
книги / Технологии и оборудование механической и физико-технической обработки
..pdf
зультате искажения профиля лунок. Первая группа неровностей взначительной степени будет определятьсяразмерами лунок: rл, hл, β. С использованием данных факторов становится возможным определение параметров шероховатости. Вторая группа неровностей полностью обусловлена случайными факторами, определение которых практически невозможно. Таким образом, реальный профиль шероховатости можно разделить на две составляющие: систематическую и случайную. Случайная составляющая профиля шероховатости составляет примерно 10–15 % от систематической[24].
Шероховатость зависит в первую очередь от энергии импульса и свойств обрабатываемого материала [20]:
R = |
β2 |
k |
|
3 W , |
(4.4) |
3 |
|
||||
z |
|
4 |
и |
|
где β – коэффициент перекрытия лунок (для максимальной шероховатости β = 1,2); k4 – постоянная величина, не зависящая от длительности и энергии импульса (значения коэффициента k4 для различных материаловприведены в табл. 4.2); Wи – энергия импульса.
Чем выше электроэрозионная обрабатываемость материала, тем большую высоту микронеровностей имеет обработанная поверхность. Стоит отметить, что параметры шероховатости поверхности, обработанной электроэрозионным способом, существенно отличаются от параметров поверхностей, обработанных резанием и виброобкатыванием.
Таблица 4.2
Значения коэффициента k4
|
|
Материал заготовки |
k·103, см/Дж1/3 |
Al |
12–15 |
Cu |
6–8 |
Fe |
5,5 |
Ni |
67 |
Сталь 45 |
5–6 |
ВК-6 |
1,5–2 |
ВК-15 |
2,5–3 |
51
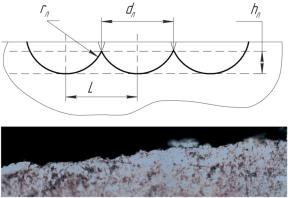
На рис. 4.7 представлены общая схема формирования параметров шероховатости поверхности и реальный профиль обработанной поверхности.
Рис. 4.7. Схема формирования параметров шероховатости
иреальный профиль обработанной поверхности
Сувеличением энергии импульса Wи шероховатость обработанной поверхности возрастает. Это объясняется тем, что с увеличе-
нием Wи будет выделяться большее количество теплоты в течение одного импульса, следовательно, будет наблюдаться большее проплавление металла, что, в свою очередь, приведет к увеличению ра-
диуса лунки rл и, как следствие, коэффициента перекрытия β. Таким образом, для получения меньших значений параметров шероховатости необходимоправильно подбиратьрежимобработки.
На рис. 4.8 представлена номограмма режимов и технологических характеристик при обработке стали 45 медным ЭИ на чистоте 400 имп/с (режим по току до 600 А). С использованием номограммы
режим обработки выбирается следующим образом: при расчетной площади обработки Fр = 100 см2 поднимаются от точки 100 см2 нижней шкалы по вертикали до пересечения с наклонной прямой, затем по горизонтали перемещаются влево до пересечения со шкалой тока и определяют Iср = 270 А. Следуя по горизонтали по правой
52
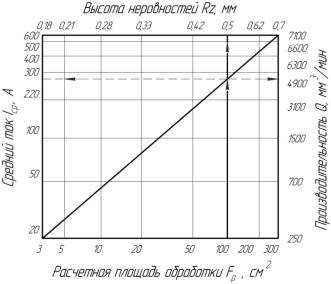
шкале, находим производительность Q = 4300 мм3/мин. На верхней шкале показана высота неровностей Rz, которая для рассматриваемогопримера равна0,5 мм [17].
Рис. 4.8. Номограмма режимов и технологических характеристик
Условно режимы ЭЭ-обработки делят на чистовую, черновую и доводочную, но возможно и другое разделение, например на жесткие, средние, мягкие.
Еще одним важным фактором, оказывающим влияние на параметры шероховатости обрабатываемой детали, является износ электрода инструмента.
