
книги / Руководство по ревизии, наладке и испытанию шахтных подъёмных установок
..pdfПри ревизии и наладке механизмов перестановки, изображенных на рис. 4.10–4.13, необходимо проверить следующее:
1.Отсутствие утечек масла (воздуха). При необходимости – заменить манжеты.
2.Состояние смазки. Шлицевое подвижное соединение (направляющие пальцы) и зубчатое зацепление механизма перестановки должны быть обильно смазаны (приложение 2).
3.Состояние шлицевых соединений и направляющих пальцев.
4.Затяжку пружин. Затяжка пружин механизма перестановки, изображенного на рис. 4.10, определяется положением втулок 7, ограничивающих выход обоймы 4. Зазоры между втулками и обоймой должны быть равны величине выходаобоймыиодинаковыми длявсех втулок во избежаниеперекосаобоймы.
Для механизма перестановки, изображенного на рис. 4.13, затяжка
пружин 7 определяется положением гильз 8, ограничивающих выход зубчатого колеса 9. Для машин 2×2,5×1,2 зазоры между гильзами 8 и стаканами 6 должны быть равны 70 мм.
Для механизма перестановки машин 2Ц-3,5×1,7А (см. рис. 4.11) затяжка пружин 15 при включенной муфте должна быть равна 67,3 мм.
При значительной усадке или поломке пружин они должны быть заменены новыми.
5.Затяжку всех болтовых соединений.
6.Состояниезубьев. Износ зубьевпотолщинеболее 15 % не допускается.
7.Работу механизма блокировки при перестановке. Конечные выключатели механизма блокировки должны соответственно блокировать тормоз переставного барабана в начале выхода муфты из зацепления и разрешать включать приводной двигательмашины после входазубчатойполумуфтывзацепление.
8.Четкость работы механизма перестановки (см. подразд. 4.2.3).
При включении муфты зубья должны входить в зацепление на всю длину, а ход подвижной части должен ограничиваться буферными устройствами, предусмотренными конструкцией механизма перестановки.
4.2.3. Общие указания по производству перестановки барабанов
Перестановку барабанов (заклиненной части разрезного барабана) необходимо производить не менее чем двумя лицами (машинистом подъема и электрослесарем или механиком подъема). При этом следует придерживаться определенной последовательности проведения всех операций:
–перед перестановкой барабанов предупреждать шахтный персонал на нижней и верхней (нулевой) площадках о предстоящей работе;
–подъемные сосуды разгрузить;
–подъемный сосуд переставного барабана (переставной части разрезного барабана) установить на посадочные устройства (кулаки, посадочные
31
брусья). Для подъемных установок с БЦКБ необходимо определить положение сосудов, когда перестановка будет наиболее благоприятной с точки зрения создания необходимых запасов тормозного момента;
–переставной барабан (переставную часть разрезного барабана) застопорить специальным стопорным устройством;
–перед перестановкой проверить исправность тормозной системы и запас хода поршней тормозных цилиндров. При запасе хода меньше допустимого произвести соответствующую регулировку тормоза;
–после включения механизма перестановки барабанов необходимо убедиться, что произошло полное расцепление зубчатого колеса с зубчатой обоймой и зубчатого зацепления расцепного устройства регулятора подъема машин НКМЗ;
–включить подъемный двигатель и со скоростью не более 0,3 м/с произвести проворачивание заклиненного барабана (заклиненной части разрезного барабана), установив сосуд в требуемую точку ствола. При этом необходимо проверить отсутствие заедания во втулках (подшипниках) переставного барабана (переставной части разрезного барабана);
–после регулировки взаимного расположения сосудов в стволе произвести сцепление барабанов.
После окончания перестановки необходимо скорректировать показания указателя глубины, положения этажных выключателей АЗК, профилей ретардирующих дисков ограничителя скорости. Со скоростью не более 1 м/с выполнить перегон подъемных сосудов на приемные площадки. При этом следует убедиться, что показания указателя глубины, положение этажных выключателей и профилей на ретардирующих дисках соответствуют положению подъемных сосудов в стволе.
