
книги / Эффективные строительные материалы на основе гипса и фосфогипса
..pdfХарактеристика
процесса
Механизм твердения
Структурообразующие
факторы
Прессованная система CaS04»2H?Q — вода
с добавками гип |
термоактивиро |
термоактивиро |
сового вяжущего |
ванная с частич |
ванная с полной |
и извести, а также |
ной дегидрата |
дегидратацией |
гидравлическими |
цией дигидрата |
дигидрата суль |
добавками |
сульфата каль |
фата кальция |
|
ция |
|
на основе ди гидрата суль фата кальция
(S |
= 8000... |
уд |
о |
...12 000cMZ/rJ
на основе тон- |
активирован- |
коизмельчен- |
ная механохи- |
ного (S = |
мическим спо- |
= 9000 V |
собом с гидрав- |
11 000 см2/г) ! Т ! С“ И.МИ яо' дигидрата сульбавками
фата кальция с известковыми и др. добавками
Гидратацион- |
Гидратаци- |
ный с созданием |
онный — гид |
искусственным |
ратация полу- |
путем пересыще |
гидратной фазы |
ния и его поддер |
на поверхности |
жанием |
зерна дигидрата |
|
CaS |
1,2, За, 4 ,5 |
2, За, 4 |
Гидрата- |
Негидра- |
Негидрата- |
Гидрата- |
ционный |
тационный с |
ционный с пе |
ционный — гид |
|
перекристал |
рекристалли |
ратация гид |
|
лизацией ди |
зацией диги |
равлического |
|
гидрата |
драта CaS04 |
компонента |
|
CaS04 |
и карбониза |
на поверх |
|
|
ности зерна |
|
|
|
цией извести |
|
|
|
дигидрата |
|
|
|
|
|
|
|
|
CaS04 |
1 ,2 , 3, 4 ,5 |
1 (1а), 2, |
1,2, За, 5к, |
1а, 2, 3,3а, |
|
За, 6 |
6 |
4 ,5 |
При применении фосфогипса вместо природного гипса наблюдается уве личение остаточного В/Т до 0,26...0,28 вследствие значительной дефектности кристаллов двуводного гипса (см. рис. 2.1, а—в) . Особенностями химйкоминералогического и зернового состава, наличием примесей в кристалличе ской решетке и особым характером строения кристаллов фосфогипса можно объяснить и снижение почти вдвое прочности получаемого материала, а также уменьшение в среднем на 20 % коэффициента размягчения по сравне нию с лучшими показателями для композиций на природном гипсе. Показа тели прочности при сжатии образцов на основе борогипса, характеризующего ся еще большим содержанием примесей, были еще ниже.
Дальнейшие исследования были посвящены выявлению стабильности свойств полученного на основе фосфогипса материала во времени. С этой целью в течение длительного временного интервала методами дифферен циально-термического и рентгенофазового анализа изучался фазовый состав материала на образцах оптимального состава. Образцы изготовляли по двум
технологическим схемам, отличающимся порядком введения |
компонентов |
в смесь и технологией предварительного гашения извести. По |
первой схеме |
(серия образцов 1 ) из негашеной извести и воды приготавливалась известко вая суспензия, в которую затем добавляли фосфогипс. В полученную смесь однородной консистенции вводилось гипсовое вяжущее, после перемешива ния в течение 0,5 мин масса укладывалась в пресс-форму и формовалась по заданному режиму. По второй технологической схеме (серия 2) фосфогипс смешивали с водой до однородного состояния смеси, негашеная известь гаси лась в пушонку, которая смешивалась с гипсовым вяжущим. Полученная смесь свежепогашенной извести и гипсового вяжущего тотчас же вводилась в
фосфогипсовое тесто. После перемешивания в течение 0,5 мин оно укладыва лось в форму и прессовалось.
