
книги / Технология производства проводов
..pdf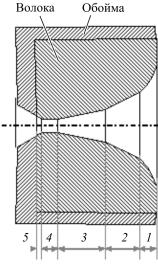
оборудованы различными механическими или электромагнитными устройствами для автоматического регулирования скорости вращения приемной катушки в процессе ее заполнения.
В последнее время нашли применение устройства для непрерывного приема проволоки (сдвоенные приемники).
Непрерывный прием может производиться и в контейнер (бочку). Проволока проходит через специальное устройство – головку, с которой витки свободно падают по одному в контейнер. Когда контейнер заполнен, головка перекрывается и витки не падают в контейнер.
1.11. ВОЛОЧИЛЬНЫЙ ИНСТРУМЕНТ
Основным инструментом для осуществления деформации при волочении является волока (рис. 1.12). Важнейшая часть волоки – отверстие заданной формы (волочильный канал).
|
|
Входная зона, или входная |
|||
|
|
распушка 1, канала предназначена |
|||
|
|
для облегчения ввода протягиваемой |
|||
|
|
проволоки в волоку и предупрежде- |
|||
|
|
ния задирания металла при контакте |
|||
|
|
его с краем волочильного канала. |
|||
|
|
Смазочная воронка 2 служит для |
|||
|
|
обеспечения поступления |
смазки |
||
|
|
в канал волоки. Длина ее вместе |
|||
|
|
с входной зоной равна 0,8–1,2 диа- |
|||
|
|
метра калибрующей зоны. Угол |
|||
|
|
смазочного конуса 45°. Рабочий |
|||
|
|
конус 3 – основная часть канала, в |
|||
|
|
котором |
осуществляется |
процесс |
|
|
|
деформации. Угол рабочего конуса |
|||
Рис. 1.12. |
Волока |
16–20° – для меди, 24–26° – для |
|||
алюминия. |
Калибрующий поясок 4 |
||||
|
|
51
обеспечивает заданные размеры проволоки. Длина калибрующего пояска принимается в пределах 20–65 % его диаметра. Выходная распушка 5 предназначена для устранения задираний металла, возникающих при контакте его с краями волочильного канала.
Для волочения проволоки применяются в основном монолитные волоки. В процессе волочения волока подвергается сильному давлению изнутри и может разрушиться, если не имеет достаточно прочной опоры снаружи. Роль такой опоры играет металлическая обойма, в которую крепится волока.
К характеристикам волочильного инструмента относятся: материал инструмента и его механические свойства, геометрия рабочей поверхности, наружная форма волоки и устройства для установки и крепления инструмента.
Для изготовления волок применяют материалы, обладающие высокой твердостью, износостойкостью, антикоррозийной стойкостью, хорошей полируемостью.
Для производства волок в основном используются металлокерамические сплавы, естественные и искусственные алмазы, некоторые марки стали.
Металлокерамические сплавы состоят из 90–98 % карбида вольфрама и 2–10 % кобальта, который цементирует карбид и обеспечивает однородность смеси всех компонентов. Металлокерамические сплавы по твердости близки к алмазу (88–90 HRC), а кобальт придает сплаву требуемую вязкость.
Для волочения проволоки диаметром менее 0,3 мм применяются алмазные волоки. Это необходимо, так как при волочении тонкой проволоки канал волок из металлокерамических сплавов быстро изнашивается и обеспечить точный размер проволоки невозможно.
Для изготовления обойм используется сталь или латунь. Для придания каналу волоки надлежащих размеров и фор-
мы, а также для получения высокого класса чистоты поверхности этого канала волоки подвергаются шлифовке. Изготовление или перешлифовка волок относится к числу наиболее ответственных
52
процессов. Обработке подвергаются как новые волоки, так и волоки, бывшие в употреблении.
После шлифовки производится доводка, т.е. механическая обработка канала с целью придания ему точных размеров, и полировка – получение гладкой поверхности рабочего канала.
