
книги / Оптические методы контроля интегральных микросхем
..pdfТ а б л и ц а 8
Основные критерии отбраковки ИС оптическими методами контроля по стандартам MIL-STD-883 и MIL-STD-883A
|
MIL-STD-883А |
MIL-STD-883 |
||
Критерии |
Метод 2010.2 |
Метод 2010 |
||
|
|
|
|
|
|
Условие А |
Условие В |
Условие А |
Условие В |
1 |
2 |
3 |
4 |
5 |
Дефекты металлизации
Царапины |
и |
пусто |
|
|
|
|
|
ты: |
|
резисто |
|
|
|
|
|
пленочных |
|
|
|
|
|||
ров и затворов МОП- |
0—25 |
25—100 |
25 |
75—100 |
|||
структур, %, не более |
|||||||
других элементов, в |
|
|
|
|
|||
том |
числе |
|
много |
|
|
|
|
слойной металлиза |
|
|
|
|
|||
ции и после |
зонди |
|
|
|
|
||
рования, %, |
не бо |
25—50 |
25—100 |
25—100 |
75— 100 |
||
лее |
|
разводки |
|||||
Смещение |
|
|
|
|
|||
затворов МОП-струк- |
|
|
|
|
|||
тур, |
контактных |
|
|
|
|
||
окон |
(рис. |
4), %, |
0—25 |
0—50 |
50 |
75—100 |
|
не более |
|
между |
|||||
Промежуток |
|
|
|
|
|||
контактным |
|
окном |
|
|
|
|
иметаллизацией,
% |
(мкм), |
не менее |
50 (2,54-6,35) |
- (2,54) |
25 ( - ) |
|
|||
|
Нестравленные |
уча |
|
|
|
|
|||
стки, |
оставляющие |
|
|
|
|
||||
промежуток |
|
между |
|
|
|
|
|||
металлизацией (рис. 5), |
50 (2,54-6,35) |
- ( 2 , 5 4 ) |
25 ( - ) |
0 ( - ) |
|||||
% |
(мкм), |
не |
менее |
||||||
|
|
|
|
|
|
Дефекты диффузии |
|
|
|
|
Ширина |
диффузии I |
Видимая полоса |
изоляции |
|
||||
изоляции |
(рис. |
6) |
I |
|
|
|
|
||
|
|
|
|
|
Дефекты защитной пленки |
|
|
||
Покрытие |
площади |
|
|
|
|
||||
контактной |
площадки, |
25 |
50 |
|
|
||||
Уо, не более |
|
|
раз |
|
|
||||
Максимальный |
|
|
|
|
|||||
мер непокрытой |
части |
|
|
|
|
||||
площади, |
мкм, |
не бо |
127 |
127 |
381 |
—1 |
|||
лее |
|
|
|
|
|
|
|
|
|
|
Продолжение табл. 8 |
||
|
1 |
|
|
|
2 |
3 |
4 |
5 |
|
|
|
|
Дефекты скрайбирования |
|
|
||
Ширина полосы пас |
|
|
|
|
||||
сивации |
вокруг |
эле |
|
|
|
|
||
ментов |
схемы, |
мкм, |
2,54—12,7 |
0—12,7 |
|
0 |
||
не менее |
трещины |
в |
12,7 |
|||||
Длина |
|
|
|
|
||||
сторону |
активной об |
|
|
|
|
|||
ласти схемы, |
мкм, |
не |
|
25,4 |
|
|
||
более |
|
|
|
|
|
|
|
|
Длина любой другой |
|
|
|
|
||||
трещины (рис. 7), мкм, |
76,2 |
127 |
|
|
||||
не более |
|
|
|
|
|
|
||
|
|
|
|
|
Дефекты соединений |
|
|
|
|
|
|
|
|
Любые соединения |
|
|
|
Площадь соединения |
|
|
|
|
||||
на кристалле, %, |
|
|
|
|
||||
не менее |
|
|
|
50—75 |
50 |
50—75 |
50 |
|
на корпусе, %, не |
|
100 |
|
|
||||
менее |
устано |
|
|
|
||||
покрытая |
|
|
|
|
||||
вочным |
материалом |
|
|
|
|
|||
кристалла, %, не более |
25 |
50 |
|
|
||||
Промежуток |
|
между |
|
|
|
|
||
соединением и |
|
сосед |
|
|
|
|
||
ними элементами схе |
|
|
|
|
||||
мы, мкм, |
не менее |
|
2,54—25,4 |
2,54 |
12,7 |
|
