
книги / Машины и оборудование нефтяных и газовых промыслов. Оборудование для эксплуатации и ремонта нефтяных и газовых скважин
.pdf–трехпревенторная с двумя линиями манифольда (рис. 1.5, б);
–трехпревенторная с тремя линиями манифольда (рис. 1.5, в);
–трехпревенторная с четырьмя линиями манифольда (рис. 1.5, г).
Обвязка |
«превенторы – манифольд» предназначена для управления давлением |
в скважине при |
нефтегазопроявлениях путем воздействия на пласт закачкой раствора и |
создания противодавления на него. Манифольд состоит из линий дросселирования и глушения, которые соединяются со стволовой частью оборудования для герметизации и представляют собой систему трубопроводов и арматуры (задвижки и регулируемые дроссели с ручным или гидравлическим управлением, манометры и др.). Линия глушения соединяется с буровыми насосами и служит для закачки в скважину утяжеленного раствора по межтрубному пространству. При необходимости линия глушения используется для слива газированного бурового раствора в камеру-дегазатор циркуляционной системы буровой установки.
Линия дросселирования служит для слива бурового раствора и отбора флюидов из скважины с противодавлением на пласт, а также для закачки в скважину жидкости с помощью цементировочных агрегатов. В схеме на рис. 1.5, г, применяемой при бурении скважин с повышенной опасностью нефтегазопроявлений, верхняя линия дросселирования служит резервной.
Манифольды рассчитывают на рабочее давление 21; 35; 70 МПа. В зависимости от конструкций задвижек они бывают двух типов: МП – с клиновыми задвижками и МПП – с прямоточными задвижками. Манифольды типа МП в блочном исполнении шифруются МПВ. В шифре манифольдов цифрами указывается диаметр их проходного отверстия (мм) и рабочее давление (МПа). Например, манифольд диаметром 80 мм (принимаемый в настоящее время для всех манифольдов) на давление 35 МПа шифруется МПВ-80×35.
Манифольды устанавливают на рамах-салазках с телескопическими стойками, позволяющими регулировать высоту их расположения в пределах 0,65–1,25 м в зависимости от положения колонной головки над устьем скважины. Высота расположения головки изменяется после спуска и цементирования каждой обсадной колонны. Высота разъемного желоба устанавливается по расстоянию между фланцевой катушкой и ротором буровой установки.
Как видно из схем на рис. 1.5, на установках монтируют один или два плашечных превентора. В морских скважинах с устьем на дне моря устанавливают три, а иногда и четыре плашечных превентора, а над ними универсальный превентор. В морских установках монтируют иногда два универсальных превентора. При бурении под давлением над этим превентором располагают вращающийся превентор.
После монтажа линии манифольдов превенторы подвергают гидроиспытаниям под давлением, в 1,5 раза превышающим рабочее [3].
1.3. Эксплуатация оборудования для герметизации устья скважины
Оборудование для герметизации устья скважины применяется как противовыбросовое оборудование, не работающее в процессе бурения. Оно может быть использовано для регулирования давления в скважине в процессе бурения. Однако отказ в работе его может привести к тяжелым последствиям и в некоторых случаях к гибели людей. Неисправная работа этого оборудования особенно опасна при бурении на море, где борьба с открытыми фонтанами нефти наиболее тяжелая.
Для обеспечения исправной и надежной работы необходимо выполнять следующие условия:
–монтировать оборудование в соответствии с инструкцией завода-изготовителя;
–проверять монтаж и проводить испытание оборудования на пробное и рабочее давление;
11
–систематически в процессе проводки скважины ухаживать за оборудованием и делать пробные его испытания в установленные сроки, независимо от того, используется оно или нет;
–по окончании бурения, если оборудование не будет сейчас же использовано, его необходимо очистить, проверить и законсервировать, а в случае неисправности отремонтировать.
