать в таблицу.
8.Построить точечную диаграмму для D и L в порядке возрастания размеров.
9.Подсчитать средний размер в партии Lcp, поле рассеивания L и погрешность настройки H .
10.Составить отчет.
Контрольные вопросы:
1.Что называется базой в машиностроении?
2.Виды баз и их назначение.
3.Методы получения размеров при механической обра-
ботке.
4.Принципы постоянства и совмещения баз.
5.Причины возникновения погрешности базирования.
6.Что называется погрешностью базирования?
7.Методы уменьшения погрешности базирования.
8.Как рассчитать настроечный размер?
78
ЗАКЛЮЧЕНИЕ
Авторемонтное производство как любая производственная система должно непрерывно развиваться. Необходимым условием качественного восстановления работоспособности деталей, узлов и агрегатов транспортных и транспортно-технологических машин и оборудования является наличие на производстве специалистов высокой квалификации.
Современное высшее образование при подготовке выпускников должно быть ориентировано на формирование не только теоретических знаний, но и практических умений и навыков, что невозможно без соответствующей материальной и методической базы.
В результате успешного освоения лабораторных работ, представленных в данном практикуме, студенты приобретут:
–умение расчета технологических процессов изготовления деталей;
–навыки работы с измерительным инструментом;
–навыки обнаружения различных дефектов деталей транспортных и транспортно-технологических машин и оборудования;
–умение проводить расчеты, необходимые для регулировки сборочных единиц;
–навыки подготовки технической документации (дефектных ведомостей);
–навыки организации технологического процесса дефектовки на производстве.
79
СПИСОК ЛИТЕРАТУРЫ
1.Синельников А.Ф. Основы технологии производства и ремонта автомобилей: учебное пособие. – 2-е изд., стер. – М.:
Академия, 2013. – 320 с.
2.Бойко Н.И., Санамян В.Г., Хачкинанян А.Е. Механизация процессов технического обслуживания и ремонта наземных транспортно-технологических машин: учебное пособие / УМЦ ЖДТ. – М., 2015. – 332 с.
3.Иванов В.П., Ярошевич В.К., Савич А.С. Ремонт автомобилей: учебное пособие. – Минск: Вышэйшая школа, 2014. – 336 с.
4.Торопыгин С.И., Терских С.Е. Технология ремонта машин. Проектирование технологии ремонта узла: учебное пособие. – Красноярск: Изд-во КрасГАУ, 2012. – 167 с.
5.Юнусов Г.С., Михеев А.В., Ахмадеева М.М. Монтаж, эксплуатация и ремонт технологического оборудования. Курсовое проектирование: учебное пособие. – СПб.: Лань, 2011. – 156 с.
6.Карагодин В.И., Митрохин Н.Н. Ремонт автомобилей и двигателей: учебное пособие для студентов учреждений среднего профессионального образования. – М.: Академия, 2009. – 496 с.
7.Балихин В.В., Иванов Н.Ю. Ремонт машин: учебное пособие / СПбГЛГУ. – СПб., 2009. – 128 с.
8. Восстановление деталей машин: справочник / Ф.И. Пантелеенко, В.П. Лялякин, В.П. Иванов, В.М. Константинов; под ред. В.П. Иванова. – М.: Машиностроение, 2003. – 672 с.
9. Технология ремонта машин / Е.А. Пучин, В.С. Новиков, Н.А. Очковский [и др.]; под ред. Е.А. Пучина. – М.: КолосС,
2007. – 488 с.
10. Настройка делительной головки для нарезки зубчатых колес: метод. указания к лабораторной работе / сост.: Б.И. Калмин, М.С. Корытов. – Омск: Изд-во СибАДИ, 2012. – 12 с.
80