
книги / Материаловедение.-1
.pdf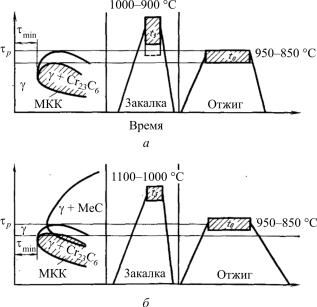
Рис. 34. Схема термической обработки аустенитных нержавеющих сталей: а – нестабилизированные; б – стабилизированные TiC (или NbC)
Для сталей без титана и ниобия возможен стабилизирующий отжиг, который приводит сталь в состояние высокого сопротивления МКК. В сталях, легированных Ti и Nb, при отжиге происходит превращение карбидов хрома в специальные карбиды TiC (или NbC), что также устраняет склонность к МКК. Хромоникелевые коррозионно-стойкие стали содержат дефицитный и дорогостоящий никель, и поэтому имеют высокую стоимость. В ряде случаев применяют более дешевые стали, в которых весь никель или часть его заменен марганцем. До температуры –196 °С и в слабоагрессивных пищевых средах вместо стали 12Х18Н10Т может быть использована сталь 10Х14Г14Н4Т.
91
12.3. ЖАРОСТОЙКИЕ СТАЛИ
Жаростойкость– это способность материала сопротивлятьсягазовойкоррозиипривысокотемпературномнагреве.
Повышать жаростойкость можно тремя способами:
1)путем нанесения жаростойких покрытий;
2)методами химико-термической обработки (алитирование, хромирование, борирование и т.д.);
3)с помощью легирования сталей (принцип легирования заключается во введении элементов, повышающих температуру интенсивного окалинообразования).
Жаростойкость в большей степени зависит от химического состава сталей. Жаростойкими могут быть стали любых структурных классов. Термическая обработка будет зависеть от структурного класса стали. Примеры – сталь 12Х13, 12Х17, 12Х18Н10Т; сплавы ХН45Ю, Х20Н80 и т.д.
12.4. ЖАРОПРОЧНЫЕ СТАЛИ И СПЛАВЫ
Жаропрочность – это способность материала сопротивляться деформации и разрушению под действием внешних нагрузок при высоких температурах. Жаропрочные материалы применяются при рабочих температурах выше 450 °С.
В качестве современных жаропрочных материалов приме-
няют следующие группы: перлитные, мартенситные и аустенитные жаропрочные стали, никелевые и кобальтовые жаропрочные сплавы, тугоплавкие металлы.
Для работы в интервале температур 350–500 °C применяют легированные стали перлитного, ферритного и мартенситного классов.
К группе перлитных жаропрочных сталей относятся ко-
тельные стали и сильхромы. Они применяются для изготовления деталей котельных агрегатов, паровых турбин, двигателей внут-
92
реннего сгорания. Стали содержат относительно мало углерода. Легирование сталей хромом, молибденом и ванадием производится для повышения температуры рекристаллизации (марки 12Х1МФ, 20Х3МФ). Используются в закаленном и высокоотпущенном состоянии. Иногда закалку заменяют нормализацией. В результате этого образуются пластинчатые продукты превращения аустенита, которые обеспечивают более высокую жаропрочность. Предел ползучести этих сталей должен обеспечить остаточную деформацию в пределах 1 % за время 10 000–100 000 ч работы.
Перлитные стали обладают удовлетворительной свариваемостью, поэтому используются для сварных конструкций (например, для труб пароперегревателей).
Для деталей газовых турбин применяют сложнолегиро-
ванные стали мартенситного класса 12Х2МФСР, 12Х2МФБ, 15Х12ВНМФ. Увеличение содержания хрома повышает жаростойкость сталей. Хром, вольфрам, молибден и ванадий повышают температуру рекристаллизации, образуются карбиды, увеличивающие прочность после термической обработки. Термическая обработка состоит из закалки от температур выше 1000 °С в масле или на воздухе и высокого отпуска при температурах выше температуры эксплуатации.