При монтаже все оборудование собирают, затем проверяют соосность его расположения, заземление пультов управления, заполнение резервуаров газом и маслом, соответствующими времени года, и регулируют давление включения электронного манометра (10 ± 0,25 МПа) и выключения (9 ± 0,25 МПа). После этого опрессосывают гидросистему на рабочее давление 10 МПа в течение 10 мин. При этом снижение давления не должно быть более 3 %. Одновременно осматривают соединения.
Вслучае обнаружения утечек их устраняют, а испытание повторяют.
Оборудование, подлежащее испытанию пробным давлением, проверяют при давлении в 2 раза больше рабочего с выдержкой в течение 6 мин. Для устранения в системе воздушных пробок и стабильности работы и времени срабатывания многократно закрывают и открывают задвижки и превенторы всеми распределителями до тех пор, пока время их закрытия не будет постоянным и соответствовать установленному.
Для работы противовыбросового оборудования при отрицательных температурах должна быть подсоединена система обогрева или его следует утеплить так, чтобы все системы работали исправно при температуре окружающей среды до –40 °С.
Противовыбросовое оборудование может эксплуатироваться в двух режимах работы: нормальная работа, когда непосредственной угрозы выбросов и газопроявлений нет; оперативная готовность при прохождении пластов с возможными нефтегазовыми проявлениями, при этом все должно быть тщательно проверено в соответствии с заводской инструкцией и готово к работе в любой момент.
В периоды нормальной работы буровой мастер должен в процессе СПО проверять исправность превенторов, задвижек и системы их управления, а при бурении и других операциях проверять исправность действия превенторов и задвижек 1 раз в неделю и результаты проверки заносить в журнал. При герметизации скважины дополнительное давление на выкиде превенторов следует снижать постепенно по 0,3–0,7 МПа в 1 мин.
Допускается смена плашек превенторов на буровой. Для этого плашки приводят в крайнее открытое положение; развинчивают винты крепления крышки к корпусу и откидывает ее; выдвигают частично плашку из крышки и снимают ее с выступа штока; заменяют вкладыши или уплотнение. Для смены плашек гидросистему не разбирают. При открытии крышки превентора необходимо каждый раз вынимать торцовые уплотнения, очищать канавки и торцовые поверхности крышки и корпуса, полость плашек и сами плашки от бурового раствора и выбуренной породы, так как она препятствует полному открыванию плашек.
Регулярно 1 раз в 2–3 мес. проверяют состояние резиновых уплотнений и заменяют их при обнаружении даже небольших повреждений. Производят полную замену. Резиновые уплотнения заменяют полностью 1 раз в 2 года. Масло в гидросистеме проверяют не реже чем 1 раз в 3 мес. Допускается содержание примесей в нем не более 0,05 %. При загрязнении гидросистемы масло сливают, промывают систему бензином, просушивают и заполняют свежим маслом.
В процессе эксплуатации все манифольды ежедневно проверяют путем открывания задвижек. Утечки жидкости в манифольде свидетельствуют о неисправности его уплотнений. Замеченные неисправности устраняют [1, 2, 3].
12
1.4. Система управления оборудованием для герметизации устья скважины
Оборудование для герметизации устья скважины служит для быстрого перекрытия его в случаях газопроявлений в скважине, а также для управления давлением в процессе бурения. При газопроявлениях выброс нефти или газа начинается очень быстро и протекает интенсивно, что может привести к повреждению скважины, оборудования и загрязнению окружающей среды.
Оперативное дистанционное управление превенторами и задвижками предназначено для герметизации устья скважины, ее разрядки, создания давления на пласт, его регулирования и закачки раствора для восстановления и поддержания циркуляции.
При помощи оборудования для герметизации устья выполняют следующие операции:
–герметизацию устья скважины при наличии или отсутствии в ней бурильной колонны;
–расхаживание и проворачивание (при вращающемся превенторе) бурильной колонны при герметизированном устье скважины во избежание ее прихватов;
–восстановление циркуляции промывочной жидкости с противодавлением на
пласт;
–быстрое снижение давления в скважине;
–закачку бурового раствора через затрубное пространство для создания обратной циркуляции;
–поддержание на забое равновесного давления при бурении.
