
ЭКСПЛУАТАЦИЯ ВСПОМОГАТЕЛЬНОГО ОБОРУДОВАНИЯ
4.1. СРЕДСТВА РЕГУЛИРОВАНИЯ ПРОИЗВОДИТЕЛЬНОСТИ И КОНТРОЛЯ ЗАШТЫБОВКИ
ЗАГРУЗОЧНЫХ УСТРОЙСТВ
Одно из условий работы конвейеров в заданном режиме — обеспечение подачи определенно дозированного по массе грузо потока. Для этой цели служат загрузочные устройства в виде бункеров с затворами, сводообрушителями и питателями, во ронки (течки) и вспомогательные средства, контролирующие процесс перегрузки материала. Бункера, обычно устанавливае мые в начале конвейерной линии, реже в промежутке между конвейерами, выполняют функции аккумулирующих, усредняю щих и регулирующих грузопоток механизмов.
Бункера с затворами и сводообрушителями. Регулирование истечения грузопотока из бункера непосредственно на конвейер осуществляется с помощью затворов. Они выполняются в виде клапанов, шиберов (заслонок), поворотных секторов, лотков, челюстных механизмов, подвижных замкнутых ленточных кон туров, конусных люков, управляемых вручную или с помощью привода. В некоторых случаях, например, при порционной по даче груза на конвейер, разгрузка бункера может осущест вляться периодически отдельными порциями. В таком бункере имеются поворотный двухкарманный лоток и уплотняющие пла стины (рис. 4.1, а). Вначале заполняется один из карманов лотка. Затем последний поворачивается на 180°, происходит раз грузка заполненного кармана, а в это время заполняется грузом другой карман.
Используя заслонки и клапаны, можно получить заданную производительность загрузочного устройства (рис. 4.1, б). Зас лонка устанавливается в направляющих бункера на Г-образном поворотном рычаге с возможностью регулирования положения. В нижней части рычаг имеет клапан с окном, относительно ко торого располагается седло. Последнее может подниматься или опускаться с помощью винтовой опоры. Клапан снизу подпру жинен и имеет относительно стенок бункера зазор. Поток мате риала, проходящий заслонку, делится на два: основная масса материала проходит через окно, остальная — через зазор между клапаном и стенкой бункера. В случае увеличения количества материала, поступающего на клапан, последний, преодолевая сопротивление пружины, опускается и с помощью рычага воз действует на заслонку, уменьшая тем самым проходное сечение
РИС. 4.1.
Средства регулирования производительности загрузочных устройств:
а — поворотный |
двухкарманный |
лоток: / — бункер; 2 — лоток; 3 — уплотняющие |
пла |
|||||||||||
стины; |
о — заслонки |
и клапаны: |
/ — заслонка; |
2 — направляющая; 3 |
— рычаг; |
4 — |
||||||||
клапан; |
5 — седло; |
5 — пружина; |
в — сводообрушающая |
штанга: / — штанга; |
2 — рас |
|||||||||
секатель; |
3 — направляющие; |
4 |
— горловина |
с |
вибратором; |
г —ленточный |
питатель: |
|||||||
/ — подвижный |
уплотняющий |
борт; 2 — лента; |
3 — бункер; |
д — вибрационный |
пита |
|||||||||
тель; |
е — роторный |
питатель: |
|
/ — бункер; |
2 — лопасть; |
ж — дисковый |
питатель; |
/ — |
||||||
бункер; |
2 — воротник; 3 — диск; |
|
з — барабанный |
двигатель: |
/ — бункер; |
2 — заслонка; |
||||||||
3 — барабан |
|
|
|
|
|
|
|
|
|
|
|
|
течки, в результате чего поток восстанавливается. В случае уменьшения количества материала, поступающего на клапан, все элементы устройства смещаются в обратном направлении. Путем регулирования положения заслонки и клапана устанав ливается необходимая производительность загрузочного устрой ства. Применение конструкции целесообразно при доставке мел косыпучих материалов.
Нарушение режима истечения грузопотока из бункеров, вер тикальных воронок обычно связано с заклиниванием отдельных кусков или сводообразованием. Такое явление наблюдается при разгрузке кусковых грузов и грузов, склонных к налипанию. Для устранения сводообразования и регулирования истечения грузопотока бункера оснащаются специальными устройствами активного действия. К таким относятся, например, пневматиче ские инерционные и диафрагменные вибраторы конструкции НИГРИ. Они прикрепляются к корпусу бункера или выпускной площадке и сообщают им колебания, способствующие равномер ному истечению грузопотока [25].
Бункера, имеющие большую вместимость, оснащаются сводообрушающими элементами, непосредственно воздействую щими на груз. Они выполняются в виде вращающихся и вибри рующих штанг, шнеков.
С целью улучшения режима вибрации бункера он выполня ется составным из верхнего цилиндра и упруго подвешенной к нему нижней горловины. В середине бункера проходит вра щающаяся сводообрушающая штанга (рис. 4.1, в) с рассекате лем грузопотока, вокруг которого жестко на горловине смон тированы спиральные направляющие. Горловина оснащается электромагнитным вибратором. Благодаря вибрации предотвра щается сводообразование, и грузопоток равномерно поступает из бункера на конвейер.
Прошли опытную проверку бункера с пневматическим и гид равлическим сводообрушением материала. В стенки бункера встраиваются сопла, через которые под давлением подается сжа тый воздух или вода. Они образуют на стенках бункера слой смазки и одновременно активно воздействуют на материал, не допуская его слеживания. Однако при прямом выпуске сыпу чего материала из бункеров с затворами и направляющими теч ками возникает сложность в стабилизации истечения и подаче грузопотока со скоростью движения ленты в направлении дви жения последней. Это приводит к повышенному пылеобразованию, нарушению формирования грузопотока при поступлении на конвейер, просыпям, интенсивному износу ленты в месте за грузки. В этом отношении более совершенны загрузочные узлы, состоящие из бункера в сочетании с питателем и направляю щими элементами (лотками, отбойными и ограничивающими щитками). Последние осуществляют принудительную выгрузку заданного количества материала из бункера при снижении вы соты падения и обеспечения скорости движения и направления
Ш
грузопотока, близких к скорости и направлению движения ленты.
Всистеме бункер — питатель бункер имеет наклонные стенки
ивыходное отверстие, точно соответствующие производительно сти конвейера, благодаря чему уменьшается разброс грузопо тока. Питатели способствуют выпуску материала из бункера и выполняют функцию перегружателя. Условия работы питателя под бункером требуют использования мощных двигателей, несу щей конструкции и грузонесущего (одновременно и тягового) органа большой прочности. Из известных конструкций питате лей наиболее распространены ленточные, пластинчатые, скреб ковые, вибрационные, шнековые и роторные (лопастные, диско вые, барабанные).
Ленточные питатели (рис. 4.1, г) применяются при выпуске мелко- и среднекусковых грузов. Производительность питателей зависит от ширины (от 650 до 2500 мм) и скорости движения (от 0,15 до 2 м/с) ленты и составляет 5—3600 т/ч. На длину пи тателя влияет то, в какой мере он используется одновременно и
вцелях транспортирования. Питатель устанавливается под бун кером с трапециевидным отверстием и наклонными сужающи мися нижними стенками, уменьшающими сводообразование. На передней стенке бункера обычно имеется шарнирная заслонка, регулирующая высоту слоя материала на ленте при выгрузке. Толщина слоя не должна быть менее 7з ширины выпускного от верстия бункера для уменьшения усилия среза стенками бун кера слоя материала на ленте при ее движении. Нижние кромки стенок питателя оснащаются уплотняющими бортами (рубаш ками, фартуками), снижающими образование пыли и просыпи. Однако уплотняющие элементы способствуют износу ленты при заклинивании частиц и кусков груза. Для уменьшения износа ленты уплотняющие борта выполняются в виде подвижных кон туров из клиновидных ремней. Производительность питателя Qn (т/ч)
<2п=б0грЛмв,
где v — скорость движения ленты, м/мин; р — плотность груза, т/м3; Лм — толщина слоя груза на ленте, м; В — ширина ленты, м.
Потребляемая мощность питателя N„ (кВт): для бункера с прямоугольным отверстием
хт |
2рB2L0v |
i»n = |
„ — > |
|
6,12 |
где Ь0— длина выходного отверстия бункера, м; для бункера с квадратным или круглым выпускным отвер
стием
N \,6рВ*0'
6,12
Расчетную величину мощности питателей следует увеличи вать на 30—40 %.
В ИГТМ АН УССР разработана серия ленточных питателей: ПЛ 3-08, ПЛ 3-10, ПЛ 3-14 длиной 1,5—12 м для выдачи из бун керов горной массы крупностью 0—250 мм и плотностью до 1,6 т/м3. Производительность питателей составляет 400—2000 т/ч при ширине ленты 800—1400 мм. В них максимально исполь зуются серийно выпускаемые узлы конвейеров. Питатели вклю чают в себя раму, барабаны с винтовым натяжным устройством и привод с цепной передачей на последней ступени для улучше ния компоновки питателя под бункером. Компоновка рамы поз воляет монтировать ленты на барабаны уже в состыкованном виде. В качестве опор для ленты могут быть применены роликоопоры или опоры скольжения. Привод имеет бесступенчатое ре гулирование скорости движения ленты и, соответственно, произ водительности.
Опытные образцы питателей с опорами скольжения из са женаполненного полиэтилена с лентой шириной 800 мм и ско ростью движения 0,62 м/с успешно испытаны на обогатительных фабриках ПО «Донецкуглеобогащение». Питатели устанавлива лись под бункерами, куда железнодорожными вагонами пода вался уголь. Малые масса конструкции и энергоемкость пере грузки, возможность взвешивания грузопотока позволяют пита телям такого рода успешно конкурировать с традиционными типами питателей. На основе полученных данных разработан типоразмерный ряд ленточных питателей для работы в тран спортных комплексах угольных предприятий.
Пластинчатые питатели применяются при выпуске из бунке ров кусковых грузов, имеют ширину грузонесущих пластин 600— 3000 мм, длину става 2,5—30 м, скорость движения пластин 0,05—0,40 м/с и производительность 60—2000 т/ч. Регулировка производительности осуществляется ступенчатым изменением скорости движения пластин. Конструкция пластинчатого пита теля аналогична конструкции пластинчатого конвейера. Однако пластинчатый питатель устанавливается на более массивной и прочной раме, его пластины изготавливаются из особопрочных материалов, например из марганцовистой стали. Пластинчатый питатель оснащается двигателями постоянного тока или много скоростными двигателями переменного тока. Толщина слоя груза не должна превышать половины ширины пластинчатого полотна. Потребляемая мощность пластинчатого питателя в 1,5—2 раза больше, чем ленточного. Расчетное значение мощ ности пластинчатого питателя следует увеличивать на 30—50 %. Большое внимание уделяется смазке движущихся и вращаю щихся элементов.
Скребковые питатели также успешно применяются для пере грузки кусковых грузов и имеют производительность до 3500 т/ч при скорости движения цепей со скребками до 2 м/с. Многоцеп ные питатели состоят из нескольких одноцепных контуров, при
воды которых сблокированы между собой. Грузонесущими могут быть верхняя и нижняя ветви питателя. Энергоемкость скребко вых питателей выше, чем ленточных.
Вибрационные питатели отличаются компактностью, надеж ностью и возможностью перегружать различные по крупности, в том числе горячие, грузы. Они устанавливаются на упругих опорах и поэтому работоспособны при высоких динамических нагрузках, возникающих от падения крупных кусков груза. Про изводительность питателей достигает 3000 т/ч при длине желоба до 10 м. Для определенной группы материалов подбираются свои оптимальные амплитуда и частота колебаний желоба пи тателя. При выпуске материалов, склонных к налипанию, уве личение угла вибрации способствует росту производительности питателя. Для уменьшения налипания вязких грузов желоба пи тателей футеруются полихлорвинилом, полиэтиленом, фторопла стом и другими гидрофобными покрытиями.
Регулирование производительности желоба вибропитателя достигается одновременно изменением режима колебаний и угла наклона желоба (рис. 4.1, д). Кроме основного вибратора, мон тируемого под днищем желоба, устанавливается дополнитель ный вибратор на торцевой стенке желоба. Направление и час тота колебаний дополнительного вибратора не совпадают с основным. Это оказывает стабилизирующее воздействие на истечение грузопотока. Угол наклона желоба изменяется путем регулирования длины тяги подвески желоба.
Шнековые питатели применяются для выпуска мелкосыпу чих, склонных к пылеобразованию материалов в тех случаях, когда требуются небольшая (до 200 т/ч) производительность и высокая точность дозирования. Желоб питателя может иметь открытое или закрытое исполнение. В верхней части закрытого желоба делается одно окно, равное по размерам отверстию бун кера. Для регулирования производительности питателя изменя ется частота вращения шнека или шаг установки лопастей шнека. Для различных материалов степень заполнения шнека составляет 15—45% (для угля — 45, песка— 15, цемента — 30, глины — 15%). В соответствии с этим по данным табл. 4.1 вы бираются оптимальные частота вращения шнека и производи тельность шнековых питателей.
Потребляемая шнековым питателем мощность Nn (кВт):
дг (?n(In -f 3 1 б) [ ( 1 , 8 5 - 1 ,4 8 Р ш) р + 0 ,3 0 4 - 0 , 4 6 5 Р Ш]
где Ln — длина питателя, м; Lб — длина бункера, м; й ш— диа метр шнека, м.
В роторных питателях (рис. 4.1, е) рабочим органом является лопастное колесо, диск или барабан. Лопастное колесо имеет горизонтальные лопасти в виде скребков, которые прилегают к задней стенке бункера. При вращении скребки захватывают материал с полки бункера и подают его в лоток, откуда мате-
Степень запол |
Диаметр |
Максимальный |
Частота враще |
Производитель |
нения желоба |
шнека, мм |
размер кусков |
ния шнека, |
ность за 1 |
шнека. по |
|
груза, мм |
сб/мин |
об мин. м1ч |
4 5 |
153 |
19 |
170 |
0 ,0 6 5 |
|
2 2 9 |
3 8 |
160 |
0 ,2 2 8 |
|
3 0 5 |
5 0 |
145 |
0 ,5 5 0 |
3 0 |
153 |
19 |
120 |
0 ,0 4 3 |
|
2 2 9 |
3 8 |
П О |
0 ,4 6 0 |
|
3 0 5 |
5 0 |
100 |
0 ,3 3 0 |
15 |
153 |
19 |
6 5 |
0,021 |
|
2 2 9 |
3 8 |
6 0 |
0 ,0 8 0 |
|
3 0 5 |
5 0 |
5 5 |
0 ,2 9 0 |
риал попадает на конвейер. Питатели с вращающимся скреб ком успешно используются для крупных бункеров.
Дисковые питатели применяются для выпуска |
из бункеров |
с круглым отверстием плохо текущих материалов |
(например, |
рудных концентратов). Производительность их 5—125 т/ч при размере выпускного отверстия бункера до 2,5 м, частоте вра щения диска 2—10 об/мин, потребляемой мощности 1,5—35 кВт. Питатель представляет собой вращающийся диск, установлен ный под выпускным отверстием бункера (рис. 4.1, ж). Между диском и отверстием располагается спиральный или винтовой воротник, выполняющий функцию регулирующей заслонки и способствующий равномерному истечению материала. Сбрасы вающий скребок монтируется в месте наибольшего подъема винтовой линии. В центре диска при вращении образуется кону сообразный выступ из материала, занимающий 40—50 % по перечного сечения отверстия бункера. Это ведет к увеличению потребляемой мощности. Регулирование производительности пи тателя осуществляется изменением высоты слоя материала на диске, положением и параметрами сбрасывающего скребка, ча« стотой вращения диска. Во избежание просыпи материала уста навливаются уплотняющие борта.
Рабочим органом барабанных питателей (рис. 4.1, з) служит вращающийся барабан с лопастями. Регулирование производи тельности достигается изменением частоты вращения барабана и заслонкой в бункере. Барабанные питатели применяются для перегрузки мелко- и среднекускового материала на углеобога тительных фабриках.
Контроль заштыбовки загрузочных устройств. Грузопоток должен поступать на ленту направленно плотной непрерывной струей с минимальным разбросом. С этой целью выходные от верстия бункеров, течек, оснащаемых направляющими элемен тами, не рекомендуется выполнять излишне большими. Однако такое ограничение увеличивает вероятность сводообразования, которое приводит к заштыбовке загрузочных узлов перегружае-
мым материалом. При заштыбовке загрузочного устройства кон вейер останавливается.
Для исключения заштыбовки загрузочных узлов осущест вляют контроль процесса загрузки и заполнения бункеров и те чек. Известными средствами контроля перегрузки материала являются следующие датчики: реагирующие на верхний уровень заполнения бункера или течки; срабатывающие на прекращение истечения материала в результате сводообразования или закли нивания; контролирующие нижний уровень заполнения бункера или течки с целью создания защитной, так называемой пород ной, подушки; срабатывающие на переполнение загрузочной ча сти конвейера транспортируемым материалом.
Для контроля верхнего уровня материала в течке предназ начен датчик ДЗШ-2 (рис. 4.2, а), выпускаемый Днепропетров ским заводом шахтной автоматики. Датчик имеет подвижный элемент, который при контакте с материалом наклоняется. Рас положенный в подвижном элементе шарик перемещается и за мыкает контакт цепи управления. Датчик монтируется в верх
ней части бункера |
или течки. |
Функцию |
датчика |
может вы |
|
полнять шарнирная |
плита |
с |
постоянным |
магнитом. Задняя |
|
часть бункера выполняется |
из |
неферромагнитного |
материала |
с магнитоуправляемым контактом. При накоплении в течке материала сверх заданного предела плита поворачивается и магнит воздействует на магнитоуправляемый контакт. Послед ний замыкается и включает цепь управления приводом подаю щего конвейера, который при замыкании контакта отключается. После ликвидации заштыбовки течки плита освобождается от материала и возвращается в исходное нижнее положение под действием упругого элемента. Магнитоуправляемый контакт размыкается, и подающий конвейер снова включается.
При сводообразовании прекращается истечение материала из выпускного отверстия и одновременно происходит переполнение бункера или течки. Датчики контроля сводообразования монти руются на выходе течки. Механические датчики могут выпол няться в виде рычага с противовесом (рис. 4.2, б). При непре рывной подаче материала рычаг опускается и замыкает кон такт в цепи управления подающего конвейера. В случае прекращения истечения материала рычаг поднимается, контакт размыкается и привод подающего конвейера отключается. Вместо рычага может быть использован трос с подвешенным к нему через блок грузом (рис. 4.2, в). Трос поднимается при истечении материала и опускается при отсутствии его, замыкая и размыкая контакт в цепи управления привода подающего кон вейера.
Более надежны в работе датчики излучения (радиоактивные или ультразвуковые). При образовании длительных по времени пауз, в течение которых материал не проходит через отверстие течки, интенсивность регистрируемого приемником излучения возрастает и система срабатывает (рис. 4.2, г).
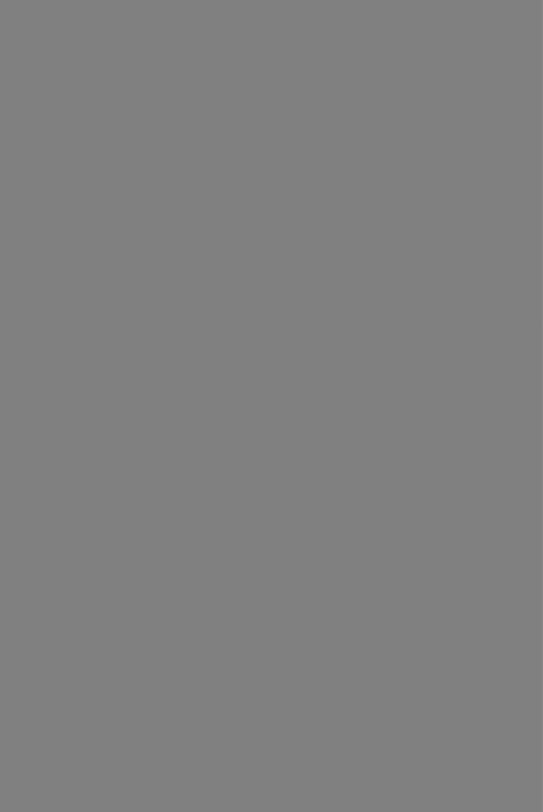
В более универсальных схемах одновременно посредством специальных зондов контролируются верхний уровень заполне ния бункера материалом и сводообразование (рис. 4.2, д). Дат чик сводообразования предупреждает о возникшем заторе,, а датчик верхнего уровня материала подает сигнал на отклю чение привода подающего конвейера, если за заданный проме жуток времени затор не ликвидируется.
При перегрузке крупнокусковых материалов включение по дающего и приемного конвейеров контролируют таким образом,, чтобы в выходной части течки оставался определенный слой, на зываемый породной подушкой (рис. 4.2, е). При одновременном запуске подающего и приемного конвейеров большие куски груза не попадают сразу на ленту, а при падении тормозятся породной подушкой. Для осуществления такого режима работы узла перегрузки течка оснащается датчиком нижнего уровня. В ПО «Карагандауголь» на шахте им. Ю. Н. Костенко для кон троля верхнего уровня заполнения приемных бункеров и гезен ков используется радиоактивный датчик, а для контроля ниж него уровня — датчик аппаратуры контроля воздуха АКВ-2П. Мембрана датчика монтируется на трубке, вставляемой в от верстие в бункере. Контакт датчика вводится в цепь реле ИКС2Н, управляющего работой приемного конвейера-питателя. При снижении уровня материала ниже расположения датчика аппа ратуры АКВ-2П в зоне расположения датчика снижается дав ление воздуха, мембрана прогибается и контакт в цепи реле- ИКС-2Н размыкается — привод приемного конвейера-питателя останавливается.
При эксплуатации автоматизированных конвейерных линий предусматривается контроль заштыбовки загрузочной части конвейера (рис. 4.2, о/с). Для этой цели используется конечный выключатель ВКВ-380, устанавливаемый на консольном крон штейне. Выключатель взаимодействует с поворотным рычагом с отбойной плитой. В момент заштыбовки загрузочной части приемного конвейера отбойная плита с рычагом поворачивается, и выключатель ВКВ-380 срабатывает. Привод приемного Кон вейера отключается.
4.2. СРЕДСТВА ДЛЯ УМЕНЬШЕНИЯ ОБРАЗОВАНИЯ ПЫЛИ И ПРОСЫПИ
Конвейерный транспорт — один из основных источников об разования пыли и просыпи (обычно сопутствующие друг другу процессы). Пыль и просыпи ухудшают условия эксплуатации конвейерного оборудования. Образующаяся в перегрузочных уз лах и на ставах конвейеров пыль загрязняет воздух, оседает На полу, стенах, выступающих элементах зданий и оборудования. Повышенная запыленность воздуха создает антисанитарные ус ловия и снижает безопасность работ для обслуживающего Пер сонала, вызывает преждевременный износ оборудования, мо>иет
быть причиной взрывов и пожаров. Из-за уборки пыли и про сыпи снижается производительность труда, при этом часто за трагивается тяжелый ручной труд. В угольной промышленности пз общем комплексе мер, направленных на повышение безопас ности работы в шахтах, мероприятиям по борьбе с пылью при дается важное значение. За годы десятой пятилетки на ком плексное обеспыливание переведено 678 шахт, 33 разреза, 47 обогатительных фабрик. Средствами пылеподавления оснащены все места перегрузки угля.
Конструкции узлов конвейеров должны способствовать уменьшению измельчения и разбрасывания груза, уплотнению и герметизации участков его движения. Основными узлами совер шенствования в этом отношении являются лотки, направляющие •борта и уплотнения, загрузочные устройства, ставы и укры тия [26].
Лотки. Для уменьшения пыли лотки должны обеспечивать правильное формирование и истечение грузопотока, снижение ударных нагрузок. Криволинейные лотки позволяют уменьшить высоту падения груза на ленту, придают ему скорость, близкую или равную скорости ленты. Таким образом уменьшаются из мельчение груза и пылеобразование в зоне загрузки.
Применение в лотках футеровок из листов обычной резины или снятой с эксплуатации ленты способствует снижению дроб ления груза и, следовательно, пылеобразования. Крепление фу теровок может осуществляться вулканизацией (или склеива нием резины с металлом) и механическими соединительными элементами. С целью улучшения амортизирующей способности футеровки выполняют с профильными выступами, благодаря чему куски груза падают на элементы футеровки под прямым углом (рис. 4.3, а). На шахтах ПО «Средазуголь» в узлах пере грузки конвейеров 1ЛБ100 и 1Л 100 используются футеровки :<в виде резиновых листов размером 300x200x40 мм, монтируе мых на горизонтальных стержнях, которые устанавливаются с перекрытием на каркасе. Футеровки успешно работают при грузопотоке до 4000 т/сут и высоте падения 2,9 м. Дробление угля снижается до 2 %.
Направляющие борта и уплотнения. К основным требова ниям, предъявляемым к бортам и уплотнениям, относятся прос тота конструкции, снижение трудоемкости монтажа и замены элементов, износостойкость, минимальное воздействие на ленту, герметичность. Обычно применяют неподвижные борта с уплот нениями и реже — подвижные. Неподвижные борта (рис. 4.3, б) включают в себя жесткие продольные элементы прямоугольной формы, устанавливаемые над лентой. Чем больше высота сво бодного падения груза и скорость ленты, тем длиннее борта. Последние снабжены сектором с отверстиями, поворотным ва лом с фиксатором, кронштейнами и прижимными продольными планками. Уплотнение в виде прямоугольного листа устанавли вают с небольшим зазором к ленте между жестким элементом
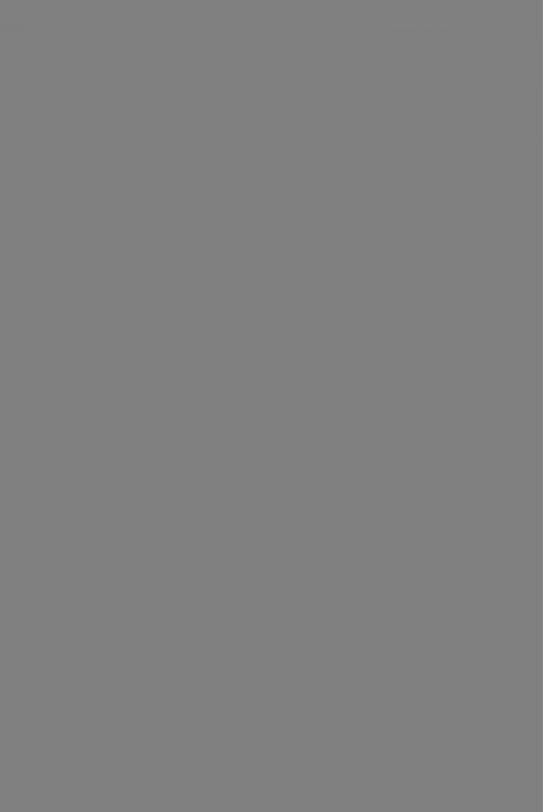
сирующими выступами. Как только между лентой и уплотне нием возникает зазор, уплотнение сдвигается вниз, и зазор лик видируется. Для уменьшения износа эластичные уплотнения вы полняют составными (рис. 4.3, д) из основного и дополни тельного (более эластичного), взаимодействующего с бортовым участком ленты. Материал, попавший за основное уплотнение, не просыпается благодаря контакту дополнительного уплотне ния с лентой. Дополнительное уплотнение легко регулируется с помощью кронштейна и болтов. Постоянного прижатия уплот нения к ленте можно достигнуть также путем автоматического выдвижения его в направляющих обоймах с подпружиненным толкателем.
Загрузочные устройства. По сравнению с лотками загрузоч ные устройства более эффективны в отношении снижения пылеобразования пыли и просыпи. Они лучше приспособлены для формирования грузопотока. Как правило, загрузочные устрой ства (рис. 4.4, а) выполняются закрытыми с уплотнениями и блокировками для исключения завала и просыпи. Блокировки в узле загрузки обеспечивают автоматическое отключение по дающего конвейера при остановке приемного конвейера. Такая
а
|
|
|
РИС. 4.4. |
|
|
|
|
|
|
Загрузочные и центрирующие |
грузопоток устройства: |
|
|
||||
а —загрузочное с блокировкой подающего и |
приемного |
конвейеров: |
1 —тормоз; 2 — |
|||||
рычаг; |
3 — шарнир; |
4 —емкость; |
5 —выключатель; б — загрузочное |
с пылеподавляю |
||||
щими |
пластинами: |
/ —кожух; 2 —листы; 3 — вибростол; в — центрирующее |
с изме |
|||||
рительной платформой: / —платформа; 2 —динамометр; |
г — центрирующее |
с |
форми |
|||||
рователем: 1 —направляющие; |
2 —катки; |
3 —щит; |
4 —дефлекторные |
ролики |
блокировка возможна благодаря подвижной компоновке загру зочного устройства. Она с одной стороны опирается на пру жину, а с другой — на шарнир с рычагом. Последний соединен с ленточным тормозом, установленным на одной оси с разгру зочным барабаном подающего конвейера. С зазором относи тельно емкости загрузочного устройства устанавливается концевой выключатель. При работе транспортируемый груз с подающего конвейера поступает в загрузочное устройство и направляется на приемный конвейер. Когда емкость заполняется до определенного уровня, она растягивает пружину, поворачи вается относительно шарнира и воздействует с помощью рычага на ленточный тормоз подающего конвейера. Усилие торможения зависит от степени заполнения емкости. При полном заполнении «емкости срабатывает концевой выключатель, и привод подаю щего конвейера выключается.
Мелкосыпучие грузы на выходе из загрузочного устройства движутся с завихрением. Для снижения завихрения и пыления груза используются наклонные или вибрирующие волнистые пластины (рис. 4.4, б). Они устанавливаются в направлении движения ленты параллельно друг другу и с зазором по отно шению к ленте. Волнистая форма пластин уменьшает завихре ние и вспучивание груза. Кроме того, под лентой находится виб ростол, жестко соединенный с вибратором. Возбуждаемые виб ратором колебания передаются через вибростол на скользящую по нему ленту и через нее на сыпучий материал. Благодаря этому уменьшаются трение и износ ленты.
Центрирование грузопотока. В некоторых случаях образова ние просыпи в узле загрузки связано со смещением грузопотока к одной из стенок загрузочного устройства. Происходит смеще ние грузопотока по ширине ленты и просыпание материала. Для контроля смещения грузопотока относительно загрузочной части конвейера может быть применен измеритель рассогласования с динамометрами. Измеритель состоит из прямоугольной плат формы (рис. 4.4, в), установленной на четырех динамометрах и поддерживающей ленту в месте загрузки. Формирователь сиг налов управления выполнен по мостовой схеме, в плечи которой включены динамометры. При пространственном смещении гру зопотока относительно приемного участка конвейера происходит неравномерное нагружение динамометров. В результате этого на выходах формирователя возникают сигналы, соответствую щие отклонению центра тяжести грузопотока от оси приемной платформы. Сигналы подаются на исполнительные механизмы загрузочного узла, обеспечивающие продольное и поперечное смещения грузопотока. В процессе поступления сигналов дости гается пространственное согласование грузопотока с приемным участком конвейера в двух взаимно перпендикулярных направ лениях.
Во многих случаях поперечное смещение грузопотока отно сительно ленты связано с боковым ее сходом. Последний ис-
150
пользуется в качестве регулирующего воздействия для центри рования и формирования грузопотока. Формирователь грузопо тока (рис. 4.4, г) выполняется в.виде щита с дугообразным вы резом для верхнего и бокового ограничения грузопотока. Щит имеет катки, расположенные в направляющих, и стенки с дефлекторными роликами. При поперечном сходе боковые кромки ленты упираются в дефлекторные ролики, что приводит к сме щению устройства со щитом. Боковые стенки щита направляют поток груза по центру ленты.
Ставы и укрытия. Компоновка ставов и укрытий должна спо собствовать уменьшению образования пыли и просыпи. При по вышенных скоростях движения ленты не всегда удается обес печить нормальное истечение грузопотока в загрузочном узле.
На линейной части конвейера, где образование пыли связаносо встряхиванием груза на роликоопорах и взаимодействием его с воздушным потоком, преобладает тенденция к применениюлегких быстросъемных укрытий в виде навесов, козырьков ог раждений, закрытых кожухов. Укрытия позволяют существенноснизить загрязнение окружающей среды и производственных по мещений пылью, образующейся в процессе транспортировки груза. Наиболее простые укрытия выполняются в виде метал лических или пластмассовых козырьков (рис. 4.5, а). Козырьки с одной стороны имеют проушины с пальцем для установки в кронштейнах рамы конвейера. Подъем и опускание козырьков: могут производиться вручную. При более герметичном испол нении козырьки имеют форму полуцилиндров, телескопически входящих один в другой и снабженных уплотняющими поло сами. Особенно нежелательно образование пыли на конвейерах,, устанавливаемых в помещениях, где находятся люди. Если пылеобразование значительно, вся грузовая ветвь ленты герме тично укрывается с помощью бортов с уплотнениями и сплош ным кожухом, имеющим смотровые окна или поворотные люки. Укрытие монтируется на легких трубчатых конструкциях.
Основываясь на проведенных исследованиях, ИГТМ АН УССР рекомендует применять для подземных конвейеров уголь ных шахт укрытия закрытой конструкции, при которой загру зочный узел и линейная часть конвейера полностью изолиру ются от окружающей среды (рис. 4.5, б). Такие укрытия исклю чают взаимодействие воздушных потоков с транспортируемым углем и вынос пыли в атмосферу горной выработки. При отсут ствии закрытого укрытия запыленность воздуха в зоне узла за грузки достигает 2500 мг/м3 и, хотя резко снижается по мере удаления от узла загрузки, все же может превышать санитар ные нормы. Оставшаяся в воздухе пыль в количестве 40— 50 мг/м3 содержит до 98 % опасных для человека мелких фрак ций из пылинок размером менее 10 мкм.
Полностью изолирующий кожух (рис. 4.5, в) конвейера мон тируется из гибких листовых секций, дугообразно сгибаемых: в верхней части. Листы имеют продольные (внешние и внутрен-
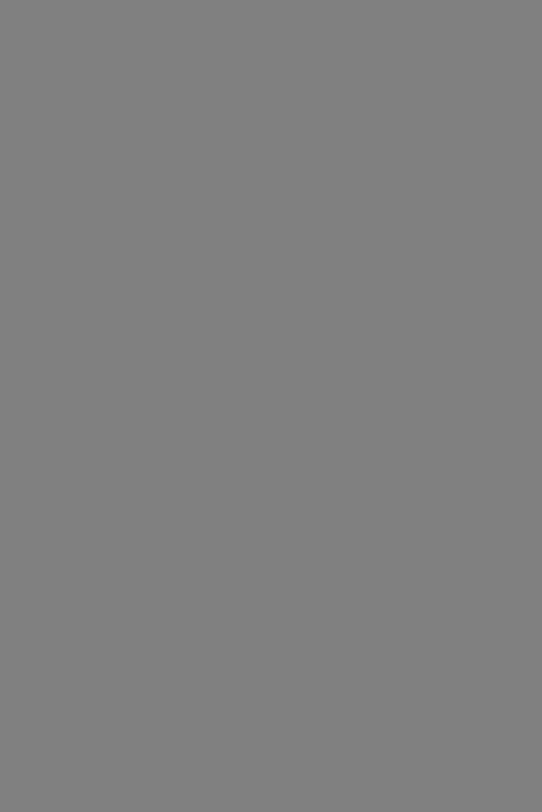
динамическое сопротивление выработок при подаче свежего воз духа на участки.
Для конвейеров, устанавливаемых в шлюзовых проемах гор ных выработок, вентиляционных сооружений шахт, использу ются эластичные уплотняющие элементы в виде фартуков (рис. 4.5, г). Фартуки располагаются над грузонесущей и под холостой ветвями ленты и между ними. Кроме фартуков име ются также эластичные стенки и дополнительные уплотнитель ные элементы, число которых зависит от величины депрессии в вентиляционном сооружении. Транспортируемый груз верхней ветвью конвейерной ленты перемещается к шлюзовому укры тию, поднимает фартуки, которые охватывают его по контуру поперечного сечения. Образовавшиеся вследствие контакта фар туков с транспортируемым грузом просыпи ссыпаются и попа дают на наклонные щитки, далее на нижнюю ветвь ленты и вы носятся за пределы шлюзового проема.
4.3. МЕРОПРИЯТИЯ ПО ПЫЛЕПОДАВЛЕНИЮ И УБОРКЕ ПРОСЫПИ
4.3.1. ПЫЛЕПОДАВЛЕНИЕ
Поскольку при интенсивном образовании пыли в процессе перегрузки и транспортирования горной массы сложно обеспе чить полную герметизацию оборудования, целесообразно пылеподавление с использованием орошения, аспирации, пены, рас творов или одновременно нескольких средств.
Пылеподавление орошением. К основным характеристикам пылеподавления орошением относятся влажность груза, запы ленность воздуха и расход воды. По данным Черноморниипроекта (г. Одесса), при перегрузке руд и углей запыленность воз духа и расход воды можно определить из соотношений
Q — CI PB + D it
Яв= С2<275—£>2,
где Яв — запыленность воздуха в зоне перегрузки, мг/м3; а, Ь— коэффициенты, равные 3731 и 111 соответственно; Гвл — влаж ность груза, %; QB— расход воды через форсунки, л/мин; рь — давление воды перед форсунками, МПа; Сь Dx, С2 и Я2— коэф фициенты, равные 0,594 и 2,605; 71042 и 44,068 соответственно.
Запыленность в узле перегрузки снижается с увеличением влажности груза. При этом существует порог влажности (для угля 4%), начиная с которого происходит резкое снижение уровня запыленности (рис. 4.6, а). Предварительное увлажне ние груза требует значительного расхода воды [27]. Так, при
О0,05 0,10 0,15 0,20 рв,МПа
РИС. 4.6.
Зависимости характеристик пылеподавления орошением:
« —запыленности воздуха от влажности груза; б —расхода воды от давления перед форсунками: 1, 2, 3 —диаметр форсунки 2, 1,5 и 1 мм соответственно; в —запылен
ности воздуха от расхода воды при диспергированном орошении
производительности перегрузочного узла 100 т/ч и достижении необходимой влажности угля 18 % расход воды составляет 18 м3/ч. Сократить расход воды можно путем диспергирован ного орошения в виде водяного тумана из форсунок с малым диаметром и выбора оптимального давления воды (рис. 4.6, б). Расход воды в этом случае'при достижении норм запыленности снижается до 0,3 м3/ч (рис. 4.6, в).
Применение орошения на всех стадиях добычи, транспорти ровки и переработки горной массы позволяет уменьшить запы ленность воздуха на 60—90 %. Система орошения конвейеров роторных экскаваторов ЭРГВ-630-9/0,5, ЭР-1250/1,5Д, ЭРШРД- ■500-30/7 имеет две форсунки, устанавливаемые в зоне пере грузки материала из ковшей ротора на приемный конвейер и
сприемного конвейера на перегружатель.
