
книги / Основные новые разработки в технологии аммиака
..pdf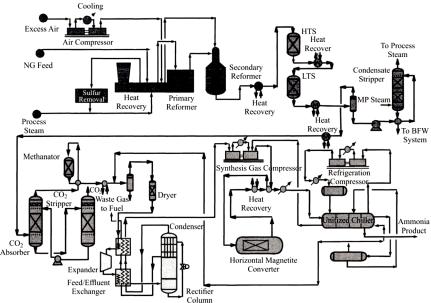
Рис. 7. Принципиальная технологическая схема производства аммиака австралийской фирмы Burrup Fertiliser Pty Ltd
Синтез аммиака осуществляется при давлении 150 атм в горизонтальной колонне синтеза с тремя полками, заполненными магнетитовым катализатором, и двумя теплообменниками для охлаждения газа между полками. Содержание аммиака на входе в колонну составляет 2 %, на выходе 19 %.
Синтез-газ, поступающий в цикл синтеза, содержит 0,25 % аргона, не содержит метана и имеет соотношение H/N = 3.Тепло газа, выходящего из колонны, используется для получения пара высокого давления, затем для нагревания циркулирующего газа и питательной воды. После этого газ окончательно охлаждается в холодильникеутилизаторе жидким аммиаком.
Небольшое количество продувочного газа присоединяется к потоку исходного подпиточного газа на входе в осушитель.
31
Расход природного газа на технологию в тепловом эквиваленте составляет 5,76 Гкал/т, расход газа на сжигание – 1,59 Гкал/т. С учетом выдачи пара на сторону в количестве 0,61 Гкал/т и потребления электроэнергии в количестве 0,04 Гкал/т общие затраты энергии составляют 6,78 Гкал/т.
Технология KRES
Эта технология предусматривает замену радиантной секции первичного риформинга на кожухо-трубчатый теплообменник (риформер).
Чтобы обеспечить необходимую движущую силу для переноса тепла в теплообменнике, на вторичном риформинге необходимо использовать либо обогащенный кислородом воздух, либо избыток воздуха.
Из-за расходов на проведение разделения воздуха KBR предлагает для новых заводов технологию KRES в сочетании с технологией Purifier, что позволяет снизить затраты [2].
Вобычной технологии аммиака паровую конверсию проводят
втрубчатой печи. Этот процесс имеет несколько недостатков. Например, он термически недостаточно эффективен (теплопотери, связанные с размером аппарата), а также есть проблемы с механическим и техническим обслуживанием (замена и чистка трубок). Процесс трудно контролировать, и установки риформинга с печами требуют крупных капиталовложений.
Современные технологии включают использование газовых регенераторов (Gas Heated Reformers (GHR) – дословно «газовые тепловые риформеры»), которые представляют собой трубчатые га- зо-теплообменники. В GHR выходящие газы вторичного риформинга используют для подачи тепла на первичный риформинг [3]. Один из таких риформеров используется в процессе KRES в качестве теплообменника.
Предварительно нагретый и перемешанный поток (рис. 8), состоящий из углеводородного сырья и пара, параллельно и одновременно поступает в теплообменный риформер и в автотермический
32
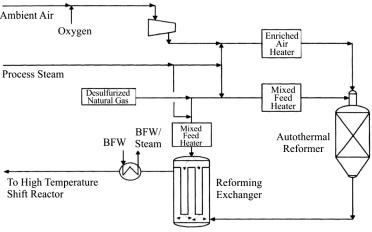
риформер (ATR). Окислитель, который представляет собой воздух, обогащенный кислородом, вместе с паром, и часть углеводородного сырья вводят в виде отдельных потоков в ATR – аппарат вторичного (автотермического) риформинга (паровоздушной конверсии СН4).
