
книги / Машины и оборудование для механизации горных работ в калийных рудниках (применительно к условиям Тюбегатанского калийного месторождения)
..pdf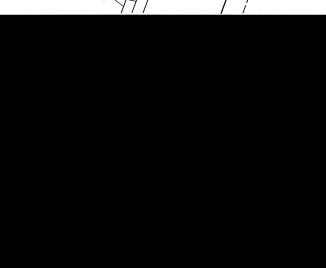
Рис. 2.2. Принципиальная схема панельного способа подготовки: Lп – ширина панели; сплошные линии – пластовые выработки; штриховые – полевые выработки
Панельные штреки располагаются перпендикулярно осям основной системы складок пласта с таким расчетом, чтобы оси очистных камер совпадали с осями складок. Это обеспечивает меньшие потери запасов при выемке, меньшее разубоживание руды, удобства ее доставки, возможность применения комбайнов и средств самоходного транспорта в камерах и более полную закладку отработанных камер.
Вентиляционные панельные штреки являются общими для смежных панелей или обслуживают только одну панель. В последнем случае вентиляционные штреки проводятся в каждой панели и между ними оставляются рудные целики. Панели имеют ширину 300–400 м и длину, определяемую размерами шахтного поля.
Руда, доставляемая из забоев очистных камер, транспортируется по панельным выемочным штрекам ленточными конвейерами до рудоспускных гезенков.
Существенным недостатком панельного способа подготовки является жестко заданная длина камер, равная половине ширины панели. Известно, что производительность средств доставки руды в камере существенно зависит от длины камеры. Для каждого типа доставочных средств (самоходных вагонов, конвейеров) существует своя
21
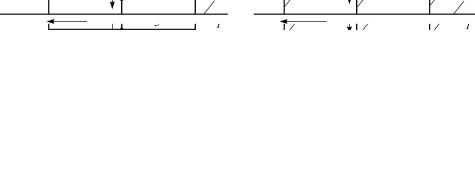
оптимальная длина камеры, при которой обеспечивается минимум совокупных затрат на подготовку и очистную выемку.
Менее эффективен панельный способ при рудной (пластовой) подготовке и прямом порядке отработки запасов панелей, особенно на пластах с недостаточно устойчивой кровлей (рис. 2.3, а). Панельные штреки включают конвейерный штрек для доставки руды, транспортный штрек (один или два) для вспомогательного автотракторного транспорта и доставки людей, а также стартовые штреки для разворота комбайнов.
|
|
|
|
|
|
|
|
|
|
|
|
а |
б |
Рис. 2.3. Принципиальная схема панельной рудной подготовки: а – при прямом порядке отработки панелей; б – при обратном; 1 – главные штреки; 2 – панельные транспортные штреки; 3 – панельные вентиляционные штреки; 4 – очистные камеры; 5 – сопряжения камер с панельными штреками; стрелками указано направление транспорта руды
Транспорт руды по панельному штреку осуществляется ленточными конвейерами.
Прямой порядок отработки приводит к большим утечкам воздуха через отработанные камеры.
Указанные недостатки панельного способа подготовки вынуждают в ряде случаев отказаться от прямого порядка отработки панелей и переходить к обратному (рис. 2.3, б).
Переход на обратный порядок позволяет значительно уменьшить утечки воздуха, снизить опасность эксплуатации панельных штреков, поскольку большинство сопряжений находится в нерабочей зоне (в выработанном пространстве).
22
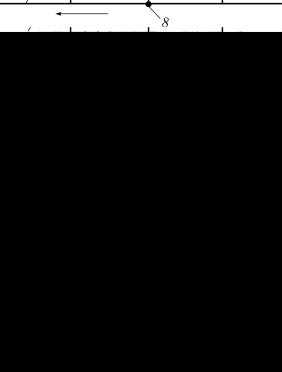
2.1.2. Панельно-блоковый способ подготовки
Панельно-блоковый способ подготовки (рис. 2.4) заключается в том, что перпендикулярно к панельным штрекам проводятся дополнительные выработки – блоковые транспортные и вентиляционные штреки, разделяющие панель на блоки. Ширина каждого блока, измеряемая по оси блоковых штреков, равна половине ширины панели (обычно 200 м), а длина блока, определяющая длину камер, может приниматься различной и изменяться в процессе отработки панели. Обычно ширина блока и, следовательно, длина камер изменяется от 150 до 300 м. Блоковые транспортные штреки, так же как и панельные, проводятся тремя ходами комбайна. Блоковые вентиляционные штреки обычно проводятся одним ходом комбайна.
