
книги / Технологии и оборудование механической и физико-технической обработки
..pdfРазличают скважность импульсов по ЭДС и по току. В первом случае скважность характеризуется при холостом ходе генератора, во втором – при нагрузке. Диапазон применяемых скважностей при электроэрозионнойобработкенаходится в пределах от1 до 30.
Частота импульсов f (измеряется количеством импульсов в секунду) определяется заданными длительностью и скважностью импульсов:
f = |
1 |
= |
1 |
. |
(4.16) |
T |
|
||||
|
|
qtи |
|
Амплитуда импульса – наибольшие значения, которых достигают изменяющиеся во времени величины тока или напряжения. Амплитуда импульсов тока изменяется при ЭЭО от единиц до тысяч ампер, а амплитуда импульсного напряжения – от десятков до нескольких сотен вольт [10].
Энергия импульса – это работа, совершаемая единичным импульсом в МЭП, Дж. Как указывалось ранее,
tи |
|
Wи = U I dtи. |
(4.17) |
0 |
|
При технологических расчетах пользоваться этой величиной неудобно, и ее заменяют эквивалентной ей величиной средней мощности Рср или средним током Iср:
Pср = UсрIср. |
(4.18) |
Производительность ЭЭО оценивается отношением объема или массы удаленного материала ко времени обработки, но в случае проволочно-вырезной ЭЭО под производительностью понимают отношение площади боковой поверхности паза ко времени обработки.
На производительность ЭЭО Q существенное влияние оказывают площадь обрабатываемой поверхности и состояние РЖ.
81
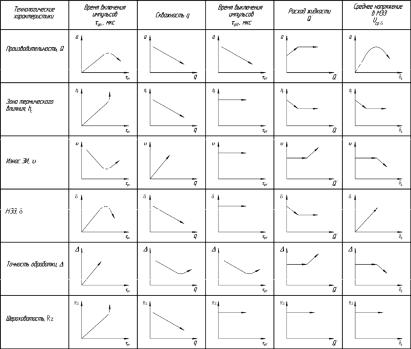
Для достижения высокой производительности необходимо правильно выбрать сочетание площади обрабатываемой поверхности и подводимой мощности.
Рис. 4.19. Основные зависимости между технологическими характеристиками и параметрами ЭЭО
Основные зависимости между технологическими характеристиками и параметрами ЭЭО представлены на рис. 4.19.
82
ГЛАВА 5. СОВРЕМЕННОЕ ПРЕДСТАВЛЕНИЕ О ПРОЦЕССЕ ФИНИШНОЙ АБРАЗИВНОЙ ОБРАБОТКИ ПРЕЦИЗИОННЫХ ПОВЕРХНОСТЕЙ ПОСТОЯННОЙ КРИВИЗНЫ
5.1. Сущность процесса абразивной доводки плоскостей
Развитие науки и техники сопровождается непрерывным повышением требований к качеству изготовления деталей машин и приборов. Так, особую роль в технологическом процессе изготовления деталей играют чистовые и отделочные методы обработки; наиболее распространенными в производстве процессами окончательной обработки поверхностей является процесс абразивной доводки и полирования.
Абразивная доводка является окончательным методом обработки, обеспечивающим высокую точность геометрической формы поверхности 2–0,2 мкм (отклонение от плоскостности, прямолинейности), качество поверхностного слоя глубиной от 2–3 до 0,5–0,05 мкм и малой шероховатости Ra 0,25…0,008 мкм. Особенно целесообразно применение операции абразивной доводки при обработке тонких и легко деформируемых деталей, а также в случаях, когда необходимо сохранить специальные свойства исходного материала, изменяющиеся при значительных тепловых и силовых воздействиях, или удалить слой металла, образовавшийся при предшествующей обработке.
Особенность этого процесса состоит в том, что абразивные зерна (а точнее, смесь зерен с компонентами пасты или смазы- вающе-охлаждающей жидкости) под воздействием притира осуществляют съем металла. Притир не только сообщает зернам необходимые движения и усилия, но и обеспечивает требуемую точность обработки поверхности.
