
книги / Инструментальное оснащение технологических процессов металлообработки
..pdf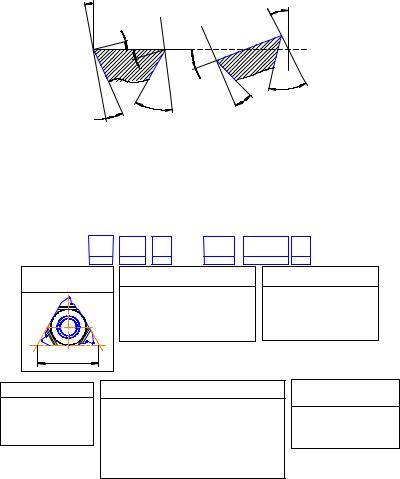
сплавов. В табл.4.1 произведено сопоставление марок твердого сплава с износостойкими покрытиями, которые рекомендованы для нарезания резьбы, соответственно в табл. 4.2 представлены марки твердых сплавов без покрытия.
τ < 3...4° |
|
|
|
τ > 3...4° |
|
|
|
|
|
|
γë |
|
λ =τ |
γë = γ ï |
|
|
|
|
|
|
|
γï |
λ |
α 1 ï |
|
≈ |
|
α |
|
|
α 1 |
1ë |
||
α 1 ë |
ï |
|
||
|
α 1 ë= α 1 - τ α 1 ï= α 1 + τ |
|||
|
|
|
Рис. 4.7. Углы подьема резьбы и наклона режущей пластины
Система обозначения резьбовых пластин и державок по ISO приведена на рис.4.8 и 4.9.
16 |
Å |
R |
- |
150 |
MMO 1 |
||||
1 |
|
2 |
3 |
|
|
4 |
5 |
|
6 |
1. Длина режущей |
|
2. Вид обработки |
|
3. Исполнение пластин |
|||||
кромки |
|
|
|
|
|
|
|
|
|
|
|
Е= для наружной резьбы |
R = правое исполнение |
||||||
|
|
N = для внутренней резьбы |
L = левое исполнение |
||||||
l |
|
|
|
|
|
|
|
|
|
4 Шаг резьбы |
5 Профиль резьбы |
|
|
|
|
|
6 Число зубьев на режущей |
||
Для метрических резьб |
VMO = неполный 60Å |
|
NJO = UNJ 60Å |
кромке |
|||||
|
|
||||||||
VWO = неполный 55Å |
|
От одного до трех. |
|||||||
равен шаг•100 |
|
MJO = MJ 60Å |
|
||||||
Для дюймовых резьб − |
MMO = метрический 60Å |
|
NFO = NPTF 60Å |
1 = 1 зуб |
|||||
число ниток/дюйм•10 |
UNO = UN 60Å |
|
|
BUO = Buttress |
2 = 2 зуба |
||||
WHO = Whitworth 55Å |
|
3 = 3 зуба |
|||||||
|
|
RDO = API Rd 60Å |
|||||||
|
RD = круглая DIN |
|
|
V38 = V-0.038R |
|
||||
|
RO = трапециидальный 30Å |
V40 = V-0.040 |
|
|
|||||
|
ACO = ACME 29Å |
|
|
V50 = V-0.050 |
|
|
|||
|
|
|
|
|
|
|
|
Рис.4.8. Система обозначения резьбовых пластин по ISO
91
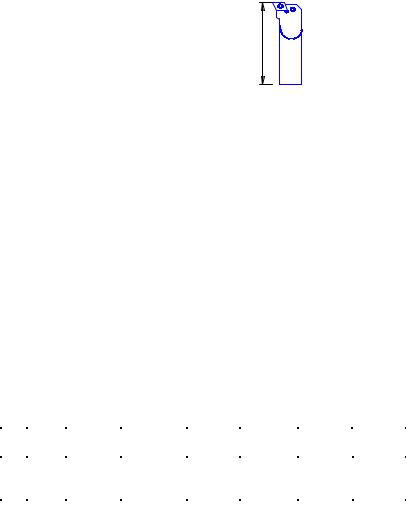
S |
|
Å |
|
R |
|
25 |
|
25 |
|
Ð |
16 |
|
|
1 |
|
2 |
|
3 |
|
4 |
|
5 |
|
|
6 |
7 |
|
1. Система крепления пластины (см.
рис.1.1).
