
книги / Технология производства проводов
..pdf
вания 30–70 м/мин. Отдающее устройство безынерционного типа имеет направляющий закрытый конус из органического стекла. Печь отжига снабжена встроенным парогенератором, трубчатая камера печи изготовлена из нержавеющей стали, среда отжига паровая. Число проходов проволоки через лаковый узел равно 12. Подача лака дозированная. Скорость эмалирования до 600 м/мин. Натяжение проволоки поддерживается в заданных пределах с помощью специальной фотоэлектрической системы. В агрегате используется приемное устройство сдвоенного типа.
Кроме того, используются эмаль-агрегаты типа NORE-МF итальянской фирмы «Сикме». Принцип работы их основных узлов мало отличается от принципа работы узлов ПГЗ 2/5.
Австрийская фирма MAG выпускает эмаль-агрегаты типа NEM для эмалирования проволоки диаметром 0,03–0,09 мм, основанные на принципе последовательного расположения эмальпечей и лаконаносящих устройств. Блок-схема эмаль-агрегата типа NEM показана на рис. 3.11.
Эмаль-агрегат такого типа обеспечивает одновременное эмалирование 40 ходов проволоки со скоростями 220 м/мин. Он имеет высокую производительность при сравнительно невысоких скоростях. Такой агрегат применяется также для производства эмалированных проводов с дополнительными защитными слоями или с комбинированной изоляцией из различных лаков.
Рис. 3.11. Блок-схема эмаль-агрегата типа NEM: 1 – отдающее устройство; 2 – печь отжига; 3 – лаковые ванны; 4 – эмаль-печи; 5 – приемное устройство; 6 – вентиляционная система
101
Вагрегате используется отдающее устройство фляйерного типа. Катушка неподвижно закреплена на горизонтальной оси,
асматывание проволоки осуществляется с помощью вращающегося легкого поводка – фляйера – через щеку катушки.
Агрегат имеет печь отжига длиной 1,6 м на все 40 ходов проволоки и лаконаносящее устройство валикового типа с канавками. Защитная среда от окисления проволоки – водяной пар. Над каждой канавкой расположена стальная пластинка, снимающая излишек лака. После лаконаносящего устройства расположены калибрующие устройства из фетра или замши. Толщина покрытия определяется давлением на калитр прижимной металлической пластинки.
Эмаль-печь снабжена устройством каталитического сжигания отходящих газов. Температура в каждой печи может быть различной, так как каждая печь имеет отдельное терморегулирующее устройство. В агрегате используется приемное устройство сдвоенного типа.
Внастоящее время фирма MAG для производства эмалированных проводов диаметром от 0,01 до 0,07 мм выпускает эмаль-агрегаты типа HS, имеющие традиционную конструкцию
(табл. 3.5).
Таблица 3 . 5
Характеристики эмаль-агрегатов фирмы MAG
Эмаль-агрегат |
Диаметрэмалированной |
Скорость |
Число |
|
проволоки, мм |
эмалирования, м/мин |
проходов |
HSO |
0,01–0,025 |
180–400 |
20 |
HSI |
0,02–0,07 |
500–1100 |
24 |
Управление эмаль-печью осуществляется с помощью микропроцессоров.
102
3.8.2. Агрегаты для эмалирования проволоки диаметром 0,05–0,45 мм
На отечественных заводах эмаль-агрегаты типов ПГЗ5/15, NORE-128, NORE-192АБ используются для эмалирования проволоки диаметром 0,05–0,14 мм, а агрегаты ПГЗ 10/30, NORE-192Л – для эмалирования проволоки диаметром 0,08–0,29 мм.
