
книги / Химия и технология полимерных материалов. Технология полимерных материалов
.pdfрода в ортоили параположениях. При действии на такие смолы формальдегидом (параформ, α- или β-полиоксиметилен) или гексаметилентетрамином в присутствии основного катализатора можно получать резолы или непосредственно неплавкий и нерастворимый материал – резит.
Новолаки, полученные из бифункциональных фенолов, при обработке формальдегидом не переходят в нерастворимое и неплавкое состояние, но переходят при нагревании выше 180 °C.
Аналогичная картина наблюдается при 250–280 °C для новолаков, полученных конденсацией 1 моль фенола и 0,8 моль формальдегида, за счет активации атомов водорода в метаположении или взаимодействия гидроксильных групп фенолов с образованием эфирных связей.
Поликонденсация в щелочной среде. В щелочной среде также сначала образуются о- и п-гидроксиметилфенолы, затем 2,4- и 2,6- дигидроксидиметилфенолы, далее тригидроксиметилфенолы. Преимущественно участвуют в поликонденсации парагидроксиметильные группы и незамещенные параположения фенольных ядер. Наиболее реакционно-способный – 2,6-дигидроксидиметилфенол, который быстро реагирует с формальдегидом с образованием тригидроксиметилфенола. В щелочной среде гидроксиметилфенолы весьма устойчивы, до 60 °C они являются практически единственными продуктами реакции. С ростом температуры они начинают взаимодействовать между собой исфенолом.
Резолы представляют собой смесь линейных и разветвленных продуктов с общей формулой
H–[–C6H2(OH)(CH2OH)CH2–]m–[–C6H3(OH)CH2–]n–OH.
Молекулярная масса резолов ниже, чем новолаков, поскольку реакцию проводят быстрее для предотвращения гелеобразования. При нагревании резолы отверждаются, образуя полимеры пространственного строения. Процесс отверждения резольных олигомеров делят на три стадии: А, В, С.
71
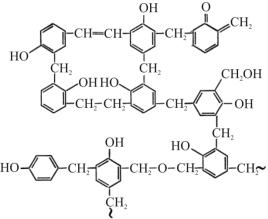
Стадия А (также называется резольной). Олигомер аналогичен новолачному – плавится и растворяется в щелочах, спирте, ацетоне. Представляет собой нестойкий продукт, который при нагревании переходит в нерастворимое и неплавкое состояние.
Встадии B полимер, называемый резитолом, частично растворяется в спирте и ацетоне, не плавится, но размягчается (при нагревании переходит в эластичное каучукоподобное состояние)
инабухает в растворителях.
Встадии C полимер, называемый резитом, представляет собой неплавкий и нерастворимый продукт, который не размягчается при нагревании и не набухает в растворителях. В стадии резита полимер имеет сложное пространственное строение:
4.2. Технология получения фенолоформальдегидных смол
4.2.1. Производство новолачных олигомеров
Получаюткак непрерывным, таки периодическимспособами. Периодический режим проводят по схеме, когда синтез олигомера и его осушка проводятся в одном аппарате. Процесс состоит из стадий подготовки и загрузки сырья, поликонденсации, сушки оли-
гомера, слива, охлаждения и измельчения готового продукта.
72
Поскольку при нормальных условиях фенол существует в твердом агрегатном состоянии, необходим обогрев коммуникаций для перекачки его расплава, особенно в зимнее время, трубопроводы должны быть тщательно изолированы. Для предотвращения затвердевания фенола готовят его смесь с водным раствором формальдегида в определенном соотношении.
Очень важна правильная дозировка компонентов, чтобы предотвратить образование резола вместо новолака. Резол твердеет в аппарате, что затрудняет его извлечение и делает невозможной переработку. Для новолачных смол берут 100 мас. ч. фенола на 25– 27,5 мас. ч. формальдегида (1:0,79–0,86 мол.). Для некоторых марок могут брать практически эквимольное соотношение 1:0,97. Катализатор– минеральные илиорганическиекислоты– 0,2–1,5 мас. ч.
Соляная кислота является активным катализатором, поскольку скорость поликонденсации пропорциональна концентрации ионов Н+, рН 1,5–1,8.
Реакция поликонденсации экзотермична, при высокой скорости смесь в аппарате кипит и может произойти выброс, поэтому соляную кислоту вводят в два-три приема, коэффициент заполнения аппарата получается ниже.
