
книги / Технология производства проводов
..pdf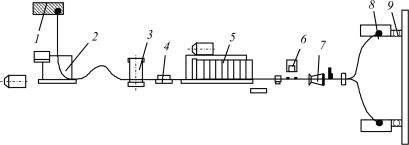
иную сторону вызывает дефекты заготовки. Кристаллизатор 2, в который металл поступает из ванны, представляет собой колесо, по ободу которого выточен паз, имеющий форму заготовки. Колесо и охватывающая его стальная лента образуют «бесконечную» изложницу. Угол обхвата колеса лентой равен 120°.
Рис. 1.7. Схема установки непрерывного литья и проката
По мере вращения колеса металл кристаллизуется и остывает до заданной температуры. Колесо и лента интенсивно охлаждаются водой.
Для отделения литой заготовки от обода колеса установлен нож-отгибатель, а кристаллизатор повернут относительно оси прокатки на некоторый угол. Между кристаллизатором и станом расположены ножницы 3 для обрезки переднего конца литой заготовки.
Прокатный стан 5 состоит из 17 клетей трехвалкового типа (могут быть и двухвалковые). На валки подается эмульсия, которая служит для охлаждения и смазки заготовки. Перед прокатным станом установлен петлерегулятор 4, который в зависимости от натяжения заготовки (уменьшения или увеличения длины петли) дает команду на увеличение или уменьшение скорости прокатки.
После согласования скорости прокатного стана и кристаллизатора работа переводится на автоматический режим. За про-
31
катным станом установлены летучие ножницы барабанного типа 6. Стрелка 7 служит для направления движения катанки в одну из моталок 8. После съема с моталки катанки увязываются в бунты на бунтовязальной машине 9 и направляются на склад.
Моталки с вращающимся барабаном обеспечивают получение бунтов до 5 т. В моталках с неподвижным барабаном масса бунта ограничивается только грузоподъемными средствами практически до 15 т.
Этим способом получают бунты алюминиевой катанки весом до 1500 кг, что дает возможность сократить отходы и повысить производительность. Процесс литья и проката обладает рядом технико-экономических преимуществ перед процессом слитковой прокатки – меньше площадь, меньше количество обслуживающего персонала, ниже себестоимость продукции.
1.6. МЕТОД «ДИП-ФОРМИНГ»
Разновидностью метода непрерывного литья и прокатки является метод «дип-форминг», разработанный американской фирмой General Electric. Он используется для получения высококачественной медной катанки из бескислородной меди.
Этот метод получил свое название из-за сходства со старым методом изготовления свечей постепенным наращиванием слоя воска. Сущность метода заключается в том, что заготовка в виде катанки со скоростью около 100 м/мин проходит через тигель с расплавленной медью, увеличивая свою массу примерно втрое, а затем поступает на прокатный стан, где и доводится до нужного размера. Схема процесса показана на рис. 1.8. Сырьем служат катодная медь (стержни, листы) или отходы катанки. В ряде случаев используется часть катанки, которая поступает непосредственно с приемного устройства прокатного стана. Плавильная печь индукционного типа имеет производительность 3–10 т/ч (обычно около 6 т/ч), температура меди в тигле
32
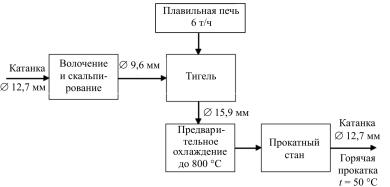
около 1120 °С, содержание кислорода в меди не более 5·10–4 % (бескислородная медь). Исходная заготовка – катанка диаметром 12,7 мм – подвергается предварительному волочению и скальпированию до диаметра 9,6 мм и подается к литейному тиглю. На этой операции за час к литейному тиглю поступает 3 т медной заготовки. На выходе из литейного тигля, в который заготовка поступает снизу, она имеет диаметр 15,9 мм. После предварительного охлаждения, обеспечивающего снижение температуры поверхности до 800 °С, медная заготовка подается к прокатному стану. Производительность стана до 9 т/ч. Так как поступающая к прокатному стану заготовка имеет круглую форму и высокую температуру, то для получения катанки диаметром 12,7 мм достаточно всего пяти прокатных клетей, калибровка которых выполнена по системе круг–овал. После горячей прокатки температура катанки составляет около 50 °С. Весь процесс осуществляется в защитной атмосфере, что позволяет получать бескислородную катанку высокой чистоты с неокисленной высококачественной поверхностью.
