
книги / Материаловедение.-1
.pdfповышенной усталостной прочностью и сопротивлением коррозии в водной среде, паровоздушной и влажной атмосфере.
Процесс азотирования состоит в выдержке в течение довольно длительного времени (до 60 ч) деталей в атмосфере аммиака при 500–600 °С. Его проводят в стальных герметически закрытых ретортах, в которые поступает аммиак. Активные атомы азота проникают в решетку α-железа и диффундируют в ней. Образующиеся при этом нитриды железа еще не обеспечивают достаточно высокой твердости. Высокую твердость азотированному слою придают нитриды легирующих элементов, прежде всего хрома, молибдена, алюминия. При совместном легировании стали хромом, молибденом, алюминием твердость азотированного слоя по Виккерсу достигает 1200 HV, в то время как после цементации и закалки твердость составляет 900 HV.
Благодаря высокой твердости нитридов легирующих элементов азотированию обычно подвергают легированные среднеуглеродистые стали. К таким сталям относятся 38Х2МЮА, 35ХМА, более дешевую 38Х2Ю6, а также некоторые штамповые стали, например ЗХ2В8, 5ХНМ.
Азотированию подвергают готовые изделия, прошедшие механическую и окончательную термическую обработку (закалку с высоким отпуском 600–675 °С, температура которого выше максимальной температуры азотирования). После такой термической обработки металл приобретает структуру сорбита, имеющую высокую прочность и вязкость. Эта структура сохраняется в сердцевине детали и после азотирования. Высокая прочность металлической основы необходима для того, чтобы тонкий и хрупкий азотированный слой не продавливался при работе детали. Высокая твердость азотирования достигается сразу и не требует последующей термической обработки. Это важное преимущество процесса азотирования.
Участки, не подлежащие азотированию, защищают путем нанесения тонкого слоя олова (10–15 мкм) электролитическим методом или жидкого стекла. Глубина азотированного слоя дос-
101
тигает 0,3–0,6 мм. Из-за сравнительно низких температур скорость азотирования значительно меньше, чем скорость цементации, и составляет всего 0,01 мм/ч и менее.
Преимуществами азотирования являются более высокая твердость и износостойкость поверхностного слоя, сохранение им высоких свойств при нагреве до 500 °С, а также высокая коррозионная стойкость. В азотированном слое создаются остаточные напряжения сжатия, что повышает усталостную прочность. Кроме того, после азотирования не требуется закалки, что позволяет избежать сопутствующих закалке дефектов.
К недостаткам азотирования, по сравнению с цементацией, относятся более высокая длительность процесса и необходимость применения дорогостоящих легированных сталей. В связи с этим азотирование проводят при изготовлении деталей, от которых требуется особо высокое качество поверхностного слоя. Его применяют в машиностроении для изготовления мерительного инструмента, гильз, цилиндров, зубчатых колес, шестерен, втулок, коленчатых валов и др.
13.2.4. Совместное насыщение углеродом и азотом
Нитроцементацией называют процесс диффузионного насыщения поверхностного слоя стали одновременно углеродом и азотом при температуре 840–860 °С в газовой среде, состоящей из науглероживающего газа и аммиака. Продолжительность процесса – 4–10 часов. После насыщения следует закалка непосредственно из печи и низкий отпуск. Структура слоя состоит из мелкокристаллического мартенсита, небольшого количества мелких карбонитридов и остаточного аустенита. Основное назначение нитроцементации – повышение твердости, износостойкости и предела выносливости стальных деталей. Нитроцементации обычно подвергают детали сложной конфигурации, склонные к короблению. Широко применяют этот процесс насыщения на автомобильных и тракторных заводах.
102
Цианированием называют процесс диффузионного насыщения поверхностного слоя стали одновременно углеродом и азотом при температуре 820–950 °С в расплавленных солях, содержащих группу NaCN. После насыщения следуют закалка непосредственно из цианистой ванны и низкий отпуск.
