
книги / Химия и технология полимерных материалов. Технология полимерных материалов
.pdf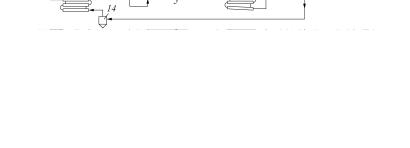
•смешение этилена с возвратным газом и кислородом;
•двухкаскадное сжатие газа;
•полимеризация этилена в конденсированной фазе;
•разделение ПЭВД и этилена, поступающего на рецикл;
•грануляция продукта.
Рис. 3.1. Технологическая схема процесса производства ПЭВД в газовой фазе: 1 – коллектор; 2 – смеситель этилена низкого давления; 3 – компрессор первого каскада; 4 – смеситель этилена высокого давления; 5 – компрессор второго каскада; 6 – трубчатый реактор; 7 – отделитель высокого давления; 8 – отделитель низкого давления; 9 – гранулирующий агрегат; 10 – вибросито; 11, 14 – циклонные сепараторы; 12, 15 – холодильники; 13, 16 – фильтры; 17 – компрессор предварительного сжатия
Для окрашивания, стабилизации и наполнения в ПЭВД вводят соответствующие добавки, послечегорасплавляюти гранулируют.
Этилен под давлением 0,8–1,1 МПа поступает в коллектор 1, затем в смеситель 2, где смешивается с возвратным этиленом низкого давления (НД). В поток вводят кислород, смесь поступает в трехступенчатый компрессор первого каскада 3, где сжимается до 25 МПа. После каждой ступени сжатия этилен охлаждается в холодильниках, очищается от смазки в сепараторах, затем поступает в смеситель 4, где смешивается с возвратным этиленом ВД из отделителя 7. Смесь направляется в двухступенчатый компрессор второго каскада 5, где сжимается до 245 МПа. После первой ступени этилен охлаждается в холодильнике, очищается
31
от смазки в сепараторах, после второй ступени при температуре около 70 °C без охлаждения поступает по трем вводам в трубчатый реактор 6 на полимеризацию.
Реактор состоит из трех зон, перед каждой зоной есть теплообменник для подогрева газа или реакционной смеси до 120–190 °C. В конце третьей зоны имеется холодильник для охлаждения реакционной массы до 200–250 °C (теплообменники и холодильник
на схеме не показаны). |
|
Условия полимеризации: |
|
температура, °C |
190–250 |
давление, МПа |
245 |
концентрация кислорода, % |
0,002–0,008 |
степень конверсии этилена за цикл, % |
26–30 |
суммарная степень конверсии этилена, % |
95–98 |
Из трубчатого реактора 6 смесь непрореагировавшего этилена с полимером через редукционный вентиль под давлением 24,5–26,3 МПа поступает в отделитель ВД, в котором за счет разности плотностей происходит разделение. Этилен из разделителя 7 направляется в циклонные сепараторы 11 и холодильники 12, где от этилена отделяются унесенные с ним частички полимера. После этого этилен охлаждается и направляется в смеситель 4 для соединения со свежим газом и возвращается в цикл.
Расплавленный полиэтилен из нижней части отделителя 7 направляется в отделитель низкого давления 8, в котором поддерживается давление 0,15–0,59 МПа. Расплав ПЭ, очищенный от остат- ковэтиленапри180–190 °C, поступаетвгранулирующиеагрегаты9.
Этилен из отделителя НД после очистки и охлаждения поступает в компрессор предварительного сжатия (0,9–1,7 МПа) 17, затем в коллектор 1 и возвращается в цикл.
В грануляторы 9 непрерывно подается стабилизирующая смесь (фенил-α-нафтилмаин с дифенил-п-фенилендиамином) и другие добавки. Полиэтилен, смешанный со стабилизаторами, подается на грануляцию. Для быстрого охлаждения гранул подается обессоленная вода. Гранулы ПЭ, охлажденные до 60–70 °C,
32
выносятся водой на вибросито 10, на которое подается теплый воздух для окончательной осушки.
ПЭВД выпускается в натуральном виде или окрашивается в различные цвета.
Производство ПЭВД в автоклаве с мешалкой. Технологиче-
ская схема производства ПЭВД в автоклаве не имеет принципиальных отличий от схемы с трубчатым реактором. Промышленные автоклавы получения ПЭВД имеют высоту около 6 м и диаметр 300 мм, емкость 0,5 м3. Производительность 15000 т/год.