2. Вид обработки (см. рис.4.2).
3.Исполнение пластины (см. рис.4.2).
4.Высота державки.
5.Ширина державки.
l1
6. Длина резца.
D=60 |
E=70 |
F=80 |
S=250 |
H=100 |
T=300 |
K=125 |
U=350 |
M=150 |
V=400 |
P=170 |
W=450 |
Q=180 |
Y=500 |
R=200 |
X-ñïåö. |
7. Длина режущей кромки
Рис.4.9. Система обозначения резьбовых резцов по ISO
Таблица 4 . 1
Марки твёрдых сплавов с покрытием для нарезания резьбы
Группы |
Sandviк |
Iscar |
Seco |
Sandviк |
Widia |
Sumitoma |
|
резания |
МКТС |
Tools |
Coromant |
(Герма- |
|||
и применения |
(Россия) |
(Израиль) |
(Швеция) |
(Швеция) |
ния) |
(Япония) |
|
|
P01 |
|
IC908 |
|
GC1020 |
|
|
|
P10 |
СТ15М |
IC507 |
СР200 |
GC4125 |
НСК20 |
|
|
|
|
|
|
|||
|
|
|
|
|
|
|
|
|
P20 |
4125 |
IC250 |
СР300 |
GC4125 |
НСР25 |
|
P |
СТ25М |
IC908 |
|
||||
|
P30 |
СТ35М |
IC928 |
СР500 |
GC1020 |
|
АС225 |
|
P40 |
|
IC528 |
|
GC4125 |
|
|
|
|
IC228 |
|
|
|
||
|
|
|
|
|
|
|
|
|
P50 |
|
IC928 |
|
|
|
АС225 |
|
M10 |
|
IC520 |
СР200 |
GC4125 |
НСМ15 |
|
|
|
IС507 |
|
|
|||
|
|
|
|
|
|
|
|
|
М20 |
СТ25М |
IC908 |
CP300 |
GC1020 |
НСК20 |
|
M |
|
4125 |
|
CP500 |
|
|
|
M30 |
СТ35М |
IC228 |
СР500 |
|
|
АС225 |
|
|
|
|
|||||
|
|
|
IC250 |
|
|
|
|
|
M40 |
|
IC928 |
|
GC1020 |
|
|
|
|
|
|
|
|
|
|
|
|
|
|
|
|
|
|
|
K01 |
|
|
|
|
|
|
|
K10 |
4125 |
|
СР200 |
GC1020 |
|
|
|
|
|
GC4125 |
|
|
||
|
|
|
|
|
|
|
|
K |
K20 |
СТ25М |
IC908 |
|
GC1020 |
НСК20 |
|
|
|
|
|
|
|||
|
|
|
|
|
|
|
|
|
K30 |
|
IC228 |
СР500 |
|
|
|
|
|
IC928 |
|
|
|
||
|
|
|
|
|
|
|
92
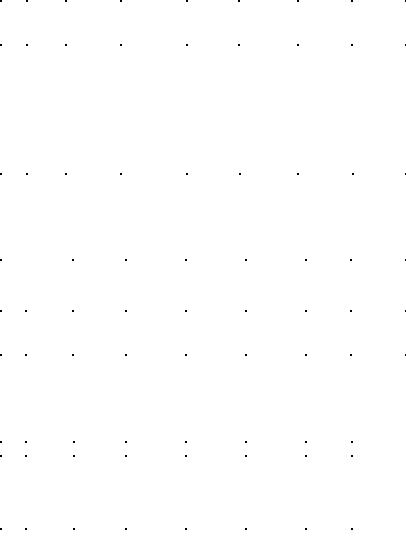
Окончание табл. 4 . 1
Группы |
Sandviк |
Iscar |
Seco |
Sandviк |
Widia |
Sumitoma |
|
резания |
МКТС |
Tools |
Coromant |
(Герма- |
|||
и применения |
(Россия) |
(Израиль) |
(Швеция) |
(Швеция) |
ния) |
(Япония) |
|
|
N01 |
|
IC520 |
|
|
|
|
N |
N10 |
|
IC908 |
|
GC1020 |
|
|
N20 |
|
|
|
|
НСК20 |
|
|
|
|
|
|
|
|
||
|
N30 |
|
|
|
|
|
|
|
S10 |
|
IC908 |
|
|
|
|
|
|
IC507 |
|
|
|
|
|
|
|
|
|
|
|
|
|
S |
S20 |
4125 |
IC228 |
СР200 |
GC1020 |
НСК20 |
|
IC928 |
СР500 |
|