В работе [26] исследовался процесс изменения свойств ЭД и ЭИ при проволочно-вырезной электроэрозионной обработке. Установлено, что с увеличением средней силы тока (следовательно, и увеличением Wи) при обработке стали 40Х происходит разрушение электрода-инструмента (рис. 4.9), что существенным образом отражается на величине Rz.
53
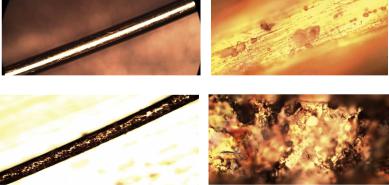
а
б
Рис. 4.9. Разрушение электрода-инструмента: а – новый ЭИ
(×100, ×1000); б – ЭИ после черновой обработки (×100, ×1000)
Изученные параметры для каждого материала не являются постоянными и изменяются в пределах исследуемых режимов обработки в большей или меньшей степени.
4.6.Структура и свойства поверхностного слоя обработанной поверхности после ЭЭО
Как установлено многими исследователями [17, 19, 24], свойства поверхностного слоя существенно изменяются в результате ЭЭО. Однако в полной мере свойства этого слояне определены. Для удобства изучения исследователи разбивают этот слой на зоны. Одни ученые делят его на белый слой и зону термического влияния, другие выделяют в нем несколько зон с различной структурой, третьи отмечают, что он состоит из расплавленного слоя, зоны, подвергшейся химическому воздействию, зоны макродеформации, зоны микродеформацииит.д. [24].
На основе изложенного представляется возможным условное разделение поверхностного слоя после ЭЭО по толщине на следующие зоны (рис. 4.10) [26]: 1 – зону насыщения элементами рабочей жидкости; 2 – зону отложения материала ЭИ; 3 – белый слой, образованный из расплавленного материала ЭД; 4 – зону
54
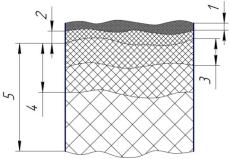
термического влияния; 5 – зону пластической деформации. Последовательность образования зон, их количество, структура и свойства в значительной мере зависят от обрабатываемого материала, а также от режима обработки, применяемой РЖ, материала ЭИ и условий ведения процесса. Между зонами, как правило, нет четкой разницы, а в большинстве случаев они перекрывают друг друга. Вместе с тем каждая из перечисленных зон имеет свои особенности, влияющие на те или иные свойства поверхности и во многих случаях определяющие возможность успешной эксплуатации детали. При этом каждая зона, даже незначительной толщины, играет важную роль [24].
Рис. 4.10. Схематическое расположение зон поверхностного слоя после ЭЭО
4.6.1. Зона насыщения элементами рабочей жидкости
Зона насыщения элементами рабочей жидкости (зона 1, см. рис. 4.10) определяется тем, что вследствие мощного теплового воздействия при выделении электрической энергии в процессе ЭЭО рабочая жидкость разлагается. Отдельные ее элементы проникают в поверхностный слой заготовки, диффундируют в него и образуют с обрабатываемым материалом химические соединения. Замечено отложение углерода в виде сажи на поверхности заготовки, обрабатываемой электроэрозионным способом на ряде режимов. Углерод образовывался в результате разложе-
55
ния минерального масла, используемого в качестве РЖ. Это, наряду с другими явлениями, приводило в процессе ЭЭО на ряде режимов к шлакованию МЭЗ, что нарушало стабильность процесса. Кроме того, углерод диффундировал в поверхностный слой, образуя карбиды [10].
При ЭЭО в смеси воды с индустриальным маслом 12 на обрабатываемых поверхностях образцов также отлагаются продукты разложения используемой РЖ в виде темных пятен. Эти пятна легко удаляются с поверхности.
