
книги / Эффективные строительные материалы на основе гипса и фосфогипса
..pdfти, обусловленные увеличением площади сечения фазовых контактов между кристаллогидратами.
Первый минимум на кривой изменения теплопроводности образцов стандартного изготовления, связанный с началом процесса перекристаллиза ции, наступает раньше (через 4 ч от начала затворения смеси), чем в образцах, сформованных под давлением (см. рис. 3.1). Объясняется это различием ско ростей и длительности процессов гидратации исследуемых систем (см. § 1.4)
Электронно-микроскопические исследования структуры твердой фазы материала стандартного изготовления подтверждают наличие в образцах воз раста до 1 сут процесса перекристаллизации, о чем свидетельствует отсутствие четкой огранки кристаллов (см. рис. 1.18, г) Рост теплопроводности образ цов возраста 4...8 ч (см. рис. 3.1) можно объяснить уменьшением равновес ной прослойки жидкой дисперсионной среды и увеличением сил когезии меж ду частицами кристаллогидратов в результате убыли влаги из системы за счет естественной сушки. Затухание перекристаллизации в образцах суточного воз раста и дальнейшее испарение влаги из материала приводят к упрочнению структуры (подъем кривой = f (г)) вследствие перехода коагуляционных связей в условно-коагуляционные и частично кристаллизационные. Следующее за этим снижение коэффициента теплопроводности на участке 4...8 сут, как и в образцах, сформованных под давлением, обусловлено практически полным замещением влаги в порах материала воздухом. Отличительной особенностью всего последующего периода твердения образцов стандартного изготовления является стабилизация тепловых и прочностных свойств материала [45].
Таким образом, показана взаимосвязь процессов переноса теплоты и вла ги в твердеющей системе и процесса формирования в ней дисперсной капил лярно-пористой структуры.
' Исследована интегральная и дифференциальная пористость прессованного гипсового камня через 1,5 ч, 1, 3, 7 и 16 сут после изготовления образцов из жестких и пластичных смесей, а также образцов стандартного твердения в воз расте 28 сут методами адсорбционной и ртутной порометрии. На основании изотерм сорбции паров воды (рис. 3.3) определялись энергия связи влаги с материалом, удельная изотермическая массоем кость, интегральная и дифференциальная кривые распределения пор по размерам. На рис. 3.4 пред-
Рис. 3.3. Изотермы сорбции паров воды гипсовым камнем, сформован
ным под давлением: |
|
|
1 - в возрасте 1,5 ч; |
2 — 1 |
сут; 3 — |
3 сут; 4 — 7 сут; |
5 — 16 |
сут |
JM____ |
Om-103 |
Дж/моль |
моль1Дж |
Рис. 3.4. Химический потенциал м и удельная изотермическая массоемкость Ст гипсового камня в зависи
мости от его влагосодержания:
1 - м для камня стандартного твер дения; 2 — то же, прессованного кам ня из жесткой смеси; 3 — то же, плаотичной смеси; 4 — С для камня стандартного твердения/77 5 - то же, прессованного из пластичной смеси
ставлены зависимости химического потенциала р и удельной изотермической массоемкости Ст от влагосодержания и для гипсовых образцов стандартного твердения и прессованных на основе жестких [131] и пластичных смесей. Полученные зависимости позволяют проанализировать различные формы свя зи влаги с материалом и установить области перехода адсорбционной влаги в капиллярную: и = 0,4...0,5 % для образца 1 и и = 1,0...1,2 % для образцов
2 и 3. Очевидно, что в гипсовом камне стандартного твердения большая часть
влаги связана |
капиллярными силами, в прессованных образцах велика доля |
адсорбционно связанной влаги. |
|
В первые |
сутки после изготовления происходит интенсивное изменение |
поровой структуры прессованного гипсового камня и значительно увели*
чивается объем пор промежуточных |
размеров (особенно радиуса от 2*10” 9 |
|
до 8*10- 9 м ) . |
|
|
Образцы в возрасте до 1 сут характеризуются максимальным объемом |
||
пор и соответственно минимальной |
прочностью. К трехсуточному |
возрасту |
в образцах происходит уменьшение |
объема пор промежуточных |
размеров, |
Рис. 3.5. Дифференциальные порограммы гипсовых образцов стандартного твердения (?) и прессованных на основе жесткой
(2) и пластичной {3) смесей в возрасте 28 сут
а затем и уменьшение общего объема пор. Таким образом, при хранении прес сованных образцов гипса в естественных условиях в них протекает процесс структурообразования, приводящий к уменьшению общей пористости и увели чению объема малых пор, вызывающий упрочнение материала.