|
|
|
|
|
Таблица 3 . 6 |
|
|
Характеристики отечественных эмаль-агрегатов |
|||||
|
|
|
|
|
|
|
|
|
Диаметр |
Коли- |
Скорость |
|
|
Эмаль- |
Исполнение |
эмалирован- |
чество |
эмалиро- |
Метод |
|
агрегат |
эмаль-печи |
ной прово- |
ходов |
вания |
эмалирования |
|
|
|
локи, мм |
|
|
|
|
ЭТ-8 |
Гориз. |
0,05–0,09 |
2 |
13–40 |
Фетровыеобжимы |
|
|
|
|
|
|
иликалибры, |
|
М-24 |
Верт. |
0,1–0,29 |
24 |
12–36 |
||
адлямасляных |
||||||
|
|
|
|
|
||
С-24 |
Верт. |
0,2–0,41 |
24 |
8–24 |
||
лаков– погружение |
Рассмотрим агрегат NORE-192. Он имеет 12 проходов, 16 ходов. Скорость эмалирования до 300 м/мин. В отдающем устройстве безынерционного типа катушки расположены вертикально. Циркуляционная система лакоподачи имеет фильтр для очистки лака. В агрегате могут быть установлены лаковые узлы двух типов: с роликовыми калибрами, фетровыми обжимами. Каталитическое устройство агрегата снабжено терморегулятором для включения вспомогательных нагревательных элементов, а также системой аварийной сигнализации. В случае превышения допустимой температуры в зоне после каталитической плиты температура газов не должна быть ниже 340 °С, так как при этом будет происходить неполное сгорание паров растворителей и быстрое загрязнение каталитических элементов. Температура катализатора не должна превышать 600 °C, в противном случае каталитические элементы могут выйти из строя. Длина
103
камеры эмаль-печи 2,5 м. Имеются две печи отжига на восемь ходов каждая. В настоящее время фирма «Сикме» выпускает более совершенные эмаль-агрегаты типа NEM, предназначенные для эмалирования проволоки диаметром 0,25–0,8 мм. Они имеют различные модификации: число ходов от 6 до 12, число проходов на каждый ход 6–14, общее количество проволок в печи 60–144.
Основным преимуществом эмаль-агрегатов типа NEM является более совершенная эмаль-печь, где применяется как электрический, так и газовый нагрев. Фирма MAG (Австрия) выпускает эмаль-агрегаты последнего поколения типа HN (табл. 3.7). Эмалирование совмещено с волочением проволоки.
Таблица 3 . 7
Характеристики агрегатов типа HN
Марка |
Диаметрэмалирован- |
Скоростьэмали- |
Число |
Число |
агрегата |
ной проволоки, мм |
рования, м/мин |
ходов |
проходов |
HN 2А |
0,05–0,15 |
250–750 |
8 |
16 |
HN 2В |
0,08–0,2 |
300–500 |
8 |
16 |
HN 4 |
0,2–0,7 |
50–220 |
8 |
12 |
Советско-итальянская фирма Camtek выпускает горизонтальные агрегаты типа НЕ (например НЕ-1000/8), предназначенные для эмалирования проволоки диаметром 0,2–0,8 мм со скоростью 44–175 м/мин.
В эмаль-печи зона испарения растворителя состоит из двух участков нагрева. В зоне полимеризации эмалируемая проволока и воздух движутся в противоположных направлениях. Эмальпечи снабжены устройством каталитического сжигания газов и рекуперации тепла. Лак на проволоку наносится с помощью как калибров, так и фетров. В агрегате используется приемное устройство сдвоенного типа, имеется волочильная приставка.
Рассмотрим горизонтальный агрегат HN4/N-8/8+4D. Его главные показатели представлены в табл. 3.8. Общий вид горизонтального эмаль-агрегата представлен на рис. 3.12.
104
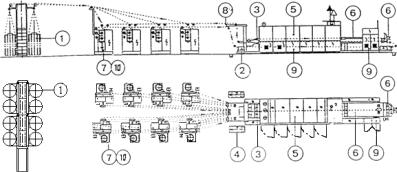
|
Таблица 3 . 8 |
||
|
Основные параметры эмаль-агрегата HN4/N-8/8+4D |
||
|
|
|
|
№ |
Показатели |
Величины |
|
п/п |
|||
|
|
||
1 |
Диаметрзаготовки, мм |
1,269–1,4 |
|
2 |
Диаметрэмаль-проводов, мм |
0,25–0,7 |
|
3 |
Количествоходов |
8 |
|
|
|
|
|
4 |
Количествопроходов |
12 (8+4) |
|
|
|
|
|
5 |
Скоростьэмалирования, м/мин |
0–280 |
|
|
|
|
|
6 |
Длинакамерыпечи, м |
4 |
|
7 |
Волочильныеприставкис числомтяговыхшайб (max) |
9 |
Рис. 3.12. Общая схема эмаль-агрегата HN-4: 1 – отдающее устройство (катушки, контейнеры); 2 – подготовка провода, отжиг; 3 – лаковый узел; 4 – бак эмаль-лака, система подачи эмаль-лака;
5 – эмаль-печь; 6 – охладитель провода, отклоняющие ролики; 7 – волочильная приставка; 8 – парафиновый узел; 9 – распредшкаф; 10 – приемное устройство
105
3.8.3. Агрегаты для эмалирования проволоки диаметром 0,4–2,5 мм
Фирма «Сикме» выпускает целую серию вертикальных эмаль-агрегатов, рассчитанных на различное число эмалируе-
мых проволок (80, 96, 112, 128, 14, 155, 160).
