
книги / Технология производства сварных конструкций. Ч. 2
.pdfщих конструкторских и технологических решений и оснастки, применявшихся приизготовленииранее выпускавшейся продукции;
–обеспечивать правильный выбор металла конструкции и используемого сортамента;
–осуществлять разбивку конструкции на сборочные единицы, состоящие из небольшого количества простых деталей, упрощающую изготовление изделия и обеспечивающую параллельную организацию работ по их изготовлению;
–обеспечивать применение типовых технологий при изготовлении деталей, сборочных единиц и изделия в целом.
Расчленение сварной конструкции на сборочные единицы обес-
печивает следующие преимущества:
–упрощается технология и снижаются затраты на механическую обработку входящих деталей за счет упрощения формы деталей, снижаются отходы металла, упрощается сборка под сварку;
–улучшается доступность мест выполнения сварки;
–улучшается доступность сварных соединений для выполнения операций контроля качества;
–появляется возможность организовать параллельное изготовление сборочных единиц, что сокращает длительность производственного цикла изготовления конструкции;
–уменьшается уровень остаточных напряжений в результате меньшей жесткости сборочной единицы по сравнению с целой конструкцией;
–возможно уменьшение сварочных деформаций путем их компенсации при сборке и сварке конструкции в целом;
–снижается объем и затраты на отделочные операции после сварки.
При проектировании уникальных изделий большого размера
имассы членение нередко является единственно возможным решением задачи, так как изготовить такие изделия целиком не позволяют ограниченные возможности существующего оборудования. Кроме того, членение делает возможным транспортировку изделия к месту эксплуатации. В этом случае часть сборочно-сварочных операций выполняется при монтаже.
31
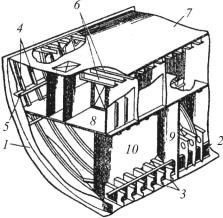
|
Примером |
использова- |
|
|
ния членения конструкции мо- |
||
|
жет быть изготовление корпу- |
||
|
сов судов большого водоиз- |
||
|
мещения. |
Корпус корабля |
|
|
представляет собой конструк- |
||
|
цию сложного очертания, со- |
||
|
стоящую из большого количе- |
||
|
ства элементов, |
соединенных |
|
|
прочными |
и герметичными |
|
|
швами (рис. 1). Значительные |
||
|
габариты и масса корпуса, |
||
|
большое |
число |
пересекаю- |
Рис. 1. Конструкция корпуса корабля: |
щихся элементов в сочетании |
||
1 – обшивка; 2 – вертикальный киль; |
с требованием герметичности |
||
3 – флоры; 4 – шпангоуты; 5 – бор- |
соединений усложняет конст- |
||
товые стрингеры; 6 – бимсы; |
рукцию узлов и |
технологию |
|
7 – верхняя палуба; 8 – нижняя палуба; |
их выполнения. |
|
|
9 – поперечные перегородки; |
Для повышения качест- |
||
10 – продольные перегородки |
ва и производительности ра- |
||
|
бот, возможности применения |
средств механизации и автоматизации, организации поточных методов производства корпус судна разбивается на блоки (рис. 2), которые в свою очередь разбиваются на секции.
Отдельные плоские и объемные секции часто укрупняют в блоксекции (рис. 3).
В ряде случаев используется технология, при которой вначале производится сборка всей конструкции в целом из отдельных деталей, а затем сварка швов. В этом случае конструкция обладает большей жесткостью, чем отдельные сборочные единицы, что ведет к снижению деформации конструкции после сварки, однако по этой причине уровень остаточных напряжений в конструкции выше.