Рис. 8. Схема процесса KRES
Из ATR поток выходит с температурой около 940–960 °С, затем поступает в межтрубное пространство теплообменника KRES. Оставшаяся часть углеводородного сырья и пара поступает в трубы теплообменника KRES. В трубном пространстве парогазовая смесь вступает в контакт с катализатором парового риформинга, который используется для ускорения эндотермической реакции. Теплота, требуемая для этой реакции, обеспечивается газами межтрубного пространства, которые представляют собой объединенные потоки из ATR и аппарата KRES. Газы межтрубного пространства после теплообмена с газами трубного пространства поступают на дальнейшую обработку.
Теплообменник (рис. 9) имеет следующие особенности:
Простая конструкция открытых трубок позволяет каждой отдельной трубе расширяться индивидуально. Наличие одной трубной решетки и открытой трубчатой конструкции устраняет любые
33
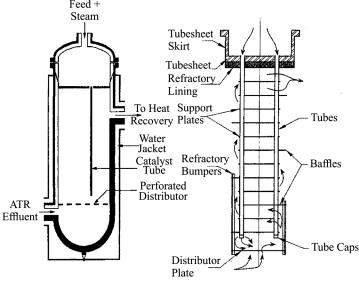
термические напряжения, возникающие в результате разницы температур трубного и межтрубного пространства.
Рис. 9. Устройство теплообменника KRES
Комплект полностью съемный, что позволяет обеспечить легкий осмотр или замену и минимальное время простоя объекта.
Трубная решетка расположена на холодном конце реактора, что приводит к более высокому пределу допустимых механических напряжений.
Трубная решетка представляет собой висячую конструкцию, что позволяет фланцевому соединению работать при равномерной температуре.
Отходящий поток ATR равномерно распределяется по полю пучка с помощью перфорированного распределителя. Это решение было оптимизировано с использованием вычислительной гидродинамики (CFD). Газ после риформинга, выходящий из открытой трубки, дополнительно смешивается с потоком после ATR через перфорированную торцевую крышку, которая разработана специ-
34
ально для интенсивного смешения с потоком из межтрубного пространства.
В конструкцию добавлены дополнительные опоры, что обеспечивает ее жесткость.
Корпус труб футерован двухслойным внутренним материалом. В дополнение корпус теплообменника снабжен водяной рубашкой для обеспечения равномерной более низкой рабочей температуры, а также добавлена защита, чтобы обеспечить нормальное завершение работы в случае поломки футеровки [4].
GHR, и в частности риформер KRES, имеют определенные преимущества перед стандартными трубчатыми печами, что можно увидеть, сравнивая их характеристики (табл. 3).
|
|
Таблица 3 |
Сравнение трубчатых печей для паровой конверсии и GHR |
||
|
|
|
Параметры |
Обжиговые печи |
GHR |
сравнения |
|
|
Размеры |
Большие |
Малые |
Поверхность теплообмена |
Большие |
Меньшие |
и теплопотери |
|
|
Конструкция |
Сложная |
Упрощенная |
Эксплуатационные затраты |
Высокие |
Низкие |
Зона конвекции |
Большая |
Отсутствует |
Капитальные затраты |
Высокие |
Низкие |
Срок службы каталитиче- |
Уменьшенный из-за |
Более длительный бла- |
ских трубок |
высоких температур и |
годаря равномерному |
|
неравномерного рас- |
распределению тепла |
|
пределения тепла |
|
Время простоя, необходи- |
Большое |
Более короткое |
мого для переподключения |
|
|
Обычное производство аммиака с использованием трубчатых печей – это хорошо налаженный процесс, а современные технологии, в которых применяются GHR, еще не получили широкого признания.
35
Технология KААР
Технология KААР основана на использовании катализатора синтеза аммиака высокой активности на основе рутения.
В 1979 г. Бритиш Петролеум обратилась к фирме Kellogg с предложением принять участие в разработке нового рутениевого катализатора. Новый катализатор позволял увеличить скорость процесса синтеза, проводить процесс при более низких температурах. Он мог бы заменить обычные катализаторы на основе железа, которые использовались более чем 80 лет. Было проведено несколько испытаний опытной установки с использованием нового катализатора – рутения, нанесенного на углеродсодержащий носитель с различными промоторами.
