
книги / Руководство по ревизии, наладке и испытанию шахтных подъёмных установок
..pdf– для кинематической схемы (см. рис. 7.2, б)
M т.р gmp ZHб ifзRт 10 3 ,
– для кинематической схемы (см. рис. 7.2, в)
|
aqcfзR рd 2 P |
|
3 |
|
|
M т.р |
m |
p |
10 |
, |
|
2 a b ed |
|
– для кинематической схемы (см. рис. 7.2, г)
|
acfзR рd 2 P |
|
3 |
|
M т.р |
т p |
10 |
, |
|
a b d |
|
(7.120)
(7.121)
(7.122)
где Р – фактическое максимальное давление в ЦРТ при рабочем торможении при минимальном давлении в воздушной сети, МПа.
11.Определить фактический коэффициент статической надежности предохранительного тормоза К по формуле (7.1) и сравнить с допустимым. Для машин и лебедок с грузовым приводом тормоза определить фактический коэффициент статической надежности рабочего тормоза Кp по формуле (7.4).
12.Определить коэффициент статической надежности тормоза при перестановке барабанов K' по формуле (7.2) и сравнить с допустимым. При разной массе тормозного груза на приводах, разной затяжке пружинных блоков, разномассовых подъемных сосудах определить наименьший коэффициент статической надежности.
13.Для машин, имеющих раздельные источники усилия рабочего и предохранительного торможения, определить коэффициент статической надежности рабочего тормоза Кp при перестановке барабанов по формулам:
– для всех кинематических схем
Kp |
M т.p |
1,2. |
(7.123) |
|
|||
|
Mcт |
|
14.Определить коэффициент статической надежности тормоза K'' при обрыве порожнего каната или противовеса по формуле (7.3).
15.Определить тормозной момент М1 первой ступени предохранительного торможения по фактической затяжке пружинных блоков или давлению воздуха в ЦРТ по формулам:
–для кинематической схемы (см. рис. 7.2, б)
|
|
3 |
(7.124) |
|
|||
M1 2gmp Z Hл Hп ifзRт 10 , |
– для кинематической схемы (см. рис. 7.2, в)
|
п |
aqcfзрd 2 R P |
|
|
|
M1 |
т.п |
p т 1 |
103 , |
(7.125) |
|
2 a b ed |
|||||
|
|
|
|||
|
|
|
|
91 |
– для кинематической схемы (см. рис. 7.2, г)
|
п |
acfзрd 2 R P |
|
|
M1 |
т.п |
p т 1 |
103 , |
(7.126) |
|
a b d |
|||
|
|
|
|
где P1 – фактическая величина давления воздуха в ЦРТ первой ступени тор-
можения, МПа, птп – количество тормозных приводов.
16. Определить максимальный тормозной момент, создаваемый рабочим тормозом, для кинематических схем (см. рис. 7.2, в, г) по формуле
M т.p пт.пM т.p . |
(7.127) |
17. Определить необходимое давление воздуха или масла в цилиндрах предохранительного торможения по большей массе тормозного груза на одном приводе по формулам
– для кинематических схем (рис. 7.2, б, в, г)
P |
4g nmт.г mп |
|
, |
(7.128) |
|
|
|||
п |
106 р dп2 dш2 з |
п |
|
где d п – диаметр поршня цилиндра предохранительного торможения (ЦПТ), м; dш – диаметр штока ЦПТ, м; ηп – коэффициент полезного действия цилин-
дра, ηп = 0,9.
18. Определить необходимое давление воздуха или масла в ЦРТ для полного оттормаживания машины Ро по большей затяжке одного из пружинных блоков Нб, а для машин НКМЗ – для поднятия тормозных грузов по большей массе груза на одном приводе по формулам:
– для кинематических схем (см. рис. 7.2, а, б, д, е)
|
4 |
|
|
|
|
P |
gmр Z (Hб hп.р.ц) |
, |
(7.129) |
||
|
|
|
|||
0 |
|
|
106 рdp2зp.ц |
|
|
|
|
|
|
|
– для кинематических схем (см. рис. 7.2, в, г)
P0 |
|
4gmт (a b) |
, |
(7.130) |
||
106 |
рdp2bзp.ц |
|||||
|
|
|
|
где hn.р.ц – ход поршня ЦРТ, ηр.ц – коэффициент полезного действия ЦРТ, принимается равным 0,9 для машин с пружинными приводами тормоза и 0,7 – для машин с грузопневматическим приводом.