Щавелевая кислота является более слабой и хуже диссоциирует, что позволяет регулировать скорость поликонденсации в широких пределах. В присутствии щавелевой кислоты скорость реакции ниже, поэтому допускается большее заполнение аппаратов, что компенсирует увеличение времени реакции.
Соляную кислоту легче удалять из продукта, но она значительно более коррозионно-активная. Щавелевую кислоту сложнее удалять, что ухудшает диэлектрические свойства продукта, но сам продукт получается более светлый и светостойкий.
Принципиальная технологическая схема данного варианта получения новолачных олигомеров приведена на рис. 4.1.
Компоненты загружают в реактор 7 и нагревают до 55–65 °C при интенсивном перемешивании. В дальнейшем температура повышается за счет тепла реакции до 90–98 °C. Холодильник 8
73
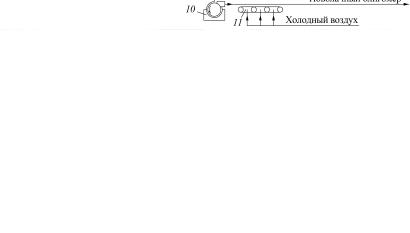
работает как обратный, возвращая сырье в реактор 7. По мере увеличения степени конденсации реакционная масса разделяется на два слоя: олигомерный и водный, содержащий непрореагировавшие компоненты и дигидроксиметилфенолы. Процесс поликондесации протекает в обеих фазах, концентрация фенола выше в олигомерной среде, формальдегида – в водной. Выход новолака и его средняя молекулярная масса напрямую зависят от времени реакции. Первая стадия поликонденсации заканчивается, когда концентрации фенола и формальдегида прекращают снижаться.
Рис. 4.1. Схема производства новолачных олигомеров периодическим способом: 1 – мерники сырьевых компонентов; 2 – сетчатый фильтр; 3 – плавитель олеиновой кислоты; 4 – напорная емкость олеиновой кислоты; 5 – напорная емкость соляной кислоты; 6 – аппарат для растворения щавелевой кислоты; 7 – реактор поликонденсации и сушки; 8 – холодильник; 9 – сборник конденсационной воды; 10 – охлаждающий
барабан; 11 – транспортер
Процесс сушки под вакуумом начинается путем переключения выхода с холодильника 8 на емкость-сборник 9. В процессе сушки удаляются формальдегид, часть фенола, летучие побочные продукты, летучий катализатор. За счет их испарения температура снижается до 85–90 °C. Поликонденсация продолжается в про-
74
цессе сушки, увеличивается вязкость продукта, снижается содержание свободного фенола в нем. Процесс сушки заканчивают при 120–130 °C. После окончания сушки в олигомер добавляют смазывающие вещества, например, олеиновую кислоту.
Готовую смолу в расплавленном виде выгружают с реактора на охлаждающий барабан 10, где при контакте с водой в ванне аппарата она затвердевает. Слой затвердевшей смолы срезается с барабана и сушится на транспортере 11.
Непрерывный режим в промышленности проводится в колонном аппарате, состоящем из нескольких секций (3–4), каждая из которых – реактор смешения. Движущая сила процесса – разница концентраций исходных компонентов в смеси, поступающей в аппарат и находящейся в нем. Эта разность выравнивается от первой секции к последней.
Многосекционный аппарат позволяет более полно использовать реагенты и интенсифицировать процесс при высокой стабильности продукции. Схема непрерывного получения новолачных олигомеров представлена на рис. 4.2.
