
книги / Материаловедение.-1
.pdfДля каждой группы сталей разработаны нормы легирования и определены оптимальные режимы обработки для получения требуемых свойств.
Автоматные стали (free cutting steels), изготовленные по ГОСТ 1414–75, применяют для массового изготовления крепежа на станках-автоматах. Основное требование к ним – хорошая обрабатываемость резанием, достигаемая за счет увеличения содержания серы и фосфора до 0,1–0,2 %, а также добавления
селена и свинца. |
Маркируются автоматные стали буквой А |
и двумя цифрами, |
показывающими среднее содержание углеро- |
да в сотых долях процента: А12, А20, А30.
При введении свинца в количестве Рb = 0,15–0,30 % стали маркируются буквами АС и цифрами среднего содержания углерода в сотых долях процента: АС11, АС14. При дополнительном легировании другими элементами их обозначают так же, как в обычных конструкционных сталях: АС35Г2, АС38ГХМ и т.д.
Строительные стали (building steels) содержат относи-
тельно малое количество углерода (0,1–0,25 %). По сравнению с углеродистыми сталями более высокая прочность строительных низколегированных сталей достигается упрочнением феррита за счет легирования сравнительно малыми количествами кремния и марганца, а также хрома, никеля, меди и некоторых других элементов. В качестве примера можно рассмотреть следующие марки: сталь 3, 14Г2, 17Г2, 14ХГС, 15ХСНД и т.д. Эти стали используются в горячекатаном или нормализованном состоянии для ар-
мирования железобетона, изготовления сварных |
конструкций |
в строительстве, мостостроении, вагоностроении, |
сельскохозяй- |
ственном машиностроении, корпусов судов в судостроении, для изготовления магистральных нефте- и газопроводов. Основные требования, предъявляемые к этим сталям, – необходимая конструкционная прочность, технологичность при изготовлении (наиболее важная характеристика – свариваемость).
Цементуемые стали. Для изготовления деталей, работающих под действием динамических нагрузок в условиях поверхно-
71
стного износа, применяют низкоуглеродистые стали, содержащие обычно не более 0,2 % С, подвергаемые цементации, закалке и низкому отпуску. В качестве примера можно рассмотреть следующие марки: 15Х, 18ХГТ, 12ХН2, 12ХН3А, 12Х2Н4А. Выбор марки стали будет существенным образом зависеть от геометрии детали, сечения и требований, предъявляемых к сердцевине. Все группы цементуемых сталей имеют свои особенности при термической обработке, которые зависят от системы легирования.
Улучшаемыми конструкционными сталями (heat treatable steels) называют среднеуглеродистые стали (0,3–0,5 % С), содержащие не более 5 % легирующих элементов (экономнолегированные стали), используемые послеоперации так называемого улучшения, состоящей из закалки и высокого отпуска. Закалку таких сталей обычно проводят в масле. Температура отпуска составляет 550–650 °С. После термообработки улучшаемые стали имеют структуру сорбита, хорошо воспринимающего ударные нагрузки. В качестве примера можно привести следующие марки: 40ХФ, 40ХН2МА, 30ХГС.
Легирующие элементы в этой группе влияют на поведение стали при закалке и на превращения при отпуске. Основная цель легирования улучшаемых сталей – увеличение устойчивости переохлажденного аустенита, т.е. увеличение прокаливаемости. При отпуске легирующие элементы влияют на все этапы превращения, включая распад мартенсита и коагуляцию карбидов.
Рессорно-пружинные стали (sping steels). Требования,
предъявляемые к рессорно-пружинным сталям:
–высокое сопротивление малым пластическим деформациям (высокий предел упругости);
–высокий предел выносливости;
–повышенная релаксационная стойкость с сохранением упругих свойств в течение длительного времени под нагрузкой.
В пружинах и рессорах пластическая деформация не допускается, поэтому высокие значения пластичности и вязкости менее существенны.
Марки стали – содержание углерода 0,5–0,85 %.
