
книги / Технология машиностроения.-1
.pdf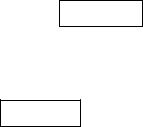
|
Z3 =52,31+ 28,65 −80,45 =1,51, |
|||||
|
∆SZ3 |
= 1,8 + 0 – (–0,35) = 2,15. |
||||
Следовательно, |
Z3 |
=1,51+2,15 |
. |
|
||
|
|
|
|
−1,11 |
|
|
В) |
[Z2 ] =(S1 +З3 ) −S2 |
(Z2min =0,4 мм), |
||||
|
|
|
→ |
← |
|
|
|
|
|
увел. |
уменьш. |
|
Z2min = S1min + З3min −S2max ,
З3min = 0,4 – 28,44 + 140 = 111,96 мм.
Технологический размер З3 =112,96+−21 .
Z2 = 112,96 + 28,65 – 140 = 1,61, ∆SZ2 = 2 +0 – (–0,8) = 2,8,
Следовательно, Z2 =1,61+−2,81,21 .
Такого рода расчеты выполняются на этапе проектирования технологических процессов, для назначения обоснованных допусков, предельных отклонений, выполняемых технологических размеров.
Контрольные вопросы по главе
1.Понятие многопереходной обработки.
2.Какие размеры могут быть замыкающими в технологических размерных цепях?
3.В какой последовательности производится расчет технологических размерных цепей?
4.Как определяется минимальное значение припуска?
5.Как производится расчёт размеров заготовки?
101
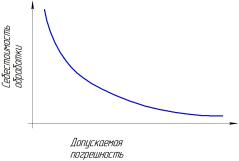
9. ТОЧНОСТЬ ОБРАБОТКИ ДЕТАЛЕЙ
Точность – основная характеристика деталей машин. Точность, обеспечиваемая механической обработкой, обусловливается многими факторами и состоит:
•из погрешностей действительных размеров деталей;
•из погрешностей формы обработанных поверхностей или её отдельных элементов;
•из погрешностей взаимного расположения поверхностей и осей детали.
Трудоемкость и себестоимость обработки детали (конкретной)
взначительной степени зависят от требуемой точности и при повышении точности (при неизменных прочих условиях) увеличиваются
(рис. 9.1).
Рис. 9.1. Зависимость между себестоимостью и точностью обработки
Точность заготовок, методы предварительной и окончательной механической обработки, методы термической обработки значительно влияют на точность окончательно обработанных деталей:
• чем выше точность заготовок, тем меньше число операций их механической обработки (меньше установок, меньше переходов) и тем выше точность готовых деталей;
102

• точность геометрической формы деталей повышается при использовании более совершенных методов механической обработки; обработку ведут на станках с «экономической точностью».
«Экономическая точность» достигается в стандартных производственных условиях (исправные станки, необходимые оснастка и инструмент, нормальная квалификация рабочих) при минимальной себестоимости.
«Достижимая» точность – это максимальная точность, которую можно достичь на данном производстве, не считаясь с себестоимостью обработки.
Виды допусков формы |
|
|
• Отклонение круглости (допуск круглости): |
{ |
|
овальность; |
|
|
огранка. |
|
|
• Отклонение цилиндричности (допуск): |
|
|
конусообразность; |
|
|
бочкообразность; |
|
|
седлообразностть. |
|
|
• Допуск профиля продольного сечения |
|
|
• Отклонения плоскостности (допуск): |
|
|
выпуклость; |
|
|
вогнутость. |
___ |
|
• Допуск прямолинейности. |
||
|
||
Допуски взаимного расположения поверхностей: |
|
|
• Допуск параллельности |
// |
|
• Допуск перпендикулярности |
2 |
|
• Допуск наклона |
|
|
• Допуск соосности |
|
|
• Допуск симметричности |
|
|
• Позиционный допуск |
|
|
• Допуск пересечения осей |
× |
|
Суммарные отклонения |
|
|
• Радиальное биение, торцовое биение |
|
|
• Полное радиальное биение |
|
103
На точность обработки влияют следующие факторы:
•неточность станков;
•точность режущего и вспомогательного инструмента и его изнашивание во время работы;
•неточность установки инструмента и настройки станка на размер;
•погрешности базирования и установки обрабатываемой детали на станки или в оснастке;
•деформации технологической системы (станок, приспособление, инструмент, деталь) под действием сил резания;
•тепловые деформации технологической системы и т.д. (неправильные измерения, ошибки измерения, ошибки исполнения).
Неточность станков. Точность станка в ненагруженном состоянии называется геометрической точностью и зависит главным образом от точности изготовления основных деталей и узлов станка
иточности их сборки. Нормы точности и методы проверки регламентированы стандартами.
Износ деталей и узлов станка в процессе эксплуатации приводит к понижению точности. Возможен износ направляющих станков, шпинделей и подшипников, преобразующих кинематических пар (винт – гайка, реечная пара, червячная пара и т.п.).
