
книги / Технология производства сварных конструкций. Ч. 2
.pdf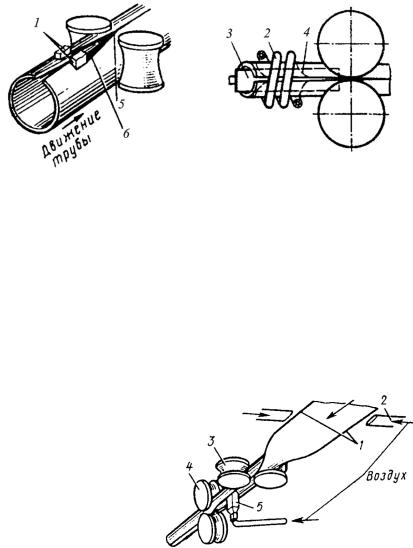
а |
б |
Рис. 17. Схема контактной сварки труб токами высокой частоты: а– приконтактномподводетока; б– прииндукционномподводе тока; 1 – скользящие контакты; 2 – кольцевой индуктор; 3 – магнитный сердечник; 4 – линии сварочного тока; 5 – место сварки; 6 – путь тока
увеличение скорости сварки (до 120 м/мин) в сравнении со сваркой под слоем флюса (110–200 м/час). Кроме того, при высокочастотной сварке одно и то же оборудование можно использовать для изготовления труб из разных материалов.
|
Использование печ- |
|
||
ной сварки для изготовле- |
|
|||
ния труб (рис. 18) позво- |
|
|||
ляет |
повысить |
скорость |
|
|
сварки до 1000 м/мин. |
|
|||
|
При этих |
способах |
|
|
изготовления труб сборка, |
|
|||
формовка и сварка выпол- |
|
|||
няются в движении, что |
Рис. 18. Схема непрерывной печной |
|||
сокращает производствен- |
||||
ные |
площади, |
упрощает |
сварки труб: 1 – штрипс; 2 – сопла для |
|
обдувки воздухом; 3 – формовочные |
||||
транспортные операции. |
||||
ролики; 4 – сварочные ролики |
51
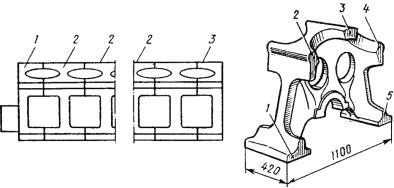
Использование способов сварки давлением кроме указанных преимуществ обеспечивает минимальные остаточные деформации, что сводит к минимуму затраты на обработку после сварки.
Высокое качество соединений обеспечивается при изготовлении не только тонкостенных конструкций (трубы, топливные баки автомобилей, отопительные радиаторы панельного типа и проч.), но и габаритных массивных ответственных изделий. Например, при серийном производстве картеров блоков транспортных дизелей (рис. 19) используется автоматический сборочно-сварочный комплекс для соединения стоек, отлитых из стали 20Л, контактной сваркой непрерывным оплавлением. При этом нижние лапы 1 и 5, боковые стенки 2 и 4 и верхняя перемычка 3 свариваются одновременно (суммарная площадь сварногосоединения достигает 50 000 мм).
а |
б |
Рис. 19. Сварной картер блока транспортного дизеля: а – схема расчленениякартеранапереднюю(1), промежуточные (2) изаднюю(3) стойки; б – литая промежуточная стойка: 1, 5 – нижние лапы;
2, 4 – боковые стенки; 3 – верхняя перемычка
В процессе сварки термический цикл и деформации всех пяти элементов стыка оказываются близкими, поэтому остаточные напряжения в направлении поперек стыка практически отсутствуют. Это позволяет обеспечить минимальную погрешность длины картера, расстояния между осями цилиндров, смещения оси стоек в поперечном направлении пропеллерности основания; уменьшить припуски на ме-
52
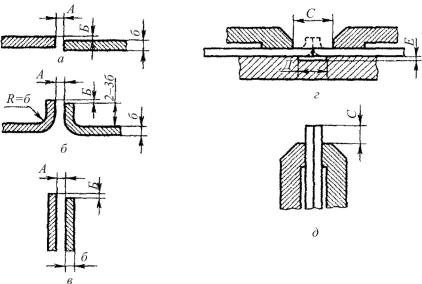
ханическую обработку. Низкий уровень остаточных напряжений главного направления и однородность структуры сварных соединений позволилиотказаться от термической обработки изделияпосле сварки.