Структура прессованных образцов, полученных на основе жесткой и плас тичной смесей,была исследована также методом ртутной порометрии.
Структурные характеристики, полученные этим методом (рис. 3.5), со гласуются с данными сорбционных измерений. Для образцов серии 2 характе рен резко выраженный максимум на дифференциальной кривой в области г ~1,8*10“ 9 м, а также в области г ^7-10” 9 м.В образце серии 3 преобладают в основном поры с радиусом от 1,8*10-9 до 10_а м, причем максимальное количество пор имеет радиус порядка (1,8...2,5) '10“ 9 м.
3.2. СВОЙСТВА КОМПОЗИЦИОННЫХ ГИПСОВЫХ МАТЕРИАЛОВ
Адгезионные свойства. Адгезия мелкодисперсных частиц (например, пы ли) к поверхности материала обусловлена молекулярными, электрическими и капиллярными силами их взаимодействия [40].
Силы, определяющие адгезионное взаимодействие мелкодисперсных частиц с поверхностью тела, делятся на две группы. Первая группа сил ха рактеризует адгезию частиц до непосредственного соприкосновения их с по верхностью тела (молекулярные и кулоновские силы, значения которых рез ко убывают с увеличением расстояния между взаимодействующими объекта ми) . Силы второй группы возникают при контакте частиц с поверхностью. Это капиллярные силы и силы, обусловленные наличием двойного электриче ского слоя в зоне контакта.
. Молекулярная и капиллярная силы адгезии определяются краевым углом смачивания в поверхности капиллярно-пористого тела. Изменение молекуляр ного взаимодействия контактирующих тел может быть достигнуто путем их модификации. Степень модификации зависит от обработки контактирую щей поверхности определенными поверхностно-активными веществами и контролируется по значению 0. Электрическая составляющая силы адгезии характеризуется способностью материала накапливать заряды статического электричества, т.е. зависит от его удельного объемного pv и поверхностного р5 электросопротивления.
Установлено, что гидрофобизация, т.е. увеличение краевого угла сма чивания, приводит к уменьшению средней силы адгезии [40]. Так, например, увеличение краевого угла смачивания до 85...110° способствует значительно му уменьшению адгезии частиц к поверхности материала.
Для обеспечения слабой адгезии мелкодисперсных частиц к поверхности ма териала в пластичную гипсовую смесь перед прессованием вводились гидрофобизирующие кремнийорганические добавки. Г идрофобность такого материала объясняется образованием на его поверхности пленки, которая имеет опре деленную ориентацию молекул. Степень гидрофобизации поверхности мате риала зависит от типа кремнийорганических соединений и их концентрации [40].