Результаты рентгенофазового и дифференциально-термического анализа свидетельствуют, что основным структурообразующим компонентом в образ цах обеих серий является дигидрат сульфата кальция. С течением времени наблюдается переход гидрата оксида кальция в кальцит. Для образцов серии 1 в возрасте 1 сут фиксировалось также наличие полугидрата сульфата кальция, СаО, С а(О Н )2 . В возрасте 1 года степень карбонизации в образцах составляла 44,5 %. Отличительной особенностью образцов серии 2 является отсутствие в них уже в суточном возрасте оксида кальция и почти полная карбонизация к полугодовому возрасту.
Как указано выше, две технологические схемы получения фосфогипсовых материалов отличаются главным образом тем, что по первой из них для гаше ния извести расходуется гораздо больший объем воды. При этом процесс га шения протекает медленнее.
Во втором случае гашение сопровождается сильным разогревом и разрых лением извести, поэтому продукт (пушонка) получается более дисперсным, выше и степень гидратации. Этим и объясняются различия в результатах исследования образцов двух серий. Учитывая, что процесс карбонизации образцов серии 2 завершается к полугодовому возрасту вместе с ростом их прочности, можно утверждать, что образцы этого и более зрелого возраста состоят из термодинамически устойчивых (равновесных) фаз, что является гарантией стабильности свойств материала во времени.
Изучена возможность замены в разработанной фосфогипсовой компози ции 0-полугидрата сульфата кальция на низкоактивный 0-растворимый ангид рит — обожженный фосфогипс Гомельского химического завода (см. табл. 1.3, 1.5), предназначенный для производства гранулированного фосфогипса для цементной промышленности. Можно было без существенного ухудшения свойств прессованного материала использовать в композиции 70 % отваль ного и 10 % обожженного фосфогипса. Однако одним из серьезных недостат ков этой композиции является значительное (20 %) содержание негашеной извести, которая, являясь в основном структурообразующей добавкой, служит и для нейтрализации фосфогипса.
Показано, что при введении извести (более 2 %) в смесь гипсового вяжу щего с водой замедляются сроки схватывания смеси. В то же время для осу ществления нейтрализации фосфогипса в жидкой пульпе/ по данным работы [26],требуется не более 1 % гашеной извести (в пересчете на сухое вещество). Исходя из этих соображений, в композиции негашеная известь (до 3 %) была заменена гашеной при одновременном введении в смесь ряда химических добавок.
Добавление извести к обожженному фосфогипсу даже в самых незначи тельных дозах обусловливает резкое замедление схватывания и в некоторых случаях приводит к полному несхватыванию смеси. Поэтому в смеси на ос нове отвального и обожженного фосфогипса, нейтрализованные известью, необходимо дополнительно вводить химические добавки, ускоряющие схва тывание [80, 87, 91]. Был проведен комплекс опытов, в которых в фосфогипсовые смеси вводили соли серной, соляной, азотной и других кислот, квас цы, нитрит натрия и др. При этом исследовали различные варианты последова
тельности введения указанных компонентов |
в смесь и варьировали их дозы. |
||
Получены образцы высокой прочности |
(Я |
= 11,9 МПа в возрасте 1 сут) со |
|
средней |
плотностью 1650 кг/м 3 при |
низком содержании гашеной извести |
|
(0,6 %) |
и незначительном содержании химических добавок (не более 1 %). |
||
Изучена возможность полной замены извести в фосфогипсовых компо |
зициях другими добавками. Для этого использовали известные ускоряющие твердение и нейтрализующие добавки первого и второго классов согласно [87] как в отдельности, так и в сочетании друг с другом. Введение добавок такого рода одновременно способствует нейтрализации смеси и положительно сказывается на прочности изделий. Наибольшая прочность образцов (до 19 МПа в возрасте 1 сут) достигается при сочетании ряда солей угольной и борной кислот. В первом случае с отвальным фосфогипсом, как правило, предварительно перемешивается карбонат калия, во втором случае — бикар бонат натрия. Дополнительные добавки, вводятся в смесь в конце переме шивания смеси вместе с обожженным фосфогипсом. В таких композициях достигается высокая степень нейтрализации фосфогипсовых смесей (pH = = 6,2...6,5).