Технические неграненые алмазы используются для изготовления волок лишь в отдельных случаях. В основном кабельные заводы получают заготовки алмазных волок. Эти заготовки сначала подвергаются огранке. После огранки алмазы центруются обычно на глубину 1/3 толщины камня. Затем производится их сверление и шлифовка на специальных станках при помощи притиров (иголок), на концы которых нанесена алмазная пудра. Угол заточки притиров последовательно изменяется, благодаря чему получается радиальная форма волочильного канала. После сверления производится подрезка, т.е. разделка выходной зоны волоки с обратной стороны камня.
1.12. ОТЖИГ МЕДНОЙ И АЛЮМИНИЕВОЙ ПРОВОЛОКИ
Одной из важнейших операций, применяемых при волочении, является отжиг. За счет деформаций при волочении структура и пластические свойства металла изменяются, происходит его упрочнение, или «наклеп», зерна металла измельчаются, вытягиваются в направлении волочения, т.е. образуется текстура. При достижении определенной степени деформации металл теряет пластичность, и волочение его становится невозможным. Одновременно снижается электропроводность металла. Для снятия «наклепа» и получения мягкой проволоки производится отжиг, термическая обработка металла, заключающаяся в нагреве его до определенной температуры, выдержке при этой температуре в течение заданного времени и последующем охлаждении до комнатной температуры.
53
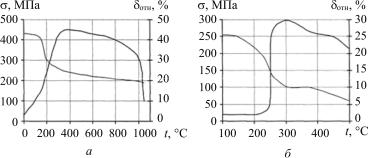
Отжиг как меди, так и алюминия происходит особенно интенсивно при переходе температуры отжига через определенную границу.
Как следует из показанных на рис. 1.13 зависимостей, для каждого металла, особенно для алюминия, имеется узкий температурный интервал, в котором происходит резкое изменение механических параметров.
Рис. 1.13. Зависимость временного сопротивления разрыву и относительного удлинения медной (а) и алюминиевой (б)
проволоки от температуры отжига
Температура отжига меди находится в пределах 450–650 °С, алюминия – в пределах 300–400 °С. Чем ниже температура отжига, тем больше должна быть выдержка при этой температуре с целью обеспечения качественного отжига. Длительный отжиг при низких температурах обеспечивает равномерность прогрева и лучшее качество, однако производительность оборудования в этом случае снижается.
Так как при температурах отжига поверхность медной проволоки на воздухе окисляется, то отжиг производится в защитной атмосфере (водяной пар, углекислый газ) или в вакууме. Отжиг алюминиевой проволоки ведется без защитной атмосферы.
По принципу работы отжигающие устройства можно разделить на устройства периодического и непрерывного действия.
54
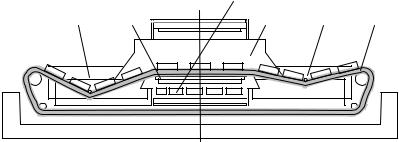
К нагревательным устройствам непрерывного действия относятся конвейерные печи с водяным затвором и установки совмещенного отжига с волочением. Для отжига проволоки из меди применяются конвейерные печи с водяным затвором (рис. 1.14).
|
|
2 |
|
|
5 |
3 |
1 |
5 |
4 |
Рис. 1.14. Схема печи отжига ОКБ-3003
Скорость конвейера 0,1–0,2 м/мин, производительность такой печи 2 т/ч. Отжигаемая проволока, пройдя водяной затвор 5, исключающий попадание воздуха в рабочее пространство печи, поступает в рабочую камеру 1, футерованную огнеупорным кирпичом 2. Под печи состоит из литых жароупорных плит 3, по которым движется конвейер 4 с бухтами отжигаемой проволоки. Через выходной водяной затвор подается вода для охлаждения отожженной проволоки.
Кроме вышеназванных получили распространение нагревательные устройства, монтируемые непосредственно на волочильных машинах, – приставки совмещенного отжига. Они уменьшают трудоемкость производства проволоки, повышают производительностьтруда, увеличиваютсъем продукции сединицыплощади.
К устройствам периодического действия относятся камерные, элеваторные и колпаковые печи.