Соединения кланом
Длина хвостов про |
|
|
|
|||
волоки, |
мкм |
(число |
|
|
|
|
диаметров проволоки), |
|
|
|
|||
не более |
|
|
- ( 2 ) |
- (2 -4 ) |
||
Длина |
соединения, |
|
|
|
||
выраженная |
числом |
0 сл |
1 |
|
||
диаметров проволоки |
0,5—5 |
|||||
сл |
||||||
Ширина соединения, |
|
|
|
|||
выраженная |
числом |
|
|
|
||
диаметров проволоки |
1 ,2 - 5 |
1,2—5 |
Шариковые соединения
Диаметр соедине |
|
|
|
||
ния, |
выраженный |
чи |
|
|
|
слом |
диаметров |
про |
ГО |
1 |
|
волоки |
|
2—6 |
|||
|
сл |
76,2
(2,5)
1.2—3
1,2—3
2—6
32
Окончание табл. 8
|
1 |
|
|
2 |
3 |
4 |
5 |
Интерметаллическое |
|
|
|
||||
соединение |
|
|
вокруг |
|
|
|
|
„шарика" |
радиально, |
|
|
|
|||
мкм, не более |
|
2,54 |
|
|
|
||
|
|
|
Соединения балочных выводов |
|
|
||
Ширина соединения, |
|
|
|
||||
% |
|
|
|
110—175 |
|
|
|
Длина |
соединения, |
|
|
|
|||
мкм, не менее |
|
25,4 |
|
|
|
||
Царапина |
на |
выво |
|
— |
|
||
де, %, не более |
50 |
|
|
||||
|
|
|
|
Дефекты внутренних выводов |
|
||
Расстояние |
|
между |
|
|
|
||
проволоками и |
сосед |
|
|
|
|||
ними элементами схе |
|
|
|
||||
мы (рис. 8), мкм (чи |
|
|
|
||||
сло диаметров |
прово |
—(2) |
50,8(—) |
|
|||
локи), не менее |
|
- ( 2 ) |
|
||||
Величина |
зарубок, |
|
|
|
|||
бороздок, складок, пе |
|
|
|
||||
режатия, |
утоньшения |
|
|
|
|||
проволоки, |
°/о, |
не |
бо |
25 |
25 |
|
|
лее |
|
|
|
25 |
|
||
Высота |
вертикаль |
|
|
|
|||
ного участка |
в |
месте |
|
|
|
||
выхода проволоки |
нз |
|
|
|
|||
шарикового |
соедине |
|
12,7 |
|
|||
ния, мкм, |
не более |
|
|
||||
Высота дуги |
прово |
|
|
|
|||
локи при виде сверху, |
|
|
|
||||
выраженная |
|
числом |
|
|
|
||
диаметров |
проволоки, |
|
3 |
|
|||
не более |
|
|
|
|
|
|
|
|
|
|
Дефекты установки кристалла |
|
|||
Отсутствие |
устано |
|
|
|
|||
вочного материала |
по |
|
|
|
|||
периметру |
кристалла, |
50 |
|
|
|||
%, не более |
|
25 |
|
|
|||
Непараллельность |
|
|
|
||||
кристалла |
относитель |
|
|
|
|||
но основания |
корпуса |
— |
— |
— |
|||
(рис. 9), |
не более |
10° |
3 —32 |
33 |
зависимости от назначения схем в аппаратуре: для клас са А—условие А, а для классов В и С —условие В. В ТУ на БИС, кроме того, исключается проверка ряда кри териев ОМК. Например, контроль БИС ЗУ на 4 Кбит осуществляется по условию В метода 2010.2 только по
Рис. 6. Дефекты диффузии |
Рис. 7. |
Дефекты |
скрайбирования
Наиболее общему критерии отбраковки —наличию ца рапин и пустот вне зависимости от участка металлиза ции (сквозные царапины или пустоты не должны умень шать ширину металлизации более чем на 50% запроек тированной ширины) [49, 50]. В качестве примера трудности оптического контроля сложных схем на рис. 10 приведено изображение топологии ИС IV сте пени интеграции.