7.5. Исполнительный орган тормоза
Исполнительный орган тормоза колодочного типа состоит из тормозных балок, тормозных колодок с фрикционными накладками, тормозного обода и рычажно-шарнирного механизма.
92
7.5.1. Тормозные балки с тормозными колодками
Тормозные балки – основная несущая конструкция исполнительного органа тормоза, на которой закреплены тормозные колодки с фрикционными накладками.
На подъемных машинах и лебедках применяются кинематические схемы исполнительного органа тормоза с тормозными балками на неподвижных опорах и с подвешенными тормозными балками, с жестким и шарнирным креплением тормозных колодок к тормозным балкам (см. рис. 7.2).
Тормозные колодки с фрикционными накладками на практике и в технической литературе обозначаются одним выражением «тормозные колодки». Поэтому в дальнейшем под выражением «зазор между тормозными колодками и тормозным ободом» следует понимать «зазор между фрикционными накладками и тормозным ободом».
При ревизии и наладке исполнительного органа тормоза необходимо проверить следующее:
1.Правильность монтажа элементов исполнительного органа тормоза. При правильно смонтированном исполнительном органе тормоза все его элементы при работе должны двигаться в плоскости, перпендикулярной к оси органа навивки. Перемещение элементов исполнительного органа тормоза вдоль оси органа навивки может появиться вследствие:
–неправильного монтажа тормозных балок или тормозного привода;
–чрезмерных зазоров в опорных шарнирах тормозных балок;
–неодинакового суммарного зазора между тормозными колодками и ободом левого и правого исполнительного органа тормоза при одном тормозном приводе.
2.Состояние шарнирных опор и фундамента под тормозными балками. Наличие трещин в фундаменте или перемещение шарнирных опор относительно фундамента не допускается. Анкерные болты должны быть туго затянуты. Нарушения фундамента и крепления шарнирных опор к фундаменту должны быть немедленно устранены.
3.Состояние тормозных балок и тормозных колодок (фрикционных накладок). Проверяются отсутствие трещин, надежность крепления тормозных колодок и фрикционных накладок. Деревянные колодки должны быть изготовлены из вербы, ивы, тополя или липы. Применение других пород дерева запрещается. Применяемое для тормозных колодок дерево должно быть сухим, однородным, без сучков со стороны рабочей поверхности и чрезмерных трещин. Допускаются лишь небольшие трещины, присущие любому просушенному дереву. На прессмассовых тормозных колодках (далее по тексту «фрикционные накладки») допускаются только небольшие сколы по углам накладок. Треснувшие фрикционные накладки должны быть заменены запас-
93
ными из комплекта, поставляемого заводом-изготовителем вместе с подъемной машиной.
4.Плотность прилегания фрикционных накладок к тормозному ободу при заторможенной машине. При монтаже подъемной машины промаркированные прессмассовые накладки устанавливаются по заводской схеме размещения накладок. Новые фрикционные накладки должны быть подогнаны
ктормозному ободу. После обкатки машины без нагрузки в течение двухтрех смен выборочно снимаются несколько фрикционных накладок для оценки размеров поверхности контакта. Площадь контакта должна составлять не менее 50 %. Для монтируемых машин, если по технологии монтажа предусматривается проточка тормозного обода, для ускорения подгонки допускается сделать насечку зубилом на тормозном ободе.
5.Величину запаса фрикционных накладок на износ. Фрикционные накладки должны быть заменены, если толщина между рабочей поверхностью накладки и наиболее выступающей частью крепящей конструкции составляет для деревянных накладок менее 10 мм, для прессмассовых – менее 5 мм. Каждая фрикционная накладка должна крепиться конструкцией, предусмотренной заводом-изготовителем.
7.5.2. Тормозной обод
При ревизии тормозного обода необходимо проверить следующее:
1.Состояние тормозного обода и надежность соединения его с органом навивки. При износе тормозного обода, превышающем 30 % первоначальной толщины, или при наличии трещин в сварных швах или на тормозном поле должен быть проведен ремонт тормозного обода по технологии, согласованной с заводом изготовителем. Рабочая поверхность тормозного обода должна быть ровной, чистой и гладкой. При наличии гребешков, царапин, борозд или вмятин обод следует проточить и прошлифовать. Недопустимо попадание масла или воды на рабочую поверхность тормозных ободьев.
