
книги / Технология производства сварных конструкций. Ч. 2
.pdfДля уменьшения остаточных деформаций, на стадии проек-
тирования сварной конструкции предпринимаются следующие мероприятия.
1.Назначение минимальных, получающихся по расчету на прочность сечений угловых швов. Площадь поперечного сечения
ивеличина погонной энергии сварки при этом сокращаются пропорционально квадрату катета. Примерно пропорционально квадрату катета уменьшаются усадочная сила и поперечная усадка.
2.Назначение и использование способов сварки, обеспечивающих минимальное тепловложение на один проход шва. Многопроходная сварка в этом отношении имеет преимущество перед однопроходной. Следует, однако иметь в виду и другие требования, относящиеся к качеству металла, скоростям охлаждения, стоимости работ и т.п. при переходе от однопроходной сварки к многопроходной. Контактные способы сварки требуют существенно меньшего вложения тепла, чем дуговые.
3.В сложных конструкциях объемного типа предпочтение следует отдавать таким конструктивным решениям, которые позволяют вначале осуществить сборку конструкции на прихватках, а затем сварку. Большая жесткость первоначально собранного элемента, как правило, обеспечивает меньшие изгибы конструкции при сварке, чем последовательная сборка и сварка конструкции методом наращивания.
4.В необходимых случаях следует использовать такие конструктивные решения, которые бы позволяли отдельным элементам конструкции беспрепятственно сокращаться, не вызывая искажения формы конструкции в целом. Например, при наличии нахлесточных соединений смещение отдельных элементов происходит свободно, изменяя лишь размер нахлестки.
5.В конструкциях с тонкостенными элементами желательно располагать швы на жестких каркасах, чтобы уменьшить коробление.
6.Конструирование элементов балочного типа с таким поперечным сечением и расположением продольных сварных швов, чтобы моменты, создаваемые усадочными силами относительно
41
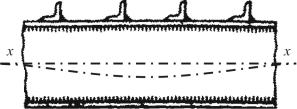
центра тяжести площади поперечного сечения, были взаимно уравновешены. В этом случае изгиб балок будет минимальным. Не следует располагать по одну сторону поперечные швы (рис. 9); их усадка может создать значительный изгиб балки.
Рис. 9. Сварная балка с несимметричным расположением поперечных швов
7. Если проявление значительных искажений от сварки неизбежно, необходимо предусмотреть возможность правки конструкции тем или иным способом. При этом должен быть обеспечен доступ к местам, необходимым для правки.
Приемы рационального конструирования разнообразны и не исчерпываются перечисленными выше способами.
Для того чтобы не терять единство проблемы по снижению остаточных деформаций рассмотрим в этом разделе также мероприятия, используемые на стадии разработки технологии и при осуществлении сварки.
1. Рациональная последовательность выполнения сборочносварочных операций. Пути решения этой сложной задачи разнообразны и все их изложить нет возможности. Например, рассмотренный выше вариант членения сложных габаритных конструкций позволяет не только упростить изготовление, но и уменьшить остаточные деформации. Расчленение конструкции на отдельные узлы, которые могут быть изготовлены с минимальными отклонениями, а затем соединены вместе, позволяет значительно уменьшить остаточные деформации. Порядок наложения швов в соб-
42
ранной конструкции также можно рассматривать как средство регулирования величины остаточных перемещений.
2.Назначение экономичных режимов или способов сварки, обеспечивающих снижение тепловложения или такой характер протекающих деформаций, который отвечает предъявленным требованиям.
3.Разработка необходимой оснастки для закрепления собираемых и свариваемых элементов. Закрепление изделий в приспособлениях эффективно лишь в отношении временных перемещений и тех искажений, которые от них возникают при постановке прихваток или
впроцессе сварки без прихваток. Положительный результат достигается за счет жесткости приспособления. Частными примерами эффективного использования являются: а) прижатие кромок тонких листов или кромок при сварке кольцевых швов; б) скрепление деталей скобами или сухарями при электрошлаковой сварке для уменьшения перемещений. Остаточные прогибы балок при закреплении их в приспособлении уменьшаются незначительно.