Рис. 1.8. Схема изготовления катанки методом «дип-форминг»
Процесс получения медной катанки методом «дип-форминг» имеет те же преимущества перед процессом горячей прокатки, что и процесснепрерывного литьяи прокатки(НПЛ):
33
1)в качестве сырья вместо дорогостоящих слитков используются катодная медь, отходы производства, медная стружка и т.п.;
2)исключается операция травления катанки;
3)длина получаемой катанки ограничивается только вместимостью приемного устройства;
4)повышенное качество катанки, обеспечиваемое равномерной мелкозернистой структурой, проявляющееся в высокой пластичности и повышенной электропроводности.
Использование катанки, полученной методом «дип-фор- минг», особенно эффективно в производстве круглых и прямоугольных эмалированных проводов больших сечений. В отличие от метода НЛП метод «дип-форминг» обеспечивает получение бескислородной меди.
1.7. ТРАВЛЕНИЕ КАТАНКИ
Горячая прокатка медной заготовки сопровождается интенсивным окислением ее поверхности, в результате чего заготовка покрывается очень твердой и хрупкой окалиной.
При горячей прокатке алюминиевой заготовки окалина не образуется, так как алюминий покрыт тонкой и очень прочной окисной пленкой Al2O3, препятствующей дальнейшему процессу окисления.
Волочение медной катанки с окалиной не производится, так как из катанки с окалиной получается проволока неудовлетворительного качества по чистоте поверхности и механическим параметрам. Кроме того, повышается обрывность проволоки, снижается стойкость волочильного инструмента и производительность оборудования.
Основным способом удаления окалины с поверхности медной катанки является травление.
34
Травление медной катанки производится в водном растворе серной кислоты, содержащей 5–15 % H2SO4, при температуре 40–60 °С. Окалина, состоящая из внутреннего слоя закиси меди Cu2O и наружного слоя окиси меди CuO, быстро растворяется в таком растворе, а медь в этих условиях с серной кислотой не реагирует.
CuO + H2SO4 → CuSO4 + H2O,
Cu2O + H2SO4 → CuSO4 + Cu + H2O.
Протравленные бухты катанки промываются холодной водой для удаления остатков кислоты и частиц металла, а затем для полной нейтрализации кислоты – раствором щелочи при температуре 55–60 °С в течение 2–3 мин (мыльный раствор). Щелочь частично остается на поверхности катанки и благоприятно влияет на процесс волочения.
Обычно производится травление катанки в бухтах, но можно совмещать травление с прокаткой при непрерывном движении катанки.
Оборудование для травления подразделяется на два основных типа: периодического и непрерывного действия.
Установки периодического действия состоят из ряда ванн и подъемно-транспортных механизмов. В таких установках медь, подлежащая травлению, в течение определенного времени последовательно проходит операции травления, промывки, нейтрализации, сушки.
Установки периодического действия применяются в основном для травления пакетов бухт, шин, коллекторной меди. Пакеты заготовок опускаются краном в бак с травильным раствором, подогретым до 40–60 °С, и остаются там на 30–40 мин до приобретения поверхностью изделий светло-розового или кирпичного цвета. Из травильной ванны катанка краном переносится на площадку для промывки, где струей из брандспойта с нее удаляются остатки травильного раствора и медная пыль.