2.Величину биения тормозного обода. Величину биения измерить индикатором, установленным на жестком основании в двух-трех сечениях по ширине обода. Индикатор можно устанавливать на деталях исполнительного органа тормоза, если есть полная уверенность в неподвижности этих деталей во время измерения. Скорость тормозного обода должна быть 0,2–0,3 м/с. При этом необходимо, чтобы тормоз в работе не участвовал, а требуемая скорость обеспечивалась системой электропривода машины, так как работа тормоза может внести погрешность в измерения, даже если индикатор закреплен не на исполнительном органе тормоза. Биение тормозных ободьев вновь смонтированных подъемных машин не должно превышать величин, приведенных в табл. 7.5.
94
Для подъемных машин, находящихся в эксплуатации, допустимая величина биения может быть: до 1,2 мм – для барабанных подъемных машин с барабаном диаметром свыше 3,5 м и параллельным перемещением тормозных колодок; до 0,8 мм – для остальных подъемных машин. При этом должен обеспечиваться запас хода поршней тормозных цилиндров при затормаживании, а суммарный зазор между тормозным ободом и фрикционными накладками не должен превышать установленной для данного типа машины величины. Если это условие не выполняется, необходимо проточить и прошлифовать тормозной обод.
Таблица 7 . 5
Допустимые величины биения тормозных ободьев
Диаметр тормозного |
Допустимая величина биения тормозного обода |
||
для вновь смонтированных подъемных машин, мм |
|||
обода, мм |
|||
Для заклиненного барабана |
Для переставного барабана |
||
|
|||
До 3500 |
0,5 |
0,6 |
|
Свыше 3500 до 4000 |
0,5 |
0,7 |
|
От 4000 до 5000 |
0,5 |
0,8 |
|
От 5000 до 7000 |
0,55 |
0,8 |
3. Температуру нагрева. Температура нагрева тормозного обода не должна превышать 70 °С. Чрезмерный нагрев может быть вызван плохой подгонкой фрикционных накладок, неправильной регулировкой исполнительного органа тормоза, неполным оттормаживанием машины вследствие неправильной регулировки тормозного привода, а также выпуклостью обода (при местном нагреве).
7.5.3. Рычажно-шарнирный механизм
При ревизии и наладке рычажно-шарнирного механизма необходимо проверить следующее:
1. Состояние шарнирных соединений. Величину износа шарнирных соединений определить разборкой и обмером их. В табл. 7.6 приведены величины зазоров в шарнире, равные разности диаметров отверстия и валика, замеренные при разборке. Можно определить величину износа шарнирных соединений стрелочным индикатором, неподвижно закрепленным магнитной струбциной на торцешарнирноговалика. Приэтомнеобходимообеспечитьплотноеприлегание индикатора к валику, чтобы избежать возможных относительных перемещений. При растормаживании и затормаживании подъемной машины индикатор зафиксирует суммарный зазор в шарнирном узле. Учитывая трудоемкость работ и длительность простоя машины, рекомендуется разобрать два-три наиболее изношенных шарнирных соединения и результаты измерений сравнить с данными, полученными при замерах с помощью стрелочного индикатора. При зазорах в шарнирах, превышающих допустимые (см. табл. 7.6), необходимо произвести их
95
ремонт. Предельные размеры расточки отверстий и возможность установки втулок необходимо согласовать с заводом-изготовителем. Ремонт шарнирных соединений необходимо производить также во всех случаях, если из-за их износа запас хода поршней тормозных цилиндров меньше допустимого (приложение 5) или продолжительность холостого хода тормоза превышает допустимую по ПБ
[25](см. подразд. 7.1).
2.Состояние смазки шарниров. Все шарниры должны быть смазаны
консистентной смазкой (см. приложение 2). Неисправные пресс-масленки необходимо заменить новыми, а маслопроводные каналы очистить от грязи и старой смазки.
Таблица 7 . 6
Зазоры в шарнирах
Зазор, мм |
|
Номинальный диаметр отверстия шарнира, мм |
||||
от 18 |
Свыше |
Свыше |
Свыше 80 |
Свыше 120 |
Свыше 180 |
|
|
до 30 |
30 до 50 |
50 до 80 |
до 120 |
до 180 |
до 260 |
Номинальный |
0,06–0,13 |
0,07–0,15 |
0,08–0,18 |
0,09–0,21 |
0,10–0,24 |
0,12–0,28 |
Максимально |
|
|
|
|
|
|
допустимый |
0,25 |
0,30 |
0,35 |
0,42 |
0,50 |
0,60 |
3.Состояние тормозных тяг и шарнирных головок. При наличии трещин тяги должны быть заменены новыми. Погнутость тяг недопустима. Детали с поврежденной резьбой необходимо заменить новыми. Новые детали должны быть изготовлены по чертежам завода-изготовителя.
