
книги / Технологии и оборудование механической и физико-технической обработки
..pdfзивного микропорошка следует принимать в пределах 0,5–1 г. При этом количество жидкой среды (смеси керосина, масла 20–25 % и олеиновой кислоты 3–5 %) должно быть порядка 3 мл.
Изменение количества абразива незначительно влияет на шероховатость, плоскостность обработанной поверхности.
Абразивные зерна при доводке подвергаются воздействию больших динамических нагрузок, превосходящих их сопротивляемость раздавливанию. Процесс съема материала сопровождается разрушением зерен абразива. В этих условиях максимальные усилия, передаваемые зернами обрабатываемой поверхности, определяются только прочностью самих зерен. Поэтому шероховатость обработанной поверхности с изменением давления изменяется незначительно. Однако при уменьшении контактного давления шероховатость поверхности несколько улучшается, уменьшаются случаи образования отдельных грубых рисок.
Производительность доводки возрастает пропорционально увеличению контактного давления, но до определенного предела (для закаленной стали 6 кг/см2). Дальнейшее увеличение давления не приводит к увеличению производительности, так как затрудняется доступ абразивных зерен в рабочую зону (увеличивается сближение притира с обрабатываемой поверхностью).
Рост производительности доводки с увеличением контактного давления объясняется тем, что по мере увеличения давления, благодаря упругим деформациям притира и детали, возрастает количество абразивных зерен, активно участвующих в работе. Оптимальное давление определяется в каждом конкретном случае экспериментально, так как существенно зависит от материала обрабатываемой детали, притира и характеристики абразива.
С увеличением времени доводки (без замены абразива) суммарный съем материала возрастает, в начальный период интенсивно, а затем с отставанием от времени. Производительность доводки (минутный съем) с увеличением времени снижается. Это объясняется постепенным затуплением и разрушением абразивных зерен, появлением шлама, испарением жидкой среды.
91
Характер изменения минутного съема во времени зависит от материала применяемого абразива. При использовании мягких абразивов минутный съем снижается значительно быстрее, чем при твердых абразивах. Самыми эффективными с этой точки зрения являются алмазные микропорошки, сохраняющие высокую режущую способность наиболее длительное время.
Уменьшение минутного съема с увеличением продолжительности доводки протекает по-разному в зависимости от материала притира. Так, при работе на чугунном притире затухание съема происходит менее интенсивно, чем на стальном закаленном притире. Это следует объяснить большей склонностью чугуна к шаржированию по сравнению с закаленной сталью.
Шероховатость доведенной поверхности по мере увеличения времени обработки снижается, что также связано с постоянным измельчением абразивных зерен.
Формообразование отверстия при хонинговании происходит в результате съема металла при действии комплекса технологических, кинематических, силовых и динамических факторов. Установив связь величины съема в каждой точке обрабатываемого отверстия с различными факторами, можно прогнозировать и управлять формообразованием. Это особенно актуально при окончательной обработке отверстий в деталях топливной аппаратуры, характеризующихся высокими требованиями по точности геометрической формы: отклонение профиля продольного сечения не более 2 мкм, отклонение от круглости 0,5–1 мкм, шерохо-
ватость Ra 0,025–0,04 мкм.
В настоящее время алмазное хонингование подобных деталей применяется главным образом на предварительных операциях [40]. Причины, ограничивающие применение хонингования при окончательной обработке, трудности в стабильном обеспечении требуемой точности геометрической формы, а также образование заусенцев на кромках пересечения обрабатываемой поверхности и радиальных отверстий, которые по техническим условиям не допускаются. Для снятия заусенцев применяют
92
инструмент в виде абразивно-полимерных щеток [41, 42]. Однако щетки сильно закругляют кромки, и стойкость их невелика. Другой способ удаления заусенцев – кинематический [43], когда режущие зерна при хонинговании двигаются по криволинейной траектории вдоль кромки пересечения. Такие условия можно обеспечить при растровом хонинговании.
