
книги / Основные новые разработки в технологии аммиака
..pdfДругим методом снижения расхода топливного газа в радиантных горелках является добавление в систему предварительного риформинга. Преимущество предварительного риформинга заключается в том, что при его использовании не требуется модернизации системы на входе катализаторной трубы. Система работает следующим образом. Парогазовая смесь подогревается до максимально допустимой температуры в системе на входе катализаторных труб, например до 500–520 °С. Далее она проходит через наполненный катализатором сосуд, в котором происходит адиабатический предриформинг и высшие углеводороды ПГС преобразуются в метан, СО и водород. Часть метана также преобразуется в СО и водород. Эти реакции приводят к падению температуры на 60–70 °С. Прореагировавшая газовая смесь, выходящая из сосуда после риформинга при температуре около 440 °С, снова подогревается в секции конвекции примерно до 500–520 °С и поступает на вход катализаторных труб первичного риформинга. Подача предварительно риформированной смеси снижает расход природного газа приблизительно на 8 %.
Третьим способом снижения нагрузки радиантных горелок является использование парогазовой смеси с более низким соотношением пар / углеводород. Такой подход снижает поток, проходящий через катализаторные трубы. Это означает, что потребуется меньше тепла для нагревания газовой смеси до требуемых 820 °С на выходе из катализаторных труб. При такой технологии достигается снижение расхода газа в радиантных горелках на 2–3 %.
В классическом производстве аммиака температура подогрева технологического воздуха составляет примерно 500 °С.
Нагрев воздуха в секции конвекции первичного риформинга до более высоких температур дает следующие преимущества. Вопервых, добавленное тепло может быть использовано для снижения расхода газа в радиантных горелках, так как реформированная газовая смесь из первичного риформинга может подаваться на вторичный риформинг при более низкой температуре. Таким образом, расход может быть снижен примерно на 5 %.
11
Во-вторых, дополнительное тепло может быть использовано для увеличения температуры на выходе вторичного риформинга. Это снизит проскок метана из вторичного риформинга и уменьшит продувочный поток в системе синтеза аммиака.
Существуют и другие способы энергосбережения в производствах аммиака. Они связаны с повышением конечной температуры вторичного риформинга, с увеличением чистоты синтез-газа, в частности за счет более полной конверсии СО и более тонкой очистки газа от СО2, с более эффективным использованием тепла синтеза аммиака, с применением новых, более активных, катализаторов.
Так, фирмой Sud-Chemie разработан и выпускается новый катализатор AmoMax-10 на основе нестехиометрического оксида железа – вюстита (Fe1–x O). Этот катализатор проявляет на 70 % более высокую активность по сравнению с обычными железными катализаторами синтеза аммиака на основе магнетита. Кроме того, AmoMax-10 имеет более низкую температуру восстановления и более высокую прочность, что обеспечивает более длительный срок его эксплуатации (до 15 лет).
3. ТЕХНОЛОГИЯ АММИАКА С ИСПОЛЬЗОВАНИЕМ СИНТЕЗА ПОД НИЗКИМ ДАВЛЕНИЕМ
Вконце 1980-х гг. фирма Imperial Chemical Industries (ICI) (Великобритания) заявила о разработке технологии AMV, при которой давление в схеме синтеза составляет менее 10 МПа. Поэтому назрела необходимость сделать обзор эксплуатации схемы синтеза при низком давлении и рассмотреть развитие этой технологии в будущем.
Вэтом разделе будет рассмотрено производство с использованием катализатора на основе магнетита (KATALCO 74-1), хотя существуют параллельные разработки с применением катализатора высокой активности на основе рутения.
12
3.1.Разработка технологии низкого давления
всхеме синтеза аммиака
Даже двадцать лет назад эта концепция не была новой. Еще в 1928 г. при первом производстве аммиака использовали технологию с давлением синтеза 10 МПа, несмотря на то что мощность этой установки составляла всего 80 т/сутки и требовалось четыре колонны синтеза с мощностью 20 т/сутки каждая.
В конце 70-х гг. одним из ведущих мотивов модернизации технологии стало снижение потребления энергии, что привело к возобновлению интереса к синтезу под низким давлением. Другая цель модернизации заключалась в уменьшении размеров и сложности компрессора синтез-газа для снижения капитальных затрат и повышения надежности.
Технология Ammonia mid volume (AMV)
Для достижения перечисленных целей фирма ICI разработала технологию AMV и связанный с ней катализатор KATALCO 74-1.