Основные узлы этих агрегатов идентичны, поэтому для примера рассмотрим эмаль-агрегат VRE-144. Агрегат типа VRE-144 предназначен для эмалирования медной проволоки диаметром 0,3–1,1 мм, имеет 24 хода, 6 проходов. Скорость эмалирования до 70 м/мин. Высота агрегата 11 м, длина 12,2 м. Используется циркуляционная система подачи лака. Метод наложения лака – неразъемные калибры. Камера печи выполнена из нержавеющей стали, нагреватели закрытые. Масса проволоки на отдающих катушках около 300 кг. В печи отжига осуществляется принудительная циркуляция пара, что обеспечивает равномерную температуру по ширине и длине камеры.
Эмаль-агрегаты типа ПГЗ 30/110 (венгерского производства) широко используются для эмалирования проволоки диаметром 0,3–1,1 мм (рассчитаны на 24 хода при эмалировании в 6 проходов), а эмаль-агрегаты ПГЗ 30/300 – для эмалирования проволоки диаметром 0,3–1,1 мм (12 ходов, 8 проходов). К числу наиболее совершенных эмаль-агрегатов относятся эмальагрегаты фирмы MAG. Характерная их особенность – вертикальное расположение печей отжига и оригинальная конструкция эмальпечей. Эмаль-агрегаты рассчитаны на эмалирование проволоки диаметром 0,3–1,6 мм в 13 проходов, снабжены волочильной приставкой.
У агрегатов ВЕ печь отжига и эмаль-печь расположены параллельно, у агрегатов ВЗЭТ – последовательно. Отожженная проволока охлаждается водой и затем сушится воздухом. Совет- ско-итальянская фирма Camtek выпускает вертикальные эмальагрегаты типа VE (например VE-1300/8). Число ходов 4–12, число проходов 8–14, скорость эмалирования 6–105 м/мин. Для
106
эмалирования проволоки прямоугольного сечения от 3,1 до 62,5 мм2 применяют агрегаты типа VREGP-36 фирмы «Сикме». Агрегат имеет 4 хода, 9 проходов. Скорость эмалирования от 3,6 до 12 м/мин. Лак накладывается на проволоку при помощи калибров. Масса проволоки на отдающей катушке 600 кг. Высота агрегата 12,3 м. Приемные катушки имеют индивидуальные тяговые устройства на каждый ход.
3.8.4. Устройство катализаторов
Поскольку используемые для эмалирования лаки содержат токсичные растворители, особым способом очистки отходящих газов является каталитическое сжигание, в результате чего возникают СО2 и Н2О. В качестве катализаторов используются либо благородные металлы (платина, палладий), либо оксиды металлов (оксид меди, оксид хрома и др.). Обычно реакция сгорания органических веществ протекает при температуре порядка 400 °С. В катализаторах активный металл или его оксид наносится на металлическую или керамическую подложку с большей поверхностью. Каталитическому сжиганию не могут подвергаться отходящие газы, которые содержат агрессивные пары ртути и ее соединений (свинца, цинка), выводящие катализатор из строя.
Современные электронные агрегаты оснащены устройством каталитического сжигания газов. В эмаль-агрегатах первого поколения таких устройств нет. Наиболее часто применяются цельнометаллические катализаторы, представляющие собой пакеты плоских проволок из нихрома или жаростойких сплавов, на поверхность которых нанесено палладиевое или платиновое покрытие. Масса нанесенного палладия составляет 0,3–0,5 % массы катализатора. При прохождении катализатора температура отходящих газов должна быть не меньше 400 °С и не больше 600 °С. Важным параметром катализатора является его сопротивление потоку проходящих газов. Для отечест-
107
венного каталитического элемента это сопротивление не должно быть больше 49 Па.
При сочетании углеводородов высвобождается большое количество тепла и температура газов, проходящих через катализатор, повышается. Ресурс работы катализатора примерно ра-
вен 12000–15000 ч.
