
книги / Химия и технология полимерных материалов. Технология полимерных материалов
.pdfние порофора и равномерное распределение в материале. Червячный пресс регулирует подачу материала в расширяющийся мундштук, где происходит вспенивание. Мундштуки различной формы позволяют получать сплошные или полые изделия.
Таким образом получают пенополистирол ПС-А мелкопористой замкнуто-ячеистой структуры. При добавлении к нему антипиренов можно получать негорючий пенополистирол. По этой же схеме можно получать пенополистирол марки ПСВ (беспрессовый). Для этого на червячный пресс устанавливают головку с отверстиями, оформляющую тонкие нити ПС, которые охлаждаются и дробятся на гранулы.
Пенополистирол устойчив к действию влаги, не гниет, стоек к действию грибков и бактерий, устойчив к минеральным средам, кроме азотной концентрированной кислоты.
Свойства полистирола. Полистирол – твердый аморфный продукт с плотностью 1050–1080 кг/м3. Молекулярная масса в зависимости от способа получения 50–300 тысяч, за исключением эмульсионного ПС. На свойства ПС влияет его полидисперсность, которая наиболее значительна для блочного. Присутствие низкомолекулярных фракций уменьшает теплостойкость и механическую прочность ПС.
На катализаторах Циглера – Натта образуется изотактический кристаллический продукт, который отличается от аморфного повышенной температурой плавления (230–240 °C) и лучшими механическими характеристиками. Изотактический стирол труднее перерабатывается в изделия, поэтому его не производят в промышленном масштабе.
ПС обладает высокой водостойкостью, хорошими оптическими свойствами. Устойчив к действию кислот (неокисляющих) и щелочей, спиртов и солей. Растворяется в четыреххлористом углероде, бензоле, нестоек к действию простых и сложных эфиров, углеводородов и их хлорпроизводных. ПС легко окисляется, сульфируется, галогенируется, нитруется. Является хорошим диэлектриком вне зависимости от влажности среды и температуры
51
(–80…+90 °C). Диэлектрические свойства эмульсионного полистирола ниже, чем блочного или суспензионного.
Перерабатывается полистирол, в основном, литьем под давлением. При экструзии пленок и нитей ПС происходит ориентация макромолекул, что способствует повышению прочности и увеличению гибкости.
Применяется ПС как электроизоляционный материал в приборостроительной и кабельной промышленности. Как конструкционный материал полистирол используют для изготовления деталей, не работающих под большими механическими нагрузками: панелей, облицовочных плиток, дверных ручек и др. Блочный ПС имеет высокий показатель преломления, пропускает 90 % видимого излучения и используется в изготовлении оптических стекол.
Полистирол используют при производстве галантерейных изделий, посуды, тары, игрушек. Для пищевой посуды подходит только суспензионный ПС, таккак вблочном вышеостатокмономера.
На основе полистирола производят лаки для электроизоляционных и антикоррозионных целей.
Впромышленности также производят полимерные материалы на основе аналогов толуола. В качестве мономеров может применяться винилтолуол и галогенстиролы. Поливинилтолуол находит применение в радио- и электротехнике в качестве теплостойкого диэлектрика.
Вкачестве мономеров для полигалогенстиролов наиболее часто используют п-хлорстирол и 2,5-дихлорстирол. Галогенсодержащие полистиролы обладают высокими диэлектрическими показателями и более высокой термической стойкостью в сравнении с незамещенным полистиролом.
Полифторстиролы также являются хорошими диэлектриками и при этом обладают высокой химической и термической устойчивостью, но ввиду сложности их производства полифторстиролы не получили широкого применения.
52
3.2.5. Сополимеры стирола
Сополимеризация стирола с различными мономерами реализуется довольно легко. В результате можно получать материалы с ценными свойствами, отличными от гомополимеров. Сополимеризация позволяет изменить растворимость материала, термическую стойкость, адгезионные свойства, механическую прочность и др. Сополимеризацией мономеров, содержащих две и более двойных связей, возможно получать жесткие неплавкие и нерастворимые полимеры пространственного строения.
В промышленности стирол сополимеризуют с бутадиеном, акрилонитрилом, α-метилстиролом, дивинилбензолом. В последнем случае получают сополимер пространственного строения, который применяютдля производства ионообменныхматериалов.
Недостатком полистирола является его недостаточная прочность, особенно ударная вязкость. Для повышения механических характеристик полистирол модифицируют путем получения привитых или блок-сополимеров стирола с каучуком.