Проведенные исследования позволили в композиции, содержащей 70 % отвального фосфогипса, 20 % негашеной извести и 10 % гипсового вяжуще го, заменить последние два компонента на менее дефицитный слабоактивный обожженный фосфогипс - 0-растворимый ангидрит. Введение в предложенную новую композицию небольших доз (не более 1...2 %) химических добавок
позволяет ускорить процесс твердения и обеспечить глубокую нейтрализацию фосфогипсовых смесей.
Таким образом, на основе дигидрата сульфата кальция получены стойкие во времени прессованные материалы с пределом прочности при сжатии поряд
ка 30 |
МПа (на основе природного гипса) и до 19 МПа |
(на основе фосфогип- |
са). К |
числу недостатков этих материалов относится |
их низкая водостой |
кость.
Для повышения водостойкости полученных материалов в качестве добав ки, регулирующей уровень пересыщения жидкой фазы, представлялось целе сообразным .вводить в смеси компонент, гидролизирующийся при смешении с водой с выделением гидроксида кальция. В этом случае механизм структурообразования системы остается прежним, как и в случае введения извести, однако в процессе твердения системы в ней появляется новая составляющая (гидросиликаты кальция), обусловливающая качественно новые свойства материала — повышенную водостойкость.
Всырьевую смесь на основе двуводного гипса вводили компоненты гид равлического твердения, перед формованием смесь выдерживали до установ ления pH жидкой фазы в пределах 8...11,после чего в нее добавляли гипсовое вяжущее.
Вкачестве гидравлического компонента можно использовать алит, пуццо лановый цемент, шлакопортландцемент,портландцемент, низкоалюминатные цементы, гидравлическую известь, белитосодержащие отходы промышлен ности.
Установлено, что оптимальное содержание гипсового вяжущего, необхо димое для создания требуемого пересыщения в системе, составляет 10...20 % (табл. 2.6).
Часть образцов твердела в воздушно-сухой среде, а часть — во влажной
(у>= 100%).
Существенное значение при составлении смеси на основе фосфогипса име ет последовательность введения компонентов в смесь, так как добавки гид равлических вяжущих, кроме указанного выше назначения, играют роль нейт рализаторов кислых примесей, присутствующих в фосфогипсе. В связи с этим было опробовано четыре следующих варианта замеса: 1) фосфогипс
затворяли |
водой, добавляли сухие гидравлическое и гипсовое вяжущие, пе |
||||
ремешивали смесь; |
2) фосфогипс затворяли водой, отдельно гидравлическое |
||||
вяжущее, |
после их |
перемешивания |
в смесь вводили гипсовое вяжущее; |
||
3) фосфогипс затворяли |
водой, |
отдельно сухие гидравлическое и гипсовое |
|||
вяжущие, |
перемешивали |
смесь; |
4) |
гидравлическое вяжущее затворяли во |
дой, на полученной суспензии затворяли фосфоги/ic, затем добавляли гипсовое вяжущее и перемешивали смесь. i Анализ результатов проведенных опытов показал, что лучшими являются !
варианты замесов 3 и 4, при которых гидравлическая составляющая вводится в смесь в виде водного раствора. Соотношение компонентов — фосфогипса, гидравлического компонента (портландцемента) и гипсового вяжущего - в этих смесях оптимально.
