
книги / Технология производства сварных конструкций. Ч. 2
.pdf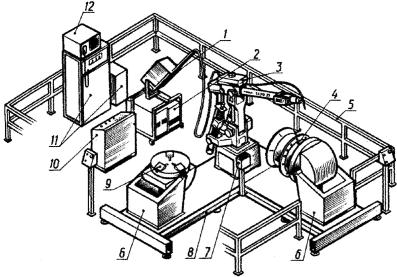
таж; причем в случае смены модели выпускаемого изделия эти линии переналадке обычно не поддаются. Более целесообразны переналаживаемые гибкие автоматизированные производственные системы (ГАПС).
Гибкой можно назвать систему, состоящую из универсального станка и квалифицированного рабочего. Замена квалифицированного рабочего промышленным роботом дает возможность автоматизировать практически любые операции, выполняемые человеком, а быстрота переобучения робота позволяет обеспечивать большую гибкость производства, чем при обслуживании оборудования человеком. В робототехническом комплексе (РТК) робот может обслуживать несколько рабочих позиций (рис. 42).
Рис. 42. РТКсдвумясварочнымиманипуляторами: 1 – механизм подачисварочнойпроволоки; 2 – сварочныйисточникпитания;
3 – роботдлясварки; 4 – свариваемое изделие; 5 – защитноеограждение; 6 – сварочныеманипуляторы; 7 – устройстводляочисткигорелки; 8 – основание; 9 – приспособление длякрепленияизделия; 10 – пульт управленияработойРТК; 11 – стойкиуправлениясвидеотерминалом 12
71
Серийное производство сварных конструкций организационно может быть построено на разных принципах.
При раздельной сборке и сварке изделий в универсальных приспособлениях доля ручного труда на вспомогательных и транспортных операциях (установка элементов, их закрепление, прихватка, освобождение от закрепления, перенос в сварочное приспособление, закрепление и поворот в удобное для сварки положение, снятие готового изделия) оказывается весьма значительной.
Использование поточных линий, оснащенных специализированным оборудованием и транспортирующими устройствами, существенно сокращает затраты ручного труда. Однако во время транспортирования заготовок технологические операции не производятся. Автоматизированные установки и линии непрерывного действия позволяют свести к минимуму потери времени на транспортные операции.
Примером организации непрерывного изготовления сварных конструкций с использованием контактной сварки может быть поточная линия изготовления отопительных радиаторов. Отопительный радиатор панельного типа (рис. 43) получают сваркой двух плоских заготовок, в которых выштампованы каналы для циркуляции воды.
Листы соединены по периметру шовной сваркой, а между каналами – точечной. В качестве заготовок используется рулонированная сталь. Все операции выполняются на непрерывных полосах, и только на последней стадии их разрезают на отдельные элементы. Это упрощает передачу заготовок с одного рабочего места на другое и обеспечивает непрерывность процесса, в том числе формовки панелей радиатора и сварочных операций на движущейся ленте.
Компоновка линии представлении на рис. 44.