72
Пример: углеродистые – сталь 65, 70, 85; легированные –
65Г, 60С2, 70С3А, 60СГ, 50ХФА, 65С2ВА, 60С2А; легирующие элементы – Сr, Si, Mn, V, W.
Термическаяобработка(ТО) рессорно-пружинныхсталейпро- водится по схеме: закалка + средний отпуск (400–480 °С). Получаемаяструктура– трооститотпускаилитроостомартенситотпуска.
Особенности ТО рессорно-пружинных сталей:
1)получение при закалке более мелкого зерна, превыше-
ние Ас3 + (20–30) °С;
2)недопустимо обезуглероживание поверхности, что ведет
кснижению упругих свойств;
3)при закалке прокаливаемость сквозная, 95 % мартенсита;
4)недопустим Аост (его наличие ведет к падению упругие характеристики, в некоторых случаях после закалки применяют обработку холодом);
5)получение стабильной дислокационной структуры (перераспределение дислокаций может привести к микропластической деформации).
Высокопрочные стали – это стали, имеющие предел прочности более 1500 МПа.
Высокую прочность стали можно получить несколькими способами:
1. Среднеуглеродистые стали. Термическая обработка:
закалка + низкий отпуск. Максимальная прочность будет зависеть от содержания углерода. Примеры: 30ХГСНА, 30ХГСН2А, 40ХГСН3ВА.
Принципы легирования:
– стали всегда высококачественные;
– обязательно легированы никелем с целью снижения критической температуры хрупкости, повышение характеристик надежности;
– должны быть минимальные остаточные напряжения после закалки и низкого отпуска.
Si, W затрудняют распад мартенсита и позволяют повысить температуру низкого отпуска.
73
Недостатки данной группы сталей:
–низкая теплостойкость;
–низкая технологичность при изготовления деталей из сталей данной группы.
2. Дисперсионно-твердеющие стали. В сталях данной группы проявляется эффект вторичного твердения, который возникает после термической обработки, заключающейся в закалке
ивысоком отпуске. После закалки структура представляет собой мартенсит и аустенит остаточный, из которого в процессе отпуска образуются карбиды дисперсные.
В основе принципа легирования лежит следующая закономерность: содержание углерода – 0,3–0,5 %; при меньшем его количестве получаем недостаточную прочность, при большем – надежность. Легирование в данном случае необходимо комплексное, с возможностью образования специальных карбидов. Примеры: 40Х5МФС или 4Х5МФС, 4Х4ВМФС.
Термическая обработка: закалка (выше 1000 °С), масло + высокий отпуск (500–600 °С). Нагрев под закалку предполагает высокие температуры для растворения вторичных карбидов, но недопустим рост зерна. Закалочное охлаждение – ускоренное. Его цель – предотвратить выделение карбидов из твердого раствора (хотя стали относятся к мартенситному классу, т.е. закаливаются на воздухе). Температуру отпуска выбирают в зависимости от требуемой прочности.
Данные стали обладают высокой теплостойкостью. Их недостатки: имеются сложности при механической обработке как в закаленном, так и в высокоотпущенном состоянии, высока вероятность деформации при термической обработке, большие припуски, в результате – высокий расход материала, низкая технологичность.
3. Мартенситостареющие стали (МСС). От первых двух групп отличаются высокой технологичностью и высокой конструкционной прочностью; обладают хорошей свариваемо-
74
стью и хорошей обрабатываемостью давлением, высокой стоимостью. Это высоколегированные дисперсионно-твердеющие безуглеродистые сплавы на основе железа. Основной легирующий элемент – никель, упрочняющая фаза – интерметалли-
ды. Примеры: 00Н18К9М5Т, 00Н18К14М5Т, 00Н18К12М5Т2.
Термическая обработка: закалка + высокий отпуск (старение). Износостойкие стали – стали, применяемые для изготовления деталей, испытывающих интенсивный износ при трении и различных видах ударного воздействия (например, кавитацион-
ный износ).
