
книги / Трибология
..pdf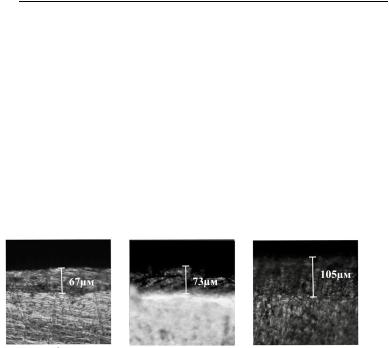
емная складчатая структура. Терморасширенный графит выбран в качестве материала электрода, так как он обладает способностью прессоваться без введения связующего. Покрытия наносили поэтапно, изменяя мощность на электроде и число проходов. Таким образом, в соответствии с литературными данными, добивались уменьшения шероховатости рабочей поверхности обрабатываемой детали. Режимы электроискрового легирования приведены в табл. 8.5.
Таблица 8.5
Режимы электроискрового легирования
Режим |
|
|
|
|
Рабочийток, А, при числе проходов |
|
|
|
|
||||||||
1 |
2 |
3 |
4 |
5 |
6 |
7 |
8 |
9 |
10 |
11 |
12 |
13 |
14 |
15 |
16 |
||
|
|||||||||||||||||
1 |
2.8 |
2.1 |
1.4 |
0.7 |
|
|
|
|
|
|
|
|
|
|
|
|
|
2 |
2.8 |
2.8 |
2.1 |
2.1 |
1.4 |
1.4 |
0.7 |
0.7 |
|
|
|
|
|
|
|
|
|
3 |
2.8 |
2.8 |
2.8 |
2.8 |
2.1 |
2.1 |
2.1 |
2.1 |
1.4 |
1.4 |
1.4 |
1.4 |
0.7 |
0.7 |
0.7 |
0.7 |
Шероховатость образцов до нанесения покрытия Ra 3,2±0,1 мкм, после нанесения покрытия шероховатость уменьшалась до Ra 2,1±0,1 мкм. Толщину покрытия определяли металлографическим методом. Микрошлифы образцов с покрытием, показанные на рис. 8.15, свидетельствуют, что с увеличением числа проходов толщина покрытия возрастает с 67 до
105 мкм.
а |
б |
в |
Рис. 8.15. Микрошлифы образцов с покрытием: а – 4 прохода; б – 8 проходов; в – 16 проходов (увеличение 100)
131

Триботехнические испытания покрытий проводили в ускоренном режиме, моделирующем работу стальных поверхностей во время пусков и остановов, когда наблюдается граничное или даже сухое трение, приводящее к значительному износу рабочих поверхностей. Образцы испытывали на машине трения по схеме «палец−диск» (см. рис. 8.1) по сухой поверхности контртела из стали 12Х18Н10Т твердостью 60HRC при комнатной температуре. Шероховатость контртела Ra 0,28 мкм; нагрузка 1 МПа; скорость скольжения 0,1 м/с; за время испытания в течение 5 мин длина пути каждого образца (пальца) составила 30 м.
Образцы (пальцы) после испытания очищали и взвешивали, приведенный износ по массе Iпm (величина, обратная изно-
состойкости) рассчитывали по формуле |
|
Iпm = m/ (FaLт), |
(8.34) |
где m − массовый износ, мг; Fa – осевая сила на один образец (палец), Н; Lт − путь трения, м.
Результаты эксперимента и обсуждение. Эксперимен-
тальные значения коэффициентов трения и износостойкости образцов (сталь Ст. 3), покрытых углеродом на разных режимах электроискровой обработки, приведены в табл. 8.6.
Таблица 8.6
Экспериментальные значения коэффициентов трения и износостойкости образцов
Покрытие |
Коэффициент трения |
|
Iпm , 105·мг/ (Н·м) |
||||||
1 |
2 |
3 |
среднее |
1 |
2 |
3 |
среднее |
||
|
|||||||||
|
значение |
значение |
|||||||
Cталь Ст. 3 |
0,24 |
0,23 |
0,25 |
0,24 |
47 |
37 |
30 |
38 |
|
без покрытия |
|||||||||
|
|
|
|
|
|
|
|
||
Покрытие, полученное |
0,21 |
0,22 |
0,22 |
0,22 |
12 |
7 |
4 |
8 |
|
в 4 прохода |
|||||||||
|
|
|
|
|
|
|
|
||
Покрытие, полученное |
0,23 |
0,21 |
0,22 |
0,22 |
1,3 |
1,3 |
0 |
1 |
|
в 8 проходов |
|||||||||
|
|
|
|
|
|
|
|
||
Покрытие, полученное |
0,22 |
0,22 |
0,22 |
0,22 |
0 |
1,3 |
1,3 |
1 |
|
в 16 проходов |
|||||||||
|
|
|
|
|
|
|
|
132
Из табл. 8.6 видно, что, несмотря на незначительное уменьшение коэффициента трения, износостойкость образцов с покрытием существенно возрастает по сравнению с необработанной сталью. С увеличением толщины покрытия износ уменьшается. Это подтвердили дополнительные испытания, в которых задавали длину 100 м пути износа. После завершения испытаний на образцах сохранилось только покрытие, полученное за 16 проходов.