Ударопрочный полистирол. Ударопрочный полистирол получают привитой сополимеризацией стирола к каучуку, латексным методом или механическим. Привитая сополимеризация является наиболее эффективным способом, ее проводят в блоке или суспензии, также возможен блочно-суспензионный способ.
При сополимеризации используется химическое инициирование (пероксид бензоила). При инициировании происходит отрыв атома водорода в α-положении относительно двойной связи с образованиемрадикала в цепи, кэтому центру прививается полистирол.
По достижении 60–70 % степени конверсии начинаются процессы гомополимеризации стирола и образование гельфракции, содержание которой составляет 14–20 % от количества привитого сополимера. Полученный продукт представляет собой смесь привитого сополимера,
С увеличением содержания каучука возрастает ударная вязкость материала, но снижается прочность на изгиб и растяжение,
53
уменьшается твердость, теплостойкость и стойкость к старению.
Вбольшинстве сортов ударопрочного полистирола содержание каучука не превышает 10 %.
Ударопрочный полистирол растворяется в ароматических углеводородах, в хлорированных углеводородах, простых и сложных эфирах, при нагревании частично деполимеризуется. Перерабатывают его литьем под давлением, экструзией, ваку- ум-формованием.
Применяется в радиотехнике, автомобилестроении, в производстве бытовых приборов, игрушек, в виде пленки используется для упаковки пищевых продуктов.
АБС-пластики. АБС-пластики представляют собой сополимер акрилонитрила (5–35 %), бутадиена (10–40 %) и стирола (25–80 %).
Всравнении с ударопрочным полистиролом АБС-пластики обладают более высокими показателями механической прочности, теплостойкостью ихимическойстойкостью.
Существует три способа получения АБС-пластиков: привитая сополимеризация, смешение латексов каучука и сополимера, механохимический способ. Для получения некоторых марок АБС-пластиков помимо стирола и акрилонитрила применяют метилметакрилат и α-метилстирол, вместо бутадиенового применяют бутадиен-стирольный каучук.
Получают АБС-пластики в эмульсии (периодически или непрерывно) или в блоке непрерывным способом. В производстве АБС-пластиков эмульсионным способом процесс включает стадию водоподготовки, а кроме того, требуется очистка образующихся сточных вод от токсичных компонентов. В связи с этим более распространенной является непрерывная блочная сополимеризация до неполной конверсии мономеров.
Применяются АБС-пластики в производстве труб для нефтяной промышленности, гальванических ванн, санитарнотехнических изделий; используются для изготовления деталей автомобилей, деталей и корпусов радио- и электротехнических приборов.
54
3.3. Производство поливинилхлорида
Поливинилхлорид (ПВХ) представляет собой термопластичный полимер с температурой стеклования 70–80 °С. Степень полимеризации ПВХ, получаемого в промышленности, находится в интервале 400–1500.
В1835 г. Реньо получил винилхлорид присоединением хлороводорода к ацетилену, им же обнаружена возможность газообразного винихлорида превращаться в порошок под действием света.
В1872 г. реакция полимеризации была исследована более подробно Бауманом. Через 40 лет Остромысленский и Клатте предложили промышленный способ получения ПВХ с помощью фотополимеризации. Позже были разработаны методы получения ПВХ по радикальному механизму с применением химического инициирования.
В1930 г. впервые был осуществлен промышленный синтез ПВХ в эмульсии. В дальнейшем были исследованы и освоены промышленные способы получения ПВХ сначала в суспензии, а затем и в блоке.
Сырьем для получения ПВХ служит винилхлорид – бесцветный газ с температурой кипения –13,9 °С, ядовит. Существует несколько промышленных способов получения винилхлорида: присоединение хлороводорода к ацетилену, присоединение хлора
кэтилену с последующим отщеплением HCl, окислительное хлорирование этилена хлороводородом.
Перед полимеризацией винилхлорид необходимо тщательно очищать от примесей, степень его чистоты не должна быть ниже 99,9 %.
ПВХ образуется при радикальной полимеризации винилхлорида в массе, эмульсии, суспензии или растворе. В промышленности наиболее распространенным является процесс получения ПВХ в суспензии. В качестве инициаторов используют пероксиды и азосоединения.