4.Пластическая деформация элементов, подлежащих сварке, с целью создания перемещений, противоположных сварочным. Применяют предварительный изгиб полок балок для уменьшения грибовидности после сварки, раскатывают края цилиндрических или сферических оболочек для уменьшения корсетного сокращения от кольцевого шва, производят местную штамповку вблизи отверстий оболочек перед сваркой в них элементов круговыми швами.
5.Сборка заготовок и назначение их размеров с учетом последующей усадки. Например, использование углового излома (рис. 10, а) или сборка с переменным зазором (рис. 10, б) для компенсации угловых перемещений, назначение завышенной длины элементов с учетом последующей усадки, раскрой стенки балки с начальной кривизной (рис. 10, в). К этим же мероприятиям относятся натяжение листов перед сваркой с целью их удлинения, если они могут потерять устойчивость после сварки вследствие усадки (рис. 10, г),
иудлинение листов путем их предварительного подогрева перед сборкой на прихватках (рис. 10, д).
43
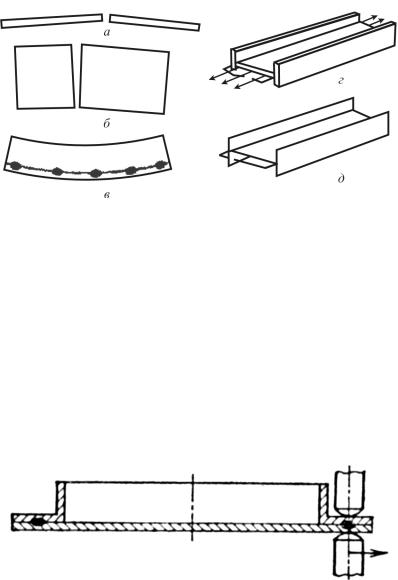
Рис. 10. Схемы создания перемещений, противоположных сварочным
6.Уменьшение площади зоны пластических деформаций путем искусственного охлаждения свариваемых элементов, например поливом водой, обдува газом или газоводяной смесью, подвода охлаждаемых зажимов в зону сварки. В некоторых случаях положительный эффект может быть достигнут путем общего подогрева изделия.
7.Создание напряжений растяжения в зоне сварного соединения путем изгиба или растяжения детали в приспособлении. Сварка по растянутому металлу уменьшает усадочную силу.
8.Создание непосредственно после сварки пластических деформаций удлинения металла путем его проковки либо специальным инструментом, например, при сварке плавлением, либо сварочным электродом – при точечной контактной сварке.
Рис. 11. Схема использования сдвига электродов при сварке для создания напряжений растяжения в тонком листе
44
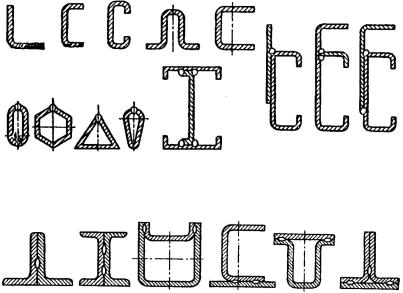
9. Создание в процессе точечной сварки направленного смещения свариваемых элементов для компенсации ожидаемой усадки. Например, потеря устойчивости тонкого листа может быть предотвращена путем его сдвига относительно каркаса в процессе сварки
(рис. 11).
4.3. ВЫБОР МЕТАЛЛА КОНСТРУКЦИИ
Выбор металла конструкции проводится по следующим критериям: обеспечение эксплуатационных требований, свариваемость, стоимость. Выбор используемого сортамента при изготовлении сварных конструкций оказывает существенное влияние на производственную технологичность (рис. 12, 13).
Рис. 12. Конструкции балок из гнутых и штампованных элементов
Рис. 13. Поперечное сечение балок, сваренных контактной сваркой
45
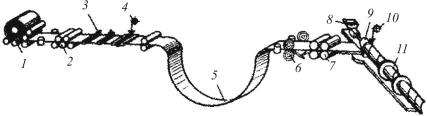
Для несущих конструкций поиск наилучших конструктивных форм, точный учет характера и значений действующих нагрузок, применение уточненных методов расчета позволяют конструктору экономить металл, устраняя излишний запас прочности.