Из двух рулонов 1 подающие ролики 2 направляют полосы к гильотинным ножницам 3 для обрезки с последующей стыковкой их при замене рулонов (см. рис. 44). Непрерывность полос необходимадля предотвращения проводки передней кромки каждого нового
72
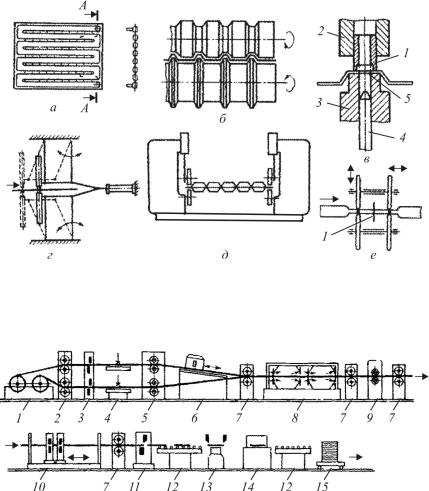
Рис. 43. Изготовление отопительного радиатора панельного типа:
а– общийвидрадиатора; б– формовкаленты; в– приваркаштуцера;
г– сварка рядов точек; д – сварка продольного шва; е – сварка поперечного шва; 1 – линия последующей разрезки полосы
Рис. 44. Автоматическаялинияизготовленияотопительных радиаторов панельноготипа: 1 – рулоны; 2 – подающиеролики; 3 – гильотинные ножницы; 4 – сварочныестолы; 5 – формующиевалики; 6 – приварка штуцеров; 7 – тянущиеролики; 8 – сваркаточечных продольныхшвов; 9 – сварка продольных швов; 10 – сварка поперечных швов;
11 – разрезка панелей; 12 – транспортер; 13 – обрезка кромок; 14 – гидропресс; 15 – укладка изделий
73
рулона через все агрегаты линии. Формовка выполняется с помощью парных валков периодического профиля (см. рис. 43, б); при этом один из валков выполняет роль матрицы, а другой – пуансона. Два штуцера привариваются к верхней полосе одновременно методом оплавления с помощью летучей контактной установки. Патрубок 1 (см. рис. 43, в) автоматически подается из питателя и верхним электродом 2 прижимается к месту сварки; после окончания сварки через отверстие в нижнем электроде 3 пуансон 4 прошивает отверстие 5 и развальцовывает лишний металл по стенкам патрубка. После приварки патрубка полосы совмещаются и устройством валкового типа подаются в неподвижную многоэлектродную машину для сварки точек между каналами. Наличие двух кинематически связанных четырехзвенников (см. рис. 43, г) обеспечивает плоскопараллельное перемещение траверс, несущих верхние и нижние электроды. Это перемещение в процессе сварки точек осуществляется за счет сцепления электродов с движущейся полосой при приложении сварочного давления. Быстрое обратное движение траверс сэлектродами выполняет пневмоцилиндр. Одновременно работает два блока электродов, выполняя сварку рядов поперечных точек. В это время два блока электродов подвергаются автоматической зачистке. Сварка продольных герметичных швов осуществляется неподвижной контактной шовной машиной с двумя парами сварочных роликов (см. рис. 43, д). Сварка поперечных швов выполняется шовной машиной с «летучими» каретками, несущими две пары сварочных роликов (см. рис. 43, е), которые выполняют одновременно два поперечных шва, расположенных на расстоянии 22 мм друг от друга. Между этими швами «летучие» гильотинные ножницы на следующей позиции отделяют радиаторы друг от друга. После обрезки продольных кромок под размер готовые радиаторы проходят гидроиспытание и поступают на окраску и сушку.
В рассмотренной автоматической линии непрерывность движения полос исключает использование накопителей и поэтому требует от оборудования особенно высокой надежности.
74
Некоторые установки в линии имеют дублирующие узлы. Так, установка для приварки патрубков имеет две сварочные головки: когда одна находится в работе, другая может проходить ремонт или наладку.
4.9. ТРАНСПОРТНЫЕ ОПЕРАЦИИ
Обеспечение высокого уровня ТКИ невозможно без рациональной организации транспортных операций.
Впроизводстве сварных конструкций рациональное выполнение транспортных операций приобретает все большее значение, поскольку при недостаточном внимании к их механизации и автоматизации затраты труда могут оказаться даже больше, чем на операции сварки.
Основные виды подъемно-транспортного оборудования сварочных цехов – тали, краны, напольный транспорт, конвейеры. Краны, в зависимости от массы и габаритов перемещаемых грузов, могут быть козловые, полукозловые, мостовые, подвесные, консольные (передвижные и стационарные), поворотные, краныштабелеры. Напольный транспорт для внутрицеховых и межцеховых перевозок состоит из погрузчиков, самоходных и несамоходных тележек, тягачей, прицепных тележек, тележек-штабелеров, рельсовых тележек. Конвейеры, используемые в сварочном производстве, могут быть роликовые (приводные и неприводные), подвесные (грузонесущие и толкающие), грузонесущие напольные тележечные, пластинчатые и др.
