
книги / Элементы и структуры систем автоматизации технологических процессов нефтяной и газовой промышленности
..pdf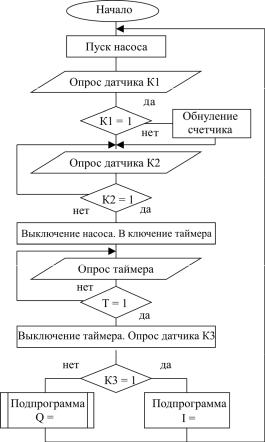
Включение гидронасоса и задвижек на общем коллекторе и на линиизамера производитсясвыходапортадискретноговыхода.
Работа микропроцессорной системы управления процессом замера дебита скважин происходит по алгоритму, представленному на рис. 86.
Рис. 86. Структура алгоритма управления автоматизированной групповой замерной установкой
Алгоритм начинается с пуска привода насоса сигналом модуля дискретного вывода. В результате этого поршень гидроцилиндра 4 ПСМ начинает поворачивать храповик с изогнутым
151
патрубком. Вместе с этим патрубком начинают вращаться и кулачковые диски 1 и 2, которые соответственно включают контакты датчиков К1 и К2. Алгоритмом последовательно проверяются их срабатывания.
При срабатывании датчика К1 завершается полный оборот патрубка переключателя, поэтому счетчик переключений должен быть обнулен.
Дальнейшим ходом алгоритма проверяется положение датчика К2, который срабатывает только тогда, когда подвижный патрубок переключателя переместится на нужный угол поворота. При каждом срабатывании дискретного датчика К2 счетчик системы увеличивает свое содержание на единицу. После срабатывания счетчика на период возврата поршня гидроцилиндра в исходное положение необходимо отключить привод насоса и включить в работу таймер. Возврат поршня под действием пружины 12 происходит в течение работы таймера.
Последовательность дальнейших операций определяется выбором соответствующей подпрограммы. Этот выбор зависит от состояния тумблера (датчика) К3, т.е. от выбора режима замера.
Операции по замеру дебита скважины могут выполняться двояко: последовательным подключением скважин на замер ипроизвольным подключением одной из них по выбору оператора. Если переключатель К3 включен, то скважины подключаются по выбору оператора, при этом алгоритм выполняет подпрограмму I, в противном случае скважины на замер подключаются последовательноиалгоритм выполняет только подпрограмму Q.
Подпрограмма Q предназначена для непосредственного управления процессом замера дебита скважины. Структура этой подпрограммы показана на рис. 87.
Алгоритм этой подпрограммы начинается с циклического опроса состояния газового клапана. Пока этот клапан открыт (ГК=0), жидкая фракция, поступающая во внутреннюю полость сепаратора, постепенно заполняет ее до уровня верхней отметки. При достижении этого уровня происходит закрытие газового
152
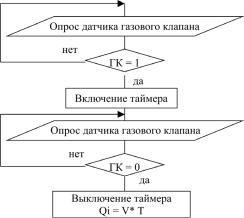
клапана, в результате этого давление во внутренней полости сепаратора начинает повышаться и жидкая фракция вытесняется в коллектор.
Рис. 87. Структура алгоритма (подпрограммы) замера дебита скважины
Процесс вытеснения жидкой фракции продолжается вплоть до открытия газового клапана, которое наступает в момент достижения жидкостью уровня нижней отметки во внутренней полости сепаратора. При выталкивании в коллектор жидкая фракция проходит через датчик расхода, сигнал которого подается к модулю аналогового входа. Одновременно по алгоритму вычисляется расход этой фракции как произведение вытесняемого в общий коллектор ее объема и времени этого вытеснения.
Подпрограмма I предназначена для управления процессом выбора номера скважины, которую оператору нужно поставить на замердебита. Структураэтойподпрограммы показана на рис. 88.
Переход к этой подпрограмме осуществляется включением оператором тумблера К3, подключенного к модулю дискретного ввода и регистрирующего вызов скважины с заданным номером для подключения на замер. Одновременно оператор включает тумблер (с I1 по In) той скважины, которую необходимо перевести на режим замера дебита.
153
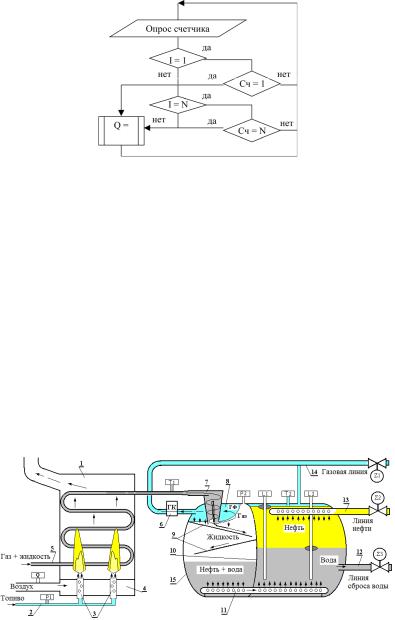
Рис. 88. Структура алгоритма (подпрограммы) замера дебита скважины по выбору оператора
Подпрограмма I первоначально опрашивает содержание счетчика и сравнивает его с номером той скважины, которую поставил соответствующим тумблером оператор на замер. Это сравнение идет в пределах от I1 до In. При совпадении содержания счетчика с номером выбранной скважины происходит переход к подпрограмме Q, а затем и выход в основную программу.