Например, при серийной постройке малых и средних судов сварка основных швов может производиться после полной сборки
32
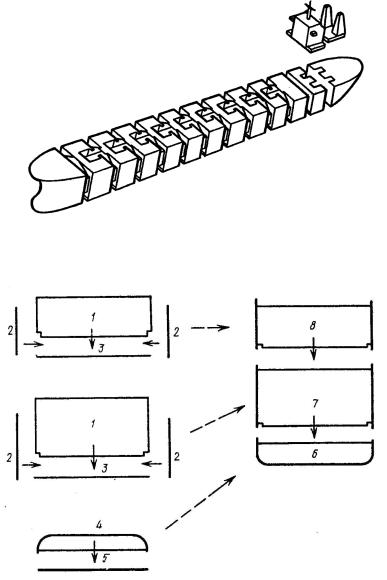
Рис. 2. Схема разбивки корпуса корабля
Рис. 3. Схема укрупнения секций:
1, 2, 3, 5 – плоские секции; 4, 6, 7, 8 – объемные секции
33
корпуса. При этом используется поточно-позиционный или поточ- но-бригадный метод организации производства.
Существует третий вариант изготовления конструкции. Изготовление ведут путем постепенного наращивания конструкции за счет присоединения отдельных деталей и изготовленных ранее сварочных единиц.
При разбивке конструкции на сборочные единицы конструктор и технолог должны учитывать количество, конфигурацию и толщину деталей, составляющих сварную конструкцию, программу выпуска изделия, а также особенности сборочно-сварочного и вспомогательного оборудования.
При изготовлении конструкций малых габаритов в массовом производстве, например электронных приборов и интегральных микросхем, развитие получили групповые методы обработки. Трудоемкость сборочно-сварочных операций при изготовлении приборов велика. В производстве электровакуумных приборов она достигает 45 % от общей трудоемкости, в производстве дискретных полупроводниковых приборов – до 25 %, а в производстве интегральных микросхем – до 60 %. Поэтому при миллиардных количествах отдельных сборочно-сварочных операций единственным путем развития производства изделий электронной техники является создание автоматизированных устройств, легко перенастраиваемых при смене номенклатуры изделий. Этого можно добиться созданием гибких производственных модулей (ГПМ) и гибких производственных систем (ГПС), состоящих из нескольких модулей, выполняющих все операции сборки, монтажа и сварки без участия человека со скоростями, в 100–1000 раз большими, чем при ручном монтаже приборов.
Наряду с проблемой роста производства изделий электронной техники важной является проблема повышения качества выпускаемой продукции.
Если представить технологию сборки-сварки с допустимым уровнем брака 1 %, то при сварке 50 выводов большой интегральной микросхемы (БИС), где каждый вывод имеет два сварных со-
34
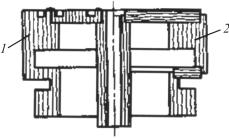
единения (на кристалле и на ножке), нельзя получить ни одной работоспособной микросхемы и, тем более, нельзя изготовить сверхбольшую интегральную микросхему. Поэтому вопросы технологической подготовки производства, контроля режимов сборки и сварки, а также контроля качества получаемых соединений в процессе их образования являются основными вопросами изготовления электронной техники. Большая роль в получении качественного соединения при изготовлении электронных приборов отводится рациональному конструктивному оформлению сварного соединения, точности изготовления и сборки входящих элементов, применению специализированной сборочно-сварочной оснастки, а также контролю за соблюдением технологии сварки.
При проектировании сварного соединения необходимо учитыватьдаже направлениеволокнистой структуры деталей, длятогочтобы исключить возможность выхода дефектов материала из полости прибора в атмосферу (рис. 4).
При выполнении свариваемых деталей из прутковых материалов (рис. 5, а) наличие перерезанных волокон в тонкостенных буртиках для сварки приводит к соединению атмосферы с полостью прибора. Переход к сборной
конструкции места сварки из элементов, изготовленных из листового материала методами пластической деформации (рис. 5, б), позволяет исключить натекание газоввполость прибора.
