
книги / Руководство по ревизии, наладке и испытанию шахтных подъёмных установок
..pdf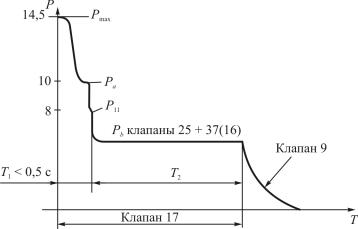
Диаграмма изменения давления при предохранительном торможении с постоянным тормозным моментом показана на рис. 7.54.
Рис. 7.54. Диаграмма изменения давления при предохранительном торможении с постоянным тормозным моментом
7.16.4. Ревизия и наладка тормозной системы
При ревизии и наладке тормозной системы необходимо проверить следующее:
–тормозные диски;
–постаменты тормоза и трубопроводы;
–плату управления ВСС-1;
–маслостанцию;
–тормозные модули;
–произвести проверку и наладку тормозов с помощью системы «Чело- век–Машина».
Тормозные диски
Визуально проверить состояние тормозных дисков и их крепление к барабану. Проверить чистоту поверхности тормозных дисков. При необходимости произвести шлифовку мелких повреждений, протирку и обезжиривание. Измерить торцовое биение и осевую игру тормозных дисков. Торцовое биение должно быть не более 0,5 мм, осевая игра – не более 1,0 мм.Произвести регулировку датчикадеформации тормозного диска. Расстояниемежду поверхностью дискаи датчикомбезучетадопуска биениядолжно бытьоколо1,0 мм.
Постаменты тормоза и трубопроводы
Визуально проверить состояние всех крепежных деталей и при необходимости произвести их затяжку.
Проверить отсутствие повреждений трубопроводов, утечек масла в соединениях трубопроводов и гидроаппаратуры.
201
Проверить положение постаментов со смонтированными тормозными блоками относительно диска. Измерить расстояние между лицевой поверхностью опоры, с которой соприкасается корпус, и тормозным диском (с обеих сторон). Разница не должна превышать 1 мм. Для всех постаментов радиальный зазор между постаментом и тормозным диском должен быть ~5 мм, но не более 1 % от диаметра барабана.
Плата управления ВСС-1
В ходе ревизии и наладки должна быть выполнена комплексная настройка платы (плат) управления ВСС-1 при помощи имеющихся на ней переменных резисторов. Перечень и последовательность выполнения настроек платы тормоза приведены в эксплуатационной документации. При наладке платы тормоза должны быть предприняты меры по снятию статического заряда.
Маслостанция
Произвести визуальный осмотр состояния аппаратуры и гидравлических соединений на отсутствие повреждений и утечек. Выяснить причины и устранить утечки. Проверить надежность крепления съемных крышек, воздушных фильтров, отдушин.
Произвести замену масла. Если система заполняется маслом после монтажа маслостанции, необходимо тщательно промыть бак, клапаны, трубопроводы
ипрочие компоненты гидросистемы. Необходимо использовать гидравлические минеральные масла с индексом вязкости в пределах 46, согласно перечню «Жидкости, рекомендуемые поставщиком для гидроприводного оборудования». Масло заливать до верхней отметки индикатора уровня, используя фильтр со степеньюочистки10 мкм. Требуетсяприблизительно200 литровмасла.
Проконтролировать температуру масла по индикатору на передней панели. Перед пуском насоса необходимо выждать, пока нагреватель нагреет масло минимум до 20 °С.
Убедиться, что все соединения выполнены правильно и что все вентили во всасывающих линиях всех насосов открыты. Доступ к вентилям рабочего
ирезервного насосов возможен через задний съемный люк.
Произвести пуск насоса. Насос должен вращаться в направлении указанном стрелкой на корпусе насосного узла. Важно, чтобы при работе насосов масло поступало в насосы без перерыва.
После монтажа тормозных блоков и выполнения разводки трубопроводов проверить систему под давлением 15 МПа в течение 15 минут. При необходимости долить масло.
Замена масляного фильтра 5 (см. рис. 7.49) производится в ходе ежегодной ревизии и наладки одновременно с заменой масла. После монтажа тормозной системы при производстве наладочных работ может потребоваться досрочная замена фильтра. Фильтр оснащен датчиком загрязнения. Предупреждение о необходимости замены фильтра отображается системой ЧМ.