Инициаторами полимеризации являются пероксид ди-трет- бутила, пероксид лаурила и трет-бутилпербензоат, которые поступают в систему в виде 4–25 % раствора в очищенном парафи-
новом масле. |
|
Условия полимеризации: |
|
температура, °C |
250–270 |
давление, МПа |
245 |
концентрация кислорода, % |
0,2–0,4 |
степень конверсии этилена за цикл, % |
15–19 |
Автоклав может быть разделен на 3 зоны, для каждой из которых задается своя температура и подается инициатор.
Для получения полимера с заданными свойствами требуется тщательно подбирать конфигурацию мешалки и частоту ее вращения, а также тип инициатора, его концентрацию и распределение инициатора по зонам.
Выделение тепла через стенку автоклава практически не происходит: процесс протекает в адиабатическом режиме. Теплота реакции расходуется на подогрев свежего этилена, который предварительно охлаждают до 25–40 °C. Степень превращения этилена определяется разницейтемператур на входе и выходеиз реактора.
Максимальная температура процесса (минимальная молекулярная масса) при рабочем давлении 196 МПа составляет 250 °C, максимальная степень конверсии в этом случае составляет 19 %. Снижение температуры и количества инициатора позволяет увеличить молекулярнуюмассу, ноприэтомпадаетстепеньконверсииэтилена.
33
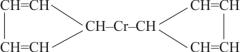
Увеличение частоты вращения мешалки с 1000 до 1500 об/мин позволяет повысить скорость подачи этилена в реактор на 20–30 % и увеличить тем самым производительность реактора, при этом повышается эффективность распределения инициатора в объеме реакционной массы.
В автоклаве более однородное распределение температур по объему, что обусловливает более узкое ММР в сравнении с трубчатым реактором.
Преимущества автоклавного процесса:
•более компактная аппаратура;
•более узкое ММР.
Преимущества трубчатого реактора:
•более эффективный теплообмен;
•более высокая степень конверсии этилена;
•кислород – дешевый инициатор;
•менее загрязненный полимер.
3.1.2. Производство полиэтилена низкого давления (высокой плотности)
ПЭНД получают в газовой и жидкой фазе при температуре 70–100 °C и давлении 0,3–2,5 МПа. Процесс проводят с применением катализаторов Циглера – Натта, хроморганических соединений, оксидов хрома. Молекулярная масса 80 000–500 000.
Получение ПЭНД в газовой фазе. Полимеризация этилена в газовой фазе проводится при давлении 2,2 МПа и температуре 100–105 °C в присутствии хроморганических катализаторов на силикатных носителях.
Наиболее распространенные каталитические системы:
• хромоцен – дициклопентадиенилхромат, нанесенный на активированный силикагель
34
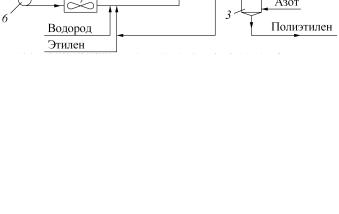
•силилхромат – бис(трифенилсилилокси)хромат [(C6H5)3SiO]2CrO2, восстановленный алюминийалкилом и нанесенный на активированный силикагель.
Активность катализатора зависит от чистоты хроморганических компонентов, удельной поверхности носителя и размеров пор (объем, диаметр), а также от условий подготовки носителя и приготовления катализаторного комплекса.
Основные стадии технологического процесса (рис. 3.2):
•очистка газов;
•приготовление катализатора;
•полимеризация этилена;
•компаундирование (стабилизация и грануляция);
•расфасовка и упаковка готового продукта.
Рис. 3.2. Технологическая схема производства ПЭНД в газовой фазе: 1 – реактор-полимеризатор; 2 – отделитель; 3 – емкость для продувки; 4 – емкость для катализатора; 5 – воздушный холодильник;
6 – циркуляционный компрессор; 7 – блок очистки этилена
Тонкая очистка этилена и других газов предотвращает отравление катализатора и способствует получению полимера с заданными свойствами.
35
Приготовление катализатора: активация силикатного носителя, получение хромоцена и силилхромата, нанесение 6 % хромоцена и 6 % силилхромата на активированный носитель. Процесс проводится в изопентане.