Выбор варианта изготовления конструкции трудно поддается формализации, и получение оптимального решения во многом зависит от опыта конструктора и технолога. Вместе с тем можно сформулировать ряд общих рекомендаций, облегчающих достижение нужного результата:
35
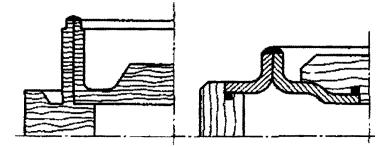
–необходимо стремиться к максимальному упрощению конструкции за счет увеличения сборочных единиц и уменьшения в них числа деталей;
–сварные швы в сборочных единицах необходимо располагать по возможности симметрично, обеспечивать доступность швов
ипомещать их в удобном для сварки нижнем положении при минимальном количестве перемещений узла в ходе сварки;
–желательно в одной сборочной единице использовать один способ сварки;
–сборочные единицы должны быть удобными для транспортирования, устойчивыми и достаточно жесткими (для исключения деформирования при транспортировке, сборке и сварке).
а |
б |
Рис. 5. Неправильное (а) и правильное (б) выполнение конструкции сварного соединения
Необходимо учитывать, что технологичность одного и того же конструктивного оформления изделия может оказаться различной в зависимости от свариваемого металла, его свариваемости, чувствительности к концентраторам напряжений, требованиям защиты зоны сварки и др. Например, конструктивно тонкостенные сосуды, работающие под давлением, являются технологичными (рис. 6). Соединение элементов осуществляется стыковыми продольными, кольцевыми и круговыми швами.
36
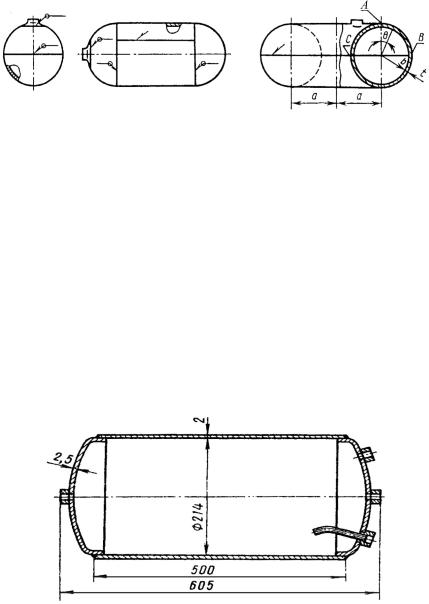
а |
б |
в |
Рис. 6. Характерные типы сосудов:
а – сферический; б – цилиндрический; в – торовый
Характерные для низкоуглеродистых сталей хорошая свариваемость и малая чувствительность к концентраторам напряжений позволяют использовать любые типы соединений и способы сварки. Поэтому при использовании таких материалов главной задачей ставится снижение трудоемкости изготовления изделия. Например, элементы тормозного воздушного баллона грузовых автомобилей изготовляются: обечайка – из горячекатаной стали 20 кп, штампованные днища – из стали 08 кп. Для повышения производительности изготовления соединение днищ с обечайкой выполняется нахлесткой. Механизация сборки путем одновременной запрессовки обоих днищ в обечайку обеспечивается приданием конусности отбортованной части днищ (рис. 7).
Рис. 7. Тормозной резервуар грузового автомобиля
37
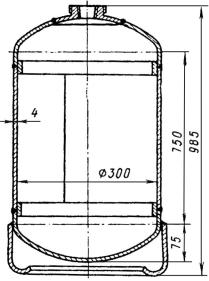
Использование прочных низколегированных сталей для изготовления сосудов исключает применение нахлесточных соединений. Например, все сварные соединения пропанового баллона из стали 15ХСНД стыковые, причем кольцевые швы допускается выполнять на остающихся подкладках, что облегчает сборку и обеспечивает отсутствие прожогов (рис. 8).
При использовании высокопрочных сталей, чувствительных к концентраторам напряже-
ний, например 25ХСНВФА, под- Рис. 8. Пропановый баллон кладные кольца применять уже
нельзя. Сборка исварка таких изделий требует использования специальных приспособлений и определенной технологии сварки.
