
книги / Машины и оборудование нефтяных и газовых промыслов. Оборудование для эксплуатации и ремонта нефтяных и газовых скважин
.pdfКонструктивно колонная головка – это сочетание нескольких связанных между собой элементов – катушек или крестовин, несущих обсадные колонны. Число этих элементов зависит от числа обсадных колонн скважины.
Условия работы колонной головки достаточно сложны: нагрузка от веса обсадных колонн может превышать в глубоких скважинах несколько сот килоньютонов. Элементы колонной головки воспринимают также давление от среды, контактирующей с ними. При наличии в пластовой жидкости или газе H2S, CO2 или при сильной минерализации пластовых вод колонная головка подвергается их коррозионному воздействию. В глубоких скважинах при закачке теплоносителей их стволы и колонные головки нагреваются до 150–250 °С, в условиях севера могут охлаждаться до температур ниже –60 °С.
Нарушение надежности колонной головки неизбежно приводит к серьезным авариям, нанесению ущерба окружающей среде, а в отдельных случаях может быть причиной возникновения пожаров, взрывов, несчастных случаев.
Колонные головки, особенно многоколонных скважин, имеют большие массы и вертикальные габариты. Высокая их металлоемкость и большая потребность в них приводят к необходимости расхода на их изготовление больших количеств стали, причем легированной. С увеличением вертикального габарита колонной головки усложняется обслуживание скважины.
Перечисленные особенности условий работы колонных головок и особенности самих головок делают обязательными при их конструировании выполнение целого ряда требований, к главным из которых относятся обеспечение высокой надежности всех элементов и в целом колонной головки в течение всего срока службы скважины, в любых условиях ее эксплуатации и минимальных металлоемкости и вертикальных габаритов.
Колонная головка для обвязки двух колонн (см. рис. 2.3) состоит из корпуса 4, навинченного на обсадную трубу 6. Внутренняя поверхность корпуса коническая, и в ней размещены клинья 3, удерживающие внутреннюю колонну обсадных труб 7. На фланце корпуса установлена катушка 1, надетая на трубу и обычно сваренная с ней. Катушка болтами соединена с корпусом. Межтрубные пространства разобщаются уплотнениями 2. На колонной головке предусмотрена задвижка 5 для обеспечения доступа в затрубное пространство. Вертикальный размер такой колонной головки – около 1 м. Масса в зависимости от диаметра обсадных труб до 500–550 кг.
Такими головками оборудуются скважины глубиной до 1500–2000 м с давлением до 25 МПа.
Изготовляют колонные головки для оборудования скважин и с большим числом обсадных колонн: трех-, четырех- и пятиколонных. Принципиальные и конструктивные схемы таких колонных головок аналогичны.
Головка для обвязки пяти колонн (рис. 2.4) предназначена для глубоких (более 5000 м) скважин с давлением до 70 МПа и вертикальным размером порядка 3 м. Основные узлы – пять крестовиков 1, 8, 9, 10, 11 для обсадных труб размером от 168 до 502 мм, клиньевые подвески 2, 4, 5, 7 и вентили 3. Обсадная колонна диаметром 168 мм – последняя, т.е. эксплуатационная. Крестовик 1 служит пьедесталом для фонтанной арматуры. Особенностью колонной головки является коническая форма тыльных поверхностей клиньев и ответных поверхностей в корпусе, а также конструкция уплотнительных элементов 6, применяемых в сочетании со смазкой, что способствует надежной герметизации зазоров.