Рис. 2.4. Принципиальная схема панельно-блоковой подготовки при обратном порядке отработки панелей: 1 – главные штреки; 2 – панельные транспортные штреки; 3 – панельные вентиляционные штреки; 4 – блоковые транспортные штреки; 5 – блоковые вентиляционные штреки; 6 – очистные камеры; 7 – сопряжения блоковых и панельных штреков; 8 – сопряжения
панельных и главных штреков; 9 – отработанные блоки
23
Панельно-блоковая подготовка позволяет устранить отмеченные выше недостатки панельной подготовки, однако наряду с преимуществами имеет и недостатки.
Поскольку при ее применении необходимо проводить блоковые штреки, то общий объем подготовительных выработок и стоимость подготовки оказываются большими, чем при панельной подготовке.
Второй недостаток панельно-блоковой подготовки связан с проявлениями горного давления, которые становятся наиболее ощутимыми с увеличением глубины разработки.
Поскольку панельно-блоковая подготовка не лишена недостатков, то она полностью не заменила панельную, поэтому на рудниках в настоящее время применяются оба способа подготовки.
2.2. Технология проведения горных выработок
Горизонтальные горные выработки на калийных рудниках проводят с помощью комбайнов, буровзрывных работ или комбинированным способом.
Наиболее высокая производительность труда рабочего и наименьшая стоимость 1 м выработки обеспечиваются при проведении выработок комбайнами. Комбайновый способ проведения выработок отличается простотой организации работ и проходческого цикла.
Комбайновый комплекс включает проходческо-добычной комбайн типа «Урал-20Р» («Урал-10КС»), бункер-перегружатель БП-14В (БП-15) и самоходный вагон 5ВС-15 (ВС-25).
Комбайн обеспечивает отбойку горной массы и передачу ее на транспортные средства. Чтобы комбайн не простаивал, необходимы: бесперебойная работа транспорта, крепление выработки вслед за забоем, хорошая вентиляция призабойной зоны, достаточное количество энергии и своевременное выполнение других вспомогательных работ в забое.
Выработки, проводимые комбайнами, можно разделить на короткие и протяженные.
К протяженным выработкам относятся главные и панельные штреки. Протяженные выработки обычно проектируются и проводятся комплексно, по несколько выработок, расположенных параллельно одна другой. Выработки соединены между собой короткими сбойка-
ми (рис. 2.5).
24
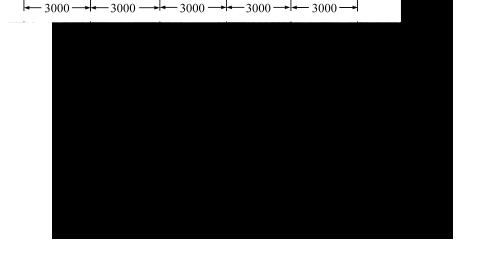
Рис. 2.5. Схема проведения выработок главных направлений: 1 – конвейерная выработка главного транспортного штрека; 2 и 3 – выработки для самоходного транспорта; 4, 5 и 6 – выработки главного вентиляционного штрека; 7 – камера временной натяжной станции; 8 – камера привода конвейера; 9 – сбойки технологического назначения; А – начало I этапа проходки; В – на-
чало II этапа проходки; С1, С2 – секции конвейеров
Обычно такие выработки проводят поэтапно, заходками, длина которых определяется не только условиями транспорта непосредственно у забоя, но и транспорта, выдающего породу по всей длине выработки. Поскольку рациональная длина транспортирования самоходного вагона сравнительно невелика и не превышает обычно 200– 300 м, то при большей длине выработки ставят последовательно несколько самоходных вагонов, работающих с перегрузкой горной массы, или монтируют в выработке стационарные конвейеры, используемые в дальнейшем при эксплуатации рудника. В схеме на рис. 2.5 длина первой заходки 600 м, длина каждой последующей заходки составляет 300 м. После проведения каждой заходки забой останавливается и в центральной выработке проводится одна из боковых выработок главного транспортного штрека. На втором этапе операции повторяются в той же последовательности, но отрезками по 300 м.
Остальные три выработки главных направлений, две выработки вентиляционного штрека и одну главного транспортного штрека проводят поэтапно в той же последовательности. На каждом направлении работают два комбайновых комплекса, а доставка руды осуществляется через технологические сбойки на главный транспортный штрек.
25

2.3. Системы разработки калийных руд
Классификация систем разработки пластовых калийных месторождений до сих пор не получила четкого однозначного решения.