Глава 5 РЕДУКТОРЫ
Подъемные машины с быстроходными двигателями оснащаются двухприводными или одноприводными редукторами (по количеству двигателей). Колеса и шестерни редукторов – цилиндрические, как правило, с двухрядным расположением зубьев, косозубые шевронного типа, с эвольвентным зацеплением или с зацеплением Новикова. Для малых машин с диаметром барабана до 3 м применялисьтакжезубчатыепередачисэвольвентнымзацеплением.
5.1. Ревизия и наладка редуктора без вскрытия крышки
При ревизии и наладке редуктора необходимо проверить следующее: 1. Состояние фундамента, анкерных болтов и их затяжку, отсутствие
масляных пятен и трещин в фундаменте. При обнаружении трещин необходимо на трещину через каждые 150–200 мм установить алебастровые маяки
32
сечением 20×10 мм и длиной не менее 30 мм. Через 2–3 дня по наличию разрывов маяков выявляют развивающиеся трещины. Попадание масла на фундамент снижает его прочность, поэтому устранению утечек масла необходимо уделять особое внимание.
2.Состояние корпуса и крышки, крепление и прилегание корпуса к фундаменту, наличие всех крепежных деталей, уплотнений по плоскости разъема, исправность маслопроводящих трубопроводов и отсутствие утечек смазки. При обнаружении отслоения фундамента от корпуса редуктора вырубить его на дефектном участке до свежего бетона и залить это место бетоном из быстросхватывающегося цемента.
3.Наличие смазки (см. гл. 8 и приложение 2).
4.Установку корпуса редуктора по горизонтали (для вновь монтируемых
редукторов). Установить поочередно уровень на строганные части корпуса и шейки валов. При правильной установке корпус не должен иметь прогибов от затяжки анкерных болтов, а оси валов должны находиться в одной плоскости (допускаетсяотклонениеосей валовдругот друга неболее чемна±0,5 мм).
5.Состояние зубьев. При осмотре зубчатых зацеплений проверить целость зубьев, износ их и состояние поверхностей. Величина износа зубьев по толщине не должна превышать 10 %. Наличие питтинга (выкрашивание металла на поверхности зубьев) не может служить причиной замены колес, если питтинг расположен у ножки зуба и занимает не более 20 % боковой поверхности его. При большой величине питтинга ножки зуба или в месте перехода его на головку зуба (что особенно опасно), а также при наличии выломанных зубьев, трещин у ножек зубьев вопрос о дальнейшей эксплуатации редуктора должен быть согласован с заводом-изготовителем.
6.Зубчатое зацепление по расположению и величине пятна контакта. Очистить и тщательно вытереть три-четыре сопряженных зуба колеса и валашестерни и покрыть их тонким слоем синей или черной масляной краски, разведенной на керосине. Включить подъемный электродвигатель и провернуть в одну и другую сторону несколько раз вал-шестерню (ввести и вывести из зацепления зубья вала-шестерни, покрытые краской). По расположению отпечатка зубьев вала-шестерни на зубьях колеса определить величину и характер пятна контакта. Проверку пятна контакта зубьев редуктора, длительное время находящегося в эксплуатации, можно производить по металлическому блеску зубьев. У редукторов с эвольвентным зацеплением пятно контакта должно располагаться растянутым овалом посередине рабочей поверхности зуба, а величина его – соответствовать нормам завода-изгото- вителя. При отсутствии завод-ских данных необходимо руководствоваться нормами величин пятна контакта зубьев редукторов с эвольвентным зацеплением, приведенными в табл. 5.1.
33
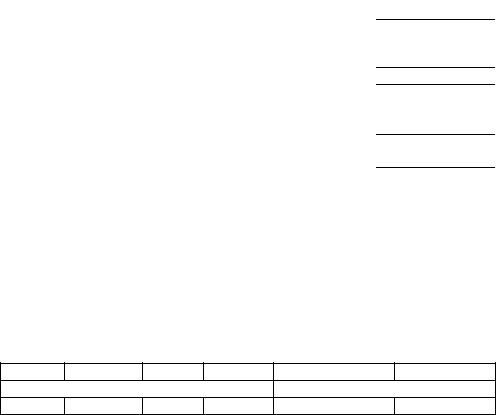
В передачах с зацеплением Новикова в редукторах ЦОН-16, ЦДН-17,
ЦОН-18, 2ЦОН-22, 2Ц-1600, Ц2Ш-1000, Ц2Ш-900, Ц2Ш-710, (Ц2Ш-800П и Ц2Ш-800У – только быстроходная передача) первоначальный контакт зацепления до приработки зубьев под нагрузкой должен равномерно распределяться вдоль зубьев в виде линий, расположенных в средней части рабочих участков профилей, распространяясь не менее чем на 80–95 % их длины (рис. 5.1, а). В процессе работы редуктора под нагрузкой происходит приработка зубьев и контакт зацеплений распространяется на всю их высоту. Шабрение или обработка зубьев напильником не допускается.
