
книги / Трибология
..pdfТаблица 8.3 Результаты экспериментальных исследований по определению коэффициентов трения композиционных материалов КМ-2 и КМ-3
Номер опыта |
Натуральные |
|
Коэффициент |
Среднее |
Доверительный |
Расчетное |
||||||
кг/м3 |
% МПа м/с |
yu1 |
yu2 |
yu3 |
||||||||
ние yu |
α = 0,95 |
yˆu |
||||||||||
|
значения факторов |
|
трения |
значе- |
интервал y |
значение |
||||||
|
ρн, |
n, |
P, |
|
V, |
|
|
|
||||
|
|
|
|
|
|
|
|
|||||
|
|
|
|
|
|
|
|
|
|
|
|
|
1 |
|
60 |
1 |
|
|
0,308 |
0,321 |
0,338 |
0,322 |
0,038 |
0,322 |
|
2 |
|
80 |
1 |
|
0,01 |
0,298 |
0,318 |
0,308 |
0,308 |
0,024 |
0,305 |
|
3 |
|
60 |
5 |
|
|
0,255 |
0,264 |
0,259 |
0,259 |
0,011 |
0,261 |
|
4 |
14 |
80 |
5 |
|
|
0,255 |
0,257 |
0,255 |
0,256 |
0,002 |
0,257 |
|
5 |
|
60 |
1 |
|
|
0,156 |
0,160 |
0,168 |
0,161 |
0,016 |
0,164 |
|
6 |
|
80 |
1 |
|
5 |
0,136 |
0,152 |
0,150 |
0,146 |
0,022 |
0,147 |
|
7 |
|
60 |
5 |
|
|
0,113 |
0,105 |
0,102 |
0,107 |
0,014 |
0,103 |
|
8 |
|
80 |
5 |
|
|
0,100 |
0,098 |
0,100 |
0,099 |
0,002 |
0,099 |
|
9 |
|
60 |
1 |
|
|
0,337 |
0,359 |
0,351 |
0,349 |
0,027 |
0,346 |
|
10 |
|
80 |
1 |
|
0,01 |
0,316 |
0,324 |
0,320 |
0,320 |
0,010 |
0,318 |
|
11 |
|
60 |
5 |
|
|
0,283 |
0,301 |
0,278 |
0,287 |
0,030 |
0,284 |
|
12 |
200 |
80 |
5 |
|
|
0,254 |
0,270 |
0,260 |
0,261 |
0,020 |
0,270 |
|
13 |
|
60 |
1 |
|
|
0,179 |
0,173 |
0,166 |
0,173 |
0,016 |
0,173 |
|
14 |
|
80 |
1 |
|
5 |
0,143 |
0,144 |
0,138 |
0,141 |
0,009 |
0,146 |
|
15 |
|
60 |
5 |
|
|
0,108 |
0,108 |
0,102 |
0,106 |
0,009 |
0,112 |
|
16 |
|
80 |
5 |
|
|
0,095 |
0,111 |
0,120 |
0,109 |
0,031 |
0,098 |
Таблица 8.4 Результаты экспериментальных исследований по определению
износа композиционных материалов КМ-2 и КМ-3
Номер опыта |
Натуральные |
|
Износ, мг |
Среднее |
Доверительный |
Расчетное |
||||||
кг/м3 |
% |
МПа |
м/с |
|||||||||
yu1 yu 2 yu3 |
ние yu |
α = 0,95 |
yˆu |
|||||||||
|
значения факторов |
|
|
|
значе- |
интервал y |
значение |
|||||
|
ρн, |
n, |
P, |
|
V*, |
|
|
|
||||
|
|
|
|
|
|
|
|
|||||
|
|
|
|
|
|
|
|
|
|
|
|
|
1 |
|
60 |
1 |
|
|
0,12 |
0,10 |
0,14 |
0,12 |
0,05 |
0,12 |
|
2 |
14 |
80 |
1 |
|
5 |
0,08 |
0,10 |
0,14 |
0,11 |
0,08 |
0,11 |
|
3 |
|
60 |
5 |
|
|
0,32 |
0,24 |
0,36 |
0,31 |
0,15 |
0,31 |
|
4 |
|
80 |
5 |
|
|
0,20 |
0,20 |
0,10 |
0,17 |
0,14 |
0,17 |
|
5 |
|
60 |
1 |
|
|
0,22 |
0,20 |
0,18 |
0,20 |
0,05 |
0,20 |
|
6 |
200 |
80 |
1 |
|
5 |
0,08 |
0,10 |
0,16 |
0,11 |
0,10 |
0,11 |
|
7 |
|
60 |
5 |
|
|
0,60 |
0,72 |
0,60 |
0,64 |
0,17 |
0,64 |
|
8 |
|
80 |
5 |
|
|
0,28 |
0,20 |
0,16 |
0,21 |
0,15 |
0,21 |
*В связи с тем, что при скорости скольжения 0,01 м/с величина износа исследуемых материалов составила менее 0,1 мг, этот фактор был исключен из регрессионного анализа.
