
МОНТАЖ, ОБСЛУЖИВАНИЕ И РЕМОНТ КОНВЕЙЕРНОГО ОБОРУДОВАНИЯ
Требования к монтажу, обслуживанию и ремонту конвейер ного оборудования определяются ведомственными правилами эксплуатации и техники безопасности. В общем случае мон таж конвейера представляет собой комплекс мероприятий, включающих в себя сборку отдельных узлов на опорном осно вании, регулировку их положения, подключение к источнику энергии, опробование и наладку режима работ. В настоящем разделе рассматриваются особенности и наиболее прогрессив ные средства монтажа, обслуживания и ремонта основных уз лов мощных ленточных конвейеров.
6.1. МОНТАЖ, ОБСЛУЖИВАНИЕ И РЕМОНТ ОПОРНЫХ КОНСТРУКЦИИ
Характерной особенностью ленточных конвейеров является низкая степень их заводской готовности, что увеличивает объем и сложность сборочных и регулировочных работ. Подго товку к монтажу конвейера начинают с разбивки осей опор ных конструкций, примыкающих устройств и сборки металло конструкций привода, натяжной станции и средней части става. Став монтируется стационарно или с возможностью пере движки. В горных выработках используется также подвеска конвейеров-перегружателей к элементам крепи. Качество мон тажа конвейера связано прежде всего с выполнением требова ний расположения става в пространстве. По рекомендации ИГД им. А. А. Скочинского допустимые значения радиуса перегиба става в вертикальной плоскости от конца участка конвейера с минимальным натяжением определяются из соот ношения
г> |
(^с шах |
^cmin)6n |
| г> |
/с 1 \ |
Кс= |
------- |
--------- Г -Kcmln» |
|
|
где Rcmax — радиус |
перегиба |
става на участке с максималь |
||
ным натяжением; Rc т ш— то |
же, с минимальным |
натяжением; |
||
Lu — расстояние от |
участка |
перегиба |
до конца |
участка кон |
вейера с минимальным натяжением; L —длина конвейера. Расчетные значения Rc (м) для ленточного (ширина ленты
800—2000 мм) конвейера в вертикальной плоскости приведены
в табл. 6.1.
Особое внимание должно уделяться прямолинейности става
|
|
Участок става с выпуклым профилем |
||
Ширина |
Участок става |
|
при макснмалг»ном натяжении |
|
при минималь |
ле]нты |
|||
ленты, мм |
с вогнутым |
|
|
|
|
профилем |
ном натяжении |
|
|
|
|
ленты |
длина конвейе |
длина конвейе |
|
|
|
ра до 500 м |
ра более 500 м |
800 |
100 |
25 |
75 |
100 |
900 |
П О |
30 |
72 |
П О |
1000 |
150 |
30 |
75 |
115 |
1200 |
300 |
35 |
80 |
130 |
1600 |
400 |
45 |
90 |
170 |
2000 |
500 |
60 |
100 |
200 |
в горизонтальной плоскости на участках, не оснащенных спе циальными поворотными устройствами. Отклонение от задан ных правил резко снижает эксплуатационные характеристики конвейера из-за просыпей, износа ленты, возникновения ава рийных ситуаций. Ориентировка става в горизонтальной плос кости осуществляется с помощью проволочных отвесов, специ альных механизмов или лазерных указателей типов ЛУН-3 и ЛУН-5. При использовании лазерных указателей положение секций става контролируется с помощью шаблона с противове сом и мишенью, относительно которой корректируется пятно луча. Одна из характеристик лазерного указателя — сходи мость светового пучка. Усовершенствованная конструкция ука зателя типа ЛУН-7 оснащена визиром в виде съемной зритель ной трубы с 20-кратным увеличением, служащей для наблюде ния за лазерным пятном. Указатель ЛУН-7 испытан на шахте им. В. И. Ленина ПО «Южкузбассуголь» при проведении кон вейерного квершлага длиной 1330 м. Прямолинейный участок выработки длиной 600 м пройден без перестановки указателя. На Харьковском заводе точного приборостроения освоен се
рийный выпуск указателей типа ЛУН-7. |
основных |
|
Обеспечение жесткости |
конструкций — одно из |
|
требований, предъявляемых |
к монтажу. Однако |
снижение |
жесткости опорных элементов возможно и в процессе эксплуа тации оборудования. Поэтому проводятся дополнительные ме роприятия по увеличению жесткости опор. Так, на шахте «Зыряновская» ПО «Южкузбассуголь» для сохранения жесткости «ставов конвейеров 1ЛТ80 применяют стяжки, изготовленные из прутков диаметром 8 мм.
В настоящее время большие требования предъявляются к снижению металлоемкости опорных конструкций, разъемно- •сти соединений отдельных частей, которые должны быть транспортабельными, особенно при доставке в шахту. Алексан дровским машиностроительным заводом им. К. Е. Ворошилова разработаны линейные секции става с профильными и разбор-
ными элементами (рис. 6.1, а). Каждая секция включает стойки, соединенные продольными и поперечными балками, траверсами и съемными кронштейнами для роликоопор. Стойки, балки и траверсы выполняются из гнутого швеллера и имеют отверстия, фигурные пазы, выступы, хвостовики и скобы, обес печивающие разъемность соединений. В нижней части стоек располагаются отверстия с пазами для установки роликов хо лостой ветви. Такая компоновка крепежных элементов умень шает деформацию продольных балок. В разборных конструк циях секций конвейеров все чаще используют трубчатые профили отдельных элементов. Стойки изготавливаются с коры тообразными опорами, имеющими пазы, на которых посредст вом штифтов монтируются трубчатые продольные балки пря моугольного сечения (рис. 6.1, б).
Для улучшения размещения оборудования в горных выра ботках установку става производят не на основании, а на под весках из канатов или цепей, которые крепятся к верхним эле ментам крепи. Это позволяет также уменьшить расход леса, загрязнение пространства, сохранить геометрию расположения става на более длительный период. Так, на шахтах ПО «Ростовуголь» конвейеры типа 1Л100К стали монтироваться на подвесках из отрезков использованной цепи скребковых кон вейеров СП63 и СР70А. Цепи с одной стороны через каждые 5 м присоединяются к крепи, а с другой — к несущим канатам с роликоопорами рабочей ветви ленты (рис. 6.1, в). На кана тах монтируются также жесткие подвески с трехроликовыми роликоопорами для холостой ветви ленты.
Фирма «Такраф» (ГДР) выпускает подвесные ставы с жест кими и гирляндными роликоопорами, для обеспечения устойчи вости которых используются растяжки, прикрепляемые к почве выработки через каждые 30—50 м. Иногда подвесные цепи оснащаются натяжными устройствами. Подвеска ставов осуще ствляется также и при монтаже их через различные препятст вия. Одной из английских фирм в Колумбии построен подвес ной канатный мост, на котором монтируется ленточный кон
вейер длиной |
1930 м, с шириной ленты 1067 мм и скоростью |
|
ее движения |
3 м/с. Конвейер имеет производительность 1600т/ч |
|
и мощность привода |
800 л. с. Разность уровней отметок опор |
|
ных мачт 108 м при |
пролетах двухканатного подвесного моста |
390 м. Конвейер транспортирует медную руду из рудника в дробильное отделение обогатительной фабрики.
Наибольшим нагрузкам канаты подвергаются в загрузоч ной части конвейера, в результате чего они прогибаются, вызывая просыпание транспортируемого материала. В шахто управлении «Мирное» ПО «Ростовуголь» для уменьшения про висания канатов применяются трубчатые опоры, приваривае мые к дополнительным стойкам (рис. 6.1, г).
В систему обслуживания ставов конвейеров входят конт роль и проверка состояния металлоконструкций, стыковых
соединений, элементов крепления, положения секций. В резуль тате длительной эксплуатации в металлоконструкциях могут возникать трещины, остаточные деформации, ослабление за клепочных и болтовых соединений. Под действием влаги, тем пературы воздуха, солнца слой краски, покрывающий элементы конвейера, разрушается или теряет свои защитные свойства. Возникает процесс коррозионного разрушения металла. Все обнаруженные трещины разделывают и заваривают, ослабшие заклепки заменяют новыми, а ослабшие болты затягиваются. В ответственных местах заваренные трещины усиливают на кладками толщиной в пределах 0,6—0,7 толщины элемента. Швы накладываются наклонно к устью, вызвавшему появле ние трещины. Не рекомендуется повторная заварка без вы рубки поврежденного места. Погнутые элементы металлокон
струкций правят без подогрева (при |
толщине |
металла 4— |
6 мл) или с подогревом (при толщине |
свыше |
6 мм). Очаги |
коррозии металла зачищают до металлического блеска и по крывают масляной краской. При большом объеме работы по ремонту металлоконструкций выполняют во время очередного планового ремонта. При этом к металлоконструкциям предъяв ляются следующие требования: контролепригодность, доступ ность для применения средств механизации, взаимозаменяе мость, при которой максимально исключаются подгоночные и регулировочные операции, стандартизация и унификация со ставных частей, восстанавливаемость.
6.2. МОНТАЖ, ОБСЛУЖИВАНИЕ И РЕМОНТ РОЛИКООПОР
Монтаж роликоопор осуществляется одновременно с уста новкой секций конвейера на всех участках трассы. Проверя ется возможность отрыва ленты от роликоопор, главным обра зом, на концевых секциях. Отдельные ролики должны про ворачиваться рукой. Более тонкая регулировка положения роликов осуществляется с помощью прокладок. В ПНР на мощ ных конвейерах контроль положения роликоопор производится
спомощью оптического прибора с визирами. При сходе ленты
сроликоопор на участке схода ослабляют крепление и пере катывают ролики в горизонтальной плоскости на стороне схода
внаправлении движения ленты. Отверстия под роликоопоры просверливаются заранее по шаблонам. Установку предвари
тельно проверенных роликоопор начинают с нижней ветви
|
|
|
|
|
|
|
|
РИС. |
6.1. |
|
|
|
|
|
|
|
|
|
|
|
|
|
|
Монтаж |
ставов: |
|
|
|
|
||||
а — с профильными |
и |
разборными элементами: |
/ — стойка с |
отверстиями и |
пазами; |
|||||||||||
2 — поперечная |
балка |
с |
хвостовиком; |
3 |
— съемный |
кронштейн |
роликоопоры; |
4 — про |
||||||||
дольная балка |
с пазами; |
5 —траверса |
с |
пазами |
и |
выступами; |
б — с трубчатыми про |
|||||||||
дольными |
балками; |
в — |
с |
подвеской |
к |
крепи: |
/ — |
цепь; |
2— канат |
с роликоопорами |
||||||
для рабочей |
ветви |
ленты; |
3 — подвески |
для роликоопор |
холостой |
ветви ленты; г — |
||||||||||
канатного |
с |
дополнительными опорами: |
/ — лента; 2 — канат; |
3 — дополнительные |
||||||||||||
|
|
|
|
|
|
|
|
|
опоры |
|
|
|
|
|
|
ленты, пока доступ к ней не закрыт роликоопорами рабочей ветви.
Жесткие роликоопоры крепят с помощью фигурных крон штейнов с системой пазов или отверстий. Более жесткую кон струкцию имеют кронштейны, повторяющие профиль желобча той роликоопоры и связанные с рамой посредством укосин. В США выпускаются опорные элементы для установки роликоопор, имеющие жесткую компоновку и изготовленные из стек ловолокна. Сборку такой роликоопоры производят благодаря системе пазов и выступов на отдельных элементах и специаль ным формам с жидким раствором стекла и смолы (рис. 6.2, а). Опоры из стекловолокна имеют высокую прочность, меньшую массу, не поддаются коррозии и обладают демпфирующей спо собностью.
Для компактного монтажа осей смежных роликов соеди няющий их кронштейн выполняется со встречными и симмет рично расположенными конусными отверстиями. При этом концы осей имеют полуцилиндрическую конфигурацию с вы ступами. Взаимодействуя друг с другом, оси роликов удержи ваются от прокручивания и осевых смещений. В стесненных условиях горных выработок иногда применяют консольное крепление роликоопор (рис. 6.2, б), используя при этом по перечины повышенной жесткости с укосиной. В этом случае секции конвейера имеют опорные стойки только на одной сто роне, благодаря чему достигается экономия рабочего про странства.
В канатных опорах жестких роликоопор наиболее слабым местом является узел подвески. Хорошо зарекомендовала себя
раздельная |
компоновка узла подвески, состоящего из втулки |
с пазом под |
канат и фиксирующими клиньями (рис. 6.2, в). |
Втулку, имеющую бурты по краям, надевают пазом на канат. В отверстия втулки с обеих сторон забивают клинья, располо женные встречно под углом друг к другу. На втулку надевают крюк роликоопры. Вращение втулки на канате исключается. При креплении гирляндных роликоопор к жесткому или канат ному ставам также используются быстросъемные подвески. На шахтах рудоуправления им. С. М. Кирова ПО «Кривбассруда» для подвески гирляндных роликоопор применяются пружинные рамки П-образной формы. Рамка охватывает полку продоль ной балки и фиксируется болтом.
Обслуживание роликоопор связано с мероприятиями по контролю их состояния и периодической смазке. Уменьшение частоты вращения или полное затормаживание ролика из-за нарушения смазки, перекосов, выхода из строя подшипникового узла в результате износа ведет к нарушению нормального хода ленты, повышенному ее износу, к дополнительным затратам мощности и нередко к аварийным ситуациям. Периодическая смазка роликов позволяет снизить сопротивление движению ленты, нагрев трущихся поверхностей, шум работы конвейера,
Монтаж роликоопор:
а — с опорными кронштейнами из |
стекловолокна; б — консольный роликов; в — с разъ |
емной подвеской |
жесткой роликоопоры к канатам |
удары и вибрации. Для роликоопор применяют густые конси стентные смазки.
Техническая характеристика консистентных смазок дана
втабл. 6.2.
Взависимости от вида добавки различают кальцевые, натро вые, кальциево-натровые, литиевые и другие консистентные смазки. Кальциевые смазки или солидолы (УС-2, УСс-2 и др.) влагоустойчивы, с водой не образуют эмульсий, но имеют сравнительно невысокую температуру плавления (ниже 90 °С). Применяются для смазки слабо- и средненагруженных механиз мов, работающих на открытом воздухе и в помещениях с высо кой влажностью воздуха. Натровые смазки или консталины (УТМ, УТ-2 и др.) с водой образуют эмульсии, но имеют сравнительно высокую (до 150 °С) температуру плавления. Применяются для смазки тяжелонагруженных узлов трения. Кальциево-натровые смазки (УТВ, НК-30 и др.) обладают про межуточными свойствами между кальциевыми и натровыми смазками. Литиевые (Циатим-201, Циатим-202 и др.) и крем нистые смазки (Циатим-221 и др.) обладают высокой морозо стойкостью (до минус 60—70 °С) и хорошими антифрикцион ными свойствами.
Тип смазки
Универсальная средне плавкая:
УСс-1 УСс-2 УС-3 Униол-1
Универсальная туго плавкая УТ-1 Морозостойкая НК-30 (УМ)
Универсальная туго плавкая водостойкая УТВ (1—13)
Универсальная тугоплав кая морозостойкая УТМ Циатим-201 Циатим-203 Циатим-221 Графитная УСс-А
Индустриальная ИП-1: летняя зимняя
Канатная 39у
Вязкость,
к
СОО
темпера тура,°С |
небо Па*слее, |
X |
S |
<У |
о. |
||
С |
с |
0 |
180 |
330—360 |
0 |
500 |
270—330 |
— |
— |
150—220 |
80 |
— |
150—300 |
0 |
500 |
225—275 |
|
_ |
300—350 |
0 |
500 |
250—290 |
|
|
275—325 |
0 |
150 |
270—320 |
0 |
100 |
— |
80 |
200 |
275—370 |
0 |
200—400 |
2—50 |
|
|
260—310 |
—— 310—350
— — 4,5
к
О .Х
5w
О.с
о» 5
1 с
say
70
75
90
200
130
90
120
120
_
—
—
75
80
75
65—75
Температура
применения,
°С
макси мальная |
мини мальная |
55 —10
60 —10
75 ___
150 —30
120 —
___ —70
П О —20
100 —60
120 —45
160 - 6 0
70 —10
65 —10
60 —15
50 —25
В соответствии с основными свойствами различают влагостойкие (В), тугоплавкие (Т), среднеплавкие (С), морозостой кие (М) и другие консистентные смазки. Кроме того, смазки
разделяют по |
назначению — универсальные |
(У); |
по составу — |
синтетические |
(с). Приведенные в скобках индексы входят |
||
в обозначение |
марки смазки (УС-3, УТ-1, |
УМ, |
УС-2, УТМ), |
характеризуя их назначение, состав, свойства.