Реактор с рутениевым катализатором может быть использован одним из трех способов: в качестве средства для расширения уже существующего производства, как элемент модернизации конструкции к уже существующему заводу или в качестве основной конструкции при строительстве абсолютно нового завода.
В 1988 г. компанией Ocelot Ammonia Company in Kitimat, Бри-
танская Колумбия (теперь известной как Pacific Ammonia Incorporated or PAI), был представлен первый коммерческий проект использования KААР. Завод этой компании по производству аммиака стал местом для первой демонстрации новой технологии. Цикл синтеза имел отдельные потоки для водорода и азота, что позволило испытать реактор KААР при различных соотношениях потоков.
К техническим особенностям процесса KААР относятся: одноступенчатый компрессор синтез-газа, радиальные потоки с промежуточным охладителем, низкое давление цикла синтеза.
Система KААР была успешно запущена в ноябре 1992 г. Она включала в себя реактор KААР, который был установлен после существовавшего конвертера. Реактор KААР имел две полки с радиальным потоком газа и с уникальной запатентованной системой, которая не допускает горячих точек в слое катализатора. В реакторе осуществлялся теплообмен между потоком питания и потоком после первого слоя. Питание реактора KААР содержало 15 % аммиака, на
36
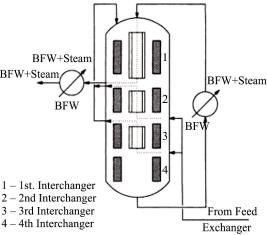
выходе из реактора доля аммиака составляла до 21 %. Добавление в систему реактора KААР и нового котла-утилизатора для производства пара среднего давления позволило увеличить мощность цикла синтеза на 40 % [2].
Проекты новых установок отличаются от модифицированных и расширительных конструкций тем, что они используют на 1-й ступени реактора обычный железный катализатор, на последующих трех – катализаторы на основе рутения (рис. 10). Причиной этого является то, что железный катализатор может обеспечивать высокую скорость реакции синтеза аммиака только при низких концентрациях аммиака. Однако по мере течения реакции концентрация аммиака увеличивается и железный катализатор теряет свою эффективность. Рутениевый катализатор позволяет обеспечить высокий выход аммиака при низких давлениях, ввиду того что его можно использовать при высоких концентрациях аммиака.
Рис. 10. Схема реактора KААР
Поэтому на первой полке помещают обычный магнетитовый катализатор, что позволяет в полной мере использовать высокую скорость реакции синтеза аммиака при низких концентрациях аммиака, на остальных – рутениевый катализатор.
37
Реактор KААР – это конвертер потоков, установленный таким образом, что он работает в серии с действующим магнетитовым конвертером.
Вреактор KААР катализатор загружен в его окисленном состоянии. Поэтому используется свежий синтез-газ, который нагревает слой катализатора до ~300 °С для улучшения процесса. Контур синтеза работает при давлении 2000 psi (13,8 МПа). Частично подогретый поток направляется на вторую полку конвертера, загруженного магнетитовым катализатором, и поступает далее в пароперегреватель и генератор, который генерирует давление 3000 psi (20,7 МПа). Этот поток, содержащий 15 % аммиака, затем переходит в конвертер KААР через боковой вход к первой полке. Когда газ опускается на вторую полку, концентрация аммиака повышается до 19 %.
Втакой схеме требуется непрерывная продувка, потому что
вгазе содержится больше инертов, чем в газе в исходной схеме. После полной модернизации энергетическая экономия состав-
ляет 10550,5 кВт.
Рутениевый катализатор, используемый в KААР, имеет заметно большую площадь поверхности и в 10–20 раз более высокую реакционную способность, чем железный катализатор.
