
книги / Эффективные строительные материалы на основе гипса и фосфогипса
..pdfТабл. 2.9. Параметры механоактивационной подготовки смесей
и физико-механические свойства получаемых материалов
|
Значения показателя для образца, прессованного из гипсоце |
|||||||
|
ментной смеси по способу |
|
|
|
|
|||
Параметры |
1-стадий |
|
|
3- стадийному |
|
|
||
|
ному |
|
|
|
|
|||
|
|
|
|
|
|
|
||
Содержание компонента |
|
|
|
|
|
|
|
|
в смеси, %: |
|
|
|
|
80 |
|
|
|
молотого природного |
|
|
|
|
|
|
|
|
гипса Новомосковско |
|
|
|
|
|
|
|
|
го месторождения |
|
|
|
|
|
|
|
|
фосфогипса ГХЗ |
|
80 |
91 |
80 |
|
80 |
80 |
91 |
портландцемента |
|
20 |
9 |
20 |
20 |
20 |
20 |
9 |
M400 |
|
|
|
|
|
|
|
|
Параметры активацион |
|
|
|
|
|
|
|
|
ной обработки смесей: |
|
|
200 |
260 |
260 |
300 |
350 |
200 |
ускорение враща |
|
|
||||||
тельного движения |
|
|
|
|
|
|
|
|
измельчающего ор |
|
|
|
|
|
|
|
|
гана при гомогени |
|
|
|
|
|
|
|
|
зации смеси, м/с2 |
|
|
|
|
|
|
|
|
время активации дис- |
|
|
0,2 |
0,25 |
0,5 |
1,0 |
0,5 |
0,1 |
пергацией с истира |
|
|
|
|
|
|
|
|
нием, мин |
|
|
|
|
|
|
|
|
относительный объем |
|
35 |
35 |
40 |
70 |
95 |
60 |
30 |
частиц размером 0,003... |
|
|
|
|
|
|
|
|
•0,07 мм в смеси, % |
|
|
|
|
|
|
|
|
Физико-механические пока |
|
|
|
|
|
|
|
|
затели материала: |
|
|
|
4,7 |
|
|
5,2 |
2,3 |
предел прочности при |
|
1,8 |
2,9 |
28,4 |
7,1 |
|||
сжатии в возрасте |
|
|
|
|
|
|
|
|
7 сут, МПа |
|
|
|
|
|
|
|
|
то же, в возрасте 28 сут |
3,0 |
7,1 |
14,9 |
38,4 |
18,8 |
16,7 |
6,2 |
|
коэффициент раз |
|
0,52 |
0,75 |
0,81 |
0,75 |
0,91 |
0,85 |
0,80 |
мягчения |
|
_ |
|
|
|
|
|
|
морозостойкость,циклов |
25 |
50 |
25 |
75 |
50 |
50 |
||
долговечность, лет |
|
— |
25 |
25 |
50 |
50 |
25 |
20 |
прочность и водостойкость (табл. 2.9), не морозостоек и не долговечен, харак теризуется пористой рыхлой макроструктурой и дефектной микроструктурой.
Механохимическую активацию дву водного гипса с цементом по 3-стадий- ному способу осуществляли следующим образом. Готовили смеси на основе двуводного гипса (фосфогипса) и цемента. При применении смесей на основе молотого природного гипса В/Т принималось равным 0,25. Для составов с фосфогипсом воду в смесь не добавляли, так как имеющийся в фосфогипсе свободной воды хватало для обеспечения удобоукладываемости смеси и протекания химических реакций гидратации цемента. Трехстадийная механоактивационная обработка фосфогипса с цементом включала простое механическое смешение их (например, в двухвальном смесителе), гомогенизацию смеси
с частичным измельчением ксрмков и гранул до отдельных частиц и кристаллов (например, в дезинтеграторе, мелотерке и других аппаратах) и собственно диспергацию со сдвиговой деформацией кристаллов (например, в жерно вых мельницах, двухвалковых разноскоростных смесителях, краскотерках и т.п .).