Известны ролики, втулки подшипников которых изготавли ваются из металлокерамической композиции с наполнителями в виде дисульфида молибдена или графита. Такие подшипнико вые узлы относят к группе самосмазывающихся. Температура применения самосмазывающихся роликов от +365 до —250 °С при коэффициенте трения 0,03—0,04. Смазка роликоопор и дру гих узлов конвейера осуществляется по паспортам или картам смазки, содержащим схемы расположения точек смазки, данные марки смазочных материалов, периодичности и способа смазки. Применяют циркуляционную и индивидуальную системы смазки. Более трудоемко индивидуальное обслуживание систем с густой смазкой с помощью ручных шприцев или пистолетов. Опыт использования централизованной смазки роликов пока-
зал, что она недостаточно надежна из-за частых повреждений. Хорошо зарекомендовали себя закладные долгодействующие смазки марки БНЗ-З и БНЗ-ЗМ Бердянского опытного нефтемаслозавода. При надежном уплотнении подшипниковых узлов морозостойкая смазка БНЗ-ЗМ обеспечивает нормальную ра боту роликов в течение трех лет без ее замены и пополнения. Интервал смазки роликов холостой ветви составляет 800— 4000 часов машинного времени в зависимости от типа ролика и марки смазки.
Необходимо постоянно следить за состоянием роликов. За тормаживание или останов ролика приводит к неравномерному износу обечайки, появлению на ее поверхности острых кромок, режущих ленту, выпуклостей от налипшего материала, вызы вающих сход ленты, а следовательно, истирание ее бортов и просыпи транспортируемого материала. На конвейерах, осна щенных центрирующими роликоопорами и дефлекторными ро ликами, следят за состоянием узлов вращения, очищают и сма зывают их в зависимости от интенсивности загрязнения.
На мощных ленточных конвейерах одним из трудоемких процессов является замена вышедших из строя роликов или роликоопор. Замена роликов осуществляется при остановленном конвейере и отсутствии груза на ленте путем подъема ленты, раскрепления узлов соединения, демонтажа и монтажа роликов. Для подъема натянутой ленты необходимо в целях обеспечения техники безопасности применять средства механизации в виде рычажных механизмов, лебедок, талей и ходовых тележек. На шахте «Байдаевская» ПО «Южкузбассуголь» замена роли ков на конвейере КРУ-350 производится с помощью опорных лыж с винтовым подъемным механизмом (рис. 6.3, а). Лыжи шарнирно через пластины присоединяются к ходовым гайкам с левой и правой резьбой, устанавливаемым на винте. При вра щении винта гайки сближаются или расходятся, благодаря чему поднимается или опускается верхняя лыжа. После подъема ленты ролик демонтируется, а на его место устанавливается новый. Менее трудоемко в изготовлении, но проще в примене нии приспособление в виде трубы с тросом (рис. 6.3, б) и опор ных кронштейнов с лебедкой. Труба с пропущенным через нее тросом заводится под ленту. Трос одним концом с помощью крюка прикрепляется к низкому кронштейну, а другим — к крюку лебедки, смонтированной на высоком кронштейне. Вра щением рукоятки лебедки поднимают трубу вместе с лентой и производят замену роликоопоры. На конвейерах тяжелого типа применение механизмов для снятия роликов с кронштейнов ста новится необходимым. Такой механизм монтируется на под вижной тележке и включает винтовой домкрат с опорной площадкой для ленты и съемным крюком (рис. 6.3, в). Съем ный крюк изготавливается совместно с зубчатой рейкой, взаи модействующей с шестеренкой. Для подъема площадки с крю ком и перемещения рейки с крюком служит одна рукоять.
V.10 Заказ № 1462 |
289 |
|
|
|
РИС. 6.3. |
|
|
|
|
|
Средства для |
замены роликоопор: |
|
|
|||
а — винтовой подъемный |
механизм: |
/ — опора; 2 — винт; |
3 — гайка; |
б — приспособле |
|||
ние: / — труба; 2 — трос; |
3 — лебедка; |
в — подъемный |
механизм |
в виде |
съемного |
||
крюка; |
/ — крюк; 2 —зубчатая рейка; |
3 —опорная площадка; 4 — домкрат; |
5—те |
||||
лежка; |
г — самоходная |
установка: |
/ — лебедка; 2 — стрела; 3 — шасси; 4 — опоры |
В процессе замены роликов тележку подкатывают к исходной позиции по направляющим, смонтированным поперечно кон вейеру. Затем вращением рукоятки поднимают ленту опорной площадкой, захватывают и поднимают ролик крюком. После перестановки рукояти врашают шестерню и выводят роликоопору из места крепления. Далее тележка с заменяемым роли ком перемещается по направляющим и выходит из-под ленты. Установка нового ролика осуществляется в обратном порядке.
На мощных конвейерах с широкими лентами должны при меняться установки, обеспечивающие полную механизацию про цесса замены тяжелых роликоопор. Самоходная установка та кого назначения используется, например на карьере «Фортуна»
(ФРГ) для конвейеров с гирляндными роликоопорами и шири ной ленты 3000—3200 мм. Она включает в себя автомобильное шасси с гидравлическими опорами, поворотной телескопической стрелой, оборудованной двумя лебедками с крюками (рис. 6.3, г). Все колеса шасси имеют управление, благодаря чему установка может перемещаться под углом. При навеске гирляндной роликоопоры установка выставляется в исходное горизонтальное положение. Выдвигается стрела, и к ней через канат одной из лебедок подвешивается роликоопора. Стрела с роликоопорой перемещается к дальней стороне ленты и опу скается. Свисающая часть роликоопоры присоединяется к ка нату другой лебедки и поднимается при опускании каната пер вой лебедки. Таким образом, путем перемещения канатов лебе док производится регулировка положения навешиваемой роликоопоры, а затем присоединение ее к раме конвейера. На замену одной роликоопоры массой 250—300 кг уходит 12— 15 мин при следующих параметрах установки: мощность двига теля— 118 кВт, высота подъема и вылет стрелы соответственно 10 и 8 м, вместимость комплектующего конвейера— 10—12 ро-
ликоопор, общая масса — 40 |
т, обслуживающий персонал — |
3 чел. |
массовые узлы, ремонтируемые |
Роликоопоры — наиболее |
горными предприятиями. При ремонтах роликов разборке подвергаются подшипниковые узлы, при этом заменяются уплот нения, подшипники, поврежденные оси. У обрезиненных роликоопор заменяются изношенные резиновые кольца. Поэтому целе сообразно иметь цехи с поточной технологией ремонта роликоопор, включающей отдельно участки: по осмотру и выбраковке, разборке, выпрессовке подшипников, дефектации и мойке дета лей (оси, крышек, корпуса, колец), запрессовке подшипника и закладке смазки, сборке ролика. В этой связи унификация ро ликов имеет большее значение для снижения трудоемкости их ремонтов. На некоторых предприятиях используют ручную или механизированную автоматическую наплавку шеек роликоопор. При автоматической наплавке на приводные барабаны стенда устанавливают ролик, частота вращения шеек которого равна скорости сварки, выполняемой автоматом ТС-17/М. Сварочный автомат монтируется на площадке из текстолита, которая пере мещается вдоль шейки ролика с помощью винта. Флюс засы пают в расходный бачок, откуда он самотеком поступает по го фрированному рукаву к головке сварочного автомата и далее в металлургическую ванночку.
6.3.МОНТАЖ, ОБСЛУЖИВАНИЕ И РЕМОНТ ПРИВОДОВ
ИНАТЯЖНЫХ УСТРОЙСТВ
Монтаж. Привод и натяжные устройства стационарных кон вейеров монтируются на бетонных фундаментах или металличе ских рамах. Анкерные болты устанавливают в колодцы фунда-
V*10* |
291 |
мента и соединяют с рамой привода или натяжного устройства. После точной регулировки положения рамы в горизонтальной и вертикальной плоскостях колодцы заливаются цементным рас твором. Перед сборкой привода проверяется балансировка всех вращающихся узлов. Нарушение балансировки ведет к повы шенным вибрациям рам и металлоконструкций. Сборка привода начинается с установки барабана в подшипниковые узлы рамы, затем вал приводного барабана через муфту соединяют с вход ным валом редуктора. После регулировки положения редук тора, двигателя и соединений все узлы окончательно крепят к раме или фундаменту. Рекомендуемые параметры точности установки барабанов приведены ниже.
|
|
|
|
|
Допустимые |
|
|
|
|
|
отклонения |
Отклонение середины барабанов от оси конвейера, мм |
. . |
2 |
|||
Неперпендикулярность оси барабана продольной оси конвейера, |
1/1000 |
||||
мм/м |
. . |
............... |
. . |
|
|
Негоризонтальность осей барабанов, |
мм . |
. |
1/1000 |
||
Несоосность валов приводного барабана и редуктора, мм |
0,5 |
||||
Отклонение ленты от оси конвейера во время ее движения, мм |
40 |
||||
Для |
шахтных |
конвейеров |
компактность |
привода — один из |
основных показателей технического уровня. Фирма «Доути Меко» (Великобритания) выпускает компактные приводы от крытой конструкции типа МВ-300 мощностью 150 кВт, предна значенные для установки в стесненных условиях при разра ботке тонких пластов угля (рис. 6.4). Высота установки кон сольной части привода, имеющей при транспортировке высоту 940 мм, регулируется. Привод обеспечивает скорость движения ленты 2,54 м/с и имеет гидромуфту, редуктор с зубчатой пере дачей и два приводных барабана. Габаритные размеры при вода после монтажа составляют: ширина 2740, высота 1300, длина 4480 мм.
Для монтажа мощных конвейеров с большим натяжением ленты требуются массивные фундаменты и конструкции. Необ ходимо также учитывать и температурные факторы, при дейст вии которых строительные конструкции (части галерей) испы тывают дополнительные напряжения. В таких случаях целесо образна раздельная компоновка линейной части конвейера от рамы и основания привода (рис. 6.5, а). При этом рама привода крепится к своему основанию через шарнирные стойки, а к ос нованию конвейера — через шарнирные распорки. Основание конвейера жестко соединяется с пролетным строением галереи, а основание привода — со строительной конструкцией здания. Усилие от натяжения ленты через раму привода и распорки пе редается на основание конвейера, т. е. на пролетное строение галереи. Так как между рамой и основанием привода, жестко связанного со строительными конструкциями здания, установ лены шарнирные стойки, горизонтальная нагрузка от натяже ния ленты на строительные конструкции здания не передается.
292
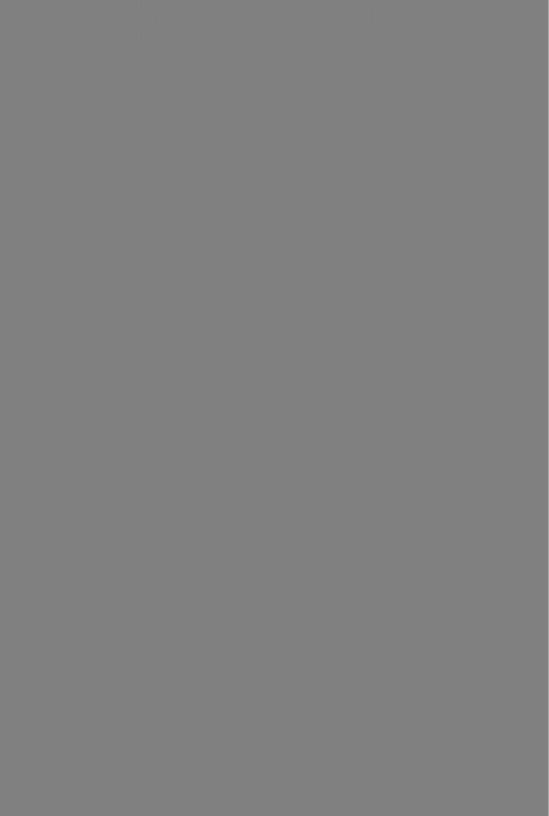
|
|
|
|
Мотор-бараба ны |
|
|
|
Параметры |
МБЛ-4-1 |
КНШ-2 |
МБ-2 |
МБ-1 |
пкти |
МБ |
|
|
|
||||||
Скорость, |
м/с |
1,19 |
1,15 |
1,73 |
1.6 |
1,2 |
1,25 |
Мощность, |
кВт |
1,7 |
2,8 |
2,8 |
4.5 |
7 |
14 |
Габариты м: |
0,243 |
0,295 |
0,285 |
0,32 |
0,335 |
0,5 |
|
диаметр |
|||||||
длина |
приводной |
0,520 |
0,555 |
0,555 |
0,65 |
0,6 |
0,81 |
ширина |
0,580 |
0,62 |
0,62 |
0,71 |
0,66 |
0,9 |
|
станции |
95 |
К |
90 |
115 |
182 |
514 |
|
Масса, кг |
|
122 |
Кроме того, температурные деформации строительных кон струкций не вызывают распора благодаря смещению распорок и стоек. Уменьшаются нагрузки также на основание привода и здание, что позволяет уменьшить сечения несуших конструкций здания и галереи.
Одной из причин, сдерживающих использование ленточных конвейеров в забоях, являются значительные габариты привода по ширине. На шахтах Кривбасса находят применение компакт ные приводы с мотор-барабанами. Они позволяют уменьшить ширину приводного блока до 30—40 %, благодаря сокращению числа монтируемых узлов до одного. Технические характери стики мотор-барабанов приведены в табл. 6.3.
Для снижения динамических нагрузок при доставке крупно кусковых грузов мотор-барабаны устанавливаются на упругих элементах (рис. 6.5, б), работающих на сдвиг— сжатие. При этом происходит дополнительное подтягивание верхней ветви ленты, что также улучшает перемещение лентой крупных ку сков.
Вбарабанах обычного типа упругая компоновка бара
бана осуществляется посредством жесткоустановленных на валу втулок и коаксиально расположенных пружин. Одни концы пружин прикрепляются к втулкам, другие— к обечайке барабана.
На мощных ленточных конвейерах обычно процесс монтажа барабанов включает крепление футеровок, повышающих тяго вые способности привода и улучшающих очистку обечайки.
На шахтах ПО «Ростовуголь» для футеровки приводных ба рабанов конвейеров КЛА250 используются отрезки конвейерной ленты. В обечайке барабанов по всей ширине выполняются два противоположно расположенных выреза. В месте выреза прива ривают широкую металлическую полосу с отверстиями. При фу теровке барабан обертывают лентой и зажимают ее на широ ких полосах с помощью узких планок и болтов (рис. 6.6, а). На дежность крепления футеровки повышается, если использовать резинотросовую ленту. Отрезок из резинотросовой ленты при-
294
Р И С . 6.6.
Монтаж |
футеровок |
на |
барабанах: |
а — эластичной; б — с металлическими сетчатыми |
полосами; в — резиновой с ромбо |
||
образными насечками; |
г — резиновой |
с |
дугообразными элементами |
соединяется с помощью свободных концов тросиков, которые входят в конические отверстия обечайки и фиксируются кони ческими зажимами, планками и шпильками с гайками.
Хорошо зарекомендовали себя барабаны с эластичной фу теровкой, имеющей ребра. Ребра обычно располагаются в два ряда под углом к середине, благодаря чему лента меньше сме щается относительно продольной оси. В качестве ребер можно использовать металлические полосы, привариваемые к обечайке барабана. На полосы сваркой наносится сетка, увеличивающая сцепление барабана с лентой (рис. 6.6, б). На мощных ленточ ных конвейерах фирмы «Штальгрубер Тип-Топ» (ФРГ) обя зательно применение для приводных барабанов резиновых фу теровок толщиной 8—12 мм с симметричными ромбообразными насечками (канавками) глубиной 3—4 мм и шириной 5—7 мм (рис. 6.6, в). Канавки отводят влагу и уменьшают загрязнение барабана. Наклеиваемые резиновые футеровки уменьшают кор розию барабана.
В другом варианте футеровка выполняется в виде резино вого листа, привулканизированного к трем дугообразным эле ментам (рис. 6.6, г), образующим после монтажа цилиндр.
Наибольшей фрикционной способностью обладают футе
ровки |
из |
керамических |
элементов. |
Такая |
футеровка |
обычно |
монтируется из |
отдельных |
прямоугольных или |
дугообразных пластин, имеющих на своей поверхности сфери ческие выступы.
При монтаже редуктора основное внимание уделяется соос ности валов редуктора и электродвигателя, перекос осей кото рых не должен превышать Г. Для исключения перекоса исполь зуются подкладки. Допустимое радиальное смещение осей ва лов определяется технической документацией на конвейер. Окончательное крепление редукторов и электродвигателей мо жно производить только после регулировки всех узлов привода.
Тормозное устройство выставляется так, чтобы соблюдалась параллельность тормозных колодок и поверхности шкива. Пятно касания каждой колодки со шкивом должно быть не ме нее 70 % рабочей поверхности колодки. По окончании сборки приводной станции необходимо залить маслом редукторы, ра бочей жидкостью гидромуфты, заправить смазкой подшипники и провести обкатку приводных блоков. Для обеспечения нор мальной смазки зубчатых передач редукторы должны быть установлены горизонтально. В качестве фрикционных материа лов для тормозных устройств должны применяться только те материалы, которые рекомендованы заводами-изготовителями. Фрикционные элементы тормозных устройств должны быть на дежно защищены от попадания на них масла, воды, грязи, ра бочих жидкостей из гидромуфт и гидропривода.
