
книги / Основные новые разработки в технологии аммиака
..pdfК основным объектам и процессам, подлежащим модернизации, относятся следующие:
–компрессор природного газа;
–компрессор технологического воздуха;
–компрессор синтез-газа;
–процесс утилизации тепла из технологического пара. Мощность, полученная при повышении до 12 МПа давления
пара, выходящего из паровой турбины на вход риформинга, включается в этот баланс потому, что ее получение зависит от рабочего давления риформинга.
При старой технологии (т.е. при давлении риформинга 3 МПа) увеличение давления риформинга действительно снижает общее потребление энергии процессом, но это вовсе не так для современных технологий с более высоким давлением риформинга.
Сегодня давление риформинга составляет как минимум 5 МПа. Ясно, что риформинг с еще бо́льшим давлением будет создавать значительные технические проблемы, и, следуя по этому пути, нельзя добиться каких-либо больших преимуществ.
Альтернативным путем является снижение давления в схеме синтеза. Схема синтеза должна работать в пределах ограничений равновесия пар-жидкость, которое управляет максимальной концентрацией аммиака на входе в реактор и реакцией равновесия, управляющей максимальной концентрацией аммиака на выходе колонны и являющейся функцией температуры. По мере понижения давления имеющаяся конверсия за один проход ограничивается максимальной концентрацией аммиака и равновесием.
Если учитывать все эти факторы, то самое минимальное давление синтеза на промышленной установке составляет в настоящее время 8,3 МПа. Дальнейшее снижение давления потребует увеличения уровня циркуляции (вследствие более низкой конверсии за один проход), а также потребует значительного увеличения объема катализатора из-за воздействия давления и температуры на скорость реакции.
По этим причинам производство без компрессора синтез-газа вряд ли станет реальностью. Поэтому практический выход заключа-
21
ется в выборе между однокорпусным компрессором (низкое давление синтеза) и двухкорпусным компрессором (высокое давление синтеза).
Компрессор с одним корпусом (низкое давление синтеза аммиака)
Как указывалось выше, основное преимущество схемы с низким давлением заключается в однокорпусном компрессоре и низком расчетном давлении для оборудования. Однако с точки зрения потребления энергии имеется крайне незначительная разница между современной схемой низкого давления и схемой высокого давления. Это происходит, главным образом, из-за того, что экономия энергии при компрессии синтез-газа в значительной мере компенсируется за счет повышения затрат на охлаждение при низком давлении.
При проекте с низким давлением хладагентами являются либо охлаждающая вода, либо аммиак, и температура охлаждения должна быть минимальна для того, чтобы снизить концентрацию аммиака, возвращающегося в колонну. Это приводит к гораздо большим затратам на охлаждение, чем в схеме высокого давления.
Теоретическое сравнение потребления энергии в схемах высокого и низкого давления показывает, что оно больше зависит от конверсии за один проход, температуры сепаратора, падения давления и т.д., чем от величины давления синтеза, и общее заключение таково, что «наиболее благоприятным» является среднее давление. Данная точка зрения поддерживается очень конкурентноспособными сделками по новым проектам, которые свидетельствуют о том, что давление синтеза мало влияет на общее потребление энергии.
В проекте с низким давлением необходимо также преодолевать ограничения, связанные с более низкой конверсией за один проход и уменьшенной скоростью реакции вследствие более низкого парциального давления вступающих в реакцию веществ. Это ведет к увеличению объема катализатора, даже такого активного, как катализатор KATALCO 74-1.
22
В схеме с низким давлением диаметры трубопроводов обычно больше, чем в схеме с высоким давлением, из-за объединенных эффектов низкого давления и высокого уровня циркуляции. Этот фактор не представляет важности для установок с производительностью до 1500 т/сутки, но он важен для установок с большей производительностью. Это означает, что концепция низкого давления имеет меньше потенциала для улучшения технических характеристик установок с очень большими мощностями.
Компрессор с двумя корпусами (высокое давление синтеза аммиака)
Обычная современная схема синтеза высокого давления состоит из одной или двух колонн синтеза аммиака, содержащих всего до трех слоев катализатора.