Примеры пятна контакта зубьев редукторов с зацеплением Новикова и допустимые размеры пятна контакта приведены на рис. 5.1. и в табл. 5.2.
|
|
Таблица 5 . 1 |
|
Величина пятна контакта зубьев редукторов |
|||
с эвольвентным зацеплением |
|
||
|
|
|
|
Тип редуктора |
Пятно контакта не менее, % |
||
по высоте зуба |
по длине зуба |
||
|
|||
ЦДП-7, 2ЦД-14, РС-700М, 2ЦД-17, 2ЦД- |
|
|
|
20, 2ЦД-23, ЦД-20, ЦД-2000, ЦО2Х2200, |
45 |
60 |
|
ЦО-20, ЦД-17, ЦД-100Т |
|
|
|
ЦД-16 |
60 |
80 |
|
ЦО-18, ЦО-22, ЦО2х1800 |
50 |
70 |
|
ЦД-115, ЦД-115у, ЦД5-115, ЦД-150М, |
45 |
50 |
|
ЦД2-163 |
|||
|
|
||
ЦД-150У, ЦД-170, РЦД-1150Л, КЦТН- |
50 |
60 |
|
710 |
|||
|
|
||
Ц2Ш-800П*, Ц2Ш-800У* |
45 |
60 |
Примечание. Для редукторов, не указанных в таблице, пятно контакта должно быть не менее 40–45 % по высоте и 60–65 % по длине зуба (большие значения относятся для колес, выполненных с 7-й степенью точности по нормам контакта зубьев, меньшее – для колес с 8-й степенью точности).
*Допуски на пятно контакта зубьев приведены для тихоходных передач редукторов.
Таблица 5 . 2
Допустимые размеры пятна контакта зубьев зацепления Новикова
а |
б |
в |
г |
д |
е |
В долях от нормального модуля |
В долях от ширины колеса |
||||
> 0,1 |
> 1,0 |
< 1,0 |
> 0,2 |
> 0,8 |
> 0,4 |
34
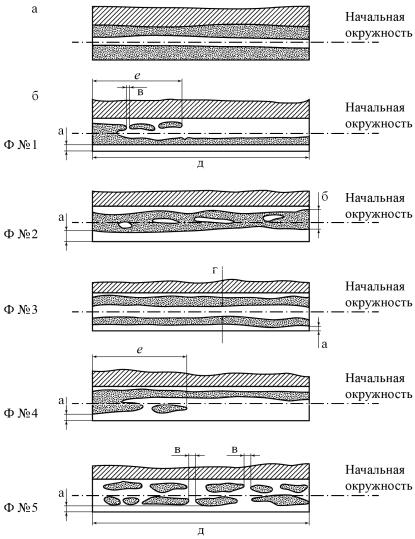
Рис. 5.1. Примеры пятна контакта зубьев с зацеплением Новикова: а – нормальный контакт зубьев; б – допустимые формы и размеры пятна
контакта в долях от нормального модуля и ширины колеса
(формы № 1, 2, 3, 4, 5)
При несоответствии величины и расположения пятна контакта зубьев заводским нормам или приведенным в табл. 5.1, 5.2 и на рис. 5.1 необходимо установить характер этого несоответствия. Если он одинаков для всех зубьев колеса, то причины могут заключаться в следующем:
– редукторы с регулируемым межцентровым расстоянием – непараллельность и перекос осей зубчатых передач;
35
– редукторы с жестким межцентровым расстоянием – перекос осей, вызванный пережимом корпуса редуктора при монтаже или горным давлением при работе редуктора в шахте.