Монтаж натяжных устройств в соответствии с правилами эксплуатации ленточных конвейеров должен осуществляться таким образом, чтобы смещение направляющих для перемеще ния кареток было минимальным, не превышающим 10 мм на длине 8 м. Превышение допускаемых смещений приводит к за тормаживанию хода кареток и нарушению режима натяжения ленты в период пуска и установившегося движения ленты. На мощных ленточных конвейерах монтаж натяжных кареток целесообразно производить за загрузочным устройством. В этом случае монтаж загрузочного устройства и загрузочной части конвейера менее трудоемок, так как осуществляется до навески и стыковки ленты. При ограничении свободного пространства в подземных условиях загрузочное устройство монтируют за натяжными каретками. Однако при этом монтаж загрузочного устройства и загрузочной части конвейера целесообразно осу ществлять уже после навески и стыковки ленты.
Обслуживание. Техническое обслуживание и надзор за со стоянием приводов и натяжных устройств заключается в про филактическом осмотре, чистке, смазке, регулировке, наладке, устранении мелких неисправностей, смазке механизмов и про ведении различных видов ремонта в соответствии с инструк. циями на оборудование. Технический надзор за исправным со стоянием электрической аппаратуры осуществляется во время ежесменных и периодических осмотров и ревизий. К основным видам работ, проводимым при техническом обслуживании электрической аппаратуры привода, относятся: обдувка аппа
ратуры сжатым воздухом для удаления осевшей пыли; зачистка подгоревших контактов; регулировка силы прижатия контактов; проверка состояния пускорегулировочных сопротивлений; за мена негодных катушек, реле; пайка и затяжка поврежденных мест проводников; проверка заземления.
Технический надзор за электродвигателями заключается в регулярной проверке состояния изоляции обмоток, щеточных аппаратов и подшипниковых узлов. Подшипниковые узлы со временных электродвигателей мощных ленточных конвейеров в большинстве случаев смазываются консистентной закладной смазкой, заменяемой через 8—10 месяцев. Если при работе электродвигателя обнаруживается перегрев (свыше 60 °С) под шипника, устанавливается и устраняется причина перегрева. Пыль, оседающая на корпусе и особенно на обмотках электро двигателей, сильно снижает теплоотдачу двигателя и обмоток, что уменьшает сроки службы изоляции. Поэтому при ежене дельных и плановых ТО электродвигатель продувают сжатым воздухом. У электродвигателей, работающих на открытом воз духе в осенне-зимний период, вследствие высокой влажности воздуха снижается прочность электрической изоляции обмоток. В этих случаях необходимо регулярно измерять сопротивление изоляции обмоток, которое должно быть не менее 3 МОм в хо лодном состоянии и не менее 0,5 МОм — в нагретом. У асин хронных двигателей с фазовым ротором при ТО зачищают кон тактные кольца, заменяют износившиеся щетки и ремонтируют шеточные аппараты. У электродвигателей постоянного тока за меняют износившиеся щетки коллектора, производят пайку ослабших контактов.
Повреждения изоляции лобовых частей обмоток устраня ются путем нанесения изоляционных лаков или применения изоляционных лент.
Для соединительных кулачковых и фрикционных муфт ха рактерен износ рабочих поверхностей кулачков и фрикционных накладок. При ТО поверхности кулачков зачищаются напиль никами или при значительном износе наплавляются, а затем обрабатываются. При износе фрикционных накладок, превы шающем 50 % их начальной толщины, они подлежат замене. Рабочие поверхности фрикционных дисков со следами износа зачищаются или шлифуются. Фрикционные муфты ленточных конвейеров обычно рассчитываются на работу при сухом тре нии. Попадание на трущиеся поверхности муфты смазки резко уменьшает коэффициент трения, поэтому необходимо следить за тем, чтобы масло не попадало в фрикционные муфты, а при ТО и плановых ремонтах следует промывать детали муфт в бензине или дихлорэтане.
Зубчатые передачи регулярно пополняются смазкой. Не раз решается работа механизма при наличии хотя бы одного зуба, сломанного на половину длины. Изношенные зубчатые колеса выбраковываются во время проведения плановых ремонтов.
|
|
|
Периодич |
|
|
Место смазки |
Тип смазки, масла |
ность |
|
Система смазки |
|
смазывания, |
|
||||
|
|
|
машино-ч |
|
|
Подшипники |
УС-2 (ГОСТ 1033—79) |
506—550 |
Централизованная гу |
||
барабанов |
|
|
|
стой |
смазкой или |
Зубчатые |
муф |
УС-2 (ГОСТ 1033—79) |
1500—1700 |
шприцеванием |
|
Закладная |
|||||
ты приводов |
Индустриальное И-50А |
1500—1700 |
Заливка масла в кар |
||
Редуктор |
при |
||||
вода |
|
(ГОСТ 20799—75) |
|
тер; |
централизован |
Подшипники |
1—13 жировая |
3000—4000 |
ная жидкой смазкой |
||
Закладная смазка |
|||||
электродвига |
|
|
|
|
|
телей |
|
УС-2 (ГОСТ 1033—79) |
1500—1700 |
Ручная шприцевани |
|
Оси блоков на |
|||||
тяжных |
уст |
|
|
ем |
|
ройств |
|
|
|
|
|
Ненормальные условия работы зубчатых передач возникают вследствие износа зубьев колес и подшипников валов, на кото рые насажены колеса. В последнем случае возникают перекос и торцевое биение колес, резко увеличиваются местные контакт ные и изгибные напряжения в зубьях. О нарушении в работе зубчатых передач судят по вибрации, перегреву масла и шуму передачи. Для ревизии состояния зубьев вскрывают люки ре дукторов и вращают зубчатые колеса вручную или от электро двигателя при самых малых оборотах.
Не реже одного раза в месяц необходимо проверять состоя ние направляющих для перемещения кареток натяжных уст ройств. Проверяются периодически плавность пуска конвейера под нагрузкой. На ленточных конвейерах с раздельным приво дом барабанов рекомендуется осуществлять проверку распре деления нагрузки между приводными барабанами с помощью амперметров.
Постоянно контролируются крепление и степень износа фу теровки барабанов. Не допускается подсыпка песка, канифоли и т. п. между лентой и приводными барабанами. Смазка меха низмов привода и натяжных устройств осуществляется по кар там смазки, прилагаемым к инструкциям по техническому об служиванию. Данные о режиме смазки приводов и натяжных устройств ленточных конвейеров для открытых работ приведены в табл. 6.4.
Основные технические неисправности приводов и натяжных устройств, способы их устранения приведены в табл. 6.5.
Ремонт. Ремонт привода и натяжных устройств осуществля ется путем замены или восстановления узлов и деталей в теку щий, средний, и капитальный ремонты. При капитальном ре монте производится почти полный демонтаж механизмов; при
Неисправность |
Причины |
Способ устранения |
При включении в сеть электродви гатель не вращается или вращается очень медленно
Внезапный останов электродвигателя
Обрыв в цепи статора. Подгорание кон тактов пускателя. Неправильно подключен электродвигатель. Механическое заедание
Сработал датчик скорости (пробуксовки) Сработал конечный выключатель хода на тяжной каретки Заштыбовался загрузочный узел конвейера
Вышел из строя электромагнит тормоза
Проверить электрическую цепь двигателя. Устранить причину заедания
Устранить причину снижения скорости лен ты, нарушения работы натяжного и загру зочного устройств, тормоза
Вибрация электродвигателя
Повышенный нагрев корпуса электро двигателя
Повышенный нагрев подшипников электродвигателя
Гидромуфта греется при нормальной нагрузке, буксует
Утечка масла из гидромуфты
Нарушена центровка электродвигателя и редуктора. Повреждены подшипники элек тродвигателя Перегрузка электродвигателя
Забились грязью вентиляционные каналы
Межвитковое замыкание одной из фаз об мотки статора
Отсутствует смазка Вышел из строя подшипник
Плохая вентиляция гидромуфты, недоста точный уровень масла
Ослаблена затяжка пробок для заливки масла Вышли из строя уплотнения
Произвести центровку электродвигателя и редуктора
Заменить подшипники Уменьшить нагрузку на конвейер до расчет ной величины
Прочистить вентиляционные каналы Заменить электродвигатель
Добавить или заменить смазку Заменить подшипник
Долить масло до нормы
Затянуть пробки
Заменить уплотнения
со |
|
ПРОДОЛЖЕНИЕ ТАБЛ. 6.6 |
о |
|
|
|
|
|
Неисправность |
Причины |
Способ устранения |
Повышенный шум в редукторе |
Отсутствие или загрязнение масла |
|
Выход из строя подшипников |
|
Чрезмерный износ зубчатых шестерен, по |
|
ломка зубьев шестерен |
|
Плохая сборка редуктора |
Проверить уровень и состояние масла Заменить подшипники и шестерни Устранить дефекты сборки редуктора
Сильный нагрев корпуса редуктора Поврежден подшипник Засорились подшипники или редуктор
Утечка масла по плоскости разъема и выходным валам редуктора
При включении в сеть электродви гатель?вращается, приводные бара баны не^вращаются
Отсутствие или сильное загрязнение масла В редуктор залито большое количество ма сла
Ослаблены болты по плоскости разъема
Износились уплотнения Срезаны или выпали вкладыши муфты
Повреждена соединительная муфта Отсутствие масла в гидромуфте Расплавились предохранительные вставки гидромуфты
Сильный нагрев подшипников бара |
Отсутствие смазки или загрязнение смазки |
бана |
Повреждения в подшипниках |
|
Перекос барабанов |
Заменить подшипник Промыть редуктор и подшипники, заменить масло Долить или заменить масло
Слить часть масла
Плоскость разъема промыть, покрыть нитро краской, затянуть болты
Заменить уплотнения Заменить вкладыши Залить гидромуфту маслом
Заменить предохранительные вставки гидро муфты
Заменить смазку Промыть и осмотреть подшипники, заменить новыми
Проверить монтаж барабанов, устранить пе рекос
Стопорение барабана |
|
Повреждение подшипников |
Заменить подшипники |
|
Проворачивание |
барабана |
относи |
Нарушение фиксации барабана на валу |
Проверить шпонку на барабане и установоч |
тельно вала |
|
|
|
ные болты |
Эксцентричная |
установка |
барабана |
Не затянуты болты на ступице барабана |
Затянуть или заменить болты |
|
|
|
или на подшипниковых узлах |
|
Колодочный тормоз не зажимает |
Заедание в шарнирах рычажной системы, |
шкив |
отсутствие смазки в пальцах |
|
Вышли из строя пружины |
|
Попадание смазки на шкив |
|
Чрезмерный износ колодок |
Удары и вибрация при торможении |
Неравномерный износ шкива по окружности |
Колодки тормоза не отходят от шкива |
Чрезмерное натяжение пружин и наруше |
|
ние регулировки колодок |
|
Сгорели катушки электродвигателя |
Появление гари и дыма у колодок, |
Сильное трение колодок из-за неравномер |
быстрый износ колодок |
ного отхода |
Сбегание ленты с барабана натяжно |
Перекос барабана |
го устройства |
|
Каретка натяжного устройства затор |
Перекос в ходовой части кареток |
маживается |
Загрязнение или повреждение подшипников |
После включения электродвигателя |
Выход из строя муфт или цепной передачи |
^ барабан лебедки не вращается |
|
о |
|
Устранить заедание, смазать пальцы
Отрегулировать или заменить пружины Промыть шкив и колодки Заменить футеровки колодок
Проточить на станке колодки или заменить
Отрегулировать натяжение пружин. Произ вести регулировку колодок Заменить катушки
Отрегулировать отход колодок
Произвести центровку барабана
Улучшить сборку кареток Промыть или заменить подшипники
Заменить полумуфты или роликовую цепь
среднем 60—80%, при текущем 40—60% объема капитального ремонта. Изношенные зубчатые передачи, подшипники, тормоз ные шкивы, шлицевые и резьбовые соединения после предель ного износа не восстанавливают, а заменяют новыми. Разрабо танные шпоночные пазы по ширине более 5 % исправляют на плавкой с последующим фрезерованием. Шпоночные пазы могут заплавляться полностью, при этом новые пазы фрезеру ются полностью. Изношенные подшипники собираются и пере даются специализированным ремонтным заводам. Посадочные места под подшипниками качения восстанавливают хромиро ванием с нанесением слоя хрома толщиной 0,3 мм и последую щей шлифовкой под нормальный размер. Большие износы от верстий восполняются наплавкой, после чего следует расточка. Цилиндрические детали — валы, оси, пальцы восстанавлива ются наплавкой с припуском на обработку 3—5 мм. Трещины в корпусах редукторов заваривают электродуговой или газовой сваркой, иногда заделывают синтетическими клеями и полимер ными материалами.
Ремонт барабанов включает в себя разборку подшипнико вых узлов, промывку и сборку или замену изношенных деталей и узлов. Особое внимание уделяется состоянию футеровки, ко торая при повреждении и износе заменяется новой. Демонтаж узлов привода мощных ленточных конвейеров производится на ремонтных площадках с помощью встроенных или привлечен ных грузоподъемных средств. Дальнейшая разборка и ремонт осуществляются в заводских условиях. Привод снимается, как правило, в сборе — редуктор, электродвигатель, рама. При го довых ремонтах, когда нет необходимости полностью демонти ровать привод, снимается только крышка редуктора и произво дится замена изношенных деталей внутри редуктора. При ре монтах механизмов привода и натяжного устройства последние должны быть надежно закреплены противоугонными устрой ствами и якорями. В грузовых натяжных устройствах укорачи вается или заменяется вытянувшийся канат.
6.4.МОНТАЖ И СТЫКОВКА КОНВЕЙЕРНЫХ ЛЕНТ
6.4.1.ОПЕРАЦИИ ПО МОНТАЖУ ЛЕНТ
Кчислу наиболее трудоемких операций по введению мощ ных ленточных конвейеров в эксплуатацию относится монтаж лент. Значительная масса широких лент повышенной прочности
(особенно резинотросовых) привела к необходимости примене ния специальных вспомогательных средств, обеспечивающих ме ханизацию труда обслуживающего персонала. Монтаж ленты до стыковки в общем случае включает следующие виды работ: до ставку, навеску, стягивание, фиксацию и разделку.
Доставка. Доставка лент в заводской или специальной упа ковке в виде бухт осуществляется с помощью подъемно-транс
портных и ходовых механизмов к месту установки конвейера. При доставке ленты в шахту по вертикальным стволам или на клонным выработкам используются вагонетки. На платформу шахтной вагонетки устанавливаются электродвигатель, редук тор и вал с бобиной и подшипниками. Для предотвращения оп рокидывания платформы при наматывании или разматывании ленты предусматриваются захваты, взаимодействующие с го ловками рельсов. Размеры бухт могут превышать сечение гор ных выработок. Поэтому целесообразно сматывание ленты с на моточной бухты большого диаметра производить на несколько рулонов без разделения ленты на части. Для этого барабан для намотки ленты монтируют из боковин с двумя намоточными цилиндрами (рис. 6.7, а). Наматывание рулонов с помощью такого барабана производится следующим образом. Середину части ленты, которую предполагается намотать на барабан, по мещают между цилиндрами и собирают барабан с козелками
иприводом. При вращении барабана лента наматывается в два слоя. После намотки рулона боковины демонтируются. При этом цилиндры сближаются под действием упругих сил рулона
ивынимаются из него. После выемки цилиндров рулон скреп ляют для предотвращения разматывания. Затем тележку с руло
ном перемещают от намоточной бухты на расстояние, равное половине длины ленты, рассчитанной для второго рулона. В том же порядке производят намотку второго и всех последующих рулонов. Состав тележек с рулонами транспортируется по на клонным и горизонтальным выработкам ограниченного сечения. Разматывание рулонов в шахте производят в обратном порядке путем перекатывания их по почве выработки или при помощи барабана. Во втором случае цилиндры вставляют в очередной рулон и монтируют барабан. Конец ленты вытягивают с по мощью лебедки. При вращении барабана другой конец ленты с остальными рулонами необходимо оттягивать локомотивом или лебедкой. Для предотвращения повреждения обкладки ленты при перекатывании рулонов по почве выработки может быть разостлана бывшая в употреблении лента.
ВНПО «Углемеханизация» выпускается устройство типа УТК для доставки в шахту резинотканевых лент шириной 1200 мм в заводской упаковке по вертикальным стволам и гор ным выработкам с углом наклона до 20° Устройство представ ляет собой ходовую платформу с поворотными опорами, на оси которых надеваются заводские бухты ленты. Платформа обору дована захватами для закрепления ее на рельсах при выполне нии погрузочно-разгрузочных работ и стопорными механизмами для предотвращения самопроизвольного поворота опор, обеспе чивающих сматывание ленты под углом до 10° к оси рельсового
пути.
Резинотросовые ленты 2РТЛО-2500 поставляются заводамиизготовителями на предприятия в бухтах диаметром 3000 мм и массой 10—12 т. Из-за больших габаритов бухты лента достав-
РИС. 6.7.