Габариты конструкции и толщина свариваемых элементов оказывают существенное влияние навыбор способа сварки. Дляизготовления электронных приборов используются следующие способы сварки: электродуговой, электронно-лучевой, лазерный, плазменный, контактный, холодный, диффузионный, ультразвуковой. Для электронной отрасли разработаны специальные способы сварки: термокомпрессионный, микроплазменный и др. Следует отметить также широкое применение всозданииприборовэлектроннойтехникиразличныхметодовпайки.
Ввиду малой толщины соединяемых металлов (0,3 мм и менее) наиболее часто используются соединения по отбортовке, по технологическим буртикам, а также принудительное охлаждение сварного соединения (рис. 20).
Рис. 20. Конструкция свариваемых кромок и оснастка для сварки:
а– стыковое соединение; б – соединение по отбортовке; в – бортовое соединение; г – оснастка для стыковых соединений и соединений по отбортовке; д – оснастка для бортовых соединений
53
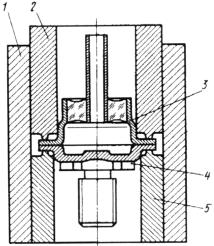
|
Для получения |
сварных |
||
|
соединений в электронных при- |
|||
|
борах |
различного |
назначения |
|
|
широко применяются не только |
|||
|
способы сварки плавлением. Вы- |
|||
|
сокую производительность свар- |
|||
|
ки, прочность и герметичность |
|||
|
сварных соединений |
обеспечи- |
||
|
вают различные способы сварки |
|||
|
давлением. |
|
|
|
|
Например, для гермети- |
|||
|
зации корпусов полупроводни- |
|||
|
ковых |
приборов используется |
||
|
холодная сварка (рис. 21). Соб- |
|||
Рис. 21. Схемагерметизациикорпусов |
ранный |
узел устанавливают |
||
полупроводниковыхприборов |
в приспособление для холодной |
|||
холоднойсваркой: 1 – направляющий |
сварки, состоящее из направ- |
|||
стакан; 2, 5 – верхнийинижний |
ляющего стакана 1 и сварочного |
|||
пуансоны; 3 – крышкакорпуса; |
инструмента (верхнего 2 и ниж- |
|||
4 – основаниекорпуса |
него 5 пуансонов). |
Приспособ- |
ление после загрузки помещают под шток гидроцилиндра пресса. На прессе задают предварительно выбранное давление и производят холодную сварку.
Правильная конструкция рабочих частей инструмента для холодной сварки определяет качество получаемого соединения. Рабочие части пуансонов должны иметь трапецеидальную форму с притуплением острых кромок с внутренней стороны для устранения подреза на утоненной части шва.
В ряде случаев наибольшими преимуществами для получения неразъемных соединений обладает пайка. Она позволяет получать прочные и герметичные соединения одномоментно по всей площади контакта соединяемых деталей; надежно соединять разнородные металлы, а также металлы с неметаллами (керамикой, стеклом и проч.). Паяные соединения могут иметь сложную про-
54
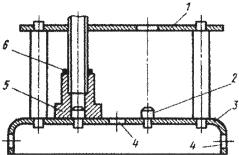
странственную ориентацию |
|
||||
и находиться в недоступ- |
|
||||
ных для сварочного инст- |
|
||||
румента местах (рис. 22). |
|
||||
Кроме того, пайка по- |
|
||||
зволяет |
вести |
групповую |
|
||
обработку сборок, что резко |
|
||||
повышает |
производитель- |
|
|||
ность. Применяемые для та- |
|
||||
ких случаев приспособления |
Рис. 22. Многоместная подставка для |
||||
должны обеспечивать |
точ- |
пайки: 1 – поддерживающий диск; |
|||
ную взаимную |
ориентацию |
||||
2 – опорная стойка; 3 – основание; |
|||||
соединяемых деталей, закре- |
|||||
4 – отверстия для циркуляции газов; |
|||||
пление и придание устойчи- |
|||||
5 – изделие; 6 – припой |
|||||
вости паяемым узлам, |
сни- |
|
жение затрат времени наперемещение и установку сборок в процессе пайки. На рис. 22 представ-
лено многоместное приспособление для пайки, в котором можно разместить детали в процессе сборки. Его можно транспортировать вуниверсальной таре, быстро устанавливать впечь и выниматьизнее.
