
книги / Руководство по ревизии, наладке и испытанию шахтных подъёмных установок
..pdfВеличина радиального биения не должна превышать значений, указанных на чертеже завода-изготовителя. При отсутствии заводских данных радиальные биения шейки валанедолжны превышатьзначений, приведенных ниже:
– диаметр шейки вала, мм |
до 200 |
более 200; |
– допустимое радиальное биение, мм |
0,02 |
0,03. |
9.Прилегание вкладыша к шейке вала (проверить при монтаже или замене подшипника). Смазать шейку вала тонким слоем краски или графита и уложить вкладыш. Поворачивая вкладыш на угол 10–15° (без перекатывания) или перемещая его вдоль оси вала на 20–30 см, получить отпечатки краски на рабочей поверхности вкладыша. Пятна контакта должны быть равномерно распределены по всей поверхности соприкосновения вкладыша с шейкой вала, и на площадку размером 2,5×2,5 см должно приходиться не менее 8–10 пятен (85 % рабочей поверхности вкладыша должно быть равномерно покрыто мелкими пятнами касания). Если прилегание неудовлетворительное, вкладыш необходимо пришабрить.
10.Наличие рабочего контакта вала с поверхностью нижнего вкладыша (проверить при монтаже или замене подшипника). Нанести на рабочую поверхность шейки вала полоску краски шириной 6–10 мм и провернуть вал на 360°. По растертой краске определить прилегание вала к нижнему вкладышу, которое должно обеспечиваться по всей длине вкладыша. В противном случае нижний вкладыш следует пришабрить, как указано выше.
11.Величину радиального зазора между шейкой вала и верхним вкладышем. Величину зазора установить согласно рекомендациям завода-изготовителя (табл. 6.1). Приотсутствии заводскихданныхдопустимыйрадиальный зазорmдоп
ввертикальнойплоскостиможно определитьпоформуле
mдоп (0,0005...0,0015)d , |
(6.1) |
где d – диаметр шейки вала, мм.
Для определения радиального зазора на шейку вала и плоскость разъема подшипника положить свинцовые проволочки диаметром 2–3 мм и длиной 20–40 мм (рис. 6.1). Затем собрать подшипник и равномерно затянуть болты крест на крест. Затяжка болтов должна быть такой, чтобы не деформировался баббит и не исказилась фактическая величина зазора. Затем подшипник разобрать и микрометром измерить толщину оттисков.
Фактическую величину радиальногозазора(мм) определитьпоформулам:
m c |
a1 b1 |
; |
|
||||
|
|
|
|||||
1 |
1 |
2 |
|
(6.2) |
|||
|
|
|
|||||
|
|
|
|
a 2 b2 |
|||
m |
c |
|
, |
||||
|
|||||||
2 |
2 |
2 |
|
|
|||
|
|
|
|
где a1, b1, c1, a2, b2, c2 – толщины свинцовых оттисков, мм. Разница между m1 и m2 не должна превышать 10 %.
41
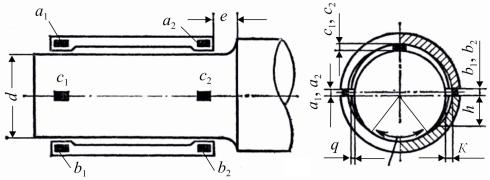
|
Допустимые зазоры между шейкой вала |
Таблица 6.1 |
||
|
|
|||
|
и вкладышем и глубина масляного кармана |
|
||
|
|
|
|
|
|
Радиальный зазор между шейкой вала |
|
|
|
|
и верхним вкладышем подшипника |
Макси- |
|
|
Диаметр |
скольжения, мм |
мальный зазор |
Глубина |
|
шейки вала, |
подъемных |
электродвигателей |
К в зоне масля- |
масляного |
мм |
машин и |
ного кармана, |
кармана h, мм |
|
|
редукторов |
при частоте вращения |
мм |
|
|
ротора до 1000 об/мин |
|
||
|
|
|
||
|
завода НКМЗ |
|
|
|
50–80 |
0,06–0,18 |
0,065–0,135 |
2,0 |
15 |
81–120 |
0,08–0,21 |
0,08–0,160 |
2,5 |
18 |
121–180 |
0,10–0,24 |
0,10–0,195 |
3,0 |
20 |
181–260 |
0,12–0,28 |
0,12–0,225 |
3,0 |
20 |
261–360 |
0,14–0,32 |
0,14–0,250 |
3,5 |
25 |
361–500 |
0,16–0,37 |
0,17–0,305 |
4,0 |
30 |
501–630 |
0,18–0,40 |
0,18–0,350 |
5,0 |
35 |
631–800 |
0,20–0,43 |
0,20–0,400 |
6,5 |
45 |
Рис. 6.1. Измерение зазоров в подшипниках скольжения
Радиальный зазор допускается регулировать изменением количества прокладок из тонкой листовой стали толщиной 0,1–0,2 мм в разъеме между верхним и нижним вкладышами. Прокладки установить так, чтобы не закрывались отверстия для прохода болтов, шпилек и отверстия для прохода масла.