21
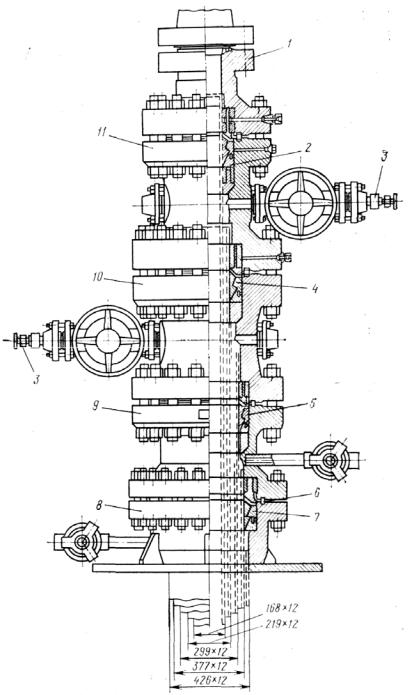
Рис. 2.4. Конструкция колонной головки для глубокой скважины с пятью колоннами
Корпуса крестовины и катушки колонных головок изготавливаются из литых стальных, реже из комбинированных заготовок с литым корпусом и приваренными коваными или штампованными горловинами и фланцами. Заготовки после сварки подвергаются термообработке для снятия напряжений и улучшения механических свойств металла. Предел текучести сталей для корпусов – 5,0–5,5 МПа, относительное удлинение – 14–15 % и ударная вязкость – до 40 Дж/см2. Для изготовления колонных головок, работающих в тяжелых условиях, используются низколегированные стали типа 35ХМЛ. Штампованные или кованые привариваемые фланцы или горловины изготавливаются соответственно из сталей типа 35ХМ, 40Х [7].
22
2.2. Оборудование скважины для предупреждения открытого фонтанирования
Некоторые виды ремонта и обслуживания нефтяных или газовых скважин в фонтанный период их эксплуатации, а иногда при эксплуатации высоконапорных пластов газлифтным или насосным способом связаны с необходимостью глушения скважин утяжеленными растворами. При этом выполняют сложные дорогостоящие работы. Однако надо отметить, что глушение отрицательно сказывается на последующей эксплуатации скважины из-за снижения проницаемости призабойной зоны пласта.
К глушению скважины прибегают и при аварийном (открытом) фонтанировании скважины, а также при спуске в фонтанную скважину труб или другого оборудования.
При разрушениях оборудования устья, обсадных колонн, фонтанной арматуры возникают открытые, неуправляемые фонтаны, т.е. аварийная ситуация, ликвидация которой обычными приемами (герметизацией устья и глушением) чрезвычайно сложна.
Каждый случай открытого фонтанирования скважины наносит серьезный ущерб окружающей среде, причем тем больший, чем продолжительней открытое фонтанирование и чем больше дебит скважины. Открытое фонтанирование часто приводит к пожарам, несчастным случаям, к нанесению непоправимого ущерба самой нефтяной или газовой залежи.
Для исключения открытого фонтанирования при аварийном разрушении устьевого оборудования или во время ремонтных работ скважины, способные фонтанировать, оборудуются размещаемыми в нижней части ствола скважины клапанами-отсекателями пласта для разъединения нижней фильтровой части скважины от ее верхней части.
Клапан-отсекатель пласта также должен позволять выполнять все необходимые в период эксплуатации скважины технологические процессы, например кислотную обработку пласта, его гидроразрыв или смену насосного или фонтанного оборудования и т.п. Поэтому клапан-отсекатель пласта дополняется другим оборудованием и представляет систему, состоящую из нескольких устройств, главными из которых являются сам клапан-отсекатель, герметизатор (пакер), якорь, удерживающий пакер на заданном уровне, канал связи для управления клапаном, собственно управление, устройство для обеспечения возможности установки и демонтажа клапана, якоря и пакера, устройство для выполнения технологических процессов и операций.
Перечисленные устройства, размещенные непосредственно над фильтровой частью скважины, эксплуатируются в условиях, определяемых особенностями эксплуатации пласта, т.е. свойствами пластовой жидкости или газа, их дебитом, агрессивностью среды, наличием или отсутствием абразива, температурой, давлением. В этих условиях каждое из этих устройств должно безотказно срабатывать в течение всего периода его эксплуатации в скважине, что является весьма сложной инженерной задачей.
Требования защиты окружающей среды, охраны труда и техники безопасности сделали этот вид внутрискважинного оборудования, несмотря на его сложность и высокую стоимость, обязательным элементом оборудования фонтанных нефтяных или газовых скважин.
Клапан-отсекатель пласта (рис. 2.5) состоит из пакера 1, клапана-отсекателя 2, разъединителя 3, циркуляционного клапана 4 для аварийного глушения скважины, клапана для ввода ингибитора 5, телескопического соединения 6 для компенсации линейных деформаций, дросселя 7 для регулировки расхода пластовой жидкости, приемного клапана 8. Пакеры отличаются направлением воспринимаемого и передаваемого на эксплуатационную колонну усилия, а также способами фиксации, посадки и извлечения, исполнениями для разных сред, размерами и конструкцией.