Для выявления ресурсов повышения стойкости стальных деталей методом электроискрового легирования исследовано влияние технологических режимов нанесения покрытий из терморасширенного графита на их триботехнические характеристики. Показана возможность использования в данной технологии ТРГ. Снижение интенсивности изнашивания достигнуто в результате обработки поверхности за 16 проходов, с максимальным значением толщины покрытия.
8.5. Исследование влияния технологических условий осаждения покрытий на основе ZrN методом магнетронного распыления на их трибологические характеристики
Опыт эксплуатации и результаты испытаний технологического инструмента и пар трения показывают, что основными причинами их преждевременного выхода из строя являются повышенные износы или задиры трущихся поверхностей, а их надежность и ресурс во многом зависят от антифрикционных свойств материалов в зоне трения. Следовательно, помимо высокого уровня износостойкости, рабочие поверхности технологического инструмента и пар трения должны обладать достаточной антифрикционностью. Для одновременного улучшения износостойких и антифрикционных свойств поверхности технологического инструмента и пар трения наиболее часто применяют дорогостоящие и трудоемкие способы: сложное легирование однокомпонентных пленок, комбинирование различных методов осаждения пленок либо осаждение многослойных пленок с различными составами и структурой слоев.
133
Целью настоящего исследования является максимальное улучшение трибологических характеристик высокоэкономичных однокомпонентных пленок на основе ZrN путем оптимизации технологических условий получения процесса магнетронного распыления.
Методика проведения эксперимента. Тестовые образцы с пленками на основе ZrN изготавливали в Научном центре порошкового материаловедения ПНИПУ на автоматизированной вакуумной установке УРМ 3.279.048. Пленки на основе ZrN формировали магнетронным распылением однокомпонентного катода из сплава Э110 на подготовленной поверхности тестовых образцов из малоуглеродистой стали Ст3 диаметром 22 мм и толщиной 5 мм при различном сочетании технологических параметров. Адгезию пленки на основе ZrN к подложке обеспечивали осаждением подслоя Zr на нагретую в процессе ионной очистки подложку.
Трибологические испытания проводили на машине трения по схеме «палец–диск» в среде СОЖ (рис. 8.16). Условия проведения трибологических испытаний:
Палец (контртело) ........................................................ |
зубок |
формы Г26 12х14 ТУ 48-19-281-90 |
|
Количество пальцев, шт. .............................................. |
3 |
Материал пальца ........................................................... |
ВК8 |
Осевая нагрузка, Н........................................................ |
175 |
Радиус кольца износа пленки r, мм............................. |
7 |
Линейная скорость скольжения пальца V, м/с............ |
0,68 |
Путь трения Lт, м........................................................... |
1500 |
Продолжительность испытания t, с............................. |
740 |
Среда испытания........................................................... |
СОЖ |
Температура T, °С ......................................................... |
20 ± 1 |
Три (угловой шаг 120°) твердосплавных пальца 6 со сферической поверхностью (рис. 8.17, а; табл. 8.7) закрепляли в держателе 5 (рис. 8.17, б; табл. 8.7). Осевую силу 175 Н прикладывали на держатель 5 с помощью рычажного устройства
134
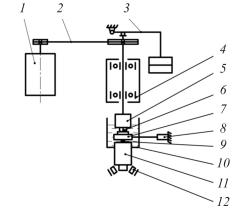
иразновесов 3 через вал, проходящий в опоре 4. Опорой для пальцев 6 служила поверхность стального тестового образца с пленкой на основе ZrN, приклеенного к диску 7, опорой которому в свою очередь через шарик 9 служила стойка 10 с подшипником 11. Держатель 5 соединяли с валом через торцовую шпонку и приводили в движение через ременную передачу 2 от электродвигателя 1. Перед трибологическим испытанием диск 7
ипальцы 6 помещали в стакан 10 с СОЖ.
