
книги / Технология машиностроения.-1
.pdf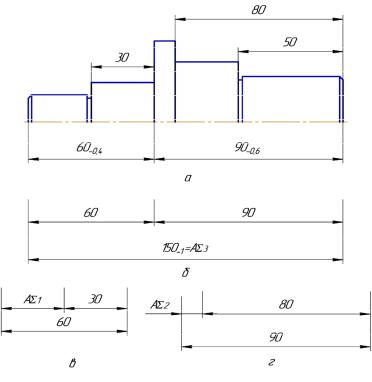
III вариант задания размеров (рис. 6.15). В первую очередь необходимо рассчитать основную размерную цепь (рис. 6.15, б) для обеспечения точности габаритного размера 150–1, он является замыкающим. Решается прямая задача.
Баланс цепи 60 + 90 = [150] = АΣ3.
Назначаем допуски: размер 60 → Т60 = 0,4; размер 90 → Т90 = 0,6;
∆SАΣ3 = 0 + 0 = 0;
∆IАΣ3 = –0,4 + (–0,6) = –1;
Результат 60–0,4 и 90–0,6.
Рис. 6.15. Третий способ задания размеров детали «Вал»: а – эскиз детали; б – основная конструкторская размерная цепь; в, г – частные конструкторские размерные цепи
81
Решение первой частной размерной цепи (рис. 6.15, в): баланс цепи АΣ1 + 30 = 60;
уравнение цепи
АΣ1 = 60 – 30;
→ ←
увел. уменьш.
∆SАΣ1 = 0 – 0 = 0;
∆IАΣ1 = –0,4 – (+0,5) = –0,9.
АΣ1 = 30–0,9, вместо 30–2,3 (во втором способе) – существенное изменение допуска размера.
Решение второй частной размерной цепи (рис. 6.15, г): баланс цепи АΣ2 + 80 = 90;
уравнение цепи
АΣ2 = 90 – 80.
→←
увел. уменьш.
Так как допуск на размер 90 равен 0,6, принимаем допуск на размер 80 также равным 0,6 для обеспечения равных квалитетов точности.
∆SАΣ2 = 0 – 0 = 0.
∆IАΣ2 = –0,6 – (+0,6) = –1,2.
АΣ2 = 10–1,2, вместо 10–3,1 (для первого варианта задания размеров). Сравнивая величины замыкающего звена АΣ (в разных размер-
ных цепях), можно сделать выводы.
1.Изменением способа задания размеров на чертеже детали можно значительно уменьшить допуск замыкающего звена (если это необходимо по каким-либо соображениям), не изменяя номиналов размеров и их допусков. Кроме того, в основной размерной цепи удается уменьшить количество звеньев и, следовательно, уменьшить допуск замыкающего звена. При этом технологичность конструкции детали не изменяется, конструкторские базы совпадают с технологическими.
2.При выборе способа задания размеров (исполнительных) следует строить размерные цепи с минимальным количеством
82
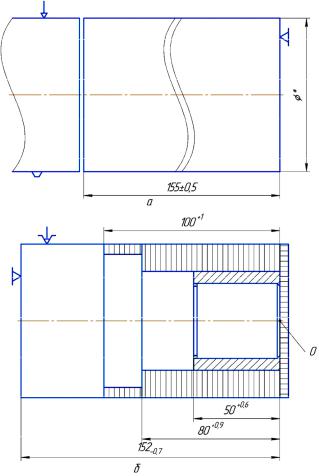
звеньев (по возможности). Чем короче размерная цепь (конструкторская), тем меньше допуск замыкающего звена.
Технологический анализ по третьему варианту задания разме-
ров (рис. 6.16).
Рис. 6.16. Технологический анализ третьего варианта задания размеров: а – заготовительная операция; б – первая токарная операция (обработка справа по чертежу)
83
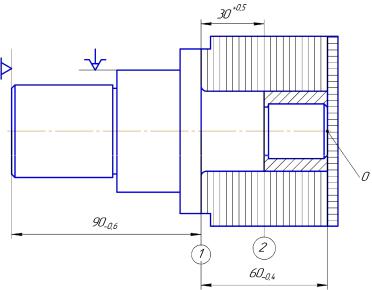
Рассмотрим подробно вторую токарную операцию, обработка слева по чертежу (рис. 6.17). В этой операции возникают некоторые особенности, связанные с последовательностью обработки:
•сначала обрабатывается поверхность 1 в размер 90–0,6;
•затем поверхность 2 в размер 30+0,6;
•только после этого подрезается торец детали в размер 60–0,4.
Рис. 6.17. Вторая токарная операция технологического процесса обработки детали «Вал» (третий способ задания размеров)
Технологические базы совпадают с конструкторскими, пересчета размеров не требуется; технологических размерных цепей не возникает; последовательность обработки (сначала справа или сначала слева, рис. 6.18) значения не имеет – возможны оба варианта, однако приводит к смене технологических баз; реализация технологического процесса с точки зрения точности размеров не представляет трудностей.
84
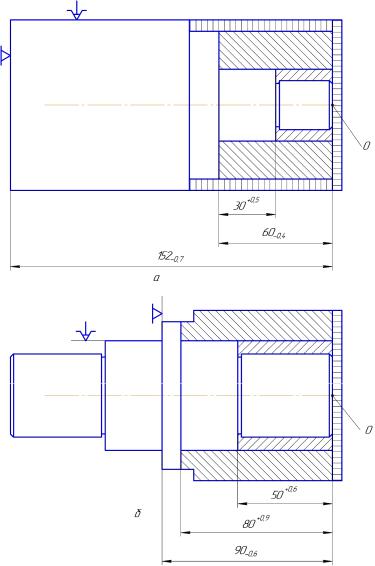
Рис. 6.18. Второй вариант обработки детали «Вал» (третий способ задания размеров): а – первая токарная операция, обработка слева по чертежу; б – вторая токарная операция, обработка справа по чертежу
85
Контрольные вопросы по главе
1.Цель размерного анализа технологического процесса.