Исследовано влияние различных поверхностно-активных веществ на адге зионные свойства прессованных гипсовых образцов (табл. 3.10). Установлено, что краевой угол смачивания образцов без добавок равен нулю. Введение
ЮЗ
Табл. 3.10. Краевой угол смачивания в поверхности прессованных гипсовых образцов
Добавка |
|
Концентрация |
в , град |
|
добавки, % |
|
|
|
|
|
|
ГКЖ-10 (этилсиликонат натрия) |
0,2 |
31 |
|
|
|
0,5 |
65 |
|
|
1,0 |
85 |
|
|
1,5 |
85 |
|
|
2,0 |
83 |
|
|
3,0 |
72 |
|
|
5,0 |
76 |
Эмульсия ГКЖ-94 50 %-я |
(полиэтилди- |
7,0 |
62 |
хлорсилан) |
|
0,1 |
23 |
|
|
0,2 |
39 |
|
|
0,4 |
58 |
|
|
1,0 |
53 |
Комплексная: 50 %-я эмульсия ГКЖ-94 |
5,7 |
110 |
|
(0,5 %), портландцемент (5 %), двуводный |
|
|
|
гипс (0,2 %) |
|
|
0 |
Алюминиевая пудра |
|
0,05 |
|
|
|
0,5 |
40 |
|
|
1,0 |
43 |
Комплексная: |
|
2,0 |
44 |
|
|
|
|
алюминиевая пудра |
(1 %), |
1,0 |
71 (66) |
1 %-й раствор ГКЖ-10* |
|
|
|
алюминиевая пудра |
(0,5 %), |
0,5 |
71 |
1,6 %-й раствор ГКЖ-10* |
|
|
|
алюминиевая пудра |
(2 %), |
2,0 |
70 |
10 %-й раствор ГКЖ-10 |
|
|
|
алюминиевая пудра (2 %), |
2,0 |
72 |
|
20 %-й раствор ГКЖ-10 |
|
|
|
Раствор полистирола в бензоле*: |
|
|
|
2 %-й |
|
|
50 |
5 %-й |
|
|
66 |
10 %-й |
|
|
70 |
15 %-й |
|
|
61 |
20 %-й |
|
|
77 |
25 %-й |
|
|
61 |
30 %-й |
|
|
67 |
•35 %-й |
|
|
65 |
40 %-й |
|
|
69 |
Раствор ГКЖ-10*: |
|
|
|
6 %-й |
|
|
0 |
10 %-й |
|
|
53 |
20 %-й |
|
|
55 |
30 %-й |
|
|
63 |
Эмульсия ГКЖ-10*: |
|
|
|
6 %-я |
|
|
40 |
10 %-я |
|
|
65 |
20 %-я |
|
|
84 |
30 %-я |
|
|
84 |
*Образцы смачивались раствором, в остальных случаях добавка вводилась
всмесь.
определенных реагентов в материал при затворении смеси приводит к моди фикации его поверхности и изменению гидрофобных свойств в зависимости от вида и концентрации соответствующей добавки. При введении в материал
силикатного клея (объемная |
доля 2...5 %), |
талька (2...5 %), оксида меди |
||
(2...5 |
%), стеариновой кислоты (0,5...2 |
%), |
углерода (1...5 %), глицерина |
|
(1...5 |
%), алюминиевой пудры |
(0,5...2 %) |
краевой угол смачивания поверх |
ности изменяется в пределах от 19° до 63 °. Лучшими гидрофобизаторами ока зались кремнийорганическая жидкость ГКЖ -10 (1...2 %) и эмульсия ГКЖ -94
(0,5...0,7 |
% ). Г ипсовые образцы с этими добавками характеризуются в = 85 °... |
1 7 0 ° и, |
следовательно, минимальными молекулярными силами адгезии. |
Для сравнения укажем, что полированный мрамор характеризуется краевым углом смачивания 6 0 °.
Проведено также исследование краевого угла смачивания гипсовых об разцов при нанесении на их поверхность гидрофобизирующих веществ: раство ров полистирола в бензоле, ГКЖ-10 и 50 %-й эмульсии ГКЖ-94. Растворы опре деленных концентраций наносили на поверхность образцов кистью (100...
200 г/м 2 ), или образцы окунали в раствор. Из табл. 3.10 видно, что наиболее эффективным (в = 84°) является поверхностное покрытие раствором эмуль
сии ГКЖ-94 30 %-й концентрации (150 г/м2 ) .
С целью оценки электрической составляющей сил адгезии определялось удельное объемное и поверхностное сопротивление прессованных гипсовых образцов и образца природного мрамора.