Процесс полимеризации проводят при температуре не выше 70–75 °С, поскольку при 75 °С происходит частичное дегидро-
55
хлорирование полимера. При этом образуются малоактивные аллильные радикалы, тормозящие процесс полимеризации:
~СН2–СНСl–СН2–СНСl–СН=СН~ + ~С•Н2–СНСl → → ~СН2–СНСl–СН2–С•Н–СН=СН~+~СН2–СН2Сl
Высокая активность радикалов винилхлорида способствует их взаимодействию с различными примесями, содержащимися в мономере. Например, ацетилен, который может содержаться в винилхлориде в качестве примеси, может выступать в роли агента передачи цепи, приводя к образованию малоактивных радикалов и замедляя полимеризацию. Другие примеси могут также вызывать передачу или обрыв цепи.
С другой стороны, реакция передачи цепи может использоваться для регулирования молекулярной массы полимера. В реакционную среду вводят специальные вещества – регуляторы, которые способны участвовать в передаче цепи. Регуляторы подбирают таким образом, чтобы образующиеся при передаче цепи радикалы проявляли достаточную активность, иначе будет иметь место ингибирование процесса полимеризации.
Присутствие кислорода в системе негативно сказывается на скорости процесса и свойствах образующегося полимера, поскольку обусловливает индукционный период реакции полимеризации, уменьшение скорости процесса, снижение молекулярной массы полимера, способствует появлению разветвленности молекул ПВХ, ухудшению его термической стабильности и совместимости с пластификаторами. Содержание кислорода в системе не должно превышать 0,0005–0,001 % от содержания мономера.
При полимеризации в массе происходит выпадение полимера в осадок, поскольку ПВХ нерастворим в мономере.
При передаче цепи на полимер на макромолекулах, выпавших в осадок образуются активные центры, на которых может продолжаться полимеризация. Ввиду малой подвижности растущих молекул полимера скорость обрыва цепи снижается, а ско-
56
рость роста вследствие большой подвижности молекул винилхлорида остается высокой. По этой причине скорость полимеризации с появлением твердой фазы возрастает. При достижении высоких степеней превращения мономера происходит постепенное снижение скорости реакции полимеризации.
3.3.1. Получение ПВХ в массе
Процесс получения ПВХ в массе протекает в среде жидкого мономера с растворенным в нем инициатором, например, динитрилазобисизомасляной кислотой. В качестве инициаторов также могут использоваться диэтилгексилперкарбонат (ПДЭГ) или ацетанилциклогексилсульфонилпероксид. Кроме того, в систему вводят 0,05–0,1 % акцепторов хлороводорода (стеараты металлов) для получения полимера с заданными свойствами.
На начальной стадии процесса полимеризации происходит зарождение частиц ПВХ, которые в дальнейшем растут за счет полимеризации адсорбированного на их поверхности мономера. В результате передачи цепи на полимер каждая макромолекула имеет в среднем по одному ответвлению на каждые 50–100 мономерных звеньев. ПВХ, получаемый полимеризацией в массе, имеет наиболее разветвленное строение в сравнении с полимерами, получаемыми другими методами.
Проведение процесса полимеризации в массе сопряжено с трудностями отвода тепла из зоны реакции, особенно при высоких степенях конверсии мономера, когда образующийся полимер налипает на стенки реактора. Поэтому полимеризацию винилхлорида в массе в обычном автоклаве можно вести до достижения степени конверсии мономера не более 10 %. В промышленности полимеризацию винилхлорида в массе проводят в две стадии: получают форполимер в обычном автоклаве, а завершают процесс в горизонтальном или вертикальном цилиндрическом реакторе, конструкция которого позволяет обеспечить эффективный отвод тепла и интенсивное размельчение полимера.
57
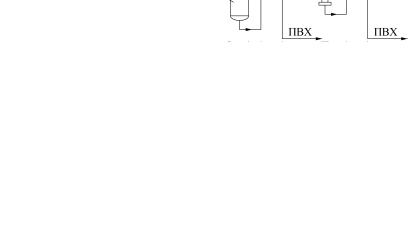
Процесс начинают в автоклаве при 30–70 °С (выбор температуры определяется свойствами полимера) в присутствии инициаторов, растворимых в диметилфталате или в мономере. Форполимеризацию ведут при интенсивном перемешивании до достижения степени конверсии винилхлорида 10 %. Полученную суспензию ПВХ в мономере переводят в основной автоклав, снабженный мешалкой специальной конструкции, в котором содержатся свежий винилхлорид, инициатор и акцептор хлороводорода. Степень превращения винилхлорида в основном автоклаве достигает 70–85 % в зависимости от марки ПВХ.