23

Рис. 2.5. Схема оборудования скважины для предупреждения открытого фонтанирования с клапаном-отсекателем пласта
С клапанами-отсекателями используют пакеры двух типов: неизвлекаемый и демонтируемый. Первые, часто называемые стационарными, удаляются из ствола скважины с предварительным разбуриванием (поэтому называются иногда разбуриваемыми), вторые извлекаются без разбуривания. Пакеры обоих типов спускаются на колонне насосно-компрессорных труб (НКТ), а иногда на канате.
Разбуриваемый стационарный пакер (рис. 2.6, а) сострит из корпуса 12 с головкой 3, имеющей пазы 6, наружную цилиндрическую поверхность 4 и внутреннюю 2, выполненную в верхней части в виде посадочного ниппеля. На штифтах 8 установлен переводник 1 с уплотнительными манжетами 5 и замком 7, входящим в паз во избежание вращения переводника относительно головки. Переводник соединяет пакер с колонной.
На нижний конец конуса навинчены две концентричные втулки 21 и 23, которые вместе с ниппелем 24 образуют поршневую камеру с перемещающимся поршнем 22 и толкателем. Поршневая полость сообщается с центральным каналом пакера отверстием А. На корпусе 12 смонтирован уплотнитель 15, состоящий из резиновых элементов и шлипсовых узлов 9, 18 и 10.
В шлипсовые узлы входят срезные штифты 14, 20 и 16, конусы 17 и 13, фиксирующие ленты 11, упорные кольца 19. Пакер устанавливается в скважине с
24
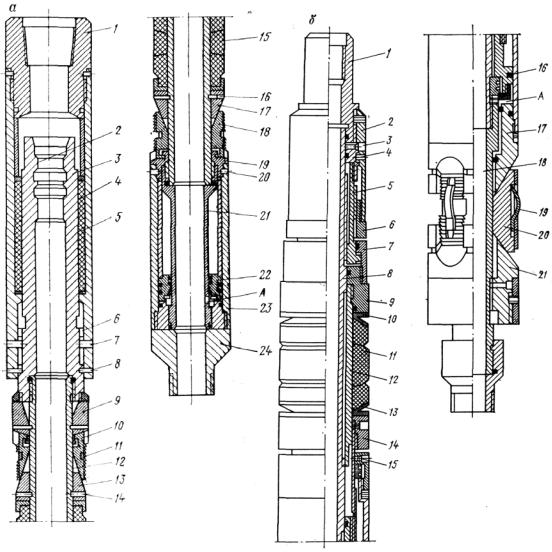
помощью колонны НКТ. После спуска колонна насосно-компрессорных труб закупоривается для возможности установки пакера.
Рис. 2.6. Конструкция пакеров, спускаемых на трубах:
а– неизвлекаемый пакер (разбуриваемый); б – извлекаемый пакер
Вколонну нагнетается жидкость, которая через отверстие А поступает под поршень 22. Под давлением жидкости поршень через толкатель действует на кольцо 19, которое после среза штифтов 20 перемещается вверх, толкая нижние шлипсы 18 на конус 17. Фиксирующие штифты 16, связывающие корпус пакера с нижним 17 и верхним 13 конусами, срезаются. Уплотнители с конусами сдвигаются вверх, нижние шлипсы 18, перемещаясь вверх по конусу 17, разрывают ленту 11 и выдвигаются наружу.
Резиновые уплотнители 15, расширяясь, разобщают и герметизируют верхнюю и нижнюю зоны затрубного пространства пакера. Шлипсы при этом удерживают пакер в стволе скважины.
При подъеме колонны НКТ прикладывается дополнительная растягивающая нагрузка, штифты 6 срезаются, переводник 7 с колонной НКТ извлекаются на поверхность, а пакер остается в скважине.