202
Произвести проверку давления сжатого азота в аккумуляторе 12, падение давления ниже 8,5 МПа указывает на необходимость его дозарядки. Аккумулятор должен быть дозаряжен азотом до номинального значения давления 10 МПа по манометру 14В с помощью имеющегося в комплекте зарядного устройства.
Проверку реле уровня 36 произвести при выполнении замены масла. Проконтролировать появление предупредительного, а затем аварийного сигналов уровня в системе ЧМ при сливе масла. При заливке нового масла, сигналы должны исчезнуть в обратном порядке. Проверить работоспособность датчика температуры путем сравнения температуры масла отображаемой системой ЧМ и термометром 98 на маслостанции.
Произвести проверку настройки реле давления 34. Замыкание контакта на выходе 1 должно происходить при повышении давления до 12,5 МПа, а размыкание при снижении до 8,5 МПа. Давление контролировать по манометру 14А при поданном напряжении на клапаны 37, 16, 132, 32, регулировку давления в системе производить клапаном на насосе 6А (6В).
Произвести проверку настройки реле давления 35. Замыкание контакта на выходе 1 должно происходить при снижении давления до 1,5 МПа, а размыкание при повышении до 1,7 МПа. Давление контролировать по манометру 14А, регулировку давления в системе производить с помощью клапана 18. Для корректировки настроек реле 34, 35 пользоваться инструкцией по эксплуатации реле давления.
Проверить работоспособность датчика давления 76 путем сравнения показаний давленияотображаемыхсистемой ЧМс показаниемманометра14А.
Работоспособность клапанов тормозной системы может быть проверена при растормаживании-затормаживании подъемной машины. Предупреждения и ошибки в работе тормозной системы будут отображаться на дисплее пульта управления машиниста.
Величина давления Рb, используемая при настройке, приводится в расчете, выполняемом фирмой-изготовителем или проектной организацией. В случае замены клапанов маслостанции или изменения нагрузок на подъемную машину необходимо выполнить перерасчет Рb и произвести перенастройку клапанов. Также настройку клапанов надо выполнить при вводе подъемной машины в эксплуатацию после монтажа.
Настройку клапанов тормозной системы удобно выполнять с помощью имитатора, позволяющего подавать питание =24 В непосредственно на каждый из клапанов и регулируемое напряжение 0–24 В на клапан 37. Для подключения имитатора в соединительной коробке маслостанции предусмотрены клеммы источника = 24 В. Методика настройки маслостанции подробно описана в эксплуатационной документации.
203
Тормозные модули BSFG 408
Произвести визуальную проверку на отсутствие утечек масла через дренажные отверстия тормозных блоков, причиной которых может быть повреждение уплотнений. Неисправный гидравлический узел тормозного блока должен быть демонтирован, произведены ревизия блока, замена уплотнений и смазка. Гидравлический узел можно снять, как единый блок, масса – около 23 кг. Узел в сборе необходимо хранить в резерве для возможной замены.
После монтажа или после того, как гидросистема разбиралась, ее необходимо заполнить маслом, для чего несколько раз подать и слить масло при максимальном давлении.
В ходе выполнении ревизии и наладки тормозных модулей должны быть выполнены следующие работы:
–регулировка воздушного зазора;
–замена фрикционных накладок (при необходимости);
–проверка состояния пакетов пружин тормозных блоков.
Регулировка воздушного зазора. Воздушный зазор должен быть отрегулирован в случае износа фрикционных накладок, а также после их замены.
Величина воздушного зазора должна быть 1,5–2,0 мм. Максимально допустимая величина воздушного зазора при износе фрикционных накладок 3,0 мм. Разница воздушного зазора с двух сторон тормозного блока не должна превышать 0,5 мм
Величины зазоров, измеренные щупом, должны совпадать с величинами, измеренными датчиками воздушного зазора и отображаемыми системой ЧМ, с точностью ±0,1 мм. При необходимости должно быть отрегулировано положение датчиков воздушного зазора относительно тормозных блоков. Для этого необходимо предварительно отпустить винт на стопорном кольце датчика.
Замена фрикционных накладок. При износе фрикционных накладок до такого состояния, при котором зазор между тормозным диском и тормозными колодками составляет менее 5 мм, фрикционные накладки необходимо заменить. После замены необходимо отрегулировать воздушный зазор.