Вследствие хрупкости и неравномерной плотности в ряде случаев поверхностный слой может быть дефектным. Он снижает прочностные свойства основного металла, так как при механических, особенно знакопеременных, нагрузках в нем легко возникают трещины, которые могут распространяться в глубь детали. Поэтому при изготовлении деталей, предназначенных для работы с большими нагрузками, обычно приходится удалять измененный слой одним из способов отделочной обработки или использовать наиболее современныеЭЭ-технологии исоответствующееоборудование[3].
4.6.2. Зона отложения материала электрода-инструмента
Образование второй зоны (см. рис. 4.10), которая характеризуется присутствием материала ЭИ, связано с переносом части энергии на заготовку факелами, состоящими из паров материала ЭИ. Материал ЭИ может не только концентрироваться на поверхности заготовки, но и диффундировать в более глубокие слои, например в слой расплавленного материала заготовки, и образовывать там различныефазы– твердыерастворы, соединенияи т.п.
В работе [26] исследовалось изменение химического состава поверхностного слоя стальной заготовки после ее обработки на проволочно-вырезном электроэрозионном станке при разных режимах (I – чистовой, II – получистовой, III – черновой). В качестве электрода-инструмента была выбрана латунная проволока.
56
В табл. 4.3 представлены данные об изменении химического состава поверхностного слоя новой и обработанной заготовки.
|
|
|
|
Таблица 4.3 |
Химический состав поверхностного слоя заготовок |
||||
|
|
|
|
|
Образец |
Новый |
Режим I |
Режим II |
Режим III |
Основа |
Fe |
Fe |
Fe |
Fe |
Cr, % |
1,1 |
1,0 |
1,0 |
1,1 |
Mn, % |
0,8 |
0,6 |
0,6 |
0,6 |
Si, % |
0,3 |
0,3 |
0,3 |
0,3 |
Cu, % |
0,2 |
3,6 |
3,7 |
7,3 |
Ni, % |
0,1 |
0,1 |
0,1 |
0,1 |
Zn, % |
0 |
6,1 |
4,8 |
4,8 |
Как видно из табл. 4.3, стальные детали можно насыщать не только медью, но и другими элементами, содержащимися в элек- троде-инструменте.
При обработке стальных деталей электродом-инструментом из графитизированного материала марки ЭЭГ и МПГ и других углеграфитовых композиций углерод, диффундируя в глубь обрабатываемойповерхности, обусловливает образованиекарбидов.
Образование зоны проникновения металла существенно влияет на свойства поверхностного слоя, а следовательно, на эксплуатационные свойства изготавливаемых деталей.
4.6.3. Белый слой
Толщина белого слоя (зона 3, см. рис. 4.10) металла зависит от величины Wи и tи, а также от температуропроводности материала заготовки. После удаления микропорции металла на поверхности заготовки появляется зона со структурой, резко отличающейся от исходной [24]. Белый слой, как правило, имеет мелкозернистую структуру, обладающую высокой химической стойкостью, что затрудняет ее выявление путем травления. На микрошлифах этот слой имеет вид белых полос, откуда он и получил свое название (рис. 4.11).
57
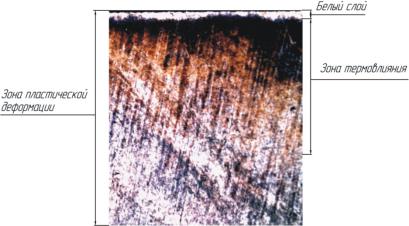
Рис. 4.11. Схематическое расположение зон поверхностного слоя после ЭЭО
В белом слое легко образуются сплавы компонентов материала с материалом электрода-инструмента и элементами рабочей жидкости, а также карбиды и окислы.
При обработке стали на мягких режимах (при Wи < 0,1 Дж
иtи < 100 мкс) белый слой располагается на поверхности заготовки отдельными участками толщиной от нескольких до 40–50 мкм
идлиной до 250–260 мкм. Размеры оплавленных участков, образовавшихся при обработке различных сталей, неоднородны, зависят от многих факторов (главным образом от свойств РЖ, ЭИ, ЭД
иособенно от режимов обработки). На грубых режимах белый слой может сплошь покрывать обработанную поверхность.