Наилучшие результаты для фосфогипсовых композиций были достигнуты активацией смеси на измельчающем агрегате при ускорении вращательного движения истирающего органа 300...350 м/с2, а для композиций на природ ном двугидрате — 260 м/с2 . Диспергацию смеси осуществляли в течение 1...2 мин, пока размеры частиц фосфогипса не становились равными 3...
...70 мкм. Исходные частицы фосфогипса характеризовались в среднем в 10...
...30 раз большими размерами. После механохимической активации смесь
подвергали прессованию на |
гидравлическом прессе |
в статическом режиме |
|
с фильтрационным удалением воды прир = 7...10 МПа. |
|
||
Полученные |
по оптимальным режимам механической активации фосфо* |
||
гипсоцементные |
материалы |
в возрасте 28 сут имели |
предел прочности при |
сжатии 14,9... 18,8 МПа, материалы на молотом природном гипсе — 38,4 МПа. Коэффициент размягчения всех изготовленных по 3-стадийному способу ком позиций достаточно высок — от 0,7 до 0,94.
При активации путем диспергации с истиранием происходит измельчение частиц смеси, причем частицы цемента с твердостью по шкале Мооса около 7 единиц являются диспергаторами более мягкого фосфогипса, обладаю щего твердостью 2 единицы. Напряжения, вызывающие сдвиговые деформа ции, могут достигать при этом высоких значений, значительно превышаю щих предел текучести кристаллов гипса, причем минимальное их значение мо жет быть более 500 МПа, а максимальное достигать 1500 МПа. В этих условиях протекает взаимная достаточно глубокая диффузия частиц, что значитель но ускоряет протекание химических реакций, в частности выделение Са (ОН) 2
из цементного клинкера, и нейтрализацию фосфорной кислоты. В таких усло виях в фосфогипсоцементных композициях при небольшой добавке цемента, оптимальных параметрах активационной обработки и фильтрационного прес сования может происходить образование моносульфоалюмината кальция, минуя эттрингитную форму. Для исследованных составов (см. табл. 2.9) эттрингит не был обнаружен как в процессе активационной обработки смеси, так и после прессования образцов во время твердения материала в воздушно сухой и влажной средах.
Полученные экспериментальные результаты хорошо иллюстрируются электронно-микроскопическими исследованиями структуры фосфогипсового
камня. На |
фотографиях (рис. |
2.6) видны |
измельченные до размеров 3... |
7 0 мкм |
частицы фосфогипса, |
покрытые |
гелевидным цементным вещест |
вом, что не наблюдается в механоактивированной системе без добавки цемен та (см. рис. 2.5, г ) . Все исследованные материалы имеют плотную, мелко кристаллическую структуру с покрытием кристаллов и кристаллических бло ков гелеобразной оболочкой из клинкерных цементных минералов. Послед нее обстоятельство и является определяющим для придания гипсовым мате риалам в принципе не присущей им высокой водо- и морозостойкости.