Для изготовления жаропрочных деталей, не требующих сварки (клапаны двигателей внутреннего сгорания), применяются хромокремнистые стали – сильхромы: 40Х10С2М, 40Х9С2, Х6С.
Жаропрочные свойства растут с увеличением степени легированности. Сильхромы подвергаются закалке от температуры около 1000 °С и отпуску при температуре 720–780 °С.
При рабочих температурах 500–700 °C применяются стали аустенитного класса. Из этих сталей изготавливают клапаны двигателей, лопатки газовых турбин, сопловые аппараты реактивных двигателей и т.д.
Основными жаропрочными аустенитными сталями являются хромоникелевые стали, дополнительно легированные вольфрамом, молибденом, ванадием и другими элементами.
93
Стали содержат 15–20 % хрома и 10–20 % никеля, обладают жаропрочностью и жаростойкостью, пластичны, хорошо свариваются, но затруднена обработка резанием и давлением, охрупчиваются в интервале температур около 600 °С из-за выделения по границам различных фаз.
По структуре стали подразделяются на две группы:
1. Аустенитные стали с гомогенной структурой 17Х18Н9, 09Х14Н19В2БР1,12Х18Н12Т. Содержание углерода в этих сталях минимальное. Для создания большей однородности аустенита стали подвергаются закалке с температуры 1050–1100 °С в воде, затем для стабилизации структуры – отпуску при 750 °С.
2. Аустенитные стали с гетерогенной структурой
37Х12Н8Г8МФБ, 10Х11Н20Т3Р.
Термическая обработка сталей включает закалку с 1050–1100 °С. После закалки старение при температуре выше эксплуатационной (600–750 °С). В процессе выдержки при этих температурах в дисперсном виде выделяются карбиды, карбонитриды, вследствие чего прочность стали повышается.
Детали, работающие при температуре 700–900 °C, изготавливают из сплавов на основе никеля и кобальта (например, турбины реактивных двигателей). Никелевые сплавы преимущественно применяют в деформированном виде. Они содержат более 55 % никеля и минимальное количество углерода (0,06–0,12 %). По жаропрочным свойствам превосходят лучшие жаропрочные стали. По структуре никелевые сплавы разделяют на гомогенные (нихромы) и гетерогенные (нимоники).
Основой нихромов является никель, а основным легирующим элементом – хром (ХН60Ю, ХН78Т). Нихромы не обладают высокой жаропрочностью, но они очень жаростойки. Их применяют для малонагруженных деталей, работающих в окислительных средах, в том числе для нагревательных элементов.
Нимоники являются четвертными сплавами никель: хром (около 20 %) – титан (около 2 %) – алюминий (около 1 %) (ХН77ТЮ, ХН70МВТЮБ, ХН55ВМТФКЮ). Используются толь-
94
ко в термически обработанном состоянии. Термическая обработка состоит из закалки с 1050–1150 °С на воздухе и отпуска – старе-
ния при 600–800 °С.
Увеличение жаропрочности сложнолегированных никелевых сплавов достигается упрочнением твердого раствора путем введения кобальта, молибдена, вольфрама.
Основными материалами, которые могут работать при температуре выше 900 °C (до 2500 °С), являются сплавы на основе тугоплавких металлов – вольфрама, молибдена, нио-
бия и др. Температуры плавления основных тугоплавких металлов следующие: вольфрам – 3400 °С, тантал – 3000 °С, молибден – 2640 °С, ниобий – 2415 °С, хром – 1900 °С. Высокая жаропрочность таких металлов обусловлена большими силами межатомных связей в кристаллической решетке и высокими температурами рекристаллизации.
Наиболее часто применяют сплавы на основе молибдена. В качестве легирующих добавок в сплавы вводят титан, цирконий, ниобий. С целью защиты от окисления проводят силицирование, на поверхности сплавов образуется слой MoSi2 толщиной 0,03–0,04 мм. При температуре 1700 °С силицированные детали могут работать 30 часов.
