
книги / Химия и технология полимерных материалов. Технология полимерных материалов
.pdfСмесь поступает в сепаратор-дегазатор 14, где отделяются пары бензина и этилена. После этого полимер подается в экструдер 15, где бензин выкипает, а полиэтилен поступает в гранулирующую часть, охлаждается и упаковывается.
Преимуществом данного варианта получения полиэтилена является то, что оксидные катализаторы менее токсичны в сравнении с металлорганическими, их легче регенерировать.
Недостатком процесса является необходимость дополнительных операций по выделению и очищению полимера, большой расходрастворителя и его регенерация– усложнение процесса.
Перерабатывают полиэтилен литьем под давлением, экструзией или прессованием.
Применение полиэтилена. Пленка ПЭВД используется для упаковки и в сельском хозяйстве. ПЭВД применяется для изготовления конструкционных деталей, домашнейутвари, игрушек, труб.
ПЭНД содержит остатки катализатора, поэтому менее устойчив к старению и деструкции, но проявляет лучшие механические свойства (прочность, жесткость). Применяется для производства труб, технических изделий, бутылей и канистр, электроизоляции и кабелей. ПЭНД методом газопламенного напыления наносят на металл для защиты от коррозии.
3.2. Полистирол
Полистирол (ПС) – термопластичный материал с высокими диэлектрическими показателями. Представляет собой химически стойкий, водостойкий, бесцветный, прозрачный материал, который растворяется в ароматических и хлорированных углеводородах, простых и сложных эфирах. Имеет низкую механическую прочность и невысокую теплостойкость, разрушается под действием кислорода при температуре выше 200 °C. Для улучшения механических свойств стирол сополимеризуют с другими виниловыми мономерами. Среди продуктов сополимеризации значение имеют привитые и блок-сополимеры стирола с каучуками,
41
обладающие повышенной ударной вязкостью, – ударопрочные полистиролы.
Впервые полистирол был получен в Германии в 1839 г., но его промышленное производство освоили в 1920 г.
ВСША во время Второй мировой войны начали развивать производство бутадиен-стирольного каучука.
ВСССР исследования синтеза и полимеризации стирола проводились в 1930–1940-х гг. Промышленное производство развернулось в послевоенные годы.
В50–60-х гг. XX в. разрабатывались процессы сополимеризации стирола с другими виниловыми мономерами, совмещения полистирола и его сополимеров с акрилонитрилом и каучуками. Получение изотактического стирола позволило значительно повысить механическую прочность и теплостойкость.
Сырье для производства. Стирол – бесцветная жидкость с характерным запахом, кипит при 145,2 °C (99 кПа). В промышленности получают дегидрированием этилбензола в присутствии катализаторов. Полученный стирол отделяют от побочных продуктов ректификацией.
Этилбензол (ЭБ) получают алкилированием бензола этиленом. Выделяют ЭБ также ректификацией. Важно удалить п-диэтил- бензол, который при дегидрировании образует п-дивинилбензол (ДБ). В присутствии ДБ при полимеризации стирола происходит сшивание линейных макромолекул с образованием неплавкого и нерастворимого продукта сетчатого строения, который не поддается переработке. Наличие ЭБ в продуктах также нежелательно, так как при его выделении из полистирола происходит растрескивание и потускнение последнего, при этом ухудшаются диэлектрические свойства материала.
Нежелательно образование полимера в стироле при хранении. Чтобы предотвратить полимеризацию, в стирол добавляют ингибиторы: гидрохинон или третбутилпирокатехин. Перед полимеризацией ингибиторы удаляют перегонкой мономера в вакууме или промывкой раствором щелочи с последующей тща-
42
тельной осушкой. Если полимеризацию проводят в суспензии или эмульсии, то осушку не проводят.
Стирол полимеризуют как по радикальному, так и по ионному механизму. По радикальному механизму образуется аморфный полимер с атактической структурой. Ионно-координационной полимеризацией получают аморфный или кристаллический (изотактический) полимер в зависимостиотприменяемого катализатора.
Аморфный ПС получают в массе, эмульсии, суспензии или в растворе; инициирование химическое или термическое.
Изотактический ПС получают на катализаторах Циглера – Натта. При нагревании изотактического ПС выше температуры плавления (около 250 °C) он необратимо переходит в аморфный.