6.2.2. Автоматизация технологического процесса первичной сепарации нефти
Технология первичной сепарации нефти (рис. 89) складывается из процесса ее подогрева до заданной температуры в печи 1 с последующим разделением ее на три фракции: нефть, газ и воду.
Рис. 89. Структура технологического процесса первичной сепарации нефти
154
Подогрев исходной нефтегазовой смеси, которая поступает по трубопроводу 5 от автоматизированной групповой замерной установки (АГЗУ), производится в печи 1 за счет тепла горелок 3, в которых сжигается газообразное топливо в смеси с воздухом, поступающее по соответствующему трубопроводу.
Нагретая смесь через циклон 7 поступает далее в герметичную полость сепарационной емкости 15, которая носит название буллита. В этой первичной полости буллита, на выходе циклона, исходная смесь разделяется на газовую и жидкую фракции.
Газовая фракция с помощью газового клапана 6, создающего внутреннее давление, вытесняется через него из буллита в трубопровод газовой линии 14. При этом газ проходит через соответствующий фильтр 8, который отделяет из него остаточный конденсат.
Жидкая фракция исходной смеси медленно стекает вниз по наклонным поверхностям 9. При этом от нее отделяется остаточная газовая фракция. Жидкая фракция скапливается в нижней части первичной герметичной полости буллита и внутренним давлением через отверстия выталкивается из нее в трубу 11, которая соединяет первичную герметичную полость со вторичной. Эти полости разделены перегородкой 10. Во второй герметичной полости жидкая фракция отстоем разделяется на нефть и воду.
Нефть после отстоя отводится по трубе 13 в нефтяную линию, а вода по трубе 12 в линию сброса воды.
Технологический процесс первичной сепарации нефти контролируется автоматически с помощью первичных датчиков и исполнительных устройств, к которым относятся:
Р1 – датчик давления топливного газа; Р2 – датчик давления в герметичной полости буллита;
Т1 – датчик температуры смеси на входе буллита; Т2 – датчик температуры в герметичной полости буллита; L1 – датчик верхнего уровня нефтяной фракции;
L2 – датчик верхнего уровня водяной фракции;
Q – датчик расхода воздуха, подводимого к горелке;
155
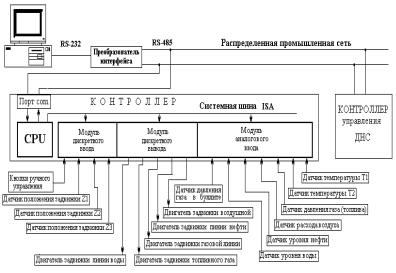
Z1 – Z3 – датчики положения задвижек соответствующих линий.
Управление технологическим процессом первичной сепарации нефтипроизводитсявавтоматизированном режиме (рис. 90).
На верхнем информационном уровне этой системы расположен компьютер оператора, связанный через информационную сеть с функциональными элементами нижележащих уровней.
Рис. 90. Структура системы автоматизированного управления работой установки первичной сепарации нефти
На уровне управления расположены управляющие контроллеры. Один из них управляет процессом первичной подготовки нефти, а другой процессом работы дожимной насосной станции
(ДНС).
Первый из этих контроллеров является контроллером локального типа. Он через процессор CPU связан по системной шине ISA с модулями расширения, к которым подключены соответствующие датчики и исполнительные устройства.
156
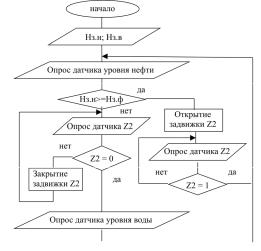
К модулю дискретного ввода подключены все кнопки управления процессом и датчики положения задвижек. Аналоговые датчики температуры и давления, а также датчики уровня и расхода подключены на вход модуля аналогового ввода. Выходные сигналы этой системы формируются модулем дискретного вывода, к которому подключены двигатели всех задвижек.
Работа микропроцессорной системы управления технологическим процессом первичной сепарации нефти происходит по алгоритму, часть которого представлена на рис. 91.
Рис. 91. Часть структуры алгоритма контроля уровня жидкой фракции
После запуска этого алгоритма и ввода задающих сигналов производится опрос аналогового датчика уровня нефти во вторичной камере буллита. Затем этот фактический уровень нефти сравнивается с заданной величиной, и если он превысит это заданное значение, то подается сигнал на открытие задвижки в линии нефти. При этом в цикле типа «пока» производится опрос состояния задвижки до тех пор, пока она не откроется полностью. После открытия задвижки цикл опроса датчика ее положения прекращается и происходит возврат к опросу датчика уровня нефти в буллите.