Различают среднетемпературное (820–860 °С) и высокотемпературное (930–950 °С) цианирование. Среднетемпературное цианирование применяют для получения упрочненного слоя небольшой толщины (0,15–0,35 мм) на мелких деталях. Для получения слоя большой толщины (0,5–2,0 мм) применяют высокотемпературное или глубокое цианирование. Строение цианированного слоя аналогично цементованному. После высокотемпературного цианирования детали охлаждают на воздухе, а затем для измельчения зерна закаливают с нагревом в соляной ванне или печи и подвергают низкотемпературному отпуску.
Процесс цианирования, по сравнению с процессом цементации, требует меньшего времени для получения слоя заданной толщины, характеризуется значительно меньшими деформациями и короблением деталей сложной формы и более высоким сопротивлением износу и коррозии. Его недостатками являются высокая стоимость, ядовитость цианистых солей и необходимость принятия в связи с этим специальных мер по охране труда.
13.2.5. Борирование
Борирование придает поверхностному слою исключительно высокую твердость (до 1800–2000 HV), износостойкость и устойчивость против коррозии в различных средах. Его часто проводят при электролизе расплавленных солей, например буры Na2B4O7 10Н2О, где стальная деталь служит катодом. При температуре около 1050 °С и выдержке 4–7 ч на поверхности образуется твердый борид железа, толщина слоя достигает 0,1–0,2 мм. Применяется для обработки втулок грязевых насосов и других деталей, подвергающихся истирающему абразивному износу.
103
13.2.6. Диффузионная металлизация
Диффузионной металлизацией называется процесс диф-
фузионного насыщения поверхностных слоев стали различными металлами. Детали, поверхность которых насыщена алюминием, хромом, кремнием, приобретают ряд ценных свойств, например жаростойкость, коррозионную стойкость, повышенную износостойкость и твердость.
Металлизация бывает твердая, жидкостная и газовая. При жидкостной металлизации стальную деталь погружают в расплав металла. При твердой и газовой металлизации насыщение происходит с помощью летучих соединений хлора с металлом А1С1з, CrCl3, SiC14, которые при температуре 1000–1100 °С вступают в обменную реакцию с железом с образованием диффундирующего элемента в активном состоянии. В результате этого образуются твердые растворы железа с металлом или соответствующие химические соединения.
При алитировании, т.е. насыщении алюминием, которое обычно проводится в порошкообразных смесях или расплавленном алюминии, детали приобретают повышенную коррозионную стойкость благодаря образованию плотной пленки Al2O3, предохраняющей металл от окисления. Толщина слоя составляет 0,2–0,5 мм. Алитированию подвергают топливники газогенераторных машин, чехлы термопар, клапаны и другие детали, работающие при высокой температуре.
При хромировании обеспечивается высокая стойкость против газовой коррозии до 800 °С, а также стойкость против коррозии в воде, морской воде и кислотах. Толщина слоя составляет до 0,2 мм. Хромированию подвергают детали паровой арматуры, паросилового оборудования, а также детали, работающие на износ в агрессивных средах.
Силицирование, т.е. насыщение кремнием, придает высокую кислотоупорность в соляной, серной и азотной кисло-
104
тах. Силицированные детали обладают окалиностойкостью при температурах до 700–750 °С. Применяется такой вид насыщения для деталей, используемых в химической и нефтяной промышленности. Толщина слоя находится в пределах
0,3–1,0 мм.
Диффузионная металлизация может быть существенно интенсифицирована при нанесении на поверхность детали паст или суспензии, содержащих мелкодисперсные частицы насыщающих элементов. Использование суспензий, содержащих частицы алюминия, позволяет получить толщину диффузионного слоя до 0,3–0,5 мм при температуре процесса 900–1000 °С за 15 мин. Установлена также возможность использования этого метода при комплексной диффузионной металлизации сталей алюминием и кремнием, что существенно повышает жаростойкость покрытий. Применение комплексного бороалитирования повышает пластичность, жаростойкость и износостойкость борированного слоя.