Наилучшие показатели по прочности и водостойкости показали образцы,
твердевшие во влажной среде. |
Прочность при |
сжатии образцов в возрасте |
28 сут для 3-го варианта замеса |
составляет 20,7 |
МПа, этот показатель для об- |
Табл. 2.6. Составы фосфогипсовых композиций и их показатели (при воздушном хранении)
Состав композиций |
Содержа- |
pH смеси |
Коэффи |
Предел прочности |
ние компо |
|
циент раз |
при сжатии образца |
|
|
нента, % |
|
мягчения |
в возрасте 28 сут# |
|
|
|
|
КП П |
Молотый природный гипс; |
60 |
11 |
0,81 |
18,2 |
3Ca0*Si02 (клинкерный мине- |
30 |
|
|
|
рал); |
10 |
|
|
|
гипсовое вяжущее |
|
|
|
|
Фосфогипс ГХЗ; |
60 |
8,0 |
0,67 |
19,6 |
шлакопортландщемент; |
30 |
|
|
|
гипсовое вяжущее |
10 |
|
|
|
Фосфогипс ГХЗ; |
70 |
11,0 |
0,68 |
24,8 |
клинкерный цемент; |
10 |
|
|
|
гипсовое вяжущее |
20 |
|
|
|
Фосфогипс ГХЗ; |
70 |
10,5 |
0,59 |
21,3 |
гидравлическая известь; |
15 |
|
|
|
гипсовое вяжущее |
15 |
|
|
|
Цитрогипс; |
60 |
9,8 |
0,62 |
24,1 |
пуццолановый цемент; |
30 |
|
|
|
гипсовое вяжущее |
10 |
|
|
|
разцов в водонасыщенном состоянии снижается до 15,1 МПа. С течением вре мени прочность образцов нарастает и в годичном возрасте достигает 28 МПа (при смешении компонентов по схеме 4 ). Для водонасыщенных образцов этот показатель ниже — 25 МПа. Коэффициент размягчения в случае введения в качестве гидравлической добавки портландцемента составляет^ 0,88 для об разцов возраста 28 сут и 0,91 для образцов годичного возраста.
Коэффициент размягчения всех исследованных композиций растет при влажном хранении образцов (вплоть до годичного их возраста) в отличие от не водостойкой (фосфогипсовой композиции с добавками извести и гипсового вяжущего. Это свидетельствует о длительности процесса гидратации гидравли ческого компонента смеси и интенсивном образовании гидросиликатов каль ция, обладающих повышенной водостойкостью.
Микроскопическое исследование структуры образцов (рис. 2.5) показы вает, что материал сложен кристаллами исходного фосфогипса, срастание между которыми обеспечивается гелевидной массой, появляющейся в результа те гидратации цемента или алита, а также вторичными кристаллами гипса. В случае смешения компонентов по схеме 1 представленные цементной фазой новообразования развиты очень слабо и локализованы в основном в поровом пространстве системы. В случае замеса по схеме 3 цементные новообразо вания располагаются как в контактной зоне между кристаллами, так и на по верхности кристаллов фосфогипса, наблюдаемое при этом покрытие кристал лов гипса гелевидным веществом равномерное и повсеместное. Для всех об разцов характерно наличие единичных кристаллов эттрингита, исчезающих
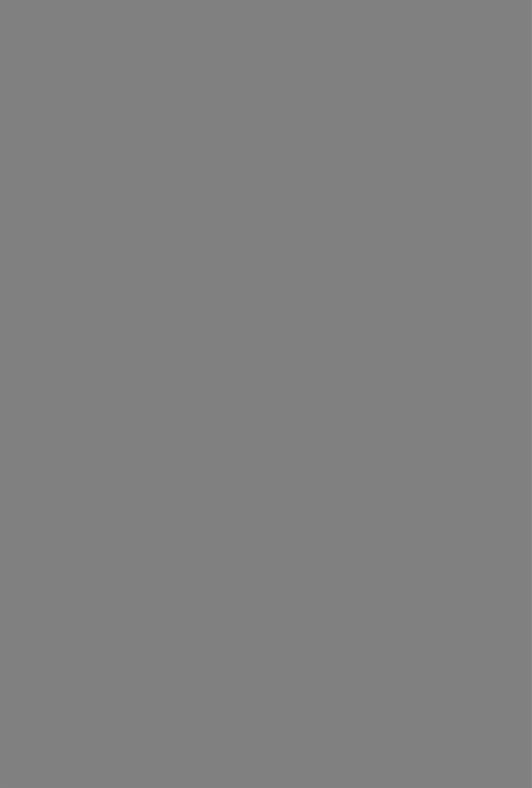
Изделия на основе гипсовых вяжущих с повышающими их водостой кость добавками цемента не долговечны вследствие образования в них эттрингита (трехсульфатной формы гидросульфоалюмината кальция). Показано [16# 20, 28, 29], что для стабильности прочностных свойств материала во вре мени необходимо в гипсоцементную смесь вводить активную кислую мине
ральную добавку. |
|
|
Нами предложено вместо введения пуццолановой |
добавки выдерживать |
|
смесь двуводного гипса и цемента до установления |
в ней pH = |
после |
чего добавлять гипсовое вяжущее и формовать изделия методом |
фильтра |
ционного прессования. Достижение указанного уровня pH жидкой фазы до формования изделий является необходимым для предупреждения образова ния в дальнейшем эттрингита в затвердевшей структуре отпрессованного изделия. При этом существенным является то, что указанная выдержка гип соцементной смеси возможна лишь для смесей на основе двуводного гипса, которые практически не схватываются.