35
Промывка должна быть тщательной. В конце промывки стекающая с бухт вода должна быть бесцветной. После промывки бухты погружаются в бак нейтрализации, где должен находиться раствор мыла или каустической соды в воде, подогретой до температуры 50–70 °С.
Установки непрерывного действия предназначены для травления медной катанки в бухтах. Такие установки имеют транспортеры, при помощи которых бухты автоматически перемещаются из ванны в ванну.
Во избежание уменьшения концентрации серной кислоты ванны травления соединены с установкой для регенерации раствора. Происходит постоянный обмен порциями раствора между ванной травления и ванной регенерации, для чего предусмотрено автоматическое регулирование уровней в обеих ваннах.
При выходе из ванны травления бухты промываются холодной проточной водой под давлением. Затем они поступают
вванну нейтрализации, в которой и происходит подогрев бухт, что ускоряет дальнейшую сушку.
Раствор в ванне нейтрализации постоянно обновляется, т.е. часть раствора через сливной штуцер уходит в канализацию, а в ванну добавляется холодная водопроводная вода.
После нейтрализации бухты желательно обдуть подогретым воздухом или паром. Сухие протравленные бухты поступают на приемный стол, где их освобождают от подвески. Затем идут на склад.
Для приготовления травильного раствора применяется
техническая серная кислота с содержанием H2SO4 62–67 %. Травильный бак заполняется водой до половины объема, после чего
внего тонкой струей вливается серная кислота. В полученный раствор снова доливается вода с таким расчетом, чтобы полностью был покрыт протравливаемый металл. Концентрация серной кислоты должна быть равна 8–12 %. Раствор подогревается
до температуры 50–60 °С.
36
Раствор для нейтрализации приготавливается из 40%-ного хозяйственного мыла и каустической соды. Разведенное мыло и каустическая сода добавляются в бак для нейтрализации 2–3 раза в смену. Кусковое мыло перед загрузкой в бак должно быть растворено в горячей воде.
В процессе травления в растворе накапливаются сернокислые соли меди, которые замедляют реакции растворения окислов и делают раствор непригодным для травления. Его необходимо заменить. На заводах для извлечения меди из растворов используются следующие методы.
1.Электролитический. Извлечение меди ведут путем электролиза травильного раствора после перекачки его в специальную ванну. В ванне находятся медные и свинцовые пластины, к которым подводится постоянный ток. Медная пластина – катод, свинцовая – анод. На катоде осаждается медь, на аноде – кислород. Одновременно с извлечением меди регенерируется (восстанавливается) отработанный раствор, который применяется для повторного использования.
2.Выпаривание. Отработанный раствор перекачивают
вбак для выпаривания. Во время нагрева раствор испаряется до насыщения его медным купоросом. Насыщенный раствор перегоняется в баки-кристаллизаторы, в которых при охлаждении выделяется медный купорос. Кристаллизуется купорос на устанавливаемых в баках свинцовых пластинах в течение
3–4 дней.
3.Извлечение меди в виде фольги. Для извлечения меди из растворов применяется барабанный электролизер с нерастворимым анодом. Травильный раствор закачивается насосом
внапорный бак, откуда он самотеком поступает в ванну электролизера и из нее обратно в травильную ванну. Медь непрерывно осаждается на вращающемся барабане-катоде. Она отделяется от барабана в виде непрерывной ленты; последовательно проходит через слой воды, концентрированной серной кислоты и снова через слой воды; обмывается струями чистой
37
воды; просушивается горячим воздухом и наматывается на шпулю. Толщина фольги зависит от силы тока и скорости вращения барабана.
Отработанные травильные растворы и промывочные воды перед сливом в канализацию обезвреживаются путем пропускания их через слой извести.
H2SO4 + Ca (OH)2 → CaSO4 + 2H2O,
CuSO4 + Ca (OH)2 → CaSO4 + Cu (OH)2 .