Технология AMV была одной из первых высокоэффективных крупномасштабных технологий аммиака современного поколения. Низкое давление в системе синтеза (8–10 МПа) является одной из основных характеристик этой технологии, и для нее специально был разработан катализатор KATALCO 74-1.
Применение синтеза под низким давлением в этой технологии позволило снизить потребление энергии компрессором синтез-газа и дало возможность использовать компрессор с одной ступенью.
Другой характеристикой технологии является использование избытка воздуха (обычно на 20 % больше стехиометрической потребности) с целью снижения нагрузки на первичный риформинг. Получаемый избыток азота подается на криогенную установку получения водорода. Низкое давление схемы позволяет работать этой установке с таким же давлением, что устраняет повторную компрессию полученного водорода.
Особенностью схемы синтеза в технологии AMV является использование циркулирующего газа, насыщенного азотом, с обычным
13
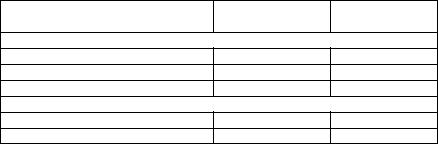
соотношением азот/водород 2,2 : 1,0 на входе колонны. Основной причиной этого является увеличение концентрации азота в потоке продувочного газа. Последний очищается в криогенной установке для получения водорода и отделения избыточного количества азота, который подается во вторичный риформинг. Высокая концентрация азота минимизирует поток продувочного газа, необходимого для отделения данного количества азота. В условиях реакции синтеза более высокая концентрация азота ускоряет реакцию кинетики катализатора на основе магнетита за счет адсорбции азота на поверхности катализатора.
Можно было бы ожидать, что нестехиометрическая газовая смесь будет неблагоприятно воздействовать на содержание аммиака в равновесии. Однако это не так, потому что влияние соотношения водород/азот на равновесие реакции синтеза аммиака мало и гораздо более важным является влияние на равновесие других параметров, особенно температуры.
Данные, представленные в табл. 2, позволяют сравнить технические параметры процесса синтеза аммиака в соответствии с технологией AMV фирмы ICI и традиционной технологией.
Таблица 2
Технические показатели процесса синтеза аммиака по технологии AMV и традиционной технологии
Показатели |
Технология AMV |
Традиционная |
|
|
технология |
Типичные режимы первичного риформинга |
||
Соотношение пар/углерод |
2,75–3,0 |
3,5 |
Температура газа на выходе, °С |
780 |
800–820 |
Проскок метана, об.% |
16 |
11 |
Типичные режимы вторичного риформинга |
||
Температура газа на выходе, °С |
950 |
1000 |
Проскок метана, об.% |
1,0 |
0,3 |
Агрегаты четвертого поколения фирмы ICI (AMV Process) характеризуются следующими особенностями:
14
–подачей избыточного количества воздуха (на 20 %) во вторичный риформинг;
–более мягкими условиями первичного риформинга;
–низким давлением синтеза (80–110 атм);
–рекуперацией водорода из продувочных газов при давлении синтеза;
–экономией энергии (затраты 6,8–6,9 Гкал/т).
Технология Leading concept ammonia (LCA)
Технология LCA предназначена для производств аммиака малой и средней мощности и имеет ряд особенностей.
В данной технологии применяется риформинг с подогревом газа, в котором горячий газ из вторичного риформинга используется для обеспечения поступления тепла для реакции первичного риформинга. Избыточный технологический воздух используется для уравновешивания теплового баланса в первичном и вторичном риформингах.
Преимущество такой системы заключается в отсутствии традиционной печи риформинга и относящегося к ней оборудования утилизации тепла. Риформированный газ из межтрубного пространства риформинга с подогревом газа поступает в одноступенчатый изотермический реактор конверсии и затем охлаждается и очищается в адсорбционной установке переменного давления (короткоцикловая адсорбция) с целью удаления двуокиси углерода и избытка азота. Далее синтез-газ направляется в метанатор и сушилку газа перед поступлением в компрессор синтез-газа и схему синтеза.
Преимущества синтеза с низким давлением в данной технологии связаны, главным образом, с компрессором синтез-газа.
Во-первых, низкое давление синтеза гарантирует, что действительный объем потока, проходящий через компрессор, достаточно большой для обеспечения высокой эффективности компрессии.