На носителе должен быть минимум гидроксильных групп для предотвращения образования циклических структур. Для это-
го силикагель дегидратируют при 600–800 °C. |
|
Условия процесса: |
|
температура, °C |
90–105 |
давление, МПа |
2,1–2,2 |
концентрация катализатора, % |
0,0004–0,0008 |
расход циркуляционного газа, м3/с |
7,5–7,8 |
высота псевдоожиженного слоя, м |
9 |
степень конверсииэтилена, % |
15–20 |
Реактор 1 – полая колонна высотой 25 м, нижний диаметр 4 м, верхний – 8 м, объем 140 м3. В нижней части перфорированная решетка для равномерного распределения потока этилена и создания кипящего слоя. Тепло реакции отводится за счет охлаждения циркулирующего газа на воздушном холодильнике 5. Циркуляция осуществляется с помощью одноступенчатого центробежного компрессора 6. Образующийся полиэтилен накапливается в нижней части реактора. Степень конверсии этилена составляет 97 %. Выгрузка получаемого полимера из реактора циклическая, время цикла 6 мин. Образовавшийся полиэтилен поступает в отделитель 2, где отделяется непрореагировавший этилен. Этилен направляют на очистку 7 и возвращают в цикл.
Полиэтилен поступает в емкость 3 для продувки азотом, после чего направляется на стабилизацию и грануляцию, затем на расфасовку и упаковку готового продукта. Плотность получаемого полиэтилена составляет 940–965 кг/м3, ММР может быть как узким, так и широким. Данный способ позволяет получать также сополимеры этилена с пропиленом и бутеном.
Производство ПЭНД в жидкой фазе. Полимеризация прово-
дится на катализаторах Циглера – Натта – смеси диэтилалюминий-
36

хлорида и тетрахлорида титана с соотношением 1:1 или 1:2. Катализаторный комплекс разрушается под действием кислорода и влаги, поэтому процесс проводят в атмосфере азота в среде обезвоженного растворителя. Диэтилалюминийхлорид легче поддается очистке, дешевле и менее огнеопасен, чем триэтилалюминий.
Стадии технологического процесса (рис. 3.3):
•приготовление катализаторного комплекса;
•полимеризация этилена;
•промывка, выделение и сушка ПЭ.
Полимеризация этилена, выделение и сушка полимера осуществляются непрерывно.
Рис. 3.3. Технологическая схема производства ПЭНД в жидкой фазе: 1 – весовой мерник диэтилалюминийхлорида; 2 – весовой мерник тетрахлорида титана; 3 – смеситель катализаторного комплекса; 4 – аппарат для разбавления комплекса; 5 – промежуточная емкость; 6 – полимеризатор; 7 – газодувка; 8 – центробежный насос; 9 – скруббер; 10 – холодильник; 11 – газоотделитель; 12 – сборник суспензии; 13 – аппарат для разложения катализатора; 14, 17 – центрифуги; 15 – аппарат для нейтрализации
маточника; 16 – промыватель; 18 – сушилка с кипящим слоем
Катализаторный комплекс готовят смешением растворов диэтилалюминийхлорида и хлорида титана в бензине, подаваемых из мерников 1 и 2 в смеситель 3 при температуре 25–50 °С. Получен-
37
ный комплекс выдерживают в течение 15 мин, затем в аппарате 4 разбавляют бензином до концентрации 1 кг/м3. Готовый катализаторный комплекс подается в промежуточную емкость 5, из которой его спомощью насосовнепрерывно подают вполимеризатор 6.
Условия полимеризации: |
|
температура, °С |
70–80 |
давление, МПа |
0,15–0,20 |
концентрация катализатора в бензине, кг/м3 |
~1 |
степень конверсии этилена, % |
~98 |
концентрация полиэтилена на выходе |
|
из аппарата, кг/м3 |
100 |
Повышение температуры приводит к разложению катализаторного комплекса, в результате чего резко снижается скорость процесса. Увеличение давления выше 0,3 МПа приводит к ускорению процесса, но ухудшает теплосъем, в результате требуется большее количество циркулирующего этилена для интенсификации охлаждения.