Средства для доставки и навески лент:
?»S i t u ‘?ЛЯ Разделения бухты на несколько рулонов: / — барабан; 2 —лента;
2вити”ЛИ/НД^ |
тележки! б — устройство с |
бухтой |
и |
приводной кассетой для |
||
rbInalvaJ^yX/Ta' к?, Ролик* 5 — кассета; 4 — привод; |
в — бухта с |
приводным тросом |
||||
на салазках. 1 |
бухта; 2 — салазки; |
3 — трос; |
г — бухта |
в виде |
катучего барабана: |
|
|
1 — барабан; |
2 — кожух; 3 — рукоять |
|
ляется в шахту отрезками длиной только 80—90 м. Для устра нения этого недостатка на шахтах ПО «Донецкуголь» исполь зуются специальная кассета и устройство для перемотки. Кас сета монтируется на устройстве для перемотки, включающем в себя привод, отклоняющий ролик, тормоз и бухту, с которой перематывается лента (рис. 6.7, б). Кассету после намотки на нее ленты снимают с рамы устройства и устанавливают на те лежку, транспортируют до места монтажа конвейера, где ленту разматывают с помощью лебедок. Устройство позволяет спу скать в шахту ленту длиной 250—300 м при уменьшении вре мени на монтажные работы.
Для механизации процесса замены ленты в комплексе горно транспортного оборудования КГТО Лебединского рудника НИИКМА применена бухта, устанавливаемая на подшипни ках качения. Бухта имеет две щеки (рис. 6.7, в), одна из которых съемная, зажим для крепления конца ленты, трос диа метром 17 мм и длиной 60 м для привода бухты, стойки и са лазки. При демонтаже старой ленты салазки с помощью тягача С-100 располагают с торца конвейера. Затем трос присоеди няют к тягачу, который перемещается параллельно конвейеру, и вращают таким образом бухту. Бухту со старой лентой транс портируют к месту складирования, где демонтируется щека, освобождается зажим, поднимается вторая щека бухты, в ре зультате чего рулон с ленты снимается.
Простую конструкцию имеют бухты в виде катучего бара бана (рис. 6.7, г). Он включает в себя рукоять с подшипниками, на которых устанвлен вал барабана. Вал приводится во враще ние ручной зубчатой передачей, монтируемой на его шлицах. Барабан имеет кожух с опорными кольцами. Отрезок ленты на матывается через прорезь в кожухе с помощью ручного при вода. Затем бухта через рукоять присоединяется к трактору и буксируется к месту монтажа.
Навеска. Различают два вида навески ленты на конвейер: навеска ленты (обычно новой) при монтаже конвейера и за мена изношенной (старой) ленты новой по графику ремонтных работ. К вспомогательным средствам навески ленты относятся лебедки, привод конвейера (часто со старой лентой, выполняю щей функции тягового органа для новой ленты), специальные приводные катушки для намотки старой ленты и протягивания новой ленты и различные подъемно-транспортные механизмы.
Для шахт и обогатительных фабрик институтом «Донгипрошахт» рекомендован и внедрен способ навески ленты на кон вейер, заключающийся в следующем. Изношенную ленту (рис. 6.8, а) разрезают, конец новой ленты с бобины соединяют с концом холостой ветви старой ленты, а второй конец изношен ной ленты прикрепляют к канату, навитому на барабан. Так как новая лента соединена со старой, то при наматывании из ношенной ленты на барабан новая накатывается на роликоопоры. После укладки новой ленты ее концы стягиваются и стыкуются. Бобина и барабан съемные, устанавливаются только на время замены ленты, после чего они с помощью грузоподъ-
-а — новой |
с |
помощью |
барабана |
для |
старой |
ленты: |
1 — бобина |
с новой |
лентой; |
2 — |
||||
барабан |
для |
сматывания старой |
ленты; б — с |
использованием |
одной бухты для |
на |
||||||||
мотки старой и протягивания новой |
лент: |
1 |
— старая |
лента; |
2 — новая |
лента; |
3 — |
|||||||
бухты; |
4 |
— обводные |
ролики; |
в —■с |
несколькими бухтами на |
длинных |
конвейерах: |
|||||||
/ — старая |
лента; 2 — новая лента; 3 — бухты; |
г — с |
использованием двух |
конвейеров: |
||||||||||
|
|
|
1 — старая |
лента; |
2 — новая лента; |
3 — бухта |
|
|
емного устройства грузятся на автомашину и доставляются на
склад оборудования. Этот способ позволяет механизировать все операции по замене конвейерных лент.
В схеме навески с двумя бухтами одна из бухт может ис пользоваться одновременно для намотки старой и протягивания новой ленты. Бухты для новой и старой лент устанавливаются над конвейером (рис. 6.8, б). Старая лента разрезается, и один ее конец закрепляется на бухте, а другой — соединяется с кон цом новой ленты. При этом отрезок новой ленты обводится во круг обводного ролика и бухты старой ленты. Затем включа ется привод конвейера и осуществляется навеска ленты, пока участок соединения ленты не достигнет места установки обвод ного ролика. Здесь производится перестыковка концов лент, после чего бухты со старой и новой лентами демонтируются. Специальная установка бухт над конвейером позволяет совме стить основные операции по навеске ленты.
Для навески лент на длинных конвейерах требуется уста новка нескольких бухт с новой лентой (рис. 6.8, в).Подготовка бухт осуществляется до замены ленты. При этом в каждой бухте может быть несколько соединенных предварительно от резков новой ленты. Далее на концевых участках конвейера располагаются бухты для старой и новой лент. Конвейер оста навливают, и старая лента разрезается в двух местах в зоне расположения бухт. Один конец разрезанного участка старой ленты заводится на бухту, а другой соединяется с концом но вой ленты. Включением привода бухт для старых лент произво дятся сматывание и навеска новых лент, демонтаж и намотка старой ленты. После укладки новой ленты концы ее стягива ются и стыкуются вулканизацией. В процессе сматывания и на мотки лент скорость перемещения их изменяется в результате изменения диаметров бухт с лентой, что приводит к самопро извольному ослаблению натяжения ленты и нарушению ре жима навески. Для стабилизации скорости движения лент в приводе бухт используются электродвигатели с фазным рото ром, позволяющие регулировать частоту вращения.
На подземных ленточных конвейерах монтаж бухт для но вых лент осуществляется путем подвески их к кровле выра ботки. На шахте «Россия» ПО «Донецкуголь» протягивание новой ленты с подвешенной к кровле бухты производят после ре верса конвейера. Старая и новая ленты, соединенные в голов ной части конвейера (рис. 6.8, г), перемещаются в обратную сторону посредством включения двухбарабаниого привода кон вейера. При этом один конец старой ленты прикрепляется к ленте последующего конвейера и включением привода послед него транспортируется к головной его части. Внедрение этого способа навески позволило снизить затраты времени на замену лент в два раза.
На зарубежных карьерах широкое применение нашли само ходные тягачи с навесным оборудованием для замены лент. На
весное оборудование, применяемое в ГДР, предназначено для снятия с конвейера, последующей транспортировки и разгрузки ленты для ремонта. Оно подвешивается к траверсе тягача и включает в себя платформу со скользящими опорами, бухту с приводом и грузовую стрелу для установки бухты на плат форму. Под бухтой имеется тележка с гидроцилиндрами для поддержки бухты. После намотки ленты на бухту тягач дви жется к месту разгрузки, где бухта поднимается гидроцилинд рами и опускается на тележку, которая перемещает ее вниз. Далее поддерживающий балансир тележки опрокидывается, и бухта скатывается на разгрузочную площадку.
В условиях эксплуатации мощных ленточных конвейеров, устанавливаемых в наклонных горных выработках, где требо вания к безопасности и трудоемкости работ повышены, счита ется целесообразным использовать специальные лентопротяж ные механизмы. Так, лентопротяжные механизмы конструк ции фирмы «Хаммеверк Рихард Нэшер» (ФРГ) снабжены роликами, прижимающими с определенным углом обхвата ленту к приводному барабану. Механизмы оснащаются в основном пневмодвигателями. Мощность последних от 7,4 до 74 кВт, раз виваемое тяговое усилие до 80 кН при скорости перемещения ленты 0,8 м/с. Уменьшение скорости перемещения ленты до 0,4 м/с позволило довести тяговое усилие для данного типа механизмов до 160 кН при установленной мощности привода до 74 кВт.
Стягивание и фиксация. После навески ленты осуществля ется стягивание и фиксация (зажим) ее концов так, чтобы в процессе стыковки не произошло самопроизвольного натяже ния ленты. При этом обязательно применение средств механи зации. Вспомогательные средства механизации для работы с лентами шириной 1000 и 1200 мм изготавливаются серийно Краснолучским и Александровским машиностроительными за водами. Они представляют собой две пары зажимов из швел леров с блоками для каната, стягиваемых лебедкой или поли спастом и фиксируемых стяжками для сохранения положения концов ленты при стыковке. На многих горных предприятиях силами ремонтных служб создаются и успешно применяются для конкретных условий различные вспомогательные меха низмы.
При перемещении концов широких лент тяговый орган (ка нат) закрепляют, например с помощью пластины с заклепками таким образом, чтобы узел соединения минимально воздейство вал на роликоопоры (рис. 6.9, а). К пластине привариваются опорные щеки, к которым посредством прицепного устройства ПЭС-3 присоединяется канат лебедки. Для более узких лент рекомендуется использовать зажимные механизмы, исключаю щие повреждение ленты. Предлагаются различные конструкции захватов, чаще роликового типа (рис. 6.9, б). На рукояти мон тируются цилиндрический и эксцентричный ролики, между
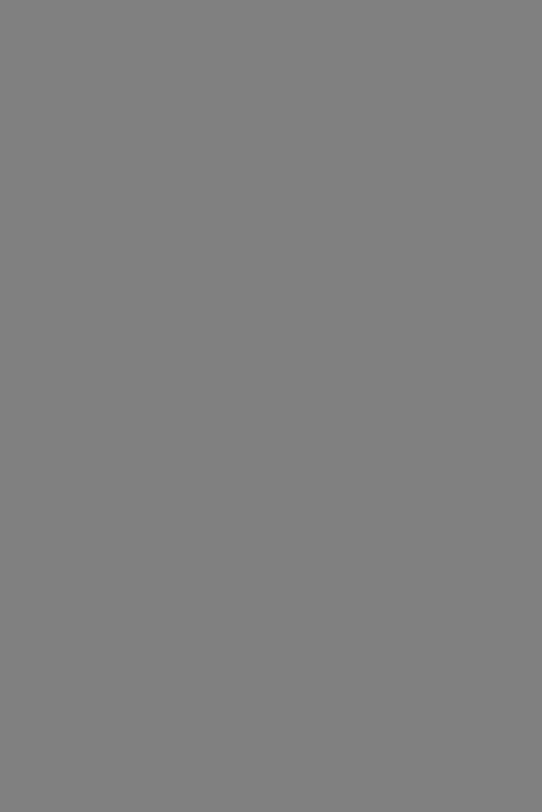
ленты зажимная планка поворачивается и прижимает ленту к боковым роликам роликоопоры или к опорной плите, которая предварительно устанавливается под лентой. Достоинства дан ной конструкции — простота в изготовлении и легкость обслу живания.
Разделка. Надежность работы стыков во многом зависит от качества разделки концов ленты. Стыкуемые поверхности дол жны иметь определенную шероховатость, чистоту, постоянную толщину при отсутствии неровных срезов, порезов и других по вреждений. Разделка ленты включает в себя операции по рас слаиванию или фрезерной обработке обкладок и прокладок, об резке и обработке шерохованием. Все операции производятся вручную приспособлениями или с использованием специальных приводных механизмов и разделочных столов. Перед разделкой концов ленты производится необходимая разметка. В резино тканевых лентах отделяемые обкладки прочно связаны с край ними прокладками, поэтому нарезка ступеней требует исполь зования ножа, захватывающих и отслаивающих ручных или приводных механизмов. В простейшем случае обкладки или прокладки подрезаются на заданную глубину разрезаются на полоски, захватываются клещами и отделяются.
Для ручного расслаивания (рис. 6.10, а) прокладок лент шириной до 1000 мм целесообразно использовать трубу дли ной 1200 мм и диаметром 50—60 мм. В трубе выполняется
|
|
|
РИС. |
6.10. |
|
|
|
|
|
|
Устройства: |
|
|
|
|
а — для |
ручного |
расслаивания ленты |
с помощью трубы: / — труба; |
2 — рукоять; |
3 — |
||
прижимные пластины; 4 — рама; б — для |
разделки широких |
лент: |
/ — тележка; |
2 — |
|||
опорный |
ролик; |
3 — направляющая |
балка; |
4 —захват для |
ленты; |
5 — лебедка; |
$ — |
источник |
питания; в — для бесступенчатой |
разделки ленты |
фрезерованием: / — опор |
||||
|
|
ный стол; 2 — цилиндрическая фреза; 3 — привод |
|
|
прямоугольный паз размером 1050X10 мм и просверливаются отверстия для вставных рукоятей. Такое устройство целесооб разно монтировать между двумя прямоугольными рамами, ос нащенными поперечинами с прижимными и направляющими пластинами с болтами. На участке между пластинами осущест вляют разделку ленты. Для этого участок ленты длиной 60 мм расслаивают с помощью ножа, заводят прокладку в паз и вра щением трубы производят расслаивание на заданную длину.
Разделка широких резинотканевых лент осуществляется устройством, обеспечивающим разделку отслаиваемого слоя с использованием привода (рис. 6.10, б). Устройство состоит из передвижной тележки, на одном конце которой смонтированы направляющая балка и опорный ролик, служащий для подачи ленты к месту разделки. На другом конце тележки располо жена вертикальная рама, в нижней части которой подвижно в поперечном направлении установлена лебедка. На конце ка ната лебедки имеется самозатягивающийся захват в виде кле щей. Верхняя часть вертикальной рамы оснащена источником питания из аккумуляторных батарей и пультом управления. Пе ред разделкой лента фиксируется на прижимной балке. Ле бедку переводят в крайнее положение и клещами захватывают полосу отделяемой обкладки или прокладки. Затем включают лебедку и производят разделку ленты. Достоинства конструк ции: высокое качество разделки ленты, исключающей порывы; возможность быстрого перемещения от одного конвейера к дру гому, автономность электропитания привода.
Послойная разделка концов широкой ленты путем расслаи вания даже с использованием механизированных средств тре бует много времени. Так, выполнение работ по подготовке и вулканизации одного стыка ленты шириной 1400 мм занимает не менее 15—22 ч. Причем свыше 2/3 этого времени приходится на подготовку концов ленты (придание им ступенчатой формы). Для ускорения процесса разработаны и внедрены механизмы с рабочим органом режущего типа. Рабочий инструмент меха низма представляет собой абразивный валик или диск с рез цами, имеющими режущую и подрезную кромки. Абразивный валик или диск устанавливается на валу. Вал посредством си стемы шестерен соединяется с приводным валом двигателя, смонтированным на регулируемых по высоте опорных катках. Для перемещения устройства служат ручки, покрытые электро изоляцией. Обрабатывающий инструмент с системой шестерен закрыт кожухом. Устройство работает следующим образом. С помощью опорных катков устанавливают глубину резания, равную суммарной толщине обкладки и одной прокладки. Держа устройство за ручки, устанавливают его на ленте так, чтобы зубья обрабатывающего инструмента находились на от меченной линии стыка. При включении устройства углубляют режущий инструмент на заданную глубину. Затем, перемещая устройство на опорных катках, снимают обкладку и один слой
прокладки. После снятия слоя ленты размечают ступеньки и опорными катками устанавливают глубину резания, равную толщине одной прокладки обрабатываемой ленты. Отступив на одну ступеньку от конца стыка, снимают один слой прокладки. Затем, отступив еще на одну ступеньку, опять снимают слой прокладки и т. д. Разделку ленты заканчивают, когда на по следней ступеньке останется один слой прокладки с обкладкой.
Хорошие результаты получены при бесступенчатой разделке концов ленты (рис. 6.10, в). В этом случае стыкуемым концам ленты придается форма клина с помощью расположенного под углом рабочего органа в виде цилиндра. Угол скоса ленты, уло женной на подвижную плиту, составляет 1,5—8°. На поверхно сти полого цилиндра закрепляют спиральное лезвие треуголь ного сечения. Цилиндр устанавилвают в подшипниках на пово ротной в вертикальной плоскости опоре. Рабочий орган имеет электродвигатель, соединенный через муфту с осью цилиндра. Положение цилиндра регулируют по высоте в зависимости от толщины ленты. Регулируется также и угол положения ци линдра относительно плоскости ленты для получения среза конца ленты под заданным углом. При обработке ленты плита подается навстречу вращающемуся цилиндру. В результате об работки получается ровная поверхность на стыкуемых концах ленты. Благодаря этому уменьшается вероятность возникнове ния воздушных пузырей и повышается прочность стыка. Вне дрение устройства на центральной обогатительной фабрике «Кальмиусская» в Донбассе позволило существенно сократить продолжительность обработки концов ленты, уменьшить за траты труда.
Для сравнения прочности ступенчатых и клиновидных сты ков, соединяемых вулканизацией, в Макеевском НИИ по без опасности работ в горной промышленности были проведены ис пытания на разрывной машине ЦМЛ-500. Испытывался ряд лент: капроновая 2ТЛК-150, лавсановая ЛХ-120 и комбиниро ванная 2НБКНЛ-100. Испытания показали, что прочность сту пенчатых и клиновидных стыков практически одинакова.