Выявить перекос валов можно при помощи уровня. Для этого уровень поочередно установить на вал-шестерню и зубчатое колесо и определить величину и направление наклона вал-шестерни и зубчатого колеса.
При невозможности установить уровень на колесе пользуются переходной призмой. Устранить перекос, вызванный пережимом корпуса редуктора, необходимо поочередным ослаблением болтов, крепящих редуктор к фундаменту, и подкладыванием стальных прокладок под корпус. После каждого ослабления болтов проверить пятно контакта по краске и измерить наклон валов. После устранения пережима корпуса произвести подливку фундамента. Кроме того, у редукторов с подшипниками качения необходимо проверить отсутствие зажатия наружных колец в корпусе редуктора или в стаканах корпусов. Для «плавающих» опор редуктора с подшипниками качения необходимо также проверить возможность их осевого перемещения и удостовериться в том, что при установленных и закрепленных крышках подшипников валы не зажаты и позволяют самоустанавливаться зубчатым передачам. Для этого в «плавающей» опоре должны быть предусмотрены зазоры на 2–3 мм больше величины удлинения вала при рабочем нагреве опоры.
7. Работу редуктора под нагрузкой. Шум редуктора при работе должен быть ровным, низкого тона, без стуков, перезвонов и пульсаций.
Стук в редукторе, вызванный колебанием зубчатых колес при резком торможении машины, не является ненормальным явлением.
В редукторах с зацеплением Новикова иногда наблюдается повышенный шум, который ослабевает в процессе приработки зубчатого зацепления.
5.2. Ревизия и наладка редуктора со вскрытием крышки
При ревизии и наладке редуктора со вскрытием крышки дополнительно
ктребованиям подразд. 5.1 необходимо проверить следующее:
1.Отсутствие трещин в ступицах, спицах и ободьях зубчатых колес; смещения бандажей и отсутствие шаткости колес на валах. Для этого при затянутых крышках подшипников и заторможенной машине несколько раз включить и выключить подъемный электродвигатель в разных направлениях. Шаткость колес устранить подтяжкой шпонок или заменой их. После подтяжки тангенциальных шпонок установить новые стопорные устройства. Разъемные колеса перед подтяжкой шпонок тщательно обтянуть. Запрещается устанавливать дополнительные прокладки под шпонки. Если при выработанном посадочном месте после затяжки шпонок появляется зазор между
36
ступицей колеса и валом, то дальнейшая эксплуатация редуктора должна быть согласована с заводом-изготовителем. После замены или подтяжки шпонок необходимо в течение года три-четыре раза проверить отсутствие шаткости колес.
2.Величину бокового зазора между зубьями передачи при помощи свинцовых оттисков. Величина зазора должна соответствовать данным, указанным на чертеже завода-изготовителя. При отсутствии заводских данных радиальный боковой зазор установить в пределах 0,15–0,25 нормального модуля передачи.
3.Отсутствие перекоса осей валов.
Допуск на непараллельность и перекос осей валов при нормальном модуле (от 1 до 30 мм) приведен в табл. 5.3.
Таблица 5 . 3
Допуск на непараллельность и перекос осей валов
|
Допуск на непараллельность и перекос осей валов (мкм) |
||||
Степень |
|
при ширине колеса или полушеврона (мм) |
|
||
точности |
от |
от |
от |
от |
от |
|
110 до160 |
160 до 220 |
220 до 320 |
320 до 450 |
450 до 630 |
7 |
21 |
24 |
28 |
34 |
40 |
8 |
26 |
30 |
36 |
42 |
50 |
9 |
34 |
38 |
45 |
52 |
60 |
4. Биение торца обода колеса. Если характер несоответствия пятна контакта зубьев нормам циклически изменяется по окружности колеса, причиной может быть биение торца обода колеса. Биение проверить стрелочным индикатором, устанавливаемым у торца венца зубчатого колеса. Для исключения влияния осевого разбега вала на показания индикатора у торца вала необходимо установить второй индикатор. Показания индикаторов вычитают, если они расположены с одной стороны колеса, и складывают, если они расположены с разных сторон.