Обычно в качестве атмосферы в таких печах используется вакуум (53 кПа). Все печи имеют приспособления для загрузки и выгрузки металла и систему автоматического регулирования
55
температуры. Наиболее распространены колпаковые печи. Бухты проволоки общей массой примерно 1 т загружаются в муфель на тележке и после откачки воздуха помещаются под колпак. Отжиг производится при температуре 450–520 °С в течение 5–15 ч.
Отжиг проволоки, предназначенной для изготовления эмалированных проводов, осуществляется на установках непрерывного отжига, совмещенных с эмаль-печью.
1.13. КАЧЕСТВО ПРОДУКЦИИ И ВИДЫ БРАКА
Брак прокатного и волоченого металла классифицируется в зависимости от характера дефектов, которые можно разделить на следующие группы:
–неправильность профиля – овальность, заусенцы, прирез, пояски, волнистость, серповидность на заготовках шинной
иколлекторной меди;
–наружные дефекты – закаты, риски, трещины, царапины, плены, чешуйчатость и т.п.;
–внутренние дефекты – раковины, закаты, окалины, волосовины;
–несоответствие механических свойств металла требованиям ГОСТа или ТУ по пределу прочности, удлинению, требованиям на перегибы, навивание, скрутку и пр.;
–несоответствие различным специальным требованиям, например высокое удельное сопротивление.
Наиболее часто встречаются на прокатном металле трещины, закаты, прирезы.
Трещины – сравнительно крупные нарушения целостности
поверхностного слоя металла. Они бывают одиночными, но в большинстве случаев располагаются группами.
Закаты появляются от вдавливания и закатывания в прокатываемую полосу всякого рода возвышений, прирезов, частиц окалины, образующихся на поверхности металла в предыдущем
56
проходе. Чаще всего закаты возникают из-за наличия заусенцев и выступов, образующихся при переполнении калибра, а также из-за наличия трещин.
Прирез – длинный продольный часто с острыми краями выступ металла на катанке, возникающий, как правило, вследствие переполнения калибра.
Основные меры, необходимые для предотвращения брака при прокатке:
–правильная калибровка валков;
–тщательная настройка и регулировка стана;
–надлежащий нагрев металла;
–работа на мало выработанных калибрах;
–систематическая перевалка валков.
Брак в производстве проволоки возникает из-за нарушения технологического процесса и плохого качества исходного материала. Брак разделяется на окончательный и исправимый. Исправимый брак может быть устранен дополнительными операциями или перетяжкой проволоки на более тонкие размеры. Окончательный брак не устраняется (трещины, хрупкость проволоки вследствие пережога).
Плены – частицы металла на поверхности изделия, отделяющиеся при изгибе от его основной массы.
Раковины – неровные углубления от уже отпавших плен. Риски – заметные по всей длине изделия глубокие про-
дольные выемки.
Забоина – местное повреждение поверхности металла, вызванное механическим воздействием (ударом) постороннего тела.
Заусенец – местная плена с заостренными краями, отделившаяся от основной массы.
57
2.ОБМОТОЧНЫЕ ПРОВОДА
2.1.КЛАССИФИКАЦИЯ ОБМОТОЧНЫХ ПРОВОДОВ
Обмоточные провода – это провода, применяемые для изготовления обмоток электрических машин аппаратов и приборов.
Объем производства обмоточных проводов непрерывно увеличивается, что связано с прогрессом электромашиностроения и электроаппаратостроения, а также с развитием приборостроения, радиотехнической и авиационной промышленности.
По применяемым проводниковым материалам обмоточные провода делятся на медные, алюминиевые и из сплавов сопротивления.
По видам изоляции различают провода:
–с эмалевой изоляцией;
–с волокнистой или эмалево-волокнистой изоляцией, в том числе со стекловолокнистой и бумажной изоляцией;
–с пластмассовой изоляцией, включая пленочную.
Кроме того, в ограниченном количестве для нужд приборостроения выпускаются обмоточные провода со сплошной стеклянной, стеклоэмалевой и керамической изоляцией.
