
книги / Подъемно-транспортные машины
..pdf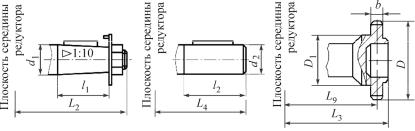
Рис. 6.2
Вопросы:
1.Какую роль в механизмах подъема играет редуктор?
2.Какие типы редукторов используются в механизмах подъема?
3.По каким параметрам выбирается редуктор механизма подъема груза? Каким условиям должен удовлетворять выбранный редуктор?
4.Дайте расшифровку условного обозначения редуктора:
редуктор 1Ц2-400-16,3-11-М-УХЛ2.
5.Какие существуют схемы соединения барабана с валом редуктора? Их достоинства и недостатки? В каких случаях они используются?
6.Какие параметры редуктора и барабана необходимо знать для осуществления соединения с помощью внутреннего зубчатого зацепления на торце барабана?
81
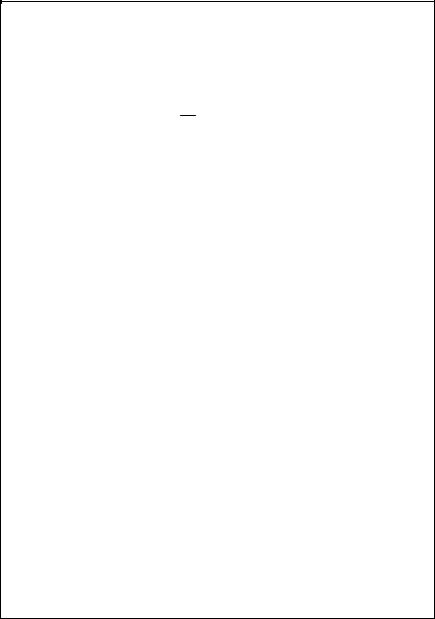
Пример выполнения задания
6. Выбор редуктора
6.1. Определяем требуемое передаточное число редуктора:
uр = nд = 945 = 16,5, nб 57,4
где nд – частота вращения двигателя, об/мин; nб – частота вращения
барабана, об/мин, |
n = |
|
uпvгр |
= |
3 20 |
|
= 57,4 |
; |
u |
п |
– кратность |
|
πD |
3,14 0,333 |
|||||||||
|
б |
|
|
|
|
|
|
||||
|
|
|
б |
|
|
|
|
|
|
|
|
грузового полиспаста; |
vгр – скорость подъема груза, |
м/мин; Dб – |
диаметр барабана по средней линии навитого каната.
6.2. Расчетная мощность на быстроходном валу редуктора
Pр = kрPдс max = 39,2 кВт,
где Pдс max – максимальная статическая мощность двигателя, кВт;
kр – коэффициент, учитывающий условия работы редуктора. Для приводов механизмов подъема кранов kр = 1.
6.3. Принимаем по каталогу [5, табл. III. 4] с учетом требуемого передаточного числа (uр = 16,5), расчетной мощности (Pр = = 39,2 кВт), режима работы (Л), частоты вращения быстроходного вала (nд = 945 об/мин) и диаметра выходного конца вала двигателя (d1дв = 65 мм) к установке
редуктор 1Ц2-400-16,3-11-М-УХЛ2
(горизонтальный двухступенчатый цилиндрический, вариант сборки 11 (см. прил. 16), конец тихоходного вала в виде части зубчатой муфты, для эксплуатации в районах с умеренным и холодным климатом под навесом или в помещениях).
Передаточное число редуктора uф = 16,3. Мощность на быстроходном валу Pэ = 47 кВт.
82
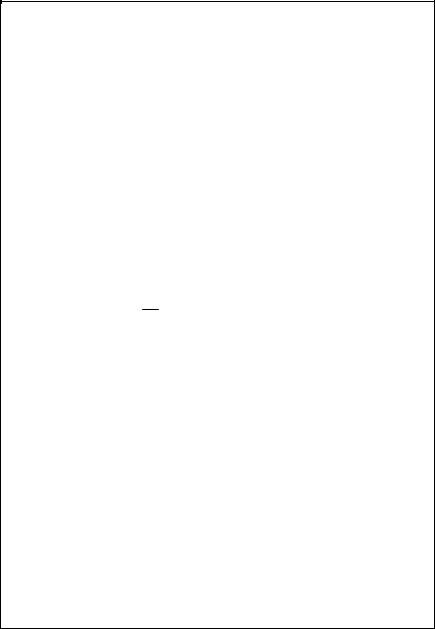
Условие Рр ≤ Pэ |
выполняется (39,2 < 47). |
|
|||||||
Диаметр выходного конца быстроходного вала d1р = 50 мм. |
|||||||||
Это составляет |
|
d1дв |
−d1р |
|
|
100 = |
65 −50 |
100 = |
23 %, что несколько |
|
|
||||||||
|
|
|
|
|
65 |
||||
|
d |
|
|
|
|||||
|
|
|
|
|
|
|
|
||
|
|
1дв |
|
|
|
|
больше рекомендованных 20 %, т.е. могут возникнуть проблемы
сподбором соединительной муфты.