Всхемах циклично-поточной технологии добычи ископаемых применяются дробильно-сортировочные агрегаты, при работе ко
торых образуется большое количество пыли. Институтом гор
ного дела Минчермета СССР создана установка |
для комп |
||
лекса |
СДСК-300 |
по орошению горной массы в зоне погрузки |
|
и разгрузки до |
дробления. Рабочий орган установки — фор |
||
сунка |
ОТЗ-З |
(ороситель — туманообразователь |
зонтичный). |
Для орошения форсунка ОТЗ-З подключается к водопровод ной магистрали. Под давлением воды на зонтичный клапан и поджимную пружину образуется кольцевая щель между зонтичным клапаном и корпусом форсунки. С помощью регу лировочной муфты можно ослабить или затянуть поджимную
пружину, изменяя ширину кольцевой щели и регулируя рас ход воды на орошение. Оптимальный расход воды во избежа ние переувлажнения груза достигается с помощью автомати чески действующих форсунок и механизмов, контролирующих: интенсивность поступления грузопотока в загрузочное устрой ство или на ленту. Широко используются шиберы, отклоняю щиеся под воздействием груза и через систему рычагов вклю чающие кран оросительной системы. Чем больше грузопоток, тем больше отклоняется шибер, сблокированный с краном расхода воды. В другом варианте регулирующим механизмом является поворотный подпружиненный лоток с запорным кла паном (рис. 4.7, а). При поступлении груза лоток поворачи вается и открывает запорный клапан на величину, пропорци ональную массе груза.
Всесоюзным научно-исследовательским институтом безопас ности труда в горнорудной промышленности (ВНИИБТГ) ус пешно испытана на Южном ГОКе (Кривой Рог) автоматическая установка для орошения ленточных конвейеров, транспортирую щих железную руду. В установку входят датчик загрузки ленты.
а —орошающее |
|
Устройства пылеподавления: |
2 —лоток; |
3 — запорный |
||||||
с подпружиненным |
лотком: / —форсунка; |
|||||||||
клапан; б —то |
же, с |
датчиком в |
виде ролика: / —ролик; |
2 —рычажный |
механизм; |
|||||
3 —шток; |
диафрагма; |
5 —плунжер; 6'—форсунка; |
в — аспирационное |
с |
фигурным |
|||||
желобом: |
/ —желоб; |
2 —укрытие; |
3 — воздуховод; |
г —то |
же, |
с пылеосаднтельными |
||||
элементами: |
/ —воздуховод; 2—пылеосаднтельные |
элементы; |
д — пеногенератором; |
/ — лоток; 2 — кожух
выполненный в виде ролика с рычажным механизмом (рис. 4.7 6), запорный вентиль диафрагменного типа и форсунка. При поступлении руды на конвейер лента прогибается и нажи мает на ролик, который поворачивает рычаги. Последние при водят в движение шток, диафрагму и плунжер. Между плунже ром и стаканом образуется 4—5-миллиметровый зазор, через ко торый поступает вода в трубопровод и форсунку.
Прокопьевским заводом шахтной автоматики выпускается аппаратура АО-3 во взрывобезопасном исполнении, предназна ченная для автоматического орошения перегрузочного узла лен точного конвейера в условиях шахт и рудников. Она включает в себя датчик наличия материала ДНМ контактного типа, ре лейный блок и вентиль с электромагнитным приводом включе ния клапана. Релейный блок предназначен для создания выдержки времени при включении электромагнита вентиля и переключения его питания на пониженное напряжение. Чтобы уменьшить расход воды, в систему управления орошением вклю чается датчик влажности груза. Датчик подает сигнал на от ключение орошения, когда влажность груза достигает величины, при которой пыль не образуется.
Пылеподавление аспирацией. Большое распространение в практике пылеподавления в узлах перегрузки получили укры тия в сочетании с аспирацией, пылесобирающими элементами и уплотнениями. Применение этих средств целесообразно в усло виях интенсивного пылеобразования, например в перегрузочных узлах поверхностных комплексов шахт и дробильно-сортировоч ных фабрик.
В загрузочных аспирационных устройствах с вертикальным истечением груза возникает разность скоростей движения груза и воздуха. Последний движется вследствие разрежения и спо собствует пылеобразованию. Для устранения этого явления раз грузочный фигурный желоб выполняется в виде усеченного ги перболоида (рис. 4.7, в). Выходное отверстие желоба герме тично соединено с укрытием, закрывающим сверху рабочую ветвь ленты конвейера. На верхней крышке укрытия установлен воздуховод аспирационной установки. Переменное поперечное сечение желоба обеспечивает по всей его длине одинаковую ско рость движения груза и воздуха за счет уменьшения скорости падения груза. Благодаря этому уменьшаются эжекция воздуха перегружаемым по желобу грузом и пылеобразование.
Улучшению пылеподавления способствуют специальные m>t- леосадительные элементы и воздухораспределительные пла_ стины. Поверхность пылеосадительных элементов должна быт*, большой. Это достигается применением пространственной ре шетки, образованной сферическими пылеосадительными элемец. тами (рис. 4.7, г). Они подвешиваются к подпружиненной сверху раме, расположенной под воздуховодом. Один из сферически* элементов контактирует с грузом, перемещаемым лентой. Запы ленный воздух, эжектируемый в желобе грузом, поступает в ук
рытие и, проходя по каналам, образованным сферическими эле ментами, засасывается в воздуховод. При этом пыль налипает на сферические элементы, колебательное движение которых приводит к коагуляции и стряхиванию пыли. Колебательному движению сферических элементов способствует упругая связь рамы с укрытием, а также взаимодействие сферического эле мента с грузом.
В процессе транспортирования материала определенная его часть уносится в виде пыли. В этом случае может быть целесо образным использовать автономные пылеуловители, встраивае мые в узел перегрузки .материала. Постоянный подсос воздуха обеспечивает удержание пыли в пределах кожуха пылеулови теля. Уплотненная пыль периодически отделяется от уловителя и возвращается в поток транспортируемого материала. Таким образом отпадает необходимость в громоздких трубчатых систе мах для транспортирования пыли и пылесборниках. Уменьша ется расход электроэнергии.
Пылеподавление комбинированными и вспомогательными средствами. Наибольший эффект в пылеподавлении достигается применением комбинированных средств, например орошения в сочетании с аспирацией. При транспортировке мелкого угля образуется пыль, подавление которой аспирацией и орошением не всегда обеспечивает снижение запыленности воздуха до са
нитарных норм. Один |
из перспективных способов борьбы |
с пылью — локализация |
очага пылевыделения высокократной |
пеной (рис. 4.7, д). Материал, обработанный пеной, не образует пыли и в процессе транспортирования. Обеспыливание пеной ис пытывалось при доставке угля на поверхностных комплексах шахт, углеобогатительных фабриках, предприятиях топливной промышленности, щебеночных заводах. Эффективность пылеподавления пеной достигает 95%. Высокократная пена, получае мая воздушно-механическим способом, вырабатывается пеногенератором. Пеногенератор подает пену в ограниченное фарту ками пространство приемного кожуха ленточного конвейера. Запыленный воздух, проходя через пенный фильтр, полностью очищается. Часть пены выносится из кожуха и покрывает сверху слой груза на ленте, что предотвращает вторичное пыление.
Применение пеногенераторов типа ППК-30 для подавления пыли требует равномерного распределения пенного потока.
Всесоюзным центральным научно-исследовательским инсти тутом охраны труда ВЦСПС разработана пылеподавляющая ус тановка, обеспечивающая равномерное покрытие пеной слоя груза. Лента конвейера проходит через закрытый кожух с лот ком и подвижной штангой, соединенной с приводом. На подвиж ной штанге крепится пеногенератор. За кожухом монтируется пеноотбойная сетка. На выходе из защитного кожуха образу ется пенное облако, которое удерживается пеноотбойной сеткой.
При скорости движения ленты более 2,5 м/с перемещение груза сопровождается фрикционным взаимодействием между
собой отдельных кусков. Последние разрушаются, образуя пыль. Для уменьшения разрушения кусков груза применяют водные? растворы карбамидной смолы и отвердители щавелевой кис лоты. По рекомендации Донецкого научно-исследовательского» угольного института смешиваются раствор карбамидной смолы. 30—40 %-ной концентрации и отвердитель 0,8—1,1 %-ной кон центрации, содержащий 15—20 % щавелевой кислоты от массы смолы. Растворы смешивают в воздухе путем пересечения их: напорных струй и сжатого воздуха.
4.3.2. УБОРКА ПРОСЫПИ
Применение орошения, аспирации и других средств пылеподавления не исключает частичного осаждения пыли на кон вейерное оборудование. Часть просыпи возникает из-за децентрированного хода ленты. Накапливаясь, пыль и куски груза образуют просыпи, которые затрудняют эксплуатацию кон вейера. Однако в большинстве случаев основная масса про сыпи возникает не из-за появления пыли и децентрированного хода ленты. При транспортировании грузов, склонных к нали панию, часть груза прилипает к поверхности ленты и не пол ностью удаляется устройствами очистки. Она попадает под хо лостую ветвь ленты и загрязняет роликоопоры. С роликоопор> на холостой ветви ленты частицы груза падают под конвейер.
Расчет объема просыпи. Просыпь по длине конвейера рас пределяется неравномерно. Чем дальше от разгрузочного бара бана конвейера, тем меньше просыпь. УкрНИИпроектом экспе риментально установлена степенная зависимость между интен сивностью просыпи и параметрами конвейера:
для угля
<7пР = 0,003алБу/Г°'45; |
(4.1> |
для глинистых пород |
|
?пр = 0,01алВ^Г°’9, |
(4-2) |
где <7пр — интенсивность просыпи, м3/(м-ч); |
ал = 0,8ч-0,9 — ко~ |
эффициент, учитывающий полноту очистки ленты от налипшего
материала; |
В — ширина ленты, м; |
v — скорость |
движения |
||
ленты, м/с; |
/с — расстояние |
от |
участка |
просыпи до |
приводной |
головки конвейера, м. |
|
|
|
|
|
Суммарный объем просыпей под конвейером |
|
||||
|
|
L |
Qn\i{U)dlct |
|
|
|
Qnp = |
/к оf |
(4 г |
где Qnp— суммарный объем просыпей под конвейером, м3; /к^- время непрерывной работы конвейера, ч; L — длина конвейере* м.
На основе формул (4.1) — (4.3) суммарный объем просыпей три транспортировании:
угля
Qnp = 0y03aJlBvtKL0A9
пород
QnP = 0,018алВи/к£0*55.
Расчет накопления просыпи за определенный промежуток времени работы конвейера позволяет более рационально ре шать вопросы выбора средств механизации по уборке просыпи. Существующие в настоящее время устройства для уборки просыпи можно подразделить на следующие группы: стационарные скребковые и гребковые, передвижные скребковые и гребковые,
.ленточные и вспомогательные механизмы.
Стационарные скребковые и гребковые устройства для уборки просыпи. На карьерах КМА находятся в эксплуатации шесть конвейерных комплексов, работающих в сочетании с ро торными экскаваторами. Общая длина конвейеров около 40 км, число конвейеров более 50. Максимальная длина конвейеров со ставляет 1900 м при теоретической производительности 8800 м3/ч грунта, ширине ленты 2000 мм, скорости ее движения 5,24 м/с. Одно из основных направлений комплексной механизации уборки просыпи в этих условиях связано с применением уст ройств для переворачивания лент, позволяющих концентриро вать просыпи на ограниченных участках конвейера, подборщи ков и погрузчиков просыпи.
Для уборки просыпи, образующейся в головной части кон вейера под холостой ветвью, разработаны и внедрены в усло виях КМА малогабаритные скребковые подборщики (рис. 4.8, а), которые включаются периодически. Рабочим орга ном является втулочно-роликовая цепь ВР-50.8 со скребками, закрепленными через каждые 3 м. Привод цепи осуществляется отклоняющим барабаном ленточного конвейера через редуктор РМ-250. Просыпь собирается в желобе конвейера и перемеща ется скребками к месту разгрузки. Производительность скреб кового подборщика 4,5 т/ч. Механизация уборки просыпи изпод конвейеров улучшила условия труда рабочих, повысила культуру производства, позволила высвободить 12 чел. Цепь со скребками может быть использована одновременно и как меха низм для очистки ленты. В определенных условиях целесооб разно просыпь перегружать на рабочую ветвь ленты. В этом случае желоб имеет продольную для загрузки просыпи и кри волинейную для подъема и разгрузки просыпи части. Такое устройство можно использовать на любом участке конвейера, где образуется просыпь.
На конвейерах длиной до 100 м уборка просыпи может осу ществляться по всей длине става с помощью каната со скреб ками, устанавливаемыми в желобе или на основании кон
а
|
|
РИС. 4.8. |
|
|
|
|
— скребковый; |
Подборщики |
для |
просыпи: |
3 — виброжелоб; |
||
б — гребковый: / — цепь |
с ковшами; |
2 — емкость; |
||||
— кольцевой: |
/ — кольцо с |
ковшами; 2 — приводной ролик; 3 — опорный ролик; в — |
||||
самоходный ковшовый; |
б —в виде отрезка |
ленты: |
/ — лента; |
2 — тележка |
вейера. По мере накопления просыпи под конвейером автомати чески включается привод лебедки с канатом, и просыпь скребками направляется в течку. В устройствах для уборки просыпи с гребковым рабочим органом вместо скребков ис пользуются ковши, что позволяет исключить из конструкции желоб. Обеспечивается перегрузка просыпи под большим углом, повышается производительность. Однако область при менения ограничивается слабоналипающими сыпучими грузами. Гребковый подборщик просыпи может монтироваться в 1комп лексе с виброжелобом (рис. 4.8, б). Просыпь с приводной го ловки конвейера попадает в виброжелоб и далее поступает в емкость. После заполнения последней просыпь захватывается ковшами, закрепленными на приводной цепи, и передается на рабочую ветвь ленты конвейера. Установка гребковых подбор щиков требует дополнительного рабочего пространства. Более компактную конструкцию имеют кольцевые гребковые подбор щики (рис. 4.8, в). Кольцо с ковшами устанавливается на опор ных и приводных роликах поперек ленты, окружая ее. Направ ляющие элементы удерживают кольцо в вертикальном положе нии. Счищенный с ленты материал падает в ковши нижней части кольца, которое, вращаясь, транспортирует просыпь на ра бочую ветвь ленты. Кольцо включается в работу автоматически вместе с конвейером. На карьерах ФРГ кольцевой подборщик просыпи применяется в комплексе со скреперной установкой возвратно-поступательного действия. Скребки скреперной уста новки подгребают просыпь к кольцевому грузчику. Она попа дает в ковши и кольцом перегружается на рабочую ветвь ленты.
Передвижные скребковые и гребковые устройства для уборки просыпи. На длинных конвейерах карьеров применение стационарных подборщиков становится экономически невыгод ным. Передвижные самоходные подборщики циклического и не прерывного действия обеспечивают захват просыпи на любом участке конвейера и погрузку ее на рабочую ветвь ленты. Оте-
6 Заказ № 14G2 |
161 |
чественные подборщики просыпей типа ППМ-1514 и ПП-Д-443А, разработанные УкрНИИпроектом на базе экскава торов Э-1514 и Д-443А, имеют специальное навесное оборудо вание с ковшевым рабочим органом. В рабочий цикл подбор щиков включаются подъезд к ставу конвейера, ориентирова ние и заведение ковша в просыпь под конвейером, выход ковша из-под конвейера, подъем и выгрузка ковша. Производитель ность рассмотренных подборщиков просыпей на Грушевском и Шевченковском карьерах Марганецкого ГОКа составила 15 и 18 м3/ч при вместимости ковшей 2,3 и 2 м3/ч.
На буроугольных карьерах ГДР в состав комплексов непре рывного действия входят самоходные ковшевые подборщики (рис. 4.8, г), оснащаемые в зависимости от горно-геологических условий и типов конвейеров различным навесным оборудова нием. Обычно навесное оборудование включает в себя систему балок и коромысел, шарнирно соединенных между собой и при водимых в движение гидродомкратами. Одно из коромысел со единяется с рукоятью, на которой монтируется ковш. Для пере мещения ковша по заданной траектории также могут приме няться гидродомкраты. Работа таких установок происходит по циклам, включающим три основные операции: подъезд уста
новки |
в |
заданную зону, |
перемещение |
рукояти с |
ковшом |
|
под конвейер и забор просыпи, перемещение |
ковша |
с про |
||||
сыпью |
в |
точку перегрузки |
просыпи на |
рабочую |
ветвь ленты |
конвейера.
Стационарные ленточные устройства для уборки просыпи.
Подборщики просыпи с ленточным рабочим органом предназна чены для предупреждения образования и уборки просыпи под конвейером. Они собирают и перегружают просыпь в специаль ную емкость или на конвейер, под которым образуется про сыпь, или на другой конвейер транспортной цепи. Нашли при менение два типа ленточных подборщиков просыпи: в виде ленточного конвейерного перегружателя и отрезка ленты, пере мещаемой возвратно-поступательно гибким тяговым органом. В ленточном конвейерном перегружателе, имеющем минималь ные габариты по высоте, нижняя ветвь ленты может опираться не на ролики, а на опоры скольжения, при этом верхняя ветвь ленты скользит по нижней. Лента имеет индивидуальный при вод или кинематически связана с грузонесущим конвейером через зубчатую или фрикционную передачу. Просыпь собира ется на ленте конвейерного перегружателя и транспортируется к узлу разгрузки.
Подборщики просыпи с возвратно-поступательным пере мещением ленты (рис. 4.8, д) включаются в работу периоди чески, по мере накопления на них просыпи. Рекомендуется ленту уборщика устанавливать на каретках, перемещаемых по направляющим с помощью канатов лебедки [28].
Вспомогательные средства уборки просыпи. Наряду с под борщиками просыпи активного действия работают различные
вспомогательные средства. Они способствуют уменьшению про сыпи под конвейером или позволяют производить более тща тельную зачистку подконвейерного пространства от просыпи и пыли. При транспортировании относительно сухих грузов реко мендуется встряхивать холостую ветвь ленты у приводного барабана и удалять упавшие частицы по лотку в общий грузо поток. Для этого в месте установки приводного или отклоняю щего барабанов шарнирно монтируется плита, взаимодей ствующая с лентой со стороны нерабочей обкладки. Под плитой располагается желоб, подвешенный к раме конвейера посред ством рессор. Плите с помощью вибропривода сообщается колебательное движение, которое передается ленте. Последняя встряхивается и очищается от прилипших частиц. Просыпь по падает в желоб и транспортируется в разгрузочную течку кон вейера.
При децентрированном ходе или перегрузке ленты просыпь попадает на нижнюю ее ветвь. Для удаления просыпи нижнюю ветвь ленты выгибают с помощью нажимных роликов (рис. 4,9, а). Просыпь скатывается на боковые наклонные щитки и попадает под конвейер. В этом случае целесообразно применение для уборки просыпи сборной ленты, периодически перемещаемой к месту разгрузки.
На предприятиях, имеющих шламовое хозяйство, для уборки просыпи широко используется гидросмыв (рис. 4.9, б). Желоба из металлических листов или цементной кладки для удаления потока загрязненной воды выполняются с уклоном 5—10 % и перекрываются съемными решетками. Водонапорная сеть дол жна обеспечивать смыв просыпи с полов галерей и зданий гиб ким поливочным рукавом длиной 20—30 м. Просыпь с водой попадает в зумпф, где осаждается на дно и выгружается грей ферным механизмом в транспортное средство или бункер с пи тателем.
На карьерах ГДР нашли применение самоходные пневмоот сасывающие установки (рис. 4.9, в). Они состоят из самоход ной тележки, всасывающей насадки, воздуховода, перегрузоч ного узла и перегружателя. Тележка перемещается вдоль конвейера, при этом всасывающая насадка заводится в подкон вейерное пространство, откуда осуществляется отсос просыпи. Просыпь через воздуховод, перегрузочный узел и перегружа тель попадает на рабочую ветвь ленты конвейера. Пневмоотса сывающая установка может оснащаться барабанным питателем, который монтируется перед всасывающим патрубком, благо даря чему повышается производительность установки.
Марганецким ГОКом разработана пневмоотсасывающая пе редвижная установка эжекторного типа (рис. 4.9, г) производи тельностью 1,5 м3/ч. Она включает в себя всасывающую на садку, рукав для подачи сжатого воздуха, эжектор, тканевый фильтр. Все узлы смонтированы на корпусе с выдвижным дни щем и тележкой, перемещаемой по направляющим рельсам.
|
|
|
|
РИС. |
4.9. |
|
|
|
|
|
Вспомогательные средства уборки |
просыпи: |
|
|
|||
а — нажимные |
ролики: |
1 — нажимной ролик; |
2 — щиток; |
3 — сборная лента; |
б — гидро |
|||
смыв; |
в — пневмоотсасывающая |
установка: |
1 — перегружатель; 2 — воздуховод; |
3 — |
||||
всасывающая |
насадка; |
г —то |
же, эжекторного типа; / — всасывающая насадка; |
2 — |
||||
рукав |
сжатого |
воздуха; |
3 — эжектор; 4 — фильтр; 5 — камера; 6 — днище; |
7 — тележка |
При подаче сжатого воздуха в эжекторе создается разрежение. Частицы просыпи крупностью до 16 мм всасываются насадкой и попадают в пылевую камеру корпуса. За счет избыточного давления в камере воздух проходит через фильтр и выходит на ружу. Крупные частицы и пыль осаждаются на днище, которое периодически выдвигается, и просыпь выгружается на ленту конвейера.
Научно-исследовательским институтом по проблемам Кур ской магнитной аномалии им. Л. Д. Шевякова совместно с Мц.
164
хайловским ГОКом испытана универсальная реактивная уста новка УРУ-01, предназначенная для уборки намерзаемой про сыпи сдувом. Она смонтирована на базе скрепера Д-357 и тур бореактивного авиадвигателя РД-ЗМ. Управление и контроль за работой авиадвигателя осуществляется с пульта управления, установленного в кабине тягача. Регулирование газовой струи задается поворотным механизмом. Технические данные уста новки: скорость перемещения 3—20 км/ч, температура газовой струи 450—500 °С, расход топлива 3,5—4 т/ч, масса 25 т.
4.4. ОЧИСТКА КОНВЕЙЕРНЫХ ЛЕНТ
Проблема эффективной очистки лент остается одной из ос новных при решении задач, связанных с повышением надежно сти работы мощных ленточных конвейеров. Неплановые простои конвейерных комплексов на открытых работах из-за ликвида ции загрязнения элементов конструкции составляют не менее 30 % общей продолжительности простоев. Загрязнение рабочей поверхности ленты приводит к резкому уменьшению тяговой
способности привода, |
увеличению |
износа |
ленты и ролико- |
опор. |
налипания на |
ленту |
транспортируемые |
По интенсивности |
в горнорудной промышленности сыпучие материалы можно раз делить на три категории: слабоналипающие, средненалипающие и сильноналипающие. Существенное влияние на величину нали пания оказывают вид, влажность, крупность транспортируемого материала, а иногда и время его транспортирования. При до ставке, например, мергель из сыпучего переходит в тестообраз ное липкое состояние. С уменьшением плотности, крупности и повышением влажности, времени транспортирования налипание материала возрастает. К слабоналипающим материалам можно отнести кусковые, сухие (влажностью до 5%) кварцитовые, гранитные и известняковые породы, руды черных и цветных металлов, уголь; средненалипающим — мелкосыпучие и влаж ные (более 5%) материалы, перечисленные выше, продукты их переработки на обогатительных фабриках (агломерат, кон центрат), а также сухие мелкосыпучие глинистые породы и
строительные материалы (песок, |
известь, цемент); сильнонали- |
|||
пающим — влажные |
мягкие породы (глина, |
суглинок, мел, |
||
мергель, |
песок) и |
строительные |
материалы |
(бетон, известь, |
цемент). |
|
|
|
|
Все известные средства очистки лент можно разделить на три группы: механические, физико-механические и комплекс ные. Особенностью механической очистки ленты является сило вое воздействие рабочего органа (плотного тела) на прилип ший материал путем сдвига, трения, разрушения, среза, отрыва, и других видов деформации. В физико-механической очистке ленты наряду с силовым воздействием можно изменять свой ства материала и ленты в направлении снижения их взаимного
прилипания. Это позволяет повысить эффективность механиче ской очистки. Комбинация различных средств очистки дает воз можность повысить эффективность очистки ленты.
4 .4 .1 . С Р Е Д С Т В А О Ч И С Т К И К О Н В Е Й Е Р Н Ы Х Л Е Н Т
Механические средства очистки лент. Наиболее распростра нена механическая очистка лент сдвигом, осуществляемая очистными устройствами скребкового типа (рис. 4.10, а).
Эффективность очистки ленты рабочими органами скребко вого типа зависит от геометрии расположения, силы прижатия и материала скребка. Скребки должны устанавливаться на жесткой раме с возможностью регулирования положения рабо чей кромки относительно поверхности ленты. Быстрее изнаши вается средняя часть скребка, поэтому целесообразно выпол нять ее утолщенной. Для очистки сильноналипающих материа лов скребки армируют твердыми сплавами, керамикой. Эластичные скребки лучше работают при очистке слабо- и средненалипающих материалов. Различают автоматически прижим ные и выдвижные по мере износа скребки, оснащаемые упру гими и рычажными механизмами регулирования положения скребка.
Необходимое условие равномерной по ширине ленты очи стки— прямолинейность участка ленты, взаимодействующего со скребком. Это хорошо достигается многоскребковыми устрой ствами (рис. 4.10, б) очистки клавишного типа с индивидуаль ным прижатием отдельных скребков. СО Промтрансниипроекта разработан и широко внедрен на Стойленском ГОКе (КМА) устройство многоскребкового типа (рис. 4.10, в). Он включает поворотные подпружиненные дугообразные держатели со скреб ками, армированными твердым сплавом ВК-15 и расположен ными в шахматном порядке с шагом 200 мм и перекрытием зон очистки на 20 мм. Небольшая толщина рабочей кромки (20 мм) и угол атаки более 90° позволяют снизить прижатие скребка к ленте, а значит, и ее износ. Усилие прижатия скребков для слабо-, средне- и сильноналипающих материалов выбирается равным соответственно 1—5, 6—10 и 11—15 Н/см. Число скреб ков в зависимости от ширины ленты, равной 800, 1000, 1200, 1400, 1600, 1800 и 2000 мм, выбирается соответственно 4, 6, 8, 10, 12, 14 и 16 шт. Полнота очистки лент шириной 1800 мм и со скоростью движения 5 м/с, транспортирующих глину и мергель, составила 95%. Дугообразная форма держателей скребков со здает условия для беспрепятственного отвода очищенного ма териала из зоны расположения скребков.
В Японии успешно применяются скребковые кольцевые очи стители (рис. 4. 10, г). При симметричном расположении отно сительно оси ленты кольцо оснащается приводом, а при несим метричном— работает без привода. Кромка кольца сначала «пропиливает» налипший слой материала, затем сдвигает и
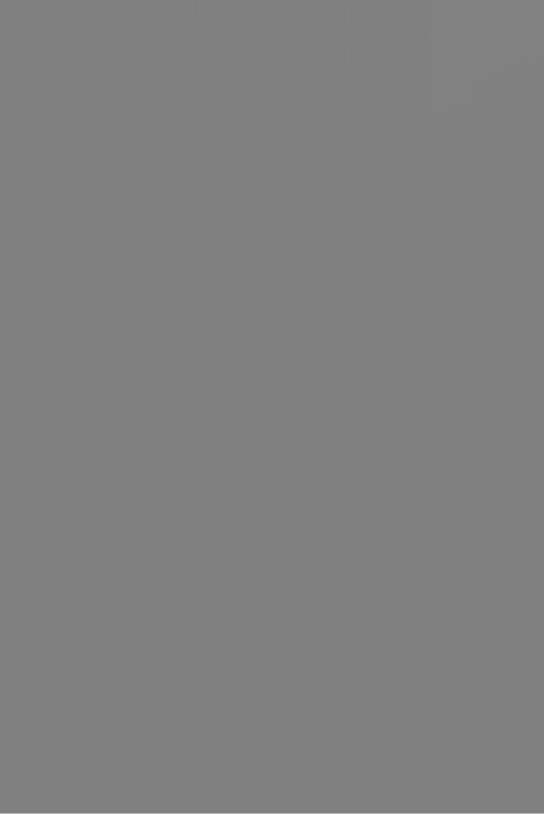
водной замкнутой цепи, движущейся со скоростью, большей или меньшей скорости ленты. Очистка ленты производится верхней, а удаление очищенного материала — нижней ветвью цепи. Кон вейерный очиститель, имеющий громоздкую конструкцию, целе сообразно использовать на мощных конвейерах большой протя женности при транспортировании средненалипающих мате риалов.
Очистка трением, как правило, сопровождается ударным разрушением и отрывом очищаемого материала. Рабочий орган имеет роторную приводную конструкцию с очистными элемен тами в виде жестких или щеточных лопастей — прямых, спира левидных, установленных на горизонтальном приводном валу. В процессе движения ленты рабочие элементы фрикционно и ударно взаимодействуют с ее поверхностью, прогибаются и про скальзывают, унося с собой очищенный слой налипшего мате риала. Гибкое и многоцикловое воздействие рабочего элемента обеспечивает качественную очистку ленты от слабо- и сильноналипающих материалов.
Очистка разрушением, сопровождаемая сдвигом очищаемого материала, характерна для роликовых очистных устройств с ди сковыми неприводными или приводными рабочими элемен тами.
Достоинствами очистки резанием являются наименьшая энергоемкость процесса отделения налипшего материала и про
стота |
компоновки |
рабочего |
элемента. |
Последний |
выполняется |
в виде |
струны или |
прутков |
(рис. 4.10, |
(9). Струна |
или пруток |
легко подрезает налипший слой при минимальном воздействии на ленту. Однако область использования этих устройств огра ничивается слабо- и средненалипающими материалами при ско рости движения ленты до 2,5 м/с, при которой уменьшается вероятность обрыва или перетирания рабочих элементов. Эту задачу можно решить путем намотки струны длиной до 1000 м на катушки и использования реле времени. Через заданные ин тервалы времени непрерывной работы конвейера реле времени автоматически подает команду на привод катушек, которые пе рематывают трос на заданную длину. При этом обеспечивается работа устройства в течение года (5000 ч). В конструкции очи стителя НИИКМА несколько параллельных струн спирально прилегают к ленте на приводном барабане с перекрытием зон очистки. Струны из легированной проволоки (ГОСТ 14 963—78) подпружинены так, что выгибаются при встрече с выступами на ленте. При обрыве струны рычаг, к которому крепится струна, с помощью троса отводится в сторону. Устройство ус
пешно испытано на конвейерах |
роторного комплекса «Михай |
|
л о в а -1» Михайловского ГОКа |
(КМА) при транспортировании |
|
суглинков влажностью до 30 %. |
|
уст |
Очистка лент отрывом обычно реализуется очистными |
||
ройствами вибрационного типа |
(рис. 4.10, е). Достоинство |
очи |
стки вибрацией — отсутствие контакта между рабочим органом
168
(вибратором) и загрязненной поверхностью ленты. Однако этот вид очистки ограничен слабоналипающими материалами. Обычно вибратор устанавливается на подпружиненной опоре, жестко связанной с осью виброролика, взаимодействующего с нерабочей поверхностью ленты. Виброролики могут выпол няться эксцентричными с выступами или ударными билами, встряхивающими ленту, при этом отпадает необходимость в ис пользовании вибратора. Упругая компоновка разгрузочных или отклоняющих барабанов обеспечивает частичную очистку ленты встряхиванием и отвод очищенного материала в течку. Для ре зинотросовых лент, включающих в себя ферромагнитные тросы, применима бесконтактная схема вибрации с использованием электромагнитной системы.
Очистка ленты деформированием осуществляется на откло няющем барабане или на роликах. Вследствие упругих дефор маций в ленте при огибании барабана нарушается сцепление прилипших частиц с рабочей обкладкой. Для обеспечения де формаций изгиба холостая ветвь ленты проходит через систему роликов. Еще больший эффект очистки от изгиба ленты дости гается дисковыми опорами, создающими волнообразные пере гибы ленты по ширине. В точках изгиба ленты слой прилипшего материала ломается и под действием сил тяжести и вибрации отпадает.
Физико-механические средства очистки лент. На обогати тельных фабриках распространена гидро- и, реже, пневмоочи стка ленты. Струя жидкости, направленная под повышенным давлением на ленту, не только механически сдвигает или раз рушает слой налипшего материала, но и изменяет его физиче ские свойства, в частности липкость, спайность. Очищенный ма териал в виде водяной пульпы направленно отводится из зоны очистки и попадает в систему шламового хозяйства. После от стойников очищенный материал может быть возвращен по зам кнутому циклу на ленту конвейера. Гидроочистка особенно эффективна, если жидкость не только соприкасается с лентой, но и ударно воздействует на нее. Для этого под участком от клоненной барабаном ленты устанавливается гидромембрана с лопастным ротором и форсункой (рис. 4.11, а). При подаче жидкости насосом включаются одновременно форсунка и ло пастной ротор, создающий через гидромембрану в жидкостном баке ударные волны. Совместное действие струи жидкости и ударных волн повышает эффективность гидроочистки. Остав шаяся часть налипшего на ленту материала, увлажненная и ос лабленная водой, легко очищается скребком. Гидроочистка — один из самых эффективных способов очистки лент от сильноналипающих материалов.
При пневмоочистке воздушная струя механически сдвигает и отбрасывает частицы материала. Для пневмоочистки очень важно обеспечить постоянство направления и силы воздействия струи воздуха при минимальном расстоянии от сопла до ленты.
РИС. 4.11.
Физико-механические и комбинированные средства очистки лент:
а — ударная |
гидроочистка: |
/ — форсунка; |
2 — лопастной |
ротор; |
|
3 — гидромембрана |
||||||||||
4 — бак |
с водой; |
б — пневмоочистка с |
поворотным |
соплом: |
/ — отжимной |
ролик; |
2-^ |
|||||||||
подпружиненное |
сопло; |
в — магнитная очистка: |
/ — барабан; 2 — упоры; 8 — магниты |
|||||||||||||
г — с помощью гидрофобного покрытия: |
/ |
— гидрофобная |
пленка; |
2 |
—лента; д — с |
по |
||||||||||
мощью |
профилактических |
растворов: |
/ — форсунка; |
2 — механизм |
выключения |
фор |
||||||||||
сунки при прохождении |
стыка; |
3 — контактный |
датчик на |
ленте; |
4 — емкость с |
рас |
||||||||||
твором; |
е— с |
помощью |
липкого |
контура, |
смачиваемого |
водой: |
/ — лента |
конвейера |
||||||||
2 лента липкого контура; |
3 — ванна; |
ж — то |
же, смачиваемого |
флотореагентом: |
|
|||||||||||
комбинированная |
очистка: / — форсунка |
для подачи |
воды; |
2 — цилиндрическая щетка |
||||||||||||
|
|
|
|
3 - скребок; 4 — виброролик |
|
|
|
|
|
|
С этой целью пневмосопло снабжают отжимным роликом, под пружинивают и устанавливают на гофрированном эластичном основании, обеспечивающем поворот сопла при набегании на ролики неровностей ленты (рис. 4.11, б). Удаление очищенного материала может осуществляться с помощью всасывающей ка меры, входящей в состав пневматической системы. Пневмоочи стка применяется на конвейерах, транспортирующих слабоналнпающие материалы. Для гидро- и пневмоочистки характерно минимальное разрушающее воздействие на ленту но сравнению с механическими очистителями.
Разновидностью пневмоочистки является тепловая сушка ленты. Известно, например, использование теплового воздуш ного потока, подаваемого вентилятором двигателя привода кон вейера в коллектор с соплами, обдувающими влажную поверх ность ленты. При этом одновременно осуществляются срыв ка пель влаги с ленты и ее сушка. Сорванные капли попадают
вкамеру пониженного давления и вентилятором отбрасываются
вкаплесборник.
Очищать ленту от материалов, обладающих ферромагнит ными свойствами, можно бесконтактным способом с помощью магнитов, монтируемых на барабане (рис. 4.11, в). Обечайка барабана выполняется из неферромагнитного материала, имеет упоры и смонтированные вдоль обечайки и связанные жестко с ней оси, на которых свободно и эксцентрично подвешены блоки магнитов. Последние в зависимости от углового положе ния обечайки опираются на упоры или под действием собствен ного веса занимают нижнее положение. В процессе очистки ленты частицы груза верхним магнитом притягиваются к обе чайке, а затем при вращении барабана отделяются от него вследствие наличия центробежных сил и ослабления магнитного потока. Затем магнит с помощью упоров занимает рабочее по ложение, и цикл повторяется.
Одно из перспективных направлений по борьбе с загрязне нием конвейерного оборудования связано с уменьшением при липания транспортируемого груза к ленте путем применения гидрофобных (водоотталкивающих) покрытий. На угольных шахтах широко эксплуатируются негорючие ленты на основе поливинилхлорида (ПВХ), которые одновременно обладают и гидрофобными свойствами. На ленту с обкладкой из ПВХ транспортируемый материал прилипает меньше, чем на ленту с обычной резиной. Трение груза о ленты из ПВХ также меньше, что ограничивает их применение на наклонных кон вейерах по условию обеспечения устойчивости груза на ленте. В настоящее время создаются ленты с гидрофобными покры тиями, фрикционные характеристики которых в сравнении с ха рактеристиками обычных лент, изменяются незначительно. Од нако в процессе эксплуатации ленты поверхностный слой рабо чей обкладки становится шероховатым, в результате чего ухудшаются гидрофобные свойства покрытия.
Промтрансниипроектом рекомендуется гидрофобное покры тие выполнять съемным (рис. 4.11, г). Для этого гидрофобная пленка или тонкая гидрофобная лента наклеивается на обыч ную ленту только в отдельных точках на краевых участках или в средней части. Транспортируемый материал загружается на пленку. На разгрузочном барабане происходит отрыв мате риала от гидрофобного покрытия, и лента самоочищается. Кроме очистительной функции гидрофобная пленка или тонкая лента играет роль защитного элемента, предохраняющего ленту от ударного и фрикционного износа. После износа пленки ее легко отделяют от рабочей обкладки и наклеивают новую.
Для борьбы с налипанием в последние годы проводились ис следования по применению различных химических веществ и растворов. Последние в качестве профилактического покрытия наносятся на ленту, выполняя функцию подложки. Прилипание подложки к ленте и транспортируемому материалу меньше, чем прилипание материала к ленте, вследствие чего лента при раз грузке очищается.