Твердение рассмотренных систем идет с участием структурообразующих
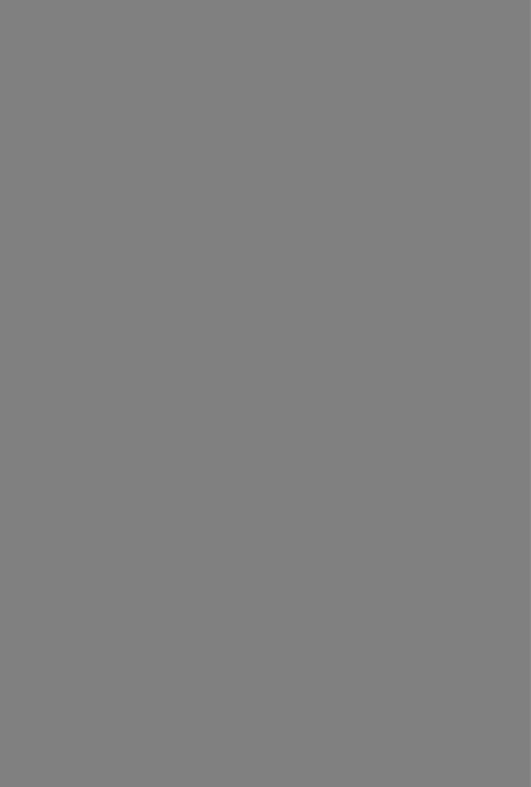
|
|
|
|
|
|
Рис. 2.7. Зависимость предела проч |
||
|
|
|
|
|
|
ности при сжатии образцов на2* |
||
во |
ЮО |
120 |
140 |
160 |
ЛС ’80 |
основе природного двуводного гип |
||
са |
Новомосковского |
месторожде |
||||||
|
|
|
|
|
|
ния |
от давления (/), |
температуры |
15 ' |
25 |
' 35 |
' |
45 |
мин 55 |
(2) |
и продолжительности термо |
|
|
|
|
|
|
|
|
прессования |
(3) |
заданной температуре внешнее давление значительно превышает давление водяных паров, выделяющихся из кристаллогидратов гипса.
Как видно из рис. 2.7, наиболее интенсивный рост прочности образцов при сжатии наблюдался при обработке смеси при температуре 150...170 °С, этому температурному интервалу соответствует также наибольшая степень дегидратации гипса. Дальнейшие исследования по выяснению влияния дав ления прессования и времени выдержки под нагрузкой на прочность образ цов и степень дегидратации гипса были проведены в указанном интервале температур. Прочность образцов резко падает при снижении нагрузки при прессовании (см. кривую 1 на рис. 2.7). Так, при уменьшении давления прес сования со 100 до 50 МПа прочность образцов уменьшается более чем в 2,5 раза. Увеличение же времени выдержки под давлением (кривая 3) в меньшей степени влияет на прирост прочности образцов при сжатии (например, если
при т = 15 мин R |
сж |
= 5 0 |
МПа, при т = 40 мин R |
сж |
= 6 8 МПа, т.е. прирост со- |
_ . _.. |
|
|
|
||
ставляет 34 %). |
|
|
|
|
|
Анализ приведенных |
графических зависимостей позволил выбрать опти |
мальный режим термопрессования, при котором степень дегидратации гипса составляет 98...100 %, давление 80...100 МПа, температура 160...170°С, время выдержки под нагрузкой задается из расчета 1,3...2,0 мин на 1 мм толщины образца.
Исследования, выполненные с использованием петрографического ана лиза с помощью микроскопа МИН-8, показали, что материал сложен из круп
ных |
кристаллов, оптические свойства которых соответствуют полугидра- |
ту |
сульфата кальция. Рентгенографическими исследованиями параметров |
его кристаллической решетки установлено, что полученный термопрессова нием материал представлен а-полугидратом сульфата кальция.
Образование в условиях термопрессования прочных систем на основе полугидрата сульфата кальция можно объяснить следующим. Внешнее дав ление активно способствует процессу дегидратации кристаллов гипса при высоких температурах, а выделяющаяся при этом кристаллизационная во да первоначально выступает в роли смазки, в свою очередь способствующей
более плотной упаковке |
кристаллов полугидратных образований в процес |
се прессования. Так как |
процесс протекает в открытом объеме, но при повы |
шенном внешнем давлении и температуре, превышающей 100 °С, вода вы-
ходит в атмосферу через отверстия в пресс-форме, а образующийся в этих условиях плотный и прочный гипсовый камень представлен в основном а-полугидратной фазой сульфата кальция [130].