105
ТЕМА 14. ЦВЕТНЫЕ МЕТАЛЛЫ И СПЛАВЫ
Цветные металлы – промышленное название всех металлов, за исключением железа. По физическим и химическим свойствам и характеру залегания в земной коре цветные металлы можно подразделить на следующие группы: легкие (алюминий, магний, титан, бериллий, литий и др.), тяжелые (медь, никель, кобальт, свинец, олово, цинк и др.), тугоплавкие (вольфрам, молибден, хром, ниобий, тантал, цирконий и др.), благородные, или драгоценные (золото, серебро, платина и платиновые металлы),
рассеянные (галлий, индий, таллий), редкоземельные (скандий,
иттрий, лантан и все лантаноиды), радиоактивные (технеций, радий, полоний и др.).
14.1. АЛЮМИНИЙ И СПЛАВЫ НА ЕГО ОСНОВЕ
Алюминий был открыт в 1808 г., но только в 1825 г. были получены его первые крупицы в чистом виде. Важнейшие свойства алюминия – низкий удельный вес, высокая электро- и теплопроводность, пластичность, хорошая коррозионная стойкость в атмосфере и ряде агрессивных сред– обусловливают широкое использование втехнике как чистогометалла, так иего сплавов.
Сплавы на основе алюминия классифицируют по технологии изготовления (деформируемые, литейные и спеченные) и по способности упрочняться при термической обработке (упрочняемые и неупрочняемые). Большинство сплавов имеют диаграмму с эвтектикой и ограниченной переменной растворимостью компонентов в твердом состоянии (рис. 36).
К деформируемым относятся сплавы, в которых может быть получена однофазная структура α-твердого раствора. Хорошее сочетание характеристик прочности и пластичности имеют дуралю-
106
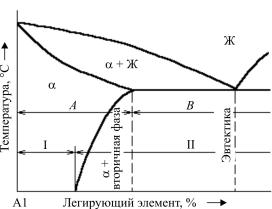
мины – наиболее распространенные алюминиевые сплавы, являющиеся типичными представителями группы деформируемых сплавов, упрочняемых термической обработкой. Они относятся к системе Al – Cu – Mg, маркируются буквой Д (например, Д1, Д16 и др.). Упрочняющая термическая обработка дуралюминов состоит из закалки на пересыщенный твердый раствор и естественного (безнагрева) илиискусственного(с нагревом) старения.
Рис. 36. Диаграмма состояния алюминий – легирующий элемент: А – деформируемые сплавы; В – литейные сплавы;
I, II – сплавы, не упрочняемые и упрочняемые термической обработкой соответственно
Согласно диаграмме состояния Al – Cu (рис. 37) структура сплавов в исходном равновесном состоянии представляет собой α-твердый раствор с включениями частиц интерметаллидов CuAl2.
После закалки (нагрева выше линии переменной растворимости аб и быстрого охлаждения) образуется пересыщенный твердый раствор замещения меди в алюминии, однако твердость и прочность сразу после закалочного охлаждения возрастают незначительно. Упрочнение дуралюмина происходит во время последующего старения.
107
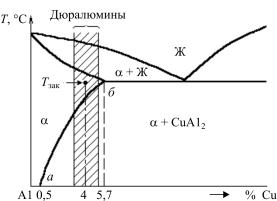
Рис. 37. Диаграмма состояния системы алюминий – медь
Сущность старения состоит в распаде неустойчивого пересыщенного твердого раствора с образованием большого количества дисперсных частиц CuAl2, равномерно распределенных в объеме. Это превращение проходит через несколько промежуточных состояний, каждое из которых можно зафиксировать, подобрав соответствующую температуру и продолжительность старения. Максимальное упрочнение достигается на ранней стадии процесса, когда скопление атомов меди в локальных участках еще не приводит к образованию частиц CuAl2, но вызывает сильные искажения кристаллической решетки матричного твердого раствора. При комнатной температуре старение прекращается именно на этом этапе через 5–7 суток. Повышение температуры увеличивает скорость процесса и может привести к перестариванию из-за образования и последующей коагуляции частиц фазы CuAl2, поэтому напрактике чащеприменяютестественное старение.