Свердловским горным институтом им. Вахрушева совместно с заводом резинотехнических изделий испытан ряд профилакти ческих растворов (рис. 4.11, д). Наиболее эффективен 45 %-ный раствор хлористого кальция, который рекомендован к промыш ленному внедрению. В установку для нанесения раствора на ленту входят емкость с раствором, насос, трубопроводы, вен тиль, форсунки. Чтобы исключить попадание раствора на стыки ленты, последняя может оснащаться контактным элементом, взаимодействующим с рычажной системой управления запор ным клапаном. Контактный элемент монтируется впереди стыка. При набегании контактного элемента на ролик рычаж ной системы запорный клапан прекращает подачу раствора к форсункам. Затем ролик опускается, нажимает на подпружи ненный рычаг с грузом, создающий заданную выдержку вре мени, и запорный клапан возвращается в исходное положение для подачи раствора.
Известный термодинамический способ борьбы с налипанием и намерзанием горной массы на ленту позволяет также осуще ствлять профилактическую обработку поверхности ленты. Об разующаяся при сгорании топлива сажа вместе с потоком горя чего воздуха напыляется на ленту в виде тонкого слоя. Отрыв липкого материала, находящегося на ленте, происходит по слою сажи. Необходимо стремиться к тому, чтобы влажность сажи была наименьшей, в противном случае резко снижается ее за щитное действие [29].
На ленточных конвейерах обогатительных фабрик, транс портирующих мелкосыпучие влажные материалы, возможно применение для очистки ленты липких подвижных контуров (рис. 4.11, е). Лента очистного устройства сначала соприкаса
ется с водой в ванне, смачивается и затем |
вступает в контакт |
с загрязненной лентой конвейера. Частицы |
материала отрыва |
ются от загрязненной ленты и прилипают к ленте очистного устройства, которая затем очищается водой в ванне. Ленты мо гут перемещаться навстречу друг другу или вдвигаться в одну сторону в зависимости от степени ее загрязнения. Устройство, работающее на аналогичном принципе, испытано Днепропет ровским горным институтом им. Артема. В отличие от рассмот ренного выше лента очистного устройства смачивается через форсунку флотореагентом, обладающим повышенными липкими свойствами (рис. 4.11, oic). Налипшие на ленту очистного уст ройства частицы груза счищаются затем скребком. Оставшийся на ленте конвейера флотореагент смывается форсункой, подаю щей воду.
Комбинированные средства очистки лент. На конвейерах, транспортирующих сильноналипающие материалы, ни одно из применяемых в промышленности отдельно работающих уст ройств не обеспечивает полной очистки лент. Наиболее эффек тивно сочетание скребковых, щеточных, вибрационных рабочих элементов, гидроочистки и сушки. На разгрузочном или обвод ном барабане устанавливается скребок грубой очистки, снимаю щий основной слой налипшего материала. Затем ленту очи щают струей воды, выходящей из форсунок, повышенного дав ления и дополнительно очищают цилиндрическими щетками, устанавливаемыми прямо или под углом к ленте (рис. 4.11, з). Далее лента проходит через скребки и ролики тонкой очистки, вибрационный ролик и камеру сушки. Многоступенчатая очи стка ленты используется на предприятиях, имеющих шламовое хозяйство в транспортных линиях, где по техническим условиям требуется высокая степень очистки ленты. Более полные дан ные о некоторых из вышерассмотренных средств очистки и ва риантах их исполнения для различных условий эксплуатации конвейеров изложены в работе [30].
4.5. ПЕРЕВОРАЧИВАНИЕ КОНВЕЙЕРНЫХ ЛЕНТ
Переворачивание конвейерных лент (ПКЛ) оказывает су щественное влияние на характер эксплуатации основных узлов конвейера, транспортирующего налипающие материалы. Лента при переворачивании опирается на роликоопоры только своей чистой стороной. Отпадает необходимость в очистке ленты, уменьшается загрязнение роликоопор на холостой ветви и соот ветственно просыпи на линейной части конвейера, снижается износ ленты и роликоопор, повышается надежность работы и уменьшается трудоемкость обслуживания конвейера, улучша ются условия труда. ПКЛ способствует решению проблемы до ставки груза одним ленточным конвейером в обоих направле ниях, использования в горных выработках конвейеров с нижней грузонесущей ветвью.
Однако ПКЛ не нашло пока широкого распространения, очевидно, из-за того, что требует оснащения конвейера опреде
ленно расположенной системой опорно-направляющих элементов усиленной конструкции, геометрия установки которых сущест венно зависит от ширины, упругих свойств, натяжения, скорости движения и степени загрязнения ленты, высоты подкон вейерного пространства, условий монтажа оборудования при водных и натяжных станций. При ПКЛ лента на участке пере ворачивания занимает винтообразное положение, при котором испытывает дополнительные фрикционные нагрузки от опорно направляющих элементов, растяжение по основе и утку, дефор мации сдвига слоев, а также возникает вероятность нарушения устойчивого формообразования (ведущего к «выбегу» ленты) и центрированного хода ленты, повышается вероятность возник новения автоколебательного режима движения ленты, повыша ются просыпи на концевых участках конвейера. Для лент ши риной более 1200 мм возникает необходимость в изменении высоты установки базовых балок става, необходимы определен ные навыки в осуществлении и контроле ПКЛ.
В соответствии с перечисленным можно сформулировать ос новные требования к оборудованию ПКЛ: система опорно-на правляющих элементов должна работать при минимальных (в пределах упругих) деформациях растяжения ленты по ос нове и утку, фрикционных нагрузках на ленту и опорно-направ ляющие ролики, сохранении устойчивого оптимального формо образования и центрированного хода ленты. Положение опорно-направляющих элементов в случае необходимости дол жно оперативно регулироваться. ПКЛ должно осуществляться при минимальном числе опорно-направляющих элементов и из менении конструктивных параметров ставов.
Промтрансниипроектом проведен комплекс исследований процесса ПКЛ, разработаны и испытаны в промышленных ус ловиях различные типы устройств для переворачивания лент. Полученные результаты подтверждают перспективность широ кого применения ПКЛ, особенно на мощных конвейерах горно рудной промышленности.
4 .5 .1 . С Х Е М Ы П Е Р Е В О Р А Ч И В А Н И Я Л Е Н Т
ПКЛ осуществляется обычно на холостой ветви ленты у го ловного и хвостового барабанов. На участках, называемых зо нами переворачивания, лента занимает винтообразное положе ние. Суммарный угол разворота ленты в двух зонах перевора чивания составляет 360°, т. е. она возвращается в исходное положение. ПКЛ, осуществляемое без применения опорно-на правляющих элементов, принято называть свободным, а с при менением опорно-направляющих элементов — направленным.
При свободном ПКЛ лента в процессе движения поддержи вается с помощью барабанов и ограничительных роликов, рас положенных по концам участка переворачивания (рис. 4.12, а). При этом лента принимает естественное, присущее упругой
174
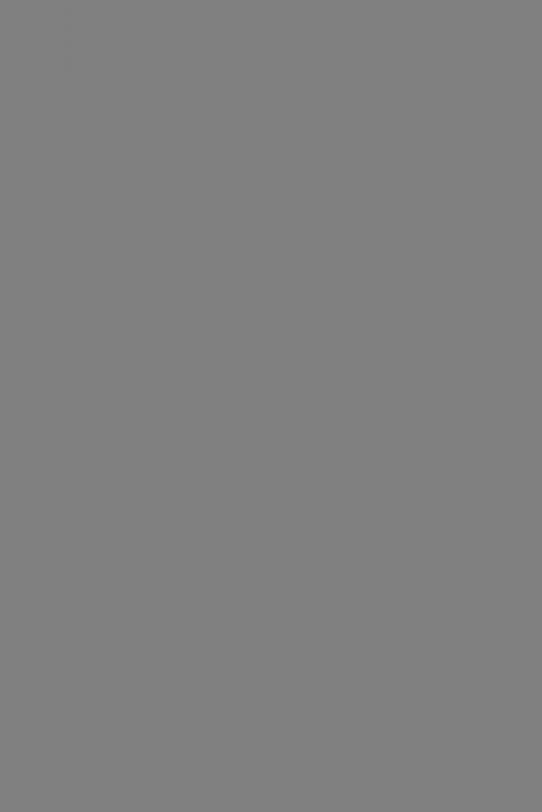
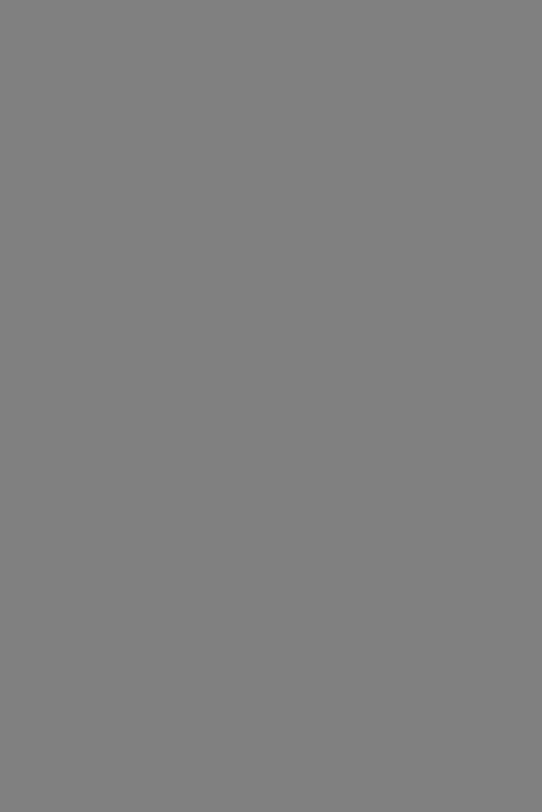
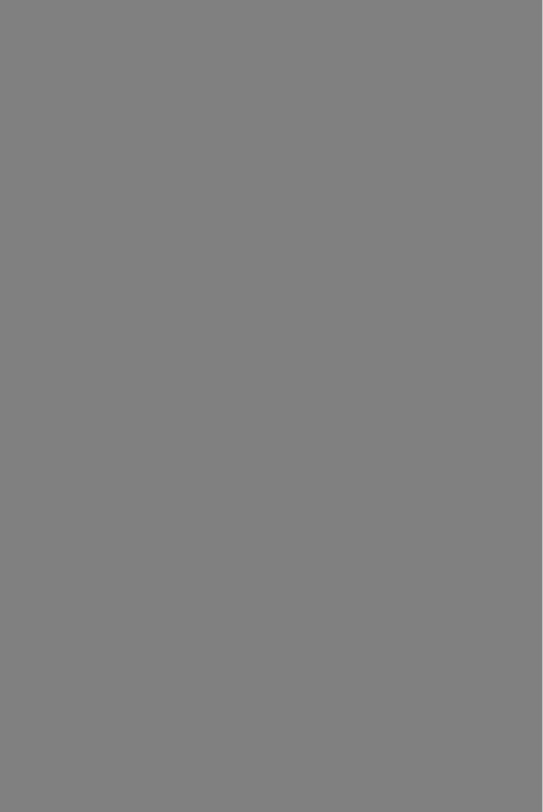
положения роликов. Число роликов в гирлянде, их длину и диа метр выбирают в зависимости от ширины ленты. Дефлекторный ролик монтируется в плоскости гирлянды с наклоном и предо храняет кромки ленты от трения о металлоконструкцию. Регу лирование положения роликов позволяет достичь оптимального опорного профиля ленты в зоне переворачивания, при котором обеспечивается наибольшая площадь контакта роликов с лен той. Ролики гирлянды создают плавный изгиб ленты.
Внутреннее расположение опорно-направляющих элементов характерно для лент шириной более 1400 мм. В зоне перевора чивания широких лент проявляется тенденция к нарушению Со образного профиля ленты, так как вес верхней нависающей части ленты превышают силы упругости. При этом лента складыва ется с резким изгибом в средней части. Чтобы избежать этого, верхнюю нависающую часть ленты подпирают опорно-направ ляющими элементами. Переворачивание ленты с внутренним расположением опорно-направлящих элементов более трудо емко в осуществлении, так как требует применения держателей сложной конструкции.
Развитием рассмотренной выше схемы расположения опорно-направляющих элементов является комбинированная, при которой широкие ленты подпираются опорно-направляю щими элементами с обеих сторон. При этом обеспечиваются уменьшение влияния веса ленты на вертикальный прогиб всего ее контура и нависающей верхней части.
Выбор схем ПКЛ и конструкции опорно-направляющих эле ментов зависит от конкретных условий эксплуатации и пара метров конвейеров. Для разработки оптимальных конструктив ных решений в технике ПКЛ и практических рекомендаций по их применению были проведены исследования деформации и устойчивости лент при переворачивании.
4.5.2. ДЕФОРМАЦИЯ И УСТОЙЧИВОСТЬ ЛЕНТ
ПРИ ПЕРЕВОРАЧИВАНИИ
Исследовался процесс ПКЛ с целью определения величины и характера деформаций ленты, условий устойчивости ее фор мообразования и движения при изменении основных парамет ров (типа, натяжения, ширины и скорости движения ленты, длины зоны переворачивания, конструкции и параметров опор но-направляющих элементов) и высоты подконвейерного про странства. Условиями нормального ПКЛ были приняты: удли нение ленты (по основе и утку для резинотканевых и по основе для резинотросовых) в пределах упругой деформации; устой чивое формообразование ленты (без резких изгибов и перело мов); устойчивое центрированное движение без возникновения автоколебательного режима с большими амплитудами и часто тами; отсутствие существенного проскальзывания ленты отно сительно опорно-направляющих элементов; осуществление ПКЛ
без реконструкции става по высоте или с минимальной ее кор ректировкой.
Экспериментальные исследования проводились на промыш ленном ленточном конвейере Челябинского металлургического завода, транспортирующем доломит крупностью 5—15 мм. Ос новные параметры стенда: длина 76,5 м, угол наклона 12°, ши рина ленты 1200 мм, скорость движения ленты 1,68—3,34 м/с, мощность привода 100 кВт, натяжное устройство — грузовое. Контур ленты выполнен составным из лент на основе тканей ТА-100, БКНЛ-150 и Б-820, состыкованных вулканизацией. Тех ническая характеристика лент, состыкованных на эксперимен тальном конвейере, приведена в табл. 4.2.
Стенд оснащался опорно-направляющими элементами шари кового, дискового, гирляндного типа и прямыми роликоопорами, выполняющими функцию ограничительных роликов. Длина зоны ПКЛ изменялась в пределах 8—145, где В — ширина ленты. Измерение деформации ленты по основе и утку в стати ческом режиме осуществлялось с помощью металлической ру летки и тензометрических датчиков с электронной аппаратурой, а в динамическом режиме (в процессе движения) — только дат чиками. Для исследования формообразования ленты в различ ных точках зоны переворачивания использовались гибкие шаб лоны, фотографирование и визуальные наблюдения. При прямых линейных измерениях удлинений ленты по основе опре делялась последовательно длина участков ленты по кромкам и сравнивалась с базовой величиной, соответствующей плоскому положению ленты за зоной переворачивания. Тензометрические измерения деформаций ленты делались с применением резино проволочных датчиков, измерительного моста и 12-канального светолучевого осциллографа.
Деформация лент. Чтобы дать оценку экспериментальным значениям удлинений ленты, связанных с переворачиванием, не обходимо знать удлинения ленты в обычных условиях на рабо чей и холостой ветвях. Упругое удлинение холостой ветви ленты
|
|
|
ТАБЛИЦА 4.2 |
|
|
Тип ткани |
|
Параметры |
ТА-100 |
БКНЛ-150 |
Б-820 |
|
|||
Длина, м |
27 |
100 |
30 |
Ширина, мм |
1200 |
1200 |
1200 |
Число прокладок |
5 |
5 |
5 |
Прочность на разрыв по основе, даН/см |
100 |
150 |
55 |
Относительное удлинение при рабочей |
3,5 |
3,5 |
4,5 |
нагрузке (10 % разрывной), °/ |
|
|
|
Толщина обкладки, мм: |
|
|
3 |
рабочей |
4,5 |
3 |
|
нерабочей |
2 |
2 |
2 |
от натяжения при номинальной загрузке конвейера меньше, чем на рабочей ветви. Таким образом, разницу в удлинениях ленты на обеих ветвях можно приближенно принять за диапазон до пустимых удлинений ленты при переворачивании:
вп. д — ел — е„,
где еп. д — допустимое удлинение ленты на холостой ветви при переворачивании, %; ел — упругое удлинение ленты на рабочей ветви при номинальной нагрузке, %; вн — упругое удлинение ленты на холостой ветви от начального натяжения SH, равного натяжению на сбегающей ветви ленты, Ло
зная удлинение ленты при рабочей нагрузке и предполагая линейную зависимость между нагрузкой на ленту и ее удлине
нием, можно записать |
|
е„ = ел^ _ , |
(4.4) |
•^нб |
|
где 5Сб — натяжение на сбегающей ветви ленты; 5 Нб — натяже ние на набегающей ветви ленты,
S„б < Scee^, |
(4.5) |
где е — основание натурального логарифма; |
ц — коэффициент |
сцепления ленты с приводным барабаном; а — угол обхвата ба рабана лентой, рад.
Отношение 5 Нб/5Сб, равное еи“, принято называть тяговым фактором. Допустимое натяжение ленты на набегающей ветви для выбранной ленты
SH6= SpBi/n, |
(4.6) |
где 5 Р — разрывное усилие ленты; В — ширина ленты; i — число прокладок в ленте; п — запас прочности резинотканевых лент (п=10).
Натяжение ленты на сбегающей ветви с учетом запаса по сцеплению
Sc6 = K ,SFBi/(ne^), |
(4.7) |
где /Ст=1,15ч-1,2 — коэффициент запаса по сцеплению |
ленты |
с приводным барабаном. |
|
Согласно зависимостям (4.4) — (4.7), получим |
|
е» = ел/Ст/е|1а); |
(4.8) |
|
<«> |
Из формулы (4.9) следует, что диапазон допустимого удли нения ленты при переворачивании пропорционален пределу ее упругого удлинения и величине тягового фактора. Значения еп. д можно определить по графику (рис. 4.14, а). При более точных расчетах величина удлинения ленты на холостой ветви отдельно
|
РИС. |
4.14. |
|
|
|
|
|
Зависимости |
удлинений кромок |
ленты |
в |
зоне |
переворачивания: |
||
а — расчетных допустимых (1—3 —для е, |
равного |
2, |
3, 4% соответственно); |
б—г — |
|||
экспериментальных соответственно для ленты ТА-100 |
при |
SM->2,4% |
5 р; БКНЛ-150 |
||||
при 5 Н=1,6% S p ; |
Б-820 при SH—4,4 % Sp;l—схема |
переворачивания |
ленты |
направ |
|||
|
ленная; 2 — то же, |
свободная; |
L n = 13B |
|
|
для головной и хвостовой зон ПКЛ и соответствующее ему на тяжение ленты определяют методом обхода по контуру ленты.
Экспериментальными исследованиями установлен характер изменения и величины деформаций ленты в статическом ре жиме при различных условиях переворачивания (рис.4.14, б—г). При свободном ПКЛ графики зависимости удлинений (еп) кро мок ленты по длине зоны переворачивания (Ln) имеют волно образную форму с максимумами на концевых участках зоны переворачивания (пределы изменения еп составляют0,1—1,1 %). При ПКЛ с использованием опорно-направляющих элементов эти зависимости также имеют волнообразную форму с макси мумами на концевых и средней частях зоны переворачивания (пределы изменения еп составляют 0,2—0,8%). Наличие трех максимумов связано с установкой в средней части зоны перево рачивания ленты опорно-направляющих элементов [31]. Заметно влияние жесткости ленты на характер изменений удлинений при свободной и направленной схемах переворачивания ленты. Чем жестче лента, тем больше удлинение кромок ленты в сред ней части зоны переворачивания. Для ленты БКНЛ-150 оно до стигает 0,4% (при SH=1,6% S p и Ln= l3B y е^а = 6). Причем
максимум удлинений для данного случая принадлежит направ ленной схеме переворачивания (рис. 4.14, в). В общем случае можно отметить меньший уровень удлинений ленты по кромкам при направленном переворачивании. Это происходит благодаря перераспределению деформации ленты. Опорно-направляющие элементы, уменьшая удлинение ленты по кромкам, одновре менно увеличивают поперечный изгиб ленты, т. е. удлинение ленты по утку.
Следует отметить отличие в характере распределения и ве личине удлинений обеих кромок ленты. Зависимости имеют противоположное направление, которое соответствует противо положному расположению гребнеобразных участков двух кро мок лент. Одна из кромок ленты имеет меньший, а другая — больший уровень удлинений, связанных с несимметричным де формированием ленты по кромкам. Например, для ленты ТА-100 (рис. 4.15, а) одна из кромок ленты имеет удлинение 0,3—0,8 %, а другая — 0,05—0,45 % (при SH=2,4 % Sp, L„=13B, euo _ 4 ). с увеличением натяжения ленты уменьшаются пре-
|
|
РИС. |
4. is. |
|
|
|
|
|
|
|
Зависимости удлинений |
кромок ленты |
ТА -100: |
переворачи |
|||||
« — в — при изменении ее |
натяжения; г, |
д — при изменении |
длины зоны |
||||||
вания; |
а — при S H—2,4 % Sp и Ln —\ЗВ; |
б — при |
S H-2,8 % S p и |
1П-13£; |
в — при S H^= |
||||
-3,35% |
Sp и Ln = 13B; г - |
при S H=2,4 % S p и |
Ln - llS ; |
д - |
при |
S H-2,8 % S ppH,Ln=: |
|||
|
—11 В; |
t, 2 — первая |
и вторая кромки |
ленты |
|
|
делы изменения удлинений ленты в кромках и одновременна происходит некоторое выравнивание удлинений кромок ленты по длине зоны переворачивания (рис. 4.15, б, в). В этом случае также возникает перераспределение деформаций, часть из кото рых переходит на уток. С уменьшением длины зоны ПКЛ (рис. 4.15, г, б) рассмотренная закономерность сохраняется, од нако при этом возрастают пределы изменения удлинений кро мок ленты, которые для кромки с большими деформациями со
ставляют 0,5—1,25% (при |
5 Н= 2,4% Sp, е^а = 4, |
Ln=l l B) и |
0,05—0,7% (при 5„ = 2,8% |
Sp, е^а = 3,5, Ln=l l B) . |
Установлено, |
что для лент ТА-100, БКНЛ-150 и Б-820 рациональными явля ются следующие сочетания параметров 5„ и Ln:S H= 2,8% Sp и Ln=(ll-f-13)B; SH= 1,9 % 5Р и Ln=13B; 5„ = 4,4 % SpHLn=12B.
На основе полученных экспериментальных данных и расчет ных значений удлинений лент в зависимости от натяжения мо жно сделать вывод, что при рациональных значениях натяже ния ленты и длины зоны переворачивания, а также схемах переворачивания суммарное удлинение ленты не превышает пре дела упругого удлинения лент при рабочей нагрузке, составляющего 3—4%. Установлено, что в отдельных случаях максимальные удлинения ленты по основе при переворачива нии возникают не на кромках, а по продольной линии, располо женной в центре между бортом и осью ленты в зоне между гра ницей участка переворачивания и опорно-направляющими эле ментами. Характер распределения удлинений ленты в зоне переворачивания зависит от длины этой зоны, натяжения ленты и установки опорно-направляющих элементов. Величина удли нений утка ленты ТА-100 (при SH= 2,8 % Sp и Ln=13fi) состав ляет 0,05—2,1 % при смещении максимума по ширине ленты к прилегающей к одной из кромок зоне и по длине зоны пере ворачивания к одному из концевых участков.
Исследовались удлинения ленты по основе и утку в дина мическом режиме. При пуске конвейера в ленте возникает коле бательный процесс с небольшой амплитудой и переменной ча стотой, который быстро затухает. В первый момент времени натяжение ленты падает, а ее растяжение уменьшается. В даль нейшем удлинение ленты по основе и утку возрастает, превы шая статическое не более чем на 25%. В установившемся ре жиме удлинения ленты близки к статическим. Аналогична торможение конвейера не оказывает существенного влияния на характер удлинений ленты.
Характер и величина деформаций резинотросовых лент при переворачивании отличается от резинотканевых. Резинотросо вые ленты имеют большие массу и продольную жесткость и меньшую поперечную жесткость. Процесс формообразования в зоне переворачивания резинотросовых лент более сложен (одновременно действуют сложный изгиб и сдвиг), так как тросы при рабочей нагрузке имеют меньшее упругое удлинение (до 0,25%). Малое удлинение и большая масса резинотросовых
лент приводят к увеличению длины зоны переворачивания и ограничивают выбор схемы. Установлено, что для резинотросо вых лент может быть рекомендовано только направленное пере ворачивание с внешним расположением опорно-направляющих элементов для лент шириной до 1200 мм и комбинированным расположением опорно-направляющих элементов для лент ши риной 1400—2400 мм. При этом Ln> \bB и возрастает с увели чением ширины ленты (например, для лент шириной 900 мм Хп=14—15В, а для лент шириной 1800 мм — Ln = 20—255).
Устойчивость лент. Нарушение формообразования ленты при переворачивании, связанное с переходом ленты из С-образного положения в S-образное, характеризует потерю устойчивости деформирования ленты. При S-образном положении ленты резко возрастает ее деформация по утку. Наблюдается тенден ция к «выбегу» перевернутого участка ленты, в результате ко торого возникает опасность разрушения ленты. Переход к S-об- разному сечению ленты происходит с увеличением натяжения ленты и уменьшением длины зоны переворачивания. Исследо ван механизм и граничные условия потери устойчивого движе ния ленты. При оптимальных значениях натяжения ленты и длины зоны переворачивания лента в средней части зоны пере ворачивания имеет С-образное сечение и процесс переворачива ния ленты происходит устойчиво. На концевых участках зоны переворачивания располагаются гребни, а в средней части лента диагонально сложена (рис. 4.16, а). С уменьшением натяжения ленты или длины зоны переворачивания у ограничи тельных роликов на участке, прилегающем к гребню, образу ется конусовидное вздутие. Это свидетельствует о возникнове нии неустойчивого режима движения ленты. Дальнейшее увели-
П ар ам етр ы
|
|
|
|
|
|
|
|
|
Б -820 |
|
|
|
Натяжение |
ленты |
( 5 „ |
4 ,4 |
4 ,4 |
4 ,4 |
5 ,2 |
5 ,2 |
6 ,5 |
2 ,4 |
|||
от Sp), |
% |
|
|
|
|
|
|
|
|
|
|
|
Длина зоны переворачи |
1 3 5 |
1 1 5 |
9 5 |
1 3 5 |
1 1 5 |
1 3 5 |
1 3 5 |
|||||
вания ( L n), м |
|
|
|
|
|
|
|
|
|
|||
Удлинение |
кромок |
лен |
|
|
|
|
|
|
|
|||
ты, %: |
|
|
|
|
|
|
|
|
|
|
|
|
от |
натяжения еп |
|
1,98 |
1,98 |
1,98 |
2 ,3 4 |
2 ,3 4 |
2 ,7 |
0 ,8 4 |
|||
при |
% |
переворачивании |
0 ,7 5 |
1,3 |
1,0 |
— |
— |
— |
0 ,6 5 |
|||
е п. |
|
|
|
|
|
|
|
|
|
|
|
|
суммарное (е„ + |
|
еп) |
2 ,7 3 |
3 ,2 8 |
2 ,9 8 |
— |
— |
— |
1,49 |
|||
Минимальный |
радиус |
145 |
100 |
92 |
|
|
|
155 |
||||
кривизны ленты по утку, |
|
|
|
|
|
|
|
|||||
мм |
|
|
|
|
|
|
|
|
|
|
|
|
Форма |
сечения |
ленты |
С |
С |
S |
S |
S |
S |
С |
<С- или S-образная)
чение натяжения ленты приводит к увеличению размеров взду тия, которое, нарастая, перемещается к среднему участку зоны переворачивания, и лента быстро переходит из С-образного в S-образное положение (рис. 4.16, б). Опасность возникнове ния S-образного сечения ленты в том, что оно ведет к наруше нию процесса разворота ленты на опорно-направляющих эле ментах и защемлению ее между ограничительными роликами (рис. 4.16, в), которое переходит в складку. Сложенный участок ленты перемещается из зоны переворачивания за ограничитель ные ролики. Этот момент характеризуется как «выбег» ленты (рис. 4.16, г). Лента в сложенном состоянии перемещается
вограниченном по высоте пространстве между роликоопорами
иперекрытием, из-за чего возникает вероятность заклинивания
иразрыва ленты. С потерей устойчивости движения в ленте, стремящейся к изменению геометрического расположения сво его сечения, сокращаются расстояния пробега крайних по ши рине ленты точек в зоне переворачивания, резко уменьшаются удлинения ленты по основе и возрастают удлинения по утку. При этом последние превышают пределы упругости, в резуль тате не исключено возникновение местных порывов. Образова нию S-образного сечения ленты способствует также уменьшение
еежесткости. Данные экспериментальных исследований позво ляют установить граничные условия устойчивого движения ленты.
Втабл. 4.3 приведены граничные условия потери устойчи вости формообразования ленты при переворачивании (переход от С-образного к S-образному сечению).
Для обеспечения устойчивости деформирования резиноткане вой ленты следует принимать ЬП>9В. Причем предварительное
|
|
|
|
|
|
|
|
|
ТАБЛИЦА 4.3 |
|
|
Тип ленты |
|
|
|
|
|
|
|
|
|
|
|
ТА-100 |
|
|
|
|
БКНЛ-150 |
|
|
|
2,4 |
2,4 |
2,8 |
2,8 |
3,3 |
1,6 |
1,6 |
1,6 |
1,9 |
1,9 |
2,2 |
и в |
9В |
13В |
11В |
13В |
13В |
11В |
9В |
13В |
ИВ |
13В |
0,84 |
0,84 |
0,98 |
0,98 |
1,16 |
0,56 |
0,56 |
0,56 |
0,66 |
0,66 |
0,77 |
1,2 |
1,0 |
0,5 |
0,6 |
0,8 |
0,75 |
1,65 |
1,0 |
0,46 |
0,8 |
0,65 |
2,04 |
1,84 |
1,48 |
1,58 |
1,96 |
1,41 |
2,21 |
1,56 |
1,11 |
1,46 |
1,42 |
150 |
74 |
160 |
150 |
140 |
185 |
175 |
71 |
165 |
166 |
182 |
С |
S |
С |
С |
С |
С |
С |
S |
С |
С |
С |
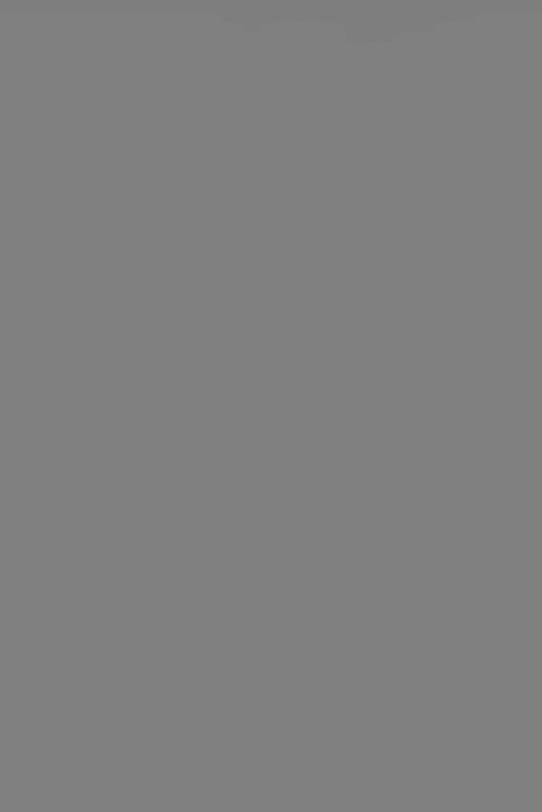
равление, до минимума снижают предварительное натяжение. В хвостовой части конвейера на длине 20—24В снимают под держивающие ролики холостой ветви. На расстоянии 10—12В от натяжного барабана вручную или с помощью лебедок ленту переворачивают на 180° (рис. 4.17, а, б). В этом месте устанав ливают ограничительные ролики, в результате чего образуются две зоны переворачивания, одна из которых расположена между натяжным барабаном и ограничительными роликами, другая — между ограничительными и крайним поддерживаю щим роликом (рис. 4.17, в). В средней части второй зоны пере ворачивания ленту перевязывают канатом и предварительно натягивают. Периодическими запусками конвейера перевязан ный участок ленты перемещают в сторону приводного бара бана. Через каждые 20—30 м в процессе протягивания ленты поддерживающие ролики перед этим участком снимают, а затем устанавливают вновь, причем минимальная длина перемещае мого участка поддерживается в пределах 10—12В (рис. 4.17, г). Далее вторая зона переворачивания перемещается до головного барабана и фиксируется ограничительными роликами (рис. 4.17, б). Съем и установку поддерживающих роликов осу ществляют вручную или с помощью специальных приспособ лений. Все поперечные связи става в подконвейерном простран стве, мешающие перемещению ленты, снимают. После фикса ции обеих зон переворачивания кольцевую обвязку снимают и монтируют опорно-направляющие элементы. Наладку устрой ства производят при неподвижной ленте (рис. 4.17, е), регули руя положение узлов. После этого проверяют работу устройства в процессе движения ленты, контролируя устойчивость и прямо линейность хода ленты, характер ее взаимодействия с узлами.
Опыт внедрения. Внедрение направленной схемы перевора чивания ленты с опорно-направляющими элементами гирляндного и роликового типов осуществлялось на конвейерах Магни тогорского металлургического комбината, Балаклавского рудоуправления им. А. М. Горького и производственного объ единения «Глинозем».
В табл. 4.4 дана характеристика внедренных устройств для переворачивания ленты на предприятиях.
На конвейерах Магнитогорского металлургического комби ната внедрены устройства для переворачивания ленты с внеш ним расположением опорно-направляющих элементов гирляндного (рис. 4.18, а) и роликового (рис. 4.18, б) типов. В устройстве с гирляндными опорно-направляющими элемен тами вместо верхнего прижимного ролика может быть исполь зована прямая роликоопора холостой ветви ленты, выполняю щая функцию верхнего габаритного ролика. Аналогичные роликоопоры в целях уменьшения габаритов рабочего простран ства устанавливаются на концевых участках непосредственно над основанием конвейера. Длина зоны переворачивания ленты на конвейерах М-20 и СДР-1 составляла 12,6—15,3 м, т. е.
а
Монтаж устройства для переворачивания ленты:
, 6 — разворот |
ленты на |
180° соответственно с помощью |
двух |
лебедок и |
с помощью |
||
Двух лебедок |
и |
блока: |
/ — зажим; 2 — канат; |
3 — лебедка; |
4 — лента; |
5 — блок; |
|
в—? — последовательность |
образования двух зон переворачивания ленты: |
/ — ограни |
|||||
чительные ролики; |
2 — обвязка; 3 — роликоопоры |
холостой |
ветви ленты; |
4 — опорно |
|||
|
|
|
направляющие элементы |
|
|
|
10,5—12,75В. Установлено, что геометрическое положение ленты в пространстве на участке переворачивания зависит не только от натяжения ленты и длины зоны переворачивания, но и от высоты подконвейерного пространства. Сначала ограничитель ные ролики устанавливались на одной горизонтальной оси вдоль конвейера, при этом лента занимала положение наклон ного параллелограмма (рис. 4.19, а). При высоте подконвейер ного пространства 760 мм наблюдалось периодическое контак тирование гребней ленты с поперечинами базовых балок и основанием конвейера. После разнесения ограничительных ро ликов по высоте (по диагонали) параллелограммный контур расположения ленты стал горизонтальным. При этом исчезло трение гребней ленты. Такую более рациональную с точки зре ния экономии рабочего пространства схему расположения огра ничительных роликов принято называть диагональной (рис. 4.19, б). При диагональной схеме расположения ограни чительных роликов граница участка переворачивания начина ется сразу после отклоняющего барабана, выполняющего функ цию одного из ограничительных роликов. Интервал между
Устройства для переворачивания ленты:
а — с опорно-направляющими элементами гирляндного |
типа; б — то же, |
роликового: |
/ — прижимной ролик; 2 — дефлекторный ролик; |
3 — ролик гирлянды; |
4 — лента |
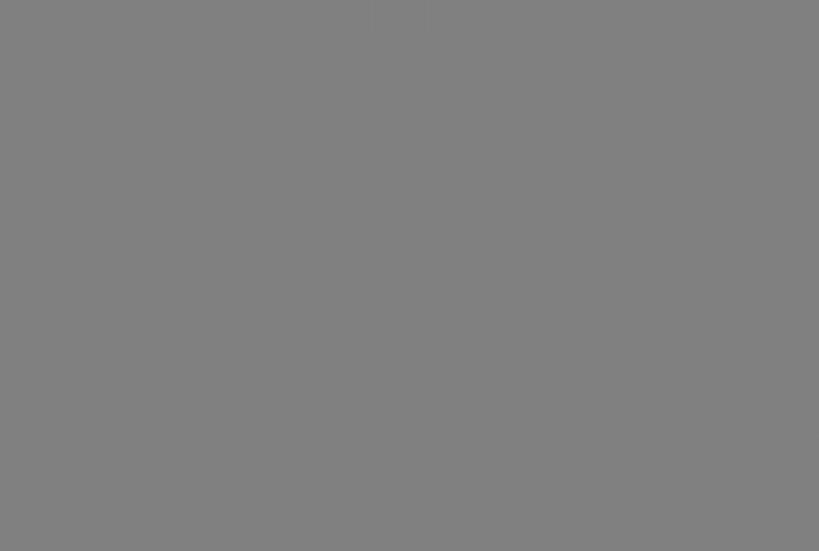
Схемы переворачивания лент:
а — с параллельным |
расположением |
ограничительных |
роликов; б, |
в — то |
же, |
диаго |
|
нальным: / — отклоняющий барабан; |
2 — ограничительные |
ролики; |
3 — базовая |
балка; |
|||
4 — опорно-направляющие элементы; |
5 — отклоняющий |
и |
центрирующий |
ролики; 6 — |
|||
заворачивающий |
ролик; 7 — габаритный ролик; 8 — кронштейн |
(сгребенка>) |
парой ограничительных роликов вдоль конвейера составляет 500—600 мм. По вертикали ограничительные ролики могут уста навливаться с перекрытием друг друга или с зазором до 300 мм. Зазор между гребнями ленты и базовой балкой конвейера не должен быть меньше 100—150 мм ввиду возможных колебаний ленты. Отмечено, что нижние ограничительные ролики могут служить для стабилизации прямолинейного хода ленты, для чего устанавливаются с возможностью регулирования в плане на 5—10° Верхние ограничительные ролики выполняют также функции габаритных или отклоняющих.