Сегодня накоплен обширный фактический материал по теории и практике формообразования при хонинговании точных отверстий [30, 44–47], и даны рекомендации по конструкции инструмента, схеме хонингования, соотношению размеров брусков и обрабатываемого отверстия, величине перебега брусков и режимам обработки. Согласно рекомендациям [48], ширину брусков следует определять с учетом диаметра обрабатываемого отверстия и количества брусков в хонинговальной головке. Суммарная ширина комплекта должна составлять 17–35 % от длины окружности обрабатываемого отверстия. Для лучшего исправления овальности рекомендуется четное количество брусков в хонинговальной головке.
Длину брусков следует назначать с учетом длины обрабатываемого отверстия в пределе Lбр = (0,5…0,75)Lотв. При меньших соотношениях Lбр/Lотв обеспечивается более равномерный износ брусков и съем металла по длине отверстия, однако чрезмерное уменьшение длины брусков может привести к сохранению волнистости отверстия. При повышенных требованиях к прямолинейности оси отверстия, а также при хонинговании относительно коротких отверстий длину брусков выбирают в пределах Lбр = (0,8…1)Lотв [30, 34]. Длина перебега брусков по рекомендации [33] назначается в зависимости от длины брусков lп = (0,25…0,5)Lбр. При традиционном хонинговании и доводке направление и скорость вращения за цикл обработки постоянны, а направление и скорость поступательного движения изменяется в точках реверсирования каждого хода инструмента или обрабатываемой детали. Такой характер движений приводит к неравенству пути перемещения и длительности контактирования точек режущей по-
93
верхности инструмента и обрабатываемой поверхности за время одного поступательного хода [45, 47, 49]. Неравномерность контактирования зависит как от кинематических факторов, так и от масштабно-геометрических: соотношения длины отверстия и инструмента, величины осевого хода и перебега брусков.
В ряде работ [32, 34, 48] отмечено повышение эффективности исправления исходной погрешности геометрической формы при алмазном хонинговании. Это объясняется тем, что всякое отклонение вызывает локальное изменение скорости съема металла, направленное на ликвидацию этого отклонения. В начальной стадии обработки взаимодействие поверхностей брусков и детали происходит лишь по отдельным пятнам касания, на которых возникает контактное давление, значительно превышающее номинальное. Для исправления местных отклонений формы отверстия в продольном сечении рекомендуется изменять положение и длину хода инструмента, осуществлять его задержку с осевой осцилляцией, а также изменять давление и скорость вращения [33, 36, 48, 50–52]. В целях повышения производительности исправления исходной погрешности формы целесообразно повышение жесткости инструмента и механизма разжима, а также управление процессом хонингования сучетомсилы резанияиликрутящего момента [30, 41, 53].
В последние годы выполнены комплексные теоретические и экспериментальные исследования с целью повышения точности и качества обработки и создания управляемого процесса алмазного хонингования. В работах [44, 46, 48, 50, 54, 55] отмечается, что в процессе хонингования с уменьшением исходных отклонений формы могут возникать новые отклонения, определяющие точность обработанных отверстий. Причиной появления новых отклонений геометрической формы могут быть неточность станка и его наладки, параметры кинематики и неравномерный износ брусков по длине. Достижение повышенных показателей точности алмазного хонингования возможно путем автоматического управления элементами режима и наладки с учетом реальных условий обработки, при этом важная роль принадлежит сохранению точной
94
формы хонинговальных брусков. В работах [46, 48] показано, что при равномерном распределении следов брусков относительно обрабатываемой поверхности обеспечивается однородная шероховатость, повышается стойкость формы брусков на 50 % и точность обработки. Распределение следов зависит от параметров кинематики процесса хонингования, количества и размеров брусков и размеров обрабатываемой поверхности. Для повышения точности формы отверстий разработаны принципы и рекомендации по построению управляемой технологии алмазного хонингования с использованием станков с ЧПУ и программно-адаптивным управлением, обеспечивающих согласованное регулирование параметров кинематики и давление брусков на этапах цикла хонингования. Это позволило стабильно обеспечивать точность геометрической формы отверстий в пределах 0,004–0,005 мм, но недостаточно для окончательной обработки прецизионных отверстий в деталях топливной и контрольно-измерительной аппаратуры.