Эмаль-агрегаты первого поколения, не имеющие циркуляции воздуха в эмаль-печи, снабжены установками дожигания газов. Их цель – максимально возможная очистка газов и последующий выброс их в атмосферу. В этих случаях повторное использование тепла не предусматривается.
В последние годы требования к предельно допустимым концентрациям вредных веществ в атмосфере резко ужесточены. Поэтому для достижения необходимой степени очистки эмаль-агрегаты дооборудованы специальными установками (вторая ступень дожигания). Эти установки представляют собой короба с дополнительно установленными элементами и электрическими нагревателями, через которые отсасывается смесь газов после первой ступени каталитического дожигания. Для дополнительного нагрева газов требуется значительный расход электроэнергии, так как обычно перед второй ступенью дожигания газы охлаждаются до температуры 300–500 °С.
Существует комбинированный адсорбционно-каталити- ческий способ очистки отходящих газов, который обеспечивает степень очистки не менее 98 %. Он основан на адсорбции органических примесей гранулированным катализатором-адсорбен- том и последующем каталитическом окислении адсорбента в псевдоожиженном слое. Катализатор-адсорбент отводится из зоны очистки в зону регенерации, где содержащиеся в нем примеси обезвреживаются и одновременно осуществляется регенерация сорбента в псевдоожиженном слое при температуре 250–450 °С. Регенерация производится воздухом – окислителем, который одновременно является и псевдоожижающим агентом.
108

Если возникает необходимость (например, эмаль-цех находится в городе, роза ветров неблагоприятна и др.), то используется третья ступень очистки, при которой все газы, отходящие из цеха, собираются в один газопровод и затем сжигаются или подвергаются специальной очистке.
3.9. ОСОБЕННОСТИ ЭМАЛИРОВАНИЯ ПРОВОДОВ ИЗ РАСПЛАВА СМОЛ
Требования к защите окружающей среды с каждым годом ужесточаются, поэтому перспективным является использование составов без растворителей.
Как мы уже отмечали, в отечественной практике широко используется полиэфирная смола ТС-1. Эта смола получена в результате переэтерификации смолы лавсан в присутствии глицерина с добавлением окиси свинца или окиси магния. Структурная формула элементарного звена смолы ТС-1 имеет вид
Вязкотекучее состояние смолы ТС-1 достигается расплавлением пленкообразующего вещества. Полученные эмаль-прово- да по своим свойствам идентичны проводам с изоляцией на основе полиэфирных лаков типа ПЭ-943 или ПЭ-939. Смолу нагревают до температуры 180–185 °С. Температурный индекс проводов равен 130 °С. Если применять полиэфирциануратимидную смолу, то получатся провода марки ПЭЦИ-РС с температурным индексом 155 °С. Наложение смолы ПЭЦИ-РС производится при температуре 160–170 °С.
Так как расплавленная смола имеет большую вязкость, чем лак, то при эмалировании в калибре возникают значительные силы трения. При высоких скоростях эмалирования сила
109
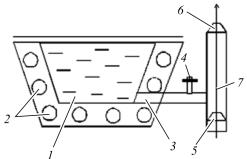
трения приводит к вытяжке или обрыву проволоки. При эмалировании из расплава смол максимальная скорость эмалирования ограничивается не процессами, происходящими в печи, а процессами нанесения расплава из смолы на проволоку. Схема эмалирования проволоки из расплава смолы показана на рис 3.13.
Рис. 3.13. Схема эмалирования проволоки из расплава смолы: 1 – ванна; 2 – нагреватели; 3 – канал для подачи смолы;
4 – вентиль для регулирования количества смолы; 5 – входной калибр; 6 – выходной калибр; 7 – проволока
В ванну 1 загружается измельченная смола. В стенки ванны вмонтированы электронагреватели 2, температура в ванне измеряется термопарой и поддерживается в нужном диапазоне. Расплав смолы через канал поступает в узел нанесения. Количество смолы регулируется вентилем 4. Узел нанесения смолы состоит из входного калибра 5 и выходного калибра 6. Калибр 5 предотвращает вытекание смолы из узла, а калибр 6 обеспечивает необходимую толщину покрытия на проволоке. Недостаток метода – низкая скорость эмалирования. Для ее увеличения необходимо уменьшить силу трения, возникающую в выходном калибре. Уменьшить силу трения можно двумя путями:
–снизить вязкость расплава за счет повышения его темпе-
ратуры;
–создать в узле нанесения тянущую силу, способную компенсировать силу трения.
110