Время установления требуемого pH жидкой фазы оказалось разным для различных исходных композиций. Для систем с пуццолановым цементом оно меньше, чем с портландцементом. В случае использования вместо молотого двуводного гипса фосфогипса оно ограничивается лишь временем перемеши вания смеси, так как кислые примеси, содержащиеся в фосфогипсе, сразу обеспечивают в системе условия, при которых становится невозможным образование высокосульфатной формы гидросульфоалюмината кальция.
Проведенные нами исследования |
фосфогипсопортландцементных составов |
(с содержанием цемента до 30 %) |
показали, что содержание в них СаО в воз |
расте 7 сут в 20...30 раз ниже допустимого по ОСТ 21-29—77 — 0,85 г/л. При этом цемент выполняет не только роль добавки, обеспечивающей водостой кость материала, но и является регулятором (подобно извести) уровня пе ресыщения жидкой фазы, необходимого для твердения системы на основе двуводного гипса.
Таким образом, в общем случае процесс структурообразования оводненных систем на основе дигйдрата сульфата кальция протекает, как при тверде нии системы на основе полуводного гипса, с участием первых пяти структуро образующих факторов (см. табл. 2 .5). Не в полной мере проявляется структу рообразующий фактор 3 вследствие отсутствия процесса выкристаллизации из раствора гидратных новообразований. Здесь действует фактор За, обуслов ливающий сближение исходных частиц твердой фазы. Для смесей жесткой консистенции на основе частично дегидратированного фосфогипса [65] также характерен гидратационный механизм структурообразования — гидратация полугидратной фазы на поверхности зерна дигидрата сульфата кальция и отсут ствие самоупрочнения во времени (структурообразующий фактор 5).
Структура систем на основе механоактивированного дигидрата сульфата кальция. Возможность твердения оводненного тонкоизмельченного природ ного двуводного гипса, так называемого безобжигового гипса, была впервые установлена в [4]. В работах [2 7 ,3 6 ,3 7 ] исследована зависимость водопот ребности,сроков, схватывания безобжигового гипса и конечных физико-меха нических характеристик затвердевшего материала от тонкости помола вяжу щего и наличия химических добавок.
Показано [103, 104], что помол фосфогипса в различных агрегатах исти
рающего, ударно истирающего |
и ударного действия до размера частиц поряд |
|
ка |
3...15 мкм и формование |
жестких смесей при давлении прессования до |
80 |
МПа позволяют получать |
камень с пределом прочности при сжатии до |
22 |
МПа для сухих образцов и коэффициентом размягчения до 0,28. Прило |
жение нагрузки к системам на основе измельченного ди гидрата сульфата кальция способствует сближению частиц гипса, ускорению процесса структурообразования и повышению физико-механических показа телей материала. К числу самых серьезных недостатков безобжигового гипса относится очень низкая водостойкость получаемого материала, а также тех нические сложности, возникающие при сверхтонком измельчении гипса до удельной поверхности 10 000...12 000 см2/г.
Наиболее рациональным является использование для производства мате риалов на основе безобжигового гипса различных гипсосодержащих промыш ленных отходов. Особенно перспективно использование мелкодисперсного фосфогипса, домол которого можно выполнить при пониженных энергоза тратах и в более короткие сроки. Применение же фильтрационного прессова ния позволяет использовать фосфогипс в его естественном высоковлажном состоянии без предварительного обезвоживания перед помолом и последую щего увлажнения, как в случае использования молотого природного гипса.