Проверка состояния пакетов пружин тормозных блоков. Перед вво-
дом тормозной системы в эксплуатацию необходимо проверить работу тормозов и усилие пружин следующим образом:
–проверить, что воздушный зазор между фрикционными накладками и тормозным диском выставлен правильно с обеих сторон;
–растормозить машину, и поместить лист бумаги между фрикционной накладкой и тормозным диском. Затормозить подъемную машину рабочим тормозом, и, медленно поднимая давление масла, определить по манометру давление, при котором лист бумаги начинает освобождаться. Это давление должно быть не менее 9 МПа, а допустимая разница давления для всех тор-
204
мозных блоков не должна превышать 10 % от максимального значения. Если допуск не выполняется, необходимо заменить оба пакета пружин в тормозном блоке.
При выставленном правильно воздушном зазоре и исправных пакетах пружин сообщения об ошибках тормозных модулей в системе ЧМ должны отсутствовать.
Проверкаиналадка тормозов спомощью системы «Человек–Машина»
Наличие непрерывного контроля состояния тормозной системы исключает необходимость периодических проверок техническим персоналом состояния следующего оборудования системы тормозов:
–износ фрикционных накладок и состояние пакетов пружин в тормозных модулях;
–работоспособность клапанов, количество и состояние масла в тормозной системе;
–сопротивление изоляции и степень зарядки аккумуляторов в системе электропитания.
Возникающие неисправности тормозной системы будут приводить к появлению на дисплее системы ЧМ мигающих светодиодов предупреждений или аварийных отключений подъемной машины. По информации на дисплее обслуживающим персоналом может быть установлена причина возникновения неисправности и затем предприняты меры по ее устранению.
По загоранию соответствующего светодиода (нижний ряд) обслуживающий персонал может определить узел тормозной системы, в котором возникла неисправность. Конкретная причина возникновения неисправности может быть определена с помощью предупреждающих символов (закрашенный желтый квадрат) или сигналов аварийного отключения (закрашенный красный квадрат), появляющихся возле контролируемого параметра на соответствующих «экранах» дисплея. Переход на необходимый «экран» производится нажатием на кнопку, расположенную ниже загоревшегося светодиода.
Нажатием на кнопку «Список тревог» может быть вызван подробный список возникших предупреждений и аварий. Текстовое сообщение «Информация о первом отказе» отображается в нижней части каждого из «экранов».
Подробная информация о пользовании системой «Человек–Машина» приводится в Руководстве по эксплуатации электрооборудования подъемной машины.
Система «Человек–Машина» позволяет автоматизировать в ходе выполнения ревизии и наладки следующие проверки тормозной системы:
–проверка пакетов пружин тормозных блоков;
–измерение воздушных зазоров;
–проверка защиты минимального замедления (>1,5 м/с2) предохранительного торможения в плате ВСС;
205
– определение величины тормозного момента каждого из тормозных блоков и тормозной системы в целом.
Режим выполнения проверок задается переключателем на пульте управления подъемной машиной. Измерения производятся при движении подъемных сосудов на скорости дотягивания, необходимые изменения давления в тормозной системе выполняются автоматически. Принцип измерения момента основан на измерении вращающего момента привода, который преодолевает тормозной момент, создаваемый заторможенными одним или несколькими тормозными блоками.
Результаты проверок отображаются на соответствующих экранах дисплея пульта управления.
Тормозной момент каждого блока должен превышать минимально допустимое значение, и общая их сумма должна превышать величину трехкратного статического момента.
Комплексная проверка тормозной системы с помощью системы ЧМ должна быть выполнена также перед перестановкой барабанов на двухбарабанной подъемной машине. Положительный результат проверки разрешает выполнение перестановок в течение времени, установленного в программе контроллера.
7.17. Аппаратура для проведения наладки и испытаний тормозных устройств шахтных подъёмных установок
7.17.1.Общие сведения
Всоответствии с требованиями правил безопасности [6, 25, 26] ответственными лицами за состояние подъемной установки должна периодически проверяться исправность работы предохранительного тормоза, защитных устройств и остальных элементов подъемной установки.
Развитие электронных технических систем и датчиков позволяет выйти на новый уровень проведения проверочных работ, характеризующийся высокой степенью точности измерений и скорости проверки, что положительно сказывается на безопасности эксплуатации шахтной подъемной установки.