Циркуляция в схеме синтеза является функцией конверсии за один проход в колонне синтеза. Более высокая конверсия за один проход может быть получена при высоком давлении. Высокое давление благоприятствует также кинетике реакции, что ведет к уменьшению объема катализатора.
По сравнению с проектом низкого давления оптимизация условий синтеза высокого давления способствует более высокой концентрации инертных веществ и более высокой температуре для аммиачного сепаратора. Это ведет к экономии затрат на утилизацию продувочного газа и систему охлаждения.
Схема высокого давления также очень хорошо интегрируется с системой пара высокого давления, которая обычно используется на больших производствах аммиака. Весь получаемый на установке пар высокого давления подается на турбину, приводящую в действие компрессор синтез-газа, и далее используется для получения технологического пара среднего давления и для питания других нагрузок турбины.
В схеме низкого давления мощность, получаемая от понижения давления пара с высокого до технологического уровня, может превышать потребность в мощности компрессора синтез-газа, и то-
23
гда необходима другая схема турбины. Например, можно соединить ее нагрузки, т.е. использовать один привод для компрессора синтезгаза и системы охлаждения, или использовать электропривод, как в технологии LCA.
Однако для очень больших производств обычная система турбины высокого давления, приводящая в действие двухкорпусный компрессор, все еще является привлекательным решением.
Можно сделать вывод, что концепция низкого давления имеет реальные преимущества для установок малой мощности (около 500 т/сутки). Для установок средней мощности (1000–1500 т/сутки) разница в схемах низкого и высокого давления не очень значительна. Для более крупных производств с производительностью 2000 т/сутки и более концепция высокого давления имеет больше потенциала модернизации установок.
Технология двойного контура (Uhde)
Для установок, мощность которых значительно превышает 2000 т/сутки, прямое увеличение размеров проекта может не быть привлекательным вследствие ограничений, таких как наличие стандартных элементов трубопроводов, например фланцев, и ограничение размеров теплообменников.
Однако при отсутствии стандартных размеров и материалов альтернатива прямого увеличения может стать привлекательной, и данный подход привел к разработке технологии двойного контура Uhde для крупных производств аммиака.
Технология Uhde с двойным контуром основана на использовании однопроходной колонны для получения некоторого количества аммиака перед поступлением газа в обычную схему синтеза.
Хотя эта концепция колонны с подпиточным газом не нова, в технологии с двойным контуром компрессия осуществляется в два этапа и однопроходная колонна расположена перед вторым этапом компрессии синтез-газа.
Наличие высокоактивного катализатора для низкого давления дает возможность улучшить интегрирование однопроходной колон-
24
ны и компрессора синтез-газа так, чтобы сократить относительный размер компрессора и размер схемы синтеза. В действительности же это заставляет строить очень большие схемы синтеза.
По технологии Uhde схема синтеза (запатентованная) включает в себя следующие стадии:
1.На первом этапе компрессия подпиточного газа осуществляется в двухступенчатом компрессоре с внутренним охлаждением. Это корпус низкого давления компрессора синтез-газа. На нагнетании компрессора давление составляет около 11 МПа.
2.Далее газ поступает в однопроходную колонну. Однопроходная колонна с тремя слоями катализатора и с внутренним охлаждением при таком расположении может произвести одну треть от общего количества аммиака. Вследствие низкой концентрации инертных веществ в однопроходной конверсии потребность в катализаторе гораздо ниже, чем в имеющейся технологии низкого давления.
3.Полученный водород с установки продувочного газа возвращается обратно перед однопроходной колонной.
4.Потоки на выходе однопроходной колонны поэтапно охлаждаются противотоком аммиака, и продукционный аммиак отделяется.
5.На втором этапе компрессии непрореагировавший газ сжимается в корпусе высокого давления компрессора, который работает при гораздо меньшей температуре, чем обычно. Преимущество глубокого охлаждения заключается в том, что корпус высокого давления производит больший напор, и это снимает большую часть падения давления при однопроходной конверсии.
6.Далее газ поступает в обычную схему синтеза.