Табл. 3.11. Результаты исследования |
электросопротивления и плотности |
|||||
|
поверхностного заряда гипсовых образцов |
|
||||
Образец |
Концентра |
V ю |
9, |
ps - 10" 9' |
<?,Ю8. |
|
ция добав |
|
|
Кл/м2 |
|||
Ом*см |
Ом |
|||||
|
ки. % |
|||||
|
|
|
|
|
||
Без добавок |
|
7,2 |
|
57;6 |
0,13 |
|
С добавлением |
0,05 |
7,35 |
|
64,5 |
0,22 |
|
50%-й эмульсии |
0,1 |
9,32 |
|
110 |
0,27 |
|
ГКЖ-94* |
0,2 |
11,4 |
|
125 |
0,30 |
|
С комплексной |
0,4 |
12,9 |
|
146 |
0,31 |
|
5,7 |
13,1 |
|
157 |
0,31 |
||
добавкой: эмульсия |
|
|
|
|
|
|
ГКЖ-94 (0,5 %), порт |
|
|
|
|
|
|
ландцемент (5 %), дву |
|
|
|
|
|
|
водный гипс (0,2 %) |
|
|
|
47,4 |
0,09 |
|
С добавлением |
0,5 |
3,6 |
|
|||
ГКЖ-10 |
1,0 |
2,1 |
|
27,2 |
0,07 |
|
Смоченный эмуль |
1,5 |
2,0 |
|
25,4 |
0,05 |
|
|
|
|
|
|
||
сией ГКЖ-94: |
|
|
|
441 |
0,27 |
|
10 %-й |
|
9,4 |
|
|||
20 %-й |
|
9,8 |
|
645 |
0,28 |
|
30 %-й |
|
9,8 |
|
695 |
0,31 |
|
Смоченный раство |
|
|
|
|
|
|
ром ГКЖ-10: |
|
7,3 |
|
13,9 |
0,03 |
|
10%-м |
|
|
||||
20%-м |
|
7,6 |
|
10,7 |
0,02 |
"Добавка вводилась в смесь.
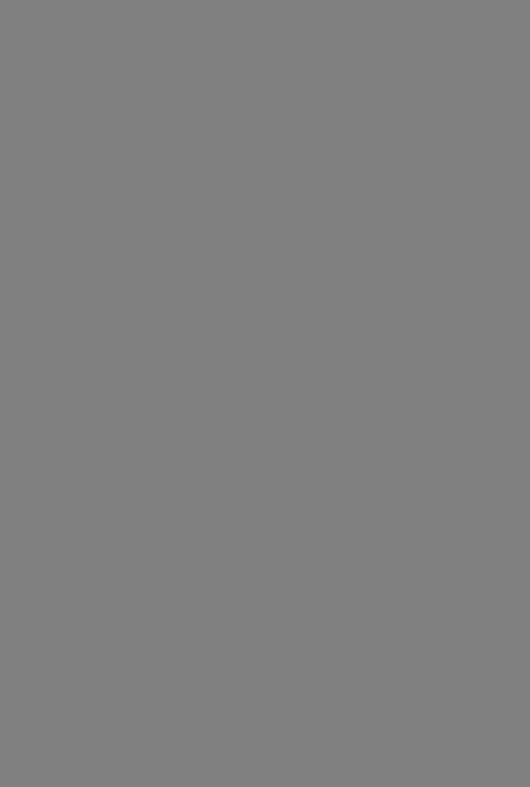
Проведенные исследования позволили заключить, что используемые для замены натурального облицовочного камня прессованные гипсовые мате риалы со специальными добавками обладают значительно меньшей адгезией к частицам пыли, чем образцы природного мрамора [44].
Адгезионные свойства плитных материалов исследованы также экспери ментально с учетом качества и структуры их поверхности (рис. 3.6) методом растровой электронной микроскопии. Пылеудерживающая способность по верхности плит определялась путем сдувания осажденных частиц потоком фильтрованного воздуха с использованием специальной установки [44, 60].
Проведенные эксперименты показали, что при скорости потока воздуха! до 160 м/с сдувается основная масса крупных частиц и около 50 % всех види мых остальных. При скорости потока 200 м/с остается некоторая часть частиц размером менее 7,5 мкм вследствие микронеоднородностей поверхности. Количество удаленных при сдуве частиц пыли зависит ot структуры поверх ности образцов.
