
книги / Технологии и оборудование механической и физико-технической обработки
..pdf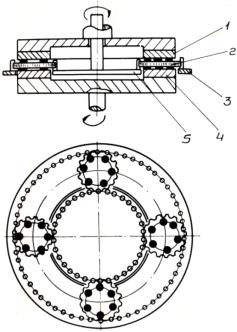
Рис. 5.5. Устройство станков Peter Wolters с планетарными сепараторами
Из однодисковых станков с вращающимся притиром наиболее совершенными являются станки с правящими кольцами. Схема такого станка показана на рис. 5.6. Обрабатываемые детали 5, размещенные в окнах сепаратора 4, устанавливаются внутри правящих колец 3, которые лежат на рабочей поверхности доводочного диска 1. Правящие кольца (в количестве 3–4 шт.) служат для непрерывной правки рабочей поверхности притира во время доводки с целью поддержания её плоскостности. При вращении доводочного диска правящие кольца, удерживаемые опорными роликами 2, вследствие разности окружных скоростей вращаются вокруг собственных осей вместе с обрабатываемыми деталями. В зависимости от характера износа рабочей поверхности притира правящие кольца можно смещать относительно центра, обеспе-
101
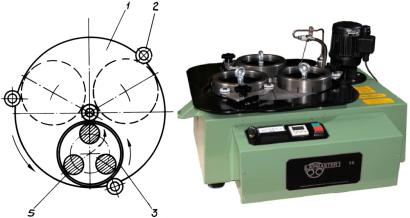
чивая получение правильной геометрической формы рабочей поверхности. Рабочее давление при доводке создается за счет веса детали, лежащей на деталях опорной пластины и грузов.
Рис. 5.6. Однодисковый станок с правящими кольцами
По такой схеме работают отечественные станки моделей СППД-2, 3804П, 3806, 3808, а из зарубежных станков можно от-
метить Lapmaster (Англия, Франция, США), Peter Wolters (Германия), Miсrolap и Superlap (США), Flexibox (Англия). К недос-
таткам этих станков относятся ограниченность (внутренним диаметром правящих колец) размеров доводимых деталей и высокий расход абразивной пасты на доводку самих колец.
Особую группу составляют станки для обработки поверхностей оптических деталей типа ШП, ПД, П и Д [35]. На рис. 5.7 представлена схема оптического шлифовально-полировального станка. При равных угловых скоростях планшайбы 1 с изделием 2 и инструмента 3 их относительное движение не вращательное, а поступательное. Однако, несмотря на равенство относительных скоростей всех точек поверхности, изделие обрабатывается неравномерно вследствие разных степеней перекрытия в центре и на периферии.
102
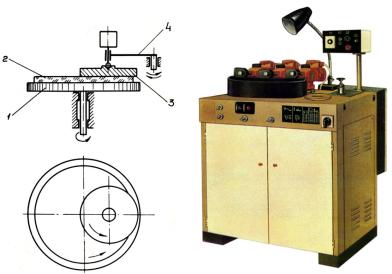
Рис. 5.7. Станок для доводки оптических деталей
Механизм верхнего звена 4 сообщает инструменту или обрабатываемой детали движение подачи и создаёт рабочее усилие. Движение подачи может быть качательным, вращательным или тем и другим одновременно. В механизмах верхнего звена без нагружающего устройства рабочее усилие создаётся грузами, которые устанавливаются на поводок или каретку коромысла.
Большую группу представляют шлифовально-полировальные станки, предназначенные для подготовки поверхностей из различных материалов с целью исследования их микроструктуры. Станки выпускаются различных конструкций и типоразмеров и представлены главным образом зарубежными фирмами: Buehler (США), Struers (Дания), Logitech (Англия), Allied (США) и др.
По исполнению станки предназначены для ручной и механизированной обработки. Отличие заключается в том, что последние снабжены нагружающими устройствами, позволяющими вести обработку в полуавтоматическомрежиме. Большинство шлифовальнополировальных станков имеютнастольноеисполнение (рис. 5.8).
103
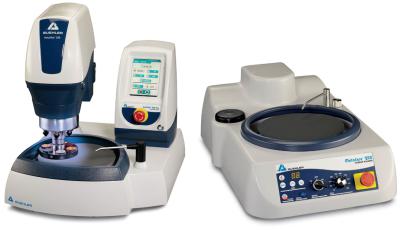
EcoMet250/300 |
MetaServ250 |
Рис. 5.8. Шлифовально-полировальные станки фирмы Buehler
Выпускается также узкоспециализированное оборудование, например полировальная машина фирмы Seikoh Giken (Япония) для шлифования и полирования ферул волоконно-оптических коннекторов. Возможность использования данного оборудования для обработки изделий из других материалов, существенно отличающихся по размерам и конструкции от ферул, связана со значительными трудностями по переналадке.