Демонтируется такой пакер разбуриванием – фрезерованием верхних шлипсов инструментом с ловителем. При спуске инструмента ловитель проходит в корпус, фрезы упираются в верхние шлипсы, и в результате вращения, срезав шлипсы, ловитель
25
удерживает сборку ниже пакера и предохраняет ее от падения на забой во время подъема. Извлекаемый съемный пакер (рис. 2.6, б) устанавливается, как и стационарный, созданием в центральном канале давления жидкости, поступление которой в камеру А разводит толкатель 17 и поршень 16 после среза штифтов 15 в противоположные стороны. Поршень давит на нижнее кольцо 14, которое деформирует манжеты 11, герметизирующие и разобщающие зоны выше и ниже пакера. При опускании толкателя 17 шлипсы 20 с пружиной 19 выдвигаются по корпусу 21 и заякоривают пакер в эксплуатационной колонне скважины.
Освобождение пакера достигается вращением и приподниманием колонны НКТ. При этом срезаются штифты 4, связывающие втулку 2 с переводником 1, а при первых оборотах упор 6 сворачивается с разгрузочной муфты 5, перемещаясь вверх до упора в торец переводника 1. В результате обеспечивается сообщение центрального канала пакера через отверстие 3 во втулке 2 с затрубным пространством. При дальнейшем повороте муфта 5 сворачивается с верхней трубы 8 и перемещает вверх подшипниковый узел 7 и кольцо 9, которое через гильзу 12 увлекает вверх камеру с поршнем 16 и толкателем 17. Уплотнения 11 и шлипсы 20 освобождаются от торцевых упоров 10 и 13. После этого пакер извлекается на поверхность колонной НКТ.
Рассмотренные пакеры изготавливаются двух типов с перекрытым проходным каналом (ПРТ) и с каналом для клапана-отсекателя (ПР-К). Способ посадки пакеров – гидравлический, максимальный перепад давления, воспринимаемый пакерами, – 21 МПа, температура рабочей среды – 100 °С [2, 7, 8].
2.3. Прискважинные сооружения
По мере развития нефтегазодобывающей промышленности в связи с постепенным усложнением и увеличением числа выполняемых на скважине технологических процессов и особенно в связи с разработкой месторождений нефти и газа на заболоченных территориях, на Крайнем Севере, на мелководном и глубоководном морском и океанском шельфе появилась необходимость в сооружении вокруг скважины специальных нивелированных площадок для размещения на них стационарного или передвижного технологического оборудования и для других целей.
Эксплуатационные нефтяные и газовые, а также нагнетательные скважины на суше оснащаются горизонтальной площадкой, размеры которой должны позволять размещать агрегаты и другое оборудование для выполнения различных технологических процессов, необходимых по условиям эксплуатации скважины в различные периоды разработки месторождения. К таким агрегатам, прежде всего, относятся агрегаты подземного ремонта скважин, а также для промывки, кислотной обработки, гидроразрыва пласта, депарафинизации.
Поверхность площадки должна быть строго горизонтальной, ровной и обладать несущей способностью, исключающей возможность ее деформации. Наиболее экономически целесообразно такую площадку сооружать с цементным покрытием, монолитную или блочную, рассчитанную на весь срок службы скважины. Расчеты показывают, что даже при относительно редко проводимых подземных ремонтах расходы на сооружение капитальной с твердым покрытием прискважинной площадки окупаются после нескольких подземных ремонтов скважин.
Площадки эксплуатационных скважин промыслов, расположенных на заболоченных площадях, чаще всего создаются отсыпкой или намывкой грунта с последующей нивелировкой поверхности до отметки выше возможного уровня воды. Площадки соединяются сетью дорог, проложенных по дамбам. Так как подобные месторождения разрабатываются, как правило, кустами наклонно направленных скважин, то каждая площадка сооружается для бурения одного куста и в дальнейшем обустраивается для эксплуатации этих скважин.
26
Иногда на заболоченных территориях площадки и дороги, связывающие их, сооружаются на свайных фундаментах и уложенных на них металлоконструкциях. Подобные же сооружения применяются в широких масштабах для разработки морских шельфовых месторождений.
Наиболее сложных, качественно новых решений потребовала разработка месторождений на глубоководном морском и океанском шельфе. Необходимость создания площадок – оснований для проводки скважины и ее последующей эксплуатации обусловила возникновение многочисленных вариантов базирования средств бурения и эксплуатации скважин, к которым в настоящее время относятся стационарные, плавучие, полупогруженные и подводные основания. Все эти сооружения весьма сложны, металлоемки и дороги. Стоимость их соизмерима со стоимостью скважины, а часто превышает её.