Пример. Опишите возможные виды брака при термической обработке дуралюминов.
Решение. Проведение закалки дуралюминов требует нагрева на строго определенную температуру (например, для сплава Д16
108
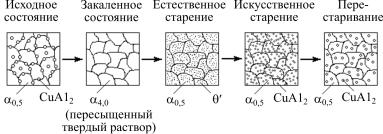
Tзак = 500 ± 5 °С) и резкого охлаждения в воде. Нагрев под закалку должен обеспечить полное растворение частиц интерметаллидов и образование однородного α-твердого раствора меди в алюминии. При более высоких температурах происходит пережог (окисление и частичное оплавление металла по границам зерен), что резко снижает прочность и пластичность. При недогреве часть интерметаллидов не растворится, концентрация меди в твердом растворе будет меньше, следовательно, старение не приведет к максимальному упрочнению. Резкое охлаждение в воде при закалке необходимо для того, чтобы зафиксировать высокотемпературное состояние, полученное при нагреве, и предотвратить выделение частиц CuAl2 по границам зерен во время охлаждения.
Температуру и продолжительность старения назначают в зависимости от требуемых свойств. В том случае, когда одинаковый уровень прочности можно получить разными способами старения, предпочтительнее естественное старение, которое обеспечивает более высокую пластичность и коррозионную стойкость, крометого, нет опасностиперестаривания.
В упрощенном виде изменение структуры при термической обработке дуралюмина, содержащего 4 % Cu, показано на рис. 38.
Рис. 38. Схема структурных изменений в сплавеAl + 4 % Cu в процессе термической обработки: индексами показано содержание меди в α-твердом растворе; θ' – зоны с высокой концентрацией меди
109
К литейным алюминиевым сплавам относятся сплавы,
содержащие в структуре эвтектику. Наличие большого количества эвтектики, кристаллизующейся при постоянной температуре, обеспечивает высокую жидкотекучесть, малую усадку и, как следствие, точность формы и размеров отливки. Для литейных алюминиевых сплавов наиболее распространена классификация по химическому составу (Al – Si; Al – Cu; Al – Mg). Лучшими литейными свойствами обладают силумины (система Al – Si). Основным способом повышения механических свойств силуминов является измельчение структуры путем модифицирования. Для доэвтектических сплавов, кроме того, применяют термическую обработку, состоящую из закалки и старения.
14.2. МЕДЬ И СПЛАВЫ НА ЕЕ ОСНОВЕ
Медь известна человеку с глубокой древности, это связано с тем, что она часто встречалась в виде самородков. Наиболее ценными свойствами меди являются электро- и теплопроводность. Однако эти свойства зависят от чистоты металла: чем меньше содержание примесей, тем больше электро- и теплопроводность. Вредными примесями в меди являются сурьма, мышьяк, висмут. Техническая медь (М1, М2 и др.), как и все чистые металлы, имеет низкие прочностные свойства и высокую пластичность, поэтому возможно упрочнение наклепом. В машиностроении медь используют в виде сплавов (латуни и бронзы).
Латуни – сплавы меди с цинком; могут быть дополнительно легированы другими элементами для улучшения свойств; например, небольшое количество свинца обеспечивает улучшение обрабатываемости резанием, олово добавляют для повышения коррозионной стойкости в морской воде. Латуни используют и как деформируемые, и как литейные материалы. Латуням присущи все положительные свойства меди (высокая электро-
110