Рис. 8.16. Машина трения для трибологических испытаний по схеме «палец–диск» в среде СОЖ: 1 – электродвигатель; 2 – ременная передача; 3 – рычажное устройство с разновесами; 4 – опора; 5 – держатель; 6 – контртело – палец; 7 – диск
с образцом и рычагом; 8 – тензометрический датчик силы; 9 – шарик; 10 – стакан с СОЖ; 11 – стойка; 12 – подшипник
Регистрацию силы Fд, возникающей в зоне трения, и температуры СОЖ в процессе трибологических испытаний производили с использованием измерительно-регистрирующего комплекса ИРК-2007, включающего тензометрический усилитель Microtechna типа 1101, термопару и компьютер с регистрирующей платой. Передачу силы Fд с диска 7 на тензометрический датчик силы 8 осуществляли через жестко прикрепленный к диску рычаг. По регистрируемой с частотой опроса 550 Гц си-
135
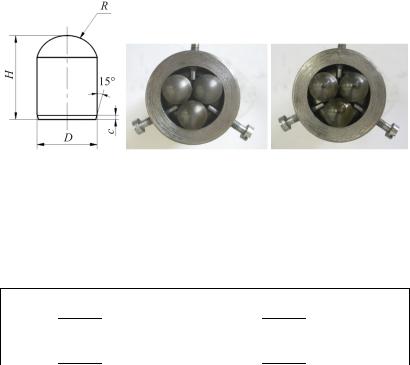
ле Fд рассчитывали момент трения МТР, а затем вычисляли коэффициент трения:
Мтр Fдlд , |
(8.35) |
где Fд – сила, передаваемая на тензометрический датчик 8, Н; lд – расстояние от оси вращения держателя 5 до тензометрического датчика силы 8, м;
f |
Mтр |
|
Fдlд |
, |
(8.36) |
|
|
||||
|
F r |
F r |
|
||
|
a |
a |
|
где Fa – осевая сила, Н; r – радиус кольца износа пленки, м.
За коэффициент трения f принимали среднее значение коэффициента трения (за 3 с) после прохождения пальцами 10 м.
а б в
Рис. 8.17. Палец: а – зубок Г26 12х14; пальцы в держателе: б – до испытаний; в – после испытания
Таблица 8.7
Геометрические характеристики зубка Г26 12 14
Размеры, мм
|
D |
|
H |
|
R |
|
c |
||||
номин. |
|
пред. |
номин. |
|
пред. |
номин. |
|
пред. |
номин. |
|
пред. |
|
откл. |
|
откл. |
|
откл. |
|
откл. |
||||
12,14 |
|
–0,027 |
13,70 |
|
–0,15 |
6,5 |
|
± 0,25 |
1,0 |
|
+0,25 |
136
Величину массового износа (∆m) образцов без пленок ZrN и с пленками ZrN, сформированными при различных технологических параметрах, устанавливали взвешиванием на аналитических весах ВЛР-200 с точностью до пятого знака после запятой.
Приведенный износ пленки Iп (величину, обратную износостойкости) по массе определяли из выражения
Iп = m/ (FaLт), |
(8.37) |
где ∆m массовый износ, мг; Lт – путь трения, м; Fa– осевая сила. Изнашивающую способность пленки оценивали по диаметру пятна износа сферической поверхности пальца (рис. 8.17, в),
который измеряли на металлографическом микроскопе Альтами МЕТ 5 по методике, описанной в ГОСТ Р ИСО 12156-1–2006.
Потерю объема контртела определяли из выражения
Vсферы = h2 (R 1/3h), |
(8.38) |
где h = R (R2 [dср /2]2)1/2, мм; dср – средний диаметр пятна износа, мм; R – радиус сферы, мм; h – высота изношенного сегмента, мм.
Приведенный износ контртела-пальца Iк определяли из выражения
Iк = Vсферы / (FaLт). |
(8.39) |
Пятно износа пальца фотографировали с использованием цифровой камеры.
Результаты эксперимента и обсуждение. Результаты трибологических испытаний пленок на основе ZrN и их технологические условия осаждения приведены в табл. 8.8.
Проведенный технологический эксперимент и трибологические испытания пленок на основе ZrN позволили установить зависимость трибологических характеристик пленок от технологических условий их осаждения. Графики зависимостей трибологических характеристик от технологических параметров процесса магнетронного распыления приведены на рис. 8.18.