В промышленности ПС получают в блоке, эмульсии или суспензии. Полимер, получаемый в растворе, имеет низкую молекулярную массу и его трудно выделять из реакционной смеси.
3.2.1. Получение полистирола в блоке
Полимеризация в блоке проводится в каскаде из 2 реакторов с перемешиванием (рис. 3.5).
Стадии процесса:
•подготовка стирола;
•полимеризация стирола в реакторах 1 и 2 ступеней;
•удаление и ректификация непрореагировавшего мономера;
•окрашивание расплава ПС;
•грануляция;
•расфасовка и упаковка.
Из емкости 1 стирол непрерывно подается в реактор первой ступени 2 – цилиндрический аппарат с коническим днищем 16 м3 и листовой мешалкой (30–90 об/мин). Процесс в реакторе 2 протекает при 110–130 °C до конверсии 32–45 % в зависимости от марки продукта. Съем тепла – за счет испарения стирола из реакционной массы. Реактор второй ступени аналогичен первому, но с ленточной мешалкой (2–8 об/мин). Обеспечивает эффективное переме-
43
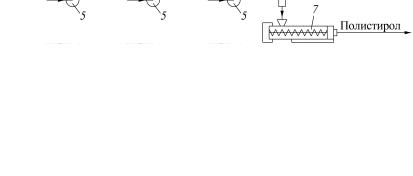
шивание высоковязких сред. Температура процесса 135–160 °C, степень конверсии 75–88 % в зависимости от марки продукта.
Раствор ПС в стироле насосом 5 подается в вакуум-камеру через трубу, обогреваемуюпаром с давлением неменее 2,25 МПа. При этом происходит дополимеризация до 90 %. В вакуум-камеру ПС поступает с температурой 180–200 °C, в трубчатке перегревателя вакуум-камеры ПС нагревается до 245 °C и поступает в полую камеру (10 м3) с остаточным давлением 2–2,6 кПа. Стирол из расплава испаряется, его остаточное содержание 0,1–0,3 %. Пары стирола поступают на регенерацию ивозвращаются в емкость 1.
Рис. 3.5. Технологическая схема производства блочного полистирола в каскаде аппаратов непрерывным способом: 1 – емкость для стирола; 2, 3 – каскад полимеризаторов; 4 – холодильники; 5 – насосы;
6 – вакуум-камера; 7 – экструдер с гранулятором
Расплав ПС из вакуум-камеры поступает в экструдер 7 и на грануляцию.
Оба реактора работают под вакуумом: 0,04–0,05 МПа первый и 0,02–0,03 МПа второй, избыточное тепло удаляется испарением части стирола.
По такой же схеме можно получать сополимеры стирола с каучуком, тогда происходит их предварительное смешение в емкости перед первым полимеризатором. В процессе получения блочного ПС образуются стирольные конденсаты, которые можно утилизиро-
44
вать двумя путями: очищать ректификацией до получения стирола стандартной чистоты (не менее 99,6 мас. %) или получать из них ПС несколько худшего качества для получения менее ответственных изделий. В промышленности реализуются обаварианта.
3.2.2. Получение полистирола в суспензии
Суспензионная полимеризация стирола имеет ряд преимуществ по сравнению с блочной:
•наличие водной дисперсионной среды облегчает теплоотвод – легчеуправлятьпроцессомирегулироватьрежимработыреактора;
•возможность варьирования в широких пределах условий процесса – получение большого ассортимента марок ПС;
•регулируемая молекулярная масса и узкое ММР – выше теплостойкость и ударная вязкость;
•ниже остаточное содержание стирола в полимере (до 0,1 %) – возможностьпроизводитьизделия дляпищевых продуктов.