Устройство для переворачивания ленты с опорно-направляю щими элементами гирляндного типа создает оптимальный па раболический «опорный профиль» для ленты в зоне перевора чивания. Наибольшую нагрузку испытывают нижние ролики гирлянды. При неправильном расположении роликов гирлянды в ленте могут возникать изломы. С дефлекторным роликом гир лянды взаимодействует чаще только нижняя кромка ленты или
обе кромки одновременно. При монтаже устройства необхо димо предусматривать зазор (40—50 мм) между дефлекторным роликом и кромками ленты. Целесообразно опорно-направляю щие элементы устанавливать со смещением к средней части конвейера, при котором не происходит касания кромками ленты дефлекторного ролика. Для резинотканевых лент шири
ной 1200 мм и длины зоны переворачивания |
(11-7-13) В и вы |
соты подконвейерного пространства Яп = 800 |
мм переворачива |
ние ленты обеспечивается без реконструкции |
(подъема) става. |
Рекомендуется при высоте подконвейерного пространства 700— 900 мм использовать диагональную схему положения ленты. Прямолинейные ограничительные, габаритные и отклоняющие ролики должны иметь усиленную конструкцию с выносными подшипниковыми узлами. Длина конвейера, на котором целе сообразно применять переворачивания ленты, должна состав лять не менее (504-60) В.
Устройство для переворачивания ленты с внешним располо жением опорно-направляющих элементов роликового типа вне дрено на конвейере СДР-5 с высотой гюдконвейерного про странства 800 мм. Оно включает прямые ограничительные и опорно-направляющие ролики (см. рис. 4.18, б). Ролики послед него типа образуют роликовую обойму, состоящую из двух го ризонтальных и двух вертикальных роликов. Если лента в по перечном направлении не смещается, то вертикальные ролики могут быть исключены. Ограничительные ролики в данном слу чае также использовались и как центрирующие путем разворота их в плане. В рассмотренной схеме особое значение приобре тает обеспечение прямолинейности хода ленты. Если прямоли нейность хода ленты нарушается, возникает процесс «выбега» ленты. Таким образом, применение более простой конструкции устройства для переворачивания ленты с опорно-направляю щими элементами роликового типа связано, как правило, со снижением надежности переворачивания ленты или повышен ными требованиями к геометрии установки роликов.
На катучем реверсивном конвейере 7а Балаклавского ру доуправления им. А. М. Горького применен наиболее упро щенный вариант устройства для переворачивания ленты с од ним опорно-направляющим элементом роликового типа. Для этой цели использованы ограничительные барабаны диаметром 169 мм и опорно-направляющий элемент из одного стандарт ного ролика диаметром 127 мм, монтируемые на подвесных П-образных рамках с кронштейнами в виде гребенок, на кото рых устанавливаются барабаны и ролики. Высота подконвей ерного пространства до головки рельсов составила 690 мм. Наличие клепаных стыков и реверса ленты не нарушило устой чивости процесса переворачивания ленты. Однако высота рас положения гребней ленты из-за увеличения жесткости состыко, ванных участков возросла на 70 мм. Наличие специальных барабанов с выносными подшипниками в качестве ограничитель-
192
ных элементов оказалось оправданным ввиду действия боль ших нагрузок.
На Пикалевском ПО «Глинозем» опытную проверку про шла конструкция устройства для переворачивания резинотро совых лент. Установлено отличие в деформации и геометриче ском положении резинотросовой ленты, имеющей меньшую жесткость в поперечном и большую в продольном направле ниях, чем резинотканевая. Для резинотросовой ленты менее выражено образование гребней, однако имеет место больший провес в зоне переворачивания. С учетом этих особенностей ис пытана конструкция устройства роликового типа для перево рачивания резинотросовой ленты шириной 900 мм.
В комплект устройства входят ограничительные (располо женные по диагональной схеме), опорно-направляющие (два горизонтальных), заворачивающий и габаритный ролики (рис. 4.19, в). Ограничительные ролики диаметром 159 мм имеют усиленную конструкцию с выносными подшпниковыми узлами. Остальные ролики диаметром 127 мм (кроме завора чивающего) стандартные, но с удлиненными осями для упрощения их установки в кронштейнах с пазами, предназначен ными для регулирования положения роликов в плане. В каче стве заворачивающего ролика принят стандартный дефлекторный ролик, устанавливаемый вертикально рядом с первым по ходу движения ленты ограничительным роликом. За счет сило вого воздействия на кромку ленты заворачивающий ролик спо собствует сохранению устойчивого движения ленты без «вы бега». Верхний ограничительный ролик на концевом участке переворачивания создает прижимное усилие на ленту, рас прямляя ее, что также уменьшает вероятность «выбега» ленты. Габаритный ролик позволяет уменьшить высоту подконвейер ного пространства, которая составляла 680—700 мм. При этом длина зоны переворачивания ленты находилась в пределах
(15,5-7-16,6) В.
Эффективность внедрения переворачивания ленты на опыт ных участках была связана с исключением просыпи материала и загрязнения роликоопор на линейной части конвейера, умень шением износа обкладок, опирающихся на роликоопоры только своей чистой стороной, вероятности нарушения прямолиней ности хода ленты на холостой ветви, износа ленты и ролико опор, необходимого тягового усилия и затрат на электроэнер гию, повышением надежности работы оборудования и улучше нием условий труда.
Просыпи при переворачивании лент. Опыт внедрения пере ворачивания лент показывает, что проблема уборки просыпи в этом случае решается не полностью — существенно умень шается только общее количество просыпи под конвейером. По данным ИГД Минчермета СССР, при длине конвейера 100— 500 м и переворачивания ленты количество просыпи состав ляет только 7—0,5 % количества просыпи на конвейерах без
7 Заказ № 1462 |
193 |
переворачивания ленты. Однако все это количество просыпи приходится на головную (30%) и в большей мере (70%) на хвостовую зоны переворачивания ленты. Увеличение количе ства просыпи на участках переворачивания ленты объясняется се дополнительным деформированием и ломкой налипшего слоя материала. Таким образом, применение переворачивания ленты связано, как правило, с решением вопроса механизиро ванной уборки просыпи на участках переворачивания ленты.
На конвейерах Стойленского и Михайловского ГОКов (НИИКМА) эффективно используется кольцевой подборщик просыпи с ковшами в сочетании со скреперным подгребающим механизмом. Просыпь, упавшая в желоб, перемещается тяговым канатом со скребками к ковшам, совершающим кольцевое движение. Разгрузка ковшей происходит над рабочей ветвью ленты. Из других известных средств можно рекомендовать передвижные подборщики просыпей с гребковым рабочим ор ганом непрерывного или циклического действия.
На четырех конвейерах роторного комплекса «Стойлен- ский-П» (НИИКМА) (с лентой шириной 1800 мм и скоростью ее движения 5 м/с) с целью улучшения отвода просыпи внед рена новая схема расположения двух зон переворачивания ленты с опорно-направляющими элементами роликового типа. Хвостовой участок переворачивания ленты перенесен на рабо чую ветвь ленты и располагается между концевым отклоня ющим барабаном и загрузочным устройством. Просыпь, упав шая с хвостового участка переворачивания ленты, отводится в сторону наклонными щитками и не попадает в подконвейер ное пространство.
4.6. БОРЬБА С НАМЕРЗАНИЕМ ТРАНСПОРТИРУЕМОГО МАТЕРИАЛА НА КОНВЕЙЕРЕ
Снижение надежности |
работы конвейерного |
оборудования |
в условиях воздействия |
низких температур (до |
—50 °С), ха |
рактерных для угольных предприятий Северного Урала, Казахстана и Сибири, в значительной мере связано с намерза нием транспортируемого материала на отдельные узлы кон вейера (ленту, барабаны, роликоопоры). Уголь, обычно содер жащий влагу, при понижении температуры не только смерза ется сам, но и, попадая на ленту, барабаны, роликоопоры, примерзает к последним. Примерзание материала к узлам кон вейера ведет к его загрязнению при налипании. Кроме того, резко ухудшаются условия эксплуатации ленты, связанные г пробуксовкой в период пуска конвейера, нарушением пря молинейности хода, образованием просыпей, повышением за трат мощности. Уменьшить или исключить намерзание транс портируемого материала на узлы конвейера можно путем об работки материала и ленты сушкой и растворами, нагрева и очистки барабанов, очистки роликов.
Обработка транспортируемого материала сушкой. Пример зание груза к ленте объясняется в основном кристаллизацией влаги в контактирующих поверхностях и образованием струк турных связей между ними. Для уменьшения примерзания груза необходимо влагу, содержащуюся в нем, перевести в кристаллическое состояние или удалить до погрузки на ленту. Процесс кристаллизации влаги в материале называют холодной сушкой (рис. 4.20,а). Перемещаясь в загрузочном устройстве, материал находится во взвешенном состоянии, при котором хорошо поддается обдуву потоком холодного воздуха, поступающего от охладителя. Куски материала покрываются коркой толщиной 0,1—2 мм в зависимости от режима охлаж дения.
Большое распространение получила тепловая сушка транс портируемого материала (рис. 4.20,6), которая позволяет умньшить содержание влаги в материале и степень его при мерзания. Тепловую сушку материала рекомендуется произ водить в узлах перегрузки. Загрузочное устройство оснаща ется корпусом с калориферной установкой, включающей в себя нагреватель и привод с вентилятором. Сыпучий материал про ходит через камеру, обдуваемую потоком горячего воздуха. Охлажденный воздух поступает в отсасывающий патрубок. Высокая степень сушки достигается во вращающемся бара банном сушителе, выполняющем одновременно функцию за грузочного устройства (рис. 4.20,в). Образующаяся в бара бане пыль отсасывается вентилятором и подается в сепара тор, где отделяется от воздуха и поступает на ленту раньше, чем материал из барабана. Сухая подложка из пыли позволяет уменьшить налипание и примерзание материала к ленте.
Сушку |
материала, осуществляемую при высоких скоростях |
||
движения |
(200—300 |
м/с) высокотемпературного (400—550 °С) |
|
газового |
потока, |
принято называть |
термодинамической |
(рис. 4.20, |
г). В НИИКМА разработано |
и испытано термоди |
намическое перегрузочное устройство на базе передвижной реактивной установки типа ПРУ-01, предназначенное для сушки и подачи влажных вскрышных пород к загрузочному узлу роторного комплекса. Реактивный двигатель РД-ЗМ-500 с поворотной платформой монтируется на трайлере грузоподъ емностью 4 т и через трубопровод подачи соединяется со сме сительной камерой, в которую поступает порода из бункера роторного экскаватора. В смесительной камере порода крупно стью до 500 мм подхватывается и просушивается газовой горя чей струей на глубину 1—2 мм и одновременно по транспорт ному трубопроводу диаметром 1—1,2 м и длиной 30—50 м переносится к загрузочному устройству конвейерной линии. Производительность устройства составляет 5000 м3/ч при рас ходе топлива (на основе керосина ТС и дизельного топлива) 3—7 т/ч. Термодинамическая сушка материала может осуще ствляться и в процессе уборки просыпи на участках перево-
Средства борьбы с намерзанием транспортируемого материала на конвейере:
а — холодная |
сушка |
при |
загрузке; |
б —тепловая |
сушка |
в загрузочном устройстве: |
/ — |
|||||||
камера; |
2 — вентилятор |
с |
нагревателем; |
в — то |
же, в |
барабанном сушителе; |
/ — ба |
|||||||
рабанный |
сушитель; |
2 — генератор |
тепла; 3 — вентилятор; |
4 — сепаратор |
пыли; |
г — |
||||||||
термодинамические сушка и подача материала: |
/ — реактивный |
двигатель; |
2 — бун |
|||||||||||
кер; 3 — смесительная |
камера; 4 —трубопровод; |
5 — загрузочное |
устройство; |
д — ин |
||||||||||
дукционный |
нагрев: |
/ — магннтопровод; |
2 — обмотка |
переменного |
тока; |
е — очистка |
||||||||
|
роликоопоры: |
/ — рычаг; |
2 — башмак; |
3 —лента; |
4 — роликоопора |
|
|
рачивания ленты. При этом исключается намерзание просыпи на сборный желоб и ее прилипание, если просыпь возвраща ется перегружателем на конвейер.
Обработка ленты сушкой. Удаление примерзшего материала с ленты конвейеров, эксплуатируемых в условиях открытых работ, осуществляется преимущественно термодинамической сушкой. Последняя основана на подсушивании прилипшего к ленте слоя материала высокотемпературной газовой струей. При воздействии горячей струи на загрязненную поверхность ленты происходит перераспределение влажности. Поверхност
ный слой примерзшего |
материала оказываетсся высушенным |
на толщину 1,5—2 мм, |
а на границе лента — примерзший ма |
териал возникает водяная пленка, которая уменьшает силу сцепления материала с лентой и способствует очистке [321.
Высушенный слой материала теряет сплошность, покрывается сетью трещин, и образуется твердая сухая корка, отдельные части которой при изгибе ленты на барабанах или при встря хивании отслаиваются. При температуре газовой струи 800— 1000 °С, длине сушильного желоба 20—22 м и тепловом по токе 62,5- 104 ккал/(м2*ч) обеспечивается подсушка налипшего материала толщиной 8—10 мм и влажностью до 30 %. Лента, движущаяся в желобе со скоростью 5 м/с, подвергается на греву в течение 4—6 с и на выходе из желоба нагревается до допустимой по условиям нагрева температуры 45—50 °С. Пол ная очистка ленты от примерзшего материала достигается обычно за три цикла (три оборота ленты). Продолжительность непрерывной работы термодинамической установки составляет 10 мин при длине конвейера 500 м и скорости движения ленты 5 м/с. Повторное включение установки производится через 35—40 мин.
Термодинамическая установка для сушки ленты конструк ции Московского горного института и НИИКМА включает осе вой вентилятор с диффузором и корпусом, в котором парал лельно размещены две камеры сгорания топлива, свеча зажи гания и форсунки. В камеры сгорания поступают воздух от вентилятора производительностью 190—420 м3/мин и топливо по трубопроводу с расходом 0,1—0,4 т/ч. Образовавшаяся го рючая смесь воспламеняется с помощью свечи зажигания, на правляется в диффузор, а затем в нагревающий желоб, внутри которого проходит холостая ветвь ленты. Для снижения потерь тепла горелки с диффузором можно устанавливать на участке переворачивания ленты, выполняющей функцию теплового же лоба.
Для нагрева резинотросовых лент может быть успешно ис пользован индукционный нагрев (рис. 4.20,5). Холостая ветвь ленты размещается в проеме замкнутого магнитопровода с об моткой переменного тока. При подключении обмотки к источ нику переменного тока возникает электромагнитное поле и в тросах ленты, вызывая ее нагрев, индуктируется ток. Путем подбора сечения и числа витков обмотки, частоты напряжения изменяют интенсивность нагрева ленты. Так, для конвейерного комплекса «Стойленский-1» длиной 3400 м и с температурой
воздуха |
до —10 °С |
расчетное число индукторов составляет |
20 шт., |
а при длине |
конвейерной линии 1900 м и температуре |
воздуха до —30 °С — 54 шт.
Обработка ленты растворами, понижающими температуру смерзания. При температуре окружающей среды ниже —10 °С эффективны растворы, уменьшающие температуру смерзания контактирующих поверхностей. Растворы, подаваемые на ленту путем опрыскивания, позволяют существенно снизить прочность примерзания сыпучего материала к ленте. Промышленное применение получили растворы хлористых солей натрия, каль ция, магния или нигроина по ТУ 38-1015—70. В среднем рас
ход раствора составляет по массе 30—50 г на 1 м2 поверхности ленты. По данным Свердловского горного института, водный 25—45 %-ный раствор хлористой соли кальция уменьшает прочность примерзания горных пород к ленте в 8—10 раз без заметного ухудшения упруго-прочностных характеристик ленты. Обычно раствор хлористой соли подают на ленту перед ее за грузкой и затем периодически через 1—2 ч. Раствор соли раз жижает нижележащий на ленте слой материала, устраняя его примерзание. Удаление прилипшего после действия раствора материала производится скребковыми очистителями. Для этого рекомендуются растворы хлористых солей в сочетании с меха ническими очистителями. Известно также использование хло ристых солей в аналогичных целях, но подаваемых на ленту в кристаллическом состоянии. Такая посыпка способствует раз мягчению ленты и улучшению условий ее эксплуатации. Од нако при этом увеличивается расход соли.
Обработка ленты гидрофобными растворами. Гидрофобные растворы снижают адгезионную активность материалов благо даря низкой температуре замерзания и большой вязкости. К ним относятся кубовые остатки оксосинтеза спиртов (КОС), газойль, гликоль и продукты перегонки нефти. Устройство для подачи жидкости КОС на ленту включает в себя насос, ем кость, трубопроводы и форсунки [33]. Установлены параметры режима нанесения жидкости КОС. При транспортировании угля и температуре окружающей среды —1 5 ...—20°С количество одноразового в течение суток нанесения жидкости составляет 30—50 г на 1 м2 ленты. Толщина жидкости покрытия 30— 50 мкм. Жидкость КОС как профилактическое покрытие реко мендована для применения в сочетании с механическими очис тителями на конвейерах, транспортирующих уголь и вскрыш
ные |
породы |
(глину, суглинок, |
песок, известковые породы) |
с влажностью |
15—35 % и при температуре окружающей среды |
||
—1 0 ...—40 °С. |
в качестве гидрофобных рас |
||
За |
рубежом (в ГДР, США) |
творов, наносимых на ленту конвейера при отрицательных тем пературах, получили распространение водно-кремниевые эмульсии.
Нагрев и очистка барабанов. На мощных конвейерах часть барабанов (обычно отклоняющих) обхватывается загрязнен ной стороной ленты. При отрицательных температурах окру жающей среды налипшие на барабан частицы материала при мерзают, образуя твердую корку. Это явление ухудшает усло вия эксплуатации конвейера из-за схода и дополнительного износа ленты. Для исключения намерзания материала на ба рабан используют электрические инфракрасные нагреватели мощностью 10—15 кВт с термореле, обеспечивающие нагрей обечайки барабана до температуры 40—50°С. После прогрев^ барабаны очищают скребковыми или дисковыми приводными очистителями. Хорошие результаты получены при использова
нии барабанов с самоочищающимися эластичными футеровками. Эластичная футеровка крепится с зазором к обечайке ба рабана, на поверхность которой посыпается тальк или наносится смазка. Удаление подсушенного на поверхности барабана ма териала происходит под действием упругой деформации футе ровки, причем тальк исключает адгезионное прилипание футе ровки к корпусу обечайки. Известно также применение бара банов с решетчатой или пластинчатой конструкцией обечайки. Продольные элементы обечайки, имеющие различную конфигу рацию, проскальзывают относительно ленты и счищают с себя и с ленты прилипший материал, который попадает внутрь обе чайки и затем удаляется.
Очистка роликов. Обогрев роликов не применяется. По этому при эксплуатации конвейеров в условиях воздействия низких температур на холостой ветви ленты рекомендуется ус танавливать самоочищающиеся роликоопоры (дисковые гумми рованные и прутковые со спиралевидной опорной поверхно стью). Для очистки обычных роликоопор может быть рекомен довано специальное приспособление (рис. 4.20,в). Оно состоит из опорного башмака и рычага с шарнирной опорой под ленту. Башмак устанавливается на раму конвейера, а рычаг заво дится под ленту. Путем поворота рычага поднимают ленту под углом 40°. Затем с помощью дугообразного скребка произво дится зачистка обечайки роликоопоры.
ПОВЫШЕНИЕ ДОЛГОВЕЧНОСТИ И УМЕНЬШЕНИЕ ИЗНОСА ОСНОВНЫХ УЗЛОВ
ОБОРУДОВАНИЯ
5.1. ДОЛГОВЕЧНОСТЬ И НАДЕЖНОСТЬ РОЛИКООПОР
Роликоопоры и составляющие их ролики являются самым массовым элементом ленточного конвейера. В СССР ежегодно выпускается 9,5—10 млн. роликов, в эксплуатации находится свыше 40 млн. шт. Ролики весьма разнообразны по конструк тивному и технологическому исполнениям.
Работа роликов на мощных конвейерах оказывает сущест венное влияние на износ ленты — самого дорогостоящего эле мента ленточного конвейера. На ролики приходится до 40 % всех затрат на обслуживание и ремонт конвейера или до 80— 90 % всех затрат на обслуживание и ремонт механического оборудования. Ролики относятся к числу невосстанавливаемых элементов. Их отказ не приводит к останову конвейера, но нарушает работоспособность последнего.
Условия эксплуатации роликов в горнорудной промышлен ности изменяются в широких пределах из-за различных зна чений производительности (нагрузок на ролики), свойств тран спортируемых материалов (абразивности, плотности, крупно сти, влажности, температуры, склонности к пылению), лент (массы, способа стыковки, состояния поверхности), окружаю
щей |
среды (влажности, |
температуры, запыленности). В усло |
|||
виях Урала, |
Кузбасса, |
Сибири и |
Дальнего |
Востока (обычно |
|
на |
угольных |
разрезах) |
конвейеры |
работают |
в зимнее время |
при весьма низких температурах. К тяжелым условиям эксплу
атации роликов следует отнести |
и применение конвейеров |
для доставки горючих материалов |
(кокса, агломерата, брике |
тов). В подземных выработках угольных шахт и рудников на работе конвейеров особенно неблагоприятно сказываются ог раничение габаритов ставов (из-за чего жесткость элементов крепления недостаточна), пучение почвы и кровли, накопление просыпи на трассе. Ролики часто работают в запыленной и влажной (до 85—90 %) среде, обладающей повышенной кис лотностью. Загрязненность конвейерных лент приводит к заштыбовке роликов, повышенному сопротивлению вращения. В условиях взрывоопасной среды угольных шахт ролики дол жны быть огнестойкими и с малой электростатичностью.
Срок службы роликов на рабочей ветви ленты (по данным Днепропетровского горного института) на конвейерах Кривбасса,
транспортирующих руду, составляет 1,7—9,5 года при пропуск ной способности 14,6—132 млн. т руды и числе оборотов 44,3— 431,8 млн. Соответственно для роликов на нижней ветви — 1,4—3,8 года и 44,5—184,9 млн. оборотов. Усредненный срок службы роликов верхней ветви составляет 3,8 года, а ниж ней— 2,5 года. По данным ПромтрансНИИпроекта, сроки службы роликов на конвейерах коксохимических и агломераци
онных цехов |
Магнитогорского металлургического |
комбината |
в основном не |
превышает 12 мес, а на некоторых |
конвейерах |
составляют 2—4 мес. |
|
Некоторые показатели надежности работы роликоопор верхней и нижней ветвей ленты соизмеримы с показателями наименее надежного звена конвейера — ленты.
В табл. 5.1 приведены показатели надежности основных узлов 26 конвейеров ПО «Кривбассруда», полученные Ростов ским инженерно-строительным институтом. Более 80 % времени всех простоев в рабочие смены приходится на ликвидацию от казов первых пяти основных узлов. Наименее надежны в ра боте лента, электрооборудование, перегрузочные устройства, ролики верхней и нижней ветвей ленты. Наработка 26 конвейе ров на отказ составляет в среднем 576 ч при коэффициентах готовности и технического использования соответственно 0,992 и 0,943. Суммируя значения показателей надежности роликов
верхней и нижней ветвей ленты, можно |
получить: на 106 от |
||||
казов |
лент приходится |
98 отказов |
роликов; соответственно |
||
число |
замен при П П Р— 120 и 933, доля |
времени |
на ликвида |
||
цию отказов и ППР в |
общем времени |
простоя |
конвейера — |
||
22,1 и |
27 %. Таким образом, частоты |
отказов ленты и роликов |
Узел конвейера
Лента
Электрооборудование Ролики верхней ветви Перегрузочное устрой ство Ролики нижней ветви
Редуктор с муфтами Барабаны Натяжное устройство Храповой механизм Став Тормоз
|
|
|
|
|
ТАБЛИЦА 5.1 |
|
Число отказов |
Наработка |
на отказ» ч |
Среднее время ликвидации одного отказа, ч |
Число замен при ППР |
Среднее время за одну замену, ч |
Доля времени на ликвидация отказов в общем времени простоя конвейеров, “0 |
106 |
2 |
741 |
8 ,4 |
120 |
8 ,1 |
2 2 ,1 |
44 |
6 |
6 2 0 |
1,76 |
10 |
2,1 |
18 |
34 |
8 |
5 5 0 |
1,3 |
481 |
2 ,5 |
14,9 |
76 |
3 |
82 2 |
4 ,1 2 |
2 0 5 |
3 ,9 4 |
13,3 |
64 |
4 |
5 5 0 |
2 ,3 |
4 52 |
1,95 |
12,2 |
53 |
5 |
5 0 0 |
4 ,6 8 |
75 |
3 ,8 |
6 ,3 |
4 8 |
6 |
0 7 0 |
4 ,2 |
68 |
4 ,5 |
6 |
12 |
22 |
2 8 0 |
4 ,9 |
22 |
5 ,8 |
2 ,3 |
33 |
8 |
820 |
3 |
23 |
2 ,5 2 |
1,9 |
8 |
36 |
4 0 0 |
10 |
16 |
4 ,4 4 |
1,8 |
25 |
11 |
6 20 |
3,1 |
10 |
2,1 |
1,2 |
примерно одинаковы, а время на ликвидацию отказа и ППР роликов больше, чем ленты (примерно на 20 %).
Под отказом ролика в общем случае понимается выход из строя оси, подшипников, уплотнений и корпуса, при котором номинальный момент ролика увеличивается в два и более раз. Интенсивность отказа для ролика
Яр = ЯК+ Я0 + Яп.Л+ Яп. п + Яу.л + Яу. п,
где Як, Я0, Яп.л, Яп.п, Яу.л, Яу.п — интенсивность отказа соответ ственно корпуса, оси, левого и правого подшипников, левого и правого уплотнений.
Интенсивность отказа всех роликов конвейера
Я = 2 ЯрЯр. в И- 2 — Яр>н,
4
где Яр.в, Яр.н— интенсивность отказа соответственно роликов верхней и нижней ветвей ленты; пр— число роликов верхней ветви.
Вероятность безотказной работы всех роликов конвейера
-S |
= е~ х/к, |
P ( t ) = e 0 |
где е — основание натурального логарифма; tK— время работы конвейера.
Нагрузки на ролики роликоопоры распределяются неравно мерно. На средний ролик приходится 40—45 % общей на грузки, в том числе на его подшипниковый узел до 23 %. Эта нагрузка с увеличением заполнения ленты растет примерно пропорционально общей нагрузке. Нагрузка на нижний под шипниковый узел бокового ролика при малой загрузке кон вейера составляет 12 % общей нагрузки на роликоопору и резко возрастает с увеличением заполнения ленты (до 25 %). Верхние подшипниковые узлы загружены незначительно (4— 5 %). Отмечено повышенное заполнение смазкой нижних под шипниковых узлов и вытекание из них смазки. При этом верх ние подшипниковые узлы даже при малой загрузке выходят из строя быстрее.
На срок службы подшипниковых узлов существенно влияют циклические нагрузки, вызванные изгибом оси ролика при на гружении и радиальным биением при разностенности корпуса. При значении неуравновешенной центробежной силы, близкой к статической нагрузке, появляются стук в подшипниках и из нос шеек осей и подшипников. Динамические нагрузки от ра диального биения роликов оказывают значительное влияние на работоспособность поддерживающих их конструкций — эста кад, ферм, стрел отвалообразователей и транспортно-отвальных мостов. По ГОСТу на ленточные конвейеры максимально до-
202
пустимое радиальное биение роликов для скоростей движения ленты до 3,15 м/с составляет 0,015 DH (DH— наружный диа метр трубы ролика). Для скоростей свыше 3,15 м/с норматив на допустимое радиальное биение отсутствует, тогда как совре менные высокопроизводительные конвейеры имеют скорости движения ленты до 6—7 м/с. Институтом геотехнической меха ники АН УССР измерялось радиальное биение 968 роликов верхней и 178 роликов нижней ветвей ленты. Установлено, что радиальное биение корпуса роликов верхней груженой ветви находится в диапазоне 0,5—2,5 мм при DH 159 мм, т. е. биение находится в допустимых пределах, а у большей части роликов нижней ветви биение корпуса больше, чем у верхней.
Для уточненных расчетов подшипников роликов целесооб разно определять дополнительные нагрузки, связанные с разностенностью и, соответственно, с биением корпуса. На рис. 5.1 показаны зависимости дополнительных нагрузок на подшипники, полученные расчетным путем для роликов про
изводства Сызранского |
турбостроительного завода длиной |
740 мм, диаметром 194 |
мм и толщиной стенки корпуса 7 мм |
[34]. Из рис. 5.1 видно, что нагрузки на подшипники от разностенности корпуса ролика достигают значительной величины и сравнимы с весами ролика и транспортируемого груза. Пол ная радиальная нагрузка Р на подшипники ролика при экс плуатации
P = Q + q cos (Dyfp,
где Q — радиальная нагрузка на подшипники от весов ро лика, ленты, транспортируемого груза, неправильной установки но высоте; q — дополнительная нагрузка; соу — угловая ско рость вращения ролика; tp— время действия нагрузки на ро лик.
Полная радиальная нагрузка на подшипники имеет цикли ческий характер. При работе конвейера вхолостую дополни тельная нагрузка на подшипники может быть больше радиаль ной, и полная радиальная нагрузка будет иметь знакопере менный характер. Кроме радиальной нагрузки от груза и ленты на подшипники могут действовать силы от неуравно вешенности корпуса, связанной со смещением оси вращения ролика от его геометрической оси. Наименования изнашивае мых деталей и причины износа роликов приведены ниже.
Корпуса (обечайка) |
Биение и перекосы из-за неточности изготовления |
|
и монтажа |
|
Абразивное взаимодействие с частицами и лентой, |
|
особенно при стопорении |
|
Ударное взаимодействие системы груз — лента — |
Шейки осей |
ролик |
Биение и перекосы из-за неточного изготовления и |
|
|
монтажа |
|
Ударное взаимодействие системы груз — лента — |
|
ролик |
|
П р о д о л ж е н и е |
Уплотнения |
Неточность изготовления и монтажа |
|
Засорение частицами |
Подшипник |
Влияние влаги и температуры |
Биение и перекосы из-за неточного изготовления и |
|
|
монтажа |
|
Засорение частицами |
|
Влияние влаги и температуры |
|
Нехватка или отсутствие смазки |
Испытания. Созданию более долговечных и надежных в ра боте роликов в значительной мере способствуют испытания. Последние проводятся на моделях, стендах, опытных установ ках и непосредственно в производственных условиях. Наиме нее трудоемки первые два вида испытаний, так как позволяют оперативно моделировать различные режимы нагружения и подбирать оптимальные параметры роликов. Чаще при оценке роликов пользуются ходовыми характеристиками роликов, к которым относят момент сопротивления и коэффициент со противления вращению. Измерение момента сопротивления вращению роликов на заводах обычно осуществляется посред ством зажима в виде ремня (рис. 5.2,а), к которому прикреп ляются контргруз и измерительная линейка с подвижным гру зом. В исходном положении с помощью контргруза и груза линейка занимает горизонтальное положение, соответствующее равновесию ролика перед испытанием. Затем медленно пере мещают груз вдоль линейки до начала поворота корпуса ро лика и определяют момент сопротивления вращению
Мс= Gr (Rr—Лги)>
где Gr — вес груза; RTi Rr0— расстояние груза от начальной точки соответственно при повороте и равновесии ролика.
Действующие на ролики динамические нагрузки определя ются, например, посредством пьезоэлектрического измерителя ускорений с записью на шлейфовый осциллограф. Эффективно также использование при исследовании динамических нагру зок на подшипники тензометрических датчиков, наклеиваемых рядом с подшипниками с обеих сторон шлифованной оси (рис. 5.2,6). Для увеличения чувствительности измеритель ной системы в плечи полумостов включают датчики, располо женные в зонах сжатия и растяжения и наклеиваемые в вер тикальной и горизонтальной плоскостях. Для имитации фрик ционных нагрузок на корпус роликов (рис. 5.2, б) применяется стенд в виде короткого конвейера с нагрузочными роликами, к осям которых подвешиваются грузы. Величину проскальзы вания роликов можно регулировать путем поворота их в го ризонтальной плоскости. Величина и характер износа ролика по длине определяются с помощью микрометров путем постро ения профилограмм толщины корпуса ролика.
ВНИИПТмашем проведены лабораторные исследования со противления вращению роликов, серийно выпускаемых Сыз-
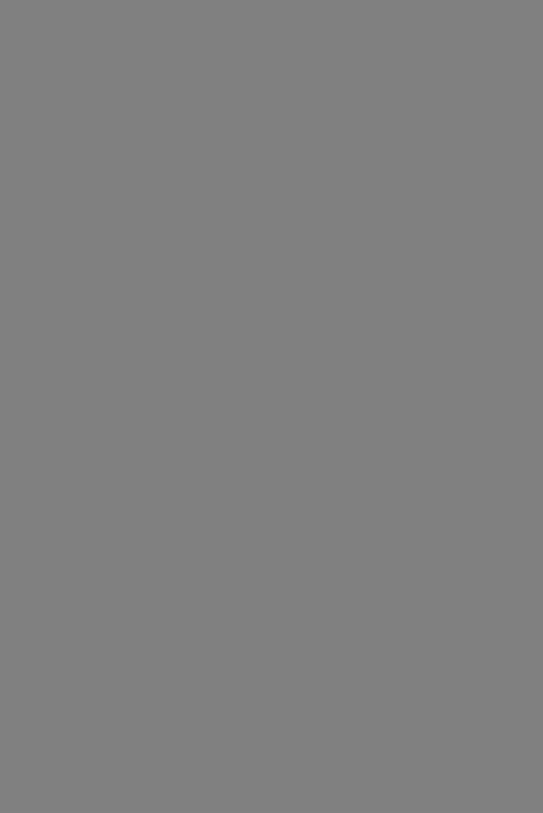
ранским турбостроительным заводом (СТЗ), для лент шири ной 1600 (рис. 5.3, а) и 2000 мм (рис. 5.3,6) и роликов фирмы «Монтан» (ГДР) для ленты шириной 1600 мм. Ролики СТЗ для ленты шириной 1600 мм имеют литой вкладыш, завальцованный в корпус. Уплотнение образовано двумя металличе скими. втулками сложной конфигурации. Шариковый подшип ник с двух сторон защищен уплотнительными упругими коль цами из бронзы. До обкатки новых роликов коэффициент
сопротивления |
вращению wc достигал 0,130. Обкатка роликов |
в течение Т0б= |
5 ч под нагрузкой привела к снижению wc до |
0,055—0,016. Через 600 ч испытаний роликов в пылевой камере wc достигает 0,010 с разбросом значений в серии до 47 % (рис. 5.4,а). В лабиринты уплотнения и под упругое уплотни тельное кольцо попадает значительное количество пыли. Ус тановлено, что удаление упругих колец снижает шс до двух раз (с 0,028±0,013 до 0,014±0,007). При этом надежность ра боты подшипниковых узлов не снижается.
Ролики СТЗ для ленты шириной 2000 мм имеют конические подшипники. Уплотнение образовано на цилиндрических по верхностях втулок. Лабиринт уплотнения усилен упругим за щитным кольцом. Входная щель перекрыта штампованной шайбой. До обкатки роликов зачение wc было не менее 0,100, после 5 ч обкатки не превышало 0,015, а за 500 ч работы ролика значение wc стало стабильным с незначительным раз бросом относительно 0,010 (рис. 5.4,6). Таким образом, этот тип роликов обладает более высокими ходовыми качествами, чем предыдущий.
а
0 О |
100 200 300 m 500 Т0у|Ч |
изс
0,01
О |
100 200 300 Ш 500 ToSlч О |
100 200 300 400 5ООТ0$,ч |
РИС. 5.4.
Зависимости коэффициента сопротивления вращению роликов от времени обкатки Тоо:
а — ролики конструкции СТЗ для лент шириной 1600 мм: / —для роликов с упругим кольцом в уплотнении; 2 — то же, без упругого кольца в уплотнении; б — то же, шириной 2000 мм; в — ролики конструкции «Монтан* (ГДР) для лент шириной 1600 мм
Ролики фирмы «Монтан» (ГДР) имеют тонкостенный штам пованный вкладыш, сваренный с корпусом плазменной сваркой; шарикоподшипник защищен многозаходным лабиринтом из трех пластмассовых шайб. Во время обкатки wc изменяется незначительно и составляет в среднем 0,011 при максималь ном 0,013 (рис. 5.4,в). У роликов практически отсутствует пе риод приработки. Уплотнение полностью предохраняет под шипник от попадания пыли. Ролики имеют массу в 14,7 кг. Ролики СТЗ такого же типоразмера имеют массу 25,5 кг.
В соответствии с полученными данными приняты к исполь зованию при проектировании конвейеров значения сопротив ления движения ленты по роликоопорам, в которых кроме со ставляющей сопротивления вращению роликов учитываются (согласно РТМ 24.093.04—80) составляющие сопротивления ог деформации ленты и груза, вдавливания роликов в ленту, а также влияние длины и условий эксплуатации конвейера. Значения коэффициента сопротивления движению ленты по роликоопорам wc приведены ниже.
|
|
Коэффициент |
||
|
|
сопротивления wQ |
||
Длина конвейера, |
м |
До 100 |
Более |
|
Условия эксплуатации: |
|
100 |
||
0,020 |
0,018 |
|||
легкие |
|
|||
средние |
|
0,025 |
0,022 |
|
тяжелые: |
|
0,035 |
0,032 |
|
летом |
|
|||
зимой |
|
0,045 |
0,042 |
|
очень тяжелые: |
|
0,040 |
0,036 |
|
летом |
|
|||
зимой |
|
0,055 |
0,050 |
|
Для исследования динамических нагрузок на ролики от |
||||
дебаланса и |
биений ГПКИ |
Союзпроммеханизация |
разра |
ботан специальный ролик с вкладышем, имеющим эксцен тричную расточку и элементы фиксации относительно корпуса. Поворачивая вкладыш, можно изменять величину эксцентриси тета оси, а следовательно, биение ролика и динамические на грузки. Последние измеряются тензометрическими датчиками, устанавливаемыми на оси.
ВНИИПТмашем, УкрНИИпроектом, НИГРИ созданы экс периментальные установки для исследования действия ударных нагрузок на ролики, имитирующие работу конвейера при до ставке крупнокусковых грузов. Ролики с помощью системы грузов и рычагов прижимаются к футерованному барабану со сферическими выступами (рис. 5.5,а). При вращении бара бана ролик находится под постоянной статической нагрузкой и одновременно подвергается ударам от выступов. Статическая нагрузка регулируется сменными грузами, а вывод ролика из контакта с барабаном осуществляется посредством педалей. Недостатком данного стенда является отсутствие системы
Стенды для исследования динамических нагрузок на роликоопоры при до ставке крупнокусковых грузов:
а — с |
барабаном со |
сферическими |
.выступами: |
/ — барабан; |
2 — выступ; 8 — ролик, |
||||
б — с |
колесом, |
оснащенным грузами: / — лента; |
2 — груз; |
3 — колесо; |
4 — канат; |
5 — |
|||
натяжное устройство; |
6 — роликоопора; в — с |
валами, |
оснащенными |
билами: |
/ — |
||||
|
лента; |
2 — била; 3 — канат; |
4 — натяжное устройство; |
5 — роликоопора |
|
груз — лента — роликоопора. В конструкции стенда с ленточным контуром имеется колесо с грузами, имитирующими крупные куски груза (рис. 5.5,6). Грузы подвешиваются на гибких сваях и входят во взаимодействие с лентой. При набегании груза на роликоопору в системе груз — лента — роликоопора возникает удар. Таким образом, моделируется прохождение крупных кусков груза через роликоопору, близкое к реальному.