Следует помнить, что при установке прокладок в разъеме между вкладышами необходимо также устанавливать прокладки и в разъеме между корпусом и крышкой подшипника для обеспечения требуемого зазора (натяга) между верхним вкладышем и крышкой. Уменьшить радиальный зазор между шейкой вала и верхним вкладышем можно, прострогав или спилив плоскости разъема вкладышей. В таком случае между верхним вкладышем и крышкой также необходимоустанавливатьпрокладку дляобеспечениятребуемогозазора(натяга).
42
Вообще, установка прокладок весьма нежелательна и может быть рекомендована только как временная мера. При увеличении радиального зазора более допустимой величины необходима перезаливка вкладышей.
12. Величину бокового зазора между нижним вкладышем и шейкой вала в плоскости разъема. Допустимый боковой зазор qдоп принимается равным
половине допустимого радиального зазора между валом и верхним вклады-
шем (qдоп= mдоп/2).
13.Величину масляного кармана (холодильника), обеспечивающего подачу масла вдоль вкладыша и способствующего затягиванию масла в рабочую зону. Максимальная величина зазора K в зоне масляного кармана и глубина масляного кармана h не должны превышать допустимых (табл. 6.1). Длина масляных карманов не должна превышать 5/6 длины вкладыша.
14.Величину осевых зазоров е между галтелями вала и торцами вкладыша подшипника и осевого разбега валов. Осевой разбег вала электрической машины, равный сумме осевых зазоров, установить в пределах 2–4 мм в обе стороны от центрального положения ротора, определяемого совпадением магнитных осей статора и ротора. Для остальных валов осевой разбег установить согласно рекомендациям завода-изготовителя. При отсутствии заводских данных исходят из предположения, что вал удлиняется на 0,5 мм на 1 м длины при повышении его температуры на 40 °С.
15.Величину натяга между верхним вкладышем и крышкой подшипника. Фактическую величину натяга (мм) определить по формуле
Н |
Ф |
с |
а3 а4 b3 b4 , |
(6.3) |
|
3 |
4 |
|
|
|
|
|
|
где a3, a4, b3, b4 – толщины свинцовых оттисков по разъему между корпусом и крышкой подшипника, мм; c3 – толщина свинцового оттиска между верхним
вкладышем и крышкой подшипника, мм. Величина натяга должна быть в пределах 0,05–0,1 мм.
16.Чистоту масляной ванны (у подшипников с кольцевой смазкой). При обнаружении загрязнений старую смазку удалить, подшипник промыть керосином и залить свежее масло.
17.Состояние смазочных колец. Кольца не должны иметь заусенцев, задиров, вмятин и деформаций в виде овальностей и изгибов. При работе машины смазочные кольца должны вращаться плавно без рывков и заеданий.
18.Сборку подшипника. Затяжку диагонально расположенных болтов произвести одновременно. Уплотнение по плоскости разъема обеспечить пастой «Герметик» (см. подразд. 5.2 п. 5).
43
19. Работу подшипника под нагрузкой. Проверить подачу масла к подшипнику, вращение смазочных колец, температуру нагрева, отсутствие повышенного шума, стука и вибрации.