137

138
Таблица 8.8
Трибологические характеристики пленок на основе ZrN,
осажденных магнетронным распылением при различных технологических параметрах
Трибологическая |
Давление газовой |
Мощность магнетрон- |
Напряжение |
|
Расстояние |
|
Содержание азота |
||||||||||
смеси, Па |
ного разряда, кВт |
смещения, В |
мишень-подложка, мм |
в газовойсмеси, % |
|||||||||||||
характеристика |
|||||||||||||||||
|
|
|
|
|
|
|
|
|
|
|
|
|
|
|
|
||
0,8 |
1,0 |
1,2 |
2,03 |
2,46 |
3,23 |
60 |
80 |
100 |
120 |
140 |
160 |
30 |
35 |
40 |
50 |
||
|
|||||||||||||||||
Момент трения, Н∙м |
0,27 |
0,09 |
0,10 |
0,09 |
0,10 |
0,09 |
0,13 |
0,09 |
0,09 |
0,12 |
0,10 |
0,10 |
0,30 |
0,09 |
0,12 |
0,13 |
|
|
|
|
|
|
|
|
0,11 |
|
|
|
|
|
|
|
|
|
|
Коэффициент трения f |
0,22 |
0,07 |
0,08 |
0,07 |
0,08 |
0,08 |
0,07 |
0,07 |
0,10 |
0,08 |
0,08 |
0,24 |
0,07 |
0,10 |
0,10 |
||
Массовый износ плен- |
3,55 |
0,42 |
5,65 |
0,42 |
6,00 |
5,25 |
5,30 |
0,42 |
0,42 |
11,90 |
7,60 |
5,60 |
2,35 |
0,42 |
4,6 |
5,9 |
|
ки m, 10–3, мг |
|||||||||||||||||
Интенсивностьизноса |
|
|
|
|
|
|
|
|
|
|
|
|
|
|
|
|
|
пленки по массе Iп∙ 10–5, |
1,35 |
0,16 |
2,15 |
0,16 |
2,29 |
2,00 |
2,02 |
0,16 |
0,16 |
4,53 |
2,90 |
2,13 |
0,90 |
0,16 |
1,75 |
2,25 |
|
мг∙Н–1∙м–1 |
|
|
|
|
|
|
|
|
|
|
|
|
|
|
|
|
|
Средний диаметр пятна |
0,58 |
0,44 |
0,75 |
0,44 |
0,97 |
0,63 |
0,71 |
0,44 |
0,44 |
0,81 |
0,86 |
0,88 |
0,61 |
0,44 |
0,48 |
0,44 |
|
износа пальца dср, мм |
|||||||||||||||||
Интенсивность износа |
|
|
|
|
|
|
|
|
|
|
|
|
|
|
|
|
|
пальца Iк ∙10–8, |
1,00 |
1,26 |
2,74 |
1,26 |
7,78 |
1,32 |
2,22 |
1,26 |
1,26 |
3,68 |
4,78 |
5,23 |
0,9 |
1,26 |
4,49 |
0,33 |
|
мм3∙Н–1∙м–1 |
|
|
|
|
|
|
|
|
|
|
|
|
|
|
|
|
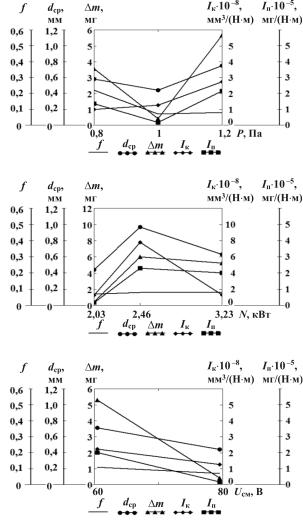
а
б
в
Рис. 8.18. Зависимости трибологических характеристик пленок на основе ZrN от переменных технологических параметров:
а– давления газовой смеси; б – мощности магнетронного разряда;
в– напряжения смещения на подложке; г – расстояния мишеньподложка; д – содержания азота в газовой смеси
(см. также с. 140)
139
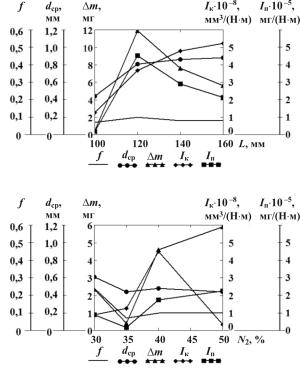
г
д
Рис. 8.18. Окончание
Полученные зависимости позволяют заключить, что технологические параметры неоднозначно влияют на трибологические характеристики износа пленки: ∆m, Iп, f и изнашивающую способность пленки контртела: dср, Iк. Минимальные значения всех указанных характеристик соответствуют следующим оптимальным технологическим условиям осаждения пленок на основе ZrN методом магнетронного распыления: Р = 1,0 Па; N = 2,03 кВт;
Uсм = 80 В; L = 100 мм; N2 = 35 %.
Результаты технологического и трибологического исследований однокомпонентных пленок на основе ZrN, выбранных в качестве модельных, позволяют заключить, что основные регу-
140