Испытание подвесных роликоопор в производственных ус ловиях требует длительного периода — не менее 2—3 лет. Для ускоренного испытания одновременно двух подвесных ролико опор, устанавливаемых в месте загрузки, УкрНИИпроектом используется стенд с лентой шириной 1200 мм и скоростью движения до 4,9 м/с. Ударный механизм включает в себя два
кинематически связанных между собой вала со сменными би лами (рис. 5.5, в) с регулируемыми по длине держателями. Частота ударов регулируется путем изменения частоты враще ния валов, а сила ударов — изменением длины держателей и массы бил. Регулировка натяжения канатов става конвейера осуществляется винтовым механизмом, а контроль натяже ния— тензометрическими датчиками. Билы поочередно уда ряют по среднему и боковым роликам подвесных роликоопор. При этом предполагается, что общая деформация упругой си стемы незначительна по сравнению с местной, т. е. за время удара упругая система не воздействует на массу роликоопоры.
Контактная сила удара
F к — Ai&p -f- А 2&р»
где А х и А2— коэффициенты, |
определяемые экспериментально; |
£Р — максимальное сближение |
била и роликоопоры в момент |
удара.
Частота колебаний роликоопоры во время контакта ее с би лом
где Zр — жесткость роликоопоры; те, щ — соответственно массы била и роликоопоры.
Максимальное перемещение роликоопоры по направлению удара
где ибр— относительная скорость соударения била и ролико опоры.
Комплекс экспериментальных исследований, связанных с изучением работы мощных конвейеров в условиях доставки крупнокусковых грузов, позволяет проводить опытная уста новка конструкции ВНИИПТмаша. Она включает основной конвейер (длиной 36,5 м, с приводом мощностью 55 кВт, лен той шириной 1600 мм и скоростью движения 1—2,5 м/с) и на грузочный цепной конвейер с подвешенными к цепи грузами, движущийся Над лентой синхронно с ней или со смещением. Основной конвейер оборудуется жесткой и гибкой (канатной) частями става, амортизирующими частями в виде ленточного контура и секции амортизирующих роликоопор, жесткими и подвесными гирляндными роликоопорами. Таким образом, ус тановка обеспечивает испытание разных узлов конвейера, спо собствующих снижению динамических нагрузок на элементы конструкции»
Уменьшение износа роликоопор. Мероприятия по уменьше нию износа роликоопор можно свести к четырем основным группам: выбор оптимальных эксплуатационных параметров узлов конвейера; улучшение технологии изготовления роликов; создание более совершенных конструкций, особенно в части вы полнения подшипниковых узлов, уплотнений, систем и вида смазки; улучшение техники и технологии монтажа, обслужи вания и ремонта роликов.
По проекту ГПКИ Союзпроммеханизация и ВНИИПТмаша предусматривается шесть типов роликов по подшипниковым узлам, данные по которым приведены ниже.
Тип ролика |
I |
II |
III |
IV |
V |
VI |
Диаметр, мм: |
89 |
108 |
133 |
159 |
194 |
194 |
корпуса |
||||||
оси |
12 |
17 |
20 |
25 |
30 |
40 |
Номер подшипника |
202 |
203 |
304 |
7305 |
7306 |
7308 |
При этом ролики делятся на группы: для лент шириной 400— 650 мм, 800—1200 мм и 1400—1600 мм. Для каждой группы предусмотрены два — три типа роликов (легкий, нормальный и тяжелый). Таким образом, при шести типах для лент различ ной ширины имеется 40 типоразмеров роликов, предназначен ных для различных условий работы. Новые ролики имеют за крытые шарикоподшипники с долговременной закладной смаз кой, бесконтактное лабиринтное уплотнение из штампованных деталей.
Выбор типа роликоопоры для конвейеров общего назначе ния осуществляется [35] в зависимости от группы абразивности транспортируемого груза в соответствии с данными табл. 5.2.
Снижению динамических нагрузок на подшипники мощ ных ленточных конвейеров в значительной мере способствует выбор оптимального диаметра роликов. Последний определя ется в зависимости от ширины ленты, плотности транспортиру емого груза и скорости движения ленты в соответствии с дан ными, приведенными в табл. 5.3.
При проектировании высокопроизводительных ленточных конвейеров большой протяженности характерно стремление к установлению оптимального шага роликоопор по всей трассе транспортирования. Это позволяет улучшить технико-экономи ческие показатели благодаря уменьшению капитальных и экс плуатационных расходов на роликоопоры. Рекомендуется, в частности, за основу принимать расстояние между роликоопорами в зависимости от ширины ленты, массы и размеров отдельных кусков груза только для средней части конвейера. Расстояния между верхними роликоопорами рекомендуется вы брать в соответствии с данными табл. 5.4.
Расстояния между роликоопорами на других участках кон вейера принимаются обычно на 15—20% большими в зонах наибольшего натяжения. При доставке кускового груза в зоне
Группа
абразивности
груза
Роликоопора верхняя
обозначение по ГОСТ 22645—77
Роликоопора нижняя
обозначение по ГОСТ 22645—77
Мало- И |
Прямая |
П |
Прямая |
|
Н; НЛ |
среднеабра- |
|
|
|
|
|
зивные |
|
|
|
|
|
(А, В, С) |
Желобчатая |
ж |
Желобчатая |
НЖ; НЖЛ |
|
|
|||||
|
Желобчатая |
ЖЦ |
Прямая |
центриру |
НЦ; НЦЛ |
|
центрирующая |
ЖА |
ющая |
|
|
|
Желобчатая |
|
|
|
|
|
амортизирующая |
|
Прямая дисковая |
НД; НДЛ |
|
|
|
|
|||
Сильно |
Прямая |
ПФ |
Желобчатая дисковая |
НЖД; НЖДЛ |
|
Прямая |
футерован |
НФ; НФЛ; |
|||
абразивные |
футерованная |
|
ная; дисковая |
НДЛ |
|
(Д) |
Желобчатая |
ЖФ |
Желобчатая футеро |
НЖФ; НЖФЛ; |
|
|
|||||
|
футерованная |
ЖФЦ |
ванная; дисковая |
н ж д л |
|
|
Желобчатая, |
Прямая |
футерован |
НЦФ; НЦФЛ |
|
|
футерованная, |
|
ная, центрирующая |
|
центрирующая
установки загрузочного устройства устанавливаются пять— шесть амортизирующих роликоопор. Приведенные в табл. 5.4 значения расстояний между роликоопорами уменьшаются на 10 % при доставке груза с кусками 350—500 мм и на 20 % при доставке груза с кусками более 500 мм. Зависимость зна чений расстояния между роликоопорами от ширины ленты и плотности груза (см. табл. 5.4) отражает оптимальную связь расстояния между роликоопорами с сопротивлением движению
ленты |
(мощностью привода), |
статической и |
динамическими |
||
|
|
|
|
|
ТАБЛИЦА 5.3 |
Диаметр |
Диапазон ширины |
Наибольшая |
Наибольшая |
||
плотность транспор |
|||||
ролика, мм |
ленты, мм |
тируемого груза, |
скорость движения |
||
|
|
|
|
т м;‘ |
ленты, м/с |
83 И 89 |
800 |
1,6 |
1,6 |
||
102 |
и |
108 |
800—1200 |
1,6 |
2,5 |
127 |
и |
133 |
800—1200 |
2,0 |
2,5 |
152 |
и |
159 |
800—1200 |
3,5 |
4,0 |
194; 219 |
и 245 |
1600—2000 |
3,5 |
3,2 |
|
800—1400 |
3,5 |
4,0 |
|||
|
|
|
1600—2000 |
4,0 |
6,3 |
Ширина |
|
|
Плотность груза. т,мя |
|
|
||
|
От 0.51 |
От 0,81 |
От 1,21 |
От 1.61 |
От 2.01 |
Более |
|
ленты, мм |
До 0.5 |
||||||
|
до 0,8 |
до 1.2 |
до 1,6 |
до 2,0 |
до 2.5 |
2.5 |
|
800 |
1,5 |
1,4 |
1,3 |
1,3 |
1,3 |
1,2 |
1,1 |
1000 |
1,3 |
1,3 |
1,2 |
1,2 |
1,2 |
1,1 |
М |
1200 |
1,2 |
1.3 |
1,2 |
1,2 |
1,2 |
1,1 |
1,1 |
1400 |
|
|
|
|
|
|
|
1600 |
1,3 |
1.3 |
1.2 |
1,2 |
1,2 |
1,1 |
1,1 |
2000 |
1,3 |
1.3 |
1,2 |
1,2 |
1,0 |
1,0 |
1,0 |
нагрузками на подшипники роликов, натяжением и попереч ным колебанием ленты. Для высокопроизводительных конвей еров с повышенными скоростями движения ленты необходимо также учитывать возможность скольжения груза на ленте, от рыва его от ленты, лотковость ленты и технико-экономические показатели. Рекомендации Казахского политехнического ин ститута по выбору оптимального расстояния между роликоопорами для подземных конвейеров с учетом устойчивости груза и технико-экономических показателей даны в табл. 5.5.
На отечественных заводах технология изготовления роли ков постоянно совершенствуется. Николаевский машинострои тельный завод подъемно-транспортного оборудования, Арте мовский и Краснолучский машиностроительные заводы изго товляют ролики только с литыми чугунными вкладышами. Гороховецкий завод подъемно-транспортного оборудования использует вкладыши из волокнита и древесно-смолистого плас тика. Полевский машиностроительный завод получает эти де тали методом литья из алюминиевого сплава, а также из во локнита. Донецкий машиностроительный завод им. Ленин ского комсомола Украины производит ролики со стальными штампованными вкладышами. Александровский машинострои тельный завод наряду с чугунными литыми применяет сталь-
ТАБЛИЦА 5.5
Конвейер и угол его наклона, градус
Параметры |
|
1Л80 |
1Л100 |
2ЛУ100 |
1ЛУ120 |
||||
|
|
0 |
6 |
0 |
6 |
6 |
18 |
0 |
18 |
Длина конвейера, м |
480 |
190 |
1500 |
500 |
800 |
380 |
1750 |
310 |
|
Скорость ленты, |
м/с |
2 |
2 |
1,6 |
1,6 |
2 |
2 |
2,5 |
2,5 |
Шаг роликоопор |
по пас |
1,4 |
1,4 |
1,25 |
1,25 |
1,25 |
1,25 |
1,2 |
1,2 |
порту, м |
|
1,9 - |
1,6— |
2,1 |
2,1— |
2 |
1,1— |
1,8 |
1,3— |
Расстояние между роли- |
|||||||||
коопорами, м |
|
2,2 |
2,2 |
|
2,2 |
|
2 |
|
1,8 |
ные штампованные вкладыши. Белохолуницкий машинострои тельный завод и Узловский машиностроительный завод для роликов тяжелых конвейеров используют чугунные вкладыши, а все остальные ролики оснащают вкладышами из древесно смолистых пластиков. Наиболее надежны и долговечны ролики со стальными и чугунными вкладышами. Вкладыши из неме таллических материалов менее стойки к воздействию влаги, масел, абразивной среды, ударных нагрузок.
На Сызраиском турбостроительном и Белохолуницком ма шиностроительном заводах для предотвращения попадания в полость подшипников продуктов коррозии и окалины в роли ках тяжелого типа со стороны внутренней стенки трубы уста навливают защитную трубу между наружными кольцами под шипников, а вместо шариковых радиальных применяют роли ковые конические подшипники. Смазка роликов легкого и нормального типов — долгодействующая закладная, у роликов тяжелого типа смазка осуществляется шприцеванием через пресс-масленки или как централизованная от насосной мас ляной станции. Ролики тяжелого типа входят в состав оборудо вания [36], изготовляемого для десяти конвейерных трактов карьеров Минчермета СССР. В таких конвейерах приняты же сткий став и трехроликовая желобчатая роликоопора с роли ками повышенной точности со сквозной осью на конических подшипниках. Средний ролик смещен в плане относительно боковых, установленных с наклоном 30°, что обеспечивает бо лее равномерное распределение нагрузки между роликами, уменьшает высоту става, улучшает условия обслуживания и снижает сопротивление движению ленты, она меньше повреж дается острогранным грузом.
Восьмилетний опыт эксплуатации роликов на Ингулецком ГОКе показал, что принятая конструкция роликоопор имеет высокую работоспособность. Наработка роликов до выхода из строя — до 100—120 млн. т крупнокусковой руды. При этом долговечность средних и крайних роликов примерно одина кова, так как при полном заполнении ленты рудой только 45— 50 % всей нагрузки приходится на средний ролик, а нагрузка на смежные подшипниковые узлы средних и крайних роликов примерно одинакова. Холостая ветвь также принята желобча той. Роликоопора — двухроликовая с наклонным роликом до 10°. Ролики со сквозной осью на шарикоподшипниках футеро ваны резиновыми кольцами. Ролики рабочей и холостой вет вей должны пополняться смазкой БНЗ-З один раз в год через пресс-масленки в торцах осей. Это снижает трудоемкость их обслуживания в 10 раз по сравнению с применением заклад ной смазки, требующей снятия, разборки, сборки и обратной установки роликов. По опыту эксплуатации трудоемкость по полнения смазки пресс-масленки составляет 150 чел-ч на каж дый километр става конвейера. Уплотнения, выполненные ме тодом штамповки из стальной ленты, имеют минимальные
зазоры, более стойки к воздействию влаги, масел, абразивных частиц и менее трудоемки в изготовлении.
На многих металлургических предприятиях СССР и за ру бежом ресурс роликов, работающих в абразивной среде, повы шается в несколько раз путем оснащения их сплошными или дисковыми футеровками из различных материалов, например резины, неопрена с вискозным волокном, цинка, полиуретана, каменного литья, ситаллов, шлакоситаллов и др. Крепление футеровки может осуществляться с помощью клеевой массы, заполняющей пространство между фигурными выточками фу теровки и корпусом ролика. В Великобритании для подземных конвейеров применяются термоусадочные футеровки, стойкие к действию влаги, щелочей и кислот. Для повышения жесткости соединения футеровки корпус выполняется с фигурными па зами, в которые входят выступы футеровки.
В ФРГ, США и Великобритании все большее распростране ние получают ролики из пластмассовых полиамидных матери алов с пределом прочности 46—47 МПа. Пластмассы имеют меньшую массу, хорошо штампуются и обрабатываются, стойки к действию шахтных вод, износостойки и недороги. Пластмас совые ролики из ударопрочного поливинилхлорида, выпускае мые фирмой «Аргуто» (США), имеют высокие жесткость и стойкость к ударным нагрузкам, самосмазывающиеся подшип ники, низкие коэффициент сопротивления вращению и уровень шума при работе. В определенных условиях к пластмассовым роликам предъявляется требование антиэлектростатичности. Они оснащаются электропроводными стопорными кольцами, проводящими заряды от корпуса к подшипникам, осям ролика
идалее на металлоконструкцию конвейера.
ВСССР и США имеется некоторый опыт изготовления и применения роликов с деталями из древесного материала (твердой высушенной древесины, пропитанной смазочным ма териалом, древесной стружки, пропитанной фенолформальде гидной смолой и прессованной на гидравлических прессах, дре весного композиционного пластика, армированного стеклово локном). Подшипники скольжения из древесины, пропитанной смазкой, обладают самосмазывающимся свойством. При увели
чении нагрузки подшипник размягчается и смазка выступает на поверхность и смазывает ее. В некоторых конструкциях подшипники выполняются с резервуарами, заполняемыми смазкой, которая равномерно расходуется в процессе работы.
В Могилевском технологическом институте создан ролик комбинированной конструкции, корпус которого выполняется из древесины, а втулка и подшипники — металлическими серий ного производства. Известные конструкции роликов с дета лями из дерева пока не нашли широкого применения прежде всего из-за невысоких эксплуатационных качеств (повышен ного коэффициента сопротивления вращению, низкой стойко сти к ударным нагрузкам и надежности в работе).
Установлено, что ударные нагрузки на роликоопоры и ленты не могут быть снижены только за счет амортизирующей подвески. На силу удара существенное влияние оказывает уп ругость роликов. Применяемая для футеровки резина обладает относительно малой податливостью. Использование же резины
смалым модулем упругости малоэффективно и неэкономично.
Всвязи с этим изыскиваются пути создания роликов, облада
ющих большой податливостью. Целесообразно связь корпуса с подшипниковыми стаканами осуществлять через пластинча тые упругие элементы (рис. 5.6,а1). Последние позволяют уменьшить динамические нагрузки на подшипники и став кон вейера, а также существенно снизить изгибающий момент на подшипники от изгиба оси. Величина момента, воспринимае
мая |
подшипниковым |
узлом при действии внешней |
нагрузки |
|||
от |
1 |
до 4 кН, |
для |
жесткого ролика составляет |
7—35 Н • м, |
|
а |
для ролика |
с упругим элементом — 0,2—1,2 |
Н*м |
(ИГТМ |
АН УССР). Упругие элементы можно выполнять переменными в сечении в виде двутавра (рис. 5.6, б) с возможностью регу лирования их жесткости. При этом упругий элемент соединя ется со стаканом подшипника путем вулканизации, раскреп ляется конусными кольцами между корпусом ролика и стака ном подшипника и стягивается конусными кольцами посред ством болта и гайки. Внешняя поверхность упругих элементов смазывается клеем для лучшего соединения с корпусом.
В конструкции ролика, разработанного ИГТМ АН УССР, упругие элементы выполнены со сферической поверхностью, расположенной с зазором по отношению к корпусу (рис. 5.6,б). Упругие элементы опираются на стаканы подшипников через кольцевые выступы. Подшипниковые стаканы с упругими эле ментами вставляются в расточки корпуса ролика и завальцовываются. Вулканизация упругих элементов, шайб и выступов стаканов производится в пресс-форме совместно. При взаимо действии кусков груза с роликом в соударении сначала уча ствуют только корпус и боковые участки упругих элементов, работающих на сдвиг. Затем корпус ролика вступает в контакт с упругими элементами и сжимает их. Упругий элемент выпол няет роль амортизатора с нелинейной характеристикой жестко сти, работающего последовательно на сдвиг и сжатие.
Для повышения надежности крепления упругих элементов ролик оснащается стяжными крышками (рис. 5.6,г). При сжатии упругих элементов на них образуются выступы, кото рые заполняют отверстия в корпусе и препятствуют смещению упругих элементов относительно корпуса. В другом варианте упругие элементы выполняются с расположенными с обеих сторон фигурными выступами. Верхние вьгступы входят в пазы
корпуса, |
а |
нижние — в |
пазы стаканов |
подшипников. Система |
|
выступов |
обеспечивает |
надежную |
связь упругих элементов |
||
с корпусом и стаканом подшипника. |
|
роликов свидетельст- |
|||
Большое |
разнообразие конструкций |
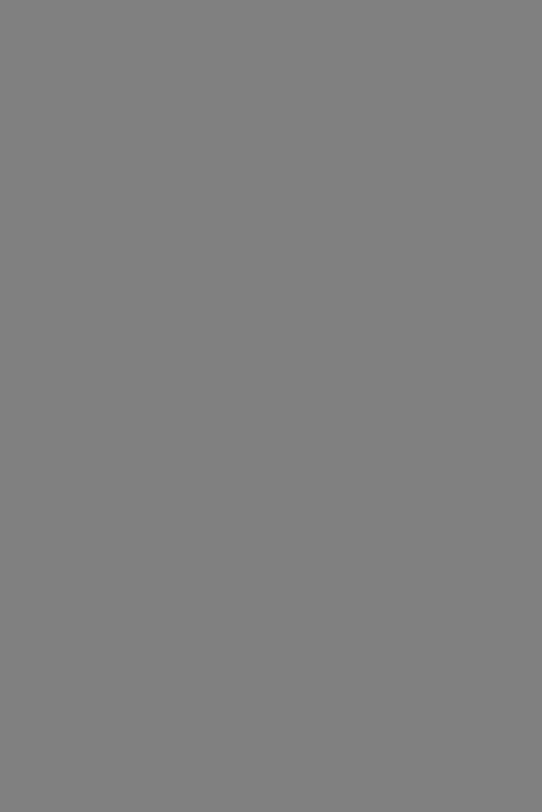
нах роликоопоры. Подшипники закрыты крышками и зафикси рованы стопорными кольцами. Торцевые части корпуса имеют переменное сечение с утолщением в местах наибольшей кон центрации напряжений. Роликоопоры с роликами моноблочной конструкции изготавливаются желобчатыми с углом наклона боковых роликов 20 и 30° и вынесенным вперед средним ро ликом, а также прямыми.
Параметры унифицированных роликов моноблочной кон струкции приведены ниже.
Диаметр ролика, |
мм |
|
|
|
Длина ролика, мм |
|
|
|
|
||||
89 . . . |
160, |
200, 250, 500, 600, 750 |
500, |
600, |
750, |
950, |
|||||||
108 (102) |
160, |
200, |
250, |
315, |
380, |
465, |
|||||||
133 (127) |
1150 |
380, |
465, |
950, |
1160, |
1400 |
|
|
|
|
|
||
315, |
|
900, |
950, |
1150, |
|||||||||
159 (152) |
315, |
380, |
465, |
530, |
600, |
670, |
750, |
||||||
194 |
1400, |
1600, |
1800 |
1150, |
1600, |
1800, |
2200 |
|
|||||
530, |
600, |
750, |
900, |
|
Исполнение корпуса ролика закрытым делает его герметич ным, исключающим проникновение продуктов коррозии и ока лины из внутренней полости корпуса в узел подшипника. Ме таллоемкость ролика снижена на 30 %. Уменьшение числа де талей и исключение соединения корпус — вкладыш позволяет уменьшить трудоемкость изготовления ролика в несколько раз. Улучшен доступ для осмотра и смазки подшипниковых узлов. Упрощается комплекс оборудования для изготовления и сборки роликов. Уменьшается сопротивление вращению роли ков, а следовательно, и затраты электроэнергии благодаря уменьшению массы вращающихся частей. Предполагается уве личение срока службы роликов моноблочной конструкции по сравнению с выпускаемыми обычного исполнения в 1,5—2 раза. Дальнейшее совершенствование роликоопор с моноблочной компоновкой связано с применением подшипников, обеспечива ющих работу роликов не менее трех лет. Производство моно блочных роликов освоил Николаевский машиностроительный завод подъемно-транспортного оборудования для лент шири ной 650 и 800 мм, а также Белохолуницкий машиностроитель ный завод для лент шириной 1400 мм (нижние ролики).
5.2. ОПРЕДЕЛЕНИЕ РЕСУРСА КОНВЕЙЕРНЫХ ЛЕНТ
Согласно статистическим данным, стоимость ленты состав ляет в среднем 50—60 % стоимости конвейера, а для шахтных конвейеров достигает 67 %. Еще больше эксплуатационные рас ходы, связанные с заменой и ремонтом лент. Затраты на амор тизацию лент на шахтах составляют 70—80 % всех затрат на амортизацию конвейеров. Поэтому изучение вопросов ресурса и износа лент имеет большое практическое значение. Ресурс конвейерных лент — это наработка лент от начала эксплуата ции или после восстановительного ремонта до наступления предельного состояния, определяемого конкретными условиями.
Ресурс конвейерных лент зависит от характера действующих на нее нагрузок и видов износа. Многие факторы в той или иной мере влияют на износ ленты. Наибольший интерес пред ставляют те, которые являются доминирующими и степень влияния которых можно эффективно изменять с положитель ным эффектом без ущерба процессу доставки груза, принятому порядку расчета и выбора оборудования, технико-экономиче ским показателям, правилам техники безопасности и условиям труда.
Виды износа лент можно классифицировать по характеру
разрушения |
элементов конструкции ленты |
в соответствии |
с данными |
(табл. 5.6). |
лент на пред |
Статистическое обследование эксплуатации |
приятиях черной и цветной металлургии дали следующее рас пределение видов износа по элементам конструкции ленты: ра бочей обкладки — 56%, каркаса — 20%, бортов— 13%, нерабо
чей обкладки — 3%, |
аварийный износ всей ленты (включая |
нарушение стыкового |
соединения)— 8% [37]. Распределение |
по характеру износа для конвейеров угольной промышленности составляет: истирание средней части рабочей обкладки — 27%, полосовое истирание рабочей обкладки, порезы, вырывы рабо чей обкладки и прокладок —19%, износ бортов— 13%, исти
рание и разрушение нерабочей обкладки |
(включая |
воспламе |
нение)— 11 %, ударное разрушение— 10%, потеря |
прочности |
|
ленты из-за стыков— 10%, разрушение |
обкладок |
и каркаса, |
связанное с воздействием температуры и агрессивной среды (шахтных вод),— 4 %, усталостный износ обкладок и кар каса — 6 %.
Представляет интерес распределение видов износа в зави симости от крупности транспортируемого груза. По данным ИГТМ АН УССР, при транспортировании горной массы круп ностью 0—160 мм на предприятиях черной металлургии рас пределение видов износа следующее: истирание средней части
рабочей обкладки — 76%, |
общая |
потеря прочности |
(в |
основ |
|
ном из-за низкого качества |
и стыковки лент) — 13 %, |
продоль |
|||
ные порывы — 5% , |
усталостный |
износ каркаса — 3 %. |
исти |
||
рание и разрушение |
нерабочей |
обкладки — 3 %. В |
условиях |
доставки горной массы крупностью 0—300 мм из-за износа рабочей обкладки, общей потери прочности ленты (из-за сты ков и качества изготовления лент), усталостного износа и про дольных порывов выходит из строя — 70, 17, 7 и 6 % лент со ответственно. При транспортировании горной массы крупно стью 0—400 мм количество изношенной ленты составляет: из-за общей потери прочности ленты (связанной со стыковкой, ка чеством лент) — 43%, износа каркаса и нерабочей обкладки — 33 %, износа рабочей обкладки — 24 %.
Данные о распределении конвейеров по крупности транс портируемого груза, полученные ИГД Минчермета СССР, ИГД им. А. А. Скочинского, ВНИИнерудом и ПромтрансНИИпроек-
Вид износа
Истирание средней части рабочей об кладки с последующим разрушением каркаса Полосовое истирание рабочей об
кладки, порезы, вырывы рабочей об кладки и прокладок о последующим
разруш ением каркаса
Износ бортов ленты с последующим расслаиванием каркаса
Ударное разрушение рабочей обклад ки и каркаса
Истирание и разрушение нерабочей обкладки с последующим разруше нием каркаса Усталостный износ обкладок и кар
каса с последующей потерей проч ности ленты
Разрушение обкладок и каркаса, свя занное с воздействием повышенных или пониженных температур и окру жающей среды Общая потеря прочности ленты
Аварийный износ
ю
3.
Причина |
Факторы |
Скольжение груза по ленте в месте загрузки н на роликоопорах
Повышенное трение ленты об эле менты конструкции конвейера
Взаимодействие ленты с элементами конструкции конвейера при децен трироваином ходе Ударное взаимодействие кусков груза
с лентой в месте загрузки и на ро ликоопорах
Проскальзывание нерабочей обклад ки на роликоопорах и барабанах
Многоцикловая деформация ленты при взаимодействии с элементами конструкции конвейера и транспор тируемым грузом Влияние повышенной или понижен
ной температуры окружающей среды
Увеличение количества стыков и участков ремонта на ленте, низкое качество лент
Нарушение правил эксплуатации
Транспортирование горной массы повышенной абра зивности; повышенные скорость, угол транспорти рования, провес ленты между роликоопорами Наличие уплотняющих бортов, сбрасывателей груза и устройств очистки, заклинивание посторонних предметов
Неравномерная загрузка и серповидность ленты; перекос конструкций, роликов и барабанов
Повышенные крупность, высота падения груза и скорость движения ленты; отсутствие амортизирую щих опор в загрузочной и на линейной частях кон вейера Доставка налипающих и абразивных грузов; нару
шение работы роликов и пробуксовка барабанов; заклинивание посторонних предметов Отклонение параметров эксплуатации от оптималь
ных (типа, натяжения и скорости ленты, расстояния между роликоопорами, диаметра барабанов, круп ности транспортируемого груза)
Доставка горячих грузов; эксплуатация лент при низких температурах и отсутствие защитных соору жений
Применение механических соединений; многоразо вое использование восстановительного ремонта; не соблюдение технологии изготовления и хранения лент Неправильный выбор лент; отсутствие своевремен
ного ремонта; выход из строя оборудования в про цессе эксплуатации ленты и др.
том, показывают, что 80—85 % ленточных конвейеров транс портируют горную массу или продукты ее обработки крупно стью 0—160 мм. В этих условиях при правильной эксплуата ции лент доминирующим видом износа ленты (60—80 %) является истирание рабочей обкладки с последующим разруше нием каркаса. Таким образом, износ и, соответственно, ресурс рабочих обкладок является решающим фактором в определе нии ресурса или срока службы ленты.
Сроки службы конвейерных лент на предприятиях горной и металлургической промышленности колеблются в широких пределах — от нескольких месяцев до 7—8 лет. Среднестати стические сроки службы лент составляют для предприятий ме таллургической промышленности — 24—27 мес, угольной — 27—30 мес, нерудной — 30—35 мес. На некоторых предприя тиях даже при доставке абразивных грузов среднестатистиче ские сроки службы лент достигают 50—70 мес. Большое зна чение в повышении ресурса лент имеют прогнозирование долговечности, выбор параметров ленты и ее отдельных эле ментов.
Износ рабочей обкладки. Износ рабочих обкладок конвей
ерных |
лент — сложный |
процесс, изучение |
которого не |
может |
быть |
эффективным без |
выяснения вида и |
механизма |
износа. |
Из фундаментальных работ по трению и износу высокоэла стичных материалов следует, что для определения механизма износа необходимо знание комплекса признаков. В частности, для обкладок лент выбраны признаки, по которым можно су дить о механизме износа обкладок в конкретных условиях экс плуатации. К таким признакам относятся свойства взаимодей
ствующих |
пар трения — геометрические характеристики и уп |
ругость; |
эксплуатационные факторы — нагрузка, 'скорость |
скольжения; интенсивность износа; характер поверхности и рисунок истирания обкладки.
Известные предположения о механизме изнашивания ре зиновой обкладки, основываясь только на данных абразивно сти грузов, сводятся к тому, что рабочие обкладки испытывают абразивный износ. Этот вид износа связан с микрорезанием поверхности эластичной обкладки острыми твердыми микро выступами груза. В этой связи изучены, в частности, геомет рические и минералогические характеристики поверхностей Же лезных руд и карбонатных пород и резиновой обкладки. Ре льеф поверхности кусков груза определяется минералогической структурой и характером технологической обработки. Геомет рия (шероховатость) поверхности кусков груза образуется в ре зультате спайки зерен минералов, которые через свои выступы контактируют с обкладкой ленты (рис. 5.8,а, в). Главной формой рудных минералов и минералов карбонатных пород является ромбоэдрическая, а кварца и корунда— удлиненно призматическая. Поверхность таких минералов может быть мо делирована сферой и конусом (рис. 5.8, б) [38].
РИС. Б.8.
Минералогические (а, б) и микрогеометрическая (в) характеристики груза:
1—4 — формы минералов гематита, кварца, корунда и кальцита; 5—8 — их модели как единичных выступов груза; 9—11 — номинальная, контурная и фактическая площади контакта куска груза с обкладкой
Для исследования геометрических характеристик и площа дей касания образцов железных руд, карбонатных пород и ре зиновой обкладки применен метод профилографирования. Про филограммы (рис. 5.9, а—г) снимали по точкам — ординатам неровностей поверхности путем суммирования участков, охва тываемых окуляром микроскопа МИС-11. Одновременно иссле довали микрогеометрию поверхностей шлифовальной шкурки монокорунд-150 и металлических сеток, применяемых при ис пытании резин на истирание (рис. 5.9,в,г). Обработку профилограмм и расчет геометрических характеристик проводили по методу Н. Б. Демкина с использованием математической обра ботки результатов измерений.
Поверхности кусков |
железных |
руд |
и карбонатных пород |
с геометрической точки |
зрения |
могут |
быть моделированы |
в виде набора жестких сфер, расположенных с постоянной плотностью, а обкладка — гладкой, весьма упругой поверхно стью. В соответствии с этим металлическая сетка более близко моделирует поверхность руд и карбонатных пород, чем шлифо вальная шкурка монокорунд-150.
При фрикционном воздействии шероховатых поверхностей различают номинальную, контурную и фактическую площади касания и, соответственно, номинальное, контурное и факти ческое давление (нагрузки). Интенсивность износа при трении зависит от фактической площади касания. Номинальная пло щадь в рассматриваемых условиях определяется габаритными размерами кусков груза, а в общем случае — площадью за полнения ленты горной массой. Контурная площадь образуется как сумма пятен касания кусков груза с обкладкой. Установ лено, что для железных руд и карбонатных пород контурная площадь контакта может быть приближенно принята равной номинальной. Таким образом, контурное давление принима-
мкм
л/ii\ \ х
мкм
/ 7 "
71
г—
о
, л Г ) |
-А |
А |
/ А |
* А |
|
1лL/' |
/ J 1/1л/^ \ |
V,\ |
/ |
л |
i |
1 |
|
|
|
1,0 |
|
|
1,5 ММ! |
РИС. 5.9. |
|
|
|
Профилограммы поверхностей:
а — железной руды; |
б — шлифовальной шкурки монокорунд-150; |
в — железной руды |
(с увеличением по |
горизонтали); г — металлической сетки для |
испытания резин на |
|
истирание |
|
ется равным номинальному. В соответствии с принятыми моде лями определены геометрические характеристики грузов и по лучена формула для расчета фактической площади касания груза с обкладкой:
( гср Л 2V+1 |
Г |
1»5яРн П • |
и2) |
2v |
(5.1) |
J 2v+1 » |
|||||
V ятах) |
L |
к 2е |
|
|
|
|
|
|
где г]ф — фактическая площадь касания, относ, един; у = 0>87 — коэффициент, учитывающий упругость обкладки; /С2» b, v — показатели шероховатости поверхности груза; гср— средний радиус выступов груза, мкм; Нтах — максимальная высота вы ступов груза, мкм; Е — модуль упругости обкладки, Па; ц = = 0,5 — коэффициент Пуассона для резины; Ри— номинальное
222
давление (нагрузка). Определяется как произведение плотности груза на высоту сечения груза на ленте, кгс/см2.
Экспериментально получены параметры геометрии (шеро ховатости) поверхности груза, которые приводятся ниже.
Вид груза: железная руда известняк
* I ,00 .О У■
340
Н шах* |
м к м Я тах/гср |
Ь |
V |
Кг |
162 |
0,50 |
2,1 |
4 |
0,60 |
148 |
0,43 |
2,6 |
4,4 |
0,75 |
Для железной руды
' ср
^ т а х
для известняка
'ср |
\0 '4У |
Р н У ,9° |
|
Н шах |
/ |
\ |
Е ) |
Отношение гср/#тах характеризует остроту выступов. Факти |
|||
ческая площадь касания кусков |
|
груза с обкладкой возрастает |
|
с увеличением радиуса выступов |
и |
давления и уменьшается |
с увеличением модуля упругости обкладки, высоты или остроты выступов (рис. 5.10).
На основании найденных геометрических моделей поверхно стей трения была установлена физическая сущность процесса истирания обкладки ленты транспортируемой горной массой [39]. В месте загрузки и на роликоопорах горная масса про скальзывает относительно ленты, взаимодействуя своей жесткой шероховатой поверхностью с поверхностью упругой обкладки. Элементарной моделью трения в этом случае будет движение жесткого сферического индентора, имитирующего отдельный вы ступ груза (зерна минерала) по упругому пространству обкладочной резины. Сферические выступы поверхности груза в ре зультате скольжения вызывают изнашивание обкладки, меха низм которого заключается в следующем. Каждый выступ поверхности груза увлекает поверхностный участок обкладки, сжимая его впереди себя и растягивая позади (рис. 5.11, (а—в)). Затем участок поверхности обкладки преодолевает силу трения за счет сил упругости и возвращается в исходное положение. Выступ проскальзывает вперед, воздействуя на другие участки обкладки. В наиболее нагруженной зоне позади выступа (ин дентора) приведенное напряжение растяжения пропорционально коэффициенту трения и фактическому контактному давлению
Опр = ЩРф
или
Опр = kfPн/Лф*
где егПр — величина приведенного к растяжению напряжения

0,2 |
_ J __ |
0,6 |
0,8 |
1,0 |
1,2 |
|
*тах/гcp |
I |
_J___ |
|
_i_ |
|
|
|
|
40 |
80 |
120 |
160 |
200 |
240 |
260 |
/^maXfMKM |
l |
i |
_ i___ |
_J___ |
_ J ___ |
i |
_I______i_____ I |
|
100 |
150 |
200 |
250 |
300 |
350 |
400 |
rCp’/D,MKM |
РИС. 5.10.
Зависимости влияния различных факторов на фактическую площадь касания груза с обкладкой ленты г|ф
в точке позади выступа; |
К — коэффициент пропорциональности |
||
(для |
высокоэластичных |
материалов К = 8); |
f — коэффициент |
трения |
груза по обкладке; Рф— фактическое |
контактное дав |
|
ление. |
|
|
|
Во время проскальзывания горной массы поверхностный слой обкладки подвергается воздействию большого количества выступов. Многократные нагружения, имеющие место в области контакта, вызывают усталостное разрушение и отделение частиц обкладки, если число циклов превысит некоторый предел. Этот предел зависит от фрикционной усталости обкладки. Количе ство циклов до отделения обкладки можно получить из уравне ния кривой усталости для резин
Механизм взаимодействия выступов груза с обкладкой ленты при трении:
а — схема скольжения выступа; |
б — две |
стадии |
деформации |
поверхности обкладки; |
а — распределение |
напряжений на |
поверхности |
обкладки |
|
ИЛИ |
|
|
|
|
|
Лр ( |
0оГ)Ф У р |
(5.2) |
|
|
V |
KfPH) |
|
|
где 0 о — прочность обкладки на разрыв; /р — коэффициент ди намической выносливости обкладки.
Таким образом, износ резиновой обкладки грузом крупно стью 0—160 мм происходит в основном в результате фрикцион ной усталости поверхностного слоя скользящими выступами груза. Согласно теории фрикционно-усталостного износа при уп ругом контакте по И. В. Крагельскому, линейная интенсивность износа связана с числом циклов до разрушения соотношением
(v |
тахЛФ |
(5.3) |
1) rtpdcp |
|
|
где / л — линейная интенсивность износа, |
характеризующая от |
|
ношение высоты изношенного |
слоя к пути трения; е — относи |
тельное сближение поверхности обкладки с выступами груза; dCp — средний диаметр единичного пятна касания выступа груза с обкладкой ленты.