Одной из возможных является классификация систем разработки по нескольким основным и дополнительным классификационным признакам. К числу основных признаков можно отнести:
1)соотношение между полной и вынимаемой мощностью пласта;
2)длину очистных забоев.
По первому признаку различают: системы разработки с выемкой пласта на полную мощность и с разделением на слои. По второму признаку различают: системы с длинными очистными забоями и системы с короткими очистными забоями.
Системы разработки с короткими очистными забоями разделяют на камерные и камерно-столбовые. В основу такого деления положены два дополнительных признака: конфигурация целиков (ленточные целики при камерных и столбчатые при камерно-столбовых системах) и длительность работы целиков, определяемая их назначением. При камерных системах оставляемые междукамерные целики предназначены для длительного поддержания кровли.
При камерно-столбовых системах междукамерные целики предназначены для поддержания кровли на период выемки запасов камеры и ее закладки (если она предусматривается), после чего междукамерные целики отрабатываются частично или полностью.
На калийных месторождениях применяют практически все перечисленные типы систем разработки, однако наибольшее распространение в настоящее время имеют камерные системы как с «жесткими», так и с податливыми целиками.
Камерная система разработки пластов*
Камерная система разработки применяется независимо от того, какая схема подготовки (панельная или панельно-блоковая) используется на руднике. Применение камерной системы на Тюбегатанском месторождении обусловлено гипсометрией калийных пластов.
Существует большое количество вариантов камерной системы, что вызвано существенными различиями в условиях залегания пла-
* Параграф написан совместно с канд. техн. наук И.П. Аманом.
26
стов и, главным образом, различной устойчивостью пород кровли пластов.
Очистные камеры, как правило, располагаются в меридиональном направлении. Расположение очистных камер в направлении, близком к направлению осей складок, значительно снижает разубоживание добываемой руды.
Основными параметрами камерной системы разработки являются ширина очистной камеры, высота очистной камеры, ширина междукамерного целика и длина камеры. Ширина камеры определяется устойчивостью пород кровли пласта и шириной исполнительного органа применяемого комбайна. По ширине очистные камеры делятся на одноходовые (ширина камеры равна ширине исполнительного органа комбайна) и многоходовые (ширина камеры больше ширины исполнительного органа комбайна). Многоходовые камеры могут отрабатываться с наложением ходов комбайна или без наложения ходов с оставлением междуходового целика.
Высота камеры определяется мощностью разрабатываемого пласта, высотой исполнительного органа комбайна, необходимостью оставления в кровле защитной пачки. По высоте очистные камеры делятся на однослойные (высота камеры равна высоте исполнительного органа комбайна) и многослойные (высота камеры больше высоты исполнительного органа комбайна). Многослойные камеры отрабатываются с наложением ходов комбайна по высоте.
На рис. 2.6 показаны варианты отработки промышленного пласта Нижний II Тюбегатанского калийного месторождения. В зависимости от горно-геологических условий предусмотрены однослойная (рис. 2.6, а) и двухслойная (рис. 2.6, б) отработка верхнего и нижнего слоев пласта Нижний II с оставлением междукамерных целиков.
Для увеличения степени извлечения полезного ископаемого предусмотрен вариант отработки промышленного пласта двухходовыми камерами с оставлением межходовых и междукамерных целиков (рис. 2.6, в), а также вариант отработки с «присечкой» (рис. 2.6, г).
Длина камеры при разработке пластов составляет около 200 м, что определяется канатоемкостью барабана самоходного вагона.
Ширина междукамерного целика рассчитывается исходя из геомеханических расчетов. Ширина междуходовых целиков не рассчитывается, а принимается, как правило, в пределах 0,7–1,2 м в зависимости от высоты камеры.