Вединичном и мелкосерийном производстве транспортирова-
ние заготовок, деталей, узлов и готовых изделий осуществляют главным образом с помощью мостовых кранов, автопогрузчиков
исамоходных тележек. Механизацию закрепления и освобождения листовых элементов при использовании кранов обеспечивают применением специализированных захватов. Для плоских деталей эффективно использование вакуумных захватов. При транспортирова-
75
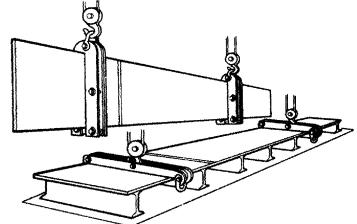
нии стальных заготовок и узлов широко используют магнитные захваты. Их достоинство – отсутствие ограничений по сплошности захватываемой поверхности. Для транспортировки элементов большой длины и малой жесткости используются жесткие траверсы с несколькими захватами, закрепленными на подвесах (рис. 45).
Рис. 45. Захваты для кантовки и переноски полотнищ
Самоходные порталы дополняют крановое оборудование. Они удобны для подачи листовых заготовок и деталей с промежуточного склада к рабочему месту, а иногда для манипулирования деталью.
В серийном производстве для транспортирования используют различные конвейеры. Универсальные типы конвейеров находят применение и в мелкосерийном производстве. Роликовые приводные и неприводные конвейеры широко используются для транспортировки листовых и цилиндрических заготовок. Движение по неприводному конвейеру обеспечивается либо наклоном секции конвейера на 1,5°–3°, либо с помощью тягового элемента. Приводные роликовые конвейеры с групповым или индивидуальным приводом перемещают изделие по горизонтали. Перегрузку листовых элементов на параллельный конвейер можно осуществлять с одновременной кантовкой на 90° (рис. 46, а) или 180° (рис. 46, б, в).
76
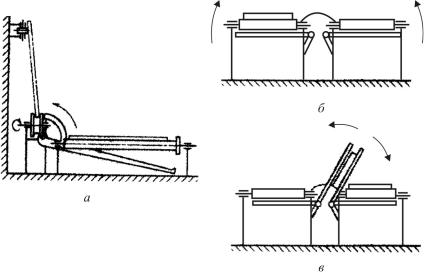
Рис. 46. Схемы перегрузочных устройств
Для транспортировки различных заготовок и узлов в сварочном производстве широко используются пластинчатые конвейеры.
Подвесные конвейеры получили широкое распространение как одно из основных транспортирующих устройств современных предприятий при серийном и массовом производстве. Конфигурация, габариты и масса транспортируемых грузов могут быть разнообразны. Достоинством подвесных конвейеров являются пространственность трассы, доступ к изделию со всех сторон, экономия производственных площадей, возможность взаимодействия с другими транспортными системами (рис. 47).
Их используют не только для перемещения узлов или изделий к рабочим местам. Нередко одновременно с транспортированием изделия могут проходить различные технологические операции: мойку, очистку, сушку, окраску и др.
Снабжение грузовых кареток подвесных конвейеров самоотце- пом-автостопом позволяет производить автоматическую сортировку
77
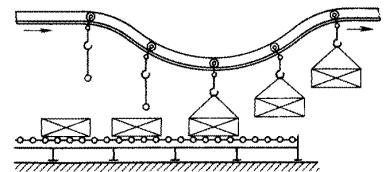
Рис. 47. Загрузка подвесного конвейера с роликового конвейера
грузов и комплектацию деталей и узлов в порядке выполнения сбо- рочно-сварочных операций. Кроме того, появляется возможность организации подвесных складов под потолком цеха на подвесках, создания отпускных секций. Подвесные толкающие конвейеры обеспечивают наиболее высокую производительность и являются основным внутрицеховым транспортным средством при разветвленной и устойчивой схеме перевозок со значительным количеством мест разгрузки и загрузки. Толкающие конвейеры позволяют применять автоматическое адресование грузов.