Целесообразно вместо пространственных решетчатых конструкций использовать оболочковые, обеспечивая требования высокой жесткости применением гнутых или гофрированных тонколистовых, а также сотовых элементов. При работе на продольную устойчивость лучше использовать трубные элементы.
При проектировании конструкции необходимо стремиться к минимальной номенклатуре используемых марок и сортаментов металлов. Применение рулонированного металла, проектирование комбинированных штампосварных и лито-сварных конструкций обеспечивают снижение расхода металла, повышение качества и производительности сварочных работ. Например, использование рулонной стали позволяет изготовлять трубы практически любого диаметра с толщиной стенки до 14 мм (рис. 14).
Рис. 14. Схема изготовления спиральношовных труб диаметром 520–1420 мм
Полоса из рулона 1 проходит правильные вальцы 2 и накапливается в компенсационной петле 5, обеспечивая непрерывность выполнения спирального шва при обрезке концов полос гильотинными ножницами 3, а также при сборке и сварке их стыка на установке 4.
После компенсационной петли лента движется со сварочной скоростью, задаваемой вращением толкающих валков 7. С помощью дисковых ножей 6 обрезаются продольные кромки под сварку. Сворачивание полосы в трубу осуществляется заталкиванием ее
46

в формовочное устройство 9. Спиральный шов выполняется сваркой под флюсом тремя сварочными головками. Две из них крепятся на общей штанге 8, вводимой внутрь трубы, третья головка 10 расположена снаружи. Выходящая из стана непрерывная труба летучим устройством 11 разрезается на трубы мерной длины.
Настройку стана на требуемый диаметр трубы производят разворотом формовочной машины и выходного моста. Такая организация производства позволяет получать трубы любого диаметра и длины с минимальным расходом металла.
Выбор металла открывает большие возможности для снижения массы изделия. Наибольшая экономия металла может быть получена при использовании прочных и высокопрочных сталей, а также сплавов свысокой удельной прочностью (алюминиевых, магниевых, титановых). Однако повышение прочности металла нередко сопровождается ухудшением его свариваемости, что усложняет технологию иповышает стоимость сварочных работ. Кроме того, при выборе металла конструкции необходимо учитывать высокую стоимость высокопрочных сталей и цветных сплавов. Поэтому экономия металла засчет повышения его прочностицелесообразнатолькоприучетевсехэтихфакторов.
Для несущих конструкций, работающих в обычных условиях, чаще всего используются малоуглеродистые и низколегированные стали. Для изделий, работающих в специальных условиях (агрессивные среды, повышенные и пониженные температуры и проч.), применение дорогостоящих высоколегированных сталей и сплавов из цветных металлов неизбежно. Для таких случаев большие перспективы имеет применение композиционных материалов, например двухслойных сталей (рис. 15).
Рис. 15. Последовательность сварки стыка корпуса реактора толщиной 150 мм из стали 15Х2НМФА с внутренней плакировкой сталью 08Х18Н10Т
47
Кроме того, необходимо использовать новые марки сталей с экономным легированием, обеспечивающие высокие специальные свойства при относительно невысокой стоимости и обладающие хорошей технологичностью (в том числе свариваемостью).
4.4. ОБОСНОВАНИЕ ВЫБОРА СПОСОБА СВАРКИ
При назначении способа сварки сборочных единиц конструктор и технолог определяют вначале возможные способы сварки для каждой сборочной единицы, а после сравнительного анализа – целесообразность их использования. Критерии, по которым выбираются способы сварки изделия, следующие: обеспечение качественной и производительной сварки материала конструкции с учетом конструктивных ее особенностей; стоимость оборудования и сварочных работ; наличие на предприятии сварочного оборудования и опыта использования того или иного способа сварки.