В качестве износостойких применяют три основных группы сталей:
1.Стали упрочняемые с поверхности ХТО или другими видами поверхностного упрочнения (ТВЧ, лазерная закалка, поверхностная, плазменная закалка). Пример – цементация, нитроцементация, хромирование, азотирование. Примеры сталей– улучшаемые, цементуемыеит.д.
2.Высокомарганцовистые аустенитные стали. Пример – Г13 или 110Г13Л. Кавитационно-стойкие стали 30Х10Г10 (аустенитного класса). Применение для винтов и лопастей, работающих
вжидкихсредах.
3.Шарикоподшипниковые стали (ГОСТ 801–80).
Шарикоподшипниковые стали общего назначения (примеры:
ШХ15, ШХ, ШХ6, ШХ9, ШХ15СГ) применяются в подшипниках качения в машино- и приборостроении, на железнодорожном транспорте. Требование по структуре – высокая износостойкость, обусловленная высокой твердостью. Высокая контактная выносливость обеспечивается высоким металлургическим качеством. Термическая обработка: закалка с температуры Ас1 + 300 °С, затем обработка холодом, далее низкий отпуск (2000 °С) продолжительность отпуска – 2–8 часов. Получаемаяструктура– мартенситотпускаикарбиды.
Шарикоподшипниковые стали специального назначения.
Пример – ШХ4-РП, где буквы РП обозначают, что данная сталь
75
регламентируемой прокаливаемости (ПП – пониженной прокаливаемости). Это стали с высокой теплостойкостью, работающие при повышенных температурах. Стали типа быстрорежущих и дисперсионно-твердеющих (8Х4М4В2Ф1-Ш). Термическая обработка: закалка выше 1000 °С, охлаждение в масле, затем трехкратный отпуск при температуре 560 °С.
В случае работы шарикоподшипников в агрессивных средах используют сталь 95Х18 и др. Термическая обработка: закалка выше 1000 °С и низкий отпуск.
76
ТЕМА 11. ИНСТРУМЕНТАЛЬНЫЕ СТАЛИ
Инструментальные стали предназначены для изготовления режущих, измерительных и штамповых инструментов. В большинстве случаев для этого применяют высокоуглеродистые стали, обрабатываемыенамаксимальнуютвердость, более 60 HRC. Стали нелегированные (У7, У8, У12 и др.) и малолегированные (9ХС, 9ХФ, ХВГ и др.) для получения высокой поверхностной твердости и износостойкости подвергают термической обработке, включающей закалку и низкий отпуск. Основные требования к данной группе сталей – высокая износостойкость, стабильностьразмеров, теплостойкостьивысокоесопротивлениепластическойдеформации.
Различают следующие виды инструментальных сталей по назначению:
1. Стали для режущего инструмента. Примеры марок сталей: У10, ХВГ и т.д. (нетеплостойкие), Р6М5К5, Р18, Р9 и т.д. (теплостойкие).
Пример. Назначить режим окончательной термической обработки для фрезы, изготовленной из стали У10А.
Решение. Исходная структура стали У10А перед окончательной термической обработкой – перлит зернистый. Режим обработки на твердость 63–64 HRC: неполная закалка с температуры 770–800 °С, охлаждение через воду в масло + низкий от-
пуск 150–160 °С (рис. 25).
Закалка в двух средах состоит в том, что нагретый инструмент сначала погружают в воду, а затем, после короткой выдержки, переносят в масло. Быстрое охлаждение в воде предотвращает распад аустенита на перлит, а последующее более медленное охлаждение в масле уменьшает закалочные напряжения в мартенситном интервале. Неполная закалка с температуры немного выше точки Ас1 обеспечивает получение структуры мелкокристаллического мартенсита с включениями цементита. Низкий отпуск необходим для частичного снятия закалочных напряжений при сохранении высокой твердости.