Сопоставим некоторые физико-механические свойства термопрессованно го полугидратного камня (табл. 2.10) и материалов стандартного изготовле ния (литьевая технология) на вяжущем Г-4БИ из полугидрата сульфата каль ция ^-модификации Минского завода/ на основе молотого термопрессованно го а-полугидратного камня и полученного способами, описанными в работах
[31,38,72]. |
|
|
Прочностные |
показатели |
полугидратного термопрессованного камня |
(см. табл. 2.10) |
значительно |
выше, чем образцов стандартного изготовления |
на основе вяжущего как (3-, так и а-полугидратной формы. Необходимо от метить довольно высокие физико-механические свойства гипсового вяжу щего, полученного помолом термопрессованного камня, близкие к свой ствам полугидратного материала, являющегося промежуточным продуктом при упрочнении плитных заготовок из природного гипсового камня [31, 72]. Отметим, что прочностные показатели термопрессованного материала также выше, чем дигидратного, изготовляемого из порошка двуводного гипса по схеме дегидратация — гидратация.
Упрочненный гипсовый камень, полученный в соответствии с [31, 32, 62, 72], характеризуется высокими прочностными показателями, приближаю
щимися |
к |
характеристикам описываемого термопрессованного материала. |
|||
Отметим, |
однако, что |
для осуществления процесса по схеме дегидратация |
|||
в открытом |
объеме — |
гидратация |
в водном растворе |
требуются заготовки |
|
природного |
гипсового |
камня с |
высокой начальной |
прочностью (У?^ = |
= 18...26 МПа). Промежуточный а-полугидратный материал имеет более низ кие показатели, чем термопрессованный, сложенный из той же фазы полугид рата сульфата кальция.
Кроме того, полученный из заготовок природного гипсового камня а-полугидратный промежуточный продукт состоит из термодинамически
неустойчивой фазы с высокими |
удельной |
поверхностью (до 9000... |
||
...10 000 см2/г) |
и объемом порового |
пространства (до 14...15 см3/ г ) . При |
||
относительной |
влажности воздуха |
= |
95...100 |
% этот материал вследствие |
интенсивной капиллярной конденсации водяных паров в поровой структуре переходит в дигидрат сульфата кальция со сниженной механической проч ностью [72].
Исследования структурных и массообменных свойств полученного нами термопрессованного гипсового материала показали, что его максимальное гигроскопическое влагосодержание в 4 раза меньше, чем контрольных об разцов из вяжущего а-полугидратной формы, объем промежуточных пор с
радиусом до 0,01 |
мкм почти в 5 раз, а суммарный объем пор в 4 и более |
раза меньше, чем |
в гипсовом камне стандартного твердения. В полученном |
материале преобладают поры размером 0,0018...0,0023 мкм, которые в образ цах стандартного твердения отсутствуют вообще. Таким образом, полученный
в результате |
дегидратации гипса под давлением при определенных термо |
|
динамических |
условиях а-полугидратный материал характеризуется высо |
|
кой плотностью и прочностью, низкой пористостью и невысоким |
водопогло- |
|
щением. При длительном хранении в нормально-влажностных (г = |
(20 ± 2)°С , |
Табл. 2.10. Физико-механические характеристики термопрессованного и упрочненного гипсового камня
|
|
Гипсовый камень |
|
|
|
|
|
стандартного |
стандартного |
полугидрат- |
дигидратный. |
упрочненный**** |
упрочненный**** |
||
изготовления |
изготовления |
ный, полу |
термопрессо |
[31] |
|
[72] |
|
Показатели материала |
из полугид- |
ченный тер |
ванный в за |
|
|
|
|
|
ратного тер |
мопрессова |
крытом объ- |
дигид- |
проме- |
проме- |
дигид- |
|
мопрессован |
нием в от |
еме*** [38] |
ратный |
жуточ- |
жуточ- |
ратньГ |
|
ного камня** |
крытом объ |
|
|
ный по- |
ный по- |
|
|
|
еме*** |
|
|
лугид- |
лугид- |
|
|
|
|
|
|
ратный |
ратный |
|
Средняя плотность. |
1240 |
1380 |
кг/м3 |
|
|
Предел прочности |
4,35 |
13,2 |
при сжатии, МПа |
|
|
Предел прочности |
2,2 |
5,75 |
при изгибе, МПа |
24,7 |
18,9 |
Водопоглощение, % |
||
Пористость, % |
47,1 |
38,5 |
Коэффициент раз- |
0,32 |
0,45 |
мясченив |
|
|
Микротвердость, МПа*
2220...2320
55,1 ...75,9
10,2...15,6
О) со |
00 со |
6,9...10,2
0,52...0,61
4,0...4,5
1603 |
...1810 |
2150...2300 |
|
|
|
|
2010... |
2310 |
13,8... |
34,3 |
50„,70 |
13... |
14 |
8,7... |
13,6 |
28,8... |
60,2 |
2,8...6,9
10,5...13,1
|
|
3.. |
|
.9 |
|
0,32... |
0,51 |
0,5... |
0,6 |
0,5 |
...0,6 |
|
|
4.0... |
5.0 |
8... |
10 |
*Из вяжущего 0-полугидратной формы.