121
Рассчитав коэффициенты уравнения (8.16) и исключив статистически не значимые, получили уравнение регрессии для коэффициентов трения и для износа:
yˆ 0,213 5,5 10 3 |
X |
1 |
7,8 10 3 |
X |
2 |
0,027X |
3 |
0,083X |
4 |
|
(8.29) |
|
|
|
|
|
|
|
|||||
2,6 10 3 X1X2 3,5 10 3 X1X4 3,4 10 3 X2 X3; |
|
|
|
||||||||
yˆ 0,233 0,058X1 |
0,083X2 0,098X3 0,045X1X2 |
|
|
(8.30) |
|||||||
0,014X1X3 |
0,058X2 X3 |
0,027X1X |
2 X3. |
|
|
||||||
|
|
|
Проверка уравнений (8.29) и (8.30) по критерию Фишера показала их адекватность. Для приведения данных уравнений к виду с натуральными значениями факторов использовали формулу кодирования (8.16), подставляя в уравнения вместо кодовых натуральные значения факторов. В результате получили следующие зависимости:
f 0,297 1,19 10 5ρн |
9,87 10 4 n 8,5 10 3 P 3,15 |
(8.31) |
|
10 2V 2,84 10 6ρ |
|
n 1,53 10 5ρ V 1,71 10 4 nP; |
|
н |
|
||
|
н |
|
|
I 1,26 10 2 4,12 10 4ρн 9,92 10 4 n 1,25 10 1 P |
|
||
5,38 10 6ρнn 1,2 10 3ρнP 1,38 10 3 nP |
(8.32) |
||
1,43 10 5ρнnP. |
|
На рис. 8.7–8.10 представлены зависимости экспериментальных значений коэффициента трения и износа от концентрации ТРГ в композиционных материалах КМ-2 и КМ-3 при различных значениях насыпной плотности ТРГ, прилагаемой нагрузки и скорости скольжения.
Анализ полученных экспериментальных результатов и зависимостей (8.31) и (8.32) свидетельствует о том, что с увеличением содержания ТРГ в композиционных материалах, давления на образцы и скорости скольжения при испытании коэффициенты трения уменьшаются. При этом коэффициенты трения КМ на
122
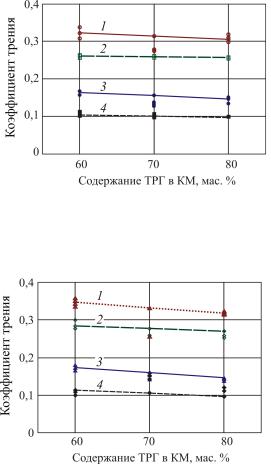
основе ТРГ с насыпной плотностью 14±1 кг/м3 меньше, чем КМ с насыпной плотностью 200±10 кг/м3. Величина износа уменьшается с увеличением содержания ТРГ в композиционных материалах и увеличивается с повышением давления на образец.
Рис. 8.7. Зависимость коэффициентов трения композиционного материала КМ-2 от содержания ТРГ: 1 – P = 1 МПа, V = 0,01 м/с;
2 – P = 5 МПа, V = 0,01 м/с; 3 – P = 1 МПа, V = 5 м/с;
4 – P = 5 МПа, V = 5 м/с
Рис. 8.8. Зависимость коэффициентов трения композиционного материала КМ-3 от содержания ТРГ: 1 – P = 1 МПа, V = 0,01 м/с;
2 – P = 5 МПа, V = 0,01 м/с; 3 – P = 1 МПа, V = 5 м/с;
4 – P = 5 МПа, V = 5 м/с
123
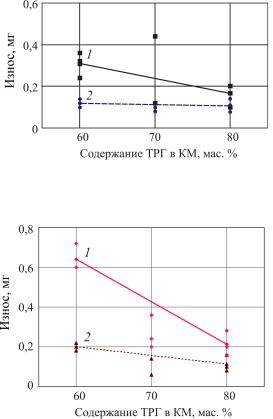
Рис. 8.9. Зависимость износа композиционного материала КМ-2 от содержания ТРГ: 1– P = 5 МПа; 2 – P = 1 МПа
Рис. 8.10. Зависимость износа композиционного материала КМ-3 от содержания ТРГ: 1 – P = 5 МПа; 2 – P = 1 МПа
Экспериментальные исследования показали, что износ образцов КМ, испытанных по схеме «палец–диск», характеризуется достаточно малой величиной, поэтому дальнейшие испытания проведены по схеме «кольцо–диск».