Биение измеряют не менее чем в восьми точках по окружности колеса. Если фактическая величина биения превышает допустимую, то дальнейшая работа редуктора должна быть согласована с заводом-изготовителем. Допустимая величина торцевого биения зубчатого колеса, отнесенная к 100 мм его диаметра, приведена в табл. 5.4.
37

|
|
|
|
|
|
|
Таблица |
5 . 4 |
||
Допустимая величина торцевого биения зубчатого колеса |
|
|||||||||
|
|
|
|
|
|
|
|
|
|
|
Степень точ- |
|
Биение (мкм) при ширине колеса или полушеврона, (мм) |
|
|||||||
|
от |
|
|
|
|
|
|
|
|
|
ности по |
до |
от 110 |
от 160 |
от 220 |
от 320 |
от 450 |
от 630 |
от 900 |
||
нормам кон- |
55 |
до |
до |
|||||||
такта |
55 |
до |
160 |
до 220 |
320 |
до 450 |
до 630 |
до 900 |
до 1250 |
|
|
|
110 |
|
|
|
4,2 |
|
|
|
|
7 |
21 |
11 |
8 |
6 |
5 |
3,6 |
3,2 |
|
2,8 |
|
8 |
26 |
14 |
10 |
8 |
6 |
5,2 |
4,5 |
4,0 |
|
3,6 |
9 |
34 |
18 |
12 |
10 |
8 |
6,5 |
5,5 |
5,0 |
|
4,5 |
10 |
42 |
22 |
16 |
12 |
10 |
8,5 |
7,0 |
6,0 |
|
5,5 |
5.Состояние разъема. Вскрыть крышки редуктора и подшипников, очистить поверхность разъема, затем промыть ее керосином или соляровым маслом
ипротереть денатурированным спиртом или растворителем РПВ. На просушенную поверхность непрерывным слоем нанести пасту «Герметик» вдоль всей поверхности разъема узкой струйкой. Установить крышку и равномерно затянуть болты. Под действием давления паста растекается по всей поверхности разъема, заполняя все неровности и пустоты. Через 2–3 часа после герметизации редуктор может быть включен в работу. Запрещается устанавливать уплотнительные прокладки внепредусмотренных конструкциейредуктораместах.
6.Работу редуктора под нагрузкой (см. подразд. 5.1 п. 7).
5.3. Ревизия и наладка подпружиненного редуктора
При ревизии и наладке подпружиненного редуктора дополнительно к требованиям подразд. 5.1 необходимо проверить следующее (см. рис. 6.9 гл. 6):
1.Состояние и крепление пружинных опор к фундаменту. Передней опорой принято считать опору, расположенную со стороны привода тормоза.
2.Горизонтальность верхней поверхности тумбы пружинной опоры (при вводе редуктора в эксплуатацию). Отклонение от горизонтали не должно превышать 0,5 мм на 1 м длины.
3.Биение корпуса (при вводе редуктора в эксплуатацию или при неудовлетворительной работе). Установить два стрелочных индикатора так, чтобы ножка одного из них упиралась в боковую, а второго – в торцевую стенку корпуса редуктора. Медленно провернуть канатоведущий шкив и определить амплитуду биения в горизонтальной плоскости. Если фактическая величина амплитуды биения превышает 0,6 мм, то необходимо проверить соосность валов машины с редуктором и редуктора с электродвигателями
(см. подразд. 6.4.2).
4.Состояние и крепление демпфера. Внутреннюю полость демпфера залить полностью маслом. Наличие воздуха в демпфере не допускается. Регулирование демпфера произвести при работе машины с номинальной на-
38
грузкой. Регулировочными болтами добиться такой степени дросселирования отверстий, которые перепускают масло из одной полости в другую, чтобы число колебаний редуктора при пиковых нагрузках, возникающих при включении электродвигателей, было минимальным.
5. Установку демпфера (при вводе редуктора в эксплуатацию). У правильно установленного демпфера поршень должен занимать такое положение в цилиндре, чтобы расстояние от крышки до круговой риски на штоке соот-
ветствовало: |
|
– для редуктора 2ЦД-14 |
0 мм; |
– для редукторов 2ЦД-17, 2ЦД-20, 2ЦД-23 |
5 мм. |
При максимальных усилиях, возникающих при пуске машины, когда выбираются полностью зазоры между упорами и корпусом редуктора, поршень демпфера не должен доходить до крайних положений, а удары должны отсутствовать.