Известно, что с уменьшением высоты микронеровностей поверхности вероятность осаждения крупных частиц уменьшается, возможность удаления осевших частиц возрастает. В результате проведенных исследований установ-
Табл. 3.12. Результаты исследования структуры поверхности мраморных
|
|
и гипсовых образцов |
|
|
|
|
Но |
|
Содержание |
Высота |
|
Отношение |
|
мер |
Состав |
компонента, |
микроне |
Характер |
числа удален |
|
об |
|
мае. ч. |
ровностей, |
поверхности |
ных к числу |
|
раз |
|
|
мкм |
|
осажденных |
|
ца |
|
|
|
|
видимых |
|
|
|
|
|
|
частиц, % |
|
|
Мрамор |
|
5...10* |
Гладкая с |
|
75 |
|
|
|
|
плоскими рако |
|
|
|
|
100 |
|
винами |
|
80 |
|
Гипсовое вя |
До Ю |
С бороздка |
|
||
|
жущее |
|
|
ми, кристалличе |
|
|
|
|
100 |
|
ской структуры |
|
100 |
|
Гипсовое вя |
1...3 |
Гладкая , |
|
||
|
жущее; |
|
|
кристаллической |
|
|
|
гк ж -ю |
1,5 |
|
структуры |
|
100 |
|
Гипсовое вя |
100 |
1...3 |
Гладкая по |
|
|
|
жущее; |
|
|
ристая, кристалли |
|
|
|
портландцемент; |
5 |
|
ческой структуры |
|
|
|
двуводный гипс; |
0,2 |
|
|
|
|
|
эмульсия ГКЖ-94 |
0,5 |
|
|
|
90 |
|
Гипсовое вя |
100 |
1...5 |
Пористая, крис |
||
|
жущее; |
|
|
таллической струк |
|
|
|
портландцемент; |
5 |
|
туры |
|
|
|
эмульсия ГКЖ-94 |
0,5 |
|
Слабая порис |
100 |
|
|
Гипсовое вя |
100 |
ДоЗ |
|||
|
жущее; |
|
|
тость,кристалли |
|
|
|
известь; |
3 |
|
ческой структуры |
|
|
|
эмульсия ГКЖ-94 |
0.5 |
|
|
|
|
* Ширина выступов и впадин до 30 мкм.
лено, что по структуре поверхности и адгезионным свойствам гипсовые прессованные образцы Зг 4 и 6 (табл. 3.12) значительно превосходят природ ный мрамор.
На основании проведенных исследований можно заключить, что получен ный прессованный гипсовый материал может быть использован взамен при родного мрамора для облицовки интерьеров помещений со специальными са нитарно-гигиеническими требованиями (обеспыливание среды) [60].
Плотность, прочность и водостойкость. Как видно из табл. 3.13, для ком позиций с пуццолановым и шлакопортландцементом значения средней плот ности и пористости близки к соответствующим показателям для прессован ного камня без добавок. Включения кварцевого песка значительно повышают среднюю плотность материала, введение целлюлозного волокна обусловливает снижение почти на 30 % средней плотности материала при существенном по вышении его пористости.
Эффективное повышение водостойкости прессованных образцов на ос нове гипсового вяжущего достигалось путем сочетания его с доменным шлаком, цементом, гидрофобизирующими добавками. В качестве добавок ис пользовались кремнийорганические жидкости ГКЖ -10 и ГКЖ-94.
Из представленных в табл. 3.14 результатов видно, что прочностные ха рактеристики и водостойкость прессованных композиционных образцов пре восходят эти показатели для литых образцов на основе гипсоцементно-пуццо- лановых вяжущих, имеющих в своем составе высокопрочное вяжущее a-мо дификации [20, 28, 29].