5.4. Методы и оборудование для финишной абразивной доводки плоскостей и хонингования отверстий
Установлено, что сложное рабочее движение интенсифицирует процесс резания, способствует повышению точности и производительности обработки и создает условия для управления формированием микрорельефа обработанной поверхности [32, 37, 56, 57]. Сложный характер кинематики доводки и хонингования оказывает благоприятное влияние на эффективность процесса по следующим причинам [34, 58, 59]:
1)обеспечивается более равномерный износ рабочей поверхности инструмента, что способствует повышению точности размеров и формы обрабатываемых деталей;
2)абразивные зерна получают возможность работать большим числом своих вершин и граней, что повышает их режущую способность и стойкость;
95
3)увеличивается число режущих зерен вследствие уменьшения вероятности попадания последующего зерна в след предыдущего;
4)на обрабатываемую поверхность наносится равномерная сетка штрихов, что способствует получению качественно однородной поверхности;
5)уменьшается длина срезаемой каждым зерном стружки вследствие многократного пересечениятраекториидвижения зерен;
6)повышается эффективность действия СОЖ за счет улучшения вымывания шлама из зоны контакта и уменьшения нагрева детали.
Доводочные операции отличаются друг от друга способом нанесения абразивных зерен, методом их закрепления и характером осуществления процесса резания. В зависимости от этих условий различают следующие виды абразивной доводки:
1)доводка с непрерывной подачей абразивной смеси;
2)доводка с нанесением (намазкой) абразивной смеси на
притир;
3)доводка шаржированными притирами;
4)доводка притирами со связанным абразивом в виде специальных мелкозернистых кругов.
Доводочные станки обеспечивают рабочее движение путем комбинации двух-трёх вращательных или поступательных движений. По кинематическому признаку и связанной с ним степенью универсальности плоскодоводочные станки можно разделить на три группы:
1)станки с неподвижными притирами;
2)станки с вращательным движением притира;
3)станки с колебательным движением притира.
Станки с неподвижными притирами в основном применяются при доводке плоскопараллельных концевых мер длины. К ним относятся: двухдисковый станок конструкции завода «Калибр» и станок конструкции Д.С. Семенова. Станки отличаются кинематикой и траекторией рабочего движения.
96
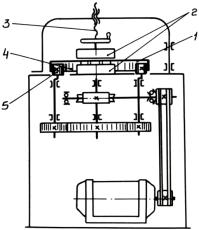
Двухдисковый станок конструкции завода «Калибр» представлен на рис. 5.2, он предназначен для плоскопараллельной доводки. Сепаратор 1 с обрабатываемыми деталями перемещается между двумя неподвижными притирами 2. Давление на детали создается за счет веса верхнего притира и силы сжатия трех пружин, на которые воздействует винт 3. Приводной механизм передает вращение от привода на опорную шестерню 4, связанную внутренним зацеплением с тремя эксцентриковыми шестернями 5. Траектории точек сепаратора представляют собой гипотрохоиды.
Рис. 5.2. Двухдисковый станок для плоскопараллельной доводки
Станок конструкции Д.С. Семенова предназначен для окончательной доводки концевых мер, схема представлена на рис. 5.3. Рабочее движение деталей, расположенных в лентах-сепараторах 1, складывается из двух возвратно-поступательных движений во взаимно перпендикулярных направлениях. В продольном направлении ленты приводятся от барабана 2, в поперечном направлении – от опорных роликов 7, перемещающихся вдоль своей оси. Величина продольного и поперечного ходов регулируется за счет изменения эксцентриситета пальцев кривошипов 4 и 3.