6.4.Определяем отклонение передаточного числа:
∆u = |
uф −ир |
100 % = |
|
16,3 −16,5 |
|
|
100 % =1, 2 % ≤15 %. |
|
|
||||||
|
|
|
|
|
|||
и |
16,3 |
|
|
||||
|
|
|
|
|
|||
|
ф |
|
|
|
|
|
|
Условие выполняется.
6.5. Уточняем выбор электродвигателя. Фактическое значение скорости подъема груза
vгр ф = uр vгр =16,5 20 = 20,2 м/мин, uф 16,3
где vгр – скорость подъема груза, м/мин.
Отклонение фактической скорости груза от заданной
∆v = |
vгр −vгр ф |
100 % = |
|
20 −20, 2 |
|
|
100 % =1 % ≤15 %. |
|
|
||||||
|
|
|
|
|
|||
гр |
vгр |
|
20 |
|
|
|
|
|
|
|
|
|
Условие выполняется.
Уточненная мощность электродвигателя
P |
= |
(Q + q) gvгр |
= |
(10 |
+0,19) 103 9,8 |
20,2 |
= |
|
|
|
|
||||
дс max |
|
η0 |
|
|
0,85 60 |
|
|
|
|
|
|
|
|
=39,6 103 Вт =39,6 кВт.
Pтр = (0,7…0,8)Pдс max = (0,7…0,8) · 39,6 = 27,7…31,7 кВт.
Соответствует Pдв = 30 кВт.
83
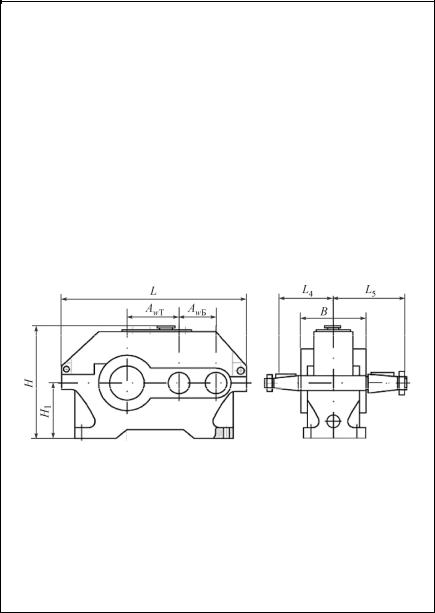
6.6.Выбираем вариант крепления барабана к валу редуктора
спомощью встроенной зубчатой муфты.
Основные технические характеристики редуктора:
Тип |
Режим |
Переда- |
Фактиче- |
Максимальная |
Частота |
Мас- |
редук- |
работы |
точное |
ское пере- |
мощность на |
вращения |
са, |
тора |
|
число u |
даточное |
быстроходном |
быстроход- |
кг |
|
|
|
число uф |
валу, кВт |
ного вала, |
|
|
|
|
|
|
об/мин |
|
Ц2-400 |
Легкий |
16,5 |
16,3 |
47 |
1000 |
315 |
Габаритные и присоединительные размеры:
АwT |
АwБ |
L |
L5 |
B |
H |
H1 |
250 |
150 |
805 |
150 |
380 |
505 |
265 |
|
|
|
|
|
|
|
Геометрические параметры концов валов редуктора:
Быстро- |
|
|
Тихоходный вал |
|
|
||||
ходный |
|
|
|
|
|
|
|
||
|
Форма конца в виде части зубчатой муфты |
|
|||||||
|
вал |
|
|
||||||
|
|
|
|
|
|
|
|
||
d1 |
|
l1 |
m |
z |
D |
D1 |
b |
L3 |
L9 |
50 |
|
85 |
6 |
40 |
252 |
140 |
30 |
280 |
255 |
|
|
|
|
|
|
|
|
|
|
84
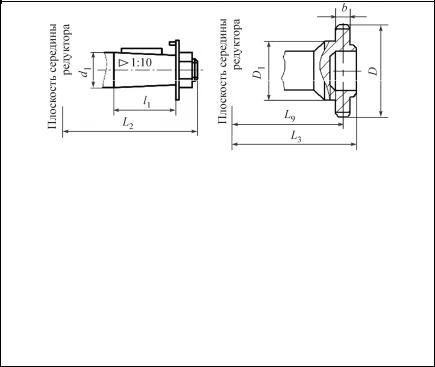
6.7. Определяем |
геометрические параметры зубчатой полу- |
муфты на канатном барабане: |
|
– модуль |
m = 6; |
– число зубьев |
z = 40; |
–диаметры:
•делительной окружности, d = mz = 6 · 40 = 240 мм;
•вершин зубчатого венца, da = d – 2m = 240 – 2 · 6 = 228 мм;
• впадин зубчатого венца, df = d + 2 · 1,25m = 240 + + 2 · 1,25 · 6 = 255 мм.
