
книги / Технология машиностроения.-1
.pdf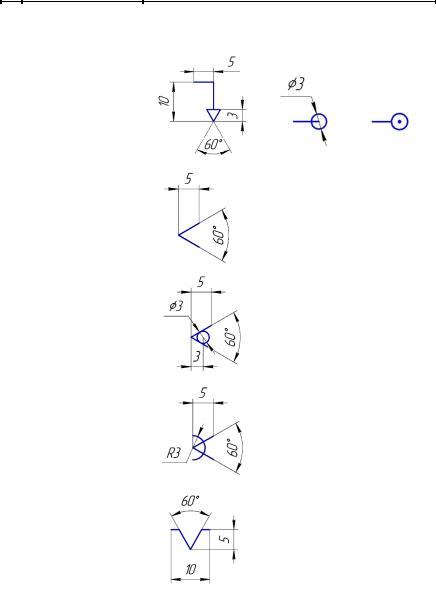
Продолжение табл. 2.1
№ |
Наименование |
Обозначение на видах |
|
||
установочного |
|
|
|
||
спереди, сзади |
сверху |
снизу |
|||
|
элемента |
||||
|
|
|
|
||
6 |
Двойной зажим |
|
|
|
|
|
|
|
|
|
|
7 |
Центр |
|
|
|
|
|
неподвижный |
|
|
|
|
|
|
|
то же |
то же |
|
|
|
|
|
|
|
8 |
Центр |
|
|
|
|
|
вращающийся |
|
|
|
|
|
|
|
то же |
то же |
|
|
|
|
|
|
|
9 |
Центр плавающий |
|
|
|
|
|
|
|
то же |
то же |
|
|
|
|
|
|
|
10 |
Оправка |
|
|
|
|
|
цилиндрическая |
|
|
|
|
|
|
|
то же |
то же |
|
|
|
|
|
|
21
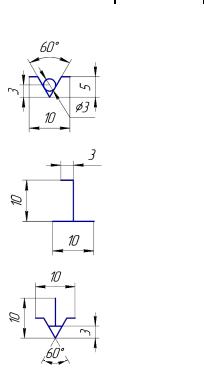
Окончание табл. 2.1
№ |
Наименование |
Обозначение на видах |
|
|
||
установочного |
|
|
|
|
|
|
спереди, сзади |
|
сверху |
|
снизу |
||
|
|
|||||
|
элемента |
|
|
|||
|
|
|
|
|
|
|
11 |
Оправка шариковая |
|
|
|
|
|
|
(роликовая) |
|
|
|
|
|
|
|
|
|
то же |
|
то же |
|
|
|
|
|
|
|
12 |
Патрон поводковый |
|
|
|
|
|
|
|
|
|
то же |
|
то же |
|
|
|
|
|
|
|
13 |
Патрон цанговый |
|
|
|
|
|
|
(кулачковый) |
|
|
|
|
|
|
|
|
|
то же |
|
то же |
|
|
|
|
|
|
|
2.3. Принцип постоянства и совмещения баз
Наибольшая размерная точность изготовленных изделий достигается в случае обработки без переустановок от одной и той же базы, благодаря чему отсутствуют возможные смещения осей и поверхностей детали при каждой новой установке.
Центровые отверстия – это базы (рис. 2.3):
•для обработки справа и слева при токарных операциях и обработке резьб;
•для обработки справа и слева при шлифовании;
•для возможного фрезерования как справа, так и слева.
22
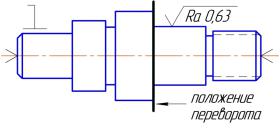
Рис. 2.3. Использование центровых отверстий в качестве баз
Любая технология начинается с подготовки баз. В большинстве случаев невозможно обработать деталь полностью на одном рабочем месте, поэтому приходится вести обработку и на других станках. Установкой по одной и той же базе достигается наибольшая точность при обработке на различных станках. В этом и заключается принцип постоянства баз: необходимо стремиться использовать одну и ту же базу для всех операций обработки детали (не считая смены черновой базы).
В качестве измерительной базы целесообразно использовать технологическую базу, если это возможно.
Еще более высокой точности обработки можно достигнуть, если конструкторская база является одновременно технологической и измерительной. В этом заключается принцип совмещения баз
(рис. 2.4).
Поверхность 3 является технологической базой для обработки поверхностей 1 и 2. При обработке поверхности 2 в размер В и поверхности 1 в размер А1 технологическая и измерительная базы для этих размеров совпадают, принцип совмещения баз выполняется
(рис. 2.4, а).