Процесс съема материала (формирование обработанной поверхности) при доводке осуществляется в результате действия аб-
83
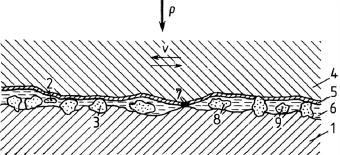
разивных зерен, химически активных элементов и рабочей поверхности притира на обрабатываемую поверхность (рис. 5.1) [29].
Рис. 5.1 Схема доводки: 1 – притир; 2 – стружка; 3 – шаржированное абразивное зерно; 4 – обрабатываемая деталь; 5 – размягченный под химическим воздействием слой материала; 6 – жидкая фаза с химически активной добавкой; 7 – размягченный под воздействием трения слой материала; 8 – перекатывающееся абразивное зерно; 9 – осколок абразивного зерна
К числу общих признаков, характеризующих процесс абразивной доводки, относятся [30]:
1)одновременное воздействие на поверхность детали большого числа режущих зерен, протекающее при относительно низких скоростях и давлениях;
2)движение режущих зерен по сложным траекториям;
3)незначительная роль тепловых явлений и отсутствие связанных с ними структурных изменений в поверхностном слое металла (как при шлифовании, точении, фрезеровании).
На основании имеющихся результатов исследований и производственного опыта можно считать, что процесс доводки состоит из механических и химических явлений.
Механические явления сводятся к микрорезанию металла абразивными зернами с отделением мельчайших стружек либо к трению с изнашиванием обрабатываемой поверхности вследствие многократных пластических деформаций. Соотношение между процессами резания и трения определяется свойствами обраба-
84
тываемого материала, геометрией и физико-механическими свойствами абразивных зерен, рабочим давлением и скоростью резания при доводке. Доводка резанием более производительна, но дает более высокую шероховатость поверхность, доводка же трением с изнашиванием, наоборот, менее производительна, но зато дает более низкую шероховатость.
Химические явления при доводке заключаются в чрезвычайно быстром (сотые доли секунды, порядка 0,05) образовании окисных пленок (1–1,5 нм) и адсорбционных слоев (10–20 нм), которые затем удаляются движущимися абразивными зернами. При этом существенная роль принадлежит жидким компонентам, входящим в состав пасты или суспензии, их составу и химической активности. Жидкие компоненты в процессе доводки выполняют следующие функции [30]:
1)подводят абразивные зерна в рабочую зону, равномерно распределяют их по поверхности притира и создают зазор между притиром и деталью, необходимый для размещения и движения абразивных зерен;
2)образуют поверхностные пленки и проникают в микротрещины обрабатываемого материала, что способствует его более интенсивному разрушению, т.е. повышают производительность доводки; создают так называемое адсорбционное пластифицирование поверхностного слоя вследствие эффекта Ребиндера;
3)создают смазывающий слой, предохраняющий металлические поверхности детали и притира от непосредственного контакта, приводящего к их схватыванию и повреждению;
4)удаляют отходы процесса – частицы металла и абразива, (постоянной подачей сусппензий);
5)охлаждают в процессе работы деталь и притир. Образующийся на поверхности детали тончайший гранич-
ный слой смазки снижает режущее действие абразивных зерен и способствует получению менее шероховатой поверхности.
85
5.2. Сущность процесса хонингования отверстий
Хонингование – это сложный механический процесс удаления припуска с обрабатывающей поверхности посредством массового динамического воздействия абразивных зерен, базирующихся на рабочей поверхности бруска в закрепленном состоянии, на поверхностный слой обрабатываемой детали при их относительном перемещении под нагрузкой [31, 33]. Кинематика процесса включает три основных движения: вращение, возвратно поступательное движение и радиальное перемещение брусков с целью создания необходимого контактного давления абразивных зерен на обрабатываемую поверхность. При этом хонингование сопровождается, как правило, обильной подачей в зону контактирования смазочно-охлаждающей жидкости, чем обеспечивается удаление продуктов износа, снижение силы трения и температуры в зоне контакта и улучшение условий микрорезания металла абразивными зернами.