По методике Н. Б. Демкина
г = ( |
*,5я ^ 2V-4-1 |
( |
Гср |
Ч 2у4-1 Г |
^ н(1 — ц2) 1 2V+1 |
(5 4 ) |
|
\ |
/ |
\ |
Нmax ' |
L |
Е |
J |
|
8 Заказ № 1462 |
225 |
|
|
1___ |
V - f l |
V |
|
|
|
|
Ap_ 2 ( - i ) « |
|
|
r " + ' |
[ |
f *(1 ~ l**>] ’V+' |
|
||
|
|
|
|
|
|
|
|
(5.5) |
На основании соотношений |
(5.1) —(5.5) |
можем записать, что |
||||||
l,65(vv)2 |
Р^+Р'р |
f |
Е |
V—Р<р—1Г { |
Н max V |
К/ Т |
|
|
^ 2^«(V+1) |
Ч |
1 — |i* / |
1Л Гср / |
о0С0 J |
|
|||
1 |
Л=- |
|
|
|
0 |
|
2v+1 |
(5-6) |
Р= |
" |
2v + |
1 ’ |
С = yb 2v+i |
|
|||
2v + 1 ’ |
|
|
|
|
|
где K G — коэффициент, учитывающий неравномерность контакт ных напряжений (для железных руд /Сб=1 ,4 9 , для известняка Кв= 1,5).
В соответствии с найденными значениями шероховатости груза и коэффициентов уравнения интенсивности износа имеют вид:
для железной руды
J„ = 0,92P^1+0•шp£0’89'p-, ( - i-J p ;
для известнякаL
Решение уравнения (5.6) с помощью ЭВМ при вариации зна чений входящих в него параметров, характеризующих различ ные условия эксплуатации лент, позволило установить следую щее (рис. 5.12). Интенсивность износа обкладок значительно возрастает при увеличении нагрузки, коэффициента трения и па дает с увеличением разрывной прочности и коэффициента динамической выносливости обкладки. Износ также увеличива ется с ростом модуля упругости обкладки при условии постоян ства усталостно-прочностных характеристик. В противном слу чае при определении зависимости интенсивности износа от модуля упругости необходимо учитывать изменение усталостно прочностных характеристик.
Экспериментальные исследования характера и интенсивно сти износа рабочих обкладок конвейерных лент проводились в лабораторных условиях (рис. 5.13) и на действующих конвей ерах Балаклавского РУ им. А. М. Горького. В качестве груза использовались железные руды, гранитный и известковый щебни.
Экспериментальные значения интенсивности износа известця.
ком резиновых обкладок на |
основе НК + БСК |
приведены |
в табл. 5.7 (расчетное значение |
/ л=1,14-10—8 при |
крупности |
куска 60 мм, коэффициенте трения 0 ,6 , нормальном давлении 0,01 МПа).
J-W8
2.5
2,0
1.5 |
|
|
|
|
|
|
1,0 |
|
|
|
|
|
|
0,5 |
|
|
|
|
|
|
0,004 |
0,006 |
0,008 |
0,010 |
0,012 |
о,on |
0,016 |
I |
I |
1 |
I |
| |
I |
|
0,4 |
0,5 |
0,6 |
0,7 |
0,8 |
0,9 |
? |
1 |
I |
1 |
3 |
г |
5 |
|
0 |
1 |
2 |
4 |
6 |
||
1 |
I |
1 _ |
I |
i |
I |
I |
70 |
85 |
100 |
115 |
130 |
П5 |
1f0 |
I |
i |
I |
i |
I |
| |
|
2,3 |
2,5 |
2,7 |
2,9 |
3,1 |
3,3 |
3,5 |
1 |
I |
I |
i |
I |
1 |
i |
0,1 |
0,2 |
0,3 |
0,4 |
0,5 |
0,6 |
0,7 |
|
|
|
РИС. 5.12. |
|
|
Ри,МПа.
___ i________ l
V _ ь
£,МПа. i ’ I
,б0,Ша
3,7 t
ii
^т а х / г ср
Зависимости влияния различных факторов на интенсивность износа обкладки
В процессе исследований изучался характер износа поверх ности обкладок и измерялась толщина истертого слоя обкладок с помощью радиоактивных изотопов. Линейная интенсивность износа определялась как отношение толщины истертого слоя обкладки к пути трения груза. Наблюдение за характером по верхности изнашиваемых обкладок показало следующее. В про цессе истирания на рабочей обкладке появляются темные пятна касания (износа). Пятна тем ярче, больше и плотнее располо жены относительно друг друга, чем абразивнее и крупнее куски груза, больше скорость движения ленты, а значит, и проскаль зывание (рис. 5.14,а). После завершения серии испытаний на лабораторном конвейере на сравнительно гладкой осповидной поверхности рабочей обкладки с редко расположенными цара пинами заметных порезов не наблюдалось (рис. 5.14,6). Та кой характер поверхности рабочей обкладки свидетельствует
|
РИС. 5.13. |
|
|
Лабораторный |
конвейер для исследования износа |
обкладок |
лент: |
/ — электродвигатель; |
2 — регулятор скорости; 3 — редуктор; 4 |
— конвейер; |
5 — бункер |
о преобладании фрикционно-усталостного износа. На нерабочей обкладке имеются поперечные трещины, связанные с усталост
ным износом от |
многократного |
изгиба ленты на |
барабанах |
(рис. 5.14,в). |
представлены |
фотографии рабочих |
обкладок |
На рис. 5.15 |
с трех промышленных конвейеров, отличающихся интенсивно стью воздействия груза на рабочую обкладку. На всех кон вейерах зафиксировано шевеление и скольжение груза на роликоопорах верхней ветви ленты и в месте загрузки. На кон вейере № 1 был установлен криволинейный лоток, который позволил существенно снизить проскальзывание груза в месте загрузки.
Рабочая обкладка ленты конвейера № 1 после 39,5 мес экс плуатации имеет сравнительно гладкую поверхность с попереч ными трещинками (длиной 2—2,5 мм) усталостного порядка (рис. 5.15,а). В данном случае по характеру поверхности рабо чей обкладки преобладает фрикционно-усталостный износ.
На наклонном конвейере № 2 наблюдалось более интенсив ное проскальзывание груза на роликоопорах и в месте загрузку причем количество воздействий груза на ленту в месте загрузки больше в 9 раз, чем на конвейере № 1 , так как больше соответ ственно число циклов ленты. Лента после 21 мес работы снята с эксплуатации. Поверхность ее рабочей обкладки имела ярко выраженную шероховатость, царапины, выступы и впадины ко торой располагаются беспорядочно, образуя осповидную по верхность (рис. 5.15,6). Характер поверхности рабочей обкладки свидетельствует о совместном действии фрикционно-усталостного и абразивного износа.
Рабочая обкладка конвейера № 3 после 13 мес работы в еще более тяжелых условиях (транспортировался известняк крупн^-
Конвейер
Лабораторный
Промышленный:
№1
№2
г |
со |
|
Параметры конвейера |
|
|
длина, м |
угол накло на, градус |
скорость движения, ленты, м с |
ширина ленты, мм |
1,5 О-г-50 1,5—5,0 800
Характеристика |
Условия износа обкладки ленты |
|
|
|
груза |
|
|
крупность, мм |
коэффици тренияент |
нормальное давление, МПа |
Линейная интен |
сивность или вид |
|||
|
|
характер взаимодействия |
износа / к |
|
|
груза с обкладкой |
|
|
|
1 |
|
60 |
0 .6 |
0,01 |
Незначительные ударные нагруз |
2,8*10-8 |
|
|
|
ки, сильное проскальзывание |
|
250 |
0 |
2.1 |
1000 |
0—160 |
0 ,6 |
0,01 |
Ударные нагрузки |
отсутствуют, |
1,33*10-8 |
|
|
|
|
|
|
|
проскальзывание незначительное |
|
|
28 |
15 |
2 |
1000 |
0—160 |
0 ,6 |
0,01 |
. Незначительные |
ударные на |
Фрикционно-уста |
|
|
|
|
|
|
|
грузки, сильное проскальзывание |
лостный и абра |
|
|
|
|
|
|
|
|
|
|
зивный |
68 |
12 |
2 |
1000 |
0—300 |
0 ,6 |
0,02 |
Значительные ударные нагрузки, |
Ударное разруше |
|
|
|
|
|
|
|
|
сильное проскальзывание |
ние |
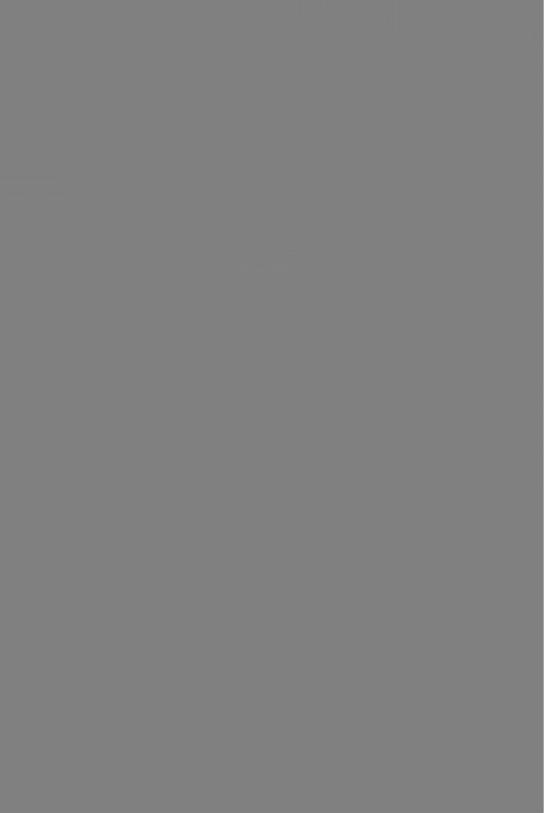
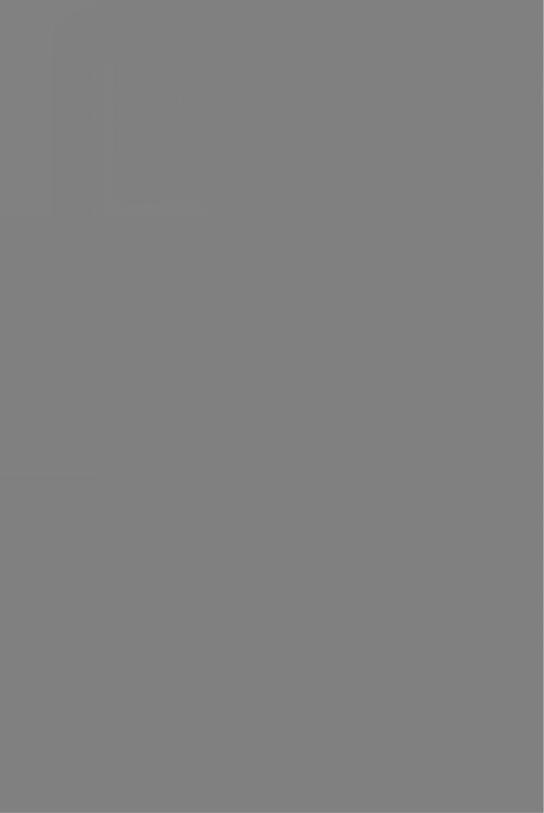
232
Вид износа |
Характер воздействия на ленту |
Признаки износа |
Скорость износа |
Ориентировочный |
срок службы |
||||
|
|
|
|
ленты,, лет |
Фрикционно-усталостное |
Незначительное проскальзывание гор |
Сравнительно глад |
Умеренная |
2 —3 и более |
||||||
истирание |
|
ной |
массы |
крупностью |
0—150 мм |
кая осповидная по |
|
|
||
|
|
|
|
|
|
|
верхность |
|
|
|
Абразивное |
истирание |
Значительное |
|
проскальзывание гор |
Порезы и |
царапины |
Интенсивная |
2—0,5 и менее |
||
|
|
ной массы крупностью 0—300 мм |
|
|
|
|
||||
Истирание |
«скатыва |
Заклинивание |
кусков горной массы |
Глубинные |
вырывы |
Очень интенсивная |
1—0,5 и менее |
|||
нием» |
|
крупностью 0—300 мм |
|
|
|
|
|
|||
Ударное разрушение |
Ударные нагрузки и сильное про |
Сквозные |
пробои и |
То же |
1—0 ,5 и менее |
|||||
|
|
скальзывание |
горной массы крупно |
порезы |
|
|
|
|||
|
|
стью 0—300 мм и более |
|
|
|
|
|
|||
Усталостный износ |
Многоцикловая деформация обкладки |
Трещинки |
|
Самостоятельного |
4—5 и более |
|||||
|
|
на роликоопорах, барабанах и от |
|
|
значения не имеет |
|
||||
|
|
горной массы |
|
|
|
|
|
|
||
Химический износ и ста |
Активная внешняя среда |
(темпера |
Образование липкой |
То же |
4 — 8 и более |
|||||
рение (деструкция) |
тура, |
влага, |
кислород) |
|
крошки |
|
|
|
ленту горной массы, наблюдаются переходы от одного вида из носа к другому или совместное действие нескольких видов из носа.
Следует, однако, отметить, что при высоком техническом уровне эксплуатации лент, транспортирующих горную массу крупностью 0—160 мм, преобладает фрикционно-усталостный износ в совокупности с усталостным. Эти виды износа менее ин тенсивны, чем абразивный и ударное разрушение. В практике необходимо стремиться к тому, чтобы воздействия потока гор ной массы на ленту были минимальны. Срок службы лент в та ких условиях достигает больших значений.
На рис. 5.16 представлены фотографии поверхности обкла док на конвейере № 1 Балаклавского рудоуправления имени А. М. Горького после 5 лет эксплуатации. На рабочей обкладке отсутствуют такие виды износа, как порезы, пробои, вырывы, благодаря обеспечению безударной погрузки горной массы на ленту и без существенного проскальзывания. Износ рабочей обкладки происходил в основном в средней части (рис. 5.16,а), рабочая обкладка в которой имела сравнительно гладкую (ос повидную) поверхность с редкими усталостными трещинками, что свидетельствует о преобладании фрикционно-усталостного износа. Бортовые участки рабочей обкладки, свободные от гор ной массы, мало изношены по толщине; на поверхности их ча сто расположены поперечные трещины усталостного порядка (рис. 5.16,6). На участках рабочей обкладки, расположенных между средним и боковым роликами, имелись глубокие и длин ные усталостные трещины (рис. 5.16,в). В этой зоне происхо дит так называемое «жевание» ленты с многократными резкими продольными изгибами. Для лент с малым числом прокладок этот вид износа в ряде случаев может быть решающим. В со временных конструкциях роликоопор средний ролик смещен по ходу движения ленты, что позволяет уменьшить изгибы ленты. На нерабочей обкладке по всей ширине ленты фрикционно усталостный износ не является преобладающим, в то время как проявление усталостного износа более существенно. Поверхность нерабочей обкладки покрыта трещинками различного направле ния, образующими сетку (рис. 5.16,г).
Поскольку при многих исследованиях абразивное истирание отличалось в неразрывной связи с ударными разрушениями (аб разивно-ударный износ), можно предположить, что эти два вида износа возникают чаще одновременно, так как сильное про скальзывание груза в большинстве случаев связано с предше ствующим ему ударным воздействием груза на ленту. Это об стоятельство также подтверждает самостоятельное значение фрикционно-усталостного износа и определенность условий его возникновения. Кроме того, следует различать абразивно-удар ный износ рабочей обкладки и ударно-усталостный каркаса. В первом случае происходят разрушение и удаление поверхно стного слоя ленты рабочей обкладки, а во втором — усталостное
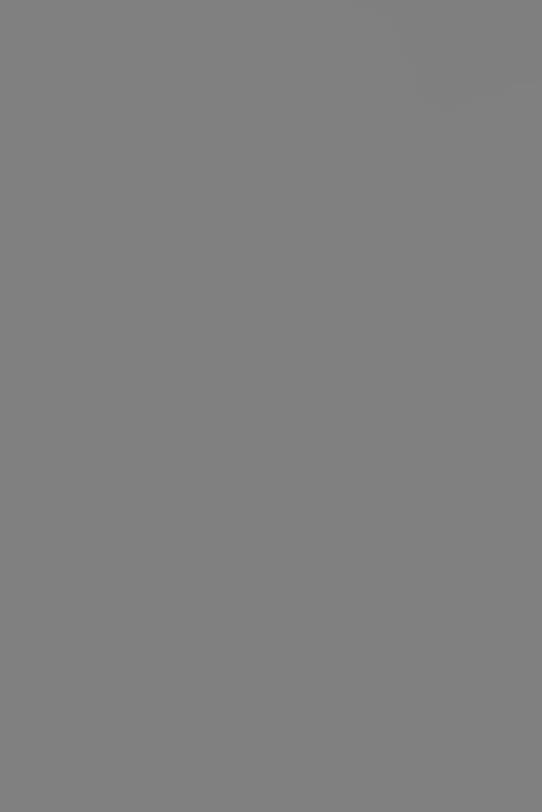
кладка ;лентьг, расположенной'*®» жесткой роликоопоре,'повреж дается сразу при падении* куска^груза./массой 30—50 кг с вы соты 2—3 м. Различными мероприятиями (применение специаль ных загрузочных устройств; 1^лён1\ Ставов и подсыпки) добива ются снижения ударных нагрузок, а значит, уменьшения доли ^Ьразкйно’-ударногб изноба.
Усталостный к химический виды йзноса’ рабочей обкладки также сопутствуют друг другу и, как правило, самостоятельного значения не имеют. Однако в^определенных условиях (напри мер, при длительном воздействии низких и повышенных темпе ратур, влаги с ^включением щелочи и кислоты, солнечных лучей) эти виды износа могут быть основными. Длительное воздей ствие низких и повышенных температур, влаги с включением щелочей и кислот, солнечных лучей приводит ,к резкому ухуд шению упруго-прочррстных характеристик обкладки. Соответст венно возрастает скорость фрикционно-усталостного, абразив ного и ударного видов износа. Повышением качества изготов ления лент, применением новых материалов, защитных соору жений, систем охлаждения добиваются снижения усталостного и химического износа на ресурс лент.
Ресурс рабочих обкладок. Установление видов, особенностей и интенсивности износа рабочих обкладок позволяет более полно подойти к проблеме ресурса конвейерных лент. Известно, что на конвейерах, транспортирующих горную массу крупностью О—160 мм, ресурс ленты до восстановительного ремонта может быть определен через ресурс рабочей обкладки. После износа обкладки каркас ленты, как правило, сохраняет свою целост ность и тягово-несущую способность. Дальнейшая эксплуатация ленты без обкладки приводит к ее быстрому разрушению, в ре зультате чего восстановление ленты становится практически не возможным. Период эксплуатации ленты до полного износа ра бочей обкладки может быть принят как гарантийный. В этом случае предлагается определять ресурс ленты по продолжитель ности износа рабочей обкладки. Основные положения настоя щей методики сводятся к следующему. Износ рабочей обкладки происходит вследствие ее истирания транспортируемым грузом в месте загрузки и на роликоопорах с учетом дополнительных повреждений в виде усталостных трещин, пробоев, вырывов, порезов.
Ресурс ленты (рабочей обкладки) в часах (при загрузке конвейера во времени в продолжении смены, равной 0,75— 0,85):
|
(5.7) |
где б — толщина рабочей обкладки, мм; h —линейный |
износ |
рабочей обкладки, мм/ч, |
|
h = hn -\-hpy |
(5.8) |
где Лш Лр — линейный износ рабочей обкладки, |
соответственно, |
в месте загрузки и на роликоопорах, мм/ч; |
|
АЛ= ДАПЛГ, |
(5.9) |
где Д/1п — линейный износ рабочей обкладки в |
месте загрузки |
за один оборот ленты, мм; N — число оборотов ленты за 1 ч ра |
|
боты конвейера, |
|
N ~ I8 OO0 /L, |
(5 .1 0 ) |
где v — скорость движения ленты, м/с; L — длина конвейера, м;
Ар = ДАрМ, |
(5.11) |
где ДАр— линейный износ рабочей обкладки |
при прохождении |
одной роликоопоры, мм; М — число проходов ленты над роликоопорами рабочей ветви ленты за 1 ч,
|
М = |
1800и//, |
(5.12) |
|
где I — расстояние |
между |
роликоопорами |
рабочей ветви |
|
ленты, м. |
(5.7) —(5.12): |
|
||
С учетом формул |
|
|||
Т 0 = |
6 |
(5.13) |
||
ААП |
||||
|
180СЫ |
|
L
АЛп — J ji*Sni
АЛР = Jд5р>
где / л — линейная интенсивность износа, значения которой, оп ределенные теоретически по формуле (5.6) и экспериментально, приведены в табл. 5.9; 5П, Sp— длина участков проскальзыва ния груза на ленте (приближенно принимаемая за путь тре ния), соответственно, в месте загрузки и на роликоопорах за один оборот ленты, мм.
ТАБЛИЦА Ъ.9
Группа транспор |
Характеристика груза |
тируемого груза |
АСилыюистирающий: руда черных и
цветных металлов
БСреднеистирающий: известняки и др.
ВСлабоистирающий: песок, уголь, мягкие породы и др.
Линейная интен
сивность износа
/л•!<)-’
1,65
1,33
0,85
Длина участка проскальзывания груза на ленте в месте за грузки
где von— начальная скорость проскальзывания, мм/с; g — уско рение свободного падения, мм/с2.
Для определения начальной скорости проскальзывания и, со ответственно, длины участка проскальзывания примем допуще ния: частица заменяет поток груза, частица скользит по ленте без перекатывания и проскоков, лента в средней части пред ставляет собой гладкую поверхность. Формулы выведены для следующих основных случаев погрузки на ленту конвейера [40].
I случай — погрузка с питателя или конвейера: при транспортировании вверх или вниз
с _ |
103 [v ± л / 2 £ Я г s in a j2 |
On — |
--------------------------■* |
|
2 g(fcos a 2 ± sin a2) |
при транспортировании по горизонтали
с- 10V .
"2gf ;
II |
случай — погрузка |
с |
наклонного прямолинейного |
лотка: |
|||
при транспортировании вверх или вниз |
|
|
|||||
|
£ = |
Ю3 [у — |
V |
2g H n (1 + /л ctg «i) cos («! ± a2)]2 e |
|
||
|
|
|
|
2g(/cos a2 + sin a 2) |
|
|
|
при транспортировании по горизонтали |
|
|
|||||
|
о _ |
103 [у — V 2g//п (1 ~г /л ctg Cti) COS OCi] 2 |
|
||||
|
|
|
|
|
2gf |
' |
|
III |
случай — погрузка |
с |
криволинейного |
наклонного |
лотка: |
||
при транспортировании вверх или вниз |
|
|
|||||
|
|
о |
_ |
|
Ю3 ( О » 2 |
|
|
|
|
Оп — |
----------------------------- * |
|
|
||
|
|
|
|
2g (f cos a2 4= sin a2) |
|
|
|
при транспортировании по горизонтали |
|
|
|||||
|
|
|
с |
_ |
103(0,2и)2 |
|
|
|
|
|
•Ьп — ---- “ :---- » |
|
|
||
|
|
|
|
|
2gf |
|
|
где Нг — высота |
падения |
горной массы, м; |
Нп— высота |
пере |
пада лотка, м; /л — коэффициент трения горной массы о днище лотка; ai — угол наклона лотка, градус; аг — угол наклона кон вейера, градус.
В приближенных расчетах Von можно выразить через v. Уста новлено, что при использовании в местах загрузки конвейеров
криволинейных лотков, и специальных загрузочных устройств (обеспечивающих подачу грузопотока без существенного про скальзывания) 0 On^O,2 i;, а при использовании прямоли нейных (обычных) лотков и других направляющих элементов
1>оп«0,4и.
Sp= т к п ,
где Кп — коэффициент проскальзывания груз^ на роликоопоре рабочей ветви ленты, характеризующий отношение пути прог скальзывания груза на одной роликоопоре к расстоянию между роликоопорами.
На конвейерах N° 1— 3 Балаклавского рудруправления им. А. М. Горького экспериментально исследовалась величина про скальзывания груза на роликоопорах. Пррскадьзывание опреде лялось путем измерения линейного перемещения окрашенных кусков груза по всей длине .става конвейера. На рис. 5.17 пока зан характер проскальзывания груза на конвейере № 1 после перемещения слоя груза от места погрузки до разгрузочного барабана.
Из рис. 5.17 видно, что на среднем участке ленты проскаль зывание груза больше, чем на боковых. Более крупные куски груза имеют наибольший путь проскальзывания. Среднее значе ние коэффициента проскальзывания груза на роликоопорах со ставило 0,0024.
Значения показателей износа рабочих обкладок в месте по грузки A/zn и на роликоопорах A/ip, полученные на основе теоре тических и экспериментальных данных, приведены в табл. 5.10.
С учетом режима работы конвейера и коэффициента допол нительных повреждений ленты ресурс ленты по обкладке рас считывается по формуле
|
|
|
ТАБЛИЦА 5.10 |
|
|
Скорость |
Линейная интенсивность |
||
Показателя износа (условия погрузки) |
движе |
износа |
/Л-1(Г для группы груза |
|
ния |
|
|
|
|
|
ленты. |
А |
Б |
В |
|
м/с |
|||
A/in, мм (погрузка наклонным пря |
1,6 |
0,43 |
0,35 |
0 ,2 2 |
молинейным лотком или другими на |
2 ,0 |
0 ,6 8 |
0,55 |
0,35 |
правляющими элементами) |
2,5 |
1,05 |
0,85 |
0,54 |
|
3,15 |
1,67 |
1,34 |
0 ,8 6 |
|
4 |
2,70 |
2,17 |
1,39 |
ДЛП, мм (погрузка криволинейным лот |
5 |
4,20 |
3,39 |
2,16 |
1,6 |
0,11 |
0,09 |
0,05 |
|
ком или другими специальными загру |
2 |
0,17 |
0,14 |
0,09 |
зочными устройствами) |
2,5 |
0,26 |
0,21 |
0,14 |
|
3,15 |
0,41 |
0,33 |
0,21 |
|
4 |
0 ,6 8 |
0,55 |
0,35 |
ДЛр |
5 |
1,05 |
0,85 |
0,54 |
— |
0,04 |
0,032 |
0 ,0 2 |
Характер проскальзывания груза |
на |
А\ш |
л г |
|
|||||||
роликоопорах |
конвейера: |
|
*—■ |
|
I / |
|
|||||
1, II, |
III — положения |
кусков груза |
до |
|
|
|
|
||||
перемещения |
ленты; |
I, |
IV, |
///' — то |
же, |
|
|
|
|
||
после |
перемещения |
ленты |
на 220 м |
вид А |
|
|
|||||
|
|
|
|
|
|
|
|
|
|
||
|
|
|
|
|
|
|
|
(подернут о) |
|
||
|
|
|
|
|
|
|
|
'Яа®*^ Ш ' |
j |
||
|
|
|
|
|
|
|
|
|
О |
Перемещение |
|
|
|
|
|
|
|
|
|
Т/ |
О©# |
|
|
|
|
РИС. |
5.18. |
|
|
0 |
А |
|
|||
Зависимости |
ресурса |
рабочей |
об |
|
|
|
d |
||||
кладки |
от распределения |
ее износа |
" |
|
|
||||||
на роликоопорах |
и |
в |
месте погрузки |
|
|
||||||
|
|
и |
|||||||||
|
|
|
|
|
|
|
|
100 |
5 0 0 |
где Том — ресурс ленты по обкладке, мес; /м —число часов
239
работы цеха в месяц; /Сд— коэффициент дополнительных по вреждений ленты; /Сд=1,25— хорошие условия эксплуатации ленты (отсутствуют направляющие борта, дефлекторные ролики, сбрасыватели, очистные устройства); /Сд= 1 , 6 — средние условия (присутствуют перечисленные выше условия); /Сд = 2 — тяжелые условия (передвижные забойные конвейеры).
Представляют интерес данные о количественном распределе нии износа рабочей обкладки на роликоопорах и в месте за грузки и степени влияния такого распределения на ресурс об кладки. Экспериментальные данные о линейном износе рабочих обкладок за неделю (115 ч работы) на двух последовательно установленных конвейерах № 1 и № 2 различной длины Ба лаклавского РУ им. А. М. Горького позволяют рассчитать рас пределение износа. Значения расчетных параметров и распреде ление износа обкладки на роликоопорах и в месте загрузки при ведены ниже.
Показатели |
1, м |
N |
М |
h, мкм |
A/in, мкм |
|
Конвейер: |
|
|
|
|
|
|
№ 1 |
1,2 |
1650 |
3 4 6 5 0 0 |
20 |
4 ,5 Х |
10—3 |
№ 2 |
0 ,6 |
2 7 6 0 |
6 0 9 2 9 0 |
83 |
4 ,5 Х |
10“ 3 |
|
|
|
|
|
П р о д о л ж е н и е |
|
Показатели |
A/ip, мкм |
Лп. |
hp, |
^п* |
/1р, |
|
Конвейер: |
|
мкм |
мкм |
0/ |
% |
|
|
|
12,6 |
|
|
|
|
№ 1 |
3 ,6 - ю - 6 |
7 ,4 |
3 7 |
6 3 |
|
|
№ 2 |
3 , 6 - 1 0 - 5 |
61 |
22 |
73 |
2 7 |
|
Врасчетах было принято, что за один оборот ленты разность
ввеличинах линейного износа рабочей обкладки на конвейерах № 1 и № 2 приходится на разность чисел роликоопор (или про ходов участков ленты над роликоопорами за один оборот ленты) на этих конвейерах.
Линейный износ рабочей обкладки в месте загрузки на два порядка (123 раза) больше, чем на одной роликоопоре, что со ответствует отношению проскальзывания груза в месте загрузки
ина одной роликоопоре. Полученные экспериментальные данные
позволяют выявить закономерности износа рабочих обкладок на конвейерах. Анализ зависимости (рис. 5.18) показывает, что существенное влияние длины конвейера на ресурс рабочей об кладки (ленты) прямо связано с характером распределения из носа обкладки на роликоопорах и в месте загрузки. Абсолютный износ рабочей обкладки на роликоопорах практически не зави сит от длины конвейера. С увеличением длины конвейера умень шается число циклов движения ленты и, соответственно, абсо лютный износ обкладки в месте загрузки. Доля износа ленты в месте загрузки также падает, так как износ на роликоопорах по абсолютной величине не изменяется — значит, возрастает в долевом отношении износ рабочей обкладки на роликоопорах.
240
|
|
Толщина рабочей обкладки при длине конвейера, |
м |
|||||
обкладки, мес |
100 |
200 |
300 |
400 |
500 |
600 |
700 |
900 и |
|
более |
|||||||
6 |
1 |
0,5 |
0,5 |
0,5 |
0,5 |
0,5 |
0,5 |
0,5 |
12 |
1,5 |
1,0 |
1,0 |
1,0 |
1,0 |
1,0 |
1,0 |
1,0 |
18 |
2,5 |
2,0 |
1,5 |
1,5 |
1,0 |
1,0 |
1,0 |
1,0 |
24 |
3,0 |
2,5 |
2,0 |
2,5 |
1,5 |
1,5 |
1,5 |
1,5 |
36 |
5,0 |
4,0 |
3,5 |
3,0 |
2,5 |
2,0 |
2,0 |
2,0 |
48 |
7,0 |
6,0 |
5,0 |
4,5 |
4,0 |
4,0 |
4,0 |
3,5 |
72 |
10 |
7,0 |
6,0 |
5,5 |
5,0 |
5,0 |
4,5 |
4,0 |
При этом общий износ ленты асимптотически падает, прибли жаясь к определенной величине.
Таким образом, выявлена степень эффективности увеличения длины конвейеров как отдельных звеньев транспортной цепи. На конвейерах длиной 25—50 м доля износа рабочей обкладки на роликоопорах составляет 10—15%, в месте загрузки 85— 90%, а на конвейерах длиной 200—300 м соответственно 60— 65 % и 35—40 %. На конвейерах длиной 800 м износ на ролико опорах является уже доминирующим и достигает 85%. Для конвейеров малой и средней длины (до 400 м) увеличение длины конвейера весьма положительно влияет на ресурс обкладки. Так, с увеличением длины конвейера от 50 до 400 м ( 8 раз) ре сурс рабочей обкладки возрастает в 3 раза. Дальнейшее уве личение длины конвейера несущественно влияет на ресурс ра бочей обкладки. Существенное влияние на ресурс рабочей об кладки ленты оказывает также скорость движения ленты. Оно проявляется через число циклов движения ленты (число прохо дов ленты в месте загрузки и на роликоопорах) за время ра боты конвейера, а также величину проскальзывания груза.
Иногда целесообразно по запланированному ресурсу ленты до восстановительного ремонта определять требуемую толщину
рабочей обкладки: |
|
б = 1800Гом^„/Сд ( ^ - + |
• |
По заданным ресурсу рабочей обкладки и длине конвейера толщина рабочей обкладки для сильноистирающих грузов опре деляется по табл. 5.11.
Пример расчета ресурса ленты по рабочей обкладке. Исходные данные:
конвейер |
стационарный с роликовым ставом; L= 200 м, /=1,2 м; и = 2,5 |
м/с; |
||||
i M= 500 ч |
(при трехсменной работе цеха), загрузочный узел — прямолинейный |
|||||
наклонный |
лоток, |
транспортируемый груз — дробленая железная |
руда |
|||
(группы А) |
крупностью 0—160 мм; условия эксплуатации конвейера — хоро |
|||||
шие (/Суд= 1,25). |
На конвейер согласно тяговому расчету была навешена |
|||||
лента ТА-100 шириной 1200 |
мм с обкладкой, имеющей толщину |
6 = 4 |
мм. |
|||
По табл. 5.10 |
находим |
Д/?п = 1,05 • 10~ 6 мм и A/iP = 0,04 • 10_в |
мм. |
Под- |
ставляя известные данные в формулу (5.14), определяем ресурс (срок службы) ленты по обкладке:
б
18ОО0/м/< д (_ ^ + - ^ ) |
|
4 |
= 37 мес |
|
Износ нерабочей обкладки. Состояние нерабочей обкладки, как правило, не влияет на общий ресурс ленты. В отличие от рабочей обкладки усталостный износ поверхностного слоя резины нерабочей обкладки не сопровождается активно действую щими фрикционным и ударным видам разрушения. В этой связи толщина нерабочей обкладки в применяемых лентах значи тельно меньше толщины рабочей обкладки. Однако такой под ход к выбору толщины нерабочей обкладки не всегда оправдан. На мощных конвейерах резко возрастают касательные напря жения, связанные с передачей приводными барабанами значи тельных тяговых усилий ленте через нерабочую обкладку. При недостаточной ее толщине и определенных упруго-прочностных характеристиках после некоторого количества воздействий про исходит раздир тонкого слоя резины с последующим отрывом. Возможны также срывы нерабочей обкладки в зоне связи с кар касом.
Отмеченные виды износа нерабочей обкладки, в частности, имеют место на мощных конвейерах с параметрами: длина кон вейера 400—2000 м; ширина ленты 1400—2000 мм; скорость движения ленты 3,15—5,24 м/с; число прокладок в ленте 5—10; прочность лент на капроновой, анидной и нейлоновой основах 24—32 кН/см, транспортируемый груз — железная руда крупно стью 350—400 мм, угол наклона конвейера 0—16° После 9— 2 1 мес эксплуатации лент на этих конвейерах наблюдались от рывы нерабочей обкладки на площади, равной 15—25 % ее по верхности (по данным ИГД Минчермета СССР).
Интенсивность износа нерабочей обкладки возрастает с по вышением мощности и, соответственно, длины и угла наклона конвейера. Отсюда следует, что отношение толщины рабочей и нерабочей обкладок должно уменьшаться с увеличением длины конвейера. Более стойки к срывам нерабочей обкладки ленты монолитной конструкции с применением многоосновных тка ней [41].
Износ каркаса. Для каркаса ленты наиболее характерны сле дующие виды износа: ударное разрушение прокладок по основе и утку при транспортировании крупнокусковых грузов; устало стный износ, связанный с потерей прокладками упруго-прочно стных характеристик в результате многократных растяжений на барабанах, роликоопорах; расслоение прокладок из-за действия
242
значительных касательных напряжений на барабанах,^особенно в лентах -с большим -числом Прокладок и толщиной обклйдоК; химический (старение) износ из-за проникновения’ вгчиатериал прокладок воды, кислот, щелочей и др. На ленточных кон&Ьйерах предприятий черной металлургии 1 0 % лент снимаются с эксплуатации из-за ударного износа рабочих обкладок и кар каса, преимущественно в местах загрузки. Однако при повышен ных скоростях движения ленты (более 3 м/с) возрастает по движность отдельных кусков груза на роликоопорах конвейера. Динамические воздействия на роликоопорах могут быть*' значи тельны и решающими в ударном разрушении прокладок и дол говечности ленты. Ресурс ленты от ударного разрушения опре деляется на основе статистических наблюдений.
Ресурс лент по усталостному износу каркаса пропорциона лен. числу циклов нагружения ленты нормальными растягиваю щими, касательными и динамическими растягивающими уси лиями. По данным ИГД Минчермета СССР, наиболее .веро ятное число циклов растяжения каркаса на барабанах состав ляет 1,3-10е. На горнорудных предприятиях такое число цик лов нагружения испытывает только 2 % снятых с эксплуата ции лент, срок службы которых составляет более 4 лет. Боль шое число циклов нагружения на каркас до его разрушения объясняется высоким значением запаса прочности прокладок, составляющим по техническим требованиям 9—12, а в реаль ных условиях обычно 20—25 и достигающих весьма больших величин. Следует, однако, иметь в виду, что высокие значения запаса прочности каркаса устанавливаются с учетом действия динамических и статических нагрузок, неравномерности рас пределения напряжений в прокладках, стыковых соединений, формообразования для обеспечения данной производитель ности.
Многократные касательные смещения слоев ленты относи тельно друг друга приводят к расслоению прокладок, образо ванию внутренних гофр, разрыву прокладок на отдельных уча стках и в конечном счете к снижению прочности ленты.
Химический износ каркаса связан с нарушением целостно сти обкладок. Например, проникновение агрессивной влаги под обкладки резинотросовых лент, эксплуатируемых на шахтах, приводит к ускоренной коррозии и порывам тросов. Коррозия •тросов — одна из основных причин износа резинотросовых лент на шахтах.