Система управления рассчитана на работу в интервале температур от –40 до + 50 °С и должна действовать надежно и быстро. Для этого, например, управление плашечными превенторами выполняется резервированным: гидравлическое дистанционное – с поста бурильщика; и ручное – со штурвалами, расположенными на уровне земли на расстоянии 10–15 м от устья.
На рис. 1.6 приведена схема управления оборудованием для герметизации устья скважины 7. Оборудование представлено универсальным 2 и одним или несколькими плашечными 3 превенторами, а также системой их обвязки.
Управление превенторами резервировано, для чего имеются по два штурвала управления 4 каждым плашечным превентором, двойная система дистанционного гидропневматического управления: с пульта бурильщика 1 и основного пульта 6. С этих пультов осуществляется дистанционное управление плашечными и универсальным превенторами. Затрубное пространство скважины связано системой трубопроводов с блоками дросселирования 5 и глушения 8. Трубопроводы перекрывают задвижками с ручным управлением.
Управление превенторной установкой. Превенторная установка на устье скважины управляется: механической, гидравлической и электрической системами управления.
Исполнительными органами в превенторах являются гидравлические цилиндры или механические устройства, развивающие большие усилия, которые необходимы для перемещения рабочих органов – плашек или манжет для уплотнения пространства между трубами и скважиной при больших давлениях. Электрические системы применяют только для включения или выключения. Для этих устройств необходимо быстро подводить значительную мощность, поэтому гидравлическое управление с давлениями жидкости до 10 МПа, поступающей от гидропневматических аккумуляторов, получило наибольшее распространение.
Гидравлическое управление предназначено для оперативного дистанционного управления превенторами и задвижками манифольда.
13
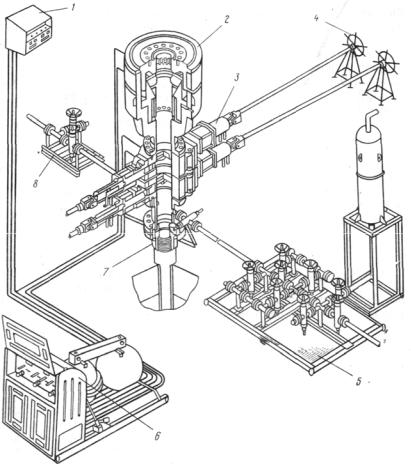
Рис. 1.6. Схема управления оборудованием для герметизации устья скважины
Оперативное дистанционное управление превенторами и задвижками манифольда осуществляется гидравлическим приводом с двух взаимно сблокированных пультов: основного и вспомогательного. Схема гидравлического управления рассчитана на дистанционное управление тремя плашечными превенторами, одним универсальным и двумя задвижками манифольда.
Основной пульт (рис. 1.7) предназначен для управления превенторами и задвижками с безопасного места вне буровой. В основной пульт входят: шестеренный насос 9 с электродвигателем 8, электрооборудование 7, ручной насос 12, гидропневматический шаровой диафрагменный аккумулятор 11, масляный бак 6, распределительный блок 5 с рукоятками управления 2 и 4, фильтр 14, предохранительный 10 и обратный 15 клапаны. Все элементы смонтированы на общей раме 13 и представляют собой комплектный транспортабельный блок.
Электродвигатель привода насоса имеет автоматическое управление от электроконтактного манометра 3, электросистема которого регулируется на давление 10 МПа для включения и отключения электродвигателя. Для визуального контроля давления служит манометр 1.