Во-вторых, низкое давление синтеза позволяет использовать компрессор с одним корпусом, что сокращает капитальные затраты и повышает надежность.
15
И, наконец, уменьшенная нагрузка на компрессор обеспечивает маневренность при конструировании машинного привода, и можно использовать компрессор с электроприводом.
Часть концепции технологии LCA заключается в упрощении установок по обработке химреагентов и отделении их от систем утилизации пара и энергии. Такая схема противоположна схеме обычных установок аммиака, в которых применяются высокоинтегрированные системы утилизации.
Первые две установки с использованием технологии LCA, подтверждающие эффективность этой концепции, были построены фирмой ICI в Великобритании (Севернсайд) и пущены в эксплуатацию в 1988 г.
Всоответствии с концепцией упрощенного производства все основное оборудование имеет электропривод, включая компрессор синтез-газа.
3.2.Конструкция колонны с низким давлением синтеза
Втехнологиях AMV и LCA производства аммиака под низким давлением использовались аммиачные колонны с разнообразными конструкциями.
Впервые установка с низким давлением, разработанная ICI, была применена в производстве аммиака по технологии AMV в Канаде и пущена в эксплуатацию в 1985 г. Колонна синтеза на этом производстве имела простую конструкцию с аксиальным потоком
ис тремя слоями катализатора. Охлаждение в ней производилось
с помощью охлаждающего газа между первым и вторым слоем и с помощью теплообменника между вторым и третьим слоем.
Следующие колонны с низким давлением синтеза были разработаны фирмой ICI для двух установок, работающих по технологии LCA, в Великобритании. Основные характеристики конструкции этой колонны следующие. Охлаждение трубы и адиабатическая конструкция обеспечивают температурный режим, близкий к оптимальному для минимизации необходимого объема катализатора. Преимущество такой колонны с охлаждаемыми трубами, в отличие от обычной колонны с несколькими слоями, заключается в том, что
16
профиль падения температуры по направлению к нижней части колонны таков, что позволяет получить низкую температуру на выходе и, следовательно, обеспечивает достижение более высокого содержания аммиака.
При такой конструкции колонны можно изменять интенсивность охлаждения по длине охлаждающих труб, так как они имеют две зоны с разными свойствами передачи тепла.
Однако при найденной оптимальной конструкции колонны с участком охлаждения в нижней ее части не было адиабатической секции. Назначение этой секции состоит в предотвращении чрезмерного охлаждения и приближения к реакции равновесия.
Наличие одного слоя катализатора позволяет осуществлять быструю его загрузку и выгрузку.
Конструкция механической части очень простая в связи с отсутствием требования передачи газа между многочисленными слоями катализатора и теплообменников. Охлаждающие трубы поддерживаются расположением коллектора без трубных досок, которые имелись в колонне старого поколения с трубами охлаждения.
По сравнению с обычной трехслойной колонной с внутренним охлаждением для такой же нагрузки колонна с трубным охлаждением и адиабатической секцией требует почти такого же объема катализатора, но механическая часть колонны гораздо проще. Данная конструкция колонны является идеальным решением для установок производства аммиака средних размеров.
Впоследующих разработках установок для технологий AMV
иLCA использовали трехслойную колонну с радиальным потоком, похожую на ту, которая используется в других, высокоэффективных производствах аммиака. Детальная разработка проекта такой колон-
ны была сделана фирмами Uhde (в Китае) и Ammonia Casale (в США).
3.3. Катализатор для синтеза при низком давлении
Катализатор KATALCO 74-1 был разработан фирмой ICI в конце 70-х гг. специально для работы при низком давлении. Этот катализатор на основе железа имеет те же самые активаторы, что
17
и обычный катализатор синтеза (Аl2O3, K2O, СаО), а также незначительное количество кобальта (в виде соединения СоО) и других оксидов.
Катализатор KATALCO 74-1 являлся частью проекта модернизации производства, работавшего при давлении 13 МПа, и, находясь в эксплуатации с 1988 по 2001 г., продемонстрировал отличные свойства. Затем была произведена дальнейшая реконструкция производства путем перевода колонны на аксиально-радиальный поток с использованием технологии Ammonia Casale. На основе опыта эксплуатации с 1988 г. KATALCO 74-1 снова выбрали для использования в модернизированных колоннах.
Высокоактивный катализатор KATALCO 74-1 также использовался при модернизации установок по производству аммиака в мировом масштабе для замены катализатора на основе драгоценных металлов в конечном слое колонны, что позволило при эксплуатации быстро достигать расчетного уровня концентрации аммиака на выходе (более 18 %).