Данная технология работает при более низких температурах и давлениях, давая значительную экономию денег и энергии. Вместо 100–250 атм, как правило, можно использовать давление в 40 атм. Хотя новый катализатор стоит дороже, это компенсируется за счет других сокращений расходов.
Внедрение технологии KААР позволило заводу сохранить 100 % своей производственной мощности с одновременным уменьшением использования пара на 30–40 % и потребления электроэнер-
гии на 5–10 % [3].
Из-за высокой активности рутениевого катализатора в реакторе KААР необходимы тонкие полки для сохранения рабочих температур в пределах предписанного диапазона. В большинстве радиальных реакторов верхняя часть полки заполнена с избытком, который представляет собой неиспользованный катализатор. Это
38
предотвращает подачу газа в обход секции реакции, когда катализатор оседает.
Реактор имеет собственную систему герметизации. Эта технология исключает неравномерное распределение катализатора, что может привести к образованию горячих точек в слое катализатора. Система также позволяет использовать 100 % от загруженного объема катализатора [4].
4.2. Технология аммиака компании Thyssen Krupp Uhde
После слияния компаний Thyssen Krupp и Uhde объединенная компания Thyssen Krupp Uhde является одним из немногих производителей, кто может быть одновременно и лицензиаром технологии и поставщиком оборудования [7].
Основу производств аммиака компании Thyssen Krupp Uhde составляет традиционная технология аммиака, разработанная фирмой Uhde. В дальнейшем компанией в нее были внесены усовершенствования, которые способствовали увеличению эффективности. Основные из них следующие:
1.Смещение части риформирования природного газа водяным паром на вторичный риформинг путем проведения вторичного риформинга с избытком воздуха. Это потребовало установки блока рекуперации продувочного газа, посредством которого водород возвращают на вход компрессора синтез-газа, позволяя тем самым поддерживать соотношение водорода и азота в газе около 3:1.
2.Предварительный нагрев технологического воздуха для вторичного риформинга до более высокой температуры (600 °С), что обеспечивает перенесение части реакции на вторичный риформинг,
атакже приводит к снижению рабочей температуры в главном первичном риформере и, следовательно, к экономии топлива.
3.Использование сниженной начальной нагрузки на паровой риформинг, что позволяет увеличить давление в риформере до 44 бар, сохраняя при этом расчетный срок службы труб риформера до 100 000 ч. Это влечет за собой снижение общего потребления энергии за счет уменьшения количества энергии, необходимой для работы газового компрессора синтеза-газа.
39
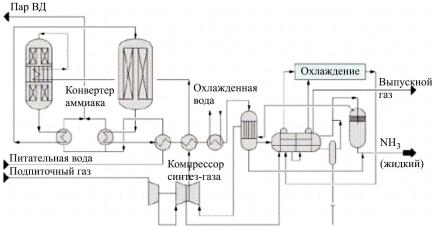
4.Увеличение температуры предварительного нагревания парогазовой смеси, что снижает расход топливного газа в первичном риформинге за счет смещения теплопередачи из радиантной секции
всекцию конвекции.
5.Уменьшение соотношения пар/газ до 3,0. Этого достаточно для предотвращения образования углерода на катализаторе первичного риформинга. Уменьшение примеси пара приводит к тому, что меньше тепла поглощается в основной радиантной секции риформинга и, следовательно, снижается расход топлива. Тем не менее такое соотношение пар/газ достаточно высоко, чтобы свести к минимуму образование побочных продуктов на стадии низкотемпературной паровой конверсии СО даже при использовании неселективных катализаторов [7].
Усовершенствованная схема процесса фирмы Uhde приведена на рис. 11, 12.
Рис. 11. Схема риформингов и паровой конверсии СО в технологии аммиака фирмы Uhde
Наиболее существенным изменениям по сравнению с ранней схемой подвергся узел синтеза аммиака (см. рис. 12).
40