
книги / Статическая выносливость элементов авиационных конструкций
..pdf№ по |
Термин |
|
пор. |
||
|
33Одноступенчатая повторная нагрузка
34Многоступенчатая повторная нагрузка
33 Программа нагружения
36Ступень программы нагру жения
37Спектр нагрузок
38 Усталостное повреждение
Продолжение
Определение
Нагрузка с постоянной амплитудой
Нагрузка с амплитудой, изменяю щейся в определенной последователь ности
Полное число всех циклов нагруз ки за все время испытания
Часть программы нагружения, со ставленная непрерывным повторени ем одного и того же цикла с постоян ной амплитудой до определенного числа циклов
Все эксплуатационные нагрузки на конструкцию, различающиеся по ве личине, направлению и частоте с уче том температуры •
Уменьшение выносливости материа ла или конструкции от действия по вторных нагрузок постоянной ампли туды
39 |
Усталостный срок |
службы |
Срок |
службы, определяемый |
толь |
|
|
конструкции |
|
ко выносливостью конструкции |
|
||
40 1 |
Эксплуатационный |
срок |
Срок |
службы, |
определяемый |
при |
|
службы |
|
всей совокупности |
условий эксплуа |
||
|
|
|
тации |
|
|
|
Замечания по терминологии
1. Выносливость конструкций может быть количественно вы ражена величиной напряжения (нагрузки) при заданном разру шающем числе циклов нагружения или разрушающим числом циклов при заданном напряжении.
В литературе по вопросам выносливости число циклов, при котором образец разрушается, часто называется долговечностью или усталостной долговечностью образца.
Но при испытании конструкции, особенно в условиях, близ ких к эксплуатационным, когда наблюдаются длительные пере рывы в работе конструкции, переменные по интенсивности нагре вы, коррозионные процессы и т. п., вместо термина «долговеч ность конструкции» правильнее применять термин «срок служ бы конструкции» и выражать результат испытания на вынос ливость числом циклов нагружения при разрушении. По сущест ву срок службы конструкции, выраженный разрушающим чис лом циклов, характеризует выносливость ее при принятой про грамме нагружения, учитывающей основной спектр нагрузок при эксплуатации.
11
2. Под термином «усталость» материала или конструкции следует понимать такое состояние без разрушения, до которо го доводится образец или конструкция многократным повторе нием нагрузки. Усталость как состояние конструкции выражает некоторую степень ее «утомления», пределом которой является разрушение [5], [6], [7], [8].
3. Кроме обычного приема графического изображения ре зультатов испытания на выносливость в виде кривой выносливо
сти, построенной в |
осях а—N (напряжение — число циклов), |
можно построить |
кривую выносливости в осях К—N (/< = |
=ОповтАгразр— коэффициент напряженности, выражающий от носительную напряженность образца в безразмерных единицах, N — разрушающее число циклов).
При этом кривые всех сплавов будут выходить из одной точ ки на оси ординат, соответствующей значению /С = 1. Эта точка соответствует статической прочности образца, т. е. моменту до стижения максимальной нагрузки перед разрушением образца при однократном нагружении, когда нагрузка постепенно нара стает от нуля до максимального значения. Этот момент при рас тяжении наступает при (JB=Pm&JPo, если образец не имеет концентратора напряжений, и при аРаэр=Лпах/[£о]петто, если об разец имеет его (отверстие, надрез, сварной шов и т. п.).
Расположение кривых в виде пучка, выходящего из общей точки, дает возможность наглядно сравнивать конструкционные сплавы между собой по их относительной выносливости, при данной относительной напряженности (при данном К). Количе ственная оценка выносливости сплава при данной относительной напряженности может быть выражена, как обычно, разрушаю щим числом циклов N.
Сравнительная характеристика сплавов по графику, постро енному в осях /С—N, позволяет металловеду следить за относи тельным изменением выносливости сплава при изменении его состава и установить влияние ряда технологических параметров, определяющих его структурное, напряженное и деформирован ное состояние. Конструктору же этот график вместе с обычным графиком, построенным в осях а—N, помогает полнее учесть прочностные свойства сплава при выборе его для конкретной конструкции в соответствии с условиями эксплуатации.. Сущест венную помощь конструктору он может оказать в том случае, когда прочностные свойства сплава могут изменяться в зависи мости от условий и срока эксплуатации конструкции (перемен ная температура, коррозионные процессы и т. п.). Чем меньше относительная выносливость сплава, тем осторожнее следует его применять, проверяя, является ли разрушающее число цик лов нагружения достаточным для ожидаемого срока службы конструкции. Для конструкций, в которых весовая характеристи ка играет существенную, а иногда и решающую роль, как на пример, для транспортных машин (летательные аппараты, авто
12
мобили, речные и морские суда и т. п.), следует учитывать также
иудельный вес сплава.