124
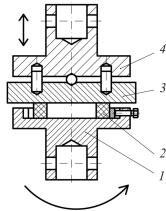
8.3. Определение коэффициента трения и износостойкости композиционных материалов на испытательной машине МИ-40КУ по схеме «кольцо–диск»
Методика проведения эксперимента. На испытательной машине МИ-40КУ по схеме «кольцо–диск» (рис. 8.11) определяется износ и коэффициент трения образцов. Износ оценивается по потере массы:
h |
m |
, |
(8.33) |
|
Aa |
||||
|
|
|
где m – потеря массы, г; – плотность вещества, г/м3; Aa – площадь поверхности трения; h – линейный износ, м.
Рис. 8.11. Приспособление для исследования процесса изнашивания образцов:1 – захват; 2 – кольцевойобразец; 3 – контртело; 4 – самоустанавливающийся захват
Кольцевой образец 2 размером 50 70 10 мм закрепляется в захвате 1, который через переходник крепится к выходному валу кручения испытательной машины МИ-40КУ (на рис. 8.11 не показаны). Контртело в виде диска 3 устанавливается в самоустанавливающемся захвате 4, который через переходник кре-
125
пится к комбинированному датчику силы и момента (на рис. 8.11 не показаны). Момент трения записывается через систему сбора данных на компьютер, а затем рассчитывается коэффициент трения. Износ образцов рассчитывается с использованием метода потери массы. Масса образцов определяется с помощью электронных весов с разрешением ±0,1 мг. Стальной диск практически не изнашивается. Каждое испытание повторяется по 5 раз. Перед началом каждого испытания поверхность контртела очищается с помощью ацетона и сжатого воздуха.
После предварительного определения коэффициентов трения и исследования износа тестовых образцов в различных средах на машине трения по схеме «палец–диск» на предприятии ООО «Силур» были произведены образцы с выбранными соотношениями ТРГ и связующего для испытания по схеме «кольцо–диск».
Результаты исследований композиционного материала КМ-1. По схеме «кольцо–диск» коэффициент трения и износ колец по сухой поверхности контртела в виде диска из стали 20Х13 с твердостью 50HRC и шероховатостью Ra = 0,84 мкм определяли на испытательной машине МИ-40КУ со специально разработанным приспособлением (см. рис. 8.11) при давлении в контакте 1…5 МПа, скорости скольжения 0,003…0,015 м/с, комнатной температуре, относительной влажности 25…35 %.
Для оценки влияния схемы испытаний на износ были проведены испытания по схеме «кольцо–диск» кольцевых образцов композиционного материала КМ-1 после приработки в течение 30 мин, результаты которых представлены на рис. 8.12.
Результаты испытаний показывают, что при испытаниях по схеме «кольцо–диск» с увеличением содержания ТРГ средний коэффициент трения КМ-1 уменьшается, а износ увеличивается после прохождения точки минимума при содержании ТРГ 60 мас. %.
126
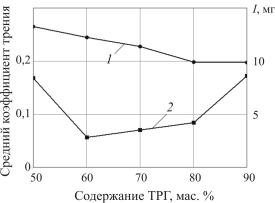
Рис. 8.12. Зависимость триботехнических характеристик КМ-1 от содержания ТРГ: 1 – средний коэффициент трения; 2 – суммарный
износ образцов после трех испытаний (tисп = 30 мин)
Результаты исследований композиционных материа-
лов КМ-1, КМ-2, КМ-3. Длительность испытания композиционных материалов КМ-1, КМ-2, КМ-3 по схеме «кольцо–диск» составила 12 ч с определением износа через каждые 2 ч взвешиванием на аналитических весах и расчетом скорости изнашивания. Нагрузку на образец варьировали в интервале 1…5 МПа. Каждое испытание проводили на трех образцах, а затем вычисляли среднее арифметическое значение.