Схема синтеза аммиака работает в нормальном диапазоне давления до 21 МПа. Высокое давление в схеме синтеза достигается сочетанием охлаждения второго корпуса компрессора синтез-газа и немного повышенного давления начального цикла. Необходимое давление начального цикла определяется исходя из опыта фирмы Uhde по производству установок аммиака.
При применении технологии с двойным контуром в настоящее время можно достигнуть производительности 3300 т/сутки, используя действующее на производстве оборудование.
25
Данная технология имеет низкий уровень риска для установок аммиака очень большой мощности.
Концепция низкого давления в сочетании с высокоэффективным катализатором KATALCO 74-1 показала свою эффективность и надежность.
Синтез с низким давлением и катализатором на основе железа остается лучшим вариантом для установок небольших и средних размеров. Технология низкого давления имеет отличные перспективы и для крупных установок, использующих технологию аммиака
сдвойным контуром либо катализаторы с большей активностью.
4.ТЕХНОЛОГИЧЕСКИЕ РАЗРАБОТКИ ФИРМ
KELLOGG BROWN & ROOT, THYSSEN KRUPP UHDE
ИHALDОR TОPSOE
4.1. Технологии аммиака фирмы Kellogg Brown & Root
Фирмой Kellogg Brown & Root (KBR) разработана технология [4, 5], которая включает два новых улучшенных процесса фирмы
Kellogg: The Kellogg Advanced Ammonia Process (KААР) и The Kellogg Reforming Exchanger System (KRES), а также процесс Purifier,
разработанный фирмой Brown & Root [6]. В процессе KААР используется новый катализатор на основе металлического рутения, нанесенного на карбидную основу. В процессе KRES используется вместо трубчатой печи парового риформинга новый аппарат – теплооб-
менный риформер (reforming exchanger).
Разработано несколько вариантов данной технологии.
Основные варианты технологии фирмы KBR
Первый вариант – базовый, он включает традиционную технологию аммиака, которая усовершенствована процессом KААР (рис. 2). На рис. 3 процесс KААР показан более детально.
Особенностями процесса KААР являются: применение одноступенчатого компрессора синтез-газа, использование низкого давления в цикле синтеза, четырехслойной колонны синтеза с радиаль-
26
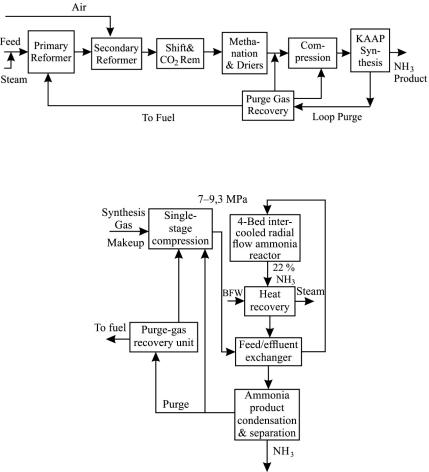
ным ходом газа в слоях катализатора и промежуточным охлаждением между слоями. В первый по ходу газа слой загружен магнетитовый катализатор, в остальные три – рутениевый.
Рис. 2. Блок-схема базовой технологии аммиака, усовершенствованной фирмой Kellogg
Рис. 3. Блок-схема процесса KААР
Второй (улучшенный) вариант технологии предусматривает сочетание процессов KAAP и Purifier и носит название Purifier – KААР (рис. 4).
27
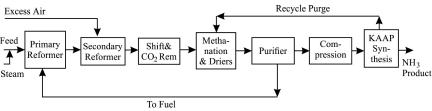
Рис. 4. Блок схема варианта технологии Purifier – KААР
Весьма существенными особенностями этой технологии являются использование на стадии вторичного риформинга избытка воздуха и применение криогенной установки (стадии Purifier) для удаления из синтез-газа избытка азота и инертных примесей. Это перераспределяет нагрузку с первичного на вторичный риформинг, создает условия для большей эффективности процесса синтеза за счет снижения содержания инертных примесей, уменьшает затраты на циркуляцию и на выделение аммиака из газа.
