
книги / Элементы и структуры систем автоматизации технологических процессов нефтяной и газовой промышленности
..pdfмышленной сети, которые называются ОРС-серверами. Основная задача ОРС-серверов состоит в привязке состояния конкретных переменных (тегов) пакетов программ верхнего уровня к параметрам конкретных внешних устройств. SCADA-системы могут работать только в определенной операционной среде. Основной средой для них считается Windows в разных версиях.
Разработчики SCADA-систем выставили на рынке множество программных пакетов верхнего уровня, среди которых
InTouch фирмы Wonderware; GENESIS32 фирмы Iconis; WinCC
фирмы Simens; iFIX фирмы Intellution.
Среди программ ОРС-серверов преобладает универсальный пакет Universal OPC фирмы Fastwel. В то же время и другие разработчики представили для пользователей подобные продукты. Например, фирма Advantech разработала PCLS-OPC/ADM ОРС-сервер для модулей серии ADAM. ОРС-серверы позволяют создавать дополнительные программы-драйверы для оборудования, которое не внесено в библиотеки стандартных ОРСсерверов. Для написания этих приложений применяют языки высокого уровня, такие как: Visual Basic, Visual C, C и C++. Но чаще всего в стандартном ОРС-сервере обновляется его библиотека, в которую с помощью одного из вышеуказанных языков вносится новое оборудование.
6.АВТОМАТИЗАЦИЯ ПРОИЗВОДСТВЕННЫХ ПРОЦЕССОВ В НЕФТЯНОЙ И ГАЗОВОЙ ПРОМЫШЛЕННОСТИ
Автоматизация производственных процессов в нефтяной и газовой промышленности призвана обеспечить рост производительности труда, сокращение оперативного персонала при обслуживании технологического оборудования, снизить трудоемкость оперативногоуправленияиповыситьегоинформативность.
Средства автоматизации, внедренные на нефтяных и газовых промыслах, позволили резко повысить производительность добычи и снизить трудоемкость этого процесса.
131
Современные нефтяные и газодобывающие предприятия представляют собой сложные комплексы технологических объектов, рассредоточенных на больших площадях и в мало пригодных для проживания регионах страны. Отличительные особенности этих промыслов:
1)непрерывность и однотипность технологического цикла;
2)связь всех технологических объектов месторождения через единый нефтяной пласт;
3) недостаток информации о процессах, происходящих
внефтяных пластах;
4)большая инерционность происходящих в нефтяном пласте процессов;
5)непостоянство пластового притока нефти или газа на месторождение;
6)уникальность условий залегания и состава полезного ископаемого на каждом месторождении.
Для добычи нефти и газа последовательно применяют следующие технологические процессы:
1)бурение скважин для вскрытия продуктивного пласта;
2)транспортировку определенным способом нефти или газа до уровня земной поверхности (технологический процесс добычи);
3)первичную обработку (подготовку) добытого сырья;
4)транспортировку нефти или газа по магистральным трубопроводам к потребителям или на переработку.
6.1. Автоматизация процесса бурения нефтяных или газовых скважин
Бурение скважин является трудоемким и капиталоемким, но необходимым процессом, без выполнения которого невозможна разведка и вскрытие нефтяных и газовых месторождений. Эффективность процесса бурения скважин во многом зависит от его автоматизации, успешное внедрение которой определяется использованием современных средств автоматики.
132
Основная трудность автоматизации бурения нефтяных или газовых скважин заключается в том, что информация о происходящих забойных процессах пока может быть получена только косвенным образом с помощью поверхностной аппаратуры, измеряющей реакцию узлов буровой установки на результат протекания этих процессов. Точность замера результата забойных процессов с помощью поверхностной аппаратуры не всегда достаточна для эффективного управления процессом бурения в автоматическом режиме.
Повысить точность этой аппаратуры можно путем использования сложных алгоритмов, учитывающих одновременно несколько косвенных параметров проявления забойного процесса. Однако это возможно при условии применения в управлении процессом бурения современных вычислительных устройств, в том числе и микропроцессорной техники.
Проходка нефтяных или газовых скважин может выполняться одним из двух возможных способов: роторным или турбинным.
Роторное бурение скважин (рис. 76) применяется на на-
чальном этапе их сооружения, когда они бурятся по относительно слабым и геологически сложным породным горизонтам. При этом способе бурения вращение буровому долоту передается от механизма вращения буровой установки вращением буровой колонны.