6.2. Ревизия и наладка подшипников качения
Валы современных подъёмных машин и редукторов имеют опоры с подшипниками качения. Оси направляющих (копровых) и отклоняющих шкивов, переставные барабаны двухбарабанных и переставные части барабанов однобарабанных с разрезным барабаном подъёмных машин, свободно посаженные ступицы заклиненных барабанов также опираются на подшипники качения.
Подшипники качения подшипниковых заводов имеют основное условное обозначение по ГОСТ 520 – 71, состоящее в общем случае из семи цифр. Первые две цифры справа обозначают внутренний диаметр подшипника. Для получения внутреннего диаметра в мм при диаметре от 20 до 495 мм это двухзначное число следует умножить на 5. В условном обозначении подшипников с внутренним диаметром 500 мм и более вместо шифра из двух цифр через косую черту указывается внутренний диаметр в мм.
Третья цифра справа обозначает серию подшипника по диаметру и ширине (легкая, средняя, тяжелая и т.д.). Четвертая цифра справа обозначает тип подшипника: 0 – радиальный шариковый; 1 – радиальный шариковый двухрядный сферический; 2 – радиальный с короткими цилиндрическими роликами; 3 – радиальный роликовый двухрядный сферический; 4 – игольчатый; 5 – с витыми роликами; 6 – радиально-упорный шариковый; 7 – радиально-упорный роликовый конический; 8 – упорный шариковый; 9 – упорныйроликовый.
Пятая и шестая цифры обозначают конструктивные особенности подшипника (с коническим отверстием, с закрепительной втулкой и т.п.). Седьмая цифра справа обозначает серию подшипника по ширине (нормальная, узкая, широкая).
Основное условное обозначение подшипника наносится на торец внутреннего кольца способом клеймения, дополнительное – электрографом или травлением [42].
ПрименяемыевпоследнеевремяподшипникикаченияфирмSKF (Швеция), FAG (Германия), FBC (Великобритания), BCA (США) и др. имеют условные обозначения, указанныевсоответствующейсправочнойлитературеданныхфирм.
Перечень подшипников качения, применяемых в опорах главного вала и механизме перестановки барабанов подъёмных машин заводов НКМЗ и «Донецкгормаш», приведены в приложении 3.
В опорах редукторов подъёмных машин применяются в основном роликовые двухрядные сферические, роликовые с короткими цилиндрическими роликами и радиально-упорные роликовые конические подшипники.
44
Ревизию и наладку подшипниковых узлов с подшипниками качения выполнить в следующей последовательности:
1.Проверить состояние корпуса и крышек, наличие крепежных деталей, затяжку болтов, крепящихкорпусподшипниковогоузла крамеили опорам.
2.Вскрыть торцевые крышки, удалить старую смазку, промыть подшипник керосином, соряркой или другим растворителем.
3.Произвести осмотр колец, тел качения и сепараторов.
Наиболее часто встречаются следующие дефекты:
–усталостное выкрашивание рабочих поверхностей дорожек и тел качения (питтинг) вследствие длительной эксплуатации подшипника. Большему износу подвержена дорожка качения внутреннего кольца;
–задиры рабочих поверхностей в виде борозд на дорожках качения, образующихся при недостаточной смазке, а также при слишком малых радиальных зазорах, получившихся в результате неправильной посадки подшипника на вал;
–пластическая деформация в виде лунок и вмятин на дорожках качения. Наблюдается у тихоходных подшипников при действии больших или ударных нагрузок;
–абразивный износ рабочих поверхностей в результате недостаточной защиты от попадания в подшипник пыли вследствие несовершенства или неисправности уплотнений подшипникового узла;
–коррозия поверхностей деталей подшипника;
–износ и разрушение сепараторов;
–трещины и сколы на поверхности колец и тел качения в результате неправильного или небрежного монтажа.
4. Проверить перекос осей наружного и внутреннего колец подшипника. При отсутствии перекоса торцы наружного и внутреннего колец должны находиться в одной плоскости. Дополнительную проверку отсутствия перекоса произвести по равномерности распределения нагрузки между рядами роликов. Число нагруженных (зажатых) роликов в нижней части подшипника должно быть одинаковым в обоих рядах и симметричным относительно вертикальной оси. Одновременно проверить угол зоны нагружения, в пределах которого находятся зажатыеролики. Оптимальныйуголзонынагруженияравен90° – 120°.