4.Для выражения степени асимметрии цикла нагружения часто применяется так называемый «коэффициент асимметрии»
г= . являющийся отношением минимальной нагрузки цик
ла к максимальной с их знаками. При этом симметричный цикл (т. е. цикл с нулевой асимметрией) количественно характери зуется величиной г — —1, пульсирующее растяжение г = О, пульсирующее сжатие г = —со . Таким образом, количественное значение коэффициента г нисколько не помогает выяснению вида рассматриваемого цикла.
|
|
I|1 |
ft |
|
in |
ill |
111 |
|
s § |
|
511 |
|
|
|
|
I I - 5 |
|
|
|
w |
|
|
|
|
CL <-0,5 OL =-0,S -0,5< CL<0 |
+0,5>ct>o OL=+015 |
a.>+0,5 |
||
|
CL<0 |
\OL>0 |
|
|
-{PC?>0
Рис. 1. Схема разновидностей циклов при разных значениях показателя их асимметрии а
Для выражения степени асимметрии цикла нагружения мож но принять такой «показатель асимметрии» (именно показатель, а не коэффициент), который действительно показывал бы по величине и знаку степень и направление асимметрии. За такой показатель можно принять отношение средней нагрузки цикла с
ее знаком к наибольшей по абсолютной величине (независимо от
р
ее знака) нагрузке цикла а = —р — . Этот показатель при сим-
I ^liriax
метричном цикле в соответствии с самим названием цикла принимает нулевое значение (отсутствие асимметрии); при преоб ладании растяжения, в том числе и при пульсирующем растяже нии, он положителен, при преобладании сжатия — отрицателен. Все разнообразие значений показателя асимметрии а представ
13
лено на рис. 1. Ввиду большего удобства этого показателя по сравнению с коэффициентом г он и принят в дальнейшем для выражения асимметрии цикла нагружения.
5. Определением термина «усталостное повреждение» имеет ся в виду исключить смешение этого понятия с понятием о влия нии одной ступени программы на выносливость образца при последующих ступенях. Это влияние может быть и упрочняю щим, в зависимости от величины и знака нагрузки и вида циклов сопоставляемых ступеней программы нагружения.
Глава I
ЭФФЕКТ ДЕЙСТВИЯ ПОВТОРНЫХ НАГРУЖЕНИЙ
1.ОСНОВНЫЕ ИСХОДНЫЕ ПОЛОЖЕНИЯ
Одной из основных характеристик механических свойств кон струкционных сплавов является предел упругости (ау) сплава, представляющий то наименьшее напряжение, при котором в ис пытываемом образце начинают появляться остаточные (пласти ческие) макродеформации. Количественное выражение этой ха рактеристики, вообще говоря, зависит от точности измеритель ной аппаратуры, при помощи которой измеряются деформации образца при нагрузках и разгрузках. Чем точнее измерительная аппаратура, тем раньше обнаруживается пластическая дефор мация и тем ниже количественное выражение предела упруго сти. В большинстве случаев для определения предела упругости употребляется измерительная аппаратура, позволяющая надеж но определить в ходе испытания (на растяжение) то напряже ние, при котором остаточная деформация образца при разгрузке достигает 0,001% измеряемой длины образца (базы измерения). Иногда принимаются и другие значения остаточной деформации, которые обязательно должны указываться одновременно с дан ными по величинам предела упругости. Так, например, введен ный с 1 января 1962 г. ГОСТ 1497—61 так определяет предел упругости: «предел упругости (условный) (То,os кГ/мм2— напря жение, при котором остаточное удлинение достигает 0,05% от длины участка образца, равного базе тензометра».
Введение в само определение предела упругости конкретной величины допуска на остаточное удлинение (0,05%), которая во много раз больше того, что может быть надежно измерено современными тензометрами, вносит дополнительные затрудне ния и путаницу и в без того запутанную терминологию по меха ническим свойствам материалов. Таким образом, характеристика сплава, на которой основывается объяснение явления устало сти — предел упругости, — является величиной, до известной степени условной. Следует отметить, что эта характеристика не редко смешивается с другой характеристикой — пределом теку чести. Под таким наименованием несколько десятилетий назад
15
подразумевалась точка на диаграмме растяжения железоугле родистого сплава (рис. 2), в которой направление касательной к кривой, построенной в осях «напряжение — удлинение», резко изменялось (точка ат), и в дальнейшем течение кривой продол жалось на некотором участке практически параллельно оси абс цисс, т. е. деформирование сплава продолжалось без существен ного изменения нагрузки. Происходило «течение» сплава, что и было выражено термином «предел текучести». Точнее было бы назвать эту точку началом, а не пределом текучести. Но термин
Рис. 2. Схема диаграммы растяжения |
Рис. 3. Схема диаграммы растя- |
сплава, имеющего физический предел |
жения сплава, не имеющего фнзн- |
текучести <гт и зону текучести |
ческого предела текучести |
этот вошел во всеобщее употребление и держался несколько десятилетий.