Рис. 3.9. Технологическая схема получения ПВХ в массе: 1 – автоклав предварительной полимеризации; 2 – емкость винилхлорида; 3 – автоклавполимеризатор; 4 – фильтр; 5 – конденсатор винилхлорида; 6 – бункерциклон; 7 – грохот; 8, 12, 13, 16 – приемники ПВХ; 9 – емкость; 10 – дробилка; 11 – сито; 14 – мельница; 15 – воздушный фильтр
Технологическая схема получения ПВХ в массе представлена на рис. 3.9. В реактор-автоклав 1 подают жидкий винилхлорид из емкости 2 и инициатор. Процесс ведут в течение 1–1,5 ч при интенсивном перемешивании под давлением 0,9–1,1 МПа до дос-
58
тижения 10 % конверсии винилхлорида. Температура в реакторе регулируется подачей пара или холодной воды в рубашку. Суспензия полимера в винилхлориде сливается в горизонтальный автоклав 3, где смешивается со свежей порцией мономера, инициатором, акцептором хлороводорода и другими добавками. Процесс протекает в течение 8–11 ч до достижения степени конверсии мономера 60–85 %. Температура и давление в реакторе поддерживаются на заданном значении подачей воды в рубашку.
Непрореагировавший винилхлорид через фильтр 4 поступает в конденсатор 5, откуда в сконденсированном виде стекает в емкость 2. Автоклавы 1 и 3 перед загрузкой вакуумируют или продувают азотом для удаления воздуха. Образующийся ПВХ в виде пылевоздушной смеси пневмотранспортом поступает в бункер-циклон 6, где отделяется от воздуха и направляется на рассев. Порошкообразный полимер через грохот 7 подается в бункер-приемник 8 и в емкость 9, затем измельчается в дробилке 10, просеивается на сите 11 и собирается вбункер 12, откудапоступаетнаупаковку.
Крупная фракция ПВХ предварительно дробится, после чего порошок с нестандартным размером частиц через бункер 13 подается на мельницу 14 для окончательного измельчения. Просеянный ПВХ собирают в бункере16 и также направляютнаупаковку.
3.3.2. Эмульсионный ПВХ
Особенность эмульсионной полимеризации винилхлорида в водной среде – использование водорастворимого инициатора. Инициаторами процесса полимеризации являются персульфаты аммония или калия, также могут использоваться окислительновосстановительные системы (персульфат калия + бисульфат или тиосульфат аммония, пероксид водорода + соль двухвалентного железа и др.). Для регулирования pH среды добавляют буферные растворы: фосфаты, карбонаты. В качестве эмульгаторов применяют соли алифатических карбоновых и сульфокислот, ароматических карбоновых кислот, а также алкилсульфонаты. В результате эмульсионной полимеризации образуется латекс с
59
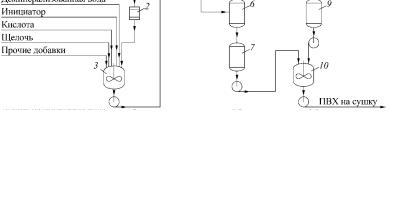
размером частиц 0,1–1 мкм, полимер из латекса выделяют в виде тонкодисперсного порошка.
Технологическая схема получения ПВХ в эмульсии непрерывным способом представлена на рис. 3.10. В эмалированный автоклав с мешалкой и рубашкой непрерывно подают жидкий винилхлорид и растворенные в воде эмульгатор, инициатор и регулятор pH среды. Отношение винилхлорида к водной фазе составляет 1:(1–2). Процесс полимеризации контролируют по плотности эмульсии и температуре среды в автоклаве. На выходе из реактора плотность эмульсии должна составлять 1120 кг/м3. Из реактора латекс с содержанием ПВХ около 40 % через фильтр 5 подается на дегазацию в аппарат 6. Остаточный мономер удаляют из латекса под вакуумом.
Рис. 3.10. Технологическая схема получения ПВХ в эмульсии: 1 – аппарат для растворения эмульгатора; 2, 5, 11 – фильтры; 3 – сборник водной фазы; 4 – полимеризатор; 6 – дегазатор латекса; 7 – сборник латекса; 8 – растворитель соды; 9 – сборник раствора соды; 10 – емкость для стабилизации латекса
После дегазации латекс поступает в сборник 7, из которого он направляется в емкость 10 для стабилизации раствором соды, а после стабилизации латекс направляют на сушку. Сухой продукт с
60