4.5. РАЗРАБОТКА СХЕМЫ ТЕХНОЛОГИЧЕСКОГО ПРОЦЕССА ИЗГОТОВЛЕНИЯ СВАРНОЙ КОНСТРУКЦИИ
Технологическая схема изготовления сварной конструкции включает в себя: все операции производственного процесса, начиная от выбора исходных заготовок, для деталей, составляющих сборочные единицы; операции заготовительного производства; сборочные, сварочные операции; операции контроля качества и исправления дефектов сварки.
Часто операции заготовительного производства не включаются в технологическую схему изготовления сварной конструкции, т. к. они выполняются на другом участке специалистами по механической
55
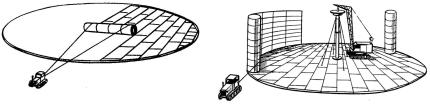
обработке металлов. При составлении схемы операций на сборочносварочном участке предполагается, что детали поступают готовыми.
При разработке технологической схемы необходимо выделить сборочные единицы, сгруппировать составляющие их детали, определить последовательность и приемы выполнения технологических операций и указать параметры режимов сварки. Выбранная последовательность выполнения работ должна обеспечивать минимальное количество операций, необходимых для изготовления конструкции. Кроме того, последовательность выполнения работ определяет возможную трудоемкость изготовления конструкции, расход сварочных и вспомогательных материалов, возможность механизации и автоматизации производства, качество сварных швов.
Например, при изготовлении таких габаритных конструкций, как вертикальные резервуары для хранения нефтепродуктов, возможно применение полистовой сборки и сварки на монтажной площадке. Такая технология требует большого объема ручных работ, что снижает качество и производительность. Разработанный отечественными инженерами метод рулонирования позволил значительный объем работ выполнять в заводских условиях. Узлы конструкции (боковые стенки, днища) в виде полотнищ большого размера собирают, сваривают и сворачивают в рулон на специальных установках в цеховых условиях. При этом используются механизированные и автоматизированные способы сборки и сварки. На монтажной площадке производится разворачивание, сборка и сварка элементов конструкции (рис. 23).
а |
б |
Рис. 23. Схема работ с рулонированными полотнищами при монтаже вертикального резервуара: а – раскатка полотнищ днища; б – разворачивание стенки резервуара
56
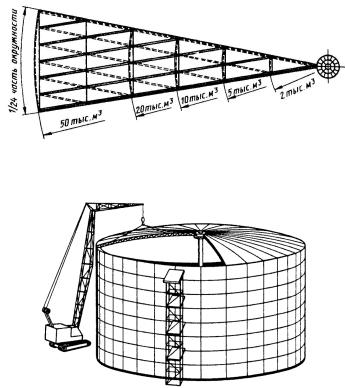
Рис. 24. Компоновка щитов крыши резервуаров различного объема
Рис. 25. Монтаж щитов крыши резервуара
Крыша резервуара выполняется из типовых щитов (рис. 24), которые изготовляются также в заводских условиях, а затем производится их сборка на монтаже (рис. 25).
4.6. ВЫБОР СБОРОЧНО-СВАРОЧНОЙ ОСНАСТКИ
На этапе разработки технологической схемы формируют данные для выбора сборочно-сварочной оснастки и приспособлений, а также составляют техническое задание на проектирование нестандартного оборудования, технологической оснастки и приспособле-
57
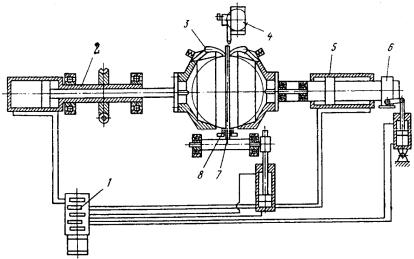
ний. При этом должны быть решены такие вопросы, как выбор схемы базирования и закрепления деталей при сборочных и сварочных операциях; оценка необходимых перемещений изделия с целью обеспечения удобства сборки и сварки, а также перемещений в процессе выполнения сварки.