По мере появления новых сплавов, не имевших явно выра женного предела текучести (рис. 3), возникло затруднение при сравнении этих сплавов по способности к образованию значи тельных пластических' деформаций. Железоуглеродистые спла вы можно было сравнивать по пределу текучести. Поэтому была введена новая характеристика сплавов для определения их спо собности к образованию значительных пластических деформа ций. За такую характеристику было принято напряжение (при испытании на растяжение), при котором пластическая дефор мация достигает 0,2% измеряемой длины образца. Первона чальное название этой характеристики было «предел ноль два» в отличие от действительного предела текучести.
В последующем эту характеристику стали называть «услов ный предел текучести»j а с течением времени слово «условный» во многих работах стали опускать. Получился опять предел те кучести, но уже с другим содержанием. Прежний, так сказать, «настоящий» предел текучести сплава стали называть «физиче ским пределом текучести». Кроме того, в некоторых технических
16
условиях на приемку сплавов в качестве допуска на пластиче скую деформацию стали назначать не 0,2%, а иные величины, продолжая характеристику называть тем же термином «предел текучести». Так создалась путаница вокруг этого термина. Но какая бы величина допуска на пластическую деформацию ни была принята (за нормальный допуск следует принимать 0,2% измеряемой длины), «условный предел текучести» представляет действительно совершенно условную характеристику, нужную и удобную для сравнения сплавов между собой, но не являющую ся показателем какого-нибудь предельного физического состоя ния сплава.
Эта условная характеристика, как отмечалось выше, нередко ошибочно употребляется в разных формулировках вместо пре дела упругости в отечественных работах и особенно в пере водных.
Обе указанные характеристики — предел упругости и услов ный предел текучести — при растяжении количественно выра жаются как частное от деления соответствующей нагрузки на площадь начального сечения образца, что равносильно предпо ложению о равномерном распределении напряжений растяжения по площади поперечного сечения образца. На самом деле напря жения в сечении образца распределяются неравномерно вслед ствие дискретности строения сплава, состоящего из множества кристаллов. Указанная величина напряжения принимается как средняя статистическая из всех действительных значений напря жений от минимального до максимального для всего сечения. Дискретность строения сплава объясняется спецификой процес са образования твердого сплава из жидкого состояния.
На рис. 4 приведена известная схема кристаллизации сплава
из расплава |
(т. е. из жидкого состояния) при его остывании [9]. |
|
На рис. 4, а |
показаны семь очагов кристаллизации, соответст |
|
вующих |
разным стадиям формирования кристаллов:— от пер |
|
воначальной |
(показана в середине условно одиночным квадра |
|
тиком) |
и до |
более сложной (девять квадратиков). |
На рис. 4, б и в показаны дальнейшие стадии роста кристал лов. На рис. 4, г намечаются контуры будущих кристаллов, ко торые на рис. 4, д уже почти оформились — остается еще в жид ком состоянии только небольшая межкристаллитная прослойка.
На рис. 4, е показан разрез уже окончательно затвердевшего сплава с полностью оформленными кристаллами. В сплаве их принято называть зернами или кристаллитами в отличие от кри сталлов, закончивших процесс кристаллизации свободно, без стеснения их окружающими кристаллами. Черными жирными линиями показана межкристаллитная прослойка, отделяющая кристаллы друг от друга и имеющая иной состав и иные свой ства, чем сами кристаллы.