4.2.СНИЖЕНИЕ СВАРОЧНЫХ ДЕФОРМАЦИЙ
ИОСТАТОЧНЫХ НАПРЯЖЕНИЙ
Вподавляющем большинстве случаев возникающие при сварке деформации, напряжения и перемещения отрицательно влияют на технологический процесс производства сварных конструкций, а также на их качество и работоспособность.
Влияние пластических деформаций и остаточных напряжений создает следующие проблемы при изготовлении сварной конструкции и ее эксплуатации.
1. Если при сложении рабочих напряжений с остаточными создаются такие напряженные состояния, при которых происходят пластиче-
38
ские деформации в металле, то жесткость конструкции при первом нагружении оказывается меньше расчетной. После снятия нагрузки появляются искажения размеров конструкции. При последующих нагруженияхциклическогохарактеравеличинаискаженийможетнарастать.
2.Остаточные напряжения сжатия отрицательно влияют на местную устойчивость тонкостенных элементов сварных конструкций. Нередко потеря устойчивости тонколистовых элементов возникает только от остаточных напряжений.
3.Пластические деформации металла при сварке, его старение, в особенности в зоне концентраторов, остаточные напряжения растяжения снижают сопротивляемость сварной конструкции хрупким разрушениям.
4.Остаточные напряжения растяжения снижают прочность сварных соединений и конструкций при переменных нагрузках.
5.Остаточные трехосные напряжения растяжения с примерно равными компонентами образуют такую схему напряжений, при которой возникает опасность хрупкого разрушения конструкции, в особенности при невысоком качестве металла и наличии дефектов в нем.
6.Остаточные напряжения создают в сварной конструкции запас потенциальной энергии, которая в значительной степени может быть истрачена на распространение начавшегося разрушения.
7.Остаточные напряжения растяжения и пластические деформации могут усиливать процессы коррозии и коррозионного растрескивания металла.
8.Деформации металла и напряжения в высокотемпературной зоне сварного соединения, которые возникают непосредственно в процессе сварки, способствуют образованию кристаллизационных (горячих) трещин.
9.Остаточные напряжения растяжения являются одной из главныхпричинобразованияхолодныхтрещинприсварке.
Влияние остаточных деформаций и перемещений, вызванных сваркой, также приводит к неблагоприятным последствиям.
1.Остаточные перемещения, как правило, затрудняют сборку элементов сварных конструкций или делают ее даже невозможной,
39
так как форма и размеры стыкуемых участков конструкции не совпадают с проектными. Возникает необходимость правки, подгонки и специальных мер во время сварки, чтобы обеспечить ее качественное выполнение.
2.Временные перемещения могут отрицательно влиять на качественное ведение процесса сварки, например, в случае сварки тонкого металла, когда кромки теряют устойчивость. При электрошлаковой сварке существенно меняется сварочный зазор и ряд других параметров.
3.Значительные остаточные перемещения являются причиной, по которой требуется увеличение припусков на механическую обработку после сварки.
4.Остаточные перемещения могут изменять геометрические характеристики рабочих сечений, например уменьшают момент инерции сечения двутавровой балки при появлении грибовидности полки. Это увеличивает напряжения от нагрузки.
5.Искажение формы тонкостенных элементов конструкции снижает их устойчивость. Изгибы стоек и других элементов, работающих на сжатие, ухудшают их несущую способность.
6.Эксплуатационные характеристики конструкций специального назначения могут быть значительно ухудшены остаточными перемещениями, возникшими после сварки. Например, сопротивление потоку жидкости или газа увеличивается в судах и летательных аппаратах из-за искажений формы поверхностей. Для уменьшения этих явлений требуется правка или механическая обработка рабочих поверхностей.
7.Искажения формы могут приводить к неудовлетворительному внешнему виду изделий, например автомобилей, вагонов, холодильников и др.
На стадии разработки конструкторской и технологической документации необходимо принимать меры для обеспечения ми-
нимальных искажений формы и размеров сварных конструкций после сварки.
40