Осевое усилие на долото создается частью веса буровой колонны, которая подвешивается с помощью вертлюга и канатной полиспастной системы на буровой вышке. Величина этого усилия регулируется тормозным моментом на барабане буровой лебедки. На этот барабан наматывается канат полиспастной системы подвески буровой колонны. Для удаления продуктов бурения из забойной части скважины во внутреннюю полость буровой колонны подается буровой раствор, плотность которого достаточна для выноса на земную поверхность продуктов разрушения забоя. Этот раствор подается под давлением, которое
133
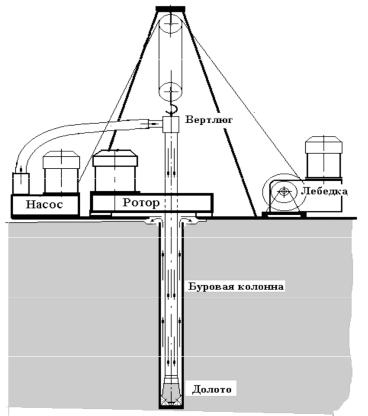
создается буровым насосом. После выноса на устье скважины продуктов бурения буровой раствор очищается от них, дополнительно обрабатывается и вновь закачивается в скважину. Для того чтобы при бурении стенки скважины не подвергались разрушению, они закрепляются специальными трубами, которые называют обсадными. Эти трубы на всей длине скважины соединяются в обсадную колонну.
Рис. 76. Технологическая схема роторного бурения скважин
Турбинное бурение скважин (рис. 77) применяется при больших глубинах бурения.
134
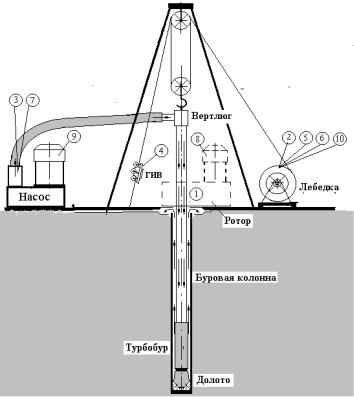
Рис. 77. Технологическая схема турбинного бурения скважин
Особенностью технологии турбинного бурения является то, что буровая колонна в этом случае остается неподвижной, а вращение бурового долота обеспечивается специальным устройством, которое называется турбобуром. Турбобур находится в нижней части буровой колонны и с помощью встроенной в его конструкцию системы турбин преобразует давление бурового раствора в момент вращения долота, жестко связанного с этой системой. После выхода из турбобура буровой раствор омывает забой скважины и, как в предыдущем способе бурения, выносит продукты бурения на устье скважины. В остальном эта технология мало отличается от предыдущей.
135
Разновидностью турбобуров являются электробуры, которые оборудуются асинхронными электродвигателями специальной конструкции, электроэнергия к которым подается по специальному кабелю, расположенному во внутренней полости труб буровой колонны. Момент от этого двигателя через редуктор передается буровому долоту. Сложность этой конструкции состоит в том, что буровой раствор на забой скважины должен проходить через электродвигатель и редуктор.
6.1.1. Регулирование параметров при бурении нефтяных или газовых скважин
Основной задачей системы автоматизации при бурении скважин является автоматическое регулирование независимых параметров, к которым относятся частота вращения долота, оптимальная осевая нагрузка и необходимый расход бурового раствора. От соотношения этих параметров зависит скорость проходки скважины с учетом механических свойств буримых пород и фактической глубины бурения.
При роторном бурении частоту вращения бурового инструмента можно плавно изменять за счет применения асинхронного двигателя с частотным регулированием скорости вращения его якоря. Аналогично возможно менять величину подачи в скважину бурового раствора. Наиболее сложным является процесс регулирования оптимальной осевой нагрузки на буровое долото и частоты его вращения при турбинном бурении, так как в этом случае частота зависит от осевой нагрузки.
При ручном управлении процессом бурения скважины буровой мастер по показаниям приборов с помощью тормоза буровой лебедки устанавливает расчетную для данной глубины бурения величину тормозного момента. При этом на долото должна воздействовать такая часть веса буровой колонны, которая не превосходит предельно допустимого усилия на долото. В процессе самого бурения скважины происходит перераспределение веса буровой колонны, в результате чего возрастает на-
136
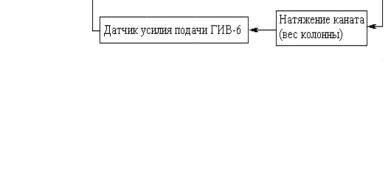
грузка на талевую систему подвески буровой колонны и сокращается ее осевое воздействие на буровое долото. Если осевое воздействие на долото достигнет нижнего предельного уровня, то эффективность бурения резко снизится, поэтому буровой мастер вынужден аналогичным способом снова устанавливать расчетную нагрузку на это долото.
При автоматическом управлении процессом бурения скважины система управления должна постоянно поддерживать расчетную нагрузку на долото на всем интервале рейсового бурения. Автоматическая система управления процессом бурения имеет двухконтурную структуру (рис. 78).
Рис. 78. Структура системы управления нагрузкой на долото при бурении скважины
Одним из контуров управления в этой системе является контур управления нагрузкой на долото. Этот контур имеет приоритет перед другим − контуром регулирования скорости подачи.