Вольфрам – наиболее тугоплавкий металл. Его используют в качестве легирующего элемента в сталях и сплавах различного назначения, в электротехнике и электронике (нити накала, нагреватели в вакуумных приборах). В качестве легирующих элементов к вольфраму добавляют молибден, рений, тантал. Сплавы вольфрама с рением сохраняют пластичность до –196 °С и имеют предел прочности 150 МПа при температуре 1800 °С.
95
ТЕМА 13. МЕТОДЫ ПОВЕРХНОСТНОГО УПРОЧНЕНИЯ СТАЛЬНЫХ ДЕТАЛЕЙ
Конструкционная прочность многих деталей машин зависит от состояния материала в поверхностных слоях деталей. Так, долговечность деталей, работающих в условиях изнашивания (валы, шестерни), зависит от сопротивления материала изнашиванию в тонких поверхностных слоях. Износ выше допустимых норм выводит деталь из строя, несмотря на то что материал детали в целом может быть вполне работоспособным. Разрушение деталей, работающих при изгибающих нагрузках, в условиях циклического действия нагрузки обычно также начинается в поверхностных слоях детали. Основными и широко применяемыми методами поверхностного упрочнения стальных деталей являются поверхностная закалка и химико-термическая обработка (ХТО).
13.1. ПОВЕРХНОСТНАЯ ЗАКАЛКА СТАЛИ
Наибольшее распространение имеют электротермическая закалка с нагревом изделий токами высокой частоты (ТВЧ) и газопламенная закалка с нагревом газово-кислородным или кислородно-керосиновым пламенем.
Для осуществления закалки ТВЧ необходим индуктор, форма и размеры которого должны соответствовать нагреваемому изделию. Качество закалки ТВЧ в значительной мере определяется величиной зазора между индуктором и нагреваемой деталью. Время нагрева при закалке ТВЧ зависит от скорости нагрева; оно находится обычно в пределах 1,5–40 с, после чего следует охлаждение. После закалки ТВЧ детали подвергают низкотемпературному отпуску при 150–200 °С.
96
Преимущества индукционной закалки, по сравнению
собычной, следующие:
–большая экономичность, так как нет необходимости расходовать теплоту на нагрев всей детали и печи, что характерно для обычной закалки; при закалке ТВЧ значительно меньше брак по короблению и образованию закалочных трещин;
–при нагреве ТВЧ не происходит окалинообразования
ивыгорания углерода;
–механические свойства после закалки ТВЧ выше, чем после обычной закалки;
–легко регулируется толщина закаленного слоя;
–внедрение ТВЧ позволяет заменить в ряде случаев легированные стали дешевыми углеродистыми сталями;
–весьма высокая производительность труда;
–установки ТВЧ без затруднений вписываются в поточные линии механических цехов, для них легко осуществляется автоматизация производственного процесса.
Недостатком закалки ТВЧ является необходимость в специализированном оборудовании (генераторы ТВЧ) и сложных приспособлениях (индукторах).
В случае газопламенной закалки поверхностный нагрев осуществляется ацетиленокислородным, газокислородным или керосинокислородным пламенем с температурой 3000–3200 °С. Газопламенная закалка применяется для крупных изделий, имеющих зачастую сложную поверхность (косозубые шестерни, червяки и пр.). Этот метод может применяться в массовом и индивидуальном производстве (в том числе при ремонтных работах). Механизированные установки газопламенной закалки могут легко включаться в поточные линии механических цехов. Результаты газопламенной закалки при автоматизированном режиме равноценны закалке ТВЧ, хотя производительность при газопламенной закалке несколько ниже. Труднее регулировать температуру нагрева и глубину закаленного слоя.
97
13.2. ХИМИКО-ТЕРМИЧЕСКАЯ ОБРАБОТКА МЕТАЛЛОВ
13.2.1. Общие закономерности ХТО
Химико-термической обработкой называют процесс, со-
четающий в себе поверхностное насыщение стали тем или иным элементом при определенной температуре и термической обработки, в результате которых происходит изменение химического состава, микроструктуры и свойств поверхностных слоев деталей.