Наибольший объем применения находят дуговые способы сварки плавлением благодаря их универсальности, мобильности и отсутствию ограничений по толщине свариваемых материалов. Наиболее универсальной и мобильной является ручная дуговая сварка покрытыми электродами. Этот способ позволяет выполнять сварные швы в любых пространственных положениях и труднодоступных местах, но для его реализации требуется высокая квалификация сварщика. Недостатками этого способа являются низкая производительность и большая трудоемкость, что объясняет постоянное сокращение объема применения ручной дуговой сварки.
Из дуговых способов сварки наибольшую производительность обеспечивает сварка под слоем флюса, но этот способ имеет ограничения, связанные с необходимостью засыпки и удержания флюса на поверхности соединяемых деталей и удаления его после сварки. Поэтому автоматическую сварку под флюсом целесообразно применять для выполнения прямолинейных, кольцевых и круговых швов деталей толщиной свыше 4 мм в нижнем положении.
48
Автоматическая и механизированная сварка в среде защитных газов и сварка порошковой проволокой несколько уступает по производительности сварке под флюсом, но обладает большей маневренностью. Объем применения этих способов сварки постоянно увеличивается, особенно для сварки коротких и сложных по конфигурации швов, различно ориентированных в пространстве. Особенно активно растет объем применения сварки в смеси защитных газов проволокой сплошного сечения и сварки с применением самозащитной проволоки.
Повышение степени концентрации энергии в зоне сварки позволяет наряду с повышением производительности получать дополнительные преимущества. Среди них улучшение формы сварного шва, снижение тепловложения в зону сварки и, как следствие сужение зоны термического влияния, повышение служебных характеристик околошовной зоны и снижение остаточных деформаций и напряжений. Кроме того, появляется возможность сварки металлов повышенных толщин без разделки кромок, что значительно снижает затраты.
Использование сварки неплавящимся и плавящимся электродом в инертных газах, электронно-лучевой, лазерной и т.п. определяется применением цветных металлов и высоколегированных сталей для изготовления изделий специального назначения.
Удачное сочетание высокой мощности и концентрации энергии в сжатой дуге с возможностью использования широкой гаммы сварочного и вспомогательного оборудования, разработанного для дуговых способов сварки, предполагает перспективность использования плазменной сварки для производства ответственных сварных конструкций.
Перспективным направлением является использование однопроходной электроннолучевой сварки в вакууме толстостенных сосудов. Экспериментально показано, что при использовании сварки горизонтальным лучом можно выполнять продольные и кольцевые швы металла толщиной 250 мм и более при скорости сварки 2,2–5 м/ч.
49
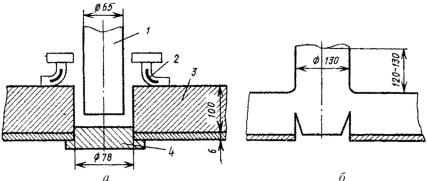
Электрошлаковый процесс используют не только для сварки толстостенных продольных и кольцевых соединений, но и для образования выступающих частей сложной формы. Например, на рис. 16 представлена схема формирования патрубка на корпусе толстостенного сосуда.
Рис. 16. Электрошлаковая выплавка патрубка: а – схема процесса; б – форма поперечного сечения выплавленного патрубка
Предварительно в корпусе 3 сверлят отверстие, в которое изнутри вставляют заглушку 4, а с наружной поверхности корпуса устанавливают медный кристаллизатор 2. Перед началом процесса в кристаллизатор заливают жидкий шлак. Плавлением электрода 1 отверстие и полость кристаллизатора заполняют жидким металлом. В результате такой электрошлаковой выплавки в корпусе образуется выступ, механическая обработка которого обеспечивает получение патрубка требуемой конфигурации.
Расчет режимов сварки и выбор сварочных материалов определяется маркой и толщиной свариваемого металла, типом шва; он должен обеспечивать максимальную производительность сварки при высоком качестве сварного соединения.
Наибольшую производительность дают способы сварки давлением (контактная точечная и шовная, стыковая, индукционная, печная и др.). Например, использование сварки токами высокой частоты для изготовления труб (рис. 17) обеспечивает значительное
50