Несмотря на сравнительно многолетнюю практику проектирования и строительства всех видов прискважинных площадок, оснований и транспортных коммуникаций, до сих пор проблема их создания не может считаться решенной с достаточной полнотой, что объясняется исключительной ее сложностью. В частности, нельзя считать решенными задачи обеспечения надежности, безопасности, защиты окружающей среды, приемлемой стоимости и металлоемкости [7].
3. ОБОРУДОВАНИЕ ДЛЯ ЭКСПЛУАТАЦИИ СКВАЖИН ФОНТАННЫМ И ГАЗЛИФТНЫМ СПОСОБАМИ
Подъем по скважине нефти, газа, воды, конденсата или их смеси, а также нагнетание в пласт воды, газа, теплоносителя осуществляется с помощью оборудования, часть которого спущена в скважину, а часть расположена на поверхности, т.е. на устье, например, фонтанная арматура или на прискважинной площадке – манифольд. Это оборудование принято называть оборудованием для эксплуатации нефтяных, газовых, газоконденсатных, нагнетательных скважин или оборудованием для подъема жидкости и газа и соответственно для их нагнетания. Для добычи нефти тремя основными способами – фонтанным, газлифтным и насосным – в настоящее время разработаны и широко применяются соответствующие виды оборудования для эксплуатации скважин: фонтанным способом, бескомпрессорным и компрессорным газлифтом, штанговыми скважинными насосами с механическим или гидравлическим приводом, бесштанговыми насосами – гидропоршневыми, центробежными и винтовыми электронасосами. Кроме того, для эксплуатации скважин, пробуренных на несколько горизонтов, применяется комбинированное оборудование, позволяющее эксплуатировать одной скважиной разными способами отдельно каждый из разрабатываемых горизонтов. Такая эксплуатация скважины часто называется совместно-раздельной.
Оборудование для эксплуатации скважины соответствующим способом имеет свою рациональную область применения. Границы этой области определяют на основе, прежде всего, экономической эффективности данного способа эксплуатации и оборудования для эксплуатации конкретной скважины, с учетом технических возможностей способа эксплуатации и влияния на эффективность глубин скважин, диаметров эксплуатационных колонн, геометрических особенностей ствола скважин, дебитов, состава пластовой жидкости или газа.
Вследствие наличия большого числа факторов, влияющих на эффективность применения того или иного способа эксплуатации и соответствующего оборудования, бывает весьма сложно, а по ряду причин иногда практически невозможно определить четкие границы областей их применения. Поэтому на практике границы этих областей перекрываются. На области применения оборудования для эксплуатации скважин влияют также освоенность производства данного оборудования, климатические
27
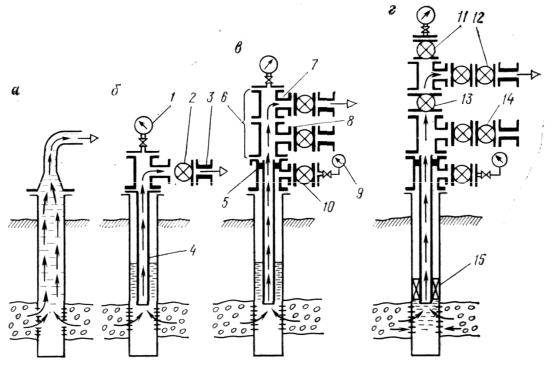
особенности региона, навыки обслуживающего промыслового персонала и уровень его квалификации, общий технический уровень и организация производства в отрасли.
3.1.Схемы оборудования для эксплуатации скважин
Вбольшинстве случаев фонтанный способ эксплуатации позволяет добывать из скважины наибольшее количество нефти при наименьших удельных затратах. Поэтому одной из главных задач при эксплуатации скважин этим способом является обеспечение возможности длительного фонтанирования скважины, что связано с рациональным использованием энергии пласта путем обеспечения высокого КПД работы фонтанного подъемника.