Недостатки полимеризации в суспензии:
•многостадийность;
•большое количество сточных вод;
•сложность организации непрерывного процесса. Препятствиями для организации непрерывного процесса по-
лимеризации являются низкая устойчивость суспензии и налипание образующегося полимера на мешалку и стенки реактора. Процесс проводят в водной среде в присутствии инициаторов, нерастворимых в воде и растворимых в мономере. Стирол при перемешивании диспергируется в воде. Для повышения устойчивости суспензии в систему добавляют стабилизаторы. В качестве стабилизаторов применяют водорастворимые полимеры (поливиниловый спирт, содержащий 10–15 % неомыленных ацетатных групп, сополимер метакриловой кислоты и метилметакрилата, желатин, карбоксиметилцеллюлозу) или нерастворимые в воде неорганические соединения, образующие тонкодисперсные взвеси: гидроксиды металлов, каолин, бентонит, фосфаты, карбонаты. Полимерные стабилизаторы концентрируются на границе раздела
45
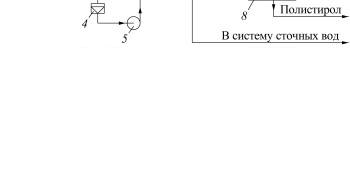
фаз и таким образом препятствуют агрегации частиц при перемешивании. Неорганические стабилизаторы наиболее эффективны, если смачиваются и водой, и стиролом (тонкая дисперсия гидроксида магния). Устойчивость суспензии зависит также от pH среды. Постоянное значение pH поддерживают добавками буферных растворов: фосфатов или карбонатов.
Полимеризация стирола в суспензии протекает по радикальному механизму.
Стадии процесса:
•подготовка сырья – очистка стирола от гидрохинона, приготовление раствора стабилизатора в воде, раствора инициатора в стироле;
•смешение компонентов, полимеризация;
•просев, промывка ПС и отжим на центрифуге;
•сушка, грануляция и упаковка готового ПС.
Схема получения суспензионного ПС представлена на рис. 3.6. Отжатый ПС с содержанием влаги около 4 % подается в сушилку 8. Сушилка барабанная в периодическом процессе, сушка в кипящем слое – в непрерывном.
Рис. 3.6. Технологическая схема производства суспензионного ПС: 1 – аппараты приготовления растворов инициаторов; 2 – емкость для стирола; 3 – реактор-полимеризатор; 4 – сито; 5 – насос;
6 – промежуточная емкость; 7 – центрифуга; 8 – сушилка
46
Растворы инициаторов из аппаратов 1 и стирол из емкости 2 подаются в реактор 3 на полимеризацию. Процесс проводится при перемешивании в течение 12–15 ч при 85–130 °C. После окончания процесса смесь охлаждают до 45–50 °C. При использовании гидроксида магния в качестве стабилизатора реакционную массу нейтрализуют серной кислотой. Суспензия полимера в воде перекачивается насосом 5 через сито 4 в промежуточную емкость 6, в которой ПС поддерживается во взвешенном состоянии мешалкой. Далее полимер поступает на центрифугу 7 для отделения от водной фазы. Начиная со стадии центрифугирования система может работать непрерывно.
3.2.3. Получение полистирола в эмульсии
При проведении полимеризации стирола в эмульсии дисперсионной средой является вода. В качестве эмульгаторов используют соли жирных кислот, а также сульфокислот парафинового и ароматического рядов. Инициаторы – водорастворимые пероксиды (пероксид водорода, персульфат калия или аммония) с концентрацией 0,25–0,5 % от массы стирола. Использование окисли- тельно-восстановительных инициирующих систем позволяет снизить температуру и повысить скорость реакции.
Полимеризация протекает по радикальному механизму. Молекулярную массу ПС регулируют добавлением агентов передачи цепи (полисульфиды, меркаптаны, ксантогенаты). Поверхностное натяжение на границе раздела фаз регулируют с помощью добавления алифатических спиртов (0,5 % от массы мономера).
Стабильность эмульсии и скорость процесса полимеризации зависят от показателя pH среды, который регулируют буферными растворами ацетатов, фосфатов и др.
Эмульсионный ПС имеет более высокую молекулярную массу, чем полимер, получаемый другими методами. Применяется в основном для получения пенополистирола. Кроме того, эмульсионная полимеризация используется для получения сополимеров стирола с другими мономерами.
47
В промышленности эмульсионный ПС получают в периодическом режиме. Перевод на непрерывную схему затруднен из-за большого количества сточных вод, загрязненных токсичными веществами, также из-за потерь пылевидного полистирола присушке.
Процесс включает в себя следующие стадии:
•подготовка сырья – очистка стирола от ингибитора, растворениеинициатора, эмульгатораиэлектролитадлякоагуляциивводе;
•полимеризация стирола;
•коагуляция ПС, промывка и центрифугирование полимера;
•сушка, просев и грануляция ПС;
•расфасовка и упаковка готового продукта.