97
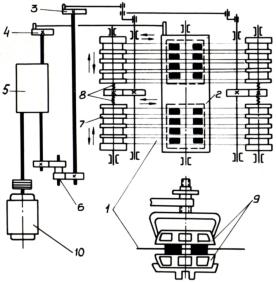
Частота ходов регулируется с помощью коробки скоростей 5 и сменных шестерен 6. В качестве притиров на станке используются чугунные плиты размером 300×300 мм2. Нижний притир расположен на направляющих стола, который перемещается в вертикальном направлении при переналадке станка на детали разной толщины. Верхний притир при доводке свободно лежит на деталях, удерживаясь от смещения коромыслом с захватами, в нерабочем положении притир отводится с помощью поворотной траверсы. Рабочее давление при доводке создается весом верхнего притира и силой сжатия пружин нажимного приспособления. Доводка измерительных плиток на станке Семенова осуществляется с помощью шаржированных притиров. Шаржирование производится вручную, правят притиры также вручную по методу трех плит. При доводке плиток на этом станке достигается высокая точность: отклонение от плоскопараллельности менее 0,1 мкм и чистота поверхности Ra 0,02–0,01 мкм.
Рис. 5.3. Станок конструкции Д.С. Семенова
98
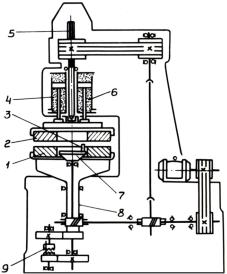
Преимущество этого станка перед двухдисковым станком завода «Калибр» состоит в том, что скорость движения всех деталей здесь одинакова. Доводка осуществляется шаржированными притирами или методом намазки абразивной пасты.
Станки с вращательным движением притира более универсальны и могут применяться как для доводки, так и полировки, поэтому получили широкое распространение. Для плоскопараллельной доводки (одновременной доводки нижнего и верхнего торцов детали) применяются двухдисковые станки. При работе оба доводочных диска (а у ряда моделей станков только нижний диск) совершают вращательное движение. На таких станках производится обработка как плоских, так и цилиндрических деталей, поэтому они считаются универсальными. На рис. 5.4 представлена схема универсально-доводочного станка 3816.
Рис. 5.4. Двухдисковый станок 3816 с вращающимися притирами для плоскопараллельной доводки
Верхний и нижний шпиндели 5 и 8, несущие притиры 2 и 1 приводятся во вращение электродвигателем через ременные и
99
червячные передачи. Верхний притир имеет шарнирное крепление, что позволяет ему самоустанавливаться по деталям, которые расположены в окнах сепаратора и свободно лежат на поверхности нижнего притира. Сепаратор насажен на палец 3 эксцентрика 7, вращающегося от привода шпинделя нижнего притира через муфту 9. При вращении эксцентрика сепаратор с деталями совершает круговые движения и дополнительное медленное вращение за счет трения о притиры.
Рабочее давление при доводке, а также подъём и опускание верхнего притира осуществляются с помощью гидроцилиндров 4 и 6. Правка притиров производится чугунными дисками, которые устанавливаются в специальном сепараторе. Станок может работать с непрерывной подачей абразивной суспензии, для чего предусмотрен бак с мешалкой и системой трубопроводов.
Следует отметить, что вращательное движение притиров отрицательно влияет на точность доводки. Вследствие разных линейных скоростей деталей, находящихся на различном расстоянии от центра вращения притира, съём материала с деталей и износ притира в разных его зонах не одинаковы. Это приводит к значительным колебаниям размеров в партии одновременно обрабатываемых деталей. Для уменьшения разности размеров работают с двумя-тремя перекладками деталей в сепараторе.
Отечественные станки, представляющие данную схему: 3816, 3816П, 3Б816, 3Б814, 3814П, 3817, а также зарубежные станки Norton (США), Hahn&Kolb, Peter Wolters (Германия), Hamai (Япония).
Особенностью станков Peter Wolters является устройство сепараторов, выполненных в виде шестерен 2 (рис. 5.5). Сепарато- ры-шестерни находятся в зацеплении со штифтовыми венцами наружного кольца 3 и внутреннего диска 5. При вращении доводочных дисков 1, 4 сепараторы с деталями совершают планетарное движение, благодаря чему достигается более равномерный износ притиров. Станки с такой кинематикой широко применяются для шлифовки и полировки абразивными суспензиями рабочих поверхностей пластин (шайб) из кристаллических и полупроводниковых материалов для микро- и оптоэлектроники.
100