Каждый кристалл развивается до известной степени незави симо от остальных кристаллов, но в зависимости от совокупно
17
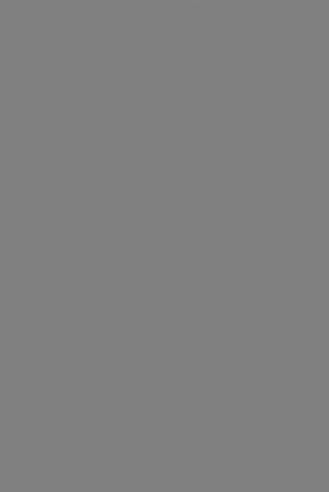
|
|
|
|
Таблица 1 |
|
Металл |
^ шах |
Стах |
Металл |
^тах |
Gmax |
(монокристалл) |
^mln |
Ощ1п |
(монокристалл) |
|
^min |
|
|
||||
Вольфрам |
1,0 |
1,0 |
Серебро |
2.7 |
2,3 |
Алюминий |
1,2 |
1,2 |
Золото |
2,7 |
2,3 |
Магний |
1,2 |
1,1 |
Медь |
2,9 |
2,5 |
Железо |
2,2 |
1,9 |
Цинк |
3,6 |
1,8 |
В табл. 2 приведены значения |
временного |
сопротивления |
||||||
разрыву а„ и удлинения после разрыва 6 тоже |
в зависимости |
|||||||
от направления растяжения по |
|
|
Таблица 2 |
|||||
отношению к |
кристаллографи |
|
|
|||||
|
|
|
|
|||||
ческим осям |
[10]. |
Как видно |
|
Металл |
(°в)шах |
8тах |
||
из табл. 1 и 2, изменения основ |
|
|||||||
ных |
механических |
характери |
(монокристалл) |
(°n)mln |
8т1п |
|||
стик |
по различным |
направле |
|
|
|
|
||
ниям |
кристаллов |
оказывают |
Алюминий |
1,95 |
3,6 |
|||
ся количественно весьма зна |
||||||||
чительными. |
Количественное |
Медь |
2,7 |
5,5 |
||||
определение изменений указан |
|
|
|
|
||||
ных |
характеристик |
в |
микро |
|
а не монокристаллов, еще |
|||
объем ах . конструкционных сплавов, |
||||||||
больше осложняется |
наличием |
межкристаллитной прослойки, |
||||||
которая обладает иными свойствами, чем сами кристаллы. |
||||||||
Из приведенных примеров анизотропии кристаллов |
следует, |
что в каждом кристалле есть направление, в котором он оказы вает наименьшее сопротивление пластическому деформирова нию по схеме сдвига. внутри зерна. Поэтому из группы различно ориентированных кристаллов при заданном направлении дей ствия нагрузки первыми начнут пластически деформироваться те кристаллы, которые ориентированы наименее благоприятно по отношению к направлению действия нагрузки. Если после этого нагрузка будет возрастать, то за ними начнут деформироваться кристаллы, расположенные несколько благоприятнее по отно шению к направлению действующей нагрузки. Наличие в спла ве межкристаллитной прослойки, отделяющей зерна сплава друг от друга, вносит большие осложнения в схему их деформирова ния, особенно при значительной напряженности, когда и сама прослойка получает остаточные деформации.
Приведенная на рис. 4, е схема строения относится к лито му сплаву, т. е. остывшему из жидкого состояния и не подвергав шемуся после этого никакой технологической обработке, связан ной с нагревом или пластической деформацией.
19
Все полуфабрикаты из деформируемых сплавов (листы, прут ки, профили, трубы, поковки, штамповки и т. д.), из которых и изготовляются конструкции при обработке их из слитков, под вергаются различным технологическим операциям, связанным с нагреванием и пластической деформацией. При этих операциях в начальном строении сплавов происходят существенные изме нения вследствие как ориентированных пластических деформа ций в значительных объемах, так и физико-химических превра щений в структуре сплавов.
Форма, размеры и строение зерен и межзеренных прослоек при этом существенно изменяются по сравнению с первоначаль
ными |
и представляют картину еще более сложную, чем на |
рис. |
4, е. |
В работе [11] для железа армко установлено, что при напря жениях, превышающих предел текучести, более слабыми при повторных нагрузках оказываются межзеренная прослойка, а при напряжениях ниже предела текучести — тело самого зерна.
Наиболее распространенной схемой пластического деформи рования зерен машиностроительных сплавов является сдвиго вая деформация, при которой одна часть зерна сдвигается по отношению к другой по некоторой плоскости, являющейся сла бейшим направлением при данном расположении рассматривае мого зерна по отношению к направлению нагрузки. Другие схе мы пластического деформирования, например схема двойникования, встречаются значительно реже и тоже сопровождаются сдвигом, но по более сложной схеме. Мы ограничимся рассмот рением только первой схемы — чисто сдвиговой деформации.
На рис. 5, а показан разрез двух зерен сплава на поверхно сти образца. Для каждого зерна штриховкой условно показаны его слабейшие в смысле сдвига направления. Эти же два зерна схематически показаны на рис. 5, б после приложения внешней нагрузки, вызвавшей пластическую деформацию. Каждое зерно претерпело сдвиговую деформацию, не разрушив еще межзеренную прослойку по ряду параллельных плоскостей, общая на правленность которых совпадает с направлением наименьшего сопротивления зерна на сдвиг.
Приведенные примеры анизотропии кристаллов ряда метал лов и общая схема зарождения и развития пластической дефор мации в них указывают на то, что для объяснения и изучения локальных явлений и процессов, происходящих при деформиро вании реальных сплавов, нельзя исходить из гипотезы о равно мерном непрерывном заполнении всего объема конструктивного элемента материалом (средой), из которого он изготовлен. Необ ходимо учитывать кристаллическое (дискретное) строение ис ходного конструкционного материала. Исходя из этих представ лений, можно полнее представить себе и схему механизма де формирования сплава.
Определение поля напряжений в объемах, соизмеримых с
20