Обрезка ленты осуществляется острыми ручными ножами или приводными фрезами. Для очистки стыкуемых концов ленты применяют шероховку поверхностей с помощью ручной или приводной щетки. После шероховки поверхности очищают от пыли и крошек резины, тщательно протирают и просуши вают.
6.4.2. МЕТОДЫ И СРЕДСТВА СТЫКОВКИ ЛЕНТ
Для мощных ленточных конвейеров большое значение имеет совершенствование технологии и средств стыковки. Например, на карьерах 70 % обрывов лент приходится на стыковые соеди нения. Конвейеры горнотранспортных комплексов простаивают до 27 % общего времени работы из-за порыва стыковых соеди-
нений. В настоящее время применены и испытаны следующие методы стыковки лент: горячей и холодной вулканизацией, ме ханическая с помощью шарниров, скоб, болтов, заклепок и сшивки, комбинированная. Известна также стыковка, при кото рой используется специальное исполнение ленты.
Стыковка горячей вулканизацией. Наиболее надежный спо соб стыковки для лент мощных конвейеров — метод горячей вулканизации. Этот метод совершенствуется главным образом в направлении оптимизации режима вулканизации (по темпе ратуре и давлению), размеров, конструкции и выбору материа лов элементов стыка. Для резинотканевых лент, стыкуемых го рячей вулканизацией, характерно разделение конструкций сты ков в зависимости от числа и вида тканевых прокладок в ленте.
Для лент с каркасом из одной усиленной прокладки, не под дающейся расслоению, предусматривается разрезание обнажен ных концов прокладки на полосы параллельно кромкам ленты (рис. 6.11 а). Полосы поочередно накладывают друг на друга и покрывают резиной или другим материалом, обеспечиваю щим их соединение.
Стыковку шахтных лент из поливинилхлорида целесооб разно осуществлять путем разрезания концов ленты в виде зубчатого профиля (рис. 6.11,6). На нагревательную плиту укла дывается полиамидная ткань. Затем оба конца ленты вставля ются зубьями друг в друга, при этом между боковыми сторо нами зубьев помещаются полоски из смеси поливинилхлорида
ивулканизируемого нитрильного каучука. После складывания
исоединения внахлестку полиамидной ткани стыкуемый уча сток укладывается на нагревательные плиты пресса, и произ водится вулканизация стыка. Угол наклона боковых сторон зубьев к продольной оси ленты должен составлять не более 3° Минимальное соотношение длины зубьев к их основанию со ставляет 3:1. Длина стыка однопрокладочных лент из многоосновной ткани МК-300-2 должна быть 500 мм при ширине ленты до 650 мм и не менее 750 мм при ширине ленты более 650 мм.
Вдвухпрокладочных лентах на одном конце ленты снима ются обкладки, а на другом — центральный слой между про кладками (рис. 6.11, в). Концы ленты после совмещения вулка низируются. Однако при этом возникает утолщение, которое
устраняют, если на одном конце ленты вырезают центральный слой и одну прокладку.
В многопрокладочных резинотканевых лентах применяется ступенчатая схема стыковки с симметричной (рис. 6.11, г) или с асимметричной (рис. 6.11, д) разделкой прокладок. Во втором случае стык имеет выступы, но обладает большей сопротивляе мостью разрушению. Для повышения прочности стыка вдоль кромок концов ленты выполняются отверстия, которые заполня ются резиновыми столбиками (рис. 6.11, е). Столбики могут располагаться в шахматном порядке. Длина средних и крайних
312
РИС. 6.11.
Стыковка методом горячей вулканизации:
а, б —однопрокладочных лент |
посредством |
со |
|||||
ответственно |
полос, расположенных |
внахлестку, |
|||||
и зубчатого |
профиля; |
в — ленты |
с |
двумя |
про |
||
кладками; |
г. |
д — многопрокладочных лент |
со |
||||
ответственно |
с симметричной |
и |
асимметричной |
||||
разделкой |
ступеней; |
е — с использованием |
ре |
||||
|
|
зиновых столбиков |
|
|
|
РИС. 6.12.
Зависимости времени вулканизации от толщины ленты:
1, 2, 3 — при |
температуре вулканизации 110, |
145, |
150 °С соответственно |
ступенек в асимметричном стыке выбирается в зависимости от прочности тканевых прокладок.
Параметры ступенек стыка резинотканевой ленты приведены ниже.
Прочность прокладки, Н/мм |
55 |
100 |
150 |
200 |
300 |
400 |
Длина ступеней, мм: |
ЮО |
150 |
200 |
250 |
300 |
350 |
средних |
||||||
крайних |
130 |
200 |
270 |
330 |
400 |
470 |
11 Заказ № 1462 |
313 |
Длина заделки стыка резинотканевых лент зависит от ши рины ленты и составляет по рекомендациям НИИРПа: для лент шириной до 650 мм — 30 мм; более 650 до 800 мм — 50; более 800 до 1400 мм — 75; более 1400 мм — 120 мм.
Давление плит пресса на стыкуемый участок ленты должно быть не менее 1 МПа. Отсчет времени вулканизации следует считать с момента достижения температуры в плитах пресса + 140 или 150 °С (рис. 6.12). При недостаточной площади плит пресса вулканизация стыка ведется в несколько приемов, при чем начинается со средней части стыка. Вспомогательные сред ства и нормы расхода материалов для стыковки и ремонта ре зинотканевых лент приведены соответственно в табл. 6.6 и 6.7.
Резервом повышения прочности стыка резинотканевых лент является выполнение их косыми по отношению к продольной оси ленты. При этом напряжения в прокладках ленты и рези новых прослойках распределяются по всей ширине стыка, ста новясь меньше. При косом стыке улучшаются условия входа стыка на барабаны и ролики, что весьма благоприятно сказыва ется на эксплуатации высокопрочных лент на мощных конвей ерах. Стыки высокопрочных лент, выполнненные без скоса, по условию расслоения имеют прочность 20—25 % прочности целой ленты. Исследованиями Днепропетровского горного института установлено, что равнопрочность стыка и целой ленты по усло вию расслоения для высокопрочных лент можно достичь только при углах скоса 70—80° При существующей технологии сты ковки лент применение таких углов скоса затруднено, так как длина стыка при этом будет достигать 6—10 м, что значительно увеличивает расход ленты и трудозатраты на изготовление стыка. В практике изготовления стыков высокопрочных лент угол скоса принимается равным 18°30/ при горячей вулканиза ции 26°40' при холодной. При таких углах скоса прочность стыка высокопрочных лент по условию расслоения не превы шает 30 % прочности целой ленты. Такие стыки удовлетвори тельно работают на тех конвейерах, где фактический запас прочности ленты более чем в два раза выше номинального. В противном случае заниженная прочность стыка по расслое нию может привести к простоям конвейера, связанным с пере стыковкой ленты.
Стыковку резинотросовых лент осуществляют исключительно горячей вулканизацией. Установка тросов в стыке производится встык, с перекрытием и встык с перекрытием и применением до полнительных армирующих элементов. Передача тяговых уси лий в соединении происходит через резиновые слои, располо женные между тросами. При соединнии в стык не требуется
очистка |
тросов от резины, тросы при этом располагаются |
в виде |
ступенчатых пирамид, входящих одна в другую |
(рис. 6.13, а). Чем меньше число пирамид и тросов в одной сту пени, тем меньше общая длина стыка. Большей прочностью на разрыв обладают стыки с расположением стыкуемых тросов
|
Наименование |
|
|
Число |
Выполняемые операции |
|
||||||||
Штанген-циркуль |
|
|
1 |
Разметка стыка |
|
|
|
|
|
|
||||
Рулетка длиной 10 м |
|
|
1 |
То же |
|
|
|
|
|
|
|
|
||
Угольник |
|
|
|
1 |
» |
|
|
|
|
|
|
|
|
|
Шнур длиной 10 м |
|
|
1 |
» |
|
|
|
|
|
|
|
|
||
Мел (восковой карандаш) |
|
1 |
» |
|
стыка, |
подрезка |
про |
|||||||
Нож с коротким лезвием |
|
2 |
Разметка |
|||||||||||
Нож с длинным лезвием |
|
2 |
кладки |
|
обкладок |
и |
прокладок |
|||||||
|
Удаление |
|||||||||||||
Отвертка (длиной 400 мм и ши |
2 |
лент |
|
обкладок |
и прокладок |
|||||||||
Отслоение |
||||||||||||||
риной рабочей кромки 20 мм) |
2(1) |
Удаление |
обкладок |
|
и |
прокла |
||||||||
Клещи кузнечные (лебедка с за- |
|
|||||||||||||
хватами) |
|
|
|
1 |
док |
|
поверхности |
|
прокладок |
|||||
Электрическая шероховальная ма- |
Зачистка |
|
||||||||||||
шина |
с гибким валом |
|
|
2 |
и обкладок |
|
|
|
|
|
|
|||
Кист* |
щетинные (пылесос) |
|
Удаление резиновой крошки с по |
|||||||||||
Кисти щетинные № 3 |
|
|
2 |
верхности стыка |
|
|
|
поверхно |
||||||
|
|
Освежение стыкуемых |
|
|||||||||||
Кисти щетинные N° 2 |
|
|
2 |
стей бензином |
|
|
|
|
|
|
||||
|
|
Промазка заготовок клеем |
упо |
|||||||||||
Ручка деревянная (длиной 500 мм, |
1 |
Размешивание |
клея |
перед |
||||||||||
диаметром 35 мм) |
диаметром |
2 |
треблением |
|
|
|
|
|
|
|||||
Прикаточный |
ролик |
Удаление воздуха нз стыка |
|
|||||||||||
50 мм |
|
|
|
|
|
|
|
|
|
|
|
|
|
|
Емкости: |
|
|
|
|
Хранение |
клея |
перед |
употребле |
||||||
5—8 л |
|
|
|
1 |
||||||||||
0,5—1 л |
|
|
|
|
нием |
клея Лейконат |
|
|
|
|||||
|
|
|
1 |
То же, |
|
|
|
|||||||
8—10 л |
|
|
|
1 |
То же, бензина или растворителя |
|||||||||
Ограничительные линейки |
|
2 |
•Формирование кромок стыка при |
|||||||||||
Целлофановая |
пленка |
или |
ткань |
|
вулканизации |
|
|
|
плит пере |
|||||
1 |
Установление нижних |
|||||||||||||
(длиной 3—4 м, шириной |
1,5 м) |
— |
носного пресса на настил |
|
||||||||||
Набор жестяных пластин с циф |
Нумерация стыка |
|
|
|
|
|
||||||||
рами |
|
|
|
|
|
Укладка плит переносного пресса |
||||||||
Настил (щит переносной) |
|
1 |
||||||||||||
Термометры и термопары |
|
3 |
Контроль |
температуры |
вулкани |
|||||||||
Устройство для стягивания |
|
1 |
зации |
|
|
|
|
|
|
концов |
||||
|
|
Удержание стыкуемых |
|
|||||||||||
Переносной |
вулканизационный |
1 |
ленты |
|
|
|
|
|
|
|
|
|||
Вулканизация стыка |
|
|
|
|
||||||||||
пресс |
|
|
|
|
2 |
Резка |
тросов |
в |
резинотросовой |
|||||
Ножницы типа НТ |
|
|
||||||||||||
|
|
|
|
|
|
ленте |
|
|
|
|
|
|
|
|
внахлестку (рис. 6.13, б). Тросы.в |
таком |
стыке располагаются |
||||||||||||
в виде полупирамиды, |
число |
тросов — ступеней |
в |
которой |
мо |
жет быть различным. Для лент прочностью до 4 кН/см реко мендуется от одной до четырех ступеней. Чем больше число ступеней в стыке, тем он менее жесткий, но длина такого стыка и трудоемкость его изготовления возрастают. Для лент мощных конвейеров число ступеней обычно три и реже четыре.
11* |
315 |
Норма
расхода
Наименование материалов на 1 м2 Выполняемые операции стыка»
кг
Клей резиновый Л-425 |
1,5 |
Промазка |
ступеней |
стыка, про |
|
Клей Лейконат |
0,15 |
слоенной и |
обкладочной |
резины |
|
Приготовление клеевой |
компо |
||||
Резина прослоенная № 450 тол |
1 |
зиции |
прослоек |
на ступенях |
|
Прокладка |
|||||
щиной 0,5—1 мм |
1 |
стыка |
|
|
|
Резина обкладочная каландровая |
Заделка кромок стыка |
|
|||
№ ИРГИ371 (толщина 2 мм) |
0,5 |
Освежение |
поверхности |
ступенек |
|
Бензин БР-1 или БР-2 |
|||||
Этилацетат |
0,1 |
стыка и резиновых заготовок |
|||
|
|
|
|
Схемы стыковки резинотросовых лент:
а — встык; б —встык и с перекрытием; в — с перекрытием
Тип ленты
РТЛ-500 РТЛ-1000 РТЛ-1500 РТЛ-1500У
мм |
в стыке |
Диаметр троса, |
Число ступеней |
2,8 |
1 |
3,5 |
1 |
4,2 |
2 |
6 |
1 |
ступени,мм |
стыка*мм |
Тип ленты |
|
|
|
Длина |
Длина |
|
300 |
600 |
РТЛ-2500 |
500 |
800 |
РТЛ-3150 |
500 |
1300 |
РТЛ-4000 |
800 |
1100 |
|
Диаметр троса, мм |
Число ступеней в стыке |
Длина ступени, мм |
Длина сты , мм |
7,5 2 800 1900
8.23 1000 3300
10,9 4 800 3350
В табл. 6.8 приведены рекомендуемые в СССР параметры сты |
|
ков резинотросовых лент. |
|
Вспомогательные средства, применяемые при стыковке рези |
|
нотросовых лент, те же, что и для резинотканевых |
лент (см. |
табл. 6.6). |
|
Нормы расхода материалов для стыковки резинотросовых |
|
лент приведены ниже. |
|
|
(Расход |
|
материала |
на 1 м* стыка, кг |
|
Обкладочная каландрованная резина толщиной 2 или 3 мм для |
|
лент: |
|
общего назначения (2—560) |
18 |
огнестойких*(2—724) |
18 |
теплостойких1(2—1588) |
|
Прослоечная каландрованная резина 2—590 толщиной 1 или |
|
1,5 м м ...................................................................................... |
7 |
Резиновый клей 425 с концентрацией 1 :4 |
2.3 |
БензинжБР-1 или БР-2 |
2,3 |
Вулканизация резинотросовых лент осуществляется в соот ветствии с заданным режимом (табл. 6.9), причем отсчет вре мени вулканизации следует считать с момента достижения тем пературы вулканизации.
Увеличить прочность стыка резинотросовой ленты можно пу тем взаимного перекрытия всех тросов, смежные из которых располагаются с изгибом (рис. 6.13, в). Рекомендуется концы тросов на участке стыка оформлять в виде конусов, уменьшаю щих относительное смещение тросов при прохождении бараба нов. Во Франции при стыковке резинотросовых лент концы тро сов сначала смазывают, а затем заключают в нейлоновую обо лочку, которая защищает тросы от коррозии.
Вулканизационные прессы. Для обеспечения быстрой и ка чественной стыковки горячей вулканизацией предприятия дол жны располагать стационарным и переносным вулканизацион-
Тип
ленты
РТ Л - 1 2 0 0
РТ Л - 1 5 0 0
РТ Л -2 5 0 0
РТ Л - 3 1 5 0
Толщина гото вой ленты» мм
2 0 ,5
2 1 ,5
23
25
Время вулка |
|
|
низации стыка» |
|
|
мм» при пемпе- |
Тип |
|
ратуре |
||
|
|
ленты |
143± |
162+ |
|
±3 °С |
±2 °С |
|
50 |
35 |
Р Т Л - 4 0 0 0 |
52 |
38 |
Р Т Л -5 0 0 0 |
55 |
40 |
Р Т Л - 6 0 0 0 |
60 |
45 |
|
вой готоТолщина ммленты,
27
30
29
Время вулка низации стыка» мм* при темпе
ратуре
143± |
152± |
±3 °С |
±2 °С |
65 |
50 |
70 |
55 |
70 |
55 |
ным оборудованием. Основу его составляют прессы, оснащен ные средствами регулирования заданного давления и темпера туры. Применяемое на горных предприятиях вулканизацион ное оборудование еще не в полной мере отвечает современным требованиям. При вулканизации стыков лент мощных конвейе ров должно создаваться равномерное по площади стыка дав ление не менее 1 МПа для резинотканевых и 1,5—1,8 МПа для резинотросовых лент при температуре 151 ± 2 и 140±5 °С. С учетом норм ручной переноски тяжестей наибольшая масса частей переносного пресса не должна превышать 50 кг. При серийном производстве пресс должен иметь минимальное число типоразмеров с максимальной унификацией элементов, средств автоматического контроля давления прижимных эле ментов и температуры нагревателей, взрывобезопасное или об щее исполнение. Техническая характеристика вулканизацион ных прессов, используемых на предприятиях страны, приведена в табл. 6.10.