Исследования были начаты с механоактивационной обработки вторично го гипса — отходов производства сухой гипсовой штукатурки и гипсокартон
ных листов.
В опытах использовались отходы производства гипсокартонных листов Минского завода. Исходными материалами при их производстве служили гипсовые вяжущие марок Г-4 — Г-6 и картон облицовочный,удовлетворяющий требованиям ГОСТ 8740-85. Содержание картона в готовом высушенном изделии составляло в среднем 0,06 от массы двуводного гипса. Предваритель но отходы дробили до кусков размером 4...7 см, затем осуществляли помол их в шаровой мельнице.
Была исследована возможность измельчения гипсокартонных отходов как сухим способом, так и мокрым. Сухой помол отходов оказался неэффек тивным по двум причинам: вследствие налипания порошка к поверхности мелющих тел и стенкам помольной камеры и невозможности сухого дисперги рования в шаровой мельнице. Для осуществления мокрого помола дробленые куски отходов предварительно замачивались в воде в течение 1...3 сут. Затем они загружались в мельницу и подвергались помолу до удельной поверхности 9000 см2/г. Предварительная выдержка гипсового камня в воде, ведущая к снижению прочности межчастичных контактов, значительно облегчила про цесс тонкого его измельчения. В процессе мокрого помола гипсокартонных отходов происходит распушение картона и равномерное распределение его во локон в объеме материала. По сравнению с сухим помолом значительно улуч шалось качество и ускорялся процесс измельчения получаемого продукта.
На основе молотых гипсокартонных отходов без добавок и с добавками готовили тесто нормальной густоты. Затворенное тесто укладывали в прессформу и прессовали по режиму: подъем давления до 10 МПа в течение 1 мин и выдержка под давлением в течение 3 мин. Испытывали как воздушно-сухие, так и водонасыщенные образцы, полученные путем фильтр-прессования. Все образцы обладали достаточно высокой распалубочной прочностью и не нужда-
Табл. 2.7. Прочность при сжатии образцов в зависимости от их исходного
|
|
состава и условий хранения |
|
Н0Мер |
Компонент |
Содержание |
Предел прочности при сжатии |
состава |
компонентов, |
образцов в возрасте 7 сут, МПа |
|
|
|
% |
' _ |
1 II
Ша
1116
Ills
111 г
|
|
воздушно- |
водонасыщен- |
|
|
сухих |
ных |
Молотые отходы |
100 |
22,8 |
0 |
Молотые отходы;, |
60 |
|
|
гипсовое вяжущее Г-5 ВII |
40 |
10,4 |
0 |
Молотые отходы; |
60 |
14,9 |
5,7 |
известь-пушонка; |
40 |
|
|
' Молотые отходы; |
75 |
15,6 |
5,5 |
известь-пушонка |
25 |
|
|
Молотые* отходы; |
85 |
17,1 |
4,6 |
известь-пушонка |
15 |
|
|
Молотые отходы; |
93 |
20,1 |
4,5 |
известь-пушонка |
7 |
|
|
лись в принудительной сушке. Как видно из табл. 2.7, наибольшей проч ностью обладают образцы из молотых гипсокартонных отходов без добавок. Однако при водонасыщении они размягчаются и полностью теряют прочность.
При введении в смесь гипсового вяжущего снижается прочность образцов (более чем в 2 раза), а свойства водонасыщенных образцов не улучшаются. Добавление свежепогашенной высокодисперсной извести-пушонки также при водит к снижению прочности образцов воздушно-сухих (чем больше содержа ние добавки, тем ниже прочность), однако при этом резко улучшаются пока затели водонасыщенного материала.