77
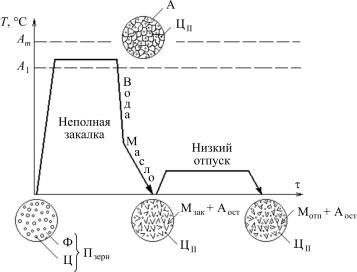
Рис. 25. Изменение структуры стали У10А при термической обработке
Особое значение в группе инструментальных сталей имеют быстрорежущие стали, применяемые в случае, когда к инструменту предъявляются особые требования по теплостойкости. Для изготовления режущих инструментов высокой производительности применяют быстрорежущие стали. Главным свойством этих сталей является высокая теплостойкость, которая определяется химическим составом и специальным режимом термической обработки на вторичную твердость (рис. 26).
В быстрорежущих сталях основным легирующим элементом, обеспечивающим сохранение твердости 60 HRC и более до рабочих температур 600–650 °С, является вольфрам. В современных марках сталей часть дефицитного вольфрама заменена молибденом. Вольфраммолибденовые стали, например Р6М5, не только дешевле вольфрамовых, но имеют также меньшую карбидную неоднородностьи лучшие механическиесвойства.
78
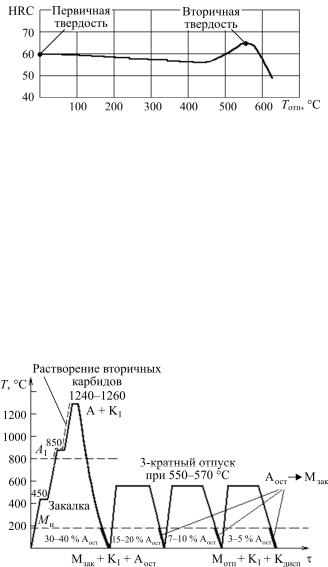
Рис. 26. Изменение твердости при отпуске быстрорежущих сталей
По структуре в отожженном состоянии быстрорежущие стали относятся к ледебуритному классу. Ледебуритную эвтектику, располагающуюся по границам зерен литого металла, устраняют горячей деформацией, при которой происходит измельчение и более равномерное распределение первичных карбидов. После отжига общее количество карбидов разного происхождения (первичных, вторичных, эвтектоидных) в структуре составляет 20–30 %. Высокие режущие свойства инструменты из быстрорежущих сталей приобретают после закалки и многократного отпуска (рис. 27).
Рис. 27. Схема термической обработки быстрорежущей стали
79
Высокая температура нагрева под закалку необходима для растворения в аустените большого количества вторичных карбидов и получения высоколегированного мартенсита. Несмотря на высокие температуры нагрева, близкие к температуре плавления, в быстрорежущих сталях сохраняется очень мелкое зерно. Охлаждение при закалке чаще всего проводят в масле или горячих средах (ступенчатая закалка). После закалки стали не обладают максимальной твердостью, так как в их структуре, кроме мартенсита и первичных карбидов, содержится 30–40 % остаточного аустенита. При отпуске происходит выделение из мартенсита и остаточного аустенита мелкодисперсных карбидов, вызывающих дисперсионное упрочнение. Аустенит, обедненный углеродом и легирующими элементами, становится менее устойчивым и при охлаждении с температуры отпуска превращается в мартенсит. Это явление, называемое вторичной закалкой, приводит к дополнительному упрочнению стали. Однократного отпуска недостаточно для превращения всего остаточного аустенита, поэтому проводят двухили трехкратный отпуск с выдержкой по 1 часу и охлаждением на воздухе. Структура после закалки и многократного отпуска – отпущенный мартенсит и карбиды, твердость 63–65 HRC.
Термическая обработка на вторичную твердость используется также для штампового инструмента горячей и холодной обработки давлением, когда наряду с достаточной прочностью
иизносостойкостью необходимо обеспечить высокую теплостойкость сталей.
2.Штамповые стали. Выделяют стали для холодного (примеры марок сталей: У8–У12, 9ХС, Х (углеродистые, малолегированные); Х12, Х12М, Х12ВМ и т.д. (высоколегированные))
игорячего деформирования (табл. 8).
Дополнительные требования для штамповых сталей для горячего деформирования:
1) высокая разгаростойкость (устойчивость против образования трещин при многократном нагреве и охлаждении);
80