При наладочных работах на вновь смонтированных машинах измерение
перекоса осей наружного и внутреннего колец произвести при помощи индикатора часового типа, установленного на валу. Измерительный стержень индикатора при производстве измерений должен упираться в торец наружного кольца подшипника. Перекос осей не должен превышать значений, указанных в документации завода-изготовителя подъёмной машины. При отсутствии заводских указанийможноруководствоваться допусками, приведеннымивтабл. 6.2.
45
5. Измерить величину радиального зазора между роликами и наружным кольцом. Зазор измерить пластинчатым щупом с обоих торцов подшипника. При замере щуп должен с небольшим усилием от руки проходить между роликом и дорожкой качения по всей длине ролика или большей части его. Ролик при измерении должен быть отжат к внутреннему борту подшипника. Накатывание ролика на щуп не допускается. Измерение произвести четыре раза, каждый раз поворачивая вал на 90°. У двухрядных подшипников измерения зазоров произвести в обоих рядах. За величину рабочего радиального зазора подшипника принять среднее арифметическое этих измерений.
Таблица 6 . 2
Допуски на перекос осей наружного и внутреннего колец подшипника
|
Допуск на перекос |
|
Допуск на перекос |
|
Тип |
оси наружного |
Тип |
оси наружного коль- |
|
кольца относитель- |
ца относительно оси |
|||
подшипника |
но оси внутреннего |
подшипника |
внутреннего кольца |
|
|
кольца подшипни- |
|
подшипника, |
|
|
ка,мм на 1 м |
|
мм на 1 м |
|
Роликовый, |
|
Роликовый с |
|
|
шариковый, |
3 |
короткими |
0,1 |
|
сферический, |
цилиндрическими |
|||
|
|
|||
двухрядный |
|
роликами |
|
|
Шариковый, |
|
Роликовый |
|
|
радиальный, |
0,5 |
конический |
0,1 |
|
однорядный |
|
|
|
Кроме того, можно пользоваться методом измерения величины радиального зазора фирмы SКF для подшипников средних и больших размеров. Данный метод предполагает использование щупа для измерения радиального внутреннего зазора подшипников в домонтажном и послемонтажном состоянии. Измерение величины зазора всегда следует производить между наружным кольцом и ненагруженным роликом (рис. 6.2).
Перед измерением провернуть наружное кольцо несколько раз. Убедиться в том, что оба кольца подшипника и ролики отцентрированы по отношению друг к другу. Зазор определить следующим образом (рис. 6.2):
–измерить зазор c в положении 12 часов для стоящего подшипника или
вположении 6 часов для подшипника, установленного на шейке вала (опирающегося на вал);
–измерить зазор а в положении 9 часов и зазор b в положении 3 часа, не меняя положение подшипника;
46
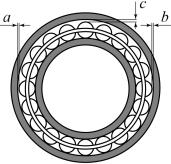
– величина «истинного» радиального внутреннего зазора равна
0,5(а+ b + c).
У подшипников качения различают следующие виды ради-
|
альных зазоров: |
|
|
– начальный, который имеет ме- |
|
|
сто в подшипнике до его монта- |
|
|
жа; |
|
|
– посадочный (монтажный), об- |
|
|
разующийся в подшипнике после |
|
|
посадки его на вал и в корпус; |
|
Рис. 6.2. Измерение величины радиального |
– рабочий, образующийся в рабо- |
|
тающем подшипнике под влияни- |
||
зазора в подшипниках качения |
ем нагрузки, упругих деформаций |
|
по методу фирмы SКF |
||
деталей подшипника, температу- |
||
|
||
|
ры и износа колец и тел качения. |
В справочниках и каталогах приводятся начальные зазоры подшипников качения основного ряда (с нормальными зазорами) и дополнительных рядов (с увеличенными и уменьшенными зазорами). В приложении 10 приведены посадочные и допустимые при износе радиальные зазоры некоторых типов подшипников основного ряда.