**Из вяжущего а-модификации.
***Йз порошка двуводного гипса.
****Из заготовок облицовочных плит из природного дигидрата сульфата кальция.
Табл. 2.11. Схема структурообразования систем на основе порошка двуводного гипса
|
|
|
|
Процесс |
|
|
Параметры |
термопрессо |
ударное прес |
прокатка |
высокоскорост |
||
вание с дегид |
сование |
|
ная импульсная |
|||
процесса |
|
|||||
ратацией гипса |
|
|
штамповка |
|||
|
|
|
|
|
||
|
|
|
в открытом |
|
|
|
|
|
|
объеме |
|
|
|
Механизм струк |
Негидрата- |
Твердофазовый с пластическими дефор- |
||||
турообразования |
ционный,с пере- |
мациями кристаллов и их "спеканием" |
||||
|
|
|
кристаллизацией |
|
|
|
|
|
|
дигидрата сульфа |
|
|
|
|
|
|
та кальция в полу- |
|
|
|
|
|
|
гидрат |
|
|
|
Структурообра- |
6 ,4 ,8 |
4,7,8,9а |
4,7,8,9а |
4,7,8,9а |
||
зующие факторы |
В полугидрат- |
В дигидратной фазе |
||||
Схема контакте- |
||||||
образования |
|
ной фазе |
|
|
|
|
Р = 60 |
%) |
условиях материал не теряет прочности и не претерпевает суще |
||||
ственных фазовых и химических превращений. |
|
|
||||
Процесс образования структуры термопрессованного полугидратного |
||||||
гипсового |
камня |
(табл. 2.11) протекает по следующей схеме. Вначале идет |
||||
процесс |
дегидратации CaS04 • 2Н20 , завершающийся перекристаллизацией |
дигидрата сульфата кальция в полугидратную фазу (структурообразующий фактор 6 ). Далее с небольшим смещением во времени идет интенсивное кон тактообразован ие в полугидратной фазе в условиях воздействия внешней нагрузки (фактор 4 ). Завершается процесс образованием прочной кристал лической структуры (фактор 8). Отметим, что при повышении внешней на грузки до значений, приближающихся к пределу текучести кристаллов гип са (р > 100 МПа), может наблюдаться начальное пластическое деформиро вание кристаллов двуводного гипса, а после удаления кристаллизационной воды — и кристаллов полугидрата. В предложенной схеме структурообразую щий фактор 7 отсутствует, так как оптимальное давление прессования, харак терное для рассматриваемой схемы, р = 80... 100 МПа.
Для материалов, изготовленных по технологии, предложенной в работе
[38], процесс |
структурообразования идет с участием следующих факторов. |
|
Вначале, как и |
в нашей схеме,''работает*фактор 6 (перекристаллизация |
ди |
гидрата сульфата кальция в полугидрат). Затем полугидрат превращется в дигидрат с участием факторов 3 и 4. Отличие, этой схемы от предложенной нами состоит в разделении во времени процессов дегидратации и гидратации гипса и доминировании гидратационного механизма твердения системы, при чем необходимая для гидратации вода высвобождается в результате дегидра тации дигидрата сульфата кальция.