Способ фильтрационного прессования смесей на основе низкомарочного вяжущего (З-модификации позволяет значительно повысить водостойкость гип сового композиционного материала [50] в сравнении с традиционными ком позиционными материалами на основе гипсоцементно-пуццолановых, гипсо-
Табл. 3.13. Физические характеристики прессованных композиционных гипсовых образцов в возрасте 28 сут
Состав исходной |
Содержание |
Средняя |
Истинная |
Пористость, % |
компонента, |
плотность, |
плотность, |
|
|
смеси |
мае. ч. |
кг/м'* |
кг/мЗ |
|
Гипсовое вяжущее; |
70 |
1920 |
2410 |
16,7 |
пуццолановый портланд |
30 |
|
|
|
цемент |
70 |
1850 |
2400 |
17,9 |
Гипсовое вяжущее; |
||||
шлакопортландцемент; |
30 |
|
|
|
ГКЖ-94 |
0,5 |
|
|
13,6 |
Гипсовое вяжущее; |
50 |
2250 |
2486 |
|
песок кварцевый монофрак- |
50 |
|
|
|
ционный |
80 |
|
2480 |
17,1 |
Гипсовое вяжущее; |
2059 |
|||
песок кварцевый |
20 |
|
2187 |
27,6 |
Гипсовое вяжущее; |
85 |
1405 |
||
целлюлозное волокно |
15 |
|
2178 |
30,1 |
Гипсовое вяжущее; |
85 |
1381 |
||
целлюлозное волокно; |
7,5 |
|
|
|
опилки древесные |
7,5 |
|
|
|
Табл. 3.14. Прочностные характеристики и водостойкость композиционных прессованных гипсовых образцов в возрасте 28 сут
Состав исходной |
Содержа |
Предел прочности, |
Ударная |
|
Коэффициент |
|
ние ком^ |
|
МПа |
проч |
размяг |
водо |
|
смеси |
понента, |
|
|
ность, |
||
|
мае. ч. |
при |
при |
кДж/м3 |
чения |
стой |
|
|
сжатии |
изгибе |
|
|
кости |
Гипсовое вяжущее, |
100 |
59,5 |
14,9 |
270 |
0,44 |
0,95 |
известь |
3 |
|
14,7 |
264 |
|
1,2 |
Гипсовое вяжущее, |
100 |
57,0 |
0,71 |
|||
известь, |
3 |
|
|
|
|
|
портландцемент, |
5 |
|
|
|
|
|
эмульсия ГКЖ-94 |
0,5 |
39,3 |
|
220 |
0,73 |
|
Гипсовое вяжущее, |
67 |
8,5 |
1.1 |
|||
доменный шлак, |
33 |
|
|
|
|
|
известь |
3 |
|
|
210 |
|
|
Гипсовое вяжущее, |
67 |
32,3 |
7,5 |
0,85 |
1,15 |
|
доменный шлак. |
33 |
|
|
|
|
|
известь, |
.3 |
|
|
|
|
|
ГКЖ-94 |
0,75 |
37,1 |
8,05 |
210 |
0,81 |
|
То же, но вместо |
|
1.1 |
||||
ГКЖ-94 вводилась ГКЖ-10 |
|
|
|
|
|
|
(0,5 %) |
70 |
59,9 |
12,0 |
320 |
0,65 |
|
Гипсовое вяжущее, |
1.0 |
|||||
шлакопортландцемент |
30 |
|
|
|
|
|
Гипсовое вяжущее, |
70 |
49,7 |
9,75 |
302 |
0,8 |
1.1 |
шлакопортландцемент, |
30 |
|
|
|
|
|
эмульсия ГКЖ-94 |
0,5 |
|
|
|
|
|
шлако-пуццолановых и гипсоизвестковых вяжущих, характеризующихся зна чительным содержанием пуццолановых добавок.