KATALCO 74-1 является идеальным катализатором для загрузки четвертого слоя, где катализатор должен работать при сочетании низких температур слоя и относительно высокой концентрации аммиака на входе.
Высокая активность этого катализатора является результатом включения СоО и других активаторов, обеспечивающих оптимальные результаты в условиях низкого давления.
Работа с готовым катализатором та же самая, что и с обычным. Концентрация СоО слишком незначительна для того, чтобы представлятьопасностьпри загрузке, эксплуатации ивыгрузкекатализатора.
Процедура восстановления та же, что и для обычного катализатора, с тем преимуществом, что температура восстановления KATALCO 74-1 значительно ниже, чем температура восстановления обычных катализаторов.
Опыт показывает, что высокая активность катализатора для работы при низком давлении обеспечивается в течение многих лет стабильной эксплуатации.
18
Наиболее удачным примером его работы является эксплуатация установок LCA в Севернсайд (Великобритания), где первоначально загруженный катализатор KATALCO 74-1 действовал в течение 14 лет.
Надежность KATALCO 74-1 в условиях низкого давления подтверждается еще и тем, что пять из шести установок AMV и LCA до сих пор работают с первоначально загруженным катализатором.
Низкий уровень потери активности связывают, главным образом, с низкими рабочими температурами в условиях низкого давления, несмотря на то что важным фактором считается низкая температура процесса восстановления, которая приводит в меньшему спеканию в этот период.
Катализатор KATALCO 74-1 демонстрирует значительные преимущества в активности при давлении до 15 МПа, но это преимущество менее заметно при более высоком давлении.
Катализатор имеет и другие преимущества, такие как легкость восстановления и низкий уровень потери активности.
По этим причинам катализатор можно использовать для целого ряда установок с давлением синтеза до 15 МПа. Примером такого применения является производство аммиака фирмы Kellogg, модернизированного ICI в 1988 г. с увеличением производительности
с550 т/сутки до 720 т/сутки.
3.4.Перспективы развития технологии синтеза при низком давлении
Начиная с 1998 г. ICI Synetix работает вместе с фирмой Uhde с целью более эффективного использования опыта усовершенствований в аммиачной промышленности одной фирмы и опыта разработки нового катализатора другой.
Учитывается много факторов, включая оптимальное давление для процесса риформинга и синтеза аммиака, эффект соотношения между давлением подпиточного газа и давлением синтеза.
Вследствие высоких капитальных затрат и специфической конструкции компрессора синтез-газа при выборе давления синтеза
19
следует учитывать давление подпиточного газа, определяемое давлением риформинга.
При обычном давлении риформинга примерно до 4,0 МПа возможен выбор одного из двух вариантов: либо компрессор с одним корпусом, обеспечивающий давление в схеме около 10 МПа, либо компрессор с двумя корпусами и результирующим давлением примерно 20 МПа.
Теоретически возможен вариант схемы и без компрессора синтез-газа.
Рассмотрим эти варианты.
Вариант без компрессора синтез-газа
Конечная цель в упрощении компрессора синтез-газа заключается в его абсолютном устранении. Этой цели можно достигнуть двумя путями: либо увеличением давления на заключительном этапе получения синтез-газа, либо уменьшением давления синтеза. Эта идея не является новой, но заслуживает того, чтобы ее рассмотрели в контексте синтеза низкого давления.
Первый вариант заключается в увеличении давления подпиточного газа, т.е. в увеличении давления риформинга. На первый взгляд кажется, что более высокое давление риформинга снизит нагрузку на компрессор синтез-газа, а следовательно, снизит общую потребность в энергии и повысит общую эффективность. Однако при ближайшем рассмотрении оказывается, что это не так.
Например, мощность, необходимая для основных нагрузок компрессии для производства аммиака 1500 т/сутки, составляет 27 МВт при давлении первичного риформинга 20 атм и 18 МВт при давлении 60 атм.
Вэтом примере номинальное давление синтеза 8 МПа, его ICI Synetix считает минимальным практическим давлением для эффективной работы с использованием современных катализаторов синтеза.
Всвязи с тем, что в данном случае давление синтеза является
постоянным, скорость циркулирующего газа в схеме и затраты на его охлаждение тоже постоянные и нет необходимости учитывать их как часть модернизации.
20