27
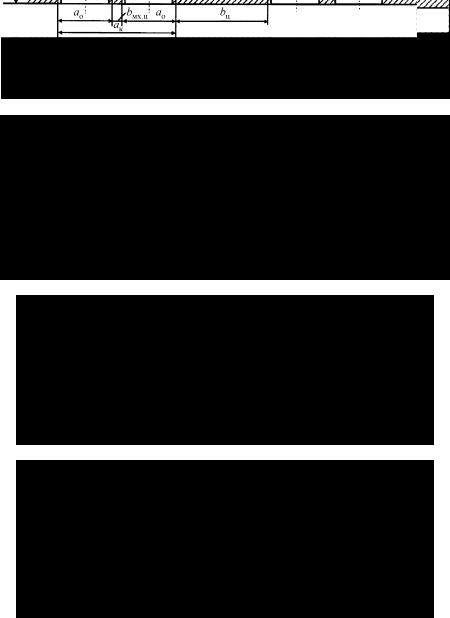
а
б
в
г
Рис. 2.6. Варианты отработки промышленного пласта Нижний II: а – однослоевая отработка; б – двухслоевая отработка; в – двухслоевая отработка с межходовыми целиками; г – двухслоевая отработка с межходовыми целиками с «присечкой»; ак – ширина камеры (выработки), м; ао – ширина хода в камере, м; bц – ширина междукамерного целика, м; bмх.ц – ширина междуходового целика, м; m – мощность полезного слоя ископаемого; mм.п – мощ-
ность межпластового пропластка
28
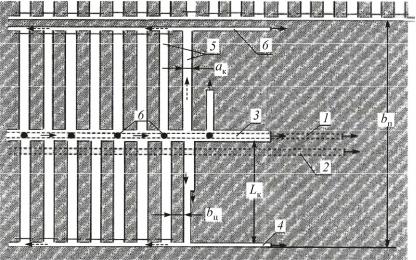
В настоящее время при разработке сильвинитовых пластов применяется только механизированная выемка в очистных камерах, которая осуществляется механизированными комплексами в составе проходческо-очистного комбайна, бункера-перегружателя и самоходного вагона.
При разработке на панели (блоке) нескольких пластов (прослоев), исходя из опыта работ на Верхнекамском калийном месторождении, очистные работы по верхнему пласту (прослою) должны опережать очистные работы по нижнему пласту не менее чем на 50 м. Кроме того, должно быть соосное расположение очистных камер и подготовительных выработок на всех пластах.
На рис. 2.7 показан вариант камерной системы разработки сильвинитового пласта при прямом порядке отработки панели (блока). Подготовка панели (блока) включает проведение конвейерного штрека 1, транспортного штрека 2, выемочного штрека 3 и вентиляционных штреков 4. Конвейерный и транспортный штреки проводятся по подстилающей каменной соли и периодически сбиваются между собой сбойками (на рис. 2.7 сбойки условно не показаны). Расстояние между сбойками не превышает 200 м. Конвейерный штрек располагается по оси панели (блока) и оборудуется ленточным конвейером.
Рис. 2.7. Камерная система разработки сильвинитовых пластов при прямом порядке отработки панели (блока): ак – ширина камеры (выработки), м; bц – ширина междукамерного целика, м; bп – ширина панели, м; Lк – длина камеры (выработки), м
29
Выемочный штрек 3 проводится по сильвинитовому пласту по оси панели (блока), разделяя панель (блок) на две полупанели (полублока). С конвейерного штрека на выемочный пробуриваются рудоспускные скважины диаметром 0,5 м. Вентиляционные штреки 4 проводятся по пласту на границах панели. При прямом порядке отработки панели (блока) пластовые штреки опережают очистные работы не более чем на 300 м.
Очистные работы ведутся одновременно в обеих полупанелях (полублоках). Очистные камеры ориентированы в меридиональном направлении. На рис. 2.7 показаны двухходовые по ширине очистные камеры, отрабатываемые с наложением ходов комбайна. Зарубка на камеры перпендикулярно оси выемочного штрека. Это требует разворота комбайна поперек выемочного штрека и, соответственно, требует ширины выемочного штрека, определяемой длиной комбайна. Такая ширина выемочного штрека возможна только при устойчивых породах кровли.
Добытая в очистных камерах руда самоходным вагоном транспортируется по камере 5 до выемочного штрека 3 и через ближайшую рудоспускную скважину 6 перегружается на ленточный конвейер, установленный на панельном (блоковом) конвейерном штреке 1.
Свежая струя воздуха подается по выемочному штреку 3. При большой длине панели (блока) свежая струя может подаваться по транспортному штреку 2 и выходить в рабочую зону пласта через специально пройденные уклоны или гезенки (иногда через скважины). Исходящая струя из камер выходит на вентиляционные штреки 4. Проветривание тупиковых ходов очистных камер производится вентиляторами местного проветривания. Проветривание ходов расширения камеры с наложением по высоте или по ширине осуществляется за счет общешахтной депрессии. Иногда для улучшения проветривания при отработке ходов с наложением в камеру заводят вентиляционный став от вентилятора местного проветривания длиной до 40 м.
При отработке панели (блока) прямым порядком возникают сложности с проветриванием очистных работ, так как воздух с выемочного штрека стремится через ближайшие отработанные камеры уйти на вентиляционные штреки. Для предотвращения утечек свежей струи на вентиляционные штреки в отработанных камерах возводятся перемычки.
30