Реакция полимеризации экзотермична. Вследствие налипания полиэтилена отвод тепла через стенки реактора идет неэффективно. Дополнительно отвод тепла осуществляется циркуляцией парогазовой смеси этилена и бензина с помощью газодувки 7 и бензина с помощью насоса 8. Нагретая парогазовая смесь поступает в скруббер 9, где, контактируя со свежим бензином, охлаждается и очищается от частиц полимера, унесенных изполимеризатора.
Бензин из скруббера 9 подается через холодильник 10 на орошение скруббера и полимеризатора. Охлажденный этилен из скруббера через отделитель 11 направляется в полимеризатор. Количество свежего этилена контролируется давлением вполимеризаторе.
Суспензия полиэтилена в бензине поступает в сборник 12, а затем в аппарат с мешалкой 13, где происходит разложение остатков катализатора. Для этого суспензия обрабатывается смесью изопропилового спирта с бензином в соотношении 1:4 при 50–65 °С. На центрифуге непрерывного действия 14 происходит отделение полимера от маточного раствора. Маточник поступает в аппарат 15
38
на нейтрализацию 20%-ным раствором метилата натрия, а затем отправляется на регенерацию.
Полиэтилен в виде пасты из центрифуги 14 подают в промыватель 16, в котором для промывки используется нейтрализованный раствор из аппарата 15. Затем полимер промывают свежей спиртобензиновой смесью или водой на центрифуге 17. После центрифугирования полимер сушат горячим азотом в кипящем слое в аппарате непрерывного действия 18. Содержание влаги в полимере снижается до 0,2 %. Высушенный полимер отправляется на грануляцию и упаковку.
3.1.3. Полиэтилен среднего давления (высокой плотности)
Полиэтилен среднего давления получают полимеризацией в растворителе при 130–150 °C и 3,5–4 МПа в присутствии катализаторов (оксиды ванадия и хрома на алюмосиликатах).
Стадии процесса (рис. 3.4):
•подготовка сырья (этилен, катализатор, растворитель);
•полимеризация этилена;
•концентрирование раствора ПЭ;
•выделение и грануляция полимера;
•регенерация растворителя и катализатора.
Суспензия катализатора в бензине, приготовленная в аппарате 1, поступает в сборник 2, из которого через дозатор 3 подается в первый полимеризатор каскада 4. Туда же подаются этилен и бензин, предварительно нагретые в теплообменнике 7 до 120 °C. В полимеризаторе при 140–145 °C и давлении 4 МПа в присутствии катализатора протекает процесс полимеризации до 8%-ной концентрации полиэтилена в бензине. Раствор полиэтилена по обогреваемому трубопроводу подается во второй полимеризатор 5, туда же поступает смесь этилена с бензином через теплообменник 8, процесс протекает до достижения 14 % полимера в растворе. Далее смесь поступает в третий полимеризатор 6, где концен-
39
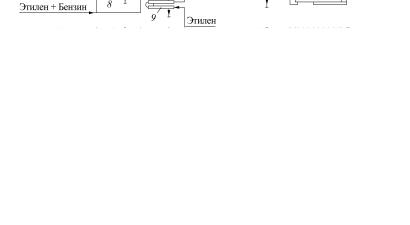
трация полиэтилена повышается до 18–20 %. Все три полимеризатора представляют собой автоклавы с мешалкой одинаковой конструкции (16 м3 каждый).
Рис. 3.4. Технологическая схема производства ПЭ среднего давления: 1 – аппарат для приготовления суспензии катализатора; 2 – сборник суспензии; 3 – дозатор; 4–6 – полимеризаторы; 7–9 – подогреватели; 10 – холодильник; 11 – фильтр; 12 – концентратор раствора ПЭ; 13, 14 – сепараторы; 15 – экструдер для выделения и грануляции ПЭ
Нормы загрузки, кг/ч: |
|
этилен на полимеризацию |
1000 |
катализатор |
1 |
этилен циркуляционный |
9000 |
бензин |
6000 |
Парогазовая часть из полимеризаторов поступает в конденсатор 10, где охлаждается водой до 60 °C. Затем смесь подается в сепаратор 13. Этилен и бензин разделяются и идут на очистку, после чего возвращаются в цикл. Раствор полимера отделяется от катализатора на фильтре 11 и поступает в концентратор 12, в котором путем дросселирования раствора с 4 до 1 МПа бензин испаряется и происходит концентрирование полиэтилена до 35 %.
40