Неточность изготовления режущего и вспомогательного ин-
струмента и его изнашивание. Точность изготовления режущего
ивспомогательного инструмента оказывает большое влияние на точность обработки деталей. Погрешности инструмента частично переносятся на обрабатываемую деталь. Это в большой степени относится к резьбообрабатывающему инструменту, протяжкам, концевому инструменту для обработки отверстий – сверлам, зенкерам, разверткам.
Точность обработки зависит от износа режущего инструмента. «Размерный» износ – износ режущего инструмента на пути резания характеризуется приработкой режущей кромки (размерный износ). Изнашивание возможно по передней и задней поверхно-
104
сти. Износ по задней поверхности особенно влияет на точность обработки.
Также на точность обработки влияет точность изготовления вспомогательных приспособлений: оправок, патронов, цанг, державок, борштанг.
Погрешность установки – это сумма погрешности базирования и погрешности закрепления.
Погрешность базирования возникает вследствие несовпадения технологической базы с измерительной. Эта погрешность определяется величиной колебания (т.е. разностью) предельных расстояний измерительной базы от режущей кромки, установленного на размер инструмента.
Погрешность закрепления возникает вследствие смещения заготовки под действием зажимной силы, прилагаемой для фиксации ее положения.
Деформации технологической системы. При обработке деталей на станках силы резания, зажатия и другие воздействуют на детали станка (деталь, инструмент, приспособление), вследствие чего происходит их деформация, изменение величин стыковых зазоров, изменение положения режущих кромок (отжим). Результатом становится отклонение размеров и формы.
Деформации упругой технологической системы под влиянием, действующих в системе сил является одним из источников погрешностей обработки.
Большая жесткость технологической системы является одним из условий достижения точности при механической обработке. Высокая жесткость также предупреждает возникновение вибраций.
Значительное влияние на точность обработки оказывает и метод обработки. В табл. 9.1 приведены квалитеты точности механической обработки заготовок различными методами.
105
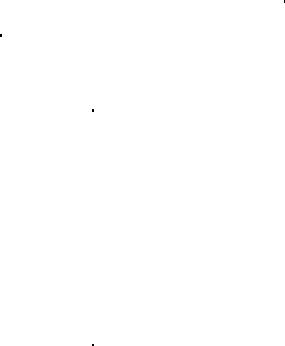
|
|
|
|
|
|
Таблица 9.1 |
|
Точность методов механической обработки |
|
|
|||||
|
|
|
|
|
|
|
|
|
Методы обработки |
|
Квалитет точности |
||||
|
|
Диаметральные |
Линейные |
||||
|
|
|
|
|
размеры |
|
размеры |
Обтачивание |
|
черновое |
|
12–14 |
|
14 |
|
|
чистовое |
|
10–11 |
|
11–12 |
||
на токарных |
|
|
|
||||
|
чистовое повышенной точности |
7 |
|
– |
|||
станках |
|
|
|
|
|
|
|
|
|
тонкое |
|
6 |
|
– |
|
|
|
черновое |
|
стали |
– |
|
12 |
|
|
|
чугуна |
– |
|
11 |
|
|
|
|
|
|
|||
Фрезерование |
|
чистовое |
|
стали |
– |
|
11 |
|
|
чугуна |
– |
|
10 |
||
и строгание |
|
|
|
|
|||
|
|
чистовое |
|
стали |
|
|
9 |
|
|
повышенной |
|
|
|
|
|
|
|
|
чугуна |
– |
|
9 |
|
|
|
точности: |
|
|
|||
|
|
за один проход |
9 |
|
9 |
||
Шлифование |
|
чистовое |
|
8–7 |
|
8–7 |
|
|
чистовое повышенной точности |
6–7 |
|
6–7 |
|||
|
|
тонкое |
|
5–6 |
|
– |
|
|
|
черновое |
|
12 |
|
14–17 |
|
|
|
чистовое |
|
11 |
|
14 |
|
Растачивание |
|
|
агрегатных: |
8–9 |
|
9–10 |
|
|
чистовое |
алмазно- |
6–7 |
|
9 |
||
|
|
расточных |
|
||||
|
|
на станках |
|
|
|
||
|
|
координатно- |
6–7 |
|
9 |
||
|
|
|
|
||||
|
|
|
расточных |
|
|||
|
|
|
|
|
|
||
Сверление |
|
без кондуктора |
12 |
|
15 |
||
|
по кондуктору |
11 |
|
10–11 |
|||
|
|
|
|||||
Развертыва- |
|
однократное |
9 |
|
– |
||
ние |
|
двукратное |
7 |
|
– |
||
|
|
Протягивание |
|
|
7–8 |
|
7–8 |
|
|
Хонингование |
|
|
6–7 |
|
– |
106
Контрольные вопросы по главе
1.Понятие точности механической обработки.
2.Понятие экономической точности.
3.Понятие достижимой точности.
4.Виды допусков формы.