Однако при обработке поверхности 2 в размер А измерительной базой становится поверхность 1, которая является вспомогательной измерительной базой, полученной после обработки поверхности 1 в размер А1 (рис. 2.4, б), принцип совмещения баз не выполняется, возникает погрешность базирования, равная допуску на размер А1.
23
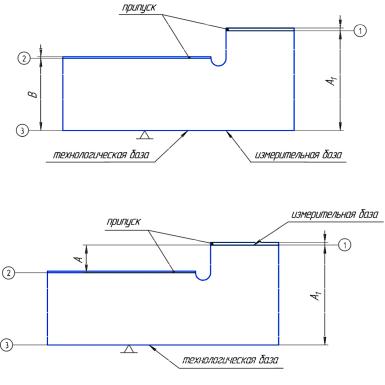
а
б
Рис. 2.4. Принцип совмещения баз: а – выполняется; б – не выполняется
Далее рассмотрим обработку детали на токарном станке с ЧПУ (рис. 2.5). Подрезкой торца в размер А от измерительной (а также технологической) базы (точка начала координат «01») вспомогательная измерительная база переносится в точку начала координат «02», от которой логично отсчитывать размеры a, b, c.
Любой технологический процесс изготовления любой детали начинается с создания чистовых технологических баз. Для этого у заготовок (поковка, штамповка, литье) создают специальные базы (заготовительные бобышки), на которые деталь базируется при об-
24
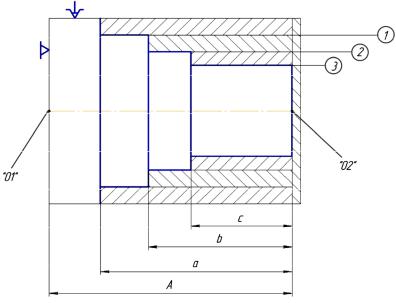
работке ее установочной поверхности (технологической базы). После обработки технологической базы обрабатывают остальные поверхности, учитывая, что деформация после лезвийной обработки может исказить ранее обработанную поверхность.
Рис. 2.5. Обработка детали на станке с ЧПУ
Поэтому сначала обрабатывают поверхности, к точности которых предъявляются меньшие требования. Последней обрабатывается наиболее точная поверхность.
На рис. 2.6, а изображена штучная заготовка, все ее поверхности являются черновыми базами. Обработкой поверхностей 1 и 2 созданы чистовые технологические базы для операции 2 (рис. 2.6, б). Обработкой поверхностей 3 и 4 созданы чистовые базы для последующей обработки (рис. 2.6, в).
25
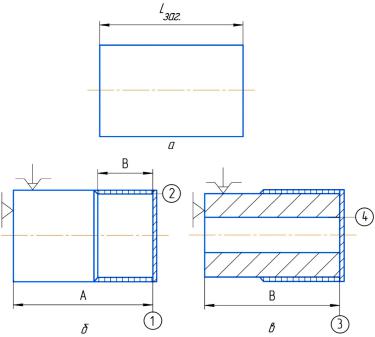
Рис. 2.6. Создание чистовых баз при обработке: а – операция 0, заготовительная (эскиз заготовки); б – первая токарная операция; в – вторая токарная операция
Контрольные вопросы по главе
1.Понятие конструкторской базы.
2.Понятие измерительной базы.
3.Понятие установочной базы.
4.Понятие двойной направляющей базы.
5.Сущность принципа постоянства баз.
6.Сущность принципа совмещения баз.
7.Условное обозначение неподвижной опоры.
8.Условное обозначение одиночного зажима.
9.Условное обозначение центра вращающегося.
10.Условное обозначение поводкового патрона.
26
3.ТОЧНОСТЬ В МАШИНОСТРОЕНИИ
ИМЕТОДЫ ЕЕ ДОСТИЖЕНИЯ
Под точностью детали понимают ее соответствие требованиям чертежа: по размерам, геометрической форме и правильности взаимного расположения обрабатываемых поверхностей.
Необходимую точность размеров готовой детали можно достичь одним из двух принципиально отличающихся методов:
•методом пробных ходов (проходов) и замеров;
•методом автоматического получения размеров на настроенных станках.