Глава 6 ВАЛЫ, ПОДШИПНИКИ, СОЕДИНИТЕЛЬНЫЕ МУФТЫ
6.1. Ревизия и наладка подшипников скольжения
Ревизию и наладку подшипников скольжения коренных валов редуктора и барабана со вскрытием крышки производят во время капитального ремонта подшипника. Ежегодно у этих подшипников необходимо проверить состояние корпуса, крышки, крепежных деталей, смазки, температуру нагрева, отсутствие стука и вибрации. Радиальные зазоры измерить щупами с торца вала. По результатам осмотра и проверки делается вывод о работоспособности подшипника. Разборку подшипника необходимо производить при обнаружении показателей неудовлетворительной работы.
При ревизии и наладке подшипников скольжения необходимо проверить следующее:
1.Состояние корпуса, крышки и их крепление. Внешним осмотром проверить отсутствие трещин в корпусе и крышке, наличие всех болтов в соединениях, регулировочных клиньев (где предусмотрено конструкцией) и крепление корпуса.
2.Величину вибрации. Эксплуатационная норма амплитуды колебаний не должна превышать значений, приведенных в [17]:
– частота вращения, мин-1 |
1500 |
1000 |
750 |
и ниже; |
– допустимая норма амплитуды |
|
|
|
|
колебаний, мкм |
39 |
47 |
53. |
|
Основными причинами возникновения вибрации являются:
–неуравновешенность вращающихся частей;
–слабое крепление подшипников;
39
–неудовлетворительная соосность валов;
–биение муфт;
–радиальныезазорывподшипниках, превышающиедопустимые нормы;
–искривление или овальность шеек валов;
–короткое замыкание в роторе электродвигателя;
–большая неравномерность воздушного зазора между сталью ротора и статора электродвигателя.
Методика измерения вибрации и правила пользования виброизмерительными приборами изложены в инструкциях завода-изготовителя.
3.Температуру нагрева. Допустимая температура нагрева подшипника не должна превышать 80 °С. Измерение температуры произвести термосигнализаторами ТКП-160 (ТСМ-100) или др. При отсутствии термосигнализаторов с достаточной для практических целей точностью температуру подшипника можно определить по температуре масла, измеренной при помощи технического термометра. Температурамасла приэтом должна бытьневыше65 °С.
4.Наличие смазки (см. подразд. 8, приложение 2).
5.Состояние рабочей поверхности вкладышей. Вскрыть торцевую и верхнюю крышки подшипника и снять вкладыш. Талью или домкратом приподнять вал, извлечь нижний вкладыш и осмотреть рабочие поверхности. Обратить внимание на отсутствие трещин, выкрашивания, оплавлений и отслаивания баббита от вкладыша.
Погрузить вкладыш в ванну с соляровым маслом, извлечь его, вытереть насухо и слегка надавить на баббит. Появление масла из микротрещин свидетельствует о некачественном сцеплении баббита с телом вкладыша. При обнаружении выкрашивания или отслаивания баббита от тела вкладыша более чем на 20 % площади вкладыш необходимо заменить.
6.Состояние шейки вала. При наличии следов ржавления, царапин, рисок, отдельных забоин шейку вала обработать бархатным напильником и прошлифовать мелким наждачным полотном или бумагой, после чего удалить частички абразива, врезавшиеся в вал, а затем промыть керосином. Крупные дефекты шеек валовустранитьпо согласованиюсзаводом-изготовителем.
7.Горизонтальность установки вала и подшипника по разъему. Протереть нижнюю поверхность уровня и поверхность, на которую он устанавливается, и измерить наклон вала и подшипника. Измерения произвести в двух положениях уровня с поворотом его на 180°. Отклонение от горизонтали вала
иподшипника не должно превышать 1 мм на 1 м длины.
8.Радиальные биения шейки вала. Проверить (при необходимости) индикатором часового типа не менее чем в восьми точках. При проверке индикатор установить на плоскость разъема подшипникового стояка или на другое жесткое основание и медленно вращать вал. Измерительный стержень индикатора должен находиться ввертикальнойплоскости, проходящей черезосьвала.
40