|||||
|
|
|
|
|
|
||
|
S30 |
|
|
|
GC1020 |
|
|
|
S40 |
|
|
|
|
|
|
|
H10 |
СТ15М |
IC908 |
|
|
|
|
Н |
|
|
|
|
|
||
|
|
|
|
|
|
|
|
H20 |
4125 |
IC507 |
|
|
НСК20 |
|
|
|
|
|
|||||
|
Н30 |
|
|
|
|
|
|
Таблица 4 . 2
Марки твёрдых сплавов без покрытия для нарезания резьбы
|
Группы |
Sandviк |
Iscar |
Seco |
Sandviк |
Widia |
Sumitoma |
|
|
резания |
МКТС |
Tools |
Coromant |
(Герма- |
|||
|
(Израиль) |
(Япония) |
||||||
и применения |
(Россия) |
|
(Швеция) |
(Швеция) |
ния) |
|
||
|
|
P01 |
|
|
|
|
|
|
|
|
P10 |
|
|
|
|
|
|
P |
|
P20 |
|
IC50М |
|
|
Р25 |
|
|
P30 |
|
|
|
S30 |
|
А30 |
|
|
|
|
|
|
|
|||
|
|
P40 |
|
|
|
|
|
|
|
|
P50 |
|
|
|
|
|
|
|
|
M10 |
|
IC07 |
|
|
|
|
M |
|
M20 |
ТК20 |
IC20 |
Н15 |
H13A |
|
|
|
M30 |
|
|
|
|
|
|
|
|
|
|
|
|
|
|
|
|
|
|
M40 |
|
|
|
|
|
|
|
|
K01 |
|
|
|
|
|
|
K |
|
K10 |
|
IC20 |
|
|
|
G10Е |
|
K20 |
ТК20 |
|
Н15 |
H13A |
К15 |
|
|
|
|
|
|
|||||
|
|
K30 |
|
|
|
|
|
|
|
|
N01 |
|
IC20 |
|
|
|
|
N |
|
N10 |
|
|
Н15 |
Н13А |
|
|
|
N20 |
ТК20 |
|
|
|
К15 |
G10Е |
|
|
|
|
|
|
||||
|
|
|
|
|
|
|||
|
|
|
|
|
|
|
|
|
|
|
N30 |
|
|
|
|
|
|
93
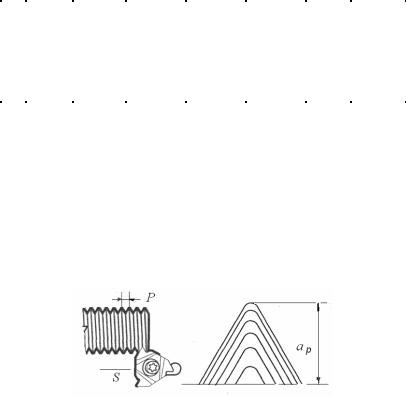
Окончание табл. 4 . 2
|
Группы |
Sandviк |
Iscar |
Seco |
Sandviк |
Widia |
Sumitoma |
|
|
резания |
МКТС |
Tools |
Coromant |
(Герма- |
|||
|
(Израиль) |
(Япония) |
||||||
и применения |
(Россия) |
|
(Швеция) |
(Швеция) |
ния) |
|
||
|
|
S10 |
|
IC07 |
|
Н13А |
|
|
|
|
|
IC20 |
|
|
|
||
|
|
|
|
|
|
|
|
|
S |
|
S20 |
ТК20 |
|
|
|
К15 |
G10Е |
|
|
S30 |
|
|
|
Н13А |
|
|
|
|
S40 |
|
|
|
|
|
|
|
|
H01 |
|
IC20 |
|
|
|
|
H |
|
H10 |
|
|
|
|
|
|
|
H20 |
|
|
|
Н13А |
|
|
|
|
|
|
|
|
|
|
||
|
|
H30 |
|
|
|
|
|
|
4.4. Назначение числа проходов, глубины врезания за проход и скорости резания при резьбонарезании
Для определения числа проходов и глубины врезания необходимо задать общую высоту профиля резьбы и глубину врезания для первого или последнего проходов (рис.4.10). Наиболее подходящее число проходов, глубину врезания и размеры пластины можно определить по табл. 4.3.