Свойства образцов с наибольшим содержанием добавки извести (состав 111а) исследовались в течение длительного времени (табл. 2.8). Часть образ цов указанного состава в возрасте 28 сут была подвергнута 30-кратному водонасыщению и высушиванию. В результате коэффициент размягчения вы рос более чем на 20 %, поверхность образцов стала более твердой (твердость по шкале Мооса составляет 3 единицы) и глянцевой. Повышенную водостой кость полученного материала можно, по-видимому, объяснить образованием в результате взаимодействия извести и диспергированных волокон картона (полуцеллюлозы и сульфатной целлюлозы) водонерастворимых компонентов, обволакивающих зерна гипса. Подтверждением этого является то обстоятель ство, что идентичные образцы, изготовленные из тех же отходов с известью, но без добавок картона, не водостойки.
Достоинствами полученного прессованием материала является его сравни тельно невысокая средняя плотность и повышенная прочность при изгибе, обусловленная наличием равномерно распределённых армирующих волокон картона.
Таким образом, из активированных гипсокартонных отходов с добавкой извести фильтрационным прессованием получен материал с высокими механи ческими показателями как при твердении в нормально-влажностных условиях, так и в состоянии водонасыщения.
Процесс структурообразован ия в активированной системе на основе ди-
Табл. 2.8. Изменение физикомеханических свойств образцов состава 111а во времени
Показатель |
|
Показатели свойств образцов в возрасте |
|
||||
1 сут |
7 сут |
28 сут |
2 месяцев |
4 месяцев |
1 года |
||
|
|||||||
Предел прочности при |
11,8 |
14,9 |
19,6 |
20,2 |
20,7 |
22,3 |
|
сжатии воздушно-сухого об |
|
|
18,5* |
|
|
|
|
разца, МПа |
|
|
|
|
|
||
|
5,7 |
8,6 |
11,0 |
12,0 |
15,4 |
||
Предел прочности при |
|
||||||
сжатии водонасыщенного |
|
|
10,0* |
|
|
|
|
образца, МПа |
|
|
|
|
|
||
|
8,0 |
|
|
|
11.0 |
||
Предел прочности |
|
|
|
|
|||
при изгибе, МПа |
|
0,38 |
0,44 |
0,54 |
0,58 |
0,69 |
|
Коэффициент раз |
|
||||||
мягчения |
|
|
0,54* |
|
|
1490 |
|
Средняя плотность, |
|
1320 |
1360 |
|
|
||
кг/мЗ |
|
30 |
25 |
|
|
17 |
|
Водопоглощение, % |
|
|
|
^Образцы, подвергнутые дополнительному 30-кратному водонасыщению и высушива
нию.
гидратных гипсокартонных отходов с добавлением высокодисперсной извести протекаете участием факторов 1, 2, За и 6 (см. табл. 2 .5). Также можно го ворить о проявлении дополнительного структурообразующего фактора 5к, способствующего длительному упрочнению материала и повышению его водо стойкости во времени. Последний фактор относится к долговременным факторам структурообразования, как и фактор 5, обусловливающий поддер жание необходимого уровня пересыщения жидкой фазы в отформованном материале и длительность процесса гидратации полугидрата сульфата каль ция (см. табл. 1.1 и 2.5) Однако в рассматриваемом случае упрочнение систе мы протекает вследствие карбонизации известковой добавки (степень карбо низации в возрасте 1 года достигает 67 % ), так как система на основе механоактивированных гипсокартонных отходов не содержит полугидратной фазы и процесс гидратации, как таковой, в ней не протекает.
Цель дальнейших исследований — повышение водостойкости материалов на основе измельченного двуводного гипса путем введения гидравлических добавок. Необходимо было найти способ механохимической активации смеси, обеспечивающий, помимо высоких прочностных показателей получаемого материала, повышение его водостойкости за счет покрытия частиц двувод ного гипса оболочкой из клинкерных цементных минералов. Если в случае частичной дегидратации химически активной клеящей прослойкой служит дегидратированная оболочка самого гипса [65, 66] ,тов рассматриваемом слу чае связующим будет являться клеящая оболочка совершенно другого веще ства, придающего системе качественно новые гидравлические свойства (повы шенные водо- и морозостойкость), не присущие материалам на основе гип сового вяжущего воздушного твердения.
При простом механическом смешении измельченного двуводного гипса с цементом (по 1-стадийному способу) прессованный материал имеет низкую