Фенол, раствор формальдегида и катализатор с помощью мерников 1 и дозировочного насоса 2 подаются в рекуперационный теплообменник 3. Разогретая смесь реагентов поступает в реактор 4. Образующиеся пары поступают в рекуперационный теплообменник 3 и конденсируются, отдавая тепло на нагрев исходной смеси. Температура в реакторе 94–98 °C. Реакционная смесь перетекает из одной секции в другую по внешним трубопроводам, соединяющим верхнюю часть предыдущей секции с нижней частью последующей. Перемешивание реакционной массы происходит за счет кипения, которое поддерживается паром в рубашке аппарата. Разделение смеси на водный и олигомерный слои происходит в отстойнике непрерывного действия 5, откуда олигомер насосом 6 подается на выпаривание в теплообменник 7,
аводный слой отводится в систему сточных вод. Далее смесь поступает в один из стандартизаторов 8, где отделяются пары летучих соединений. Пары летучих конденсируются в холодильнике 9,
аконденсат, содержащий около 30 % фенола и 2,5 % формальде-
75
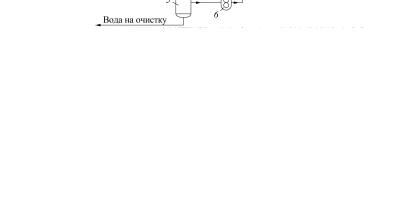
гида, собирается в емкости 10 и возвращается в процесс поликонденсации. Расплав олигомеров из стадартизатора 8 направляется на вращающийся барабан 11, на поверхности которого охлаждается в виде тонкого слоя. Если требуется гранулированный материал, вместо барабана устанавливают гранулятор.
Рис. 4.2. Схема производства новолачных фенолоформальдегидных олигомеров непрерывным способом: 1 – мерники сырьевых компонентов;
2 |
– дозировочный насос; 3 – рекуперационный теплообменник; |
|
4 |
– |
реактор; 5 – отстойник; 6 – насос; 7 – выпарной аппарат; |
8 |
– |
стандартизатор; 9 – холодильник-конденсатор; 10 – сборник |
|
|
конденсата; 11 – охлаждающий барабан |
Новолачные олигомеры – твердые термопластичные продукты от светлодо темно-коричневого цвета. Хорошо растворяются
вметаноле и этаноле, ацетоне, не растворяются в ароматике. Не отверждаются при длительном хранении и нагревании 180 °C.
Новолачные олигомеры используются в качестве связующих
впроизводстве пресс-порошков и абразивных изделий, при изготовлении оболочковых форм для литья металлов. Кроме того, новолачные олигомеры можно превращать в резольные.
Достоинством новолаков является простота технологических процессов их производства.
76
4.2.2. Производство резольных олигомеров
Резольные олигомеры получают поликонденсацией фенола с избытком формальдегида в присутствии щелочных катализаторов (гидроксид бария, аммиачная вода, едкий натр).
В зависимости от назначения резольные олигомеры получают жидкими или твердыми (т.н. сухие резолы). Твердые резолы лучше сохраняют свои свойства при хранении, содержат меньше свободного фенола, проявляют лучшие диэлектрические свойства и химическую стойкость. Твердые резолы содержат больше фенола, чем твердые новолаки, резолы ниже плавятся.
Технологический процесс получения резолов периодическим способом аналогичен процессу производства новолаков и состоит из тех же операций. Процесс сложнее осуществлять, так как резолы склонны к переходу в резитолы. При производстве резолов необходимо строго контролировать время реакции поликонденсации. Увеличение продолжительности процесса приводит к повышению вязкости реакционной среды и снижению времени отверждения. При получении резолов тепловой эффект ниже, чем при производстве новолаков, поэтому нагревание ведут до 75–80 °C. Расслоение смеси происходит хуже, так как начальные продукты конденсации лучше растворяются в реакционной смеси и более гидрофильны. Процесс сушки резолов также более сложен в осуществлении – резолы при нагревании могут образовывать твердые неплавкие и нерастворимые продукты в реакторе. Это приводит к потере готового продукта и длительному простою реактора при его очистке. Окончание процесса сушки определяется временем, когда 1 г олигомера при 150 °C на полимеризационной плитке переходит в неплавкое и нерастворимое состояние – условная скорость полимеризации (не менее 50 с для сухих резолов).
Образование полимера пространственной структуры из олигомера сопровождается сильным разогревом реакционной массы, что, в свою очередь, приводит к увеличению скорости образования сетчатого полимера. По достижении необходимой степени поликонденсации требуется быстрое охлаждение продукта в вагонах-
77
холодильниках, обеспечивающих охлаждение олигомеров в тонком слое. Вагон-холодильник – тележка с установленными вертикально металлическими листами, которые охлаждаются водой.
Врезольных олигомерах процессы конденсации могут протекать при комнатной температуре, поэтому для сухих резолов требуютсяособыеусловияхранения (температура ипродолжительность).