4.Свободу перемещения подвижных деталей исполнительного органа тормоза, которые должны перемещаться свободно, без рывков и заеданий. Все перекосы, заедания в шарнирах и другие неисправности, затрудняющие перемещение подвижных деталей исполнительного органа тормоза, должны быть устранены.
7.5.4. Регулировка исполнительного органа тормоза
Правильно отрегулированный исполнительный орган тормоза должен отвечать следующим требованиям:
1.Суммарный рабочий зазор между фрикционными накладками и ободом должен быть установлен в соответствии с рекомендациями, приведенными в инструкции завода-изготовителя. При отсутствии заводских данных зазор устанавливается в пределах 2…3,5 мм (для исполнительных органов тормоза с угловым перемещением колодокзазоризмеряетсяпосерединеколодки).
2.Выключатель износа колодок (ВИК) должен быть настроен на срабатывание при увеличении суммарного зазора между фрикционными накладками и ободом до 4 мм, а для пружинных тормозов – при уменьшении тор-
96
мозного момента не более 5 % от величины, установленной при рабочем зазоре. При срабатывании ВИК величины хода и запаса хода поршней тормозных цилиндров должны быть:
–для машин с грузогидравлическим приводом тормоза – величина хода поршня не более 250 мм, запас хода поршня до упора в нижнюю крышку цилиндра не менее 150 мм;
–для машин с грузопневматическим приводом тормоза при максимально возможном перемещении (конструктивном ходе) поршня ЦПТ 550 мм – ход поршня ЦРТ от дна цилиндра не более 110 мм, ход поршня ЦПТ при предохранительном торможении не более 480 мм, запас хода поршня ЦПТ не менее 70 мм;
–для машин с грузопневматическим приводом тормоза при максимально возможном перемещении (конструктивном ходе) поршня ЦПТ 670…700 мм – ход поршня ЦРТ от дна цилиндра не более 120 мм, ход поршня ЦПТ при предохранительном торможении не более 540 мм, запас хода поршня ЦПТ не менее 100 мм (см. приложение 5 табл. 5.1);
–для прочих машин – в соответствии с техническими характеристиками приводов тормоза (см. приложение 5).
Для облегчения визуального контроля за величинами хода поршней тормозных цилиндров рекомендуется устанавливать линейки-указатели с делениями и с отметкой положения, при котором срабатывает ВИК.
3.Величина суммарного зазора между фрикционными накладками и ободом левого и правого исполнительного органа тормоза должна быть одинаковой. Разница ходов поршней для левого и правого приводов тормоза не должна превышать величины, указанной в инструкции завода-изготовителя.
4.Суммарный зазор между фрикционными накладками и ободом должен быть распределен поровну между задней и передней тормозными балками. При работе полностью отторможенной машины не должно иметь место задевание тормознымободомфрикционных накладоквследствиебиенияобода.
5.При затормаживании машины должно быть обеспечено полное прилегание фрикционных накладок по всей дуге обхвата ими тормозного обода.
Исполнительный орган тормоза с угловым перемещением колодок. Ре-
гулировку суммарного зазора между фрикционными накладками и ободом исполнительного органа тормоза с угловым перемещением колодок (рис. 7.3 и 7.4) выполнить горизонтальными тягами. Распределение суммарного зазора между фрикционными накладками передней и задней тормозных балок иободом произвестиупорнымболтом6 (см. рис. 7.3) иупорнымиболтами7 и8 (см. рис. 7.4)
Полное прилегание фрикционных накладок к ободу по всей дуге обхвата достигают соответствующей подгонкой и притиркой накладок при работе машины.