Разработка и изготовление нестандартного оборудования позволяет учесть особенности изготовления конкретного изделия и обеспечить существенное повышение производительности и качества. На рис. 26 показан станок-автомат для сборки и сварки полых шарообразных поплавков.
Рис. 26. Схема автомата для сборки и сварки полых шаров: 1 – командоаппарат для задания программы рабочего цикла; 2 – передняяпневмобабка; 3 – пружинящиезахваты; 4 – сварочная
головка; 5 – задняяпневмобабка; 6 – колодочныйтормоз; 7 – откидной нож для установки плоскости стыка; 8 – неподвижный упор
Управление рабочим циклом производится командоаппаратом 1. Подача заготовок осуществляется по наклонному лотку. Заготовки движутся попарно до неподвижного упора 8. Совмещение плоскости стыка с плоскостью расположения электрода осуще-
58
ствляется с помощью откидного ножа 7. Во время сборки изделия нож находится в верхнем положении – между центровыми бабками. Полусферы располагаются по обе стороны от ножа и плотно прижимаются к нему штоками пневмобабок – сначала передней 2, а затем задней 5 – и закрепляется пружинящими захватами 3. Шток задней бабки 5 фиксируется колодочным тормозом 6. После этого передняя бабка 2 смещается назад на 2 мм, освобождая зажатый нож 7, который отводится в нижнее положение. Затем передняя бабка с защемленной в ней полусферой подается до полного соприкосновения со второй полусферой. Благодаря наличию тормоза 6
иножа 7 свариваемый стык располагается точно в плоскости электрода сварочной головки 4 независимо от точности изготовления полусфер. По окончании сварки шар по наклонному желобу выкатывается наружу, по пути включая механизм загрузки. Такие устройства при создании требуют больших затрат, что оправдано при большом объеме выпуска изделий.
Необходимость использования нестандартного оборудования
иоснастки требует технического и экономического обоснования. В ряде случаев применение нестандартного оборудования может быть оправданным, когда к точности и качеству конструкции предъявляют особо высокие требования.
Сборка под сварку тонкостенных соединений малогабаритных деталей является одной из наиболее трудоемких и наименее механизированных операций. Она должна обеспечивать установление деталей в заданное положение, точную сборку кромок, требуемый зазор в стыке, закрепление таким образом, чтобы взаимное расположение деталей не нарушалось в процессе сварки, а также свободный доступ к месту сварки. Перед сборкой для тонкостенных соединений требуется тщательная очистка поверхности деталей. Для этого используются травление, очистка в ультразвуковых ваннах, промывка в специальных растворителях, электрохимическая очистка.
Сборка под сварку в приспособлении должна обеспечивать минимальный зазор в стыке, не препятствующий сплавлению кромок. При различных способах сварки плавлением зазор между
59
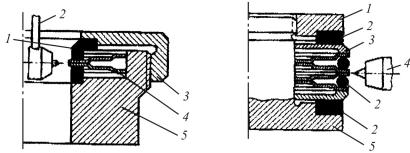
кромками стыковых соединений и превышение кромок колеблется в пределах от 0 до 20 % толщины свариваемых кромок.
Сварку металлов толщиной менее 0,3 мм предпочтительней выполнять по отбортовке кромок. В этом случае расстояние между прижимами может бытьувеличено засчет жесткости ребра отбортовки.
Помимо приспособлений, препятствующих деформациям кромок в процессе сварки, при изготовлении электронных приборов используются и другие различные по своему функциональному назначению виды приспособлений: фиксирующие взаимное положение деталей с заданной точностью; обеспечивающие теплоотвод от места сварки с целью предотвращения перегрева термочувствительных элементов прибора; улучшающие качество защиты места сварки; обеспечивающие принудительное формирование сварного шва. Часто при сварке сложных узлов используются комплексные приспособления, в которых различные функции оснастки могут совмещаться в одной детали или одном узле.
Примером многофункциональных приспособлений для сборки и сварки могут быть приспособления, применяемые для сварки сильфонов (рис. 27). Перед сваркой внутренних швов сильфонов (рис. 27, а) мембраны 4 помещаются в медные оправки 1, собираются в единый узел в корпусе 5 и сжимаются гайкой 3. Сварка выполняется горелкой 2.
а |
б |
Рис. 27. Приспособление для сборки и сварки:
а – внутренних швов сильфонов; б – внешних швов сильфонов
60