С основного пульта можно открывать и закрывать плашечные превенторы и задвижки. Универсальный превентор с основного пульта можно только закрывать. Распределитель основного пульта, управляющий универсальным превентором, подает масло в блокировочный цилиндр соответствующей рукоятки распределителя на вспомогательном пульте и переводит ее в положение «закрыто» – превентор закрывается. Блокировочный цилиндр – одностороннего действия, поэтому закрытый с основного пульта универсальный превентор открыть со вспомогательного пульта
14
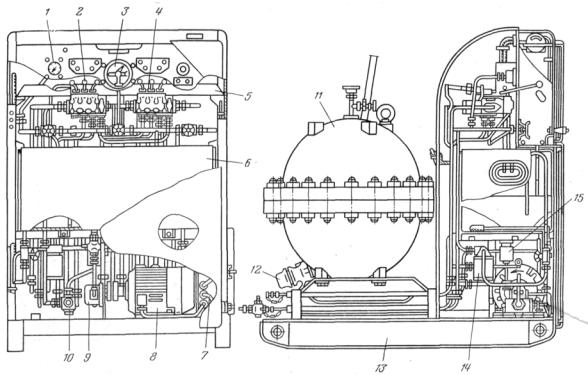
невозможно. Для управления универсальным превентором со вспомогательного пульта необходимо перевести рукоятку распределителя основного пульта в положение «открыто».
Гидропневматический аккумулятор на пульте служит для обеспечения системы управления превенторами необходимым запасом энергии и быстрого их приведения в действие (10–15 с). Поэтому в аккумулятор подается масло под давлением до 10 МПа при помощи шестеренного насоса 9, а при отключении электроэнергии – ручным насосом 12.
Рис. 1.7. Основной пульт управления превенторами с гидропневматическим аккумулятором
Внутри шарового сосуда аккумулятора размещается диафрагма, разделяющая рабочую жидкость (масло) от газа (азота), служащего пневматической пружиной для поддержания необходимого давления для приведения в действие превенторов. Вспомогательный пульт предназначен для управления превенторной установкой непосредственно с рабочего места бурильщика. С этого пульта можно закрывать плашечные превенторы, открывать рабочую задвижку манифольда, закрывать и открывать универсальный превентор.
Масло от основного пульта поступает в нагнетательную линию регулирующего клапана и одного из распределителей. Распределители, управляющие плашечными превенторами и задвижкой манифольда, подают масло в блокировочные цилиндры соответствующих распределителей на основном пульте, благодаря чему превенторы закрываются и задвижки открываются.
Распределитель, управляющий универсальным превентором, питается через регулирующий клапан, в результате этого в универсальный превентор подается любое в зависимости от настройки клапана давление (от 0 до 10 МПа). Величина давления отмечается на манометре.
В случае возрастания давления в запорной камере универсального превентора (при расхаживании бурильной колонны или ее протаскивании) выше отрегулированного на клапане избыточное количество масла через фильтр попадает в распределитель, далее в регулирующий клапан, затем сбрасывается на слив. В процессе слива нагнетательная
15
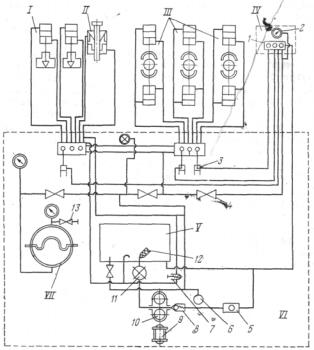
линия гидроуправления автоматически отсекается. При падении давления в запорной камере универсального превентора ниже отрегулированного на клапане недостающее количество масла поступает от гидроуправления через регулирующий клапан и распределитель.
Рис. 1.8. Схема гидравлического управления оборудованием для герметизации устья скважины: 1 – распределитель; 2 – манометр; 3 – блокировочный цилиндр;
4 и 13 – вентили масла и азота; 5 – ручной насос; 6 – масляный фильтр; 7 и 8 – клапаны предохранительный и обратный; 9 – электродвигатель; 10 – масляный насос; 11 – кран; 12 – маслосборник; I – управляемые задвижки; II – универсальный превентор;
III – плашечные превенторы; IV – вспомогательный пульт; V – масляный бак;
VI – основной пульт; VII – гидравлический аккумулятор
Для нормальной работы регулирующего клапана давление в нагнетательном трубопроводе должно быть 10 МПа. При подаче масла в нагнетательную линию под давлением выше 10 МПа часть его сбрасывается через клапан в бак. Это приводит к частому включению шестеренного насоса и быстрому выходу его из строя. При подаче масла под давлением ниже 10 МПа в нагнетательную линию регулирующего клапана в процессе протаскивания труб через превентор избыток масла сбрасываться не будет, что приводит к повышенному износу и выходу из строя уплотнителя универсального превентора.