Впрошлом (рис. 3.l, а) фонтанирование осуществлялось по эксплуатационной колонне ствола скважины. При этом КПД фонтанного подъемника был низким, расход пластового газа высоким, что приводило к сокращению фонтанного периода эксплуатации. Процесс фонтанирования был неконтролируемым и неуправляемым. При высоких дебитах и рыхлых песчаных коллекторах происходило быстрое гидроабразивное изнашивание эксплуатационной колонны скважины, приводящее к ее разрушению, а часто и к разрушению всего ствола скважины.
Для предотвращения этого и увеличения КПД подъемника в скважину начали спускать колонну фонтанных труб (см. рис. 3.l, б). Для управления фонтанированием скважины начали применять сменные штуцеры-дроссели, позволяющие изменением размера отверстия регулировать противодавление на пласт и вследствие этого дебит жидкости. Для контроля режима работы скважины стали использовать манометр, устанавливаемый на буфере.
Рис. 3.l. Этапы совершенствования оборудования для эксплуатации скважин фонтанным способом: 1 – манометр буферный; 2 – задвижка; 3 – штуцер-дроссель; 4 – фонтанный подъемник; 5 – трубная головка фонтанной арматуры; 6 – елка фонтанной арматуры; 7, 8 – тройник; 9 – манометр; 10, 11 – задвижка; 12, 14 – задвижки-дублеры;
13 – задвижка стволовая; 15 – пакер
Для замены штуцера или выкидной линии, например из-за износа, возникала необходимость перекрытия скважины запорным устройством, что приводило к ее остановке. Для непрерывности ее работы начали применять фонтанную арматуру
28
(рис. 3.l, в), состоящую из трубной головки и елки, обеспечивающей возможность резервирования выкидных линий – струн.
Для дальнейшего улучшения работы стали использовать полуторарядные или двухрядные подъемники из насосно-компрессорных труб оптимального диаметра, а для сокращения расхода газа затрубное пространство скважины стали герметизировать пакером, устанавливаемым внизу колонны, а также регулировать поток жидкости забойными и регулируемыми штуцерами. Было начато использование задвижекдублеров (рис. 3.l, г).
В результате к настоящему времени оборудование для эксплуатации скважины фонтанным способом резко усложнилось. Оно состоит из четырех основных частей: колонны труб, оборудования низа колонны, оборудования устья, т.е. фонтанной арматуры, и обвязки устьевого оборудования, обычно называемой манифольдом.
Вследствие непрерывного усложнения условий эксплуатации скважин каждый элемент оборудования подвергается дальнейшему совершенствованию, что ведет к усложнению конструкции. Однако это изменение не привело к снижению надежности фонтанного или газлифтного оборудования в целом, а способствовало ее повышению.
Принцип работы газлифтного скважинного подъемника аналогичен работе фонтанного. Однако для функционирования газлифта в подъемник необходимо подавать извне сжатый газ-энергоноситель. Когда газ компримируется, газлифт называется компрессорным. Отсюда и термин – компрессорная эксплуатация.
Существует и так называемый бескомпрессорный газлифт, когда используют газ из высоконапорных газовых пластов и поэтому отпадает необходимость в компрессорной станции. Однако бескомпрессорный газлифт применяют весьма редко. Число скважин, эксплуатируемых этим способом, не превышает 1–2 % от скважин с компрессорным газлифтом.
В настоящее время газлифтным способом эксплуатируется менее 5 % скважин, что объясняется двумя главными причинами: большой стоимостью и сложностью сооружения компрессорных станций с коммуникациями и вспомогательным оснащением и низким КПД способа (при компрессорном газлифте), а следовательно, большой его энергоемкостью.
Общий КПД комплекса «компрессорная станция – скважина» определяется как
η = ηст ηс ηгр ηл ηскв,
где ηст – КПД компрессорной станции; ηc – КПД газовой сети от компрессорной станции до газораспределителя; ηгр – КПД газораспределителя; ηл – КПД линии от газораспределителя до скважины; ηскв — КПД использования сжатого газа на подъем пластовой жидкости. Как видно, величина η не может быть большой.
При компрессорном газлифте комплекс оборудования для эксплуатации группы скважин значительно сложней, чем при фонтанной эксплуатации, и состоит из компрессорной станции, газораспределительной и газосборной сети, систем подготовки газа и газлифтного оборудования скважин.