5.Виды допусков расположения поверхностей.
6.Факторы, влияющие на точность обработки.
7.Понятие погрешности базирования.
8.Понятие погрешности закрепления.
9.Влияние жесткости технологической системы на точность обработки.
10.Влияние метода обработки на точность.
107
10. КАЧЕСТВО ПОВЕРХНОСТИ ДЕТАЛЕЙ МАШИН
В технике под поверхностью детали понимают наружный слой с измененной по сравнению с основным материалом структурой, фазовым и химическим составом. Качество поверхности характеризуется:
•физико-механическими свойствами;
•физико-химическими свойствами;
•макрогеометрией поверхности;
•микрогеометрией поверхности (+волнистость).
Качество поверхности формируется в процессе механической обработки в результате воздействия на поверхностный слой детали режущего инструмента и зависит:
•от свойств обрабатываемого материала;
•от режимов обработки (скорость, глубина, подача);
•от геометрии и режущих способностей инструмента;
•от других технологических факторов.
Основными физико-механическими характеристиками поверхностного слоя являются: твердость, величина и глубина остаточных напряжений, структурные и фазовые превращения и деформации кристаллической решетки. Под воздействием силовых и тепловых факторов свойства поверхностного слоя существенно изменяются по сравнению с исходным материалом.
Значительные деформации металла в зоне резания вызывают повышение его твердости и предела прочности и одновременное снижение пластичности. Это явление называется «наклепом». Толщина наклепанного слоя от сотых долей миллиметра (легкие режимы обработки) до десятых долей миллиметра (тяжелые режимы обработки).
10.1. Деформационное упрочнение металла поверхностного слоя (наклеп)
При обработке заготовок резанием под действием прилагаемых сил в металле поверхностного слоя происходит пластическая деформация, сопровождающаяся его деформационным упрочнением – наклепом.
108
При увеличении сил резания и продолжительности их воздействия возрастают интенсивность и глубина наклепанного слоя.
Одновременно с упрочнением (под влиянием нагрева зоны резания) в металле поверхностного слоя протекает отпуск (разупрочнение, возврат), возвращающий кристаллическую решетку металла в ее исходное ненаклепанное состояние.
Конечные свойства поверхностного слоя металла определяются соотношением интенсивности протекания процессов наклепа и отпуска, обусловленных преобладанием силового или теплового факторов в зоне резания.
Соотношение и величина наклепа изменяются от вида и режима механической обработки и геометрии режущего инструмента. Всякое изменение режима резания, вызывающее увеличение сил резания и степени пластической деформации, ведет к повышению степени наклепа.
Влияние скорости резания проявляется через изменение теплового воздействия и нагрева поверхностного слоя.
Однако в целом картина осложняется влиянием сил трения и изменением условий отвода теплоты из зоны резания (применение смазочно-охлаждающих средств).
10.2. Шероховатость поверхности
Шероховатостью поверхности называется совокупность неровностей с относительно малыми шагами на базовой длине исследуемого участка (иногда называют микронеровностями или микрогеометрией).
Шероховатость является следствием технологической обработки поверхности материала. Пластическая деформация поверхностного слоя детали при образовании стружки, копирование неровностей режущего инструмента и трение его о заготовку и многие другие причины обусловливают возникновение шероховатости.
Параметры шероховатости: 1. Высотные:
Ra – среднее арифметическое отклонение профиля; Rz – высота неровностей профиля по десяти точкам;
109
Rz = (4÷5)Ra;
Rmax – наибольшая высота профилей. 2. Шаговые:
Sm – средний шаг неровностей;
S – средний шаг местных выступов профиля; η – опорная длина профиля.
Существенное воздействие на шероховатость обработанной поверхности оказывают механические свойства материала заготовки.
Шероховатость пластичных и вязких материалов (низкоуглеродистых сталей) значительно больше, чем при обработке закаленных сталей.
При этом каждому методу обработки металлов резанием соответствует определенный диапазон шероховатостей.
Следует отметить, что во многих случаях шероховатость возникает в результате одновременного и почти равнозначного воздействия многих факторов, вследствие чего не имеет четко выраженных закономерностей. В табл. 10.1 и 10.2 приведены классы качества поверхности и величины шероховатости при различных методах обработки.
Таблица 10.1 Соответствие классов чистоты, шероховатости и методов обработки
Классы чистоты |
Шероховатость Rа, мкм |
Вид обработки |
|
14 |
0,01 |
|
|
13 |
0,02 |
Шлифование, |
|
12 |
0,04 |
||
отделка |
|||
11 |
0,08 |
||
|
|||
10 |
0,16 |
|
|
9 |
0,32 |
|
|
8 |
0,64 |
|
|
7 |
1,25 |
|
|
6 |
2,5 |
Лезвийная обработка |
|
5 |
5,0 |
||
|
|||
4 |
10,0 |
|
|
3 |
20,0 |
|
|
2 |
40,0 |
|
110