85
7. ВЫБОР ТОРМОЗА
Задание
Осуществить расчет параметров и подобрать двухколодочный тормоз для проектируемого механизма подъема.
Краткие теоретические сведения
Тормоза в механизмах подъема груза обеспечивают не только удержание груза на определенной высоте, но также остановку механизма и регулирование его скорости. Принцип их действия основан на уравновешивании целиком или частично крутящего момента на валу механизма тормозным моментом, возникающим от сил трения между подвижными и неподвижными элементами тормоза.
По способу управления тормозные устройства подразделяют следующим образом:
–автоматические – замыкающиеся при аварийной ситуации или выключении двигателя механизма, устанавливаются в механизмах с электроприводом;
–управляемые – замыкающиеся и размыкающиеся при воздей-
ствии оператора, приводятся в действие через систему рычагов и устанавливаются, как правило, в механизмах с ручным приводом или приводом от двигателя внутреннего сгорания.
По действию замыкающей силы различают следующие тормоза:
–нормально замкнутые (закрытые) – при выключенном двигателе тормозные поверхности замкнуты внешней силой (пружиной, весом замыкающего груза и т.п.), размыкание тормоза возможно только при включенном двигателе под действием электромагнитов, электрогидравлических или электромеханических толкателей;
–нормально разомкнутые (открытые) – в исходном положе-
нии тормозные поверхности разомкнуты; замыкание и размыкание тормоза осуществляется под действием внешнего усилия;
86
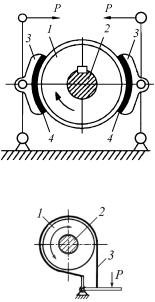
– комбинированные – в нормальных условиях работают как нормально разомкнутые, в аварийных ситуациях – как нормально замкнутые.
Согласно правилам Ростехнадзора, механизмы подъема груза должны оборудоваться только нормально замкнутыми тормозами с автоматическим управлением!
По конструктивному исполнению тормоза делятся на радиальные и осевые. Радиальные, в свою очередь, подразделяют на колодочные и ленточные, осевые – на дисковые и конусные (конические).
Колодочные тормоза состоят из |
|
|
стального кованного, реже чугунного, |
|
|
шкива 1, закрепленного при помощи |
|
|
шпонки на быстроходном валу 2, и |
|
|
стальных или чугунных колодок 3, зажи- |
|
|
мающих шкив и тормозящих его движе- |
|
|
ние (рис. 7.1). Для увеличения тормозно- |
|
|
го момента к колодкам заклепками |
|
|
крепятся фрикционные накладки 4. На- |
|
|
кладки крепятся таким образом, чтобы |
Рис. 7.1 |
|
головки заклепок не касались поверхно- |
||
|
||
сти трения тормозного шкива. |
|
|
Тормоза, как правило, делают с дву- |
|
|
мя колодками, расположенными по обеим |
|
|
сторонам шкива для равномерного рас- |
|
|
пределения нагрузки на вал. |
|
|
В ленточных тормозах (рис. 7.2) |
|
|
торможение шкива 1, закрепленного на |
Рис. 7.2 |
|
валу 2, осуществляется за счет силы тре- |
|
ния, возникающей между поверхностями шкива и стальной ленты с фрикционными накладками 3 при нажиме тормозного рычага. Применяются эти тормоза реже колодочных из-за меньшей надежности (возможен обрыв ленты), неравномерного износа ленты и возникновения значительного добавочного усилия, изгибающего вал.