Рис. 8. Дефекты внут |
Рис. 9. Дефекты установки кри |
ренних выводов |
сталла |
Требования к оптическим методам контроля кристал лов и основании микросхем, регламентированные отече ственными стандартами [51], практически мало отли чаются от требований условия В стандарта MIL-STD-883.
Следует отметить, что развитие технологии ИС влияет не только на бракующие дефекты и критерии забракова ния, как это видно из сравнения стандартов MIL-STD-883. Переход к новой технологии, как правило, вызывает и появление новых ОМК. Например, при пе реходе к рентгеновской, проекционной, лазерной и элек тронно-лучевой литографии, когда размеры элементов ИС составляют единицы микрон, возникает необходи мость использовать растровую электронную микро скопию.
При оптическом контроле ИС/ различающихся по внешнему виду, целесообразно оптимизировать парамет ры контрольной операции: время экспозиции, энергию измерения, кратность увеличения. В частности, экспери ментальное исследование БИС со степенью интеграции до 1600 переходов на кристалл свидетельствует о целе сообразности двухступенчатого оптического контроля с фотографированием. Первая ступень — получение образ ного снимка с использованием микроскопа при увеличе нии порядка 20*, целью которого является обнаруже-
3* |
35 |
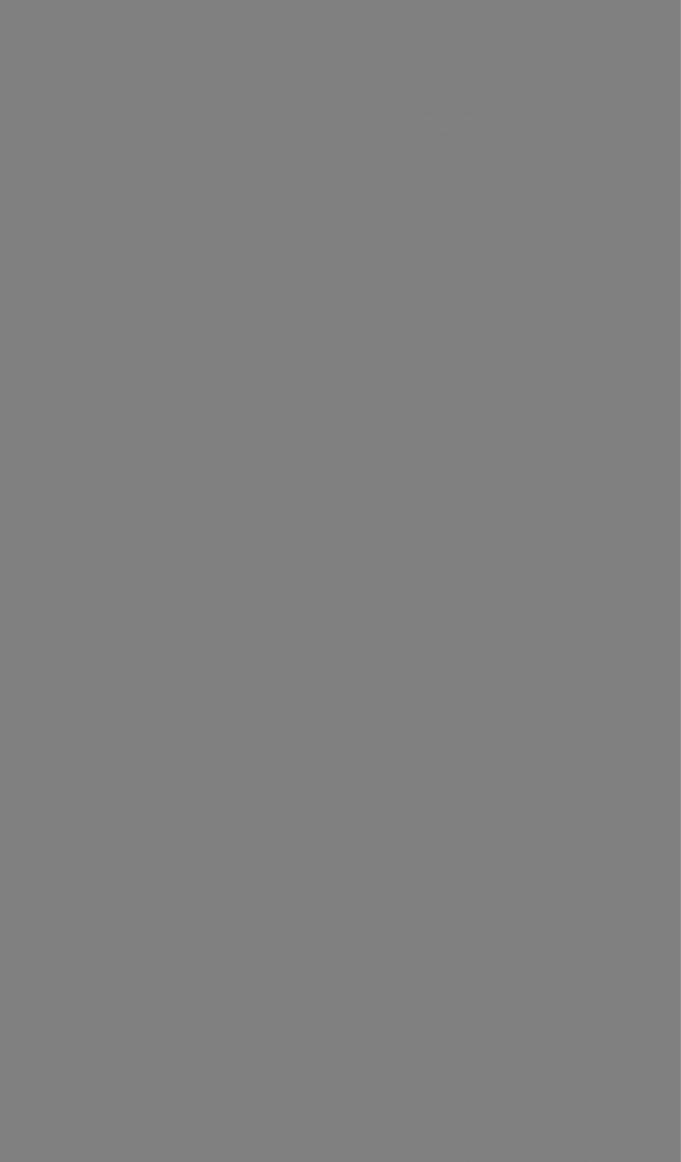
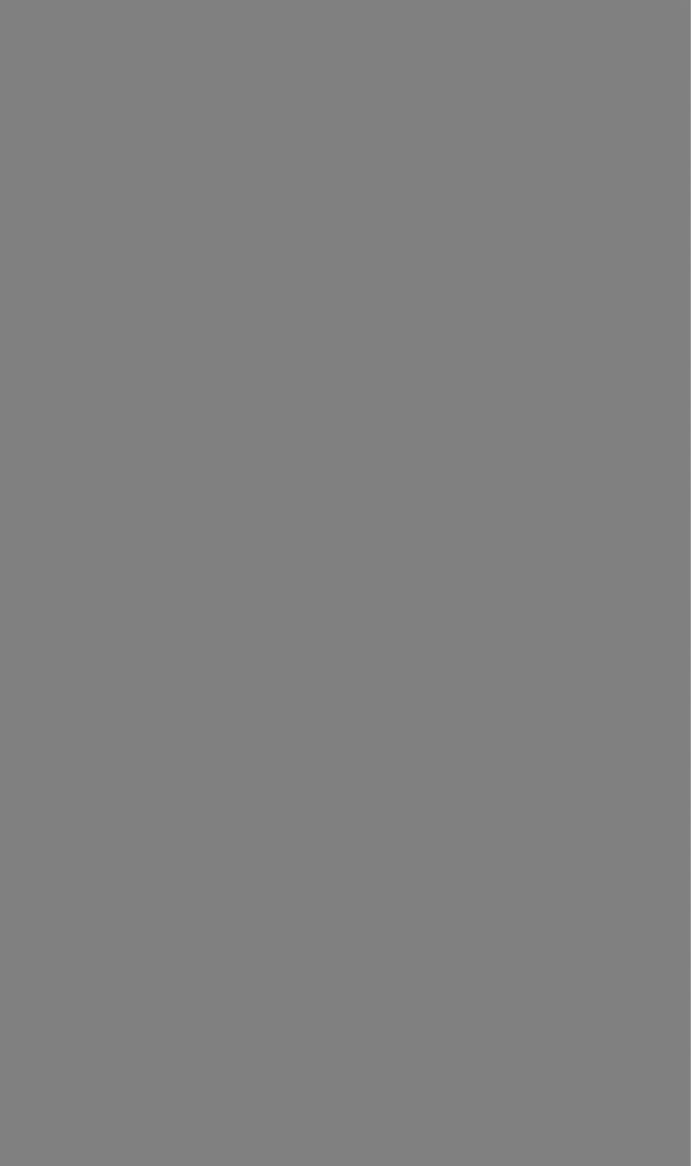
2.4. Пути дальнейшего повышения информативности методов и совершенствования документов по оптическому контролю ИС