Структурообразование систем, полученных в соответствии со .способами [31, 72], вначале протекает с участием общего для всех рассмотренных схем
структурообразующего фактора 6. Далее идет гидратация полугидратной фазы в твердом теле в условиях заготовки (монолита), имеющей довольно высокие прочностные показатели, т.е. внутри своеобразной пресс-формы. При этом образование фазовых контактов, согласно [9, 102], должно проте
кать в ''стесненных" условиях с участием |
структурообразующего фактора |
4 (воздействие внешнего давления). В |
процессе структурообразования уча |
ствует также фактор 3, обеспечивающий удержание сближенных частиц твер дой фазы до установления ближней их коагуляции. В обычных условиях для реализации этого фактора необходимо создать в системе развитую коа - гуляционную структуру и обеспечить необходимый уровень пересыщения системы гипсовым вяжущим.
Таким образом, показана возможность получения термопрессованием высокопрочных термодинамически устойчивых полугидратных гипсовых структур (по типу природного минерала— бассанита). Материал такой струк туры характеризуется физико-механическими и структурными свойствами, показатели которых даже превосходят соответствующие показатели для при родного гипсового камня.
Условия и закономерности процесса динамического прессования материа лов системы CaSO^ • 2 Н2О. Выше был рассмотрен способ получения высоко прочного гипсового материала в условиях статического прессования и по вышенных температур. Одним из серьезных его недостатков является боль шая длительность процесса прессования (до 45 мин). С целью устранения этого недостатка были проведены исследования, показавшие принципиаль ную возможность получения прочных кристаллических систем из дисперсного дигидрата сульфата кальция путем их прессования в динамическом режиме.
Для изготовления прессованного гипсового материала непосредственно из CaS04* 2Н20 без перевода его в вяжущее (ангидрит, полугидрат) использо вался лабораторный брикетировочный пресс, снабженный приспособлением для разогрева материала в процессе прессования. Порошок двуводного гипса бри кетировался в динамическом режиме при давлении 90... 100 МПа и температу ре 80...200 °С. Выяснено, что от содержания в исходном материале воды в значительной степени зависит конечная прочность брикетов. Наибольшей проч ностью после распрессовки обладают фосфогипсовые брикеты с исходной влажностью порошкообразного сырья 3 % (рис. 2 .8), несколько ниже проч ностные показатели материала, прессованного при влажности 9 и 12 %, при влажности 17 и 24 % наблюдается значительное снижение указанных показате лей. Брикетированные материалы сохраняют тенденцию к самоупрочнению в процессе естественной выдержки, что можно объяснить, как и для гипсово го камня стандартного твердения, естественной их подсушкой при хранении. При оптимальной влажности исходного порошка CaS04*2H 20 , равной 12 %, исследовано влияние температуры брикетирования на кинетику нарастания прочности получаемого материала (рис. 2.8, б) . Обнаруженная при t = 80 °С тенденция к стабилизации прочности образцов в двухнедельном возрасте со храняется и при других значениях температур брикетирования. Наибольшее значение R при исходной влажности порошка гипсового сырья 3 % соответ ствует температуре брикетирования 80...170 °С (рис. 2.9). С ее увеличением свыше 170 °С наблюдается падение прочности образцов, что особенно заметно при высокой влажности исходного порошка (кривая 7). Количество циклов
Рис. 2.8. Изменение во времени предела прочности при сжатии фосфогипсовых брикети рованных образцов:
а — при t = 80 °С и остаточной влажности фосфогипса 3 % (/), 9 % (2), 12 % (3), 17 %
(4) и 24% (5); б — то же, при исходной влажности фосфогипса 12 % и температурах брике тирования 80 °С (6 ), 120 °С (7), 170 °С (8) и 200 °С (9)
a
6
|
Рис. 2.9. |
Предел прочности при сжатии фосфоги псового камня: |
в - |
в зависимости от |
температуры при р = 100 МПа и влажности фосфогипса 17 % ( /) , |
5 % |
(2) и 3 % (3); б—в зависимости отчисла ударов пресса п при влажности сырья 24 % |
|
|
и температуре прессования 80 °С (4), 120 °С Ы , 220 °С (6) |
прессования |
тоже в значительной степени зависит от температуры прессова |
|
ния. В оптимальном диапазоне температур (80...170°С) оно равно 5...10 |
уда |
|
рам пресса, |
с увеличением температуры количество его ударов может |
быть |
уменьшено до 5...7 без существенного снижения прочностных показатели материала (см. рис. 2.9, б) .