Наибольший допустимый при износе зазор принимают приблизительно равным 3-кратному наибольшему посадочному зазору. Если фактическая величина рабочего радиального зазора превышает допустимую (рекомендуемую заводом-изготовителем или приведенную в приложении 10), то возможность дальнейшей эксплуатации подшипника должна быть согласована с за- водом-изготовителем.
6.Проверить отсутствие проворота внутреннего кольца на валу. Для возможности такой проверки следует при ревизии подшипникового узла во время пусковой наладки нанести на внутреннее кольцо и вал совмещенные метки. Признаком проворота внутреннего кольца может служить также появление продуктов контактной коррозии между кольцом и валом.
7.Проверить наличие и величину зазоров между наружным кольцом
икорпусом. Наружное кольцо подшипника должно плотно прилегать к посадочному месту, зазор между кольцом и корпусом в нижней части не допускается. Между наружным кольцом и крышкой в верхней части должен быть зазор: в пределах 0,03–0,05 мм – для подшипников с малыми размерами; в пределах 0,04–0,285 мм – для крупных подшипников (соответствуют отклонению Н7 для отверстий корпуса). При зазорах, превышающих указанные, происходит интенсивный износ посадочного места в корпусе. При отрицательном зазоре (натяге) уменьшается радиальный зазор в подшипни-
47
ке, что может привести к заклиниванию тел качения и выходу подшипника из строя.
Подшипник со стороны соединительной муфты (радиальный) устанавливается в корпусе с осевыми зазорами между наружным кольцом и торцевыми крышками («плавающий» подшипник), чем обеспечиваются свободное тепловое расширение вала и компенсация неточности монтажа. Наружное кольцо подшипника со стороны свободного конца вала (радиально-упорный подшипник) фиксируется в корпусе, благодаря чему подшипник может воспринимать как радиальные, так и осевые нагрузки.
8.При пусковой наладке вновь смонтированных подъёмных машин измерить величину осевого разбега валов, опирающихся на подшипники качения. Осевой разбег валов обусловлен наличием осевых зазоров (осевой игры)
вподшипниках. Осевая игра – это полное возможное осевое перемещение колец относительно друг друга при условии постоянного совпадения осей обоих колец. Осевая игра имеет место во всех типах радиальных и радиальноупорных подшипников. Между радиальным зазором и осевой игрой существует зависимость, определяемая типом и конструктивными особенностями подшипника. У роликовых двухрядных конических и сферических подшипников осевую игру можно принимать равной половине рабочего радиального зазора в подшипнике.
Измерение осевого разбега валов произвести при помощи индикатора, установленного на жестком основании. Измерительный стержень индикатора упереть в торец вала. При помощи рычагов, домкратом или другими приспособлениямиотжатьвалвосевом направлении воднуи другуюсторону доупора.
Разность показаний индикатора определяет осевой разбег вала, величина которого должна быть не менее указанной в документации завода-изготовителя. При необходимости осевую игру подшипников и осевой разбег вала отрегулировать установкой прокладок и осевым перемещением наружных колец в корпусах подшипников согласнорекомендациямзавода-изготовителя.
9.Произвести закладку смазки в подшипник (при консистентной смазке) и собрать подшипниковый узел. Марка пластичной смазки, её количество и периодичность замены указывается в карте смазки подъемной машины (приложение 2). Смазкой заполняют все пространство между сепаратором и телами качения. Свободное пространство в корпусе подшипника заполнить смазкой наполовину. При закладке смазки должно быть исключено попадание в подшипник песка, окалины, металлической стружки и т.п.
10.Проверить работу подшипника под нагрузкой. Подшипниковый узел
можно считать исправным, если при работе подъёмной машины в нем слышен лишь легкий равномерный шелест, отсутствуют стук, толчки и чрезмерная вибрация, аустановившаясятемператураподшипниканепревышает80 °С.