Перед пуском в эксплуатацию система опрессовывается под давлением в 1,5 раза выше рабочего. Преимущество превентора с гидравлическим управлением – их быстродействие. Так, на закрытие плашечного превентора затрачивается не более 10 с, а при ручном способе – около 70 с. Кроме того, превенторы с гидравлическим управлением просто монтируются, в них можно быстро заменить плашки без съема превентора с устья скважины, даже при наличии в ней бурильной колонны. Замена плашек осуществляется через боковые прямоугольные отверстия в корпусе превентора, закрываемые откидными крышками. Через эти отверстия плашки устанавливают в собранном виде. Для обогрева плашек в зимнее время имеется паропровод.
Схема гидравлического управления превенторами и задвижками, которая использована в современной превенторной установке, приведена на рис. 1.8. Управление может быть осуществлено с двух пультов – основного и вспомогательного.
16
С основного пульта осуществляется управление всеми перечисленными агрегатами, а с вспомогательного – непосредственно с буровой установки – управление двумя плашечными превенторами [1, 3, 4].
2.ОБОРУДОВАНИЕ ЭКСПЛУАТАЦИОННОЙ СКВАЖИНЫ
Внефтегазодобывающей промышленности сооружаются скважины разных назначений, в зависимости от чего их принято называть структурно-поисковыми, разведочными, эксплуатационными, нагнетательными, специальными.
Эксплуатационными скважинами обычно называют скважины, с помощью которых осуществляется непосредственно добыча нефти, газа или газового конденсата; нагнетательными – через которые в пласт нагнетаются вода, газ, пар. Однако в ряде случаев в процессе разработки месторождения скважины, добывающие нефть, используются как нагнетательные, а иногда и наоборот. Поэтому и те и другие скважины отнесены к эксплуатационным.
Скважины специального назначения используются для контроля хода разработки месторождения, уточнения структуры, теплового воздействия на пласт и т.д.
Эксплуатационная скважина является основным, важнейшим видом сооружений, а их совокупность представляет собой эксплуатационный фонд скважин, стоимость которого составляет до 75–80 % стоимости всего технического оснащения современного промысла. Нарушение целостности, работоспособности эксплуатационной скважины приводит к прекращению ее эксплуатации, к неизбежному уменьшению добычи нефти или газа, что делает необходимым выполнение так называемого капитального ремонта скважины – процесса длительного, трудоемкого и весьма дорогого; стоимость ремонта скважины часто соизмерима, а иногда одинакова со стоимостью ее сооружения.
Поэтому долговечность скважины должна соответствовать периоду разработки продуктивного пласта, т.е. равняется нескольким десятилетиям. Отсюда и главное требование к качеству оборудования, используемого в эксплуатационной скважине, – его надежность.
Требования к сооружению скважины и к ее оборудованию определяются условиями ее эксплуатации, которые, в свою очередь, весьма различны, зависят, прежде всего, от геологических особенностей месторождений, режима эксплуатации скважины.