Для интенсификации процесса динамического прессования и достижения эффекта саморазогрева смеси за счет сил трения частиц дисперсного порошка гипса была осуществлена скоростная импульсная штамповка образцов (30...
80 ударов в минуту). Продолжительность импульсного прессования — от 0,1 до 0,8 мин, начальное давление р и в импульсе — от 0,4 до 4,5 МПа, конеч ное р к — от 70 до 145 МПа. При вышеперечисленных параметрах процесса брикетирования температура саморазогрева материала за счет превращения
механической энергии удара в тепловую составляла 80...150 °С |
(табл. 2.12). |
||||
Табл. 2.12. Параметры прессования системы CaS04«2H20 в режиме |
|||||
|
скоростной импульсной штамповки |
|
|
||
Серия образ |
Частота им |
Продолжи |
Начальное |
Конечное |
Температура |
цов |
пульсов, |
тельность |
давление в |
давление в |
разогрева ма |
|
ударов в |
импульсно |
импульсе, |
импульсе, |
териала, °С |
|
минуту |
го прессова |
МПа |
МПа |
|
|
|
ния, мин |
|
|
|
А |
40 |
0,30 |
0,55 |
135 |
80 |
Б |
50 |
0,15 |
1,50 |
80 |
100 |
В |
50 |
0,25 |
3,50 |
120 |
130 |
Г |
60 |
0,15 |
2,00 |
100 |
150 |
Д |
70 |
0,10 |
1,00 |
120 |
110 |
Е |
30 |
0,35 |
0,40 |
145 |
90 |
ж |
80 |
0,80 |
4,50 |
70 |
80 |
При оптимальных влажности исходного порошка дигидрата сульфата кальция (10... 12 %) и режиме процесса (60...70 ударов в минуту, T Q = 0,10...0,15 мин, Рн = 1...2 МПа, р к = 100...120 МПа) обеспечивается получение гипсового мате риала со средней плотностью до 2000 кг/м 3 и пределом прочности при сжатии до 22 МПа. Наибольшая плотность и прочность материала достигаются при наи меньшей продолжительности импульсного прессования и наибольшей частоте импульсов. Показатели механических свойств материала от начального и ко нечного давления в импульсе зависят незначительно. При самых высоких зна чениях внешнего давления (135 и 145 МПа) температура материала достига
ла лишь 80...90 °С, средняя плотность — |
1507... 1550 кг/м 3 и Я ^ — 6,1... |
6,5 МПа. Это обусловлено уменьшением |
(в 1,5...2 раза) частоты импульсов, |
снижением скорости прессования и увеличением продолжительности действия импульса (образцы серий Е и А в табл. 2.12)*. Снижение конечного давления в импульсе до 70 МПа при одновременном повышении начального давления до 4,5 МПа, несмотря на рост количества ударов в импульсе, не обеспечивает разогрев материала до температуры выше 80 °С , получение высоких физико механических показателей материала: средняя его плотность не превышала 1450 кг/м 3 , /?с>й — 5,6 МПа (образцы серии Ж в табл. 2.12). Результаты экспе