Рис.4.10. Достижение глубины резьбы за несколько проходов резца
Рекомендации по назначению глубины врезания:
– начальное значение глубины врезания за проход
∆ ар= 0,12…0,18 мм, для последнего прохода глубина врезания не должна быть менее 0,05 мм;
–постепенное уменьшение глубины врезания обеспечивает постоянный объем стружки, снимаемый за каждый проход;
–последний проход без врезания не допустим.
94
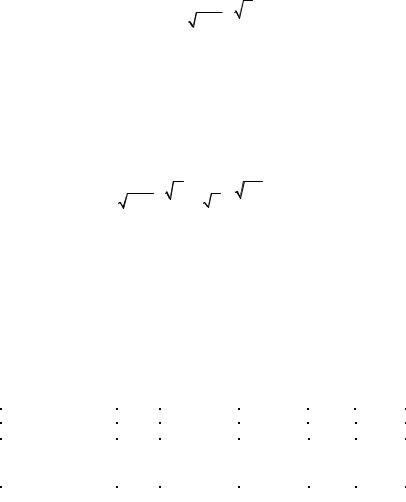
Окончательно глубину врезания и число проходов можно проверить экспериментально или по формуле [17]
∆ ap = |
ap |
ϕ , |
n −1 |
где n − число проходов; ∆ар– глубина врезания за проход; ар–
общая глубина врезания; ϕ − параметр, ϕ = 0,3 – для первого прохода; ϕ = 1,0 – для второго прохода; ϕ = n −1 для третьего и последующих проходов.
Пример. Исходные данные: наружная резьба, шаг 1,0 мм,
ар = 0,67 мм, n = 5.
Для первого прохода глубина врезания определится как
∆ ap= |
ap |
ϕ = |
0,67 |
0,3= 0,18 |
мм. |
||
n |
−1 |
4 |
|||||
|
|
|
|
Аналогично для второго прохода ар= 0,34 мм, для третьего
− 0,47 мм, для четвертого − 0,58 мм и пятого − 0,67 мм.
Таким образом, глубина врезания за первый проход равна
0,18 мм, за второй: 0,34 – 0,18 = 0,16 мм, за третий проход: 0,47 – 0,34 = 0,13 мм, за четвертый проход: 0,58 – 0,47 = 0,11 мм, за пятый проход: 0,67 – 0,58 = 0,09 мм.
Таблица 4 . 3
Число проходов, глубина врезания и размеры пластины
Метрическая резьба 60° |
Шаг |
Глубина |
Число |
Размеры пластины, |
||
резьбы |
|
мм |
||||
врезания ар , мм |
проходов n |
|
||||
|
Р, мм |
|
|
Х |
|
Z |
Наружная |
0,50 |
0,34 |
4 |
1,32 |
|
0,5 |
|
0,75 |
0,50 |
4 |
1,32 |
|
0,5 |
|
0,80 |
0,54 |
4 |
1,32 |
|
0,6 |
|
1,00 |
0,67 |
5 |
1,32 |
|
0,8 |
|
1,25 |
0,80 |
6 |
1,32 |
|
0,8 |
|
|
|
|
|
|
|
|
1,50 |
0,94 |
6 |
1,32 |
|
1,0 |
|
|
|
|
|
|
|
|
1,75 |
1,14 |
8 |
1,32 |
|
1,2 |
|
|
|
|
|
|
|
|
2,00 |
1,28 |
8 |
1,32 |
|
1,4 |
|
|
|
|
|
|
|
|
2,50 |
1,58 |
10 |
1,32 |
|
1,4 |
|
|
|
|
|
|
|
|
3,00 |
1,89 |
12 |
1,32 |
|
1,8 |
|
|
|
|
|
|
|
95
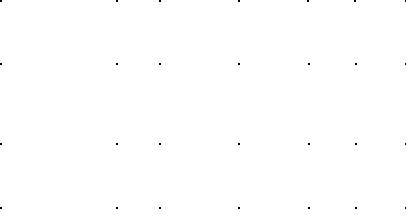
Окончание табл 4 . 3
Метрическая резьба 60° |
Шаг |
Глубина |
Число |
|
Размеры пластины, |
||||||||||||
резьбы |
|
|
мм |
||||||||||||||
врезания ар , мм |
проходов n |
|
|
||||||||||||||
|
Р, мм |
|
|
|
Х |
|
|
|
|
|
|
|
|
|
|
|
Z |
|
3,50 |
2,20 |
12 |
1,67 |
|
2,5 |
|||||||||||
|
4,00 |
2,50 |
14 |
1,67 |
|
2,5 |
|||||||||||
|
4,50 |
2,80 |
14 |
1,67 |
|
2,5 |
|||||||||||
|
5,00 |
3,12 |
14 |
1,38 |
|
2,5 |
|||||||||||
|
|
|
|
|
|
|
|
|
|
|
|
|
|