Физико-механические характеристики гипсоволокнистых материалов в значительной степени определяются параметрами прессования, составом смеси и видом составляющих композиций. Как видно из табл. 3.15, повышение
Табл. 3.15. Физико-механические характеристики гипсоволокнистого камня
|
Значение показателя для камн^армированного |
|||
Показатель |
стеклянным |
целлюлоз |
древесными |
целлюлозноволок |
|
волокном |
ным во |
опилками |
нистыми отхода |
|
длиной 5 мм |
локном |
крупностью |
ми и древесными |
|
|
|
1,25 мм |
опилками (1:1) |
Оптимальный процент армирования
Давление прессования, МПа
Средний предел плотности, кг/мЗ
Предел прочности. МПа: при игибе при сжатии
Т еплопроводность, Вт/ (м ?С)
3... |
5 |
10 |
...20 |
10... |
15 |
15 |
ся |
о |
3... |
5 |
5... |
7,5 |
3...5 |
1500...1800 1200...1400 1300...1600 1200...1500
14... |
18 |
12... |
15 |
8,0 |
...10,5 |
8... |
13 |
30... |
40 |
25... |
30 |
18... |
22 |
20..25 |
|
0,5... |
0,6 |
0,2... |
0,3 |
0,3... |
0,4 |
0,2 |
...0,36 |
Значение показателей для плит, получаемых
ПоК 8 3 8 Т 6 Л Ь |
|
по фильт-прессовой технологии |
|
||
литьем |
при распределении заполнителя |
без запол |
|||
|
|||||
|
|
в поверхност- |
в объеме мате- |
нителя |
|
|
|
|
|||
|
|
ных слоях |
риала |
|
|
Предел прочности |
|
|
|
|
|
при сжатии,МПа: |
|
|
|
|
|
через 5 ч |
1,6 |
25,0 |
22,9 |
27,7 |
|
через 28 сут |
7.1 |
53,1 |
46,2 |
59,1 |
|
Предел прочности |
|
|
|
|
|
при изгибе, МПа: |
|
|
|
|
|
через 5 ч |
1.1 |
5,5 |
4,8 |
6,3 |
|
через 28 сут |
3,5 |
10,2 |
9,1 |
17,1 |
|
Водопоглощение, % |
25 |
6,6 |
6,1 |
6,5 |
|
Коэффициент водо |
0,90 |
0,95 |
0,96 |
0,95 |
|
стойкости |
0,4 |
0,45 |
0,52 |
0,42 |
|
Коэффициент раз |
|||||
мягчения |
|
|
|
|
|
2 |
2J |
0,6 |
0,3 |
0,9 |
|
Истираемость, г/см |
|||||
Твердость поверхнос |
2 |
3.5 |
4,5 |
2,5 |
ти, ед (по Моосу)
внешнего давления во всех рассмотренных случаях приводит к повышению
средней плотности материала, Я , . |
Я |
изг |
и адекватному повышению его теп- |
сж F |
|
|
|
лопроводности. |
|
|
|
При изучении свойств гипсопесчаных композиций выяснилось, что введе |
|||
ние монофракционного кварцевого |
песка в поверхностный слой образца |
(25 %), обусловливая некоторое снижение прочностных показателей (по срав нению с прессованным материалом без заполнителя), способствует значитель ному улучшению стойкости к истиранию и твердости поверхностного слоя ма териала. Еще лучшие результаты достигаются при введении заполнителя в смеси с заменой им до 50 % гипсового вяжущего. Физико-механические свой ства гипсопесчаного материала в обоих рассмотренных случаях иные, неже ли литого гипсопесчаного материала (табл. 3.16).
Морозостойкость. Долговечность. В целях определения возможности ис пользования изделий из прессованных гипсовых композиций в условиях по вышенной влажности и для наружных работ проведены их испытания на моро зостойкость и долговечность. Исследование морозостойкости гипсового кам ня проводилось в соответствии с ГОСТ 7025-78.
Испытания образцов на долговечность проводились с имитацией эксплуата ционных воздействий атмосферной среды. Водопроницаемость лицевой по верхности образцов определяли по массе поглощенной воды, приходящейся на единицу площади. Этот показатель являете^ одним из критериев стойкости материала при определении его долговечности. Второй критерий — показатель белизны (коэффициент рассеянного отражения) — определяется с использова нием фотоэлектрического блескомера как отношение белизны материала к бе
л о