При получении лаковых олигомеров после завершения сушки продукт, содержащий 5–17 % влаги, растворяют в спирте. Растворение проводят при перемешивании до образования гомогенной системы, который охлаждают до 30–40 °C и сливают из реактора.
Для приготовления пенопластов используют жидкие резольные олигомеры, которые после сушки нейтрализуют борной кислотой. По окончании сушки в такой олигомер вводят пасту, состоящую из ПАВ и алюминиевой пудры (100:30 мас. ч.).
Впроизводстве композиционных материалов применяются эмульсионные резольные олигомеры. Особенности их получения – конденсация при меньшей температуре (85 °C), после которой олигомер частично подсушивают или отстаивают. Влагосодержание 14–18 % после сушки, 30 % после отстаивания. При содержании влаги ниже 18 % олигомеры представляют собой прозрачные жидкости, хорошо растворимые в спиртах и ацетоне.
Такие олигомеры содержат до 20 % свободного фенола. При нагревании они длительное время сохраняют плавкость и растворимость в отличие от обычных резолов. Это позволяет получать более однородные композиции.
Фенолоспирты – смесь гидроксиметильных производных фенола в сочетании с двух- и трехъядерными гидроксиметилфенолами. Используются в виде 50%-х растворов в спирте при производстве теплоизоляционных материалов, армированных минеральной ватой и стекловолокном. Получают их непрерывным методом в 8-секционной колонне, в которой реакционную массу перемешивают сжатым воздухом.
Резольные олигомеры – твердые или жидкие продукты, при нагревании или под действием кислот при комнатной температуре
78
способные образовывать полимеры пространственной структуры. Растворимость зависит от молекулярной массы. Полимеры полностью нерастворимы. Цвет олигомеров зависит от катализатора поликонденсации: светло-желтый в случае аммиака или аминов до темно-коричневого в присутствии щелочей. В отличие от новолаков свойства резолов широко различаются от условий получения.
Резольные полимеры (резиты) обладают более высокими диэлектрическими показателями, химической и водостойкостью в сравнении с отвержденными новолаками. В чистом виде используются редко. Высокие внутренние напряжения приводят к растрескиванию, быстро меняется окраска. Термообработка резитов при температуре выше 250 °C сопровождается их деструкцией с превращением в высокотермостойкий механически прочный углеродистый остаток (кокс).
В промышленности также выпускают новолачные и резольные полимеры на основе крезолов и ксиленолов. Технология их получения практически не отличается от получения ФФАС.
Новолачные олигомеры также производят путем поликонденсации фенола с фурфуролом, которые затем применяются в производстве прессовочных порошков. Кроме того, получают олигомер смешанного строения путем поликонденсации фенола с фурфуролом в кислой среде, затем с формальдегидом в щелочной.
Для нужд лакокрасочной промышленности производят маслорастворимые фенолоформальдегидные полимеры на основе паразамещенных алкил- и арилфенолов, например паратретбутилфенола.
Для улучшения ряда характеристик ФФАС совмещают с другими полимерами: полиамидами, ПВХ, каучуками, эпоксидными олигомерами.
Фенолоформальдегидные олигомеры применяются в производстве композиционных материалов: пресс-порошков, волокнитов, слоистых пластиков.
79
СПИСОК РЕКОМЕНДУЕМОЙ ЛИТЕРАТУРЫ
1.Сутягин В.М., Ляпков А.А. Общая химическая технология. – Томск: Изд-во Томск. политехн. ун-та, 2010. – 208 с.
2.Технология пластических масс: учеб. / под ред. В.В. Коршака. – 3-е изд., перераб. и доп. – М.: Химия, 1985. – 560 с.
3.Савельянов В.П. Общая химическая технология полиме-
ров. – М.: Академия, 2007. – 335 с.
4.Тагер А.А. Физико-химия полимеров. – Изд. 4-е, перераб.
идоп. – М.: Научный мир, 2007. – 576 с.
5.Семчиков Ю.Д. Высокомолекулярные соединения. – М.: Academia, 2003. – 268 с.
6.Говарикер В.Р., Висванатхан Н.В., Шридхар Дж. Полимеры: пер. с англ. – М.: Наука, 1990. – 396 с.
7.Кузнецов Е.В., Прохорова И.П., Файзуллина Д.А. Альбом технологических схем производства полимеров и пластических масс на их основе. – М.: Химия, 1976. – 108 с.
80