|
|
|
|
|
5,50 |
3,41 |
16 |
1,08 |
|
|
2,5 |
||||||||||
|
|
|
|
|
|
|
|
|
|
|
|
|
|
|
|
|
|
|
6,00 |
3,72 |
16 |
0,88 |
|
|
2,8 |
||||||||||
|
|
|
|
|
|
|
|
|
|
|
|
|
|
|
|
|
|
Внутренняя |
0,50 |
0,34 |
4 |
0,72 |
|
|
0,5 |
||||||||||
|
0,75 |
0,48 |
4 |
0,72 |
|
|
0,6 |
||||||||||
|
|
|
|
|
|
|
|
|
|
|
|
|
|
|
|
||
|
1,00 |
0,63 |
5 |
0,72 |
|
|
0,8 |
||||||||||
|
|
|
|
|
|
|
|
|
|
|
|
|
|
|
|
||
|
1,25 |
0,77 |
6 |
0,72 |
|
|
0,8 |
||||||||||
|
1,50 |
0,90 |
6 |
0,72 |
|
|
1,1 |
||||||||||
|
1,75 |
1,07 |
8 |
0,72 |
|
|
1,05 |
||||||||||
|
2,00 |
1,20 |
8 |
0,72 |
|
|
0,92 |
||||||||||
|
2,50 |
1,49 |
10 |
1,30 |
|
|
1,4 |
||||||||||
|
3,00 |
1,77 |
12 |
1,30 |
|
|
1,8 |
||||||||||
|
|
|
|
|
|
|
|
|
|
|
|||||||
|
3,50 |
2,04 |
12 |
1,64 |
|
|
2,5 |
||||||||||
|
|
|
|
|
|
|
|
|
|
||||||||
|
4,00 |
2,32 |
14 |
1,64 |
|
|
2,5 |
||||||||||
|
|
|
|
|
|
|
|
|
|
||||||||
|
4,50 |
2,62 |
14 |
1,64 |
|
|
2,5 |
||||||||||
|
|
|
|
|
|
|
|
|
|
||||||||
|
5,00 |
2,89 |
14 |
1,35 |
|
|
2,5 |
||||||||||
|
|
|
|
|
|
|
|
|
|
||||||||
|
5,50 |
3,20 |
16 |
1,06 |
|
|
2,5 |
||||||||||
|
|
|
|
|
|
|
|
|
|||||||||
|
6,00 |
3,46 |
16 |
|
0,87 |
|
|
2,4 |
|||||||||
|
|
|
|
|
|
|
|
|
|
|
|
|
|
|
|
|
|
Скорость резания (м/мин). Исходные данные при выборе скорости резания при резьбонарезании:
–марка обрабатываемого материала и его твердость;
–марка инструментального материала;
–требуемый период стойкости Т м, мин.
Действительная скорость резания Vc определяется по формуле
Vc = Vc.o·Kнв·Кт,
где Vc.o − начальная скорость резания, которая определяется в зависимости от обрабатываемого материала с определенной твердостью и выбранной марки инструментального материала по ката-
логам [6 − 36];
96
Kнв − поправочный коэффициент, учитывающий разницу в твердости обрабатываемого материала и материала, используемого при разработке нормативов резания (табл.1.13);
Кт − поправочный коэффициент, учитывающий разницу между выбранным и исходным периодом стойкости инструмента (исходный период стойкости составляет 15 мин). Значения Кт в зависимости от выбранной стойкости инструмента Т и :
Т и |
10 |
15 |
20 |
25 |
30 |
45 |
60 |
Кт |
1,10 |
1,0 |
0,95 |
0,90 |
0,87 |
0,80 |
0,75 |
97
ГЛАВА 5. ОБРАБОТКА ОТВЕРСТИЙ
Для формообразования отверстий существуют различные процессы механической обработки, выполняемые как лезвийными, так и абразивными инструментами. Из процессов, выполняемых лезвийными инструментами, наиболее распространенными являются: сверление, зенкерование и развертывание.