Контроль качества металлизации с помощью микро скопа по методу 2010.2 стандарта MIL-STD-883A из-за недостаточного увеличения и глубины резкости не по зволяет выявлять ряд важных аномалий технологическо го процесса и некоторые виды дефектов металлизации и проволочных соединений [11, 52]. Таким образом, нужно, чтобы система НТД как бы «отслеживала» дина мику качества ИС, т. е. она должна сама становиться объектом динамичного управления в общей системе управления качеством ИС.
Дальнейшее повышение информативности ОМК должно основываться на анализе взаимосвязи видов де фектов, внешних воздействий и их последствий с норма1 ми на критерии годности (табл. 9).
Ужесточение норм критериев годности с целью повы шения информативности ОМК вызывает необходимость улучшить метрологические характеристики средств конт роля. Способы определения требований к этим характе ристикам исходя из требований к качеству ИС изложе ны в [53]. Вместе с тем наступает период, когда даль нейшее повышение качества ИС требует перехода к принципиально новым методам контроля. Совершенство вание методов контроля и НТД шло по пути внедрения новых методов, позволяющих выявлять соответствующие дефекты. В первую очередь, следует отметить метод РЭМ. Например, документами НАСА внедрена специ альная методика GSFC-S-311-P-12 отбраковки изделий с дефектами металлизации с помощью РЭМ [48]. Метод РЭМ для контроля металла над ступеньками окисла введен также и в новую редакцию стандарта MIL-STD-883A (метод 2018) для контроля высокона дежных ИС, используемых в авиационной и космической технике [10].