Вулканизационный пресс ВГШ-1А используется преимуще ственно на шахтах и предназначен для стыковки лент резино
тканевых, |
резинотросовых и из |
ПВХ. Плиты пресса имеют |
||
|
|
|
|
ТАБЛИЦА 6.10 |
|
Ширина |
Температура |
Номиналь |
Мощность |
Прессы |
ленты |
|||
мм. не |
вулканиза |
ное давле |
нагревателя Масса, кг |
|
|
более |
ции. °С |
ние» МПа |
плиты. кВт |
ВГШ-1А |
До |
1200 |
143 |
ПВ |
До |
1200 |
145—150 |
ПВП |
1200 |
145±2 |
|
ТС-1 |
1400 |
150+3 |
|
ТС-1400 |
1400 |
150+3 |
|
ТС-1600 |
1600 |
150+3 |
|
ВПК-1600 |
1600 |
150 |
|
ВЛТ-2М |
1000 |
140—150 |
|
вп |
2000 |
145 |
|
632 |
1600 |
143—150 |
1,5 |
|
1,5 |
|
1,0 |
00 |
7 |
1,35—1,5
1,5 До 0,5 1,2—1,5
—
8,5 |
2175 |
10,5 |
2800 |
7,5 |
350 |
4,2—6,4 |
480—1080 |
— |
— |
— |
___ |
4,4 |
2150 |
4,4 |
250 |
6,3 |
2000 |
—100—440
электрические трубчатые нагреватели и термореле ТР-200 для автоматического включения и отключения нагревателей. При жим плит к ленте осуществляется гидроцилиндрами. Ввиду большой массы отдельных элементов пресс ВГШ-1А целесооб разно устанавливать стационарно.
ИГТМ АН УССР разработаны и испытаны прессы типа ПВП с повышенной стабильностью режима вулканизации. Пресс— переносной, включает в себя тонкие гибкие нагреватель ные плиты и эластичную камеру с гидроприводом, обеспечиваю щим равномерное распределение давления по площади вулка низируемого участка ленты независимо от изменения его толщины, наличия впадин или выступов. Давление пресса состав ляет 1 МПа при общей массе пресса 350 кг и массе наиболее тяжелого узла (гидропривода) 25,5 кг. Нагревательная плита состоит из миканитового сердечника, на который навита нихромовая полоса. Эластичная камера давления изготовлена из маслостойкой резины толщиной 4 мм. Вода в камеру пресса закачивается ручным насосом ГН-60. При такой конструкции камеры давления величина прогиба балок не влияет на распре деление давления, поэтому для их изготовления можно приме нять особопрочные легкие сплавы, например алюминиевые. В другой конструкции пресса типа ПВ во взрывобезопасном исполнении, разработанной ИГТМ АН УССР совместно с Алек сандровским машиностроительным заводом, нагрев и сжатие вулканизируемого участка ленты осуществляется жидким тепло носителем, нагнетаемым в нагревательные плиты с гибкими металлическими или резиновыми диафрагмами (рис. 6.14, а). Предварительное прижатие плит осуществляется с помощью винтовых стяжек. Давление жидкости в диафрагмах создается приводным насосом. Пресс имеет сравнительно большую массу и рекомендован для эксплуатации на предприятиях и угольных шахтах, опасных по газу или пыли.
ВНИИнеруд разработаны и внедрены в производство вулка низационные прессы ТС-1, ТС-1400 и ТС-1600.
Пресс ТС-1 имеет нагревательные плиты с расположенными внутри нихромовыми проводниками и наполненные трансформа торным маслом диафрагмы. Стык предварительно спрессовыва ется двутавровыми балками с винтовыми стяжками с последую щим доопрессовыванием диафрагмами за счет теплового расши рения нагреваемого трансформаторного масла.
Прессы типа ТС-1400 и ТС-1600, в которых используется трансформаторное масло для нагрева и давления, входят в со став комплекта вулканизационного оборудования, предназна ченного для стыковки и ремонта лент шириной до 1600 мм. Пресс ТС-1400 выпускает Боровический завод полимерного ма шиностроения. Комплект оборудования с прессом ТС-1600 (рис. 6.14, б) включает в себя собственно пресс, машинку для разделки стыков лент и устройство для стягивания концов ленты. В конструкции плит предусматривается установка тер-
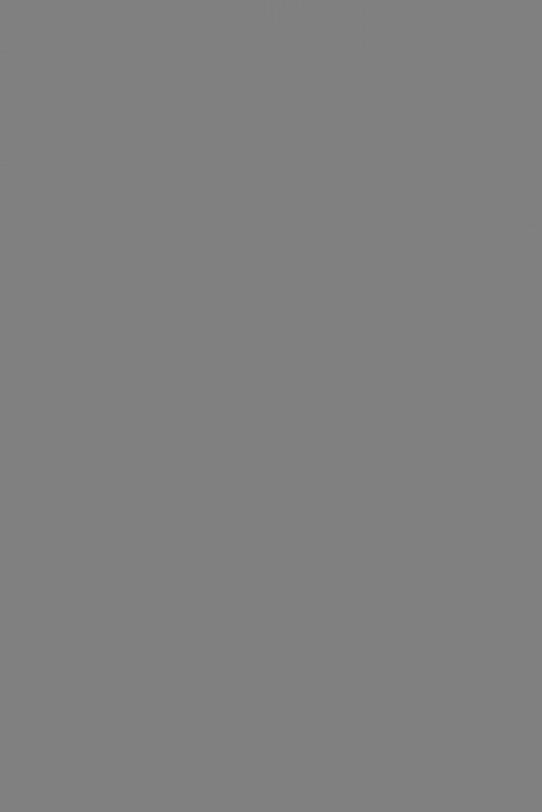
Вулканизационный пресс конструкции ПО «Кривбассрудоремонт» включает в себя зажимные балки из алюминиевого сплава, в которые вмонтированы гидроцилиндры, создающие равномерное давление на стыке. Концы балок предварительно вручную стягиваются винтами. Давление от гидроцилиндров на плиты (аналогичные по конструкции плитам пресса ВЛТ-2М) передается через нажимные шины швеллерного профиля.
Вулканизационный пресс типа 632 конструкции Промтрансниипроекта выпускается Куйбышевским опытно-механическим заводом. Пресс имеет электрический нагреватель и винтовое стяжное устройство.
Вулканизационные прессы типа Нилос, прессующие тра версы и плиты фирмы «Вагенер» (ФРГ) изготавливаются из легкого сплава. При стыковке лент шириной до 1000 мм исполь зуются шпиндельные траверсы с упорными винтами, развиваю щими давление 0,5—0,9 МПа. Винты затягивают ключом-дина мометром. Более высокое и равномерное давление достигается гидравлическими траверсами с нажимными башмачками и ши нами. Плиты нагреваются электрическими элементами, темпе ратура которых регулируется термостатом. Комбинация из де сяти типоразмеров плит и шести типоразмеров траверс (рис. 6.14, в) позволяют соединять ленты любой ширины (до 3200 мм) при длине стыка 500—3000 мм. Прессы имеют обыч ное или взрывобезопасное исполнение. В Канаде выпускаются передвижные быстродействующие вулканизационные прессы для стыковки лент шириной 1524—3048 мм. Давление в прессе, рав ное 1,37 МПа, создается нажимными элементами и гибкими ка мерами. Разогрев стыка осуществляется после достижения но минального давления.
Большим спросом пользуются прессы облегченной конструк ции, в которых отсутствуют тяжелые металлоемкие прессующие элементы. Так, прессующие плиты могут выполняться из тер мостойкой токонепроводящей резины с нагревательными эле ментами в виде перфорированных пластин (рис. 6.14, г). Прес сующие плиты от выпучивания предохранены стальными про кладками, устанавливаемыми между плитами и балками. Предварительное поджатие прессующих плит, создаваемое крепежными элементами, имеет незначительную величину. Но минальное прессующее усилие достигается путем расширения резины при нагреве.
Для ремонта стыков и резиновых обкладок лент широко ис пользуются переносные вулканизационные прессы. ПО «Воро шиловградуголь» изготовляется переносный вулканизационный пресс, состоящий из коробчатых нагревателей и струбцины с за жимными винтами (рис. 6.14, д). Нагреватели питаются от сети напряжением 127 В и обеспечивают нагрев участка ленты до 150 °С. Суммарная мощность нагревателей 3,2 кВт, а масса 67 кг. Итальянская фирма «Мальтипресс» выпускает перенос ные вулканизационные прессы для ремонта лент, в которых
321
предусматриваются элементы регулирования температуры вул канизации. Ширина плит пресса составляет 220—250, а длина — 700—2200 мм. Нагрев плит до температуры 170 °С осуществля ется за 20 мин, а охлаждение — за 4 мин при давлении 0,8 МПа. Для прижатия плит служит рычажный механизм.
Стыковка холодной вулканизацией. Стыковку резиноткане вых лент холодной вулканизацией рекомендуется проводить на лентах общего назначения и морозостойких шириной до 1200 мм с прочностью 0,55—2,0 кН/см ширины прокладки на конвейерах, работающих в средних и легких условиях. Температура окру жающей среды не должна быть ниже +15 °С. При этом на транспортной технологической линии должна предусматри ваться возможность остановки конвейеров на 24 ч. При таком времени остановки обеспечивается максимальная проч ность стыка. Для стыковки лент используются оборудование и приспособления, приведенные выше (см. табл. 6.8), за исключе нием вулканизационных прессов. В качестве стыковочных мате риалов применяют клеи СВ-5 (СТУ 38-105747—74) и«Лейконат» в пропорции 10:1. Резины прослоечные и обкладочные не при меняются. Параметры стыков и их схемы аналогичны стыкам при горячей вулканизации. Кромки обкладок, бортов лент вы полняются без фасок. Расход клея составляет 2—3 кг на 1 м2 стыка. Состав из клеев СВ-5 и «Лейконат» годен к употребле нию в течение 2—3 ч. Клей на стыкуемые поверхности нано сится дважды, продолжительность каждой сушки 20—25 мин.
В общем случае стыковка холодной вулканизацией требует меньше трудовых и материальных затрат. Вулканизация стыка происходит при его выдержке в ненапряженном состоянии в те чение 24 ч после сборки (без давления) при температуре окру жающего воздуха. При неполной загрузке лента может быть пу щена в ход через 12 ч после стыковки. При повышенной влаж ности воздуха целесообразно просушивать стыкуемый участок ленты с помощью инфракрасных излучателей. Швы стыка тща тельно промазываются клеем СВ-5 и просушиваются до исчез новения липкости. Затем на шов накладываются специальные заплатные полосы шириной 50 мм и прокатываются накаточным роликом от середины к краям для предотвращения скопления воздуха под полосой.
Стыковка механическими средствами. В определенных усло виях эксплуатации мощных ленточных конвейеров необходимо осуществлять быструю замену поврежденных или изношенных отрезков ленты. При этом допускается временное снижение прочности стыка. В этом случае применяют механические сое
динения с помощью шарниров, |
скоб, |
заклепок, сшивки и др. |
К наиболее быстроразъемным |
стыкам |
относятся шарнирные |
с соединительными звеньями (петлями), прикрепляемыми к кон цам ленты с помощью заклепок (рис. 6.15, а). Разрушения в таких стыках возникают обычно в местах расположения за клепок из-за различия в упругих удлинениях жестких звеньев
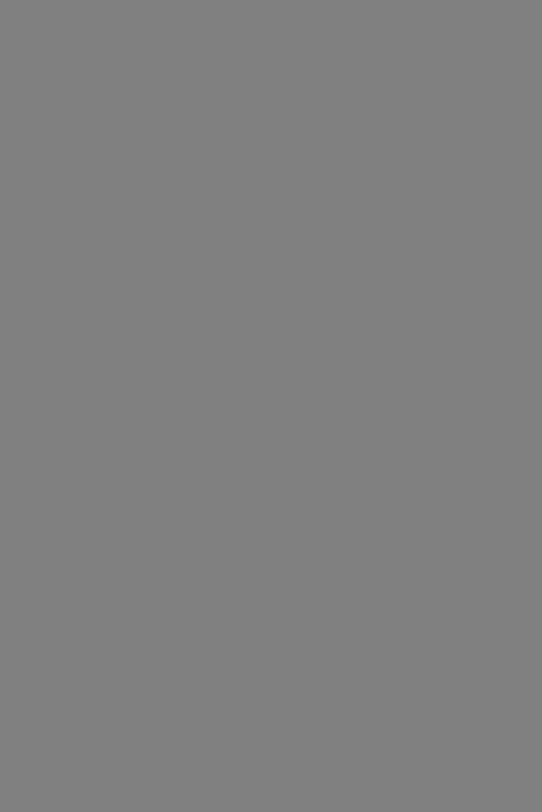
и ленты. Для более равномерного распределения нагрузок между рядами заклепок крайние ряды отверстий выполняются комбинированными: отверстия в ленте— цилиндрическими, а от верстия в звеньях — овальными и расположенными под углом. При натяжении ленты заклепки первых рядов несколько сме щаются, таким образом происходит перераспределение каса тельных нагрузок.
Более надежное крепление соединительных звеньев к ленте осуществляется с помощью специального устройства и скоб (рис. 6.15, б). Оно включает в себя матрицу с отверстиями, опор ную колодку со сферическими углублениями и нажимное при способление, состоящее из гидроцилиндра и пуансона. Конец ленты с соединительными звеньями монтируется в сшивающем устройстве таким образом, чтобы отверстия в звеньях распола гались соосно с отверстиями матрицы и сферическими углубле ниями колодки, причем между торцом ленты и звеном помеща ется стержень для образования в звене петли шарнира. После включения гидроцилиндров штоки их нажимают на пуансоны, которые вдавливают скобы в ленту. В сферических углублениях концы скоб загибаются и фиксируются как элементы крепления.
Чаще стали применяться эластичные соединительные звенья (рис. 6.15, в), которые присоединяются к ленте вулканизацией или с помощью пазов и скоб. Эластичные звенья могут иметь фигурное исполнение с цилиндрическим выступом, на который насаживаются промежуточные соединительные металлические звенья с фиксаторами (рис. 6.15, г).
Применение эластичных соединительных звеньев позволяет существенно уменьшить величину касательных нагрузок по пло щади соединения и увеличить его работоспособность. На шахтах ПО «Карагандауголь» используются приспособления, предохра няющие металлические крючкообразные соединительные звенья от быстрого износа. Отрезок ленты накладывается на звенья и прошивается скобами (рис. 6.15, д). После износа отрезка ленты он заменяется другим, в результате чего уменьшаются затраты труда на выполнение стыковочных работ.
Оригинальной конструкции соединительные звенья для сты ковки лент выпускаются фирмами ФРГ. Звенья имеют систему заостренных выступов, с помощью которых звенья закрепляются на ленте (рис. 6.15, е). Таким образом в одном элементе совме щены две детали — соединительные звенья и скобы.
Звенья в виде крючкообразных скоб изготавливаются из про волоки диаметром 2,4—2,8 мм ПО «Воркутауголь». Они реко мендуются для стыковки лент прочностью до 4 кН/см ширины ленты. При этом применяется сшиватель типа СТЛ, состоящий из ручного поршневого насоса с маслобаком, гидроцилиндра, си стемы рычагов и губок для вдавливания скоб в ленту.
Для стыковки лент мощных конвейеров механическим спосо бом требуется усиление участка крепления соединительных зве ньев. С этой целью в ленте путем вулканизации располагаются
диски с обвивающими их отрезками латунированного троса (рис. 6.15, ж). На дисковых элементах с помощью заклепок мон
тируются соединительные звенья. Концы ленты разделываются таким образом, чтобы тросы располагались в середине сечения ленты. Соединительные звенья могут быть покрыты резиновыми обкладками. При сборе стыка в проушины соединительных зве ньев вставляется стержень шарнира.
На карьерах ПО «Средазуголь» в качестве соединительных звеньев для стыковки лент применяют спирали (рис. 6.15, з), ко торые пропускаются через ленту. Витки спиралей располага ются напротив друг друга, и через них проходит гибкий стер жень шарнира. Такие соединительные элементы могут использо ваться многократно.
При срочной или аварийной стыковке внахлестку лент мощ ных конвейеров может быть использована сшивка ленты ско бами. В этом случае рекомендуются механизированные нажим ные приспособления, фигурные колодки и скобы с заостренными концами (рис. 6.15, и). Скобы шириной 15 мм изготавливаются из стальной проволоки. Их высота выбирается в зависимости от толщины ленты.
На шахтах ПО «Ростовуголь» сшивка лент осуществляется с помощью приспособления, состоящего из колодки с гнездами и ударной плиты в виде гребенки. В гнезде колодки, располо женной под лентой, вставляются скобы (рис. 6.15, к), а гре бенка устанавливается над лентой зубьями против гнезд. Уда рами молотка скобы прошивают ленту.
На шахте «Ворошиловградская» № 1 ПО «Ворошиловградуголь» изготавливается устройство для сшивки лент с автома тической подачей скоб. В него входят основание, направляющая с подпружиненной рамкой для перемещения скоб в матрицу, от носительно которой перемещается пуансон. На пуансон воздей ствуют ударом молотка. Пуансон при движении вниз захваты вает одну скобу и вдавливает ее в ленту. В магазин направляю щей входит 50 скоб.