Насыщение поверхностного слоя происходит при нагреве детали до определенной температуры в среде, выделяющей насыщающий элемент в активном состоянии, и выдержке при этой температуре. Среды, выделяющие насыщающий элемент, могут быть газообразными, жидкими и твердыми.
Основные процессы любого вида химико-термической обработки следующие:
1. Диссоциация – выделение насыщающего элемента в активном атомарном состоянии в результате разложения исходных веществ: 2СО → СО2 + С; 2NH3 → 3H2 + 2N и т.д. Степень распада молекулгаза (%) называют степенью диссоциации.
2.Абсорбция – захват поверхностью металла свободных атомов насыщающего элемента. Атомы металла, находящиеся на поверхности, имеют направленные наружу свободные связи. При подаче к поверхности детали атомов насыщающего элемента эти свободные связи вступают в действие, что уменьшает поверхностную энергию металла. С повышением температуры абсорбционная способность металла увеличивается.
3.Диффузия – проникновение насыщающего элемента вглубь металла.
В результате диффузии химический состав поверхностного слоя меняется, при этом создается градиент концентраций насыщающего элемента в поверхностных и нижележащих слоях. Диффузия протекает легче при образовании твердых растворов внедрения (С, N), чем твердых растворов замещения (Al, Cr, Si),
98
поэтому при диффузионной металлизации процесс ведут при более высоких температурах.
Поверхностный слой детали, отличающийся от исходного материала по химическому составу, называется диффузионным слоем. Материал детали под диффузионным слоем с неизменившимся химическим составом называется сердцевиной.
13.2.2. Цементация
Цементацией называется процесс диффузионного насыщения поверхностного слоя стальных деталей углеродом и последующей термической обработки. Цель цементации – достижение высокой твердости и износостойкости поверхности детали в сочетании с вязкой сердцевиной. На цементацию поступают механически обработанные детали с припуском на шлифование 50–100 мкм. В тех случаях, когда цементации подвергается только часть детали, остальные участки защищают либо специальными огнеупорными обмазками, либо тонким слоем (20–40 мкм) меди, нанесенным электролитическим способом.
Цементации подвергают стали с низким содержанием углерода (0,1–0,2 % С). После нее на поверхности концентрация углерода достигает 1,0 %.
Процесс цементации проводят при температурах выше А3 (обычно при 910–930, реже при 1000–1050 °С), когда сталь находится в аустенитном состоянии, которое характеризуется высокой растворимостью углерода. Толщина цементованного слоя в зависимости от состава стали и назначения изделия может составлять 0,5–2,5 мм. Для достижения высокой твердости поверхности и вязкой сердцевины после цементации всегда проводят закалку с низким отпуском. Целью термической обработки является упрочнение поверхности с одновременным измельчением зерна и получением вязкой сердцевины.
99
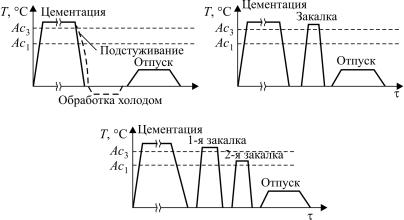
Рис. 35. Режимы термической обработки стали после цементации
В зависимости от назначения детали применяют различные варианты термической обработки (рис. 35). После такой термообработки поверхностный поверхностный слой имеет структуру отпущенного высокоуглеродистого мартенсита с включениями глобулярных карбидов и остаточного мартенсита. Структура сердцевины определяется химическим составом стали. При цементации углеродистой стали из-за низкой прокаливаемоcти сердцевина имеет феррито-перлитную структуру. Легированная сталь при цементации позволяет получать в сердцевине структуру сорбита, троостита или мартенсита, но благодаря низкой концентрации углерода сердцевина будет иметь высокую ударную вязкость.
13.2.3. Азотирование
Азотированием называется процесс насыщения поверхностного слоя азотом. Его целью является создание поверхностного слоя с особо высокой твердостью, износостойкостью,
100