87
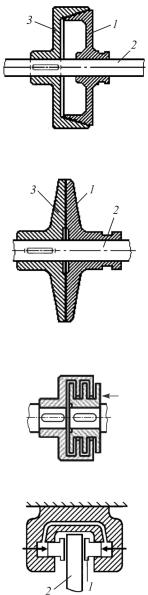
Рис. 7.3
Рис. 7.4
Рис. 7.5
Рис. 7.6
88
Тормоза с осевым давлением отли-
чаются тем, что усилие, замыкающее тормозящие поверхности, направлено не перпендикулярно, а вдоль оси вращения.
Конический тормоз (рис. 7.3) состоит из конуса 1 и неподвижной чаши с конической расточкой 3, закрепленной на валу 2 при помощи шпонки или шлиц. Замыкание и размыкание тормоза производится перемещением конуса вдоль вала при помощи рычажного механизма.
В дисковом тормозе поверхность трения представляет собой плоское коль-
цо (рис. 7.4).
Однодисковые плоские и конусные тормоза в грузоподъемных механизмах применяют редко, так как они требуют значительных усилий нажатия. Распространение, в частности в электрических талях, получили многодисковые пластинчатые тормоза (рис. 7.5), в которых сила трения создается сжатием нескольких неподвижных дисков, закрепленных в корпусе,
сподвижными дисками, сидящими на валу.
Вгрузоподъемных механизмах также могут использоваться дисково-колодочные тормоза (например, в мостовых электрических кранах). В отличие от колодочных тормозов, где тормозные колодки прижимаются к наружной поверхности тормозного шкива, в дисково-колодочных тормозах (рис. 7.6) колодки 1 выполнены плоскими и прижимаются к торцовым поверхностям шкива 2.
Вмеханизмах подъема кранов наиболее широкое применение получили колодочные тормоза (автоматические, нормальнозамкнутые, двустороннего действия). Замыкание двухколодочных тормозов в большинстве конструкций осуществляется усилием сжатой пружины, размыкание – специальными тормозными электромагнитами, электромеханическими или электрогидравлическими толкателями.
Типоразмер тормоза выбирают по каталогу в зависимости от расчетного тормозного момента.
Для полной остановки и удержания груза в неподвижном состоянии необходимо, чтобы тормозной момент был больше крутящего момента, создаваемого весом поднятого груза. Превышение тормозного момента по сравнению с крутящим называют коэффициентом запаса торможения. Коэффициент запаса торможения зависит от степени ответственности и режима работы механизма и задается при проектировании крана.
Тормозной момент зависит от величины силы трения между колодками тормоза и шкивом, а также от диаметра тормозного шкива. С увеличением диаметра шкива при одинаковом усилии прижатия колодок и коэффициенте трения тормозной момент увеличивается.
Необходимая расчетная величина тормозного момента устанавливается регулированием тормоза при помощи гаек, сжимающих пружину, прижимающую колодки к тормозному шкиву.
Взависимости от скорости начала торможения, тормозного момента и массы поднимаемого груза груз при торможении будет проходить до полной остановки определенный путь, который называют тормозным путем. Длина тормозного пути, время торможения до полной остановки и ускорение груза при торможении определяют работоспособность кранового тормоза.
89
Указания к выполнению задания
7.1. Выбор типа тормоза
Наиболее широко распространены двухколодочные тормоза следующих типов:
–ТКТ с приводом для размыкания от электромагнита переменного тока типа МО-Б;
–ТКП с приводом для размыкания от электромагнита постоянного тока типа МП;
–ТТ и ТКГ с электрогидравлическими толкателями.
Тормоза типа ТКТ конструктивно проще, поэтому их применение предпочтительнее при диаметрах тормозных шкивов до 300 мм и тормозных моментах до 500 Н·м. Их обычно применяют для механизмов групп режимов работы 1М–4М.
Вмеханизмах групп режимов работы 4М–6М, а также при использовании постоянного тока применяют тормоза типа ТКП.
Вмеханизмах групп режимов работы 4М–6М применяют также тормоза типа ТТ и ТКГ. Помимо возможности получения больших тормозных моментов, тормоза с электрогидравлическими толкателями обладают рядом следующих достоинств по сравнению с тормозами с электромагнитным размыканием:
–возможность регулирования времени срабатывания тормоза;
–плавное нарастание тормозного момента;
–большее число включений и, как следствие, высокая долговечность;
–простота обслуживания;
–бесшумность работы;
–меньший расход дорогостоящих материалов (меди), следовательно, меньшая стоимость производства и др.
Однако наличие рабочей жидкости требует высокой степени точности изготовления деталей, надежных уплотнений и осложняет эксплуатацию при низких значениях температуры.
90