Внастоящее время в практике работы многих наладочных организаций, осуществляющих ревизию и наладку шахтных подъемных установок, применяются измерительные системы, предназначенные для контроля, диагностики
иналадки тормозных систем, снятия диаграмм движения подъемных сосудов
ианализа состояния систем управления приводом шахтных подъемных установок.
206
7.17.2. Требования, предъявляемые к аппаратуре для проведения наладки и испытаний тормозных устройств
К аппаратуре для проведения ревизии, наладки и испытания шахтных подъёмных установок предъявляют следующие требования:
1.Аппаратуру необходимо сертифицировать, как средство измерения в соответствии с требованиями ст. 1 п. 3.6 Федерального закона РФ от 26.06.2008 №102-ФЗ «Об обеспечении единства измерений» при осуществлении производственного контроля за соблюдением установленных законодательством Российской Федерации требований промышленной безопасности к эксплуатации опасного производственного объекта.
2.Обеспечивать контроль, измерение, визуализацию и документирование основных параметров работы систем управления шахтных подъёмных установок, тормозной системы, электроприводовпостоянного ипеременноготока.
3.Проходить периодические испытания и поверку не реже одного раза в год, с целью обнаружения дефектов и определения погрешностей измерений. Результаты периодических испытаний оформляются актом, утвержденным руководителем предприятия-изготовителя. К акту должны быть приложены протоколыпроведенных испытаний.
4.Обеспечивать регистрацию и обработку данных о работе тормозной системы, визуализацию и документирование:
–момента разрыва цепи ТП;
–момента касания фрикционными накладками тормозного обода;
–скорости и пути торможения подъемной машины;
–скорости и пути торможения подъемных канатов (для машин со шкивами трения);
–давления в цилиндрах рабочего торможения (ЦРТ);
–давления в цилиндрах предохранительного торможения (ЦПТ);
–деформации (усилия) тормозных тяг;
–тока подъемного двигателя.
5.Обеспечивать воспроизведение графиков изменения контролируемых параметров для нескольких замеров, автоматическое создание отчёта о проведённых измерениях.
7.17.3. Системы измерительные «Силькан»
Для проведения наладки и испытаний тормозных устройств могут быть использованы системы измерительные «Силькан», которые выполняют оперативное измерение, визуализацию и документирование параметров работы тормозной системы и электропривода шахтной подъемной установки. Подробная и наглядная информация о работе тормозной системы и электропривода позволяет:
– повысить качество и сократить время проведения ревизии и наладки;
207
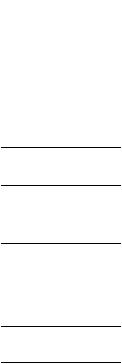
– оперативно определять причины отклонений в работе оборудования подъёмной установки.
В состав аппаратуры «Силькан» входят портативный компьютер, программное обеспечение «Силькан», блок коммутации и комплект датчиков, включающий: датчики деформации тормозных тяг, блок усилителей датчиков деформации, датчик пути (скорости), датчик давления 0–1 МПа, датчики тока (токовые клещи). Частота опроса датчиков определяется пользователем и может быть задана в диапазоне от 1 Гц до 1000 Гц.
Основные технические характеристики аппаратуры «Силькан» приведены в табл. 7.9.
Таблица 7 . 9 Основные технические характеристики аппартруры «Силькан»
Наименование изме- |
|
|
рительного канала |
Диапазон измерений |
|
(ИК) |
|
|
|
|
|
ИК силы постоянного |
±5 А |
|
тока |
±300 А |
|
|
±500 А |
|
|
±1000 А |
|
|
±4 А |
|
|
±30 А |
|
ИК силы переменно- |
(0…0,4) А |
|
го тока |
(0…4) А |
|
|
(0…30) А |
|
|
(0…200) А |
|
|
(0…1000) А |
|
ИК напряжения по- |
±250 В |
|
стоянного тока |
±1000 В |
|
|
|
|
|
±30 В |
|
ИК давления |
(0…1) МПа |
|
(0…16) МПа |
||
|
||
ИК линейного пере- |
(0,5…2000) м |
|
мещения |
||
|
||
|
|
|
ИК деформации |
(-3000 …+3000) мкм/м |
|
|
|
|
Пределы ос- |
|
Тип первичного |
новной по- |
|
преобразователя |
грешности ИК, |
|
|
% |
|
шунт 75ШСМ |
±1,5 |
|
токовые клещи |
|
|
±3,0 |
||
PROVA 15 |
||
|
||
токовые клещи |
|
|
PROVA 15 |
±3,5 |
|
|
||
токовые клещи |
|
|
АТА-2502 |
|
|
ДН-1000/250-5 |
±2,0 |
|
|
|
|
- |
±1,0 |
|
датчик давления |
±2,5 |
|
«Карат-Ди» |
||
|
||
датчик пути на базе |
|
|
±1,0 относ |
||
шифратора угла |
||
поворота |
|
|
Датчик деформации |
Не норм. |
|
ДД-1 |
|
Пример обработки результатов испытания тормозной системы шахтной подъёмной машины при подъеме груза приведены на рис. 7.55.