97

Рис. 7.3. Исполнительный орган тормоза малых однобарабанных подъемных машин: 1 – тормозная балка задняя; 2 – горизонтальная тяга; 3 – тормозной обод;
4 – фрикционные накладки ; 5 – тормозной рычаг; 6 – упорный болт; 7 – тормозная балка передняя; 8 – шарнирная опора
Исполнительный орган тормоза с пружинно-гидравлическим и пру-
жинно-пневматическим приводом. Регулировку исполнительного органа тормоза, изображенного нарис. 7.4, осуществитьвследующейпоследовательности:
Рис. 7.4. Исполнительный орган тормоза с пружинно-гидравлическим и пружинно-пневматическим приводом:
1, 2 – шарнирные головки; 3 – горизонтальная тяга; 4 – пружинные звенья; 5 – фрикционные накладки тормозных колодок; 6 – тормозные балки; 7, 8 – упорные болты; 9 – угловой рычаг
1.Опустить передний упорный болт 8 так, чтобы между головкой болта
ипередней тормозной балкой был зазор 4 мм.
2.Поднять поршень цилиндра рабочего торможения до упора в верхнюю крышку подачей масла или воздуха (при пружинно-пневматическом
98
грузовом приводе тормоза предварительно должны быть подняты тормозные грузы подачей воздуха в цилиндр предохранительного торможения).
3.Прижать заднюю тормозную балку упорным болтом 7 так, чтобы фрикционные накладки заднейтормознойколодкикоснулисьтормозногообода.
4.Установить вращением горизонтальной тяги 3 рабочий зазор 2–3 мм между тормозным ободом и фрикционными накладками 5 передней тормозной балки. Зазор измерить щупом между ободом и средней фрикционной накладкой (напротив шарнира).
5.Установить регулировкой переднего пружинного звена 4 равномерный зазор по всей дуге обхвата. Произвести несколько затормаживаний и растормаживаний. Если равномерность зазора при этом нарушается, увеличить затяжку обеих пружин.
6.Опустить задний упорный болт 7 на 4 мм, а передним упорным болтом 8 прижать фрикционные накладки передней тормозной балки к тормозному ободу. При этом зазор между тормозным ободом и фрикционными накладками перейдет на заднюю сторону.
7.Отрегулировать задним пружинным звеном равномерность зазора по дуге обхвата.
8.Распределить поровну суммарный зазор 2 мм между двумя фрикционными накладками (по 1 мм на сторону) регулировкой упорных болтов.
9.Произвести около 10 циклов торможений и затем проверить величины зазоров; при необходимости – откорректировать положение регулировочных деталей. При вращении тяги 3 контролировать положение концов тяги через отверстия, имеющиеся в шарнирных головках. Концы тяги должны находиться примерно на середине отверстий. Вывинчивание тяги за пределы кромок отверстия недопустимо.
10.Зафиксировать контргайками регулировочные элементы.
Учитывая трудоемкость изготовления пружинного звена, «Донецкгормаш» выпускает подъемные машины с исполнительным органом тормоза, в котором вместо пружинных звеньев предусмотрены винтовые упоры. Регулировка такого исполнительного органа тормоза производится так же, как и исполнительного органа тормоза, изображенного на рис. 7.4, только равномерность зазора между фрикционными накладками и ободом по всей дуге обхвата устанавливается не пружинными звеньями, а винтовыми упорами. По требованию заказчика «Донецкгормаш» поставляет подъемные машины с исполнительным органом тормоза с пружинными звеньями.
11. Для регулировки второго исполнительного органа тормоза необходимо установить ход поршня такой же величины, как и первого, и произвести регулировку в такой же последовательности по пп. 1–10.
99
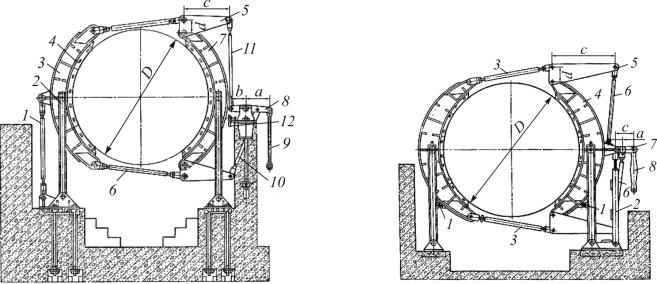
100
Рис. 7.5. Исполнительный орган тормоза |
Рис. 7.6. Исполнительный орган тормоза |
подъемных машин НКМЗ (I типа): 1 – винтовая стойка; |
подъемных машин НКМЗ (II типа): 1 – упорные болты; |
2 – стойка; 3 и 7 – тормозные балки; 4 – фрикционные |
2 – винтовая стойка; 3, 6, 8 – тяги; 4 – тормозные балки; |
накладки; 5 и 8 – рычаги; 6, 9, 10 и 11 – тяги; |
5 и 7 – рычаги |
12 – упорный винт |
|