Образующиеся нерастворимые соли извлекаются из нейтрализационных колодцев, а вода сливается в канализацию.
Наличие на поверхности заготовки после травления темных пятен и полос недопустимо, оно является следствием плохого травления, обусловленного следующими причинами:
–не выдержано время травления;
–низка температура травильного раствора;
–травильный раствор содержит много медного купороса. Смена травильного раствора и чистка ванны производят-
ся по мере выработки травильного раствора, но не реже двух раз в месяц.
Содержание H2SO4 контролируется после изготовления нового травильного раствора, а затем периодически в процессе работы. Содержание медного купороса проверяется 1 раз в смену и дополнительно при обнаружении плохого качества травления.
1.8. СКАЛЬПИРОВАНИЕ МЕДНОЙ КАТАНКИ
Травление в ванне с серной кислотой удаляет окалину. При этом на поверхности катанки обнаруживается большое количество мелких трещин, ранее невидимых под окалиной. При травлении могут оставаться включения закиси меди, полностью закрытые металлом. Максимальная глубина таких включений не превышает 0,2–0,3 мм.
38
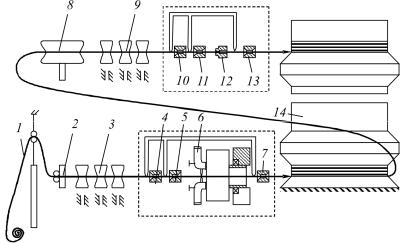
При волочении такой катанки включения закиси меди выступят наружу, появятся в виде сколов и плен, что является браком, так как при эмалировании эти дефекты могут стать одной из причин повреждения изоляционного слоя.
Если при грубом волочении поверхностные дефекты катанки приводят в основном к ухудшению качества проволоки, то при тонком, особенно при тончайшем, волочении – к повышенной обрывности, так как дефекты проволоки становятся соизмеримыми с ее диаметром.
Скальпирование – это удаление механическим путем поверхностного слоя катанки. Скальпирование увеличивает количество отходов, но повышает качество готовой проволоки. На рис. 1.9 представлена схема установки для скальпирования катанки.
Рис. 1.9. Схема установки для скальпирования медной катанки
Установка скальпирования медной катанки состоит из волочильного барабана, устройства для нарезки спирали и скальпирующей головки. Катанка 1 через направляющие ролики 2 и правильное устройство 3 поступает в обжимную фильеру 4
39
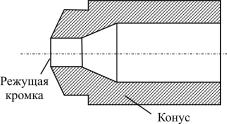
с обжатием 23–25 %. В результате деформации повышаются механические свойства катанки, и поверхностный слой меди лучше поддается обработке резанием. Нарезка спирали производится после фильеры 5 с помощью двух или трех резцов, закрепленных на суппорте при помощи винтов 6. Резцы устанавливаются по отношению к катанке таким образом, чтобы ее поступательное движение обеспечивало нарезку спирали на некоторую глубину. Через направляющую фильеру 7 катанка поступает на тяговый барабан 14, а затем через перекидной ролик 8 и правильные ролики 9 направляется во второй суппорт, в котором происходит скальпирование. После направляющих фильер 10, 11 резцом (скальпом) 12 по всему периметру катанки снимается стружка толщиной 0,1–0,2 мм. Скальпированная проволока через направляющую фильеру 13 принимается верхней ступенью тягового барабана 14. Конструкция скальпа представлена на рис. 1.10.
Рис. 1.10. Конструкция скальпа
Скорость скальпирования 70–90 м/мин. Качественное скальпирование обеспечивается при равномерном съеме стружки по периметру катанки, прямолинейном движении катанки на участке скальпирования, отсутствии вибрации инструмента и катанки. Кроме того, режущий инструмент должен иметь высокую стойкость.
Катанка, предназначенная для волочения проволоки тончайших размеров, скальпируется без нарезки спирали, так как
40