Компрессорная станция для газлифтной эксплуатации включает машинный зал с компрессорными агрегатами, оснащенный подъемными устройствами для ремонта, монтажа и демонтажа агрегатов и их узлов, водяную насосную для охлаждающей воды градирню, сборник горячей воды и емкости для запаса воды, технологическую аппаратуру с сепараторами, маслоотделителями, регенераторами смазочных масел, распределительные устройства и трансформаторы, системы трубопроводных обвязок, к которым относятся приемные и выкидные коллекторы, газовые, воздушные, водяные магистрали и маслопроводы. Кроме того, в состав станции, как правило, входят ремонтные мастерские, склад запасных частей и помещение для персонала.
29
Для газлифтной эксплуатации чаще всего применяют поршневые компрессоры с газовыми двигателями (газомотокомпрессоры) или с электроприводом, в последние годы – центробежные компрессоры с газотурбинным или электроприводом.
Газомотокомпрессор характеризуется величинами КПД газомотора, не превышающей 35 %, и компрессора – 75 %. Таким образом, ηгк не может быть более 25 %, а так как на КПД отрицательно влияют степень использования мощности, состояние и режим работы агрегатов, температура всасывания и т.п., то обычно
фактический ηгк << 25 %.
Произведение ηсηгрηлηскв < 0,5, поэтому общий КПД комплекса практически не превышает 10 %, что и позволяет относить этот способ эксплуатации нефтяных скважин к самым неэкономичным с точки зрения энергоемкости.
Преимущества этого способа следующие. Межремонтный период работы внутрискважинного оборудования при газлифтной эксплуатации в несколько раз больше, чем при других (кроме фонтанного) способах, что позволяет резко сократить объемы самых тяжелых и трудоемких работ по текущему ремонту скважин. Поэтому в экстремальных условиях, например севера, на заболоченных территориях, при обеспечении высокой надежности работы всего комплекса компрессорный газлифт способствует существенному улучшению условий труда промыслового персонала.
Эффективность газлифтной эксплуатации увеличивается с ростом отборов жидкости по скважине и с увеличением пластовой энергии и газового фактора. И, наоборот, снижается с уменьшением газового фактора, увеличением доли воды и падением пластовой энергии. Поэтому использование газлифтного способа эксплуатации экономически целесообразно, прежде всего, на месторождениях с многодебитными скважинами с большим газовым фактором, высокой пластовой энергией, низкой обводненностью при условии сохранения этих показателей на срок, соизмеримый с периодом разработки месторождения [7].
3.2. Насосно-компрессорные трубы
Для фонтанного и газлифтного подъемников используются так называемые насосно-компрессорные трубы. Название это неточно, подобные трубы широко применяются для подъемников не только при компрессорном, но и при бескомпрессорном газлифте, а также во всех фонтанных, нагнетательных скважинах для выполнения большого числа различных процессов и операций, например при гидроразрыве пласта или его соляно-кислотной обработке, при работах с внутрискважинным оборудованием, при ловильных работах, промывках песчаных пробок, для внутрипромысловых коммуникаций.
Для этого типа труб характерны небольшой диаметр, обеспечивающий возможность их спуска в эксплуатационные колонны скважин; высокая прочность, позволяющая использовать их для подъемников в скважинах больших глубин при всех способах эксплуатации скважин, а также конусная резьба.
Насосно-компрессорные трубы отличаются материалом, группами прочности, герметичностью, противокоррозионной стойкостью, резьбой, быстротой стыковки, размерами, сопротивляемостью отложению парафина и солей (рис. 3.2).
Наибольшее применение к настоящему времени получили стальные цельнокатаные неравнопрочные НКТ с муфтовыми резьбовыми соединениями (рис. 3.3, а). Как видно из расчетной схемы (рис. 3.4), неравнопрочность НКТ определяется разницей между площадями сечений тела трубы и в зоне резьбы, где снижение несущей способности пропорционально уменьшению площади сечения. Параметры резьбовых соединений определяются конусностью, размером резьбы – числом ниток на единицу длины. При этом площадь несущего сечения по резьбе примерно на 25 % меньше площади сечения по телу трубы. Таким образом, грузоподъемность колонны НКТ, собранной из труб этого типа, определяется площадью сечения по резьбе. Отсюда
30