Наиболее близким по технической сущности процессом чистовой обработки брусками цилиндрических поверхностей является суперфиниширование [31]. При общности механизма абразивного воздействия процессы хонингования и суперфиниширования имеют различие в принципах замыкания контактируемых поверхностей брусков и детали [31]. Для суперфиниширования характерна схема силового замыкания контакта через упругий элемент, при которой величина нормальной нагрузки сохраняется постоянной независимо от исходной погрешности формы обрабатываемой детали. При хонинговании применяют схему кинематического замыкания контакта, в результате контактные давления между брусками и деталью функционально связаны с исходной погрешностью формы обрабатываемой детали, т. е. процесс хонингования, обладая высокой чувствительностью к погрешностям геометрической формы поверхности, обеспечивает интенсивное их исправление [32–34].
86
К числу общих признаков, характеризующих процессы абразивной обработки брусками, относятся:
1)большая поверхность контакта инструмента с обрабатываемой поверхностью;
2)одновременное воздействие на обрабатываемую поверхность большого числа режущих зерен, различных по форме и имеющих определенное вероятное распределение по высоте;
3)сложная траектория движения режущих зерен при относительно низких скоростях;
4)невысокая температура в зоне обработки и отсутствие в связи с этим фазовых превращений и структурных изменений в поверхностном слое детали.
Основные выходные параметры процесса хонингования это качественные показатели, характеризующиеся точностью геометрической формы и шероховатостью обработанной поверхности, а также производительностью обработки и стойкостью брусков. Выходные параметры зависят от сочетания различных технологических факторов, которые могут быть разделены на следующие основные группы:
1. Факторы, определяющие технологические характеристики процесса. К ним относятся: физико-механические свойства обрабатываемого материала, характеристики брусков, их число, размеры и формы, наладочная схема хонингования, режим обработки и состав смазочно-охлаждающей жидкости (СОЖ).
2. Факторы, характеризующие кинематику процесса, – это вид траектории рабочего движения, величины и закон изменения скоростей и ускорений относительных движений инструмента и детали, а также соотношение скоростей этих движений, характеризующие плотность и угол сетки траектории.
3. Факторы, определяющие динамические характеристики процесса (динамические факторы).
Это прежде всего средняя величина и закон изменения контактного давления в сопряжении инструмент – обрабатываемая поверхность, характеризующие силовые зависимости процесса
87
хонингования и зависящие главным образом от метода осуществления радиальной подачи брусков [35, 36] и совокупного воздействия технологических и кинематических факторов.
Характеристика брусков содержит сведения о материале абразивных зерен, зернистости, о материале связки, концентрации абразива в связке, а также о форме и габаритных размерах брусков [29, 37]. Характеристика брусков назначается в зависимости от физико-механических свойств обрабатываемого материала, величины снимаемого припуска и требуемой шероховатости [38, 39]. Критерием правильного выбора характеристики брусков является получение устойчивых результатов по точности обработки и шероховатости поверхности в сочетании с высокой производительностью и экономичностью процесса.
5.3.Основные технологические факторы
иих влияние на показатели процесса доводки плоскостей и хонингования отверстий
Различные абразивные материалы, применяемые при доводке в виде порошков и паст, отличаются по своим физикомеханическим свойствам и работоспособности. Известно, что при прочих одинаковых условиях применение более твердых абразивных материалов позволяет повысить производительность доводки, но шероховатость поверхности при этом ухудшается. При сравнительном испытании в одинаковых условиях микропорошков из электрокорунда белого ЭБМ20, карбида кремния зеленого КЗМ20 и синтетического алмаза АСМ20 наибольшая производительность получена при доводке микропорошком АСМ20.