3.1. Метод пробных ходов (проходов) и замеров
Метод (рис. 3.1) заключается в том, что к поверхности заготовки, подлежащей обработке, подводится инструмент и на коротком участке заготовки выполняют пробный рез. Затем делают пробный замер полученного размера после остановки станка, определяют величину его отклонения от чертежного и меняют положение инструмента, отсчитывая коррекцию по делениям лимба станка.
Затем цикл проход-замер повторяется, вносится новая поправка. Таким образом, путем пробных ходов и замеров устанавливают правильное положение инструмента (исполнительных органов), обеспечивающее обрабатываемый размер.
Достоинства метода:
•позволяет получать высокую точность обработки на неточном оборудовании;
•при износе режущего инструмента есть возможность внести поправку в положение инструмента, износ не влияет на точность выдерживаемых размеров при изготовлении малой партии изделий;
•позволяет точно распределить межоперационные припуски
ипредотвратить появление брака;
•избавляет от необходимости изготовления сложных и дорогостоящих приспособлений (разметка и т.п.).
27
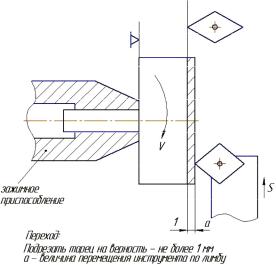
Рис. 3.1. Обеспечение точности методом пробных проходов
Недостатки метода:
•зависимость максимальной точности обработки от наименьшей толщины снимаемого слоя (при точении обычными заточенными недоведенными резцами она составляет 0,02 мм, следовательно, внести изменение в размер менее этой величины невозможно);
•низкая производительность;
•высокая себестоимость (квалификация рабочего). Используется при единичном, мелкосерийном производстве,
опытном, ремонтных производствах, в тяжелом машиностроении. В условиях крупносерийного производства метод пробных
проходов используется главным образом при шлифовании, так как позволяет компенсировать износ абразивных инструментов.
3.2. Метод автоматического получения размеров на настроенных станках
Метод в основном лишен недостатков, свойственных методу пробных ходов и замеров. При обработке заготовок данным методом
28
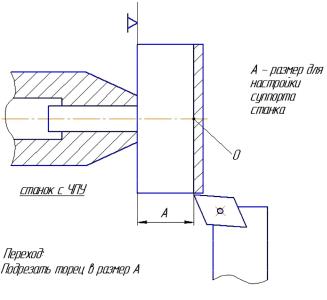
станок предварительно настраивается таким образом, чтобы требуемая точность достигалась автоматически, т.е. почти независимо от квалификации и внимания рабочего.
В этом случае задача обеспечения требуемой точности обработки переносится с рабочего-оператора на настройщика, выполняющего предварительную настройку станка (рис. 3.2), на технолога, назначающего технологические базы и размеры; на инструментальное обеспечение технологических операций.
Рис. 3.2. Метод автоматического получения размеров на настроенных станках
Преимущества метода:
•повышение точности обработки и снижение брака;
•рост производительности обработки;
•рациональное использование рабочих высокой квалификации (наладчики, многостаночное обслуживание);
•повышение экономичности производства.
29
3.3. Обеспечение точности механической обработки
Управление точностью механической обработки включает несколько направлений.
1.Расчеты точности и первоначальная настройка станков, ограничивающая систематические погрешности, а также обеспечение наибольшего времени работы станков без поднастройки.
2.Расчеты технологических режимов резания с учетом реальной жесткости технологической системы, при которых обеспечивается требуемая точность обработки.
3.Точное управление (ручное и автоматическое) процессом обработки и своевременная подналадка станков.
Для осуществления любой операции механической обработки необходимо произвести первичную наладку (настройку) станка.
Наладкой (настройкой) металлорежущего станка называют его подготовку вместе с технологической оснасткой к выполнению работы по изготовлению детали в соответствии с технологическим процессом.
В условиях единичного и мелкосерийного производства (точность достигается способом пробных ходов и замеров) настройка должна обеспечивать:
1) установку режущего инструмента и приспособлений в положения, обеспечивающие наивыгоднейшие условия резания (правильные статические и динамические углы резания), хорошие условия стружкообразования, высокую производительность обработки, стойкость режущего инструмента и требуемое качество обработанных поверхностей;
2) установку режимов работы станка.
Когда точность достигается методом автоматического получения размеров, настройка должна обеспечивать соблюдение точности относительного расположения режущих инструментов, упоров, приспособлений и множества других устройств (станки с ЧПУ), определяющих величину и траекторию перемещения инструментов относительно обрабатываемого изделия.
30