Используя современные технологии и оборудование, процесс образования белого слоя можно свести к минимуму или исключить полностью.
4.6.4. Зона термического влияния
Зона термического влияния значительно превышает по размерам белый слой (см. рис. 4.11). На структуру рассматриваемой зоны оказывают влияние материал обрабатываемой заготовки, его исход-
58

ное состояние, свойства рабочей среды, а также режимы обработки. Глубина структурных изменений определяется толщиной слоя металла заготовки, температура в которой превышает температуру структурных изменений. В первом приближении глубину Нт зоны термического влияния можно определить исходя из следующих соображений. Теплота, выделяющаяся при электрическом разряде, проникаетвобрабатываемуюзаготовку наглубину Н0 [10]:
H0 = 40 πtиа, |
(4.5) |
где tи – длительность импульса, мкс; а – коэффициент температуропроводности, см2/с.
После удаления микропорции металла объемом, ограниченным размерами единичной лунки глубиной hл, величина Нт будет определяться выражением
HT = H0 − hл. |
(4.6) |
На мягком режиме обработки зона термического влияния имеет малые размеры, что обусловливает близкие по величине высокие скорости охлаждения всех участков рассматриваемой зоны. В итоге при обработке стали У10 импульсами энергии Wи < 10–3 Дж в зоне термического влияния образуется мелкозернистая мартенситная структура.
Отмечено [24], что при обработке стальных деталей и использовании малых tи и Wи в углеродсодержащих рабочих жидкостях мелкозернистая мартенситно-тростниковая структура образуется независимо от исходной твердости обрабатываемой детали. С ростом tи (при соответствующем увеличении Wи) картина изменяется: растет толщина рассматриваемой зоны, различные ее участки начинают охлаждаться с существенно отличающимися друг от друга скоростями, что обусловливает образование разнообразнейших структур металла.
При обработке стали импульсами Wи = 10–2…10–3 Дж толщина зоны термического влияния возрастает. После обработки в мине-
59
ральных маслах и керосине увеличивается количество остаточного аустенитав структуре, зачастуювыходящегона поверхность.
Взависимости от условий ведения ЭЭО зона термического влияния имеет закаленные участки с мелкозернистой структурой, участки вторичной закалки, которые зачастую при обработке на грубых режимах чередуются с участками отпуска.
Витоге после ЭЭО углеродистой стали появление тех или иных структур и их чередование в пределах зоны термического влияния будут определяться состоянием стали, режимом обработки
исвойствами рабочей жидкости. Последовательность расположения
структур от поверхности в глубь металла после обработки закален-
ной стали на мягких режимах (Wи < 10–3 Дж) в углеродсодержащих РЖ в основном будет следующей: мартенсит, основной металл; при обработке на более грубых режимах: аустенит, мартенсит, троститосорбит, отпущенныйметалл, основнойметалл [24].
При обработке в углеродосодержащих РЖ на грубых режи-
мах при Wи в несколько джоулей на поверхности образуется ледебурит, после которого следуют указанные выше структуры. При обработке незакаленной углеродистой стали расположение структурных составляющих аналогично вышеприведенным, отличие заключается в отсутствии зоны отпуска.
Толщина зоны влияния у закаленной стали больше, чем у незакаленной, в связи с нагревом основной структуры (мартенсита) до температуры ниже критических точек [24].
4.6.5.Зона пластической деформации
Впроцессе ЭЭО металл испытывает значительные ударные воздействия, связанные с перемещением волны напряжений от расширения и сжатия металла при нагреве и охлаждении обрабатываемой заготовки под воздействием электрического разряда; от давления газа, образовавшегося в результате испарения рабочей жидкости; от давления струй факелов, движущихся со скоростью, близкой к скорости звука; от возникающих в процессе обработки электростатических и электромагнитных сил, а также от проте-
60