Срок службы лент. В практических расчетах срок службы
.ленты определяется как ресурс ленты с учетом режима работы конвейера во времени. Рассмотренные особенности износа и ре сурса конвейерных лент и отдельных ее элементов позволяют юудить о сложности данной проблемы. Абсолютный износ ленты не может быть выражен через определенную физическую вели чину. Во всех случаях эксплуатации ленты присутствуют ком поненты фрикционного, усталостного, ударного и химического
видов износа. Около 100 параметрических, эксплуатационных и организационных факторов прямо или косвенно оказывают оп ределенное влияние на ресурс ленты.
Ресурс изделия определяется календарной продолжитель ностью его эксплуатации от ее начала или от среднего или капитального ремонта до наступления предельного состояния. Предельное состояние характеризуется моментом, предше ствующим при дальнейшей эксплуатации нарушению правил эксплуатации конвейера, «уходу» заданных параметров за установленные пределы. Целесообразно в общем случае в ка честве критериев оценки предельного состояния ленты выби рать не величину того или иного вида износа, а следствие из носа— потерю лентой грузонесущей и тяговой способности, возникновение по внешнему состоянию ленты опасности нару шения правил эксплуатации. Ресурс ленты может быть пред ставлен как календарная продолжительность эксплуатации ленты до предельного состояния, при котором лента теряет необходимую тяговую и грузонесущую способность из-за истирания и разрушения обкладок, расслоения и разрушения прокладок, частых перестыковок. Кроме того, лента по внеш ним признакам (из-за локальных разрушений обкладок, бор тов каркаса) не соответствует правилам техники безопасно сти. Очевидно, что расчетные значения ресурса лент при ис пользовании той или иной методики весьма приближенны. Необходимо стремиться к тому, чтобы обеспечивалось наибо лее рациональное использование ресурса ленты на основе пе редового опыта ее эксплуатации.
Известны методики расчета ресурса ленты, базирующиеся на эмпирических, аналитических и статистических методах рас чета. Стремление некоторых исследователей учитывать в пред лагаемых расчетах возможно большее количество факторов, оказывающих свое влияние на износ ленты, нельзя считать пра вомочным. Ибо из всей совокупности факторов должны выби раться те, которые решающим образом способны изменять ре сурс ленты, степень влияния которых очевидна.
Анализ полученных данных и известных работ показывает, что основными факторами, определяющими срок службы ленты, являются вид и крупность транспортируемого материала, тип и скорость движения ленты, режим работы во времени и длина конвейера, наличие восстановительного ремонта. Режим работы конвейера во времени оказывает пропорциональное влияние на срок службы ленты. Чем больше во времени эксплуатируется конвейер, тем, соответственно, меньше календарный срок службы ленты. Учет влияния вида и крупности материала, типа ленты осуществляется в большинстве случаев на основе средне статистических данных срока службы лент. Последние устанав
ливаются для каждого вида |
материала с учетом |
его крупности |
|
и каждого типа ленты. Эти |
факторы |
и восстановительный ре |
|
монт при прочих равных условиях |
оказывают |
существенное |
244
влияние на срок службы ленты. Длина конвейера нелинейно влияет на долговечность ленты. Зависимость срока службы ленты от длины конвейера имеет, как установлено, асимптоту, связанную с тем, что доля износа ленты в местах сосредоточен ных нагрузок (от загрузочных устройств, привода и др.) с уве личением длины конвейеров падает, а на линейной части возра стает, не изменяясь существенно по абсолютной величине. В из вестных методиках определения срока службы ленты влияние скорости движения ленты учитывается как функция продолжи тельности оборота ленты или производительности конвейера. С увеличением скорости ленты пропорционально возрастает ко личество различного рода нагрузок на ленту. При повышенных скоростях движения ленты (более 2 м/с) это возрастание может быть более активным.
С учетом изложенного срок службы ленты предлагается оп ределять по формуле
Г = 1//у,
где Т — календарный срок службы ленты до восстановительногоремонта, мес; / у — удельный износ ленты, относ, един./мес.
/у = /п + /р, |
(5.15)* |
где 1П— удельный износ ленты при прохождении |
места за |
грузки, уплотняющих бортов, барабанов, устройства очистки,, сбрасывателя и других узлов, однократно воздействующих на ленту за один ее оборот; /р — удельный износ ленты на роликоопорах, многократно воздействующих на ленту за один ее обо рот;
/п = А/п^ м, |
(5.16> |
где Д/п — удельный износ ленты на указанных участках за один оборот ленты, относ, един.; NM— число оборотов ленты в месяц
/ р= Д /рМм, |
(5.17> |
где Д/р — удельный износ ленты на роликоопорах рабочей ветви ленты, относ, един.; Мм— число проходов ленты над роликоопо-
рами рабочей ветви в месяц. |
(5.10), (5.12) |
и (5.14)/ |
|
На основе формул |
(5.15) —(5.17), |
||
можно записать: |
|
|
|
Т = ---------------- |
!---------------- |
, |
(5.18) |
lM0rtcK p(-^S- + -^ £ -)
где /с — стандартное число часов работы цеха в месяц (напри мер, соответствующее трехсменному режиму работы цеха по 7 ч в смену), ч; /Ср — коэффициент режима работы цеха во вре мени, характеризующий отношение фактической продолжитель ности работы цеха к стандартному.
Формула. (5.1&) в функциональном-, отношении аналогична формуле (5Л4) для расчета ресурса»ленты по рабочей.обкладке. В обоих случаях .раздельно учитывается -износ ленды-в узлах конвейера, однократно воздействующих, на ленту за один.ее обо рот, и на ролвкоопорах; одинаково, учитываются.число оборотов ленты и режим работы конвейера во времени,, определяющие число изнашивающих воздействий на ленту в процессе, ее экс плуатации.
Согласно отечественным и зарубежным статистическим дан ным срок службы ленты, в общем случае пропорционален ре сурсу рабочей обкладки.' Поэтому выражение (5Л8 ) -можно за писать в виде
___________ 1__________ _ |
|
(5.19) |
||
Т |
|
|
|
|
№0vtcKpKo ( - ^ L + - ^ 7 e-) |
|
|
||
где Ко — коэффициент, характеризующий |
отношение |
износа |
||
ленты в целом к износу обкладки. |
|
и |
под |
|
После ввода коэффициента пропорциональности Кп |
||||
становки среднестатистических |
значений |
A/in= 0,25 • 10~ 6 |
мм и |
|
A/ip= 0,032 • 10“ 6 мм можно записать |
|
|
|
|
7 = |
КпТст |
|
|
(5.20) |
|
|
|
||
где 7СТ— среднестатистический |
календарный срок |
службы |
ленты при стандартном режиме работы цеха. Среднестатистиче ский календарный срок службы ленты показывает, какое значе ние 7ст имел бы каждый конвейер (заданной области), если бы сроки службы лент были одинаковы, а суммарное значение — такое же, как и фактическое при неусредненных значениях.
Значение коэффициента Кп можно определить, если принять 7 = 7СТ. В этом случае
Подставляя в эту формулу среднестатистические значения
параметров 0=1,6 |
м/с, /СР=1, L = 50 м и / = 1,2 м, получим: |
|
|
|
= 5,39. |
Теперь формулу |
(5.20) можно записать в виде |
|
|
j |
_____ 5,397 СТ_______ |
0КР(-^ -+ 2 ,6 7 )
или
•(-т+’-О
где Гст.р — среднестатистический |
календарный срок службы |
ленты с учетом режима работы |
цеха во времени; С — коэффи |
циент, учитывающий крупность транспортируемого груза, тем пературу окружающей среды, вторичное использование ленты;
С= СГСТС,гЬтЬр,
где Сг— коэффициент, учитывающий крупность транспорти руемого груза: для груза крупностью до —150 мм Сг=1; для груза крупностью +150 мм Сг=0,83; Ст— коэффициент, учиты вающий температуру груза и окружающего воздуха: для грузов и окружающего воздуха с температурой от —60 до 60 °С Ст= 1 (ленты типа 2,2М); для грузов и окружающего воздуха с тем
пературой до |
100 °С |
Ст= 0,5 (ленты типа 2 Т); |
для |
грузов и |
|
окружающего |
воздуха с температурой |
до 2 0 0 |
°С |
Ст= 0 , 2 2 |
|
(ленты типа |
2ТП); |
Ср— коэффициент, |
учитывающий |
вторич- |
ность использования ленты: для лент, вторично не используе мых, СР= 1 ; для лент, вторично используемых, Ср=1,1.
Значения Гст. р для различных видов материалов зависят от Кр.
Значения коэффициента режима работы цеха во времени при 7-часовой рабочей смене будут: при числе рабочих дней 265 и двухсменной работе /Ср = 0,58, при трехсменной работе /СР=0,87; при числе рабочих дней 305 и двухсменной работе /СР = 0,67, при трехсменной /СР= 1 ,0 .
Значения среднестатистического календарного срока службы
конвейерных |
лент ГСт. р с учетом режима работы цеха во вре |
мени Кр при |
7 -часовой смене приведены в табл. 5 .1 2 . |
Расчетные значения С для различных условий эксплуатации ленты приведены в табл. 5.13.
В общем случае значение коэффициента режима работы цеха во времени можно определить по формуле
П\Пг/7з |
(5 2 2 ) |
|
6405 |
||
|
где П\ — число часов работы цеха в смену; Я г— число смен ра
боты |
цеха (предприятия) в сутки; |
|
Я 3 — число рабочих дней |
цеха |
(предприятия) в год. |
|
|
Для Кр, определяемого из соотношения (5.22), Т рассчиты |
|||
вается по формуле |
|
|
|
|
5, 39Тс т . р |
С |
(5.23) |
|
|
|
где Гст.р принимается по таблице 5.15 для /СР=1.
|
|
|
|
Тст. р <мес) при Кр |
|
|
Транспортируемый груз |
0.58 |
0.67 |
0.87 |
1.0 |
||
|
|
|
||||
Асбест |
|
|
60,7 |
52,5 |
40,5 |
35,2 |
Глина |
|
|
71,4 |
61,8 |
47,6 |
41,4 |
Гравий |
песок (2 1) |
|
58,9 |
51 |
39,3 |
34,2 |
Гравий + |
|
69,5 |
60,1 |
46,3 |
40,3 |
|
Графит |
|
|
52,2 |
45,2 |
34,8 |
30,3 |
Доломит |
|
|
42,1 |
36,4 |
28,1 |
24,4 |
Известняк |
|
|
50,7 |
43,9 |
33,8 |
22,4 |
Каолин |
|
|
61,9 |
54,8 |
41,3 |
35,9 |
Кварцит |
|
|
44,8 |
38,8 |
29,9 |
26 |
Клинкер |
|
|
63,8 |
55,2 |
42,5 |
37 |
Кокс |
|
|
77,5 |
67,2 |
51,9 |
45,1 |
Магнезит |
|
|
58,5 |
50,6 |
39,1 |
34 |
Мел |
|
|
95,7 |
82,8 |
63,8 |
55,5 |
Мергель |
|
|
63,8 |
55,2 |
42,5 |
37 |
Песок |
|
|
90,3 |
78,2 |
60,2 |
52,4 |
Порода вскрышная: |
|
82,7 |
71,5 |
55,3 |
48,1 |
|
мягкая |
|
|
||||
скальная |
|
56,7 |
49,1 |
37,8 |
32,9 |
|
Руда: |
|
|
95,4 |
82,7 |
63,8 |
55,5 |
алюминиевая |
|
|||||
железная |
|
57,6 |
49,9 |
38,5 |
— |
|
марганцевая |
|
54,2 |
46,9 |
36,2 |
31,5 |
|
медная |
|
|
63,6 |
55 |
42,5 |
37 |
свинцовая |
|
44,5 |
38,6 |
29,8 |
25,9 |
|
сурьмяная |
|
57,3 |
49,6 |
38,3 |
33,3 |
|
хромовая |
|
50,9 |
44,1 |
' 34 |
29,6 |
|
цинковая |
|
47,6 |
41,2 |
31,9 |
27,7 |
|
•Сера |
|
|
75,7 |
65,5 |
50,6 |
44 |
Уголь |
|
|
96 |
83,4 |
64,4 |
56 |
Фосфогипс |
|
|
85,8 |
74,3 |
57,4 |
49,9 |
Цемент |
|
|
50,2 |
43,4 |
33,4 |
29,1 |
Шлак |
|
|
50,9 |
44 |
34 |
29,6 |
Щебень |
|
|
47,6 |
41,2 |
31,7 |
27,6 |
|
|
|
|
|
ТАБЛИЦА 5.13 |
|
|
С т = |
1 |
с.г = |
0.5 |
ст, = |
0,22 |
ср |
Сг=1 |
С г = 0.83 |
сг = 1 |
С г = 0.83 |
с г = 1 |
с г = 0.83 |
|
||||||
1 |
1 |
0,83 |
0,50 |
0,41 |
0,2 2 |
0,18 |
1,1 |
1,1 |
0,91 |
0,55 |
0,46 |
0,24 |
0,2 0 |
Для резервных конвейеров коэффициент режима работы цеха во времени принимается равным Ар/2 . При малой загрузке кон вейеров во времени и, соответственно, малых значениях Кр уста навливается предельное значение календарного срока службы ленты, равное 144 месяца (12 лет).
Таким образом, в основу расчета календарного срока службы ленты может быть положено знание среднестатистического срока службы ленты в конкретных условиях, в котором учиты ваются вид, крупность и температура транспортируемого мате риала, температура окружающего воздуха, наличие восстано вительного ремонта. Учет других параметров —длины и режима работы конвейера, скорости движения ленты позволяет анали тически устанавливать степень смещения календарного срока службы ленты в конкретных условиях от среднестатистического значения. Сочетание аналитического (с использованием экспе риментальных данных) и статистического методов расчетов спо собствует уточнению функциональной связи календарного срока службы ленты с основными эксплуатационными факторами. Сравнительно небольшое количество учитываемых в расчете факторов позволяет упростить расчет и приблизить расчетные данные к реальным в основном диапазоне изменения парамет ров эксплуатации конвейеров. Скорость движения ленты и ре жим работы конвейера во времени пропорционально влияют на срок службы ленты в сторону уменьшения, а длина конвейера — нелинейно в сторону увеличения. Так, при увеличении длины конвейера с 15 до 225 м (в 15 раз) календарный срок службы ленты возрастает нелинейно только в 2 , 6 раза. Дальнейшее увеличение длины конвейера не приводит к существенному воз растанию срока службы ленты. Наиболее активная область влия ния длины на срок службы находится в пределах 250 м. Учиты вая данные статистического распределения ленточных конвейе
ров по длине, можно |
отметить значимость |
данного параметра |
в расчетах срока службы ленты. |
факторов на срок |
|
Влияние других не |
учтенных в расчете |
службы ленты (например, загрузки конвейера по производи тельности, профилактического ремонта, культуры обслужива ния, качества изготовления ленты и др.) отражено в среднеста тистическом сроке службы ленты, являющемся комплексным параметром. Этот параметр рекомендуется уточнять по мере из менения работоспособности серийно выпускаемых конвейерных лент, применяемого оборудования и условий эксплуатации кон вейеров. В некоторых случаях, не предусмотренных расчетом,, устанавливаются индивидуальные среднестатистические сроки: службы лент.
Обычно лента заменяется новой не полностью, а отдельными^ отрезками в разное время. Тогда срок службы ленты определя ется как средневзвешенная величина:
|
|
rp |
l\T\ -f- /2 ^ 2 ~f~ |
* * * + 1пТп |
|
|
ст,р" |
/ 1 + / 2 + |
+ /я |
где |
/1, /2, ...» In — длина отдельных заменяемых отрезков ленты; |
|||
Ти |
Т2, |
7 П— сроки службы отдельных заменяемых отрезков |
||
ленты. |
|
|
|
При расчетах индивидуальных сроков службы ленты не дол жен учитываться их преждевременный или аварийный износ, вызванный нарушением правил эксплуатации, транспортировки
ихранения.
5.3.НОРМИРОВАНИЕ РАСХОДА КОНВЕЙЕРНЫХ ЛЕНТ
ИОПРЕДЕЛЕНИЕ ПОТРЕБНОСТИ В НИХ
Нормирование расхода лент. Норма расхода конвейерных лент —это установленный расчетом и планом допустимый мак симальный расход ленты на содержание в рабочем состоянии одного ленточного конвейера при заданных параметрах и ре жиме эксплуатации. При суммировании расхода ленты на от дельных конвейерах норма может быть рассчитана для пред приятия, главка, министерства в целом или на единицу выпус каемой продукции. Нормы расхода лент должны обеспечивать наиболее рациональное и экономичное использование ресурсов по ленте на производстве. В основу определения норм расхода лент положен расчет календарных сроков их службы и соответ ствующих значений коэффициентов сменяемости, устанавливаю щих долю расхода ленты в год от полной ее навески на кон вейере. Норма расхода ленты прямо пропорциональна величине навески ленты и обратно пропорциональна календарному сроку ее службы. Календарный срок службы ленты при расчете норм расхода принимается как нормативный. Порядок определения норм расхода ленты следующий. Устанавливаются в соответ ствии с ГОСТ 20—76 тип ленты и число прокладок согласно тя говому расчету. Норма расхода ленты в год для конкретного конвейера определяется по формуле
Н = МКс |
(5.24) |
где Н — норма расхода ленты, м2; М — навеска (количество на вешенной) ленты с учетом огибания барабанов и стыковки, м2; Кс — коэффициент сменяемости ленты;
М = 2,03 • 10-3LB + Mr, |
(5.25) |
где В — ширина ленты, мм; Мт— навеска ленты на сбрасываю. щей тележке, м2, значения которой приведены ниже.
Ширина ленты В , мм |
500 |
650 |
800 |
1000 |
1200 |
1400 |
Навеска ленты Мт, м2 |
1,9 |
2,6 |
4,0 |
5,5 |
7,8 |
9,8 |
Ширина |
ленты В, мм |
1600 |
1800 |
Навеска |
ленты Мт, м2 |
12,8 |
16,2J |
Продолжение
2000 |
2200 |
2400 |
20 |
25 |
31 |
Кс=12/Т |
(5.26) |
Календарный (нормативный) срок службы ленты определиется по формуле (5.21) или (5.23).
250
Норма расхода ленты в прокладках
где Н\ — норма расхода ленты, м2 прокладок; i — число про кладок.
Пример расчета нормы расхода ленты. Расчетные данные: режим ра боты цеха (число часов работы в смену Пj—7, число смен работы в сутки
П2—2, число рабочих дней в году Я3—265; |
транспортируемый груз (щебень |
||||||||
крупностью 300 мм, температура груза и |
окружающего воздуха — в |
пре |
|||||||
делах от —45 до 60 °С); длина конвейера |
L = 50 |
м; |
ширина |
800 мм, |
ско |
||||
рость движения ленты 1,6 м/с, |
число прокладок — 4. |
Конвейер |
имеет сбра |
||||||
сывающую тележку. Учитывается вторичное использование ленты. |
на |
||||||||
Определяем навеску ленты М согласно |
формуле |
(5.25) |
и |
данным |
|||||
стр. 250: М = 2,03-50-0,8 + 4=85,6 м2. |
|
|
|
|
|
|
|
||
Определяем |
коэффициент режима работы (/СР) цеха по данным на стр- |
||||||||
247 или формуле |
(5.22), находим /СР = 0,58. |
Тогда среднестатистический кален |
|||||||
дарный срок службы (7’ст. Р) |
ленты по |
табл. 5.12 будет 7’Ст .Р=47,6 |
мес. |
||||||
Устанавливаем значение |
коэффициента |
С, |
учитывающего |
крупность |
|||||
груза (Сг), температуру ее и |
окружающего воздуха |
(Ст), |
вторичное |
ис |
пользование ленты (Ср). В соответствии с расчетными данными значения этих коэффициентов Сг=0,83; Ст = 1; СР = 1,1. По приведенным на стр. 248 данным значение коэффициента С составляет 0,91.
Находим календарный (нормативный) срок службы ленты согласно фор
муле (5.21): |
|
|
|
|
|
Т _____5-” |
4 7 ' 6 0 ' 91-------- 43,4 |
« с . |
|
|
'. 6 ( - i - + 2 . 6 7) |
|
|
|
Определяем |
коэффициент |
сменяемости ленты |
по формуле (5.26): |
/Сс= |
= 12/43,4= 0,28. |
|
|
|
(5.27): |
Устанавливаем нормы расхода ленты согласно формулам (5.24) и |
||||
Н=85,6 • 0,28=24 |
м2; Hi=85,6 • 0,28 • 4=96 м2 прокладок. |
|
Расчет потребности в ленте. Расчет норм расхода ленты к потребности на предприятии составляется ежегодно. При этом: учитываются все ленточные конвейеры, находящиеся в эксплуа тации в текущем году, изменение в составе оборудования, пере ходящий запас ленты и ее остаток. Средневзвешенные значения календарного срока службы (Гп) и коэффициента сменяемости ленты по предприятию (/Сс.п) определяются по формулам:
7п=12Мп/#п,
Кс.п = 1 2 /Г п ,
где МП— суммарная навеска ленты на предприятии, м2; Яп — суммарный расход ленты на предприятии за 1 год, м2.
Пример расчета норм расхода лент и потребности в них. Расчетные дан ные для определения норм расхода лент и потребности в них на предприятия (число рабочих дней в году 265, двухсменная работа, коэффициент режима работы цехов /СР = 0,58) приведены в табл. 5.14. Транспортируемый груз — гравий крупностью 80 мм при температуре —5 ... 4-30 °С, ширина ленты конвейера £ = 1 0 0 0 мм.
Из табл. 5.14 имеем следующее. Навеска ленты на начало года на дей ствующем оборудовании 493 м2; изменение прироста навески ленты за год. (например, на 1 июля расчетного года) составило 70 м2, в том числе: за счет поступления конвейеров собственного производства 50 м2; за счет по ступления конвейеров от предприятий 40 м2. Списание вышедших из строя
Порядковый номер конвейера |
Длина конвейе ра. L, м |
Скорость движе ния ленты и.мс |
Вид ленты |
1 |
21,3 |
1,6 |
2 |
2 |
40,5 |
1,6 |
2 |
3 |
42 |
1,6 |
2 |
4 |
109 |
1,6 |
2М |
5 |
17 |
1,6 |
2 |
6 |
13 |
1,6 |
2 |
а
н
X а>
ч
со X
Uм
СОS
* ‘
43,2
82,2
85,3
221,3
34,5
26,4
Календарный срок службы ленты Т, мес |
Коэффициент сменяемости ленты /С |
Нормы расхода ленты в год Н (по навеске на начало 01. 01 расчетного го да). м- |
50,6 |
0,23 |
9,9 |
61,9 |
0,19 |
16,6 |
62,3 |
0,19 |
16,2 |
73,0 |
0,16 |
35,4 |
46,2 |
0,25 |
8,6 |
40,7 |
0,29 |
7,6 |
конвейеров в пересчете на ленту составило 20 м2. Средневзвешенный ка
лендарный срок службы ленты (Та) на предприятии
Тп |
12-493 = 63,7 мес. |
|
94,3 |
Средневзвешенный коэффициент сменяемости ленты Кс.п на предприятии
7Сс. п = 12/63,7 = 0,19.
Потребность в расходе ленты (производственно-эксплуатационная)
^493 + |
0,19 + 50 — 20 = 130,3 мг. |
В том числе: |
|
на замену изношенной ленты |
|
(493 + |
0,19 = 100,3 м*; |
на комплектацию конвейеров собственного производства
50 — 20 = 30 м2;
на переходящий запас (20 дней) |
|
20-130,3 |
? |
365 |
|
Потребность с переходящим запасом |
130,3+7,1 = 137,4 м2. |
Остаток на начало года —20 м2.
Итого потребность (фонд) составит 137,4—20=117,4 м2.
При этом указывается потребность в ленте по виду, ширине и количе ству прокладок.
5.4. ИСПЫТАНИЯ КОНВЕЙЕРНЫХ ЛЕНТ. МЕРОПРИЯТИЯ ПО ПОВЫШЕНИЮ ИХ ИЗНОСОСТОЙКОСТИ
Классификация испытаний лент. В настоящее время отечест венной промышленностью выпускается большой ассортимент конвейерных лент, отличающихся параметрическими, физико-
механическими и эксплуатационными характеристиками. Значи тельная роль в повышении ресурса лент отводится испытаниям. Целью испытаний является обеспечение оптимального выбора лент для конкретных условий эксплуатации, проверка и улуч шение качества лент в процессе их изготовления. К показателям качества, влияющим на ресурс ленты, следует отнести: упруго прочностные свойства лент и ее отдельных элементов (обкладок, прокладок и др.); деформативные (способность к образованию желобчатости); стойкость к фрикционно-усталостному, абразив ному, усталостному, химическому и ударному видам износа. Та ким образом, виды испытаний лент можно классифицировать по воспроизводимому в процессе испытаний характеру разрушения. Практическая ценность получаемых при этом результатов зави сит от того, в какой мере эти испытания моделируют характер ные виды нагрузок на ленту. В зависимости от степени слож ности воспроизводимых испытаниями нагрузок на ленты разли чают четыре категории испытаний. Испытания первой категории ставят своей целью изучение закономерностей изменения ка кого-либо определенного свойства (показателя) ленты, например модуля упругости тканевых прокладок и обкладок, прочно сти на разрыв прокладок и т. д. Для лент характерна опреде ленная взаимосвязь между ее физико-механическими показате лями. Это усложняет работу по оптимизации характеристик ленты. Поэтому при испытаниях выбираются только основные показатели и изучаются закономерности влияния их на износ ленты.
Испытания второй категории характеризуются воспроизведе нием определенного вида изнашивания на стенде в строго регла ментированных условиях, например, фрикционно-усталостного или абразивного износа на модели истирающей поверхности при определенном давлении и скорости скольжения. В таких ис пытаниях процесс заданного вида износа исследуется в чистом виде. В испытаниях третьей категории создаются условия для оценки показателей износа на опытной установке с учетом влия ния конструктивных и некоторых эксплуатационных факторов. На опытных установках наилучшим образом сочетаются чи стота стендовых испытаний образцов лент с условиями их ра боты. Перечисленные виды испытаний проводятся в лаборатор ных условиях и поэтому наиболее доступны.
Испытания четвертой категории, проводимые в производ ственных условиях, составляют заключительное звено в системе испытаний, так как позволяют дать комплексную оценку изно состойкости лент и ее элементов в отдельности, определить ка чество ленты как изделия в целом, выявить значимость отдель ных факторов или их сочетания в общем износе.
Каждый из рассмотренных видов испытаний имеет самостоя тельное значение, являясь одновременно отдельным звеном в об щей оценке качества лент. Необходимо стремиться к тому, чтобы все виды испытаний строго соответствовали поставленной цели.
Показатели качества категории и виды испытаний конвейерных лент-приведены в табл. 5.15.
! Испытания обкладок, В соответствии с изложенными пред ставлениями о механизме износа обкладок отмечена решающая роль упруго-прочностных и усталостных характеристик резины (сопротивление разрыву, раздиру, динамической усталости). Из менение этих показателей ведет к заметному изменению сопро тивления износу. Упруго-прочностные показатели обкладок мо гут быть приняты в качестве контрольных при создании износо стойких обкладочных резин. При этом рекомендуется испытания: упруго-прочностных и усталостных характеристик проводить, в динамическом режиме.
Методики (ГОСТы) испытаний обкладок конвейерных ленг отражены в табл. 5.16.
Сопротивления фрикционно-усталостному и абразивному из носу— основные показатели износостойкости обкладок. Они ха рактеризуют потерю объема обкладки в регламентируемых по давлению, скорости и пути скольжения по истирающей поверх ности условиях. Обычно испытания обкладочных резин или обкладок проводят на шлифовальной шкурке, моделирующей в основном абразивный механизм износа, связанный с микроре занием острыми зернами корунда поверхности обкладки. Для испытаний обкладок на сопротивление фрикционно-усталостному износу рекомендуется другая применяемая при испытаниях ре зин истирающая поверхность — металлическая сетка или жест кая пластина с микрометрическими сферическими выступами ня поверхности. При трении обкладки о металлическую сетку про исходит усталостное отделение частиц поверхностного слоя ре зины (фрикционно-усталостный износ) за счет многократного деформирования микрометрических участков резины сфериче скими выступами. Рассмотренные отличия в истирающих по верхностях важны тем, что сопротивление фрикционно-усталост ному износу резин существенно более чувствительно к измене нию рецептуры резиновых смесей (а значит, упруго-прочностные и усталостных характеристик), чем к абразивному износу. Такг зависимость интенсивности износа от давления при истирания резины по шлифовальной шкурке линейна, в то время как по металлической сетке — нелинейна. Нелинейность зависимости износа от давления при фрикционно-усталостном износе объяс няется тем, что с повышением давления возрастают деформиро_ вание и утомление поверхностного слоя резины, а значит, я износ. Интенсивность износа при истирании резины по метал лической сетке повышается с увеличением модуля упругости а при истирании по шлифовальной шкурке уменьшается. Метал! лическая сетка как истирающая поверхность не только воспро. изводит определенный механизм износа, но и обладает рядо^ достоинств: обеспечивает эффективный отвод тепла (таким об разом, уменьшается влияние температуры как побочного фа^_ тора), постоянство истирающей способности, определенности
254
|
Категории и виды испытаний |
|
|
Объект испытаний |
Лабораторные |
|
Производственные |
I (на стенде) |
II (на стенде) |
III (на опытном |
IV (на промышленном |
конвейере) |
конвейере) |
Рабочая и нерабо |
Сопротивление |
|
разрыву, |
Сопротивление |
фрикционно |
То же (см. для II), при |
То же (см. |
для |
II), |
||||||||||
чая обкладки |
раздиру, усталости, относи |
усталостному, |
абразивному, |
взаимодействии |
ленты |
в процессе |
эксплуа |
||||||||||||
|
тельное удлинение при раз |
ударному, |
химическому изно |
с |
транспортируемым |
тации |
|
|
|||||||||||
|
рыве, |
модуль |
упругости, |
су; |
старение, набухание, тер |
грузом, |
элементами |
|
|
|
|
||||||||
|
эластичность |
|
по |
отскоку, |
мостойкость, |
огнестойкость, |
конструкции конвейера |
|
|
|
|
||||||||
|
твердость, |
коэффициент |
морозостойкость |
при |
взаимо |
и средой |
|
|
|
|
|
|
|||||||
|
трения |
|
|
|
|
действии |
ленты с моделями |
|
|
|
|
|
|
|
|
||||
|
|
|
|
|
|
транспортируемого груза, эле |
|
|
|
|
|
|
|
|
|||||
|
|
|
|
|
|
ментами |
конструкции |
кон |
|
|
|
|
|
|
|
|
|||
|
|
|
|
|
|
вейера и средой |
|
|
|
|
|
|
|
|
|
|
|
||
Каркас |
Сопротивление |
разрыву по |
Сопротивление |
усталостному |
То же (см. для II), при |
То |
же (см. для |
II), |
|||||||||||
|
основе и утку (в том числе |
износу, ползучесть, |
набуха |
взаимодействии |
ленты |
в |
процессе |
эксплу |
|||||||||||
|
тросов |
резинотросовых |
ние, |
водопоглощение, |
термо |
с |
транспортируемым |
атации ленты |
|
||||||||||
|
лент), расслоению, раздиру, |
стойкость, |
огнестойкость |
при |
грузом, |
элементами |
|
|
|
|
|||||||||
|
относительное |
|
|
удлинение |
взаимодействии ленты с моде |
конструкции |
конвейера |
|
|
|
|
||||||||
|
при разрыве и рабочей на |
лями транспортируемого |
гру |
и средой |
|
|
|
|
|
|
|||||||||
|
грузке, |
модуль |
упругости |
за, |
элементами |
конструкции |
|
|
|
|
|
|
|
|
конвейера и средой
256
|
|
|
ПРОДОЛЖЕНИЕ ТАБЛ. 5.15 |
|
|
Категории и виды испытаний |
|
||
Объект испытаний |
Лабораторные |
|
Производственные |
|
I (на стенде) |
II (на стенде) |
III (на опытном |
IV (на промышленном |
|
конвейере) |
конвейере) |
|||
|
|
Лента (обкладки + Сопротивление разрыву по каркас) основе и утку (в том числе тросов резинотросовых лент), ударному растяже нию, относительное удлине ние при разрыве и рабочей нагрузке, модуль упруго
сти, гибкость
Сопротивление фрикционно усталостному, абразивному, усталостному, ударно-уста лостному, ударно-пробойному, химическому износу; ползу честь, старение, набухание, электропроводность, термо стойкость, огнестойкость, вос пламеняемость, морозостой кость при взаимодействии ленты с моделями транспорти руемого груза, элементами конструкции конвейера и сре дой
То же (см. для II), при |
То же, в процессе эк |
||
взаимодействии ленты |
сплуатации ленты |
||
с |
транспортируемым |
|
|
грузом, |
элементами |
|
|
конструкции конвейера |
|
||
и |
средой |
|
|
|
|
Испытания |
|
|
||
Показатели |
по ГОСТам, |
по ГОСТ 20-76 |
Рекомендуемые |
|||
применяемым |
||||||
|
|
заводами и НИИ |
на конвейерные |
|
||
|
|
резиновой |
|
ленты |
|
|
|
|
промышленности |
|
|
|
|
Сопротивление истиранию |
426—77 |
на |
426—77 |
на |
426—77 на шли |
|
|
|
шлифовальной |
шлифовальной |
фовальной шкур |
||
|
|
шкурке |
|
шкурке |
|
ке; па металличе |
|
|
|
|
|
|
ской сетке |
Сопротивление разрыву |
270—75 |
|
270—75 |
|
(ГОСТ 3924—74) |
|
|
|
270—75 |
||||
Относительное |
удлине |
270—75 |
|
270—75 |
|
— |
ние при разрыве |
|
|
|
|
|
|
Относительное |
удлине |
268—53 |
|
— |
|
— |
ние при разрыве |
262—79 |
|
|
|
|
|
Сопротивление раздиру |
|
— |
|
— |
||
Модуль упругости |
270—75 |
|
— |
|
10828—75 |
|
|
|
210—75 |
|
— |
|
— |
Эластичность по отскоку |
6950—54 |
|
_ |
|
_ |
|
Твердость |
образова |
253—53 |
|
— |
|
— |
Сопротивление |
9983—74 |
|
— |
|
— |
|
нию трещин при изгибе |
|
|
|
|
10952—75 |
|
Усталостная |
выносли |
|
|
|
|
|
вость |
|
|
|
|
|
|
геометрических параметров и возможность их подбора, чувстви тельность к изменению рецептуры резины.
Испытания резиновых обкладок рекомендуется проводить в три этапа, включающих в себя оптимизацию упруго-прочност ных и усталостной характеристик на основе подбора рецептуры резины, определение сопротивления истиранию на моделях истирающей поверхности и контроль качества на опытном или промышленном конвейерах. Наиболее трудоемок третий этап испытаний из-за сложности проведения измерений износа об кладок.
Радиометрический метод измерения износа обкладок. Сущ ность данного метода основана на измерении активности излу чения изотопных датчиков, размещенных в поверхностном слое обкладки, который поглощает часть энергии излучения. По мере износа слоя резины возрастает интенсивность излучения датчи-» ков, фиксируемая счетной аппаратурой. Схема измерений (рис. 5.19, а) включает в себя источник переменного тока, высо ковольтный выпрямитель, интегратор импульсов, усилитель, блок счетчика радиоактивных излучений и изотопный датчик. Дат чики представляют отрезки металлической проволоки размером 0,3-5-0,4 мм с добавлением радиоактивного таллия-204. Датчики с помощью медицинской иглы с плунжером вводятся на опре деленную глубину (до 2 мм) под поверхность обкладки. Тол щина слоя резины над датчиком контролируется измерением его
9 Заказ No 1462 |
267 |
РИС. 5.19.
Схема измерения (а) и тарировочный график четырех датчиков (б) для оп ределения износа обкладок радиометрическим методом:
/ — источник переменного тока; |
2 — высоковольтный выпрямитель; 3 |
— интегратор им |
пульсов; 4 — усилитель; 5 — блок |
счетчика; 6 — изотопный датчик; ши |
-КГ — число тысяч |
импульсов в минуту; dr 10* — толщина слоя обкладки над датчиком
активности — количества импульсов, зафиксированных аппара турой за определенный промежуток времени. Эмпирическая за висимость активности датчиков от толщины резинового слоя об кладки (рис. 5.19,6):
0 = (25 000-f-42 360)/е_0'003Ш,
где 0 — активность |
датчика, импульсов в минуту; |
d — толщина |
олоя обкладки над |
датчиком, мкм; е — основание |
натурального |
логарифма.
Линейный износ обкладки, соответствующий изменению тол щины обкладки над датчиком после проведения опыта (за оп ределенный период работы ленты под нагрузкой в регламенти рованных опытом условиях), определяется по формуле
Ad = d\— d%j
где Ad — линейный износ обкладки; di, d2— толщина слоя об кладки над датчиком до и после соответствующего опыта.
Эффективность счета импульсов радиометрической установ кой может изменяться из-за смещения геометрии измерений, сни жения активности датчиков в результате радиоактивного рас пада, изменения плотности воздуха и других факторов. Такие изменения фиксируются эталонным датчиком, по которому оп ределяются поправочные коэффициенты. Однако при этом увс-
личивается трудоемкость измерений. Этого недостатка можно избежать путем обеспечения регулирования геометрии измере ний с целью поддержания счета импульсов на определенном уровне, который контролируется эталонным датчиком. Значения активности группы датчиков и глубина их ввода в обкладку не должны существенно отличаться. При 10—20% -ной погрешно сти измерений соблюдались следующие условия: отклонение в активности датчиков одной группы не превышало 1000 им пульсов в минуту; отклонение в начальной глубине расположе ния датчиков в обкладке не превышало 200 мкм; линейный из нос обкладки после каждого опыта составлял не менее 50 мкм; число датчиков в группе не менее пяти. Ухудшение характери стик измерений приводит к необходимости увеличения числа датчиков в группе и, соответственно, трудоемкости работ.
Для поддержания заданной эффективности радиометриче ских измерений путем регулировки геометрии установки счет чика использован специальный блок для высоковольтных счет чиков МСТ-17 и Т25-БФЛ (рис. 5.20, а). Блок включает кор-
а — блок счетчика: |
/ — корпус; 2 — втулка; 3 —счетчик; |
4 — стопорная шайба; 5 — |
||
объектив; 6 — центрирующая шайба; 7 —датчик в обкладке; |
б — защитная капсула: / — |
|||
корпус; 2 —датчик; |
3 — амортизатор; в — лента |
с датчиками: |
1 — образцы обкладок; |
|
2 — участки ввода |
датчиков; 3 — маркировка; |
г — устройство |
для извлечения датчи |
|
|
ков; / — рукоять; 2 — фреза |
|
|
пус, втулку, во внутрь которой помещается счетчик, прокладку, стопорную шайбу, объектив с окном. При проведении измере ний на обкладку в зоне расположения устанавливается цен трирующая шайба, а на шайбу блок. После включения аппара туры проверяется эффективность счета импульсов с помощью дополнительной шайбы с эталонным датчиком. Если эффектив ность измерений оказывается меньше, то вращением объектива уменьшают расстояние между обкладкой (или датчиком в об кладке) и окном счетчика. После регулировки эффективности счета импульсов проводят измерения излучений датчиков в об кладке. Геометрическая эффективность счета импульсов, вы раженная в долях полного телесного угла, определяется по формуле
где L0— расстояние от окна счетчика до датчика; Rc— радиус окна счетчика.