В методе РЭМ используют плотно коллимированный электронный луч (3—30 нм в диаметре), который можно направить на очень малую площадь элемента. Когда электроны ударяются об образец, наблюдается неупругое рассеяние некоторых электронов. Эти так называе мые вторичные электроны собираются коллектором и служат для получения изображений. Изменением напря-
38
|
|
|
|
Т а б л и ц а 9 |
|
Примеры установления норм на критерии годности ИС |
|||||
|
по отдельным видам дефектов |
|
|||
Вид-дефекта |
Внешнее воздействие |
Последствия |
Регламентируемые нормы |
||
воздействия |
критериев годности |
||||
Царапины |
Повышенная |
Разрывы |
Ширина (площадь) |
||
на металли |
или пониженная |
металлиза |
царапины в |
процентах |
|
зации |
температура. Ме |
ции |
к ширине |
(площади) |
|
|
ханические |
на |
|
металлизации |
грузки. Электри ческий ток
Загрязне |
Повышенная |
Наруше |
||
ния |
температура. |
ние ста |
||
|
Влажность. |
|
бильности |
|
|
Агрессивная сре |
работы |
||
|
да. Радиация |
схемы |
||
Дефекты |
Механические |
Обрывы |
||
выводов и |
нагрузки. |
Повы |
или корот |
|
соединений |
шенная |
и |
пони |
кие замы |
|
женная |
темпера |
кания |
|
|
тура. Влажность. |
|
||
|
Агрессивная сре |
|
||
|
да |
|
|
|
Трещины |
Механические |
Деграда |
||
(сколы) кри |
нагрузки. |
Повы |
ция пара |
|
сталла |
шенная |
и !пони |
метров. |
|
|
женная |
темпера |
Разруше |
|
|
тура . Влажность. |
ние кри |
||
|
Агрессивная сре |
сталла |
||
|
да |
|
|
|
Загрязняющая при месь (по массе, объе му, площади) в про центах к основному материалу
Ширина (толщина, глубина, площадь) де фекта в процентах к ширине (толщине, глу бине, площади) выво да или соединения
Размер (длина, ши рина, глубина, пло щадь) трещины в аб солютных или относи тельных (по отноше нию к размеру кри сталла) величинах.
Местоположение (ориентация) трещин
жеиия электронно-лучевая трубка приводится в действие одновременно со сканирующим лучом, а се яркость мо дулируется вторичной электронной эмиссией. Взаимно однозначное соответствие сканирующего луча и растра электронно-лучевой трубки обеспечивает получение изо бражения на РЭМ [52, 54].
РЭМ обеспечивает очень сильное увеличение (от 1000 и свыше 50 000х) с большой глубиной резкости, что дает возможность рассматривать дефекты металлизации на ступени ркисла, обеспечивает видеозапись наихудших
39
случаев нарушения целостности покрытия и поэтому ши роко применяется для проверки качества металлизации и толщины покрытия.
Широкое применение РЭМ при анализе отказов на испытаниях позволило оперативно устранять их причи ны. В этом случае, как правило, используется эмиссион ный режим работы РЭМ. Этот же режим используется для отбраковки кристаллов с дефектами металлизации
и проволочных соединений [55]. |
работы |
схемы |
РЭМ используется также для контроля |
||
с помощью потенциального контраста. |
К схеме |
при |
кладывается рабочее напряжение, а изображение уве личивают с целью сканирования отдельного участка схе мы или схемы целиком. Количество вторичных электро нов несет определенную информацию о проходящих процессах, плотности материала и о напряжении сме щения. Потенциальный контраст в исходных материалах будет пропорционален приложенному напряжению. Мед ленный порядок следования сигналов входного напря жения позволяет проследить работу схемы [52, 54].
Проверка сложных логических микросхем — более трудоемкий процесс. Здесь может понадобиться приме нение быстродействующего телевизионного сканирова ния. Сканирующий растр обеспечивает получение 60 изображений в секунду, которые можно записать на видеоленту. Медленное воспроизведение ленты или остановка кадра дают возможность проследить за ходом логических операций.
К недостаткам РЭМ следует отнести необходимость предварительного удаления глассивации (стеклянного покрытия), что иногда вызывает искажение полученных данных. Сканирование должно производиться в вакууме. При анализе отказов с помощью РЭМ электронные лу чи могут дать искаженную картину, поскольку электро ны могут накапливаться па поверхности и разрушать ее или образовывать инверсные слои. Особенно чувстви тельны к этому полевые МОП и планарные р — п —р-тракзисторы. Недостатком РЭМ является так же трудность объективной оценки толщины покрытия, его высокая стоимость и необходимость больших затрат времени, что требует рационального отбора контрольных точек, технических характеристик, планов и других эле ментов методики контроля, которые могут меняться в зависимости от уровня дефектности продукции.
40