5.1. Сверление
Сверление является одним из самых распространенных способов получения отверстий и может быть сравним с токарным точением и фрезерованием, но при сверлении возникают сложности с отводом и дроблением стружки. Эти сложности возрастают с увеличением глубины отверстия. Режущим инструментом служит сверло, с помощью которого образуют отверстия в сплошном материале или увеличивают диаметр ранее образованного отверстия (рассверливание). Движение резания при сверлении − вращательное, движение подачи − поступательное. В настоящее время сверление осуществляется на токарных станках с ЧПУ или обрабатывающих центрах при вращающейся заготовке и неподвижном инструменте, который получает движение подачи, что способствует повышению производительности обработки.
Следует отметить, что этот процесс обеспечивает невысокое качество обработанных отверстий: точность не выше 11…12го квалитетов, шероховатость обработанной поверхности Rа= 6,3…10 мкм. Кроме того, сверление неизбежно сопровождается непрямолинейностьюосиотверстия (такназываемым «уводом»).
Выбор режущего инструмента для инструментального оснащения операции сверления осуществляется соответственно следующему пошаговому подходу:
1.Выбор типа сверла.
2.Выбор геометрии и инструментального материала сверла.
3.Назначение режимов резания при сверлении.
5.1.1. Выбор типа сверла
Исходные данные при выборе типа сверла: диаметр отверстия, глубина сверления, точность и качество поверхности отверстия, обрабатываемый материал, надежность обработки и производительность процесса сверления.
98

Спиральное сверло с винтовыми канавками является наиболее распространенным инструментом для сверления неглубоких отверстий. Однако между серийными сверлами из быстрорежущей стали (HSS), высокоскоростными сверлами с режущей частью из твердого сплава и сверлами с современной геометрией существует большое различие.
При выборе сверла необходимо отдать предпочтение современным твердосплавным типам сверл, обладающих высокой стойкостью и производительностью по сравнению со сверлами из быстрорежущих сталей. В табл.5.1 приведены рекомендации по выбору инструментов для различных размеров отверстий и требований к качеству обрабатываемой поверхности.
В основном цельные твердосплавные сверла или сверла с напаянными твердосплавными пластинами применяются при обработке отверстий небольшого диаметра, для которых невозможно применение сверл со сменными пластинами. Сверление сверлами с механическим креплением твердосплавных многогранных пластин − наиболее производительный и экономичный способ получения отверстий диаметром от 12 до 85 мм. Достаточно эффективно обрабатываются материалы с повышенной твердостью и труднообрабатываемые стали и сплавы. Такие сверла не требуют применения кондукторных втулок, и предпочтительный тип оборудования − фрезерные, расточные станки с ЧПУ и обрабатывающие центры.