Для уменьшения ошибок измерений необходимо, чтобы вы полнялось условие Lc>4/?c. В производственных условиях су щественное влияние на точность проводимых измерений могут оказывать ударные нагрузки от транспортируемого груза, при ходящиеся на участок расположения датчиков в обкладке ленты. Экспериментально исследовалось влияние силы удара груза о ленту на изменение активности датчиков в обкладке. Испытания проводились на стенде, представляющем собой ко пер с вертикальными направляющими, по которым сбрасы вался груз с металлическим бойком радиусом 7,5 мм. На ос нове полученных данных разработана и испытана защитная металлическая капсула (рис. 5.20, б) со сферическим углубле нием для источника и амортизатором. Для ввода датчика в об кладку ленты применяется шаблон с отверстиями, с помощью которого размечаются участки расположения датчиков (рис. 5.20, в). Извлечение датчиков из ленты осуществляется устрой ством в виде корпуса с винтовой рукоятью, фрезой и упором. Вращением рукояти вырезается резиновая пробка из обкладки, в толще которой находится датчик (рис. 5.19, г).
На промышленном конвейере № 2 (см. табл. 5.11) Балаклав ского РУ им. А. М. Горького проводились испытания рабочих обкладок на основе различных типов каучуков. Определялось сопротивление фрикционно-усталостному износу рабочих об кладок лент (в относительных единицах):
Тип каучука |
Опытная |
Произ- |
Тип каучука |
Опытная |
Произ- |
водствен- |
водствен- |
||||
в рабочей обкладке |
установка |
ные |
в рабочей обкладке установка |
ные |
|
|
|
условия |
|
|
условия |
НК + БСК |
1.0 |
1.0 |
НК . . . |
1.1 |
1,1 |
СКИ-3 |
1,2 |
0,9 |
СКИ-3 + СКД |
1,2 |
1 .5 |
|
|
1.1 |
БСК-I-СКД |
|
1.5 |
2G0
По результатам испытаний можно предположить, что на повышение сопротивления износу рабочих обкладок положи тельно влияет применение в резиновых смесях одновременно различных типов каучуков. Достоинствами радиометрического метода испытаний обкладок лент на истирание являются вы сокая чувствительность, возможность проведения эксперимен тов на опытном или промышленном конвейерах во всем диапа зоне изменения эксплуатационных факторов, малая трудоем кость и улучшение условий работ. Вместе с тем данный метод требует соответствующей подготовки персонала для работы с электронной аппаратурой и изотопными датчиками, строгого выполнения правил техники безопасности.
Испытания каркаса и ленты в целом. Разнообразие усло вий эксплуатации лент и значительное количество действую щих на износ ленты видов нагрузок обусловливают и определен ные виды испытаний. К важнейшим из них относятся испыта ния на разрыв и удлинение при рабочей нагрузке. Выбираемая по техническим условиям лента имеет 9—10-кратный запас прочности, однако агрегатный запас прочности ленты ниже расчетного. Известный метод определения агрегатной прочно сти ленты, основанный на растяжении образца ленты, не поз воляет достаточно точно оценить агрегатную прочность ленты из-за разброса упруго-прочностных характеристик прокладок. Установлено, что при нагружении образца ленты сначало раз рушится полоса образца с наименьшей деформацией, хотя раз рывная прочность этой полосы может быть наибольшей. В этом случае деформация разрыва образца ленты равна по величине деформации разрыва наиболее слабого звена. Коэффициент агрегатной прочности образца ленты
|
Д а — -------- ;---------;----------------- ;-------- • |
|
|
|
а 1 + а 2 + |
+ ° П |
|
где ол — прочность |
образца ленты; |
оь |
Ог— прочность по |
лос образца ленты. |
|
|
|
Прочность образца ленты соответствует деформации раз рыва наиболее слабой полосы образца и деформации осталь ных полос в момент разрыва. Коэффициент использования от дельных полос образцов резинотканевых лент составляет 0,65— 1,0, а коэффициент агрегатной прочности для лент с каркасом из полиамидных и полиэфирных волокон, который рекоменду ется учитывать при расчетах, составляет 0,7—0,9 (по данным Коммунарского горно-металлургического института).
Все большее значение придается исследованию модуля уп ругости каркаса и ленты в целом. В пределах рабочих нагру зок модуль упругости каркаса изменяется незначительно и за висимость напряжение — деформация практически линейна. Модуль упругости ленты существенно зависит от конструктив ных особенностей ленты, в частности, от геометрии располо
жения нитей основы. С увеличением угла наклона нитей ос новы к продольной оси ленты уменьшается модуль упругости каркаса. Модуль упругости образцов лент с каркасом из по лиамидных волокон при изменении угла наклона нитей основы от 0 до 90° находится в пределах 10700—2700 Н/см2. Модуль упругости каркаса без обкладок в аналогичных условиях со ставляет 51000—2350 Н/см2.
С повышением скорости транспортирования приобретает значение оценка упругих свойств ленты в динамическом ре жиме, в частности, при исследовании неустановившихся режи мов мощных конвейеров. Динамический модуль упругости ленты и скорость распространения в ней упругих волн можно определить методом свободных колебаний. Стенд для опреде ления динамического модуля упругости (рис. 5.21, а) ленты представляет собой зажимную балку, к которой подвешива ется лента с электрическим кольцевым динамометром и гру зом. С помощью рычажного механизма осуществляется дина мическое растяжение ленты, которая совершает продольные свободные колебания, регистрируемые динамометром. Дина мический модуль упругости в лентах с каркасом на хлопчато бумажной основе составляет 60—120 кН/см прокладки, а ско рость распространения упругой волны — 320—600 м/с. При возрастании числа прокладок в ленте от 3 до 7 динамический модуль упругости ленты увеличивается в 1,5 раза.
Один из методов, моделирующих условия динамического нагружения лент в эксплуатации,— испытание лент при пуль сирующем растяжении. Такой метод позволяет определить со противление усталостному износу каркаса с учетом пусковых нагрузок. Один конец образца ленты прикрепляется к непо движному зажиму, а другой — к подвижному (рис. 5.21, б). Подвижный зажим, соединяется шарнирно с рычагом, который оснащается грузом и приводным диском. Сопротивление уста лостному износу при динамическом растяжении определяется как число циклов нагружения до разрушения образца. Частота нагружений составляет 30 в минуту.
Для установления сравнительной работоспособности лентьг ее подвергают циклическим растяжениям при изгибе, модели рующим нагрузки на барабанах. Работоспособность лент в данном случае связана с сопротивлением прокладок, каркаса и соединительных слоев (сквиджей) усталостному износу и расслоению. При расчетных значениях диаметров барабанов и запасов прочности ленты число циклов растяжений ленты при изгибе до разрушения составляет несколько миллионов, чтосоответствует длительности эксплуатации ленты, равной 6-- 12 лет. Поэтому данный вид испытаний целесообразно приме нять для изучения сравнительной выносливости лент с боль шим числом прокладок и предельными значениями запаса прочности (лент для наклонных конвейеров с повышенными скоростью движения и производительностью, забойных кон.
вейеров с минимальными размерами барабанов). Исследова ние сопротивления усталости и расслоению проводят на специ альной установке (рис. 5.21, в). Установка включает барабан с образцом ленты, концы которого прикрепляются к рычагам механизма возвратно-поступательного действия. На образце ленты действуют напряжения изгиба и растяжения. Показа тель испытаний определяется как число циклов до расслоения или разрыва прокладок.
К эксплуатационным показателям ленты относят также пол зучесть и гибкость. Ползучесть ленты характеризует ее упруго пластические свойства при длительной нагрузке, обусловлен ной, например, предварительным рабочим натяжением ленты. Возникновение необратимых деформаций в ленте требует пе риодического изменения положения натяжного барабана или, в худшем случае, перестыковки ленты. Ползучесть ленты ис пытывается на стенде в виде копра с подвешенными к нему образцами ленты с динамометром (рис. 5.21, г). Усилие стати ческого натяжения создается с помощью рычага с грузом. Пол зучесть ленты определяется из формулы
ел = е0 — ем—е3, |
(5.9) |
где е0 — общая деформация (ползучесть) |
ленты; ем — перво |
начальная упругая деформация; е3 — запаздывающая упругая деформация.
Гибкость ленты характеризует способность ее к лоткообразованию, от которого зависит производительность конвейера. Лотковость ленты связана с величиной поперечного изгиба ленты. При отсутствии загрузки лента должна касаться одно временно боковых и средних роликов и не иметь развала в промежутке между роликоопорами. Таким образом, надо стремиться к оптимальной гибкости ленты, зависящей в основ ном от числа прокладок и типа каркаса. Для установления гибкости ленты (рис. 5.21, д) прямоугольный ее образец под вешивают на гибких связях) к опорной раме и определяют ве личину прогиба как отношение максимального смещения ленты к ее длине. Минимальные допустимые значения гибко сти (прогиба) конвейерных лент приведены ниже.
Угол наклона боковых роликов, градус |
20 |
25 |
30 |
35 |
40 |
45 |
f |
0,06 |
0,07 |
0,09 |
0,11 |
0,13 |
0,16 |
Испытания лент на гибкость по французскому стандарту проводятся как по утку, так и по основе путем измерений от клонений подвешенного к образцу ленты маятника.
В связи с расширением области применения ленточных кон вейеров для доставки крупнокусковых грузов возросло значе ние испытаний на сопротивляемость ударно-усталостному и ударно-пробойному износу. В известных стендах моделируется действие ударных нагрузок на ленту в загрузочной части кон вейера с гибкой или жесткой опорой, на роликоопорах (над
РИС. 5.21.
Стенды для исследования упруго-прочностных и усталостных характеристик лент:
а — динамического |
модуля |
упругости; |
б — сопротивления |
усталостному |
износу при |
|||
пульсирующем |
растяжении; |
в —сопротивления |
усталости |
при изгибе |
и |
растяжении; |
||
г — ползучести |
при |
статической нагрузке; д — гибкости; |
/ — образец |
ленты; 2 — Ди |
||||
|
|
|
намометр; |
3 — груз; |
4 — рычаг |
|
|
|
/
роликоопорой или между роликоопорами). Показателями каче ства ленты при этом служат: число ударов до частичного или полного разрушения нитей основы, утка прокладки или про кладки в целом, снижение разрывной прочности или сопротив ления усталостному износу после определенного цикла удар ных воздействий. Нс рекомендуется воспроизводить при испы таниях весьма значительные ударные нагрузки, при которых сразу возникает сквозное разрушение каркаса.
В испытаниях на маятниковом копре определяют сопротив ление ленты ударным нагрузкам как функцию снижения со
противления |
разрыву |
(рис. 5.22, а). Отклоняя маятник с бой |
||
ком на |
определенный |
угол, создают заданную |
ударную на |
|
грузку. |
При |
падении |
маятника боек ударяет |
по образцу |
ленты, повреждая при этом основу или уток Затем на разрыв ной машине исследуют прочность на разрыв данного образца ленты и сравнивают ее с прочностью идентичного целого об разца.
На испытательных стендах фирмы «Клаут Гуммиверке» (ФРГ) установлена эмпирическая зависимость, согласно кото рой величина максимально допустимой ударной нагрузки не должна превышать 40% ее разрывного усилия (рис. 5.22, б). Если, например, рассматриваемая лента имеет сопротивление разрыву 31,5 кН/см, то предельно допустимое ударное напря жение не должно превышать 12,6 кН/см. Это соответствует ударной нагрузке при падении куска породы массой 630 кг
свысоты 2 м.
Врассмотренных конструкциях стендов нанесение ударов
осуществляется в одну точку. В производственных условиях,
РИС. 5.22.
Стенды для исследования со противления лент ударно-уста лостному и ударно-пробойному износу:
а |
— с |
маятниковым |
копром; |
б — |
с |
вертикальным ударным |
меха |
||
низмом; в — с вертикальным |
удар |
|||
ным |
колебательным |
механизмом; |
/ — боек; 2 — образец; 3 — о п о р а
например, при падении груза в месте загрузки на средний ро лик ударные нагрузки рассредоточиваются на некоторой площади, образуя участок износа. При этом изнашивание ленты происходит быстрее. Стенд, разработанный ИГД Минчермета
СССР, обеспечивает воспроизведение рассредоточенных удар» ных нагрузок на ленту в зоне контакта с роликоопорой. В со став стенда входит рама с опорным роликом или плитой, на котором располагается образец ленты, закрепленный в за жиме (рис. 5.22, в). Ударный механизм включает в себя под вижную штангу с грузом и бойком, которая соединяется
сприводным рычажным механизмом. Эксцентричный барабан
ифигурный диск рычажного механизма обеспечивают непре рывное смещение штанги в горизонтальной плоскости на оп ределенной площади, величину которой можно изменять пу
тем регулирования частоты вращения барабанов. Испытания
проводились для лент МК-600, МК-400 и МЛК-300, ТЛК-150, ТА-300 с различными числами прокладок, толщиной рабочей обкладки, массой груза, радиусом закругления и угла за острения бойка. Определялась зависимость между числом ударных циклов, параметрами ленты и стенда. При массе груза 20—30 кг и высоте падения 0,3—0,5 м износ ленты про исходит в основном из-за расслоения прокладок. С увеличе нием массы груза до 40 кг и высоты падения до 0,5—0,75 м рабочая обкладка не отслаивается, а покрывается проколами, которые образуют сплошную зону разрушения в виде пробоя. При дальнейшем увеличении ударных нагрузок обкладка и каркас пробиваются частично или полностью.
Особую группу составляют испытания лент при повышен ных температурах на теплостойкость, огнестойкость и воспла меняемость. В испытаниях на теплостойкость определяется от рицательное влияние повышенных температур на упруго-проч ностные характеристики лент. Образцы лент выдерживают в термостате, после чего их испытывают. Результаты испыта ний сравнивают с исходными характеристиками лент при обыч ной температуре.
Для конвейерных лент, применяемых на шахтах в условиях повышенной пожароопасности, обязательно проведение испы таний на огнестойкость и воспламеняемость. Огнестойкость образцов ленты проверяется в условиях непосредственного воз действия на них пламени. В качестве показателя огнестойко сти в СССР используется продолжительность затухания горе ния образца после действия горелки. В ГДР лента считается огнестойкой (или пожароустойчивой), если термическое разру шение имеется только в зоне непосредственного воздействия пламени. В Бельгии обжигание образцов лент газовым пламе нем осуществляют на колосниковой решетке, устанавливаемой в камере (специальном штреке), имеющей размер сечения 2х Х2 м. Отрезок ленты укладывается на решетку из металличе
ских |
стержней толщиной 10 мм, устанавливаемую на |
высоту |
0,35 |
м от почвы. Газовая горелка включает трубки |
длиной |
450 |
мм и отверстиями диаметром 1,5 мм. Отверстия |
в числе |
52 шт. располагаются на расстоянии 50 мм друг от друга. По рукаву подводится пропановый газ. Испытанию подвергаются два образца, в одном из которых частично удаляется нерабо чая обкладка и делается сквозное отверстие. Другой образец испытывается целиком. Продолжительность воздействия пла мени горелки 10 мин при скорости движения воздуха в ка мере 1,5 м/с. Образцы считаются выдержавшими испытания, если после удаления горелки, затухания пламени и тления ос тается участок ленты, не поврежденный на всю ширину.
Ввиду возникновения ряда пожаров на подземных конвей ерах в ФРГ была поставлена задача по приближению испыта ний лент на огнестойкость к условиям, близким к реальным. Исследования проводились в экспериментальном шахтном
штреке сечением 6 м2 с деревянной крепью и скоростью дви жения воздуха 1,2 м/с. Отрезок испытуемой ленты длиной 20 м подвешивался к кровле. На концевом участке ленты устраи вался костер из дров массой 300 кг. Лента считалась огне стойкой, если длина сгоревшего участка ленты не превышала 4 м. Другие, аналогичные испытания проводились в штреке се чением 8 м2 при длине отрезка ленты 40 м, навешиваемой на роликоопоры. На базе производственных опытов разработана лабораторная модельная штольня длиной 2,1 м и сечением 0,35x0,35 м2, изготавливаемая из металлического листа с ог неупорной плиткой толщиной 25 мм, имеющая смотровое окно из термостойкого стекла и вентилятор. В верхнем покрытии модели имеются отверстия для установки датчиков темпера туры и скорости движения воздуха. Модель штольни оснаща ется горелкой, работающей на пропане. В результате проведе ния опытов разработаны нормы огнестойкости лент, согласно которым нормальные образцы лент на длине участка, равной 40 см, после воздействия на концевой участок ленты пламени горелки в течение 15 мин не подвергаются воздействию огня. Контрольные испытания проводились в специальном экспери ментальном огневом штреке длиной 125 м и сечением 8 м2 на одной из действующих шахт. Штрек оснащался двумя водными заслонами, смотровым ходком, источником огня из древесины, пультом управления и контроля основных параметров. Испы
танию |
подвергались образцы лент длиной 20 |
м. |
Если |
пламя |
|
не распространялось по ленте далее чем на |
10 |
м, |
то |
такая |
|
лента |
квалифицировалась как огнестойкая. |
Таким |
образом, |
в огнестойких лентах при возникновении пожаров пламя не должно распространяться самостоятельно. Кроме того, регла ментированы гигиенические характеристики огнестойких лент: при пожарах не должны выделяться в опасных количествах едкие и ядовитые газы и дым, нарушаться действие самоспасателей.
В СССР раздельно учитывается такой показатель огнестой кости лент, как ее воспламеняемость при пробуксовке бараба нов, характеризующий склонность ленты к воспламенению при трении. Обычно испытуемый неподвижный образец ленты при жимается к вращающемуся барабану и обдувается струей воз духа. Лента отвечает требованиям стойкости к воспламенению, если по истечении определенного времени не возникает возго рания или тления. Лейпцигским институтом охраны труда гор
няков |
(ГДР) не |
рекомендуется |
испытание резинотросовых |
лент |
на барабанах |
трения, так |
как в процессе горения или |
тления тросы повреждают барабан.
Сопутствующим видом испытаний лент на пожароопасность является проверка их на электропроводность. Лента относится к диэлектрикам, на поверхности которых накапливаются элек трические заряды. В шахтах, опасных по газу или пыли, искрообразование на ленте может привести к воспламенению окру
жающей среды и взрыву. Омическое сопротивление ленты не должно превышать определенного предела. Во Франции и Ве ликобритании этот предел составляет 3-10® Ом. Омическое со противление ленты устанавливается с помощью специальных электродов, источника высокого напряжения и измерительного прибора.
Показатель морозостойкости лент определяют обычно по отношению к обкладочным резинам. Морозостойкость обкла док устанавливается как степень изменения упруго-прочност ных свойств резины при пониженных температурах.
Показатель набухания ленты применяется редко и заклю чается в выдержке образца ленты в специальном жидком масле, а затем измерении приращения объема образца. Этот метод испытаний особенно полезен для оценки качества масло стойких лент.
К одним из новых показателей качества лент относится старение. В СССР этот вид испытаний проводят, располагая образцы лент на открытом воздухе в течение длительного вре мени. Затем определяют упруго-прочностные характеристики и сравнивают их с контрольными.
Износостойкость лент. Улучшение износостойкости лент достигается путем оптимизации их физико-механических и па раметрических характеристик, а также усовершенствования конструкции лент. Испытания различных типов конвейерных лент в процессе их эксплуатации показывают, что одинаковые типы лент имеют значительный разброс физико-механических характеристик. Это объясняется различиями в качестве по ставляемого на заводы сырья и соблюдения технологических регламентов. Наиболее распространенные дефекты лент — воз никновение складок и гофр в каркасе, посторонние включе ния, вмятины, снижение толщины обкладок в отдельных местах, образование воздушных полостей из-за нарушения режима вулканизации и, соответственно, вспученностей и расслоения в ленте при взаимодействии с роликами и барабанами. Износ бортов ленты происходит в основном из-за «серповидности» ленты. В результате неравномерного натяжения в резинотро совых лентах возникает преждевременный разрыв тросов без нарушения обкладочных слоев. В резинотканевых конвейерных лентах, изготовленных с соблюдением ТУ, стандартное откло нение прочности, относительного удлинения при рабочей и разрывной нагрузках составляет соответственно 10, 20 и 29%. Это обстоятельство также способствует возрастанию отклоне ния в сроке службы лент, эксплуатирующихся в одинаковых условиях. Таким образом, вопрос стабилизации характеристик
икачества изготовления лент приобретает особое значение.
Вразвитие ГОСТов на конвейерные ленты Загорским филиалом НИИРПа и институтом Союзпроммеханизация пред лагается учитывать для соответствующих условий эксплуата ции класс прочности и толщину рабочей обкладки в зависи-
Категория усло |
Класс |
Сопро |
|
Время одного оборота ленты. < |
|
||
тивление |
|
|
|
|
|||
вий эксплуата |
проч |
|
|
|
Более |
||
разрыву. |
До 24 |
25-60 |
60—120 121-180 |
||||
ции ленты |
ности |
180 |
|||||
(по ГОСТ 20—76) |
обкладки |
кН/см2 |
|
|
|
|
|
обкладки |
|
Толщина рабочей обкладки, мм |
|
||||
|
|
|
|
|
Очень тяжелые |
А |
2 |
8 |
8 |
8 |
8 |
6 |
Тяжелые |
А |
2 |
8 |
6 |
6 |
— |
— |
|
Б |
1.5 |
— |
— |
— |
6 |
6 |
Средние |
В |
1 |
6 |
4.5 |
— |
— |
— |
Легкие |
В |
1 |
— |
— |
4,5 |
4,5 |
4,5 |
|
С |
1 |
3 |
3 |
2 |
2 |
2 |
мости от интенсивности работы конвейера, зависящей от вре мени, затрачиваемого на один оборот ленты. Рекомендуемые
классы |
прочности и толщина рабочей обкладки приведены |
в табл. |
5.17. |
Для особо тяжелых условий эксплуатации лент, подвергаю щихся абразивному и ударному износу крупнокусковым гру зом, толщину обкладки целесообразно увеличивать до 10— 12 мм. В ФРГ имеется положительный опыт применения широ
ких |
резинотканевых |
и резинотросовой лент (шириной до |
3200 |
мм) с толщиной |
рабочей и нерабочей обкладок до 20 и |
8 мм соответственно. |
|
Значительным резервом в области уменьшения износа лент является улучшение методологии выбора типа и параметров лент. Это направление позволяет наиболее полно использовать работоспособность ленты при минимальных затратах. Напри мер, при интенсивном абразивном износе ленты, транспорти рующей мелко- и среднекусковые материалы, целесообразно выбирать ленты с увеличенной толщиной обкладки. При до ставке крупнокусковых грузов одновременно с увеличением толщины рабочей обкладки необходимо использовать каркас с противоударными элементами, повышающими сопротивление
ленты пробою. |
выбор параметров ленты, |
Оптимальным будет такой |
|
при котором износ отдельных |
ее элементов (обкладок, |
каркаса, сквиджей, стыков) до предельного состояния проис ходит примерно за одинаковый период эксплуатации. Отсюда следует, что целесообразно сначала устанавливать норматив ный календарный срок службы ленты для заданных условий, а затем параметры отдельных элементов, обеспечивающие со ответствующий срок службы отдельного элемента.
На продолжительность эксплуатации лент заметное влия ние оказывает правильность выбора числа прокладок не только по условию рабочего тягового усилия, но и по способности ее обеспечивать желобчатую форму без выполаживания боковых участков между роликоопорами. Контроль такого фактора, со-
|
Отношение |
Ширина |
фактического |
ленты, мм |
заполнения |
|
ленты к но |
|
минальному |
800 |
0,50 |
0,75 |
|
|
1,00 |
1000 |
0,50 |
0,75 |
|
|
1,00 |
1200 |
0,50 |
0,75 |
|
|
1,00 |
1400 |
0,50 |
0,75 |
|
|
1,00 |
1600 |
0,50 |
0,75 |
|
|
1,00 |
1800 |
0,50 |
|
0,75 |
||
200 |
||
1,00 |
||
|
Число обкладок для типа каркаса ленты
БКНЛ-65, ТА-100. ТК-100 |
БКНЛ-100, ТА-150. ТК-150 |
БКНЛ-150. ТК-200 |
ТКЛ-200 |
ТК'ТА-300 |
ТКТА-400 |
4 |
4 |
3 |
3 |
3 |
|
5 |
4 |
4 |
3 |
3 |
— |
5 |
5 |
4 |
3 |
3 |
— |
5 |
4 |
4 |
3 |
3 |
3 |
6 |
5 |
4 |
4 |
3 |
3 |
6 |
5 |
5 |
4 |
3 |
3 |
6 |
5 |
5 |
4 |
3 |
3 |
6 |
6 |
5 |
4 |
4 |
3 |
7 |
6 |
6 |
5 |
4 |
4 |
7 |
6 |
5 |
5 |
4 |
4 |
7 |
6 |
6 |
5 |
4 |
4 |
8 |
7 |
6 |
6 |
5 |
4 |
|
|
|
|
4 |
4 |
— |
— |
— |
— |
5 |
4 |
— |
— |
— |
— |
5 |
4 |
|
|
— |
— |
6 |
5 |
|
|
|
|
7 |
6 |
— |
— |
|
|
7 |
6 |
гласно данным Загорского филиала НИИРПа и Союзпроммеханизации, целесообразно осуществлять с учетом заполнения ленты транспортируемым грузом. Рекомендуемые числа про кладок в лентах по условию сохранения желобчатости на роликоопорах приведены в табл. 5.18.
Проблема создания новых износостойких конструкций лент для мощных конвейеров остается наиболее актуальной. Нельзя, например, повлиять на абразивность транспортируемой горной массы.
Признано, что для надежной доставки кусковых грузов крупностью до 600 мм и абразивностью 8—20 (по шкале Протодьяконова) при длине конвейера 300—1500 м, скорости дви жения ленты 2—3,15 м/с, высоте падения груза 0,5—2,5 м ленты должны иметь: прочность по основе 3—6 кН/см про кладки; прочность по утку 1—1,5 кН/см прокладки; защитные тканевые и брекерные прокладки, амортизирующий эластич-
ный слой, рабочие обкладки с |
повышенной |
износостойкостью |
и толщиной 5—10 мм. |
достигается |
также путем ис |
Улучшение работы обкладок |
пользования специальных материалов и добавок. Полиуретан, например, увеличивает сцепление нерабочей обкладки с бара баном, а тефлон, нейлон и поливинилхлорид уменьшают при липание груза к рабочей обкладке. Однако антиадгезионная и фрикционная способности материалов для рабочих обкладок находятся в противоречии друг с другом. Фирмами ФРГ вы пускаются ленты с поливинилхлоридными покрытиями в двух исполнениях: с гладкой антиадгезионной поверхностью для на липающих грузов и с фрикционной поверхностью с мелкими рифлениями для доставки грузов под углом до 30°. Антиадгезионными и одновременно фрикционными свойствами обла дают ленты из полиэстера, изготавливаемые английскими фир мами. Аналогичными свойствами обладают обкладки из крем-
нийорганического |
низкомолекулярного каучука |
с минераль |
|
ным наполнителем, разработанные |
Всесоюзным |
научно-иссле |
|
довательским институтом резинотехнического |
машинострое |
||
ния. |
износостойкостью |
обладают |
рабочие об |
Повышенной |
кладки с покрытием из пенополиуретана, армированного сверху тросиками, фенопласта или резины, армированной ко роткими отрезками проволоки или синтетическими волокнами. В зависимости от интенсивности фрикционного воздействия на рабочую поверхность ленты по ее ширине рабочие обкладки выполняют переменной толщины (обычно с большей толщи ной в средней части и реже — на бортовых участках). Ленты с утолщенными обкладками в некоторых случаях армируются по всей ширине, в средней или боковых частях усиливающими прокладками. Интересен опыт применения лент с одинаковой толщиной рабочей и нерабочей обкладок. После износа рабо чей обкладки до предельного состояния ленту демонтируют и навешивают вновь на конвейер, но при этом рабочей поверх ностью ленты становится другая обкладка.
Большим спросом на горнообогатительных комбинатах пользуются ленты, рабочие обкладки которых имеют рифле ния. На Лисичанском заводе резинотехнических изделий раз работан способ изготовления конвейерных лент шириной 800 и 1000 мм с рифленой рабочей обкладкой, позволяющей уве
личить угол транспортирования до 30° |
Эти ленты изготавли |
|
ваются без |
применения специальных |
пресс-форм. Стоимость |
их только на |
5—10 % больше лент с |
гладкой поверхностью. |
На собранный обычным способом каркас ленты сверху рабо чей обкладки укладывается текстильный прессующий элемент многократного использования. Рисунок переплетения нитей прессующего элемента, который можно изменять при вулкани зации, передается обкладке. Такие ленты прошли испытания на угольных шахтах Донбасса. В новом варианте прессующий
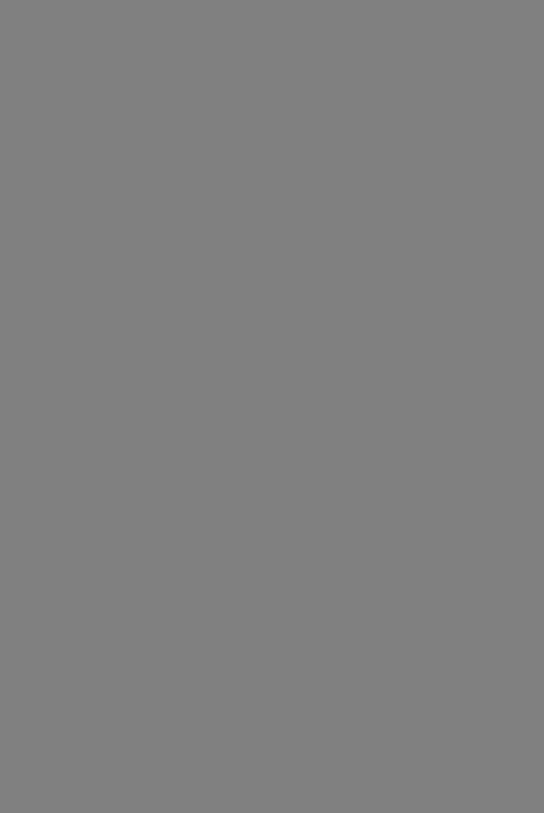
полиамидного волокна или хлопка. Нити основы почти не имеют волн изгиба и поэтому, являясь главным тяговым эле ментом прокладки, допускают минимальное удлинение ленты. Вспомогательные нити связывают между собой нити утка, на ходящиеся по обе стороны основы. Для утка в многоосновных прокладках используют капрон, так как он способствует лоткообразованию и снижению ударных нагрузок. В научно-ис следовательском институте резиновой промышленности иссле довались различные типы многоосновных прокладок и образцы лент с ними. Наиболее стабильные физико-механические свой ства и технологичность изготовления показали ленты с двух основными прокладками МЛ-200, МЛ-300, МК-300, МК-600. Уд линение лент с прокладками МЛ-200 и МЛ-300, имеющими в качестве главной основы лавсан, составило 0,8—1,5%, а для лент с прокладками МК-300 и МК-600 (в качестве главной ос новы применен капрон)— 3%. Вспомогательная основа этих лент выполняется из нитей хлопка и капрона.
Многослойные ленты включают несколько систем основных и уточных нитей, заменяющих соответствующее число слоев ткани. Многоосновные и многослойные ленты позволяют уменьшить удлинение ленты, увеличить сопротивление уста лостному износу благодаря монолитности конструкции и хоро шей связи резины с тканью, существенно сократить трудоем кость работ по изготовлению ленты, так как отсутствует опе рация сборки каркаса, уменьшить стоимость ленты. Однако, как показывает опыт эксплуатации многоосновных и много слойных лент, замена многопрокладочных лент равнопрочными им одноили малопрокладочными требует определенной осто рожности. По данным предприятий Минстройматериалов СССР,
лента МК-300 не обеспечивает равноценной замены БКНЛ-65 с пятью, а иногда и с четырьмя прокладками. Наиболее ре альная область применения ленты МК-300 —это замена лент БКНЛ-65 с тремя прокладками при доставке мелкосыпучих грузов. В более жестких условиях эксплуатации (по крупно сти груза и расчетной прочности ленты) наблюдаются развал ленты, ползучесть, разрыв стыка и раздиры. Наиболее слабым местом однопрокладочных лент является узел стыковки, так как уменьшается площадь соединения. Для многоосновных и многослойных лент обязательно применение стыковки вулка низацией.
Одним из эффективных средств повышения монолитности и сопротивления расслоению ленты является частичное или полное исполнение каркаса из разреженных прокладок. Раз личные варианты таких лент разработаны Коммунарским гор но-металлургическим институтом и Всесоюзным научно-иссле довательским институтом механизации черной металлургии. Нити основы и утка прокладки расположены с разрежением по всей площади либо для обеспечения местной гибкости только на бортовых участках и на участках изгиба между ро-
274
ликами роликоопоры (рис. 5.23, б, в). Размеры ячеек про кладки выбирают в зависимости от прочности нитей основы и утка. При пропитке и промазке прокладок в процессе изготов ления каркаса резина заполняет ячейки, образуя монолитную конструкцию. К недостатку таких лент можно отнести сниже ние общей прочности ленты на растяжение по сравнению с обычными лентами при одинаковой прочности нитей основы. Испытаниями опытных партий лент с разреженными проклад ками БЛН-150 установлено, что показатель усталостного рас слоения (число циклов на флексинг-машине до расслоения) примерно в 2 раза выше, чем лент БКНЛ-150. Несколько выше также и прочность связи между прокладками и рабочей об кладкой. Наблюдения за работой опытных лент на 14 уголь ных шахтах Донбасса подтвердили их работоспособность и по вышенное сопротивление расслоению.
В лентах комбинированной конструкции удается сохранить прочностные характеристики лент с обычными прокладками, монолитные и усталостные свойства лент с разреженными про кладками, уменьшить касательные напряжения в среднем слое ленты. Такая лента включает обкладки, верхние и нижние пары прокладок плотного переплетения, верхний, нижний и средний эластичные слои. Средний утолщенный эластичный слой, оснащенный разреженной прокладкой (рис. 5.23, г), по вышает сдвиговую податливость ленты и, таким образом, сни жает касательные напряжения. Разреженная прокладка улуч
шает монолитность и технологичность изготовления |
ленты, |
|
способствует сохранению |
постоянной толщины среднего слоя |
|
по всей площади. |
резинотехнических изделий |
прове |
Свердловским заводом |
дены экспериментальные работы по созданию лент из нетка ных нитепрошивных полотен, аналогичных по своим упруго прочностным характеристикам лентам из многоосновных тка ней. Нитепрошивные полотна вырабатываются на машинах «Малимо» и состоят из основных, уточных и прошивных нитей. Уточные нити также не переплетают основные и располага ются на них в распрямленном состоянии под определенным уг лом к горизонтали. При изготовлении ленты перпендикулярно расположенные относительно друг друга синтетические нити основы и утка подают в зону прошивки, где их скрепляют стежками петельного шва из хлопчатобумажных нитей. В опыт
ном производстве лент типа 2 взамен ткани БКНЛ-65 |
было ис |
пользовано нетканое прошивное полотно ПНК-65. В |
качестве |
основных нитей применены лавсановые крученые (термофик- |
|
сированные) нити, уточных — лавсановые иетермофиксирован- |
ные, |
прошивных — крученые |
хлопчатобумажные. |
Благодаря |
особенностям структуры в нетканом полотне лучше |
удержива |
||
ется |
дублирующая резиновая |
смесь. По сравнению |
с тканью |
БКНЛ-65 нетканое полотно ПНК-65 имеет меньшие массу и толщину, соответственно на 16 и 14%, и большую прочность
на разрыв по основе (на 10 %) и утку (на 30 %). Промежуточ ное и разрывное удлинения составляют 3 и 10%, содержание хлопка на 30 % меньше. Однако возникают трудности в ре жиме вулканизации, связанные со значительной тепловой усад кой утка. Конвейерные ленты на основе полотен ПНК-65, осво енные Свердловским заводом резинотехнических изделий, соот ветствуют требованиям ГОСТа, имеют прочность связи между слоями 34—50 Н/см, между обкладкой и прокладкой—34 и 45 Н/см, удлинение ленты не более 2 %.
Обычно мощные конвейеры фирм ГДР, ФРГ, США, Ка нады, устанавливаемые на карьерах и шахтах, оснащаются резинотросовыми лентами шириной до 3200 мм, прочностью 8—63 кН/см, толщиной рабочей и нерабочей обкладок до 16 и 8 мм, относительным удлинением 0,2 %. Основной объем вы
пускаемых |
в СССР |
резинотросовых лент шириной 800— |
2400 мм, |
прочностью |
5—60 кН/см, толщиной обкладок 4— |
8 мм, относительным удлинением 0,5 % направляется для предприятий угольной промышленности. Значительную по требность в таких лентах испытывают и другие отрасли, осо бенно металлургическая. Сопротивление усталости резинотро совой ленты при многократном изгибе зависит от отношения диаметра приводного барабана к диаметру проволоки троса; оно должно быть равным не менее 1600—2500. Тросы отечест венного производства изготовляются из проволоки с проч ностью на разрыв 2,2 кН/мм2, с содержанием углерода в стали 0,73 %. В качестве адгезионного покрытия проволок использу ется латунь, наносимая на проволоку гальваническим спосо бом. Прочность связи резины с латунированным тросом должна составлять не менее 0,4 кН/см2, при этом относительное удли нение резины при разрыве не менее 500 %, а твердость по Шору не выше 65 ед. Для обеспечения заданной прочности связи тросов с резиной отношение шага тросов к их диа метру должно составлять 1,5—3,5. Резинотросовые ленты мо гут нормально работать при запасе прочности, равном 4—10.
Совершенствование конструкций резинотросовых лент в СССР и за рубежом идет также в направлении улучшения геометрии компоновки тросов, усиления дополнительными эле ментами и применения новых материалов. Фирмой «Континен таль» (ФРГ) в качестве антикоррозионного средства для тро сов используются водоотталкивающие резиновые смеси с до бавлением минеральных масел на парафиновой и нафтеновой основах и органических соединений. Этой же фирмой разрабо тана резинотросовая лента с повышенными диаметрами тросов и расстояниями между ними, которые повышают сопротивле ние усталости без снижения прочности ленты (рис. 5.24, а). Тросы могут располагаться группами с интервалами в зонах
изгиба |
ленты для улучшения |
образования лотка |
ленты |
(рис. 5.24, б). Диаметр приводного барабана можно |
умень |
||
шить, |
если тросы компоновать из |
нескольких свободно |
распо- |