2.Состав операционного эскиза.
3.Отличие технологических размеров от конструкторских.
4.Задачи размерного анализа технологических процессов.
5.Решение прямой задачи размерного анализа.
6.Решение обратной задачи размерного анализа.
7.К чему приводит замена конструкторских баз на технологические?
8.Порядок проведения технологического анализа вариантов задания размеров детали.
9.Способы уменьшения допуска замыкающего звена.
10.Для чего необходимо уменьшение допуска замыкающего
звена?
86

7. ОПРЕДЕЛЕНИЕ МЕЖОПЕРАЦИОННЫХ ПРИПУСКОВ
Общим припуском на обработку называется слой металла (материала), снимаемого с заготовки в процессе обработки для получения годной детали заданной формы и размеров. Установление правильных размеров припусков является важной технико-экономи- ческой задачей. Назначение избыточных припусков приводит к излишним потерям материала в виде стружки, к увеличению времени механической обработки, повышенному расходу режущего инструмента, электроэнергии и т.п.
Назначение недостаточно больших припусков не позволяет полностью удалить поверхностный дефектный слой материала и достичь требуемой точности и шероховатости, а также повышает точность и стоимость исходных заготовок, увеличивает опасность (риск) появления брака.
Операционный припуск – это толщина слоя материала, снимаемого с поверхности исходной заготовки во время одной технологической операции. Операционный припуск состоит из промежуточных припусков, снимаемых на отдельных переходах, входящих в данную операцию.
Минимальный припуск складывается из следующих элементов:
Z |
min |
= Z + |
Z 2 |
+ Z 2 |
, |
(17) |
|
1 |
2 |
3 |
|
|
где Z1 – слой металла, который необходимо удалить с поверхности заготовки для устранения неровностей после предыдущей обработки Rz(I – 1) и дефектного слоя металла h(i –1), возникающего в связи обезуглероживанием, коррозией, наклепом, образованием трещин и т.п. все это вместе называется «технологической наследственностью»;
Z2 – слой металла, удаляемый для компенсации погрешностей формы и пространственных отклонений в расположении обрабатываемых поверхностей (базовых) исходной заготовки – несоосность, непараллельность, неперпендикулярность (это тоже технологическая наследственность);
87
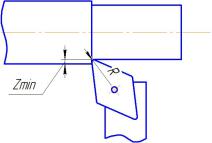
Z3 – слой металла, удаляемый для компенсации погрешности установки заготовки (погрешности базирования).
В связи с тем что Z2 и Z3 выражаются векторами, так как имеют не только величину, но и направление, они суммируются геометрически.
Установленный Zmin всегда должен превышать минимальную толщину стружки, которую может снять режущий инструмент (рис. 7.1). Глубина резания на переходе
t = Zmin > R. |
(18) |
Рис. 7.1. Минимальный припуск, снимаемый инструментом
Структура припуска
На рис. 7.2 схематично изображены составляющие припуска для вала и отверстия. Условные обозначения: Азаг и Взаг – номинальные размеры заготовки; Тз допуск на размер заготовки; Zmin и Zmax – минимальное и максимальное значение припуска на обработку; Аном и Вном – номинальные значения обрабатываемых размеров; ТА и ТВ допуски обрабатываемых размеров.
Структура припуска для вала, обрабатываемого последовательно точением (черновое и чистовое) и шлифованием, представлена на рис. 7.3.
88
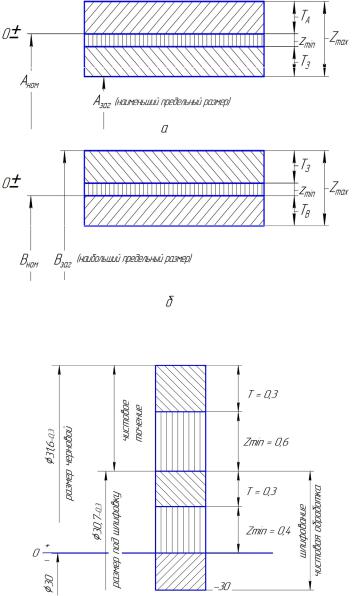
Рис. 7.2. Структура припуска: а – для отверстия; б – для вала
Рис. 7.3. Структура припуска на точение и шлифование вала 30–0,03
89
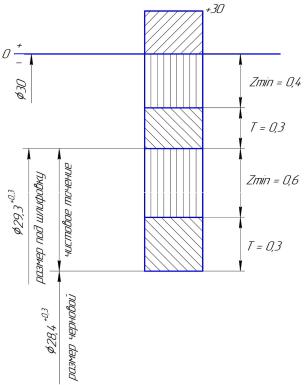
Все припуски (Zmin) рассчитываются по «Справочнику техноло- га-машиностроителя» под редакцией А.Г. Косиловой или аналогичному.
Структура припуска для отверстия, обрабатываемого точением (черновое и чистовое) и шлифованием, представлена на рис. 7.4.
Рис. 7.4. Структура припуска на точение и шлифование отверстия 30+0,03
Значения припусков и допусков на обработку показаны условно.
90