48
6.3. Ревизия и наладка соединительных муфт
При ревизии и наладке соединительных муфт необходимо проверить следующее:
1. Состояние деталей:
–зубчатых муфт (рис. 6.3) – зубчатые обоймы и втулки, прокладки
иуплотнительные кольца. Проверить состояние рабочих поверхностей зубьев
ибоковой зазор в зубчатом соединении. Величина бокового зазора характеризует износ зубьев по толщине и не должна превышать предельно допустимых значений, указанных заводом-изготовителем. При отсутствии заводских данных определить предельно допустимый боковой зазор, исходя из предельно допустимого износа зубьев по толщине (не более 15 %) по формуле
S m (S1 S2 )0,85 , |
(6.4) |
где π = 3,14; т – нормальный модуль зубьев; S1 и S2 – толщина зуба на на-
чальной окружности соответственно втулки и обоймы.
Измерения производятся по постоянной хорде Sx, определяемой на расстоянии hx от головки зуба. Величины Sx и hx являются расчетными
Sx 1,387 |
m; |
(6.5) |
|
hx 0,748 m. |
|||
|
|||
Исходные данные для определения |
Sпред приведены в приложении 4, |
табл. 4.1;
–пружинных муфт – пружины, ступицы и пазы. У вновь монтируемых муфт проверить совпадение шагов пазов и пружин;
–пальцевых муфт – соединительные пальцы, упругие втулки. При износе пальцев, упругих втулок, отверстий для пальцев необходимо заменить муфту или ее элементы.
2. Посадку втулок на валы и затяжку шпонок. При слабой посадке и шаткости втулок муфту заменить. Кернить вал или насаживать втулку на прокладки недопустимо.
Обычно при наличии шпоночного соединения полумуфты насаживают на вал по прессовой посадке 2-го класса точности. Перед расточкой втулки необходимо микрометром измерить диаметр вала в нескольких сечениях. При расточке втулки надо обеспечивать требуемый натяг. Предельные отклонения отверстия втулки от диаметра вала приведены в табл. 6.3.
При прессовой посадке втулку насаживают с подогревом в масляной ванне или индукционным способом до температуры 200 °С, предварительно осмотрев шейку вала, зачистив ее и подогнав шпонки. На шейке вала не должно быть рисок, заусенцев и других дефектов. Втулку необходимо насадить так, чтобы торец вала был заподлицо с торцом втулки.
49
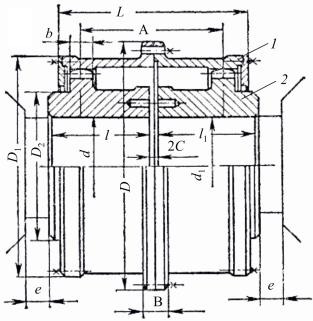
Таблица 6 . 3
Предельные отклонения отверстия втулки от диаметра вала
Диаметр вала, мм |
30–50 |
50–80 |
80–100 |
100–120 |
120–150 |
150–180 |
|
Предельные отклоне- |
-52 |
-65 |
-85 |
-95 |
-110 |
-125 |
|
ния отверстия втулки |
|||||||
-36 |
-45 |
-60 |
-70 |
-80 |
-95 |
||
от диаметра вала, мкм |
|||||||
|
|
|
|
|
|
||
Диаметр вала, мм |
180–220 |
220–260 |
260–310 |
310–360 |
360–440 |
440–500 |
|
Предельные отклоне- |
-145 |
-165 |
-195 |
-220 |
-260 |
-300 |
|
ния отверстия втулки |
|||||||
-115 |
-135 |
-160 |
-185 |
-220 |
-260 |
||
от диаметра вала, мкм |
Рис. 6.3. Зубчатая муфта: 1 – зубчатая обойма; 2 – зубчатая втулка
При бесшпоночном соединении втулок муфт с валами втулки заменяют в заводских условиях. Допуски на расточку втулок для обеспечения гарантированного натяга в этом случае определяют специальным расчетом.
3. Величину осевого зазора между торцами полумуфт. Осевой зазор должен быть в пределах значений, приведенных в приложении 4. Для пружинных муфт НКМЗ (рис. 6.4) осевой зазор, измеренный между кольцевыми выступами полумуфт, должен быть в пределах 5±1 мм, что соответствует зазору между полумуфтами по оси (2С) 15±1 мм. Для пальцевых муфт осевой зазор в зависимостиотнаружного диаметраполумуфт должен бытьвпределах:
50