Станки с колебательным движением притира наиболее универсальны, на них можно обрабатывать детали любой конфигурации и размерами, соизмеримыми с диаметром притира. К такой группе относятся станки с циклоидальной и растровой траекторией рабочего движения инструмента, опытные образцы которых разработаны и изготовлены в ПНИПУ В.П. Некрасовым. Станки предназначены для односторонней доводки методом намазки абразивной смеси на прецизионные плоские поверхности. Они позволяют обрабатывать как отдельные детали, так и партии деталей в многоместных приспособлениях и кассетах, а также осуществлять взаимную правку притиров.
104
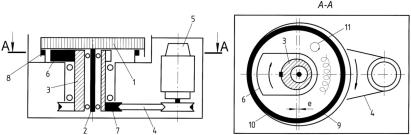
Принципиальная схема доводочного станка с циклоидальной траекторией рабочего движения [60] представлена на рис. 5.9. Доводочный диск-притир 1 закреплен на шпинделе 2, установленном на подшипниках внутри эксцентричной втулки 3, которая ременной передачей 4 связана с электродвигателем 5.
Рис. 5.9. Станок с циклоидальной траекторией инструмента
Для статической и динамической балансировки инерционных сил и их моментов в механизме привода на верхнем конце втулки оппозитно по отношению к смещению шпинделя 2 установлен противовес 6, а на нижнем конце – совмещенный со шкивом дополнительный противовес 7, направленный в сторону смещения. Фрикционная волновая передача 8 состоит из жесткого наружного колеса 9, расположенного по периферии притира, и неподвижно закрепленного, но деформируемого в радиальном направлении колеса 10. Притир совершает поступательное рабочее движение, осуществляющее съем материала, по кольцевой траектории 11 и дополнительное медленное вращение вокруг своей оси, которое обеспечивает равномерное распределение абразивного материала по поверхности притира и его равномерный износ. Результирующие траектории движения точек притира – это эпициклоиды в виде кольцевых спиралей.
Станки с растровой траекторией рабочего движения выполнены двух типоразмеров, с диаметром притира 350 мм и 220 мм. На рис. 5.10 представлен станок «Растр 220» настольного исполнения с диаметром притира 220 мм.
105
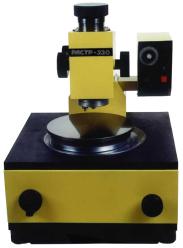
Рис. 5.10. Плоскодоводочный станок «Растр 220»
В качестве инструментов используются легкосъемные доводочные диски из чугуна, закаленной стали, оптического стекла, композиционных материалов, а также диски с закрепленным абразивным слоем. Доводочный диск (притир) установлен на шариковых опорах и приводится в движение двумя взаимно перпендикулярными шатунами, которые сообщают ему гармонические колебания с различными частотами. В результате инструмент совершает поступательное движение, а каждая его точка описывает неповторяющуюся траекторию, имеющую вид сетки сложной конфигурации с тонко регулируемыми параметрами. Нажимное устройство создаёт необходимое усилие прижима и сообщает обрабатываемым деталям дополнительное медленное круговое перемещение за счет сил абразивного трения, что способствует более равномерному износу поверхности притира.
Основные показатели процесса хонингования – точность, производительность, параметры шероховатости обрабатываемых поверхностей существенно зависят от кинематики станка, определяющей траекторию относительного движения инструмента и
106

обрабатываемой поверхности детали. Как было сказано выше, сложное рабочее движение интенсифицирует процесс резания, способствует повышению точности и производительности обработки и создает условия для управления формированием микрорельефа обработанной поверхности.
Хонинговальные станки обеспечивают сложное рабочее движение путем комбинации вращательного, возвратно-поступа- тельного и одного или двух колебательных движений.
По кинематическому признаку методы хонингования делятся на две основные группы [34]:
а) традиционный метод хонингования; б) вибрационные методы хонингования.
Традиционный метод хонингования наиболее распространен, так как большинство хонинговальных станков, выпускающихся как у нас, так и за рубежом, не снабжены механизмами осцилляции [34, 57]. При традиционном методе хонингования траектория рабочего движения инструмента образуется в результате вращения и возвратно-поступательного движения вдоль оси обрабатываемой детали. Такая кинематика обусловливает типичную для традиционного хонингования сетку следов обработки в виде пересекающихся винтовых линий. Единственным параметром траектории, позволяющим в какой-то мере варьировать количественные и качественные показатели процесса, является угол скрещивания следов обработки 2α, зависящий от соотношения скоростей вращения Vкр и скорости возвратно-поступательного движения Vос. Скорость резания V является геометрической суммой скоростей вращения и возвратно-поступательного движения инструмента:
V = V 2 |
+ V 2 |
; |
α = arctg Vос . |
кр |
ос |
|
Vкр |
|
|
|
При повторных ходах возможно совпадение или смещение фаз положений брусков. Это зависит от размера брусков, их количества и от соотношения скоростей вращательного и возврат- но-поступательного движений [48, 61]. Поэтому при заданных
107
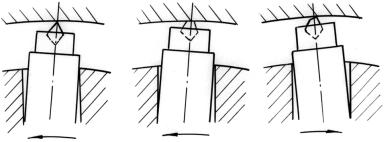
условиях обработки определяется оптимальное значение Vос из
Vкр
условий обеспечения наименьшего относительного смещения фаз положений брусков и количества двойных ходов, необходимое для равномерного заполнения обрабатываемой поверхности следами резания. Это способствует снижению шероховатости и повышению точности формы
При традиционной кинематике режущая способность брусков используется не полностью, так как наибольшее участие в резании принимают зерна, встречные направлению движения, а остальные – меньше, поскольку попадают во впадины, образованные предыдущими зернами. Для интенсификации процесса и более полного использования режущей способности инструмента при традиционном методе хонингования применяют схему обработки с периодическим реверсированием вращения [35]. На рис. 5.11 схематично изображено контактирование отдельного зерна с обрабатываемой поверхностью в трех различных фазах.