Таблица 5 . 1
Области применения различных сверл
Вид сверла |
Диаметр от- |
l /D (l – глубина |
Шерохова- |
|
Требуемая точ- |
||
верстия D, мм |
сверления) |
|
тость Rа, мкм |
ность JT |
|||
|
|
|
|||||
Цельные |
твердо- |
2,0…20 |
3…7 |
|
1,6…3,2 |
|
8…10 |
сплавные сверла |
|
|
|
|
|
|
|
С напаянными твер- |
|
|
|
|
|
|
|
досплавными |
пла- |
10…30 |
2…7 |
|
1,6…3,2 |
|
8…10 |
стинами |
|
|
|
|
|
|
|
Со сменными |
|
12…85 |
2…5 |
|
1,6…6,3 |
± 0,2 |
|
пластинами |
|
|
|||||
|
|
|
|
|
|
|
|
Трепанирующие |
60…110 |
2…3 |
|
1,6…6,3 |
± 0,2 |
||
Пушечные сверла |
0,98…35 |
100 |
|
0,1…3,2 |
|
8…9 |
|
Эжекторные |
|
19…65 |
50 |
|
1,6…2,0 |
|
9…10 |
99
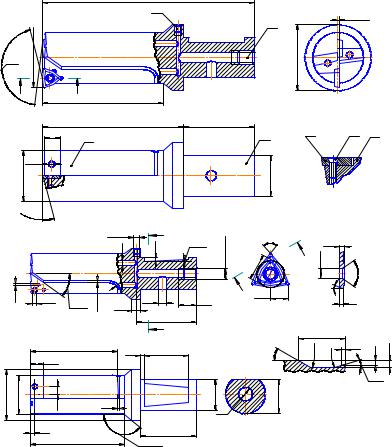
В основном большинство конструкций сборных сверл исполь- |
||||||||||||
зуют пластины типа W (ломанный треугольник) с углом при вер- |
||||||||||||
шине 80 или 84° [3, 17, 31, 33 и др.]. |
|
|
|
|
|
|
||||||
|
|
|
|
|
L |
|
|
|
|
|
|
|
|
|
|
|
|
4 |
|
|
|
0,2,,,0,3 |
|
|
|
|
|
|
|
|
|
|
|
|
|
|
|
|
|
|
|
|
|
|
|
|
5 |
|
|
|
|
2ϕ |
c |
|
|
|
|
|
|
|
1 |
|
|
|
D |
|
|
|
|
|
|
|
D |
|
|
|
|
À |
|
À |
|
l1 |
|
|
|
|
|
|
|
|
|
|
|
|
l2 |
|
|
l4 |
|
|
À-À |
|
|
|
l |
|
|
|
|
|
3 |
|
|
|
||
|
|
1 |
|
|
|
|
2 |
6 |
1 |
|
||
|
|
|
|
|
|
|
|
|
|
|
||
|
d1 |
|
|
|
|
|
|
|
|
|
|
|
|
|
|
|
|
|
|
|
2 |
|
|
|
|
d |
|
|
|
|
|
|
|
d |
|
|
|
|
|
1 |
|
|
|
|
|
|
|
|
|
|
|
|
5Å |
|
|
|
|
|
|
|
|
|
|
|
|
|
|
|
M8õ1 |
|
Á |
|
80Å |
|
s1 |
|
|
|
|
|
|
|
|
2Å50' |
|
|
|
|
||
|
|
|
|
1 |
3 |
M14õ1,5 |
|
 |
|
|
||
|
|
|
|
h |
|
|
|
|
|
|||
|
|
|
|
d |
|
|
|
|
|
|||
|
|
|
|
|
|
1 |
|
|
|
|||
|
|
|
|
|
ic |
d |
|
|
|
|||
|
|
|
|
|
|
|
|
|
65Å |
|
|
|
|
|
|
|
|
|
|
|
|
|
|
|
|
6 |
|
|
|
R |
d5 |
l7 |
 |
lp |
α |
|
|
|
d отверстия2 |
M5 |
35Å |
2 |
b1 |
|
|
|
s |
|
|
||
|
b |
|
|
|
|
|
|
|
|
|||
|
|
|
|
|
|
l8 |
|
|
Â-Â ã |
|
|
|
|
|
|
|
|
|
Á |
|
|
b |
|
|
|
|
|
l10 |
|
|
|
|
|
|
f |
|
|
|
|
|
|
|
l |
l5 |
|
Å |
R0.8 |
1 |
2 |
||
|
l |
|
|
|
6 |
|
|
0 |
R1 |
h |
h |
|
|
|
|
|
|
|
Á-Á |
3 |
|
|
|
|
|
|
|
|
|
|
|
|
|
|
|
|
||
|
|
|
|
|
|
|
|
|
|
γ |
|
|
|
|
|
|
|
|
|
|
|
|
|
|
|
3 |
|
|
|
|
|
|
|
|
|
|
|
|
1 |
|
|
|
|
|
2 |
|
|
|
|
|
|
D d |
|
|
|
|
|
|
h |
|
|
|
|
|
a |
|
|
l3 |
|
d |
d4 |
|
|
|
|
||
|
|
|
|
|
|
|
|
|
|
|
|
|
|
l9 |
|
|
|
|
l4 |
|
|
|
|
|
|
|
|
l1 |
|
|
|
|
|
|
|
|
|
|
|
|
|
|
140ű12' |
|
|
|
|
|
|
||
|
|
|
|
|
|
|
|
|
|
|
||
|
|
Рис. 5.1. Сверло с многогранными пластинами |
|
|
|
В качестве примера на рис. 5.1 представлен чертеж сверла с многогранными пластинами, производимого фирмой «Sandvik
Coromant» [17].
100