Эксплуатационные скважины в зависимости от геометрической формы их ствола сооружаются двух основных типов: вертикальные и наклонные. Наклонная форма – результат необходимости направления ствола скважины в заданный участок пласта; такие скважины обычно называются наклонно направленными. Профили этих скважин бывают разными в зависимости от требований технологии проводки скважины и способа ее эксплуатации. В любом случае профиль наклонной эксплуатационной скважины должен обеспечивать возможность эксплуатации ее рациональным способом
иисключать вероятность повреждения как самой скважины, так и спущенного в нее оборудования для ее эксплуатации выбранным способом. На рис. 2.1 показаны профили скважин: рис. 2.1, а – вертикальный, рис. 2.1, б – наклонный с наибольшим отклонением забоя от вертикали. Как видно, он состоит из трех участков: вертикального, переходного, соответствующего набору максимально необходимого зенитного угла, и наклонно-прямолинейного до забоя. Профиль на рис. 2.1, в отличается наличием участка уменьшения зенитного угла. Профиль (рис. 2.1, г) имеет вертикальный участок, участок набора зенитного угла, наклонно-прямолинейный участок, участок уменьшения зенитного угла и нижний – вертикальный. Этот профиль более сложный, обеспечивает вертикальность ствола скважины при проводке ее на несколько продуктивных горизонтов. Профиль (рис. 2.1, д) отличается отсутствием наклонно-прямолинейного участка. В профиле (рис. 2.1, е) нет наклонно-прямолинейного и нижнего вертикального участков. Каждый из показанных на схемах профилей эксплуатационной скважины
17
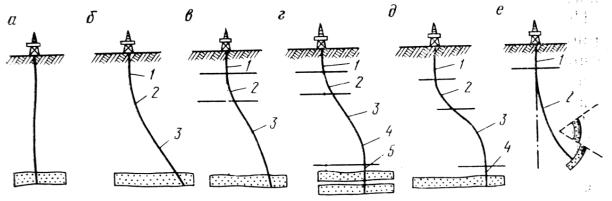
предопределяет особенности последующей эксплуатации как самой скважины, так и спущенного в нее оборудования. В тех случаях, когда расстояния между устьями скважин малы и измеряются метрами, а скважины наклонные, группа таких скважин называется кустом скважин.
Для улучшения дренирования продуктивного пласта иногда из вертикальной части скважины в пласт бурятся несколько скважин, которые называются многозабойными.
Рис. 2.1. Схемы профилей эксплуатационных скважин: 1, 3, 5 – вертикальный участок; 2, 4 – горизонтальная зона
На рис. 2.2 показана принципиальная схема эксплуатационной скважины и ее оборудования. Скважина состоит из трех основных участков – устьевого, стволового и фильтрового, каждый из которых оснащен соответствующим оборудованием: колонной головкой 1, направлением 2, кондуктором 3, эксплуатационной колонной 4, фильтром 6. Дно скважины обычно называется забоем. Иногда скважина оснащается пакером и клапаном-отсекателем 5 пласта.
Стволовая часть эксплуатационной скважины образована, как видно из схемы, концентричными колоннами обсадных труб, зацементированных в горных породах.
Последняя, т.е. внутренняя, обсадная колонна скважины называется эксплуатационной и служит каналом, соединяющим объект эксплуатации – пласт с устьем скважины (с поверхностью). Диаметр труб, из которых она состоит, должен обеспечивать возможность размещения в ней оборудования для эксплуатации скважины заданным способом, а также возможность выполнения всех технологических процессов и операций, необходимость в которых может возникнуть в течение всего периода эксплуатации скважины. Долговечность колонны должна соответствовать сроку службы скважины.
Наружная обсадная колонна скважины – направление – спускается на глубину нескольких метров, а ее затрубное пространство цементируется на всю длину. Внутри направления размещается обсадная колонна, обычно называемая кондуктором и имеющая длину, как правило, от 200 до 600–800 м. Кондуктор цементируется на всю длину.
Между кондуктором и эксплуатационной колонной могут спускаться обсадные трубы, которые обычно называются техническими или промежуточными колоннами. Они выполняют технологические функции при сооружении скважины, число и глубины их спуска определяются геологическими особенностями проходимых пород, глубиной скважины, техникой и технологией ее проводки.
Колонная головка, монтируемая на кондукторе, обвязывает в единую систему кондуктор, технические, эксплуатационную колонны скважины и служит базой для спускаемого в скважину эксплуатационного и установки на него устьевого оборудования.