Регулирование скорости подачи долота и величины осевой нагрузки осуществляется через тормозную систему буровой лебедки. При этом выходной сигнал элемента сравнения 1 увеличивает тормозной момент этой лебедки, а сигнал элемента сравнения 2 его уменьшает. В случае, если нагрузка на долото не будет превышать заданного значения, контур управления скоро-
137
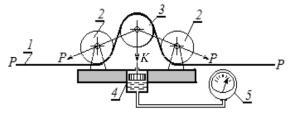
стью бурения будет поддерживать эту скорость на установленном уровне, который является максимально возможным для данного рейсового участка скважины. Если же на этом участке бурения скважины нагрузка на долото при установленной скорости бурения окажется выше заданного значения, то контур управления этой нагрузкой уменьшит ее до установленного уровня, несмотря на то, что скорость бурения при этом меньше заданного значения.
В качестве основных датчиков для системы управления процессом бурения скважины используют: тахогенератор как датчик измерения скорости бурения и индикатор веса типа ГИВ-6 как датчик замера усилия на долоте. Тахогенератор соединен с валом двигателя буровой лебедки, а индикатор ГИВ-6 подвешивается на холостом (мертвом) конце талевого каната.
Датчик ГИВ-6 (рис. 79) состоит из системы трех роликов (блоков), которые огибает талевый канат 1. Блоки 2 жестко крепятся к раме датчика, а блок 3 закреплен на штоке гидроцилиндра 4, поэтому может свободно перемещаться в осевом направлении.
Рис. 79. Схема индикатора веса буровой колонны (датчик ГИВ-6)
При изгибе каната на роликах (блоках) этого датчика происходит разложение усилия в канате на несколько составляющих, одна из которых K воздействует на шток поршня гидроцилиндра 4. Причем это усилие строго пропорционально натяжению каната. В результате этого воздействия в гидроцилиндре возникает давление рабочей жидкости, которое регистрируется
138
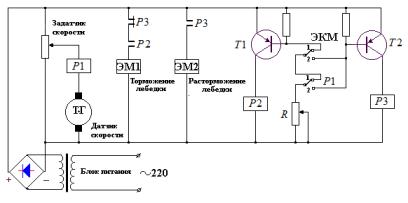
датчиком давления 5. Таким образом, усилие в канате (вес буровой колонны) регистрируется в этом датчике через показания датчика давления.
Представленная на рис. 78 структура автоматической системы управления процессом бурения нефтяных и газовых скважин реализована в аналоговых регуляторах, один из вариантов которых показан на рис. 80.
Рис. 80. Принципиальная схема регулятора подачи бурового долота
Датчиком давления в этой системе является электроконтактный манометр (ЭКМ), встроенный в конструкцию индикатора веса ГИВ-6. Задающий контакт этого манометра устанавливается буровым мастером в положение, соответствующее весу буровой колонны на данном участке бурения скважины с учетом разгрузки на крюке талевой подвески осевым давлением, которое она оказывает на буровое долото, т.е. он фиксирует заданное значение допустимой нагрузки на долото.
В зависимости от положения контактов этого манометра на базы транзисторов Т1 или Т2 через сопротивление R подается открывающий потенциал.
Заданное значение скорости бурения устанавливается потенциометром – задатчиком скорости, движок которого подключен к одному из входов поляризованного реле Р1, другой
139
вход этого реле подсоединен к тахогенератору (ТГ), связанному с валом буровой лебедки.
Электромагниты ЭМ1 и ЭМ2 управляют гидроклапанами привода тормоза буровой лебедки, соответственно увеличивают или уменьшают на ней тормозной момент.
Принцип действия этого регулятора следующий. Если нагрузка на долото не превышает установленного значения, то электроконтактный манометр устанавливает свои контакты в положение 1. Если при этом сигнал тахогенератора будет меньше значения задающего сигнала (скорость бурения меньше заданной), то поляризованное реле Р1 переключит свои контакты тоже в положение 1, в результате чего открывающий потенциал поступит на базу транзистора Т1. При открывании этого транзистора запитывается катушка реле Р2, контакты которого включают электромагнит ЭМ1, в результате чего лебедка растормаживается, увеличивая осевую нагрузку на долото и соответственно увеличивая скорость бурения. Этот процесс продолжается, пока скорость бурения меньше заданного значения или нагрузка на долото не превышает предельного значения.
В случае перегрузки по осевому усилию на долото электроконтактный манометр устанавливает свои контакты в положение 2, в результате этого открывающий потенциал поступит на базу транзистора Т2. При этом запитывается катушка реле Р3, контакты которого включают электромагнит ЭМ2, в результате этого лебедка затормаживается, сокращая нагрузку на долото. То же самое происходит в случае превышения заданной скорости бурения при допустимой нагрузке на долото. Сигнал тахогенератора будет больше значения задающего сигнала, поэтому поляризованное реле Р1 переключит свои контакты в положение 2. При этом открывающий потенциал снова поступит на базу транзистора Т2, что вызовет торможение лебедки и уменьшение скорости бурения.
Аналоговые регуляторы, подобно описанному, выполняют лишь функцию регулирования скорости бурения в соответствии с нагрузкой на долото. Попытки расширить функциональные
140