Для механизации процесса изготовления скоб на шахте «Интинская» ПО «Интауголь» применяется специальный станок (рис. 6.15, л). Он состоит из основания и корпуса, в котором пе ремещается нож-пуансон с дополнительным пуансоном. Через отверстие в корпусе подается проволока до упора в стенку кор пуса. При движении пуансона-ножа вниз отрезается часть про волоки, затем дополнительный пуансон изгибает ее в скобу. Скоба выпадает в нижнее отверстие корпуса. Пуансоны приво дятся в действие электродвигателем с эксцентриком и в исход ное положение возвращаются пружиной. Производительность станка 200 скоб в минуту.
Помимо традиционно применяемых средств стыковки хорошо зарекомендовали себя комбинированные методы стыковки. Наи более характерна комбинация механических соединений в ком плексе с горячей или холодной вулканизацией.
Стыковка резинотканевых лент комбинированным способом может быть выполнена путем ступенчатой разделки стыкуемых кондов ленты с последующей вулканизацией и дополнительным
соединением |
в определенных точках с помощью болтов |
(рис. 6.16, а) |
или заклепок. Болты или заклепки вставляют в от |
верстия, проделанные по площади стыка после вулканизации. Под шляпки болтов и под гайки устанавливают тарельчатые шайбы, обращенные выпуклой стороной к ленте. Такое соеди нение сокращает простои конвейера, связанные с периодом вул канизации.
Хорошие результаты могут быть получены при стыковке ре зинотканевых лент сшивкой и вулканизацией одновременно. На участке стыка лента освобождается от резиновых обкладок (рис. 6.16, б). Торцы тканевого каркаса сшиваются между собой прочным кордом. Затем шов растягивают для выравнивания на тяжений в нитях корда.
Комбинированные методы стыковки все чаще применяются для резинотросовых лент. Большая толщина эластичного слоя позволяет производить запрессовку в стыкуемые концы ленты выступов, имеющих форму «ласточкина хвоста» (рис. 6.16, в). Выступы обоих концов ленты соединяют между собой фигур ными планками. Между планками вулканизируются эластичные слои для придания стыку поперечной гибкости. При таком стыке уменьшается трудоемкость разделки резинотросовой ленты.
РИС. 6.16.
Комбинированные средства стыковки лент методом вулканизации с по мощью:
о — болтов; б — сшивки; |
в — фигурных выступов в ленте |
и соединительных |
планок; |
||
г —завулканизированных |
тросовых |
петель; |
д— тормозных |
шаров и накладок; е — |
|
соединительных конусных |
втулок; |
ж — трубы |
с заклинивающими стержнями |
и втулок |
Институтом горного дела им. А. А. Скочинского разрабо тана резинотросовая лента со специально предусмотренными элементами стыковки. Отдельно изготавливаемые куски ленты имеют оригинальное расположение тросов — в виде зигзагооб разно уложенных петель (рис. 6.16, г). Торцовые части кусков ленты выполнены с дугообразными пазами, из которых высту пают петли тросов. При стыковке петли стыкуемых кусков ленты соединяются между собой спиральными витками троса. Затем паз заполняется резиной и закрывается по периметру стыка ре зиновым кольцом. Прочность стыка такой ленты практически со ответствует прочности ленты.
В стыках резинотросовых лент повышенной толщины весьма эффективно использование жестких соединительных приспособ лений в виде муфт, планок, тормозных элементов и др. Чтобы исключить возможное смещение тросов на участке стыка, по следние оснащаются фиксирующими шарами (рис. 6.16, д). Шары напрессовываются на концы тросов и располагаются в выемках эластичных накладок, которые с помощью вулкани зации присоединяются к разделанному участку стыка. Шары и накладки препятствуют смещению тросов относительно друг друга при натяжении ленты. Перед вулканизацией концы про тивоположных тросов стыкуемых концов ленты можно соеди нить с помощью полых конических стальных втулок с проуши нами на торце. Концы тросов вставляют в конические отверстия втулок (рис. 6.16, е). Пространство между тросом и внутренней поверхностью втулки заполнено деформируемой композицией, например синтетической смолой. Проушины втулок имеют от верстия. Противоположные втулки соединяют пальцами, встав ленными в эти отверстия. В другом варианте стыкуемые концы тросов вводят в гильзообразную стальную втулку, затем гильзу обжимают. Внутреннюю поверхность втулки покрывают фрик ционным составом. В обжатой втулке может быть просверлено отверстие перпендикулярно к оси тросов, через которое в концы тросов впрессовывают стопорные штифты. Выступающие концы штифтов сваривают. Втулка может состоять из двух полуцилин дров, внутри которых закрепляются концы тросов. Соединение полуцилиндров осуществляется также сваркой или болтами.
Тросы стыкуемых концов ленты могут также крепиться от дельно друг от друга на общем соединительном элементе, вы полненном, например, в виде трубы (рис. 6.16, ж). В трубе име ются отверстия, в большее из которых заводится трос с предва рительно напрессованной втулкой, имеющей буртик. В трубу заводятся два овальных в сечении стержня, препятствующие выходу троса из трубы. Соединение может иметь одну трубу, при этом к ней присоединяются смежные тросы стыкуемых кон цов. Соединение может иметь две трубы, к каждой из которых прикрепляются тросы только одного конца ленты, при этом трубы соединяются между собой только за пределами ширины ленты.
К перспективным направлениям совершенствования средств стыковки лент мощных конвейеров следует отнести изготовле ние лент отдельными отрезками, в конструкции которых уже на стадии вулканизации предусматриваются соединительные эле менты. Сюда относятся также средства, способствующие более быстрой подготовке концов ленты к стыковке. Так, резино тросовые ленты могут быть выполнены на концевых участ ках со слоем талька, обладающего антиадгезионными свой ствами и расположенного между внутренним слоем резины
стросами и обкладками. В процессе стыковки ленты верхние
инижние обкладки и борта легко отделяются по граничным линиям.
Контроль стыковки. Для предупреждения аварийного раз рыва станков необходимо осуществлять профилактический кон троль за состоянием места соединения. При этом могут исполь зоваться два вида контроля: проверка величины удлинения ц целостности стыка в процессе эксплуатации. Для контроля уд линения стыка можно применять магнитные датчики, располо женные по обеим сторонам стыка. При удлинении стыка допре
дельной величины, предшествующей его разрыву, в блоке срав нения вырабатываются импульсы рассогласования, в результате чего система подает световой или звуковой сигналы, при этом привод конвейера отключается.
Контроль целостности стыков производится так же, как ц контроль целостности ленты, т. е. с применением излучателей (радиоактивных, ультразвуковых), электромагнитной техники ц механических приспособлений, работающих по принципу обна ружения просыпи при повреждении ленты.
6.5. ОБСЛУЖИВАНИЕ И РЕМОНТ КОНВЕЙЕРНЫХ ЛЕНТ
6 .5 .1 . О Б С Л У Ж И В А Н И Е Л Е Н Т
Под обслуживанием конвейерных лент понимается комплекс мероприятий, связанных с правильным хранением, эксплуата цией и контролем состояния ленты; установлением неисправно, стей в ленте и их устранением.
При хранении лент обеспечивается уменьшение степени влияния окружающей среды и различных механических воздей. ствий, начиная с момента получения предприятием ленты до первичной навески на конвейер. Хорошие условия хранения ленты могут существенно способствовать продлению ее эксплуд. тации без замены. Бухты лент лучше всего хранить в помещу, ниях, в которых предусмотрены защита от солнца, влаги, оса^. ков и поддержание прохладной и сухой атмосферы. Оптималь. ная температура хранения лент 15 °С при влажности от 20 70 %. Не следует оставлять ленту на длительное время притер, пературе ниже 4 °С или выше 32 °С. Огнестойкие ленты не ре. комендуется хранить при температуре ниже 4 °С.
Обычно ленту сохраняют в фабричной упаковке, чтобы ис ключить попадание на нее масел или других активных жидко стей. При длительном хранении бухты с лентой монтируют на стояках с горизонтальной штангой. Не рекомендуется свора чивать ленту в большие рулоны и перекатывать их с помощью ломов или ваг. Для перемещения рулонов используются штанги, вставляемые в отверстие сердечника рулона, и подъемно-транс портный механизм (погрузчик, таль, кран). При температуре ниже нуля ленты становятся жесткими, из-за чего усложняется их монтаж на конвейер. При размораживании или резком пере гибе на ленте могут появиться большие трещины, которые трудно ремонтировать. Необходимая эластичность возвращается к ленте при температуре 4 °С. Если помещение не позволяет хранить рулон вертикально, его укладывают горизонтально на
металлический |
лист. |
Для разматывания рулона |
необходимо |
|
в сердечник |
продеть |
вертикальную трубу |
и приварить ее |
|
к листу. |
|
|
|
|
Эксплуатация ленты начинается с момента навески ее на |
||||
конвейер. Вопросы улучшения эксплуатации |
ленты, |
связанные |
с выбором и установкой оборудования, выбором отдельных па раметров, учетом условий применения конвейера, рассмотрены в соответствующих разделах. В табл. 6.11 приводятся перечень неисправностей, непосредственно относящихся к ленте, причин их возникновения и рекомендации по устранению неисправно стей.
|
|
|
|
|
|
|
ТАБЛИЦА 6.11 |
|
Вид неисправностей |
|
|
Причина |
|
Рекомендации по устранению |
|||
|
|
|
неисправности |
|||||
Нарушение |
хода |
«Серповидность» |
отрезка |
Заменить отрезок ленты |
||||
ленты (сбегание |
ленты |
ленты |
имеет |
перекос |
Перестыковать ленту |
|||
в сторону) |
|
Стык |
||||||
Нарушение |
же- |
Слабое |
натяжение |
ленты |
Увеличить натяжение ленты |
|||
Повышенная жесткость но |
Оставить ленту загруженной |
|||||||
лобчатости ленты |
вой |
ленты |
натяжение |
на определенное время |
||||
|
|
Повышенное |
Уменьшить натяжение ленты |
|||||
|
|
ленты |
|
|
поверхности |
Устранить причину |
попада |
|
|
|
Загрязнение |
||||||
|
|
ленты маслом |
|
ния масла |
|
|||
|
|
|
|
|
|
|
Перевернуть ленту и эксплу |
|
|
|
|
|
|
|
|
атировать до выравнивания |
|
|
|
|
|
|
|
|
поверхности |
|
Пробуксовка |
лен |
Пониженное |
натяжение |
Увеличить натяжение ленты |
||||
ты |
|
ленты |
|
|
|
|
Перестыковать ленту |
|
|
|
Предварительная вытяжка |
||||||
|
|
ленты |
|
|
|
|
Устранить причины |
попада |
|
|
На ленту попадают смазы |
||||||
|
|
вающие |
материалы |
и вода |
ния смазывающих |
материа |
||
|
|
|
|
|
|
|
лов и воды |
|
Вид неисправностей |
|
Причина |
|
|
Рекомендации по устранению |
|||||
|
|
|
неисправности |
|||||||
|
|
|
|
|
|
|
|
|
||
Нарушение |
цело |
Недостаточная |
гибкость |
Улучшить |
элементы крепле |
|||||
стности |
механиче |
стыка |
|
|
|
|
|
ния стыка |
(соединительные |
|
ских стыков |
|
Пониженная прочность эле |
звенья, скобы) |
|||||||
|
|
|
Заменить элементы крепле |
|||||||
|
|
|
ментов крепления (соедини |
ния на более прочные |
||||||
|
|
|
тельных звеньев, скоб) |
|
Уменьшить натяжение ленты |
|||||
|
|
|
Повышенное |
|
натяжение |
|||||
|
|
|
ленты |
|
|
|
|
|
|
|
Нарушение |
цело |
Расслоение |
ступеней |
стыка |
Проверить режим вулканиза |
|||||
стности |
вулкани |
|
|
|
|
|
|
ции и параметры стыка. Пе |
||
зационного стыка |
|
|
|
|
|
|
рестыковать стык |
|||
Повышенный |
из |
Пробуксовка ленты |
на |
ба |
Увеличить натяжение ленты |
|||||
нос рабочей и не |
рабанах |
прогибы |
ленты |
То же |
|
|||||
рабочей |
обкладок |
Большие |
|
|||||||
|
|
|
между роликоопорами |
об |
Устранить |
причину попада |
||||
|
|
|
Разбухание |
резиновых |
||||||
|
|
|
кладок из-за попадания |
ния масла |
|
|||||
|
|
|
масла |
|
|
|
|
|
|
|
Повышенный |
из |
Активное |
|
взаимодействие |
Уменьшить |
активность вза |
||||
нос обкладок и |
ленты с |
элементами |
кон |
имодействия ленты с элемен |
||||||
каркаса |
ленты |
струкции конвейера и тран |
тами конструкции конвейера |
|||||||
|
|
|
спортируемым |
грузом |
на |
и грузом |
|
|||
|
|
|
роликоопорах и в месте за |
|
|
|||||
|
|
|
грузки |
|
|
|
|
|
|
|
6.5.2. ВИДЫ РЕМОНТОВ ЛЕНТ
Опыт эксплуатации мощных ленточных конвейеров в СССР
иза рубежом убедительно доказывает экономическую эффек тивность своевременного ремонта дорогостоящих лент. Благо даря своевременному проведению ремонтных мероприятий срок службы лент можно увеличить до 10—12 лет. Применяются сле дующие виды ремонта: профилактический, текущий и капиталь ный. При этом используются механические, холодные (клеевые)
игорячие вулканизационные средства ремонта. Профилактиче ский осмотр и ремонт проводятся систематически в процессе на блюдения за состоянием ленты при ее эксплуатации. Например, возможно возникновение незначительных задиров на рабочей или нерабочей обкладках, бортах ленты, которые быстро ликви дируются режущим инструментом при незначительной по вре мени остановке конвейера. При более значительных поврежде ниях, связанных с пробоем, местным порывом и разрезом ленты, места повреждений отмечаются и временно закрепляются ско-
бами, заклепками, накладными пластинами с фигурными бол тами и фиксирующими зубьями, специальным клеем.
Задачей текущего ремонта |
является поддержание ленты |
в нормальном для эксплуатации |
состоянии без демонтажа ее |
с конвейера. При текущем ремонте осуществляются заделка по вреждений обкладок, каркаса и ликвидация незначительных по рывов бортов. Текущий ремонт рекомендуется проводить мето дом холодной или горячей вулканизации. Различные механи ческие средства заделки повреждений (например, установка заплат на заклепках, вставка в пробоины шарниров) не обе спечивают необходимой надежности работы поврежденного участка.
Капитальный (восстановительный) ремонт ленты проводится при сквозном истирании обкладок, большом числе вырывов и различных разрушений на единице площади ленты. Каркас ленты не должен иметь значительных повреждений. Таким об разом, капитальный ремонт связан прежде всего с восстановле нием резиновых обкладок и бортов в стационарных вулканиза ционных мастерских или на заводах. При этом капитальному ремонту подвергаются ленты, отвечающие определенным техни ческим условиям по количеству и величине повреждений на еди ницу площади или длины ленты, а также физико-механическим свойствам. Ниже рассматриваются средства текущего и восста новительного видов ремонта ленты.
6.5.3. РЕМОНТ РЕЗИНОТКАНЕВЫХ ЛЕНТ
Ремонт обкладок резинотканевых лент с помощью клея. По врежденный участок обкладки очищается и просушивается. Ре комендуется сушку производить в вакуумной камере при темпе ратуре 60 °С. Далее шаблоном наносят контур заплаты и сре зают обкладку до прокладки. После промазки клеем и сушки поврежденного участка на него наклеивается заплата из обкладочной резины и прикатывается роликом от середины к краям (рис. 6.17, а).
Ремонт прокладок резинотканевых лент с помощью клея. С помощью шаблонов вырезаются обкладка и поврежденная прокладка. Открытую прокладку шерохуют и покрывают клеем. Затем на чистую прокладку помещают резиновую смесь, выпол няющую роль промежуточного связующего слоя. На резиновую смесь наклеивают вставку из прокладки (рис. 6.17, б), которую покрывают резиновой смесью. Последняя операция связана с приклейкой заплаты из обкладочной резины. При сквозных пробоях, разрезах или разрывах лента сначала ремонтируется со стороны рабочей обкладки до центральной прокладки, а затем со стороны нерабочей обкладки (рис. 6.17, в). Аналогично про изводится ремонт лент в случае бокового повреждения обкладок и прокладок (рис. 6.17, г). Последовательность разделки ленты при различных повреждениях показана на рис. 6.18.