Ингибитор удаляют промывкой раствором 5–10 % щелочи и последующей отмывкой от щелочи водой. Для приготовления эмульсии нужна деминерализованная вода, поскольку соли, содержащиеся в воде, снижают стабильность эмульсии и загрязняют полимер, ухудшая его диэлектрические свойства. Для коагуляции используют алюмокалиевые квасцы.
Типичная рецептура эмульсионного полистирола (мас. ч.):
стирол |
100 |
вода |
200–300 |
эмульгатор (олеат натрия) |
1–3 |
едкий натр |
0,2 |
инициатор |
0,25–0,50 |
Технологическая схема получения эмульсионного полистирола представлена на рис. 3.7. В полимеризатор 3, снабженный рубашкой, мешалкой и обратным холодильником, подают деминерализованную воду, нагретую до 50 °C, и при перемешивании – эмульгатор, затем в реактор поступает стирол. При перемешивании вводят раствор инициатора в воде. Смесь нагревают до 70–75 °C. После этого температура повышается до 80–85 °C за счет тепла реакции. Процесс проводят5–6 ч, содержание остаточного мономера – не более 0,5 %. Полученный продукт представляет собой тонкодисперсную суспензию, которую медленной струей из емкости 5 подают в осадитель 6, где находится раствор коагулянта. С его помощью
48
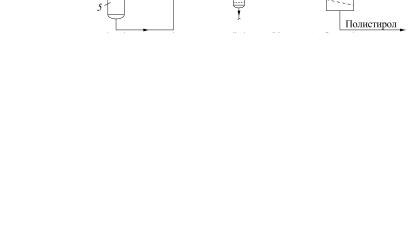
доводят pH среды до 5,5–6. Смесь продувают острым паром, нагревают до 75–85 °C, перемешивают в течение 1,5–2 ч, добавляют аммиачную воду, отделяют маточный раствор и промывают полимер горячей водой в аппарате 7. После промывки полимер отжимают на центрифуге и направляют в сушилку 10, остаточная влажность не должна превышать 0,5 %. Используют сушилки с кипящим слоем или пневмосушилки (труба с винтовой насадкой). Высушенный ПС просеиваютна виброситеи передаютнаупаковку.
Рис. 3.7. Технологическая схема производства эмульсионного ПС: 1 – хранилище стирола; 2 – мерник; 3 – реактор; 4 – холодильник; 5 – промежуточнаяемкость; 6 – осадитель; 7 – промывательПС; 8 – ловушка; 9 – центрифугаНОГШ; 10 – сушилкаскипящимслоем; 11 – вибросито
Для производства пенополистирола полученный ПС после просеивания выпускают как товарный продукт в виде тонкодисперсного порошка. В остальных случаях ПС гранулируют. При грануляции происходит частичная деструкция полимера, снижается его молекулярная масса – это облегчает дальнейшую переработку полимера литьем под давлением. Эмульсионный ПС имеет молекулярную массу около 106 и очень низкую текучесть при литье под давлением.
49
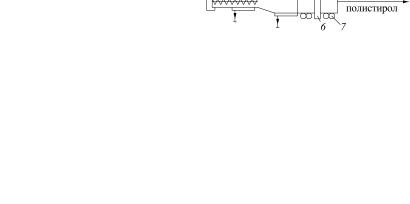
В производстве эмульсионного ПС непрерывным способом используется каскад аппаратов смешения (эмалированные аппараты с рубашками и мешалками).
3.2.4. Получение пенополистирола
Пенополистирол используется как тепло- и звукоизоляционный материал в строительстве, холодильной технике, транспорте, мебельной промышленности. Порофор – нитрил азобисизомасляной кислоты – одновременно является инициатором и вспенивающим агентом.
Рис. 3.8. Технологическая схема производства пенополистирола: 1 – смесители; 2 – расходная емкость; 3 – насос; 4 – полимеризатор; 5 – червячный пресс с расширяющимся мундштуком;
6 – нож для резки изделий; 7 – транспортер
Из смесителей 1 (рис. 3.8) раствор порофора в стироле подается в расходную емкость 2, где подогревается до 60–75 °C, затем насосом 3 нагнетается в полимеризатор 4. Полимеризатор – аппарат трубчатого типа, разделенный на секции, температура в нем повышается с 80 до 100 °C от секции к секции. Реакционная смесь из реактора поступает на червячный пресс 5, где нагревается до 120–140 °С, в результате чего происходит полное разложе-
50