Втретий вариант технологии включены два процесса: KRES и KААР. В технологии аммиака KRES – KААР (рис. 5) предусмотрено использование воздуха, обогащенного кислородом. Это требует наличия на предприятии блока разделения воздуха. Для нормальной работы системы KRES содержание кислорода в обогащенном воздухе должно составлять 30 %. Количество подаваемого обогащенного воздуха должно обеспечивать стехиометрическое соотношение водорода и азота в синтез-газе. В схеме используется четырехполочная колонна синтеза с рутениевым катализатором на трех последних полках.
Вчетвертом варианте технологии синтеза аммиака фирмы
KBR, который назван KPK Process (KRES/PURIFIER/KААР), ис-
пользованы все три новые разработки.
Этот вариант технологии включает в себя следующие основные стадии: компрессия воздуха и природного газа, очистка от серы, автотермический паровоздушный риформинг, паровой риформинг
ваппарате KRES, паровая конверсия СО, очистка от СО2, очистка газа метанированием, осушка синтез-газа на цеолитах, выделение
28
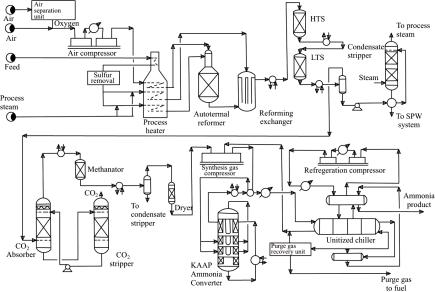
метана, части азота, аргона на криогенной установке, сжатие синтезгаза, синтез аммиака в колонне синтеза KААР, выделение аммиака в холодильном теплообменнике (рис. 6) [5].
Рис. 5. Принципиальная технологическая схема технологии KRES – KААР
К основным показателям процесса относятся:
–температура после автотермического риформинга 965 °С,
–температура газа на выходе из трубчатой части аппарата
KRES 870 °С,
–температура газа на выходе из теплообменного риформера
645 °С,
–степень удаления на криогенной установке компонентов из газа: метана – 100 %, аргона – 60 %, азота – избыток (до удаления H/N = 2, после удаления H/N = 2,9, содержание аргона 0,28 %).
Вреакторе KААР 1-й слой – катализатор на основе железа, 2,
3 и 4-й слои – катализатор на основе рутения; давление синтеза 94 атм; содержание аммиака после колонны синтеза 20–22 % [1].
29
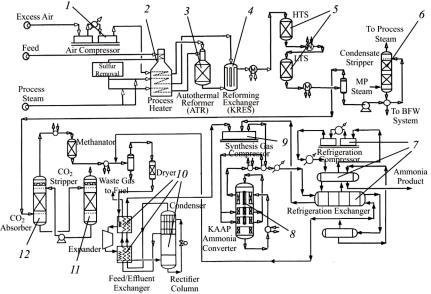
Рис. 6. Технология синтеза аммиака KРK фирмы Kellogg Brown & Root:
1 |
– воздушный компрессор; 2 – подогреватель; 3 – автотермический |
|||
риформер; 4 |
– аппарат |
KRES; 5 |
– аппараты паровой конверсии СО, |
|
6 |
– колонна |
очистки |
конденсата; |
7 – система выделения аммиака; |
8 |
– колонна синтеза KAAP; 9 – компрессор синтез-газа; 10 – система |
|||
|
криогенной очистки газа; 11 – регенератор; 12 – абсорбер |
Еще один (пятый) вариант технологии фирмы KBR применен в Австралии. В нем использована традиционная технология в сочетании с процессом Purifier. Производство построено австралийской фирмой Burrup Fertiliser Pty Ltd и пущено в эксплуатацию в 2006 г. (рис. 7). Его мощность составляет 2200 т/сутки. Это самое крупное производство в мире, использующее процесс Purifier.
Использование процесса Purifier позволяет применить избыток воздуха во вторичном риформинге. Поэтому в производстве предусмотрена подача 50%-ного избытка воздуха. Избыток воздуха увеличивает нагрузку на вторичный риформинг и уменьшает нагрузку на первичный. Это уменьшает размеры трубчатой печи примерно на треть и снижает температуру газа на выходе из печи до 725 °С [6].
30