Одним из важнейших параметров обмоточных проводов является нагревостойкость. На смену понятию «нагревостойкость» пришло понятие «температурный индекс». Этот индекс численно равен температуре, при которой в течение не менее 20 000 ч уровень пробивного напряжения (или другой параметр) выше определенного заданного уровня.
По значению температурного индекса можно классифицировать изоляцию обмоточных проводов следующим образом:
58
Температурный |
Наименованиематериалов |
|
индекс, °С |
||
|
||
105 |
Поливинилацеталеваяизоляция, изоляциянаосновемас- |
|
ляныхлаков, пропитанныйнатуральныйшелк, бумага |
||
|
||
120 |
Полиуретановая, лавсановая изоляция |
|
130 |
Немодифицированные полиэфирныелаки |
|
155 |
Полиэфиримидная истекловолокнистаяизоляция, про- |
|
питанная глифталевымилакамиит.д. |
||
|
||
|
Стекловолокнистаяизоляция, пропитаннаякремнийор- |
|
180 |
ганическими лаками, некоторые модифицированные |
|
|
полиэфиримидныелаки |
|
200 |
Полиамидимидная изоляция |
|
220–240 |
Полиимидная, фторопластовая изоляция |
Для проводов более высокой нагревостойкости температурные индексы не устанавливаются, так как при температуре 250–300 °C и выше срок эксплуатации обмоточных проводов меньше 20 000 ч.
2.2.ПРОВОДНИКОВЫЕ МАТЕРИАЛЫ, ПРИМЕНЯЕМЫЕ
ВПРОИЗВОДСТВЕ ОБМОТОЧНЫХ ПРОВОДОВ
Медная проволока круглого и прямоугольного сечения изготавливается по ГОСТ 2112–71 или ОСТ 16.0505.008–73.
При производстве круглой проволоки используется медная катанка по ОСТ 13842–80Е, причем проволоку для эмалирования проводов диаметром менее 0,38 мм и диаметром более 1,25 мм рекомендуется изготавливать из скальпируемой заготовки или из катанки, полученной методом непрерывного литья и прокатки. Медная круглая проволока изготавливается диаметром от 0,015 до 5,20 мм, она может быть мягкой (ММ) и твердой (МТ). Проволока, применяемая для изготовления эмалированных проводов, должна храниться не более 15 суток в помещении при 5–35 оС и относительной влажности не более 80 %. Ее
59
удельное сопротивление при 20 оС должно соответствовать определенному значению (1,724 10–8 Ом·м). Медная проволока прямоугольного сечения имеет сечение 1,5–150 мм2. Для производства алюминиевых эмалированных проводов применяется круглая алюминиевая проволока диаметром 0,08–2,5 мм, с другими видами изоляции – диаметром 1,35–8,0 мм, а также проволока прямоугольного сечения 7,5–125 мм2.
Для производства обмоточных проводов широко используются также сплавы высокого сопротивления – манганин, константан, нихром. Провода из таких сплавов применяются для изготовления электрических измерительных приборов, электрических нагревательных приборов, образцовых сопротивлений, реостатов.
Проводники для обмоточных проводов высокой нагревостойкости должны обладать хорошей электропроводностью, стойкостью к окислению на воздухе при повышенных температурах, и их сопротивление должно минимально увеличиться в процессе эксплуатации. Проводниковые материалы не должны оказывать каталитическое воздействие на изоляцию или диффундировать в нее, так как это вызывает тепловое старение изоляции, особенно при температурах больше 600 °C. Основными процессами, протекающими при повышенной температуре, являются окисление и диффузия. Медь при температуре выше 225 °C начинает интенсивно окисляться на воздухе. Это вызывает резкое увеличение электрического сопротивления меди, что приводит к снижению эластичности и отслаиванию изоляционного покрытия. Для устранения этого недостатка медь защищают от окисления покрытием из другого металла (например, никеля), который наносят как методом плакирования, так и гальванически. Получают биметаллическую проволоку. Такая проволока может работать длительно при температуре 400 °C и в течение ограниченного времени при 650 °C. Выпускается проволока диаметром 0,1–2,5 мм. При температуре ≈ 400 °C на-
60