Результаты испытаний представлены на рис. 8.13 и 8.14. Анализ зависимости скорости изнашивания композицион-
ных материалов от времени испытания (см. рис. 8.13) показывает, что для КМ-1 характерно резкое возрастание скорости изнашивания до недопустимых пределов, для КМ-3 скорость изнашивания на установившейся стадии значительно меньше, но также превосходит допустимую. В то же время для КМ-2 получены удовлетворительные результаты, позволяющие сделать выводы о возможности его применения в качестве уплотнительных элементов.
127
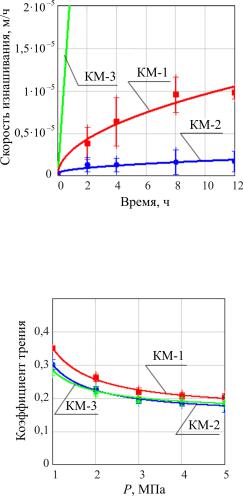
Рис. 8.13. Зависимость скорости изнашивания композиционных материалов от времени испытания (P = 5 МПа, контртело – сталь 20Х13)
Рис. 8.14. Зависимость коэффициента трения КМ по стали 20Х13 от удельного давления (время испытания 12 ч)
Как показывают результаты исследований, композиционные материалы КМ-1 и КМ-3 не могут эксплуатироваться при давлениях в контакте более 4…5 МПа.
128
Можно предположить, что более высокая износостойкость материала КМ-2 так же, как и деформационно-прочностные характеристики, связана со структурно-морфологическими особенностями используемого в данном композите ТРГ, связанными с наличием упрочняющих стержнеобразных элементов. Такого рода особенности, в свою очередь, являются следствием способа, степени и характера механического воздействия в процессе измельчения ТРГ перед формованием КМ.
В результате исследования влияния характера и степени измельчения исходного терморасширенного графита на износостойкость композиционного материала с кремнийорганическим связующим установлено, что наиболее эффективным является использование фрагментированного терморасширенного графи-
та с длиной фрагментов 0,1…3 мм (измельчение в одну стадию до ρн = 14±1 кг/м3).
8.4. Исследование износостойкости стальных деталей после электроискровой обработки терморасширенным графитом
Успешное решение проблемы повышения долговечности инструментов и деталей технологического оборудования связано с увеличением износостойкости их рабочих поверхностей.
В настоящее время все более широкое применение находят электрофизические методы обработки поверхности, в том числе метод электроискрового легирования (ЭИЛ). Метод ЭИЛ основан на явлении электрической эрозии материалов при искровом разряде в среде воздуха. На поверхности детали, являющейся катодом, в результате полярного переноса с анода продуктов эрозии формируется слой с измененной структурой и составом. Основными достоинствами метода ЭИЛ является высокая адгезия нанесенного материала с основой, отсутствие жестких требований по предварительной подготовке обрабатываемой поверхности, локальность проведения процесса, малая
129
зона термического влияния, исключающая общий нагрев обрабатываемой детали и изменение ее физико-механических свойств и геометрии.
Процесс электроискрового легирования при использовании графита в качестве анода открывает широкие возможности изменения свойств стальных поверхностей в нужном направлении. При электроискровом легировании в электрической цепи происходит «пробитие» пространства разделяющего электроды, в результате которого между электродами возникает искровой разряд, приводящий к локальному действию высоких давлений и температур. При этом поток электронов искрового разряда мгновенно разогревает анод, и частицы материала анода перемещаются к катоду в паровой, жидкой или твердой фазе. Летящие от анода к катоду частицы нагреваются до высокой температуры. При относительно небольших мощностях источника тепла 104–105 Вт/см2 и длительности искрового разряда 10–5–10–3 с на катоде образуются лунки и микрованны. В результате взаимодействия частиц анода и катода между собой и окружающей средой образуются новые фазы, структура в поверхностном слое изменяется.
Цель исследования − сравнение триботехнических свойств покрытий, полученных при различных параметрах и режимах электроискрового легирования стали Ст. 3.
Методика проведения эксперимента. Покрытия из тер-
морасширенного графита наносили с помощью установки «ЭЛИТРОН-22» для электроэрозионной обработки. Терморасширенный графит – материал, получаемый путем термического удара интеркалированных соединений графита. Процесс интеркалирования сводится к внедрению молекул и ионов серной кислоты в присутствии окислителя. При расширении графита происходит расщепление кристаллитов вдоль оси, перпендикулярной слоям углерода с гексагональной решеткой, на тонкие пачки-ленты из небольшого числа атомных плоскостей с одновременной их деформацией, в результате чего образуется объ-
130