157
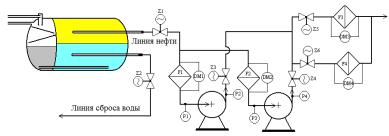
Вследствие открытия задвижки этот уровень должен уменьшаться на заданное значение, поэтому при сравнении заданного и фактического уровней ветвление алгоритма произойдет в направлении «нет». После этого вновь опрашивается датчик положения задвижки, и если она открыта, то снова подается команда на ее закрытие.
На этом этап опроса датчика уровня нефти заканчивается, иалгоритм переходит к опросу датчика уровня воды в буллите. Величинаэтогоуровнярегулируетсяалгоритмомподобнымобразом.
6.2.3. Автоматизация работы дожимной насосной станции
Дожимная насосная станция (рис. 92) после первичной сепарации нефти обеспечивает ее переток к установкам дальнейшего технологического цикла и поддержание там необходимого давления.
Рис. 92. Технологическая схема работы дожимной насосной станции
Основу этой станции составляют центробежные насосы с самозаливкой, к которым нефть поступает из установки первичной сепарации или из резервных буллитов. Закачка нефти в насосы производится через фильтры, которые устанавливаются как на всасывающих, так и на выкидных магистралях этой системы. Станция укомплектована всегда рабочим и резервным насосами Резервируют также фильтры и на ее выкидной магистрали. Включение в работу каждого из насосов или одного из фильтров на выкидной магистрали производится с помощью приводных задвижек, управляемых системой автоматики.
158
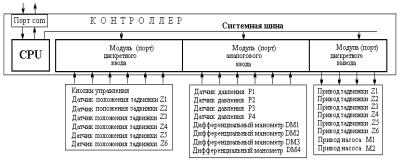
Система автоматизации управления работой дожимной насосной станции не только обеспечивает поддержание заданного давления нефти на выкидной магистрали, но и производит своевременное переключение рабочей линии на резервную в случае выхода из строя рабочего насоса или закупорки одного из рабочих фильтров. Для контроля рабочих параметров в технологической цепочке дожимной насосной станции используют следующие технические средства:
DM1 – DM4 – дифференциальные манометры;
P1, P3 – датчики давления на входе насосов;
P2, P4 – датчики давления на выходе насосов;
Z1 – Z6 – приводы задвижек и датчики их положения; F1 – F4 – фильтры на линии нефти.
Эта аппаратура подключается к соответствующим портам контроллера системы управления дожимной насосной станцией по схеме, представленной на рис. 93.
К модулю (порту) дискретного ввода этого контроллера подключены, как и в предыдущем случае, кнопки управления
идатчики положения задвижек. Аналоговые датчики давления
идифференциальные манометры подключены на вход модуля (порта) аналогового ввода. Двигатели всех задвижек и приводы насосов подключены к модулю (порту) дискретного вывода.
Рис. 93. Структура нижнего уровня системы управления дожимной насосной станцией
159
Алгоритм управления дожимной насосной станцией имеет сложную структуру, состоящую из нескольких взаимосвязанных подпрограмм. Основная программа этого алгоритма представлена на рис. 94.
По этому алгоритму после ввода величины задающих сигналов выполняется цикл ожидания нажатия кнопки «Пуск», после нажатия которой происходит автоматический выбор насоса № 1 и задвижки Z5 в качестве рабочего оборудования технологического цикла. Этот выбор фиксируется присвоением единичного значения константам N и K. По значению этих констант
вдальнейшем будет определен выбор направления ветвления
вподпрограммах алгоритма.
Эти подпрограммы запускаются основным алгоритмом сразу же после подачи команды на открытие задвижки Z1, соединяющей технологическую линию дожимной насосной станции с установкой первичной сепарации нефти. Первая из этих подпрограмм «Пуск насосов» управляет процессом запуска рабочего (или резервного) насоса, а другая подпрограмма «Контроль параметров» производит текущий контроль основных параметров технологического процесса и в случае их несоответствия заданным значениям осуществляет переключения в технологической цепочке этого процесса.
Подпрограмма «Контроль параметров» запускается циклически на всем протяжении рабочего цикла этого процесса. Одновременно в этом цикле производится опрос кнопки «Стоп», при нажатии которой закрывается задвижка Z1. Затем, прежде чем остановить основную программу, алгоритм запускает на выполнение подпрограмму «Останов насоса». По этой подпрограмме выполняются последовательные действия по остановке рабочего насоса.
По подпрограмме «Пуск насоса» (рис. 95) первоначально производится анализ содержания параметра N, которым определен номер рабочего насоса (соответственно N = 1 для насоса № 1 и N = 0 для другого насоса). В зависимости от значения это-
160