208
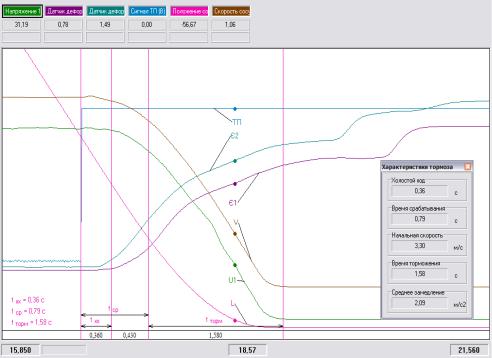
Рис. 7.55. Регистрация и расчет параметров работы тормозной системы
На рисунке представлены следующие графики:
–сигнал ТП - определяет момент подачи сигнала на предохранительное торможение;
–линейное перемещение (L) - позволяет определить момент остановки подъемной машины и тормозной путь;
–скорость (V) - значение скорости, вычисленное по данным с датчика перемещения;
–деформации тяг (Є1, Є2) - характеризуют изменение тормозного уси-
лия.
Для определения продолжительности протекания процессов на графиках устанавливаются специальные метки в виде вертикальных линий, отмечающие моменты начала торможения, соприкосновения колодок тормоза с тормозным ободом, срабатывания тормоза и стопорения подъёмной машины. Метки позволяют рассчитать продолжительность холостого хода, время срабатывания тормоза и торможения машины. Установка меток осуществляется специалистами с учетом особенностей работы тормоза, изменения скорости и другой информации.
209
Испытания тормозной системы проводят в два этапа: при неподвижном барабане подъемной машины определяют время холостого хода и время срабатывания; при движении подъемной машины с максимальной скоростью определяют все регламентируемые параметры тормозной системы.
По графикам изменения давления на выходе регулятора или в полостях цилиндров рабочего и предохранительного торможения, графикам деформации тяг определяют состояние и исправность работы каждого (левого и правого) тормоза подъемной машины. По характеру изменения давления оценивается работа первой ступени торможения, выявляется «зависание» поршня в цилиндре и определяются другие неисправности.
По характеру нарастания тормозного усилия в тяге исполнительного органа, моментам касания колодками тормозного обода определяется износ и состояние рычажно-шарнирного механизма исполнительного органа тормоза.
После устранения неполадок и проведения наладки тормозной системы проводят повторные испытания.
7.18. Испытание тормозных устройств
7.18.1. Общие положения
При ежегодных ревизиях и наладках подъемной установки, а также после ремонта или замены элементов тормозного устройства (тормозные колодки, тяги, шарниры, цилиндры и др.) и переналадки подъемной установки, связанной с изменением концевой нагрузки, необходимо проводить испытание тормозной системы.
Целью этих испытаний являются определение параметров работы предохранительного тормоза и проверка их соответствия требованиям ПБ.
При этом должны определяться и оцениваться:
–время срабатывания предохранительного тормоза;
–величины среднего замедления при предохранительном торможении при подъеме и спуске расчетного груза для данной установки;
–величина пути торможения машины с момента разрыва цепи защиты до ее полной остановки как при движении машины с максимальной скоро-
стью (Sтм), так и при движении со скоростью подхода подъемных сосудов, контролируемой ограничителем скорости (Sтп), и сравнение Sтм с величиной пути, контролируемого ограничителем скорости, а Sтп с допустимой высотой переподъема;
–отсутствие проскальзывания каната по канатоведущему шкиву (для подъемных машин со шкивами трения);
–отсутствие набегания подъемных сосудов на канат (для наклонных подъемных установок).
При испытаниях должны соблюдаться следующие условия:
1.Испытания тормозной системы разрешается проводить, если в помещении подъемной машины поддерживается температура не ниже +5°С, так
210