18
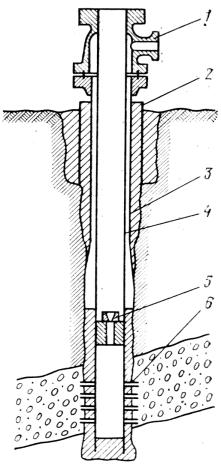
Фильтровая часть эксплуатационной скважины обеспечивает ее связь с пластом как при извлечении пластовой жидкости или газа, так и при нагнетании в пласт воды, газа и других сред.
Ствол скважины, обсадные колонны находятся под постоянным давлением горных пород, а эксплуатационная колонна – под давлением пластов или закачиваемых жидкости или газа. Кроме внутреннего и наружного давлений, обсадные колонны несут нагрузку от собственного веса, а кондуктор воспринимает вес или часть веса остальных колонн. Колонная головка воспринимает усилия от обсадных колонн, внутреннего давления, веса эксплуатационного, базирующегося на ней оборудования.
Рис. 2.2. Схема эксплуатационной скважины
Как внутреннее давление, так и наружное в процессе эксплуатации скважины меняются. При эксплуатации скважины фонтанным способом пульсирующая работа подъемника приводит к появлению переменных нагрузок, аналогично и при эксплуатации скважины штанговым скважинным насосом, приводимым в действие механическим станком-качалкой, на систему обсадных труб и цементное кольцо действуют переменные нагрузки, расшатывающие эту систему.
При штанговой эксплуатации насосные трубы из-за переменных нагрузок постоянно перемещаются в эксплуатационной колонне и истирают ее. При больших дебитах и наличии в пластовых жидкости или газе абразива возникают условия, приводящие к гидроабразивному изнашиванию труб.
Нефтяные, газовые, газоконденсатные скважины либо с начала эксплуатации, либо на определенной стадии вместе с нефтью, газом, конденсатом дают пластовую, как правило, сильно минерализованную воду, являющуюся активно коррозионно-
19
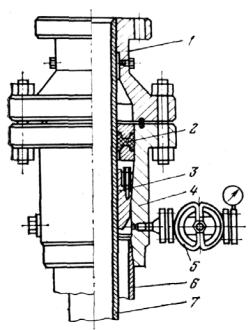
агрессивной средой, а она разрушающе действует на обсадные трубы, колонную головку и цементное кольцо.
Во все больших количествах в разработку вводятся месторождения, в которых нефть или газ содержат углекислый газ и сероводород, причем если еще недавно наличие, например, 4–5 % H2S считалось высоким, то в настоящее время в разработку вводятся месторождения с содержанием сероводорода до 20–25 %. С увеличением глубин разрабатываемых месторождений повышаются не только давление, но и температура пластовой жидкости или газа, достигающая более 250 °С в районах с высоким геотермическим градиентом.
Закачка в скважину под большим давлением кислоты, рабочих жидкостей, газа, высокотемпературных теплоносителей также приводит к осложнению условий ее работы.
Таков комплекс факторов, из которых слагаются условия работы эксплуатационной скважины, факторов, определяющих требования к конструкции, характеристикам и параметрам оборудования каждой скважины. Упущение каких-либо из них, незнание их в процессе сооружения скважины и особенно последующего периода ее эксплуатации, при ее ремонтах неизбежно приводят к серьезным осложнениям, отрицательно сказываются на надежности скважины в целом, часто являются причиной аварий, ущерба окружающей среде и несчастных случаев [7, 10].
2.1. Оборудование устья эксплуатационной скважины
На устье скважины обсадные колонны обвязываются, т.е. соединяются частью оборудования скважины, называемой колонной головкой.
Колонная головка (рис. 2.3) жестко соединяет в единую систему все обсадные колонны скважины, воспринимает усилия от их веса и передает всю нагрузку кондуктору. Она обеспечивает изоляцию и герметизацию межколонных пространств и одновременно доступ к ним для контроля состояния стволовой части скважины и выполнения необходимых технологических операций. Колонная головка служит пьедесталом для монтажа эксплуатационного оборудования, спущенного в скважину. Во время бурения на ней монтируются превенторы противовыбросного оборудования, демонтируемые после окончания бурения.
Рис. 2.3. Конструкция колонной головки
20