Автоматическую шаговую подачу непрерывных заготовок в виде лент, полос, стержней осуществляют с помощью валиковых, клещевых икрючковых устройств (рис. 48).
Валиковую подачу целесообразно использовать при приварке каких-либо элементов к полосе или ленте, а также при выполнении прессовых и гибочных операций. Привод валиковой подачи (рис. 48, а) обычно обеспечивается кинематической связью с ходом пуансона пресса или хобота 1 точечной контактной машины. При подъеме пуансона валики перемещают полосу или ленту 2 на заданный шаг.
78
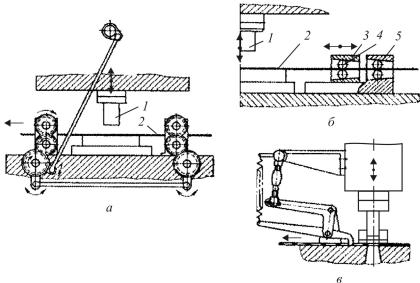
Рис. 48. Схемыустройствдляшаговойподачинепрерывныхзаготовок: а– валиковаяподача; б– клещеваяподача; в– крючковаяпродача
При клещевой подаче подвижный захват также связан с рабочим органом машины. При движении его вниз подающая каретка 3 (рис. 48, б) перемещается слева направо. При этом ролики 4 свободно скользят по ленте 2. Тормозные ролики 5 заклинены и препятствуют перемещению ленты 2 под влиянием силы трения о ролики 4. При ходе пуансона 1 вверх каретка 3 движется справа налево, лента заклинивается между роликами подающей каретки и перемещается на длину хода каретки.
Схема работы подающего устройства крючкового типа показана на рис. 48, в. Полоса или лента захватывается крюком за кромку пробитого отверстия или за выступ в рамке, куда укладывается листовой элемент, собранный под точечную контактную сварку с заданным шагом.
Для передачи деталей или узлов с одной позиции на другую в поточной, а тем более в автоматической линии широко используют шаговые конвейеры. В конвейерах этого типа детали или уз-
79
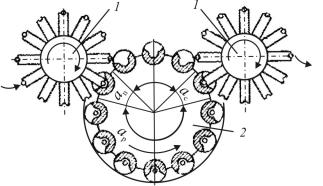
лы на размер шага перемещают устройства, совершающие поступательное или возвратно-поступательное движение (сцеп тележек, штанга или рамка).
При шаговой подаче производственный процесс имеет прерывистый характер: рабочая операция сменяется транспортной. В условиях современного производства для снижения транспортных потерь, средств и времени, а также для уменьшения производственных площадей перспективной является организация непрерывного производственного процесса. В этом случае выполнение технологических операций осуществляется в ходе транспортирования. Для длинномерных листовых заготовок это достигается непрерывной подачей рулонированного материала (см. рис. 14, 44).
При изготовлении изделий сравнительно небольших размеров
имассы целесообразно применение автоматических роторных линий
иустановок (рис. 49), где технологические операции выполняются в процессе транспортирования. Привод линии прост, поскольку все технологические и транспортные роторы находятся в жестком зацеплении. Передача штучных узлов и деталей с одного ротора на другой осуществляется захватами или специальными переталкивателями. При этом ориентация заготовок может сохраняться или, при необходимости, им придается заданное положение.
Рис. 49. Схема автоматической роторной линии: ап – сектор питания; ар – рабочий сектор; ас – сектор съема; 1 – транспортные роторы; 2 – рабочий ротор
80