а |
б |
в |
Рис. 5.11. Схема контактирования режущего зерна при традиционном методе хонингования с периодическим реверсированием вращения: а – начало работы зерна; б – притупившееся зерно; в – контактирование зерна при реверсе вращения
В результате более интенсивного самозатачивания брусков при увеличении частоты реверсирования относительный износ
108
брусков возрастает. Шероховатость поверхности изменяется незначительно. Необходимо также отметить, что с увеличением частоты реверсирования процесс хонингования приобретает более динамичный характер, поэтому большое значение имеет правильный выбор характеристики брусков.
Вибрационное хонингование осуществляется путем наложения на основные движения дополнительных колебательных движений. Методы вибрационного хонингования могут быть классифицированы по характеру осциллирующего движения. Известны схемы вибрационного хонингования с осевой, круговой, радиальной и комбинированной осцилляцией. Наиболее изучен процесс вибрационного хонингования с осевой осцилляцией [34, 60, 62–64]. Процесс исследован в широком диапазоне частот
иамплитуд колебательных движений – от низкочастотных колебаний с амплитудой в несколько десятков миллиметров до ультразвуковых колебаний с амплитудой в несколько микрон.
По сравнению с традиционным хонингованием виброхонингование с осевой осцилляцией позволяет существенно увеличить производительность процесса, в 1,5–2 раза [60, 62, 65], по мере увеличения частоты и амплитуды колебаний. Интенсивность износа брусков при этом также увеличивается, но в меньшей мере, чем съем металла. Положительным является также то, что при виброхонинговании съем металла носит незатухающий характер
исо временем изменяется незначительно, особенно при ультразвуковых колебаниях [63, 64, 66]. В работе [65] приведены результаты исследований по управлению формой отверстия в продольном сечении при хонинговании с осевой осцилляцией путем регулирования времени задержки поступательного движения в точках реверсирования. Такой прием при традиционной кинематике неэффективен, так как во время задержки хода абразивные зерна перемещаются по кольцевым рискам, и съем металла резко падает. Результаты исследований показали, что точность формы отверстия при вибрационном хонинговании при прочих равных условиях по сравнению с традиционным хонингованием повыси-
109
лась в два раза. Сравнительные результаты съема металла при хонинговании с различными видами осцилляций, осевой, радиальной и комбинированной (осевая с радиальной), показали целесообразность применения осевой осцилляции [34].
Для хонинговальных станков в большинстве случаев применяются нерезонансные механизмы осцилляции как для осевых, так
идля круговых колебаний. Механизмы осцилляции с резональными колебаниями, как правило, не допускают перестройки частоты
иамплитуды колебаний, и поэтому мало распространены. Нерезонансные механизмы выполняются обычно с регулируемыми параметрами и надежно работают в диапазоне частот 1–1000 Гц при амплитудах до 20 мм. При проектировании регулируемых механизмов с нерезонансными колебаниями следует исходить из оптимальной амплитудно-частотной характеристики, предельной по мощности и усилию колебаний. При этом необходимо учитывать, что при увеличении частоты мощность, расходуемая на резание, растет значительно медленнее, чем мощность колебаний, поэтому с повышением частоты к.п.д. механизма осцилляции уменьшается [67]. Это связано с тем, что инерционные нагрузки, определяемые массой колеблющихся частей, в большей мере зависят от частоты колебаний и меньше от амплитуды. Поэтому, видимо, виброхонингование с осевой осцилляцией рекомендуется применять при обработке отверстий с диаметром до 50 мм [34, 37].
Хонингование с осевой осцилляцией было реализовано на ранее выпускающихся вертикальных хонинговально-доводоч- ных станках ОЗПС моделей 3820, 3821. Параметры колебаний: амплитуда 0–4 мм; частота 250–630 кол/мин. На станках новой гаммы осцилляция отсутствует, хотя, как было отмечено выше, осцилляция может существенно повысить производительность обработки.
Внастоящее время осевая осцилляция применяется на вертикальных и горизонтальных хонинговальных станках фирмы
Sunnen products company, а также на станке модели «Хон-1», ко-
торый разработан и выпускается Владимирским ВПКО «Техни-
110