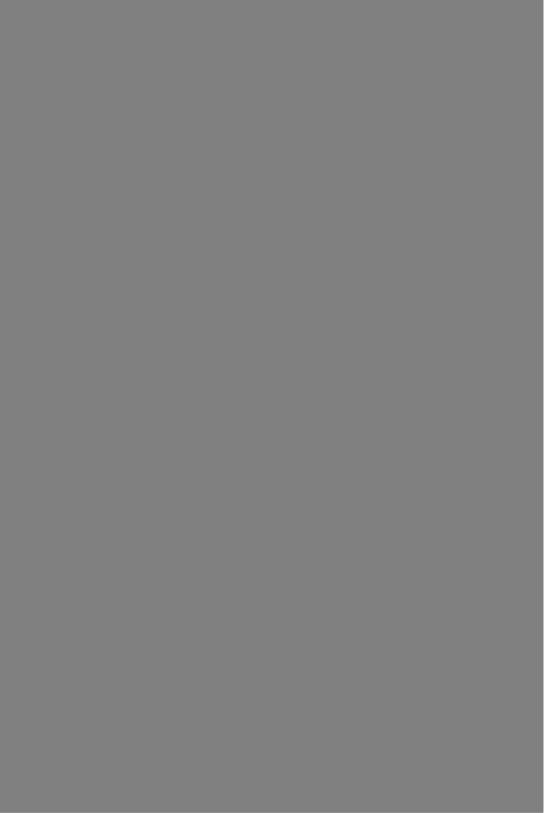
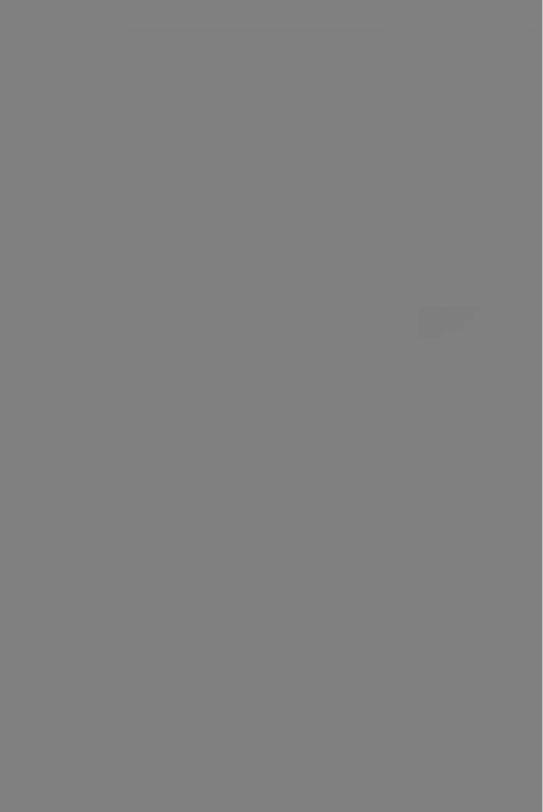
такие эластомеры не требуют вулканизации и обеспечивают ре монт ленты без заплат и швов. При ремонте поврежденного уча стка ленты пастообразная или жидкая основа полимера смеши вается с отвердителем, и получается резиноподобный материал, обладающий хорошей упругостью, износостойкостью, повышен ной прочностью на разрыв, стойкостью к химическому разру шению. Известна также заделка незначительных повреждений на поверхности ленты с помощью жидкого пенополиуретана. По крытие наносят на ленту, находящуюся в плоском состоянии. Для повышения эффективности восстановления ленты жидкость на поверхность ленты наносят в момент огибания ею привод ного барабана в зоне перехода дуги покоя в дугу скольжения (в пределах 60—120°). Подготовленную к восстановлению ленту надевают на приводной и тормозной барабаны, и приводят во вращение приводной барабан. При огибании приводного бара бана рабочая обкладка ленты растягивается, при этом обнажа ются ее микродефекты (поры и трещины), которые заполняются жидким покрытием. При переходе этой части ленты в зону скольжения рабочая поверхность ленты сжимается и покрытие защемляется в порах и трещинах. При огибании лентой тормоз ного барабана покрытие фиксируют, прикатывая его обогревае мым роликом. Восстановление ленты может производиться непо средственно на конвейере без демонтажа ленты.
6.5.4. РЕМОНТ РЕЗИНОТРОСОВЫХ ЛЕНТ
При ремонте резинотросовых лент горячей вулканизацией поврежденные участки ленты очищают от грязи, промывают и просушивают плитами пресса, нагретыми до 80—100 °С. В ме стах повреждений ленты срезают резину, производят обработку (зачистку, протирку бензином, промазывание клеем, сушку) и накладывают резиновую заплатку, которую прикатывают, а затем вулканизируют в прессе. Ремонт ленты с поврежден ными тросами осуществляется путем ее разделки, как при сты ковке, обработки и замены поврежденных отрезков тросов но выми. После наложения прослоечной и обкладочной резины ре монтируемый участок ленты помещают в вулканизационный пресс. Если количество поврежденных тросов превышает допус тимое, то такой участок ленты вырезается и производится сты ковка ленты.
В ФРГ накоплен опыт ремонта резинотросовых лент повы шенной прочности в различных климатических условиях на ос нове холодной вулканизации с применением специальных мате риалов под названием «Тип-топ». В комплект материалов вхо дят эластичные заплаты и заполняющая резина, обрезиненные тросы, порошок-цемент, отвердитель, инструменты и приспособ ления. Размеры заплат и обрезиненных тросов выбираются в за висимости от вида повреждения ленты. В ремонт входят опера ции по обрезке, очистке, шероховке, промазке и наложению за
плат. Порошок-цемент применяется в сочетании с 10 %-ной до бавкой отвердителя. Полученная смесь используется в течение 2 ч. Очищенный и отшерохованный участок ленты два раза сма зывается смесью с помощью щетки, втирающей смесь. Первый слой смазки должен быть сухим, а второй — немного клейким. Ремонтируемый участок заполняется резиной толщиной до 3 мм, при этом каждый слой резины смазывается смесью, чтобы со вмещались только смазанные поверхности. Далее непосред ственно перед наложением с эластичной заплаты снимается защитная фольга, эластичная заплата смазывается смесью, су шится до небольшой клейкости. Эластичная заплата прикаты вается сначала широким, а потом узким роликами от середины к краям. Кромки заплаты обрезаются, а затем снова прикаты ваются.
Повреждения резинового слоя ленты размером 100X100 мм или шириной 60 мм при любой длине ремонтируются только за полняющей резиной (рис. 6.19, а). При больших повреждениях обкладки используются и заполняющая резина и эластичная ромбовидная заплата. Для резинотросовых лент, имеющих боль шой срок службы, характерен продольный износ в средней ча сти ленты, связанный с абразивным истиранием, отдельными
а
Повреж дение у зк и х участ ков
6
Повреж дение ш ироких участ ков
Повреждение ленты г |
Заполняю щ ая |
с вырыванием троса |
резина CN i !мм |
РИС. 6.19.
Ремонт резинотросовых лент при поверхностных повреждениях:
а — узких участков; б — широких участков; в — порезах; г — порезах с вырывание» троса; д — борта; е — борта и тросов
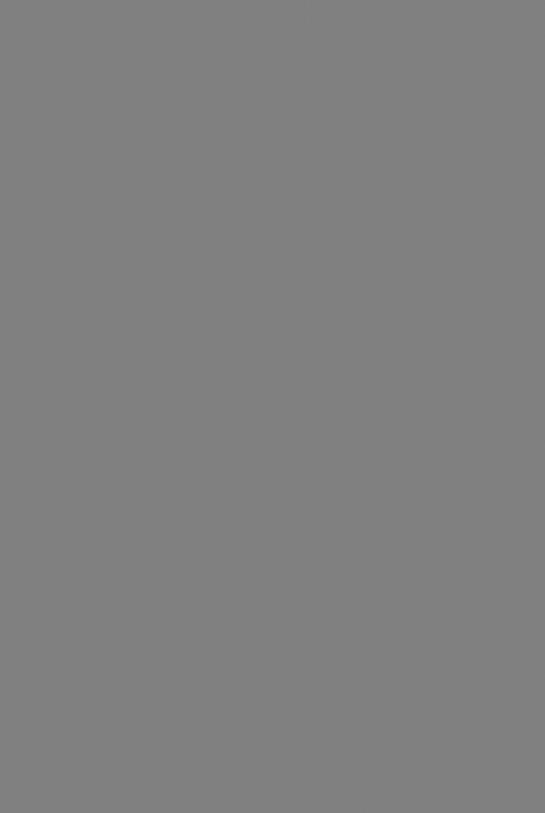
вырывами рабочей обкладки. В зависимости от глубины износа используется или только заполняющая резина или заполняющая резина и эластичная заплата одновременно (рис. 6.19, б). По верхность заплат должна быть расположена на 1 мм ниже ос новной поверхности ленты для исключения возможных задиров при взаимодействии со скребками, роликами, плужками. При порезах резинового слоя ленты повреждение разделывается так, что в поперечном сечении имеет форму треугольника, а затем заполняется слоями резины CN (рис. 6.19, в). Разделка ленты в случае повреждения резинового слоя с вырыванием троса осу ществляется аналогично, но на большую глубину (рис. 6.19, г).
Ремонт повреждения борта (рис. 6.19, д) ленты включает за делку поврежденного участка слоями заполняющей резины и покрытие его со стороны борта, верхней и нижней поверхностей ленты эластичной заплатой. Если одновременно с бортом ленты повреждены тросы, последние удаляются на длине, где резина сохранила свою целостность (рис. 6.19, е). Затем участки по вреждения восстанавливаются слоями заполняющей резины и покрываются заплатой.
Повреждения ленты, связанные со сквозными продольными порезами, требуют оперативного ремонта. Вдоль пореза по обе
стороны |
вырезается резина на расстоянии 75 мм с наклоном |
к порезу |
(рис. 6.20, а). Освобожденное пространство заклады |
вается заполняющей резиной, на которую сверху и снизу накла дываются заплаты. Для лент шириной до 1600 мм процесс ре монта продольных порезов можно ускорить за счет исключения операции разделки повреждения (рис. 6.20, б). В сквозной по
рез закладывается заполняющая резина, а сверху и снизу на кладываются продольные заплаты шириной 220 и 150 мм. Ре монт пробоев с повреждением тросов осуществляется без за кладки заполняющей резины в пробой. Ленту разделывают с двух сторон на расстоянии 50 мм от границы повреждения. Затем заполняют толстым слоем резины, на которую наклады вают заплату (рис. 6.20, в). Если число поврежденных при про бое тросов превышает три, ремонтируемый участок сверху уси ливается вставкой из стального корда (рис. 6.20, г). Вставки могут выполняться из самой конвейерной ленты в виде вклады шей, имеющих ступенчатую форму.
6.6. ВОПРОСЫ ТЕХНИКИ БЕЗОПАСНОСТИ
Интенсивный режим эксплуатации мощных ленточных кон вейеров, большое количество основных и вспомогательных меха низмов с движущимися частями, передача тягового усилия тре нием, повышенная вероятность возникновения аварийной ситуа ции, трудоемкость ликвидации ее последствий делают необходи мым проведение комплекса мероприятий по обеспечению пра вил техники безопасности. В основу этих правил должны быть положены как общие требования безопасности на конвейеры,
так и отраслевые, учитывающие особенности эксплуатации конвейеров, например, в помещениях на поверхности, на карь ерах, в шахтах, при различных климатических условиях и со ставах окружающей среды. Основные требования по технике безопасной эксплуатации мощных ленточных конвейеров мо жно подразделить на группы — требования к конструкции и пожарной безопасности, монтажным и ремонтным работам, электрооборудованию, средствам управления и защиты, вспо могательному оборудованию, эксплуатации и техническому обслуживанию.
Требования к конструкции и пожарной безопасности. Кон вейеры, транспортирующие сильнопылящие грузы, должны иметь укрывающие кожухи и аспирационные устройства.
В местах загрузки предусматриваются отбойные щитки, ис ключающие падение кусков груза с ленты за пределы кон вейера.
Конвейер оснащается устройствами и средствами контроля, обеспечивающими центрированный без пробуксовки ход ленты, исключающими самопроизвольное перемещение ленты с грузом вниз при наклонном транспортировании; сбрасывателями для удаления попавшего на холостую ветвь ленты груза; ловите лями ленты при ее обрыве.
Концевые участки конвейера (привод, натяжные устрой ства), устройства для очистки ленты должны быть ограждены с возможностью быстрого демонтажа ограждающих элементов, их блокировки с приводом конвейера. Ограждения с целью ос мотра узлов изготавливаются сетчатыми.
Для защиты от пожаров и накопления статического электри чества футеровка барабанов и роликов, элементы очистных уст ройств, направляющие элементы загрузочных и перегрузочных устройств изготавливаются из трудновоспламеняемых материа лов с поверхностным электрическим сопротивлением, не превы шающим 3*102 МОм. К применению допускаются ленты, про шедшие входной контроль на пожарную безопасность.
Для локализации и тушения пожаров в ответственных ме стах конвейеров устанавливаются автоматические и ручные средства пожаротушения с применением воды, пены.
Не рекомендуется изменять конструкцию узлов конвейера (особенно тормозных и натяжных устройств, ловителей, средств управления и защиты) без согласования этих изменений в уста новленном порядке.
Необходимо предусматривать автоматическую систему кон троля с температурными датчиками для обнаружения возгора ния и сигнализации.
Требования к монтажным и ремонтным работам. Безопасно сти монтажных и ремонтных работ способствует бирочная си стема, когда места ремонтов не просматриваются с точек воз можного включения конвейера. Включение конвейера при от сутствии бирки категорически запрещается. Наличие бирки
338
у обслуживающего персонала дает им право на производства монтажных и ремонтных работ на конвейере или конвейерной линии.
В производственных зданиях, галереях, тоннелях, на эстака дах в определенных местах должны быть предусмотрены без опасные проходы в виде мостиков с перилами шириной не менее 0,7 м и высотой не менее 2,2 м в производственных помещениях, 1,8 — в галереях, тоннелях и на эстакадах. Ширина проходов для монтажа и ремонта конвейеров должна быть не менее 0,4 м, для параллельно установленных конвейеров — 1 м, а при на личии ограждения — не менее 0,7 м.
При наклонном расположении конвейера (6—12°) монтиру ются настилы с поперечными ребрами для уверенного переме щения по ним персонала. Если угол наклона установки состав ляет более 12°, монтируются жесткие лестничные марши.
Если оси приводных и натяжных барабанов находятся на вы соте более 1,5 м от уровня пола, эти узлы оснащаются жесткими площадками для осмотра, обслуживания и ремонта обору дования.
При угле наклона и высоте лестницы соответственно более 70° и 5 м обязательно использование монтажных поясов.
Трасса конвейера должна быть снабжена указателями опас ных мест и выключателями экстренной остановки.
Должны соблюдаться соответствующие требования безопас ности при ведении такелажных и сварочных работ, к инстру менту, к подготовке персонала и журнальному учету нарушений.
Требования к электрооборудованию, средствам управления и защиты. Все электрооборудование должно иметь соответствую щее условиям исполнение.
Конвейеры или конвейерные линии должны оснащаться ап паратурой дистанционного автоматического управления с воз можностью перевода на местное управление и блокировки между собой.
Конвейеры большой длины оборудуются линейными выклю чателями экстренного отключения привода конвейера.
Особое внимание должно уделяться случаям, связанным с по ражением электрическим током. Они возможны при поврежде нии электропроводки, пусковых и заземляющих устройств. Не обходимо регулярно проверять состояние электрооборудования, изоляции, заземляющих устройств, защиту от утечки токов.
На участках трассы конвейеров, находящихся вне зоны ви димости оператора с пульта управления, должна быть установ лена двусторонняя предупредительная звуковая или световая сигнализация, действующая автоматически перед включением привода конвейера.
Конвейеры в головной и хвостовой частях оборудуются ава рийными кнопками «Ход» и «Стоп», табличками, поясняю щими применение средств сигнализации и режим работы кон вейера.
Необходимо широко использовать сигнально-предупреди тельную окраску опасных частей конвейера, электрооборудова ния, рациональное освещение рабочих мест и конвейера.
Требования к вспомогательному оборудованию, эксплуата ции и техническому обслуживанию. Мощные ленточные конвей еры, как правило, оснащаются средствами контроля схода и центрирования ленты, системами защиты ленты от ударных на грузок в месте загрузки, устройствами очистки и переворота ленты, загрузочными устройствами с элементами регулирования подачи груза и контроля заштыбовки, ловителями лент и на тяжных грузовых устройств. К этим узлам предъявляются такие же требования техники безопасности, как и к основным.
Конвейеры должны использоваться строго по назначению в соответствии с инструкцией, при этом не допускаются пере грузки.
При проведении уборки конвейера, осмотра и смазки узлов, ремонта конвейер останавливается с использованием бирочной системы и соответствующих блокировок. Если некоторые виды работ по обслуживанию конвейера проводятся без его оста новки, необходимо принимать меры по обеспечению безопас ности персонала в части четкого определения состава операций, предупреждения оператора, использования сигналов.
Особое внимание следует уделять повреждениям ленты, ко торые немедленно должны ликвидироваться в ремонтную смену. При значительных повреждениях ленты (длинных продольных порывах, разрывах стыка и бортов) поврежденные участки ленты заменяются новыми либо навешивается новая лента.
Неисправные ролики заменяются новыми, при этом ролики должны легко вращаться и не создавать шума.
Эксплуатация основного и вспомогательного оборудования производится в соответствии с правилами.
Если конвейер останавливается на длительное время (напри мер, при сезонной работе), то все узлы его подлежат «консер вации», включающей очистку, окраску и смазку элементов. Со ставляются акт о состоянии конвейера и ведомости с перечнем обнаруженных дефектов.
При работе во взрывоопасных и пожароопасных цехах, а также при наличии токсичных сред к общим требованиям без опасности добавляются дополнительные, учитывающие специфи ческие условия.