Эффективность алмазных микропорошков наиболее ярко проявляется при обработке твердых материалов. Так, при доводке закаленной стали ШХ15 микропорошком АСМ20 съем металла в 2–2,5 раза больше по сравнению с ЭБМ20 и КЗМ20. Наименьшая величина шероховатости поверхности при испытаниях получена при использовании наименее твердого материала ЭБМ20.
88
Таким образом, доводку мягких материалов следует производить микропорошками из электрокорунда или карбида кремния зеленого. При доводке твердых материалов (закаленных сталей, твердых сплавов) целесообразно применение алмазных микропорошков и паст.
На плоскостность доведенной поверхности материал абразива влияния не оказывает.
С изменением зернистости абразивных (алмазных) микропорошков и паст, при прочих равных условиях, изменяются размеры и количество абразивных зерен, участвующих в работе, соответственно изменяется нагрузка на отдельное зерно. Поэтому изменение зернистости сказывается на условиях микрорезания и влияет на производительность доводки и шероховатость обработанной поверхности.
Съем материала зависит не только от глубины рисок (размеров срезаемых стружек), но и от их количества, приходящегося на единицу площади. Конечный результат зависит от того, какой из этих факторов преобладает. В условиях растровой доводки при оптимальном количестве абразива преобладает первый фактор: при уменьшении зернистости величина съема металла снижается. Соответственно уменьшается шероховатость доведенной поверхности. Это объясняется тем, что по мере уменьшения размеров зерен возрастает их общее количество, снижается нагрузка на каждое зерно, оно меньше проникает в обрабатываемый материал и срезает стружки значительно меньшего сечения.
При применении количества абразива меньше оптимального крупные зернистости показывают не больший, а меньший съем материала по сравнению с мелкими зернистостями. Это может быть объяснено преобладанием второго фактора.
Для снижения шероховатости поверхности предпочтение следует отдавать мелкозернистым микропорошкам и пастам. В качестве примера можно привести результаты, полученные при доводке бронзы ОЦС-5-5-5 на стеклянном притире в течение
5 мин (табл. 5.1).
89
Таблица 5.1 Результаты доводки бронзы марки ОЦС-5-5-5
Параметры |
|
Микропорошки |
|
Пасты |
|
||
ЭБМ7 |
|
ЭБМ5 |
ЭБМ3 |
ЭБ3000 |
ГОИ М3 |
ГОИ М1 |
|
|
|
||||||
Ra, мкм |
0,12 |
|
0,052 |
0,047 |
0,018 |
0,027 |
0,022 |
Съем, мкм |
13 |
|
10 |
10 |
7 |
7 |
5 |
Как видно из табл. 5.1, с уменьшением зернистости шероховатость поверхности снижается, причем сохраняется достаточная производительность.
Следует отметить, что изменение зернистости абразива не оказывает заметного влияния на плоскостность обработанной поверхности.
Количество абразивного микропорошка, нанесенного на поверхность притира, оказывает влияние на результаты процесса доводки, и в первую очередь на удельный расход абразива и производительность процесса.
По мере увеличения количества абразивного микропорошка возрастает производительность доводки (величина съема материала). Причем производительность растет значительно медленнее, чем увеличение количества абразива. Так, при увеличении количества абразива в 6 раз, производительность возрастает лишь в 1,25–1,7 раза. Такое отставание съема можно объяснить тем, что с увеличением количества абразивных зерен снижается нагрузка на каждое зерно, следовательно, уменьшается интенсивность резания. Кроме того, при слишком большом количестве абразива происходит пересыщение рабочей зоны, абразивные зерна начинают свободно перемещаться, непроизводя полезнуюработу.
Оптимальное количество абразива в рабочей зоне определяется условием, при котором абразивные зерна располагаются на рабочей поверхности притира в один слой достаточно близко друг к другу без касания. Следовательно, количество абразива зависит